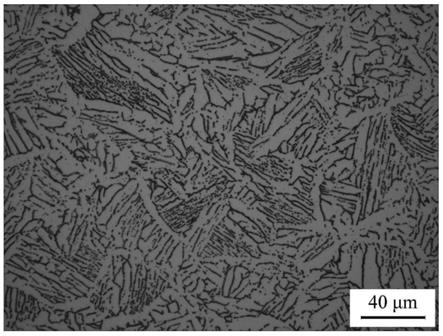
1.本发明属于合金技术领域,特别涉及一种低弹性模量锆合金及其制备方法和应用。
背景技术:
2.锆具有优异的生物相容性,广泛应用于生物医用领域。但是,目前生物医用领域的锆合金依然存在着诸多问题,如强度较低、弹性模量高的问题。例如,锆合金体系中zr
‑
nb系是典型的合金体系,现有技术中zr
‑
nb系合金的屈服强度通常只有400mpa左右,强度低,同时锆合金的弹性模量又较高。低弹性模量的锆合金又往往存在成本高的问题,例如中国专利申请cn110408815a公开了一种低弹性模量、生物医用低弹性模量度的调幅分解型zr
‑
nb
‑
ti合金材料及其制备方法,但该合金中铌含量为15~45%,原材料成本较高。
技术实现要素:
3.有鉴于此,本发明的目的在于提供一种低弹性模量锆合金及其制备方法,本发明提供的低弹性模量锆合金具有弹性模量低、强度高、塑性优异且成本低的特点。
4.为了实现上述发明的目的,本发明提供以下技术方案:
5.本发明提供了一种低弹性模量锆合金,以质量百分含量计,包括以下元素:
6.nb 0.5~15%、sn 0.5~5%、hf 0.1~4.5%和余量的zr。
7.优选的,所述低弹性模量锆合金的组织包括板条α相和/或等轴β相。
8.优选的,所述板条α相的板条宽度为1~7.2μm;所述等轴β相的晶粒尺寸为52~240μm。
9.优选的,所述低弹性模量锆合金的弹性模量为45~80gpa,屈服强度为350~600mpa,抗拉强度为600~800mpa,延伸率为12~26%。
10.本发明还提供了上述技术方案所述低弹性模量锆合金的制备方法,包括以下步骤:
11.提供合金铸锭,所述铸锭的化学组成与低弹性模量锆合金的化学组成一致;
12.将所述合金铸锭进行退火,得到所述低弹性模量锆合金。
13.优选的,所述合金铸锭的制备方法包括:将合金原料依次进行熔炼和冷却,得到所述合金铸锭;
14.所述熔炼的温度为2300~2600℃。
15.优选的,所述退火的温度为450~600℃,保温时间为1~2h。
16.优选的,所述退火在保护气条件下进行。
17.本发明还提供了上述技术方案所述低弹性模量锆合金或上述技术方案所述制备方法制备的低弹性模量锆合金在制备承力植入材料中的应用。
18.本发明提供了一种低弹性模量锆合金,以质量百分含量计,包括以下元素:nb 0.5~15%、sn 0.5~5%、hf 0.1~4.5%和余量的zr。在本发明中,nb与zr属于同一主族,具有
固溶强化的作用,能够显著提高锆合金的强度,同时,通过控制nb元素的添加,有利于提高锆合金中β相的含量,从而降低锆合金的弹性模量,提高锆合金的耐腐蚀性、塑性以及生物相容性;sn属于中性元素,在α相和β相中固溶强化作用明显,提高了合金的强度,同时,sn具备良好的生物相容性,保证了锆合金的生物相容性;hf属于中性元素,在α相和β相中固溶强化作用明显,有利于提高锆合金的强度。本发明通过严格控制各元素的含量,利用合金化,使nb与zr形成固溶体,实现固溶强化;sn和hf属于中性元素,在α相和β相中固溶强化作用明显,通过各元素协同配合,共同在保证锆合金强度的基础上降低锆合金的弹性模量。而且,本技术中nb含量低,有利于降低锆合金的成本。
19.实施例测试结果表明,本发明提供的低弹性模量锆合金的弹性模量为52~76gpa,屈服强度为421.8~591.2mpa,抗拉强度为642.3~772.6mpa,延伸率为15.2~20.3%,具有高强度和高塑性基础上还具有低的弹性模量。
20.本发明还提供了上述技术方案所述低弹性模量锆合金的制备方法,包括以下步骤:提供合金铸锭,所述铸锭的化学组成与低弹性模量锆合金的化学组成一致;将所述合金铸锭进行退火,得到所述低弹性模量锆合金。本发明通过退火,有利于消除熔炼过程中形成的残余应力并消除部分显微缺陷,使合金成分进一步均匀化;本发明仅需在熔炼后进行退火即可得到综合性能优异的锆合金,方法简单易行。
附图说明
21.图1为实施例1所得低弹性模量锆合金的金相光学显微图;
22.图2为实施例2所得低弹性模量锆合金的金相光学显微图;
23.图3为实施例3所得低弹性模量锆合金的金相光学显微图;
24.图4为实施例4所得低弹性模量锆合金的金相光学显微图;
25.图5为对比例1所得锆合金的金相光学显微图。
具体实施方式
26.本发明提供了一种低弹性模量锆合金,以质量百分含量计,包括以下元素:
27.nb 0.5~15%、sn 0.5~5%、hf 0.1~4.5%和余量的zr。
28.在本发明中,以质量百分含量计,所述低弹性模量锆合金包括0.5~15%的nb,优选为1.5~14%,更优选为2~13%,再优选为2.5~12%。在本发明中,nb与zr属于同一主族,具有固溶强化的作用,能够提高锆合金的强度;同时,本发明通过控制nb元素的添加,能够控制合金中β相的含量,从而降低锆合金的弹性模量,提高锆合金的耐腐蚀性、塑性以及生物相容性。
29.在本发明中,以质量百分含量计,所述低弹性模量锆合金包括0.5%~5%的sn,优选为0.8~4.5%,更优选为0.9~4.3%,再优选为1~4%。在本发明中,sn属于中性元素,在α相和β相中固溶强化作用明显,有利于提高锆合金的强度;同时,sn具备良好的生物相容性,有利于提高锆合金的生物相容性。
30.在本发明中,以质量百分含量计,所述低弹性模量锆合金包括0.1~4.5%的hf,优选为0.5~4.2%,更优选为1~4%,再优选为1.6~3.6%。在本发明中,hf属于中性元素,在α相和β相中固溶强化作用明显,有利于提高锆合金的强度。
31.在本发明中,以质量百分含量计,所述低弹性模量锆合金包括余量的zr。在本发明中,zr为锆合金的基体元素。
32.在本发明中,所述低弹性模量锆合金的组织优选包括板条α相和/或等轴β相。在本发明中,当所述低弹性模量锆合金的组织同时包括板条α相和等轴β相时,所述低弹性模量锆合金的组织为板条α相和等轴β相形成的网篮组织。
33.在本发明中,所述板条α相的板条宽度优选为1~7.2μm,更优选为1.5~7μm,再优选为2~6.5μm。在本发明中,所述等轴β相的晶粒尺寸优选为52~240μm,更优选为55~235μm,再优选为57~232μm。
34.在本发明中,α相的晶体结构是密排六方结构,具有强度高的特点;而β相是体心立方结构,易协调变形,易获得低的弹性模量,但是强度较低,nb含量越高,相应成分的β相比例越大,因此通过控制nb含量,调控合金中α相和β相的相对含量,有利于得到综合力学性能优异的锆合金。
35.在本发明中,随着锆合金中nb和sn元素的增加,合金的β转变温度随之降低,在相近的冷却条件下,原始β晶粒形核数目增多,生成的原始β晶粒尺寸越小,β相的含量越多,本发明通过调节合金中β相的含量来调节合金的强塑性和弹性模量,提供优异的低弹性模量锆合金。
36.本发明提供的低弹性模量锆合金具有良好的生物相容性,具有作为制备承力植入材料的应用潜力。
37.在本发明中,所述低弹性模量锆合金的弹性模量优选为45~80gpa,屈服强度优选为350~600mpa,抗拉强度优选为600~800mpa,延伸率优选为12~26%。
38.本发明还提供了上述技术方案所述低弹性模量锆合金的制备方法,包括以下步骤:
39.提供合金铸锭,所述铸锭的化学组成与低弹性模量锆合金的化学组成一致;
40.将所述合金铸锭进行退火,得到所述低弹性模量锆合金。
41.本发明提供合金铸锭,所述铸锭的化学组成与低弹性模量锆合金的化学组成一致。
42.在本发明中,所述合金铸锭的制备方法优选包括:将合金原料依次进行熔炼和冷却,得到所述合金铸锭。
43.在本发明中,所述合金原料优选为海绵锆、纯铌丝和纯锡粒;所述海绵锆中含有铪。本发明采用含铪的海绵锆,即无需对海绵锆进行提纯。本发明采用锆铪不分离的海绵锆,有利于降低原料成本。在本发明中,所述纯铌丝的纯度优选≥99.9%。在本发明中,所述纯锡粒的纯度优选≥99.9%。本发明对所述合金原料的具体来源和添加量没有特殊的限定,以得到满足化学成分要求的低弹性模量锆合金为准。具体来说,根据实际得到的合金原料的组成,合理调整各原料合金的用量,以得到满足化学成分的低弹性模量锆合金即可。
44.本发明优选将合金原料依次进行清洗和干燥,然后用于熔炼。在本发明中,所述清洗优选为超声清洗。在本发明中,所述超声清洗中的清洗剂优选为无水乙醇。本发明对所述超声清洗没有特殊限定,采用本领域技术人员熟知的超声清洗即可。本发明对所述清洗和干燥没有特殊限定,采用本领域技术人员熟知的清洗和干燥即可。本发明通过清洗去除合金原料表面的杂质和油污。
45.在本发明中,所述熔炼优选为真空电弧熔炼,更优选为非自耗真空电弧熔炼。在本发明中,所述熔炼的设备优选为非自耗电弧熔炼炉,更优选为非自耗真空电弧熔炼炉。在本发明中,所述非自耗真空电弧熔炼炉中的坩埚优选为水冷铜坩埚。本发明优选将熔炼的设备腔体抽真空后,向抽真空的熔炼的设备腔体内再充入保护气,然后进行熔炼。在本发明中,所述抽真空后熔炼的设备腔体内的真空度优选≤8
×
10
‑3pa,更优选为3
×
10
‑3pa~7
×
10
‑3pa。在本发明中,所述保护气优选为氩气。本发明对所述氩气的充入量没有特殊限定,以满足电弧熔炼用电离气体的用量即可。本发明采用先抽真空再通入氩气的方式,可以避免zr在高温的情况下,大量吸氧吸氮,发生氧化氮化,还能为真空电弧熔炼提供电离气体。
46.在本发明中,所述熔炼的温度为2300~2600℃,优选为2330~2580℃,更优选为2350~2550℃。在本发明中,所述熔炼中非自耗电弧熔炼的电流优选为480~450a,更优选为400~430a。在本发明中,所述熔炼优选在保护气条件下进行。在本发明中,所述保护气优选为氩气。在本发明中,所述保护气的压力优选为0.04~0.05mpa,更优选为0.042~0.048mpa。
47.本发明优选在每次非自耗真空电弧熔炼完成后冷却,将所得铸坯进行翻转,进行下一次非自耗真空电弧熔炼。在本发明中,每次非自耗真空电弧熔炼的时间独立地优选为3~5min,更优选为3.5~4.5min。在本发明中,所述熔炼中非自耗电弧熔炼的次数优选≥5次,更优选为6~10次。本发明优选重复进行非自耗真空电弧熔炼,有利于保证所得合金铸锭的成分更加均匀。
48.在本发明中,熔炼时熔炼液在凝固过程中先形成β相,随着温度的降低全部或部分β相转变为α相。
49.得到合金铸锭后,本发明将所述合金铸锭进行退火,得到所述低弹性模量锆合金。
50.退火前,本发明优选还包括:将所述合金铸锭的表面进行打磨抛光;本发明对所述打磨抛光没有特殊限定,采用本领域技术人员熟知的打磨即可。本发明通过打磨抛光,有利于提高合金铸锭表面平整性,有利于合金铸锭在退火时受热均匀,重复性强。
51.本发明优选将合金铸锭进行切割,以得到合金铸锭薄板;所述合金铸锭薄板的厚度优选为5~6mm。在本发明中,以合金铸锭薄板进行退火,更有利于退火均匀。
52.在本发明中,所述退火的温度优选为450~600℃,更优选为470~580℃;保温时间优选为1~2h,更优选为1.2~1.8h。在本发明中,所述退火的温度优选由室温升温获得;所述升温的速率优选为10~20℃/min,更优选为10~15℃/min。本发明优选将退火后的合金坯冷却至室温。在本发明中,所述退火后的冷却优选为随炉冷却。在本发明中,所述退火优选在保护气条件下进行;在本发明中,所述保护气优选为氩气。在本发明中,所述退火的设备优选为真空管式炉。在本发明的实施例中,所述真空管式炉优选为天津市中环实验电炉有限公司的sk
‑
g06143。本发明通过退火,有利于有效消除熔炼过程中形成的残余应力及消除部分显微缺陷,使锆合金成分进一步均匀化。
53.本发明仅需在熔炼后进行简单的退火即可得到综合性能优异的锆合金,方法简单易行。
54.退火后,本发明优选还包括:将退火所得的锆合金表面依次进行打磨。本发明对所述打磨没有特殊限定,采用本领域技术人员熟知的打磨即可。在本发明通过打磨,去除锆合金表面的氧化皮。
55.本发明提供的低弹性模量锆合金的制备方法,成本低且简单易行。
56.本发明还提供了上述技术方案所述低弹性模量锆合金或上述技术方案所述制备方法制备的低弹性模量锆合金在制备承力植入材料中的应用。
57.本发明对所述应用没有特殊限定,采用本领域技术人员熟知的承力植入材料的应用即可。
58.为了进一步说明本发明,下面结合实施例对本发明提供的一种低弹性模量锆合金及其制备方法和应用进行详细地描述,但不能将它们理解为对本发明保护范围的限定。显然,所描述的实施例仅是本发明一部分实施例,而不是全部的实施例。基于本发明中的实施例,本领域普通技术人员在没有做出创造性劳动前提下所获得的所有其他实施例,都属于本发明保护的范围。
59.实施例1
60.设计低弹性模量锆合金的化学成分为zr
‑
0.6nb
‑
0.5sn
‑
4.4hf,即按质量百分含量计为nb 0.6%、sn 0.5%、hf 4.4%、余量为zr和不可避免的杂质;
61.按设计低弹性模量锆合金的化学成分将合金原料置于无水乙醇中进行超声清洗,风干,混合后,置于水冷铜坩埚中,置于非自耗真空电弧熔炼炉中,将炉腔内抽真空至5
×
10
‑3pa,然后充入氩气,在真空度为5
×
10
‑3pa、压力为0.04~0.05mpa氩气条件下进行非自耗电弧熔炼,其中,熔炼温度为2400℃,熔炼过程中电流为420a,单次熔炼时间为4min,熔炼后冷却,将所得铸坯进行翻转,进行下一次非自耗电弧熔炼处理,共进行6次非自耗电弧熔炼,冷却后得到合金铸锭;
62.将所得的合金铸锭切割得到厚度为5mm的合金铸锭薄板,表面打磨抛光后,置于真空管式炉中,以10℃/min的速率升温至500℃,在500℃下保温100min,随炉冷却至室温后取出,打磨去除表面的氧化皮,并清洗风干,得到所述低弹性模量锆合金。
63.采用icp
‑
oes方法对所得低弹性模量锆合金进行成分检测,测定所得低弹性模量锆合金的化学成分为zr
‑
0.57nb
‑
0.44sn
‑
4.4hf,即按质量百分含量计为nb 0.57%、sn 0.44%、hf 4.4%、余量为zr和不可避免的杂质。
64.对实施例1所得低弹性模量锆合金进行进行金相显微组织测试,测试图见图1。由图1可见,本实施例制备的低弹性模量锆合金由板条α相构成,板条α相的平均板条宽度为6μm。
65.实施例2
66.设计低弹性模量锆合金的化学成分为zr
‑
3nb
‑
1sn
‑
4.2hf,即按质量百分含量计为nb 3%、sn 1%、hf 4.2%、余量为zr和不可避免的杂质;
67.按设计低弹性模量锆合金的化学成分将合金原料置于无水乙醇中进行超声清洗,风干,混合后,置于水冷铜坩埚中,置于非自耗真空电弧熔炼炉中,将炉腔内抽真空至5
×
10
‑3pa,然后充入氩气,在真空度为5
×
10
‑3pa、压力为0.04~0.05mpa氩气条件下进行非自耗电弧熔炼,其中,熔炼温度为2400℃,熔炼过程中电流为420a,单次熔炼时间为4min,熔炼后冷却,将所得铸坯进行翻转,进行下一次非自耗电弧熔炼处理,共进行6次非自耗电弧熔炼,冷却后得到合金铸锭;
68.将所得的合金铸锭切割得到厚度为5mm的合金铸锭薄板,表面打磨抛光后,置于真空管式炉中,以10℃/min的速率升温至500℃,在500℃下保温100min,随炉冷却至室温后取
出,打磨去除表面的氧化皮,并清洗风干,得到所述低弹性模量锆合金。
69.采用icp
‑
oes方法对所得低弹性模量锆合金进行成分检测,测定所得低弹性模量锆合金的化学成分为zr
‑
2.9nb
‑
0.9sn
‑
4.2hf,即按质量百分含量计为nb 2.9%、sn 0.9%、hf 4.2%、余量为zr和不可避免的杂质。
70.对实施例2所得低弹性模量锆合金进行进行金相显微组织测试,测试图见图2。由图2可见,本实施例制备的低弹性模量锆合金为典型的α β相网篮组织,其中等轴β相的体积含量为5~15%,含量较少,分布在板条α相之间,板条α相的平均板条宽度为4.5μm。
71.实施例3
72.设计低弹性模量锆合金的化学成分为zr
‑
5nb
‑
2sn
‑
4.1hf,即按质量百分含量计为nb 5%、sn 2%、hf 4.1%、余量为zr和不可避免的杂质;
73.按设计低弹性模量锆合金的化学成分将合金原料置于无水乙醇中进行超声清洗,风干,混合后,置于水冷铜坩埚中,置于非自耗真空电弧熔炼炉中,将炉腔内抽真空至5
×
10
‑3pa,然后充入氩气,在真空度为5
×
10
‑3pa、压力为0.04~0.05mpa氩气条件下进行非自耗电弧熔炼,其中,熔炼温度为2400℃,熔炼过程中电流为420a,单次熔炼时间为4min,熔炼后冷却,将所得铸坯进行翻转,进行下一次非自耗电弧熔炼处理,共进行6次非自耗电弧熔炼,冷却后得到合金铸锭;
74.将所得的合金铸锭切割得到厚度为5mm的合金铸锭薄板,表面打磨抛光后,置于真空管式炉中,以10℃/min的速率升温至500℃,在500℃下保温100min,随炉冷却至室温后取出,打磨去除表面的氧化皮,并清洗风干,得到所述低弹性模量锆合金。
75.采用icp
‑
oes方法对所得低弹性模量锆合金进行成分检测,测定所得低弹性模量锆合金的化学成分为zr
‑
5.1nb
‑
1.8sn
‑
4.1hf,即按质量百分含量计为nb 5.1%、sn 1.8%、hf 4.1%、余量为zr和不可避免的杂质。
76.对实施例3所得低弹性模量锆合金进行进行金相显微组织测试,测试图见图3。由图3可见,本实施例制备的低弹性模量锆合金为典型的α β相组织,其中等轴β相的体积含量为50~70%,含量较多,分布在板条α相之间,板条α相的平均板条宽度为5.1μm。
77.实施例4
78.设计低弹性模量锆合金的化学成分为zr
‑
10nb
‑
2.5sn
‑
3.8hf,即按质量百分含量计为nb 10%、sn 2.5%、hf 3.8%、余量为zr和不可避免的杂质;
79.按设计低弹性模量锆合金的化学成分将合金原料置于无水乙醇中进行超声清洗,风干,混合后,置于水冷铜坩埚中,置于非自耗真空电弧熔炼炉中,将炉腔内抽真空至5
×
10
‑3pa,然后充入氩气,在真空度为5
×
10
‑3pa、压力为0.04~0.05mpa氩气条件下进行非自耗电弧熔炼,其中,熔炼温度为2400℃,熔炼过程中电流为420a,单次熔炼时间为4min,熔炼后冷却,将所得铸坯进行翻转,进行下一次非自耗电弧熔炼处理,共进行6次非自耗电弧熔炼,冷却后得到合金铸锭;
80.将所得的合金铸锭切割得到厚度为5mm的合金铸锭薄板,表面打磨抛光后,置于真空管式炉中,以10℃/min的速率升温至500℃,在500℃下保温100min,随炉冷却至室温后取出,打磨去除表面的氧化皮,并清洗风干,得到所述低弹性模量锆合金。
81.采用icp
‑
oes方法对所得低弹性模量锆合金进行成分检测,测定所得低弹性模量锆合金的化学成分为zr
‑
9.8nb
‑
2.3sn
‑
3.8hf,即按质量百分含量计为nb 9.8%、sn 2.3%、
hf 3.8%、余量为zr和不可避免的杂质。
82.对实施例4所得低弹性模量锆合金进行进行金相显微组织测试,测试图见图4。由图4可见,本实施例制备的低弹性模量锆合金为典型的等轴β相组织,没有板条α相的存在,等轴β相的平均晶粒尺寸为132μm。
83.对比例1
84.设计锆合金的化学成分为zr
‑
2.5nb
‑
4.4hf,即按质量百分含量计为nb 2.5%、hf 4.4%、余量为zr和不可避免的杂质;其余技术手段与实施例1一致,得到锆合金。
85.采用icp
‑
oes方法对所得锆合金进行成分检测,测定所得锆合金的化学成分为zr
‑
2.48nb
‑
4.4hf,即按质量百分含量计为nb 2.48%、hf 4.4%、余量为zr和不可避免的杂质。
86.对对比例1所得锆合金进行进行金相显微组织测试,测试图见图5。由图5可见,本对比例制备的锆合金为典型的α β相网篮组织,其中等轴β相的体积含量为7~12%,含量较少,分布在板条α相之间,板条α相的平均板条宽度为4.5μm。
87.按照gb/t 228
‑
2002对实施例1~4和对比例1所得的锆合金进行测试,测试方法为:利用线切割将锆合金板切出骨棒状的单轴拉伸试样,按照国家标准gbt228
‑
2002对单轴拉伸试样的力学性能进行测试;测试过程中,每个实施例的样品至少切出5个拉伸试样,确保数据的可重复性,采用室温单轴拉伸实验进行测量,测试仪器型号为instron5982的万能材料试验机(生产商:英斯特朗,美国),全程用引伸计监测试样的拉伸位移,拉伸速率设定为5
×
10
‑4s
‑1,进行拉伸试验。测试结果见表1。
88.表1实施例1~4和对比例1所得锆合金的性能测试结果
[0089][0090][0091]
由表1可见,本发明提供的低弹性模量锆合金的弹性模量为52~76gpa,弹性模量低;屈服强度为421.8~591.2mpa,抗拉强度为642.3~772.6mpa,延伸率为15.2~20.3%,同时具有较高的屈服强度、抗拉强度和优异的塑性。
[0092]
以上所述仅是本发明的优选实施方式,应当指出,对于本技术领域的普通技术人员来说,在不脱离本发明原理的前提下,还可以做出若干改进和润饰,这些改进和润饰也应视为本发明的保护范围。
再多了解一些
本文用于企业家、创业者技术爱好者查询,结果仅供参考。