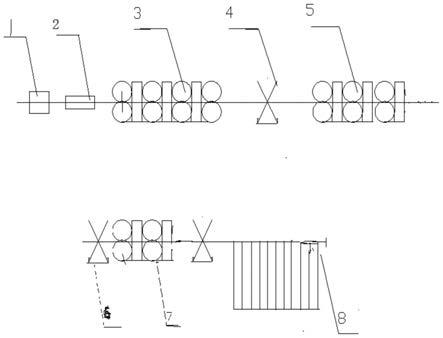
1.本发明属于金属压力加工的技术领域,具体的涉及一种提高棒材热轧平直度控制弯曲的方法。
背景技术:
2.金属压力加工领域中,热轧是在金属再结晶温度以上通过轧钢机使金属产生塑性变形。热轧工艺一般包括原料加热、原料轧制、成品冷却、成品分段包装。棒材是热轧的一种产品,部分钢种如30crmnti、j30crmntia、30crmnsitia等在热轧过程中,其棒材会出现弯曲现象,棒材在经过矫直后弯曲度仍不能满足国标要求,从而产生批量废品。弯曲度是指棒材在长度方向上的弯曲程度,每米长度上弯曲的弦高为每米弯曲度,总长度弯曲的总弦高同总长度的比为总弯曲度,各类轧件的弯曲度规定在产品标准中。
3.一般造成轧件弯曲的原因是热轧时冷却速度不均,收缩不一致;原料加热温度不均匀;热轧过程轧机附件安装不合适等。目前各轧线棒材轧制控制弯曲一般采用轧制过程中在线即时控制的方式,比如通过调整轧机进出口导卫装置和优化孔型压力配置等,但由于坯料温度不均匀,存在头尾温差以及孔型磨损不均匀等,最终的控制效果并不明显。因此亟需一种能够显著提高棒材热轧平直度,控制弯曲度的轧制方法。
技术实现要素:
4.本发明的目的在于针对上述存在的缺陷而提供一种提高棒材热轧平直度控制弯曲的方法,该方法将坯料加热、轧制温控、冷床冷却温控以及棒材的锯切与精整统筹设计,使得易弯曲棒材经过所述的原料加热、轧制温度控制和冷床冷却控制后,可有效避免钢材的弯曲状况,达到国标要求,避免棒材因弯曲矫直后带来的表面硬化现象,满足用户的需求。
5.本发明的技术方案为:一种提高棒材热轧平直度控制弯曲的方法,包括以下步骤:
6.(1)坯料加热:将连铸坯装入加热炉内加热,预热段温度500~950℃,加热ⅰ段温度950~1120℃,加热ⅱ段温度1120~1210℃,均热段温度1130~1180℃,均热段保温时间≥35分钟,总加热时间≥210分钟;连铸坯断面温差<30℃;
7.(2)高压水除磷:连铸坯出炉后进入高压水除鳞装置,去除连铸坯表面的氧化铁皮;
8.(3)粗轧:开轧温度控制在1030~1100℃,连铸坯进入粗轧机组;
9.(4)中轧:粗轧后的连铸坯进入中精轧机组;
10.(5)精轧:连铸坯经中轧后进入精轧机组,精轧后温度即终轧温度控制在900~950℃;
11.(6)冷床冷却:精轧后所得棒材进入倍尺冷床冷却,其中棒材之间以2~3个齿距的间隔排列在冷床上;上冷床温度≤920℃,下冷床温度≤350℃;
12.(7)棒材锯切:棒材经过锯切分段,收集打捆后入缓冷坑缓冷,入坑温度在240℃~
300℃;棒材在缓冷坑充分缓冷24小时,出坑温度≤100℃;
13.(8)棒材精整:棒材经过矫直、扒皮、探伤后,进行标准化包装。
14.所述步骤(1)中连铸坯规格为260mm
×
3000mm
×
7000mm。
15.所述步骤(2)中高压水除鳞的水压为25mpa。
16.所述步骤(3)中粗轧机组共设7架轧机,由6架φ1000mm轧机和1架φ780mm轧机组成;轧机类型为高刚度短应力线轧机,平
‑
立交替布置,粗轧后由液压剪切头。
17.所述步骤(4)中的中精轧机组由6架φ780mm轧机组成,中轧后由液压剪切头。
18.所述步骤(5)中精轧机组由4架φ600mm轧机组成;轧机类型为高刚度短应力线轧机,采用平
‑
立交替布置。
19.本发明的有益效果为:本发明所述方法首先通过控制坯料的加热温度使棒材保证具备适当的开轧温度和终轧温度,最终保证棒材的上冷床温度和下冷床温度具备合理的冷却范围。同时棒材在冷床上排列间隔不同,冷却速度不同,通过调整棒材与棒材在冷床上的间隔距离,控制其冷却速度,可有效降低棒材在热轧时的弯曲度,杜绝弯曲废品的产生。
20.本发明通过试验,验证热轧温度的控制、冷床冷却温控以及棒材排列间隔三者之间是具有协同性的,具体验证数据如表1。
21.表1:试验数据
[0022][0023]
由表1数据综合分析可知,热轧过程在温度控制,尤其开轧温度和终轧温度;冷床冷却的温度控制上冷床温度和下冷床温度以及棒材在冷床上的排列在对棒材弯曲程度方面的影响并非简单的单因素或简单叠加影响,而是几个因素间相互交叉协同影响。
附图说明
[0024]
图1为轧制工艺流程示意图。
[0025]
图2为冷床冷却示意图。
[0026]
其中,1为加热炉;2为高压水除鳞;3为粗轧机组;4为液压剪;5为中轧机组;6为液压剪;7为精轧机组;8为倍尺冷床;9为棒材;10为冷床齿条;11为齿型角。
具体实施方式
[0027]
下面通过实施例对本发明的技术方案进行详细的说明。
[0028]
实施例1
[0029]
以生产j30crmntia成品规格φ90mm的棒材为例,所述提高棒材热轧平直度控制弯曲的方法,包括以下步骤:
[0030]
(1)坯料加热:将规格为260mm
×
3000mm
×
7000mm的连铸坯经过工艺称重、测长,经入炉辊道和钢坯拖入机装入步进梁式加热炉内加热,预热段温度860℃,加热ⅰ段温度1120℃,加热ⅱ段温度1210℃,均热段温度1180℃,均热段保温时间≥35分钟,总加热时间为210分钟;连铸坯断面温差<30℃
[0031]
(2)高压水除磷:连铸坯出炉后进入高压水除鳞装置,水压为25mpa,去除连铸坯表面的氧化铁皮;
[0032]
(3)粗轧:开轧温度控制在1050℃,连铸坯进入粗轧机组,粗轧机组共设7架轧机,由6架φ1000mm轧机和1架φ780mm轧机组成;轧机类型为高刚度短应力线轧机,平
‑
立交替布置,粗轧后由液压剪切头;
[0033]
(4)中轧:粗轧后的连铸坯进入中精轧机组,中精轧机组由6架φ780mm轧机组成,中轧后由液压剪切头;
[0034]
(5)精轧:连铸坯经中轧后进入精轧机组,精轧机组由4架φ600mm轧机组成;轧机类型为高刚度短应力线轧机,采用平
‑
立交替布置;精轧后温度即终轧温度控制在900~950℃;
[0035]
(6)冷床冷却:精轧后所得棒材进入倍尺冷床冷却,其中棒材之间以2~3个齿距的间隔排列在冷床上;上冷床温度910℃,下冷床温度270℃;
[0036]
(7)棒材锯切:棒材经过锯切分段,收集打捆后入缓冷坑缓冷,入坑温度在240℃;棒材在缓冷坑充分缓冷24小时,出坑温度70℃;
[0037]
(8)棒材精整:棒材经过矫直、扒皮、探伤后,进行标准化包装。
[0038]
实施例1所得钢材弯曲度如表2所示。
[0039]
表2:钢材弯曲度
[0040][0041]
由表2可见,常规轧制所得钢材中每米弯曲度>4mm的占比远高于每米弯曲度>2.5mm;而按照实施例1所述方法轧制所得钢材却相反,每米弯曲度>4mm的占比远低于每米弯曲度>2.5mm。将实施例1方法轧制所得钢材与常规轧制相比较,实施例1钢材达到国标1组的占比相较于常规轧制提高了63%,国标2组的占比降低了63%。
[0042]
实施例2
[0043]
以生产30crmnsitia成品规格φ70mm的棒材为例,所述提高棒材热轧平直度控制弯曲的方法,包括以下步骤:
[0044]
(1)坯料加热:将规格为260mm
×
3000mm
×
7000mm的连铸坯经过工艺称重、测长,经入炉辊道和钢坯拖入机装入步进梁式加热炉内加热,预热段温度865℃,加热ⅰ段温度1120℃,加热ⅱ段温度1210℃,均热段温度1180℃,均热段保温时间≥35分钟,总加热时间210分钟,连铸坯断面温差<30℃;
[0045]
(2)高压水除磷:连铸坯出炉后进入高压水除鳞装置,水压为25mpa,去除连铸坯表面的氧化铁皮;
[0046]
(3)粗轧:开轧温度控制在1040℃,连铸坯进入粗轧机组,粗轧机组共设7架轧机,由6架φ1000mm轧机和1架φ780mm轧机组成;轧机类型为高刚度短应力线轧机,平
‑
立交替布置,粗轧后由液压剪切头;
[0047]
(4)中轧:粗轧后的连铸坯进入中精轧机组,中精轧机组由6架φ780mm轧机组成,中轧后由液压剪切头;
[0048]
(5)精轧:连铸坯经中轧后进入精轧机组,精轧机组由4架φ600mm轧机组成;轧机类型为高刚度短应力线轧机,采用平
‑
立交替布置;精轧后温度即终轧温度控制在900~950℃;
[0049]
(6)冷床冷却:精轧后所得棒材进入倍尺冷床冷却,其中棒材之间以2~3个齿距的间隔排列在冷床上;上冷床温度910℃,下冷床温度270℃;
[0050]
(7)棒材锯切:棒材经过锯切分段,收集打捆后入缓冷坑缓冷,入坑温度在240℃;棒材在缓冷坑充分缓冷24小时,出坑温度60℃;
[0051]
(8)棒材精整:棒材经过矫直、扒皮、探伤后,进行标准化包装。
[0052]
实施例2所得钢材弯曲度如表3所示。
[0053]
表3:钢材弯曲度
[0054][0055]
由表3可见,常规轧制所得钢材中每米弯曲度>4mm的占比远高于每米弯曲度>2.5mm;而按照实施例2所述方法轧制所得钢材却相反,每米弯曲度>4mm的占比远低于每米弯曲度>2.5mm。将实施例2方法轧制所得钢材与常规轧制相比较,实施例2钢材达到国标1组的占比相较于常规轧制提高了74%,国标2组的占比降低了74%。
[0056]
实施例3
[0057]
以生产30crmnti成品规格φ85mm的棒材为例,所述提高棒材热轧平直度控制弯曲的方法,包括以下步骤:
[0058]
(1)坯料加热:将规格为260mm
×
3000mm
×
7000mm的连铸坯经过工艺称重、测长,经入炉辊道和钢坯拖入机装入步进梁式加热炉内加热,预热段温度870℃,加热ⅰ段温度1120℃,加热ⅱ段温度1210℃,均热段温度1180℃,均热段保温时间≥35分钟,总加热时间210分钟,连铸坯断面温差<30℃;
[0059]
(2)高压水除磷:连铸坯出炉后进入高压水除鳞装置,水压为25mpa,去除连铸坯表面的氧化铁皮;
[0060]
(3)粗轧:开轧温度控制在1050℃,连铸坯进入粗轧机组,粗轧机组共设7架轧机,由6架φ1000mm轧机和1架φ780mm轧机组成;轧机类型为高刚度短应力线轧机,平
‑
立交替
布置,粗轧后由液压剪切头;
[0061]
(4)中轧:粗轧后的连铸坯进入中精轧机组,中精轧机组由6架φ780mm轧机组成,中轧后由液压剪切头;
[0062]
(5)精轧:连铸坯经中轧后进入精轧机组,精轧机组由4架φ600mm轧机组成;轧机类型为高刚度短应力线轧机,采用平
‑
立交替布置;精轧后温度即终轧温度控制在900~950℃;
[0063]
(6)冷床冷却:精轧后所得棒材进入倍尺冷床冷却,其中棒材之间以2~3个齿距的间隔排列在冷床上;上冷床温度910℃,下冷床温度270℃;
[0064]
(7)棒材锯切:棒材经过锯切分段,收集打捆后入缓冷坑缓冷,入坑温度在240℃;棒材在缓冷坑充分缓冷24小时,出坑温度60℃;
[0065]
(8)棒材精整:棒材经过矫直、扒皮、探伤后,进行标准化包装。
[0066]
实施例3所得钢材弯曲度如表4所示。
[0067]
表4:钢材弯曲度
[0068][0069]
由表4可见,常规轧制所得钢材中每米弯曲度>4mm的占比远高于每米弯曲度>2.5mm;而按照实施例3所述方法轧制所得钢材却相反,每米弯曲度>4mm的占比远低于每米弯曲度>2.5mm。将实施例3方法轧制所得钢材与常规轧制相比较,实施例3钢材达到国标1组的占比相较于常规轧制提高了74%,国标2组的占比降低了74%。
再多了解一些
本文用于企业家、创业者技术爱好者查询,结果仅供参考。