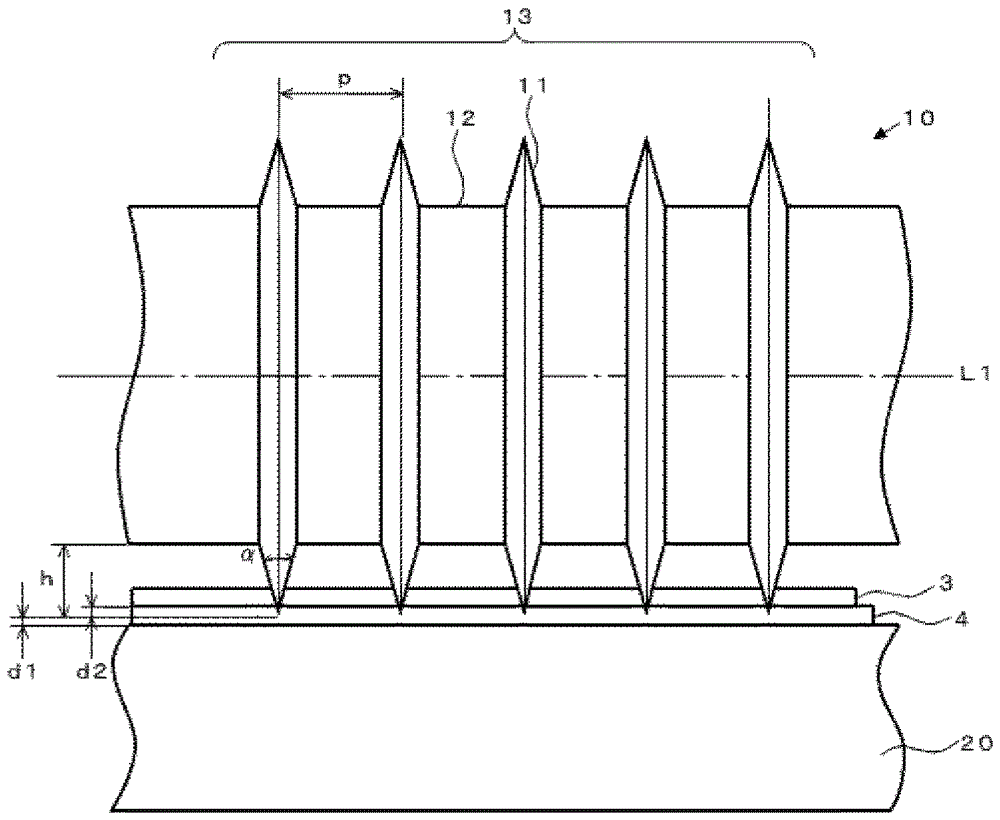
本发明涉及粘附层可剥离地层叠于基材膜的层叠膜的切缝装置、切缝方法和通过层叠膜的切缝来得到的层叠带。
背景技术
粘附层可剥离地层叠于基材膜的长尺寸的层叠带用作将图形、文字等转印至物品的转印色带等(专利文献1)。这样的层叠带通过对粘附层可剥离地层叠于基材膜的层叠膜进行切缝来制造。
粘附层可剥离地层叠于基材膜的长尺寸的层叠带还用作在将电子零件封装于基板时的粘接材料,近几年,需要细宽度的层叠带。然而,如果将粘附层可剥离地层叠于基材膜的层叠膜切缝成细宽度,则产生由于切缝而导致基材膜与粘附层剥离这一问题。与此相对的是,存在如下的这一大规模方法:用罩覆盖以使用圆盘状上刃和下刃的剪切切割方式对层叠膜进行切缝的装置整体,抑制层叠膜从被切缝到被缠绕的温度变动(专利文献2)。依据该方法,被认为是能够将层叠膜切缝成带宽0.5mm-4mm的细宽度。
另一方面,在使用上刃和下刃的剪切切割方式中,由于上刃和下刃的接触而产生的微小的刀刃的磨耗粉末有可能附着于切缝后的带。与此相对的是,不产生那样的磨耗粉末,而且,作为能够缓和为了得到完全切断面而需要的刃具的加工精度的切缝方式,在使用带刀辊和砧辊的刻划切割(score cut)方式中,存在将切缝的膜与承载膜(垫底材料)一起切缝的方法(专利文献3)。
在先技术文献
专利文献
专利文献1:日本特开2012-232392号公报
专利文献2:日本特开2007-90461号公报
专利文献3:日本特开2003-285293号公报。
技术实现要素:
发明要解决的课题
依据专利文献2所记载的方法,被认为是得到将层叠膜切缝成宽度0.5mm的细宽度的带,但未进行用于以0.5mm以下的细宽度对长尺寸进行切缝的详细探讨。另外,膜越是成为细宽度,专利文献2所记载的基材与粘附层剥离的问题就越是容易发生。因此,对于宽度0.5mm以下的细宽度的带,顾虑制品的合格品率的下降等。
依据专利文献3的记载,能够使用刃角70°的带刀辊来将聚酯膜切缝成宽度2mm。然而,根据专利文献3所记载的方法,如果欲将粘附层可剥离地层叠于基材膜的层叠膜切缝成带宽0.5mm以下,则带刀辊中的刀刃的间距变窄,由此,切缝的层叠膜的刀刃的侵入侧的面与其相反侧的面相比而沿切缝宽度方向强力地压缩,也产生粘附层的剥除或挤出的问题。
与此相对的是,本发明将下者作为课题:在基材膜与粘附层不剥离的情况下,在根本不发生粘附层的挤出的切口处,将粘附层可剥离地层叠于基材膜的层叠膜切缝成带宽0.5mm以下,特别地不到0.5mm。
用于解决课题的方案
本发明者想到下者而使本发明完成:在使用带刀辊和砧辊的刻划切割方式的切缝装置中,使用承载膜,而且,如果使带刀辊的切缝刀成为特定刃角,则即使使得带刀辊中的切缝刀的间距成为0.5mm以下,特别地不到0.5mm,也能够在基材膜与粘附层不剥离的情况下对粘附层可剥离地层叠于基材膜的层叠膜进行切缝,也能够抑制粘附层从切缝的带挤出。
即,本发明提供一种切缝装置,该切缝装置是具备多条圆盘状切缝刀以既定间距设置的带刀辊和砧辊并以刻划切割方式对膜进行切缝的切缝装置,具有使承载膜介于切缝的膜与砧辊之间的承载膜搬送机构,
切缝刀的刃角是30°以下,
切缝刀的间距是0.5mm以下。
另外,本发明提供一种切缝方法,该切缝方法是使层叠膜成为带刀辊侧而使粘附层可剥离地层叠于基材膜的层叠膜和承载膜在多条圆盘状切缝刀以既定间距设置的带刀辊与砧辊之间重复穿过并对层叠膜进行切缝的刻划切割方式的切缝方法,
使切缝刀的刃角成为30°以下,
使切缝刀的间距成为0.5mm以下。
而且,本发明提供利用上述的切缝方法来对粘附层可剥离地层叠于基材膜的层叠膜进行切缝而得到的层叠带。另外,提供如下的层叠带:是粘附层可剥离地层叠于基材膜的层叠带,带宽是0.5mm以下,在将长度1m的该层叠带的一端固定并将1N的张力施加至另一端的情况下,基材膜和粘附层不剥离。
发明的效果
如果使用本发明的切缝装置来通过本发明的切缝方法对粘附层可剥离地层叠于基材膜的层叠膜进行切缝,则能够在基材膜和粘附层不剥离的情况下得到宽度0.5mm以下,特别地宽度不到0.5mm的层叠带。即使从该层叠带任意地切除长度1m的带,将该带的一端固定,将0.5N,优选为1N,更优选为5N的张力施加至另一端,基材膜和粘附层也不剥离。因此,即使将该层叠带卷绕于卷轴并作为卷绕安装体,从卷绕安装体拉出而使用,由于缠绕时或拉出时的张力而导致基材膜和粘附层也不剥离。而且,在该层叠带的卷绕安装体中,也不发生粘附层的挤出。因此,能够防止在作为卷绕安装体的情况下产生阻塞。因而,该层叠带作为将粘附层粘贴于物品的细宽度的粘附材料变得有用,如果由固化性树脂组合物形成粘附层,则也作为粘接材料变得有用。
附图说明
图1是实施例的切缝装置的概略立体图。
图2是对层叠膜进行切缝的切缝装置的切缝刀(切削刀)的排列区域附近的侧视图。
图3A是表示实施例的装置的带刀辊与砧辊的组装构造的截面图。
图3B是表示带刀辊与砧辊的组装构造的变形方式的截面图。
图3C是表示带刀辊与砧辊的组装构造的变形方式的截面图。
图4是在利用实施例的装置的切缝刀来对层叠膜进行切缝时的切缝刀部分的放大截面图。
图5是在对层叠膜彼此由连结带沿长度方向接在一起的层叠膜进行切缝时的切缝刀部分的放大截面图。
图6是在利用刃角70°的切缝刀来对层叠膜进行切缝时的切缝刀部分的放大截面图。
具体实施方式
以下,参照附图并同时详细地说明本发明。此外,在各图中,同一符号表示同一构成元件或同等的构成元件。
<切缝装置的整体构成>
图1是本发明的一个实施例的切缝装置1的概略立体图,图2是在由切缝装置1对膜3进行切缝时的切缝刀的排列区域附近的侧视图。
如图2所示,该切缝装置1是具备下者并以刻划切割(score cut)方式对膜3进行切缝的装置:带刀辊10,其具有圆盘状切缝刀11以既定间距沿该辊12的旋转轴L1方向排列于圆筒状辊12的区域13;和圆筒状砧辊20。由于相对于在剪切切割方式中,上刃与下刃接触,依据刻划切割方式,刀刃彼此不接触,因而能够将刀刃的寿命延长。
在切缝装置1,作为使切缝的膜3穿过带刀辊10与砧辊20之间的搬送机构,设有膜退绕装置2和缠绕装置(未图示)。作为缠绕装置,能够分别具有将偶数列的带3a缠绕的缠绕装置和将奇数列的带3b缠绕的缠绕装置,以便对膜进行切缝而得到的多列带中的邻接的带在互相不同的方向上缠绕。此外,在图1中记载为,偶数列的带3a在上方缠绕,奇数列的带3b在下方缠绕,但也可以是,偶数列的带在下方缠绕,奇数列的带在上方缠绕。
在切缝装置1,作为使承载膜4介于切缝的膜3与砧辊20之间的承载膜搬送机构,设有承载膜缠绕部(未图示),承载膜缠绕部将承载膜退绕装置5、使承载膜4与膜3叠合的一对层压辊6、切缝后的膜的端部(膜耳)以及承载膜4一并缠绕。
关于该切缝装置1,如后所述,切缝的膜3不仅单层树脂膜,或多层树脂层粘接或熔敷的层叠膜,而且粘附层32可剥离地层叠于基材膜31的层叠膜30(图4)也能够切缝成宽度0.5mm以下,特别地宽度不到0.5mm。
<切缝刀>
出于使切缝方向稳定的点,设于带刀辊10的切缝刀11优选为双刃。如果使切缝刀成为单刃(即,如果将形成刀尖的2个刃面的一个作为平坦面,将另一个作为刀棱面),则在切缝时施加至切缝刀的膜宽方向的力在刀棱面上比平坦面更大,膜沿刀棱侧方向弯曲并被搬送,因而产生扩大切缝的膜的宽度方向的裕度的需要,膜端部的废弃量也变多。与此相对的是,通过作为双刃,在切缝时施加至切缝刀的膜宽方向的力在刀刃的两个侧面上相等,因而能够防止膜的搬送方向弯曲,还能够使膜端部的废弃量减少。
出于能够在基材膜和粘附层不剥离的情况下将在基材膜可剥离地设有粘附层的层叠膜切缝成宽度0.5mm以下,特别地宽度不到0.5mm的细宽度的点,切缝刀11的刃角α优选为30°以下,特别地25°以下。另一方面,出于切缝刀的耐久性的点,刃角α优选为10°以上。
切缝刀11的间距p根据对膜3进行切缝而得到的带所需要的带宽而确定,但在本发明中,为了能够与细宽度的带对应,关于上限,还能够为0.5mm以下,特别地不到0.5mm,进而0.4mm以下。关于下限,优选为0.1mm以上。
出于使切缝精度稳定的点,切缝刀11的切缝刀的刃高h优选为高的高度,对于下限,优选为0.05mm以上,更优选为0.1mm以上,进一步优选为0.24mm以上。另一方面,出于切缝刀的耐久性的点,切缝刀的刃高h优选为低的高度,对于上限,优选为0.8mm以下,更优选为0.7mm以下,进一步优选为0.5mm以下。
在如专利文献3所记载的那样,如果使切缝刀的刃角α成为70°,则使间距成为0.5mm以下的情况下,如果对粘附层可剥离地层叠于基材膜上的层叠膜进行切缝,则即使如图6所示,层叠膜30在基材膜31上依次设有粘附层32和覆盖膜33,粘附层32是不露出于膜表面的层,层叠膜30中的切缝刀11的侵入侧的面也与其相反侧的面相比而沿切缝宽度方向受到强压缩力F。因此,在切缝后的带中,基材膜31或覆盖膜33从粘附层32剥离,或产生以下等问题:粘附层32从带的侧面挤出,如果使带成为卷绕安装体,则产生阻塞。与此相对的是,在本发明中,由于将切缝刀11的刃角减小为30°以下,因而即使使得切缝刀11的间距成为0.5mm以下,特别地0.1mm以上且0.4mm以下,也减轻如图4所示地施加至切缝刀11的侵入侧的面的压缩力F,能够将粘附层32可剥离地层叠于基材膜31上的层叠膜30在不产生它们的剥离的情况下切缝,另外,能够抑制粘附层32从带的侧面挤出。由于在宽度细的带中,与宽度宽的带相比,在每单位带横截面面积施加的切缝宽度方向的力相对地大,因而变得容易发生粘附层的挤出。因此,粘附层32的挤出抑制可以说是,如果带宽变窄,则难易程度变高。
作为具有切缝刀11以上述的刃角α和间距p排列的区域13的带刀辊10,能够使用如图2所示地通过金属辊的切削加工来得到的切削刀或使刃角α的圆刀沿旋转轴方向叠合的组合刀等。其中,图2所示的切削刀能够通过将易切削合金层设于碳素钢等高强度且耐久性高的辊12的表面并由使用金刚石工具的精密切削加工装置等对该易切削合金层进行切削加工来得到。另外,组合刀通过能够利用切削加工来形成各个切缝刀11并使切缝刀以既定间距组合来得到。切缝刀的构成是,刃角30°为以下,间距为0.5mm以下,优选为不到0.5mm,更优选为0.4mm以下,只要得到本发明的效果,就未特别地限定。
作为形成切缝刀的易切削性合金(即,被削性优良的合金),能够使用镍磷合金、硬质铜合金、工具钢、超硬合金等。出于易切削性合金的耐久性的点,优选为威氏硬度是475以上的合金,更优选为500以上,进一步优选为550以上,特别地优选为1400以上。
<带刀辊和砧辊的组装>
在切缝装置1中,如图3A所示,带刀辊10和砧辊20分别由轴承15、25支撑,以旋转轴L1、L2变得平行的方式配置。只要旋转轴L1、L2是平行的,旋转轴L1、L2的方向就也可以是水平的,也可以是铅垂的。出于使层叠膜30的行进稳定的点,优选使旋转轴L1、L2的方向成为水平并将带刀辊10配置于砧辊20上。另一方面,出于异物难以附着于层叠膜30的点,优选使旋转轴L1、L2的方向成为铅垂方向。
带刀辊10和砧辊20由齿轮16、26连结,设有使这些辊沿图1的箭头方向旋转的驱动机构。另一方面,也可以设置使带刀辊10和砧辊20各自旋转驱动的驱动机构。
出于连续地稳定进行切缝的点,作为一个示例,切缝刀11向承载膜4切入的量d2(图2)优选为10-100μm,更优选为10-50μm,进一步优选为10-20μm。优选在切缝装置1设置如下的调整机构:使带刀辊10的安装位置相对于砧辊20活动,以便能够根据承载膜4的厚度而调整切入量d2。作为该调整机构,能够设置通过调整螺钉18使带刀辊10沿着导向部17移动的线性导向机构等。
另一方面,在使用一定膜厚的承载膜的情况下,如图3B所示,也可以将比切缝刀11的刀尖更向砧辊20侧突出的大直径部分14设于带刀辊10,将该大直径部分14推压至砧辊20。将该大直径部分14推压至砧辊20的推力能够成为800N左右。如果过度地增大该推力,则在带刀辊10中产生挠曲的问题。另外,如图3C所示,也可以使通过利用切断、切削、研磨来将工具钢、超硬合金等精加工成圆形的厚度0.5mm以下的圆刀组合并由螺栓19固定此圆刀而构成组合刀,由组合刀形成切缝刀的排列区域13。关于图3C所示的方式,也与图3A所示的方式同样地,砧辊20和带刀辊10的安装位置由调整螺钉18调整,因而不需要用于将带刀辊10推压至砧辊20的推力。
<切缝方法>
本发明的切缝方法是使粘附层32可剥离地层叠于基材膜31的层叠膜30在上述的带刀辊10与砧辊20之间穿过并对层叠膜30进行切缝的方法,是如下的方法:使层叠膜30成为带刀辊10侧,使承载膜4成为砧辊20侧,重复穿过层叠膜30和承载膜4,由此以刻划切割方式对层叠膜30进行切缝(图1、图4)。如后所述,在层叠膜30由基材膜31、粘附层32、覆盖膜33组成的情况下,如图4所示,一般将层叠膜30的基材膜31作为带刀辊10侧,将覆盖膜33作为承载膜4侧。在该情况下,将覆盖膜33和承载膜4粘接而进行切缝,在切缝后将覆盖膜33和承载膜4一并从粘附层32剥离。另一方面,也可以将层叠膜30的覆盖膜33作为带刀辊10侧并将基材膜31作为承载膜4侧而进行切缝。
由于利用该切缝来对承载膜4进行半切割,但以既定间距对层叠膜30进行贯通切割,因而分别由缠绕装置将偶数列的带3a和奇数列的带3b缠绕,以便将通过对层叠膜30进行贯通切割来得到的多列带中的邻接的带在互相不同的方向上缠绕。
此外,切缝后的层叠膜30的端部(层叠膜的耳)3c和被半切割的承载膜4一并缠绕。另外,也可以将覆盖膜33与承载膜4一起缠绕。
由切缝刀11向承载膜4切入的量d2如前所述地优选为10μm以上且100μm以下。另外,相对于刃高h,被切缝物(层叠膜30和承载膜4)的合计厚度优选为90%以下,例如,在刃高为300μm时,被切缝物的合计厚度优选为270μm以下(图2)。更优选为,使被切缝物的合计厚度相对于刃高h成为70%以下,进一步优选为50%以下。
此外,切缝优选在洁净室中进行,不需要为了抑制环境温度的变动而设置覆盖切缝装置整体的罩,但也可以设置该罩。
<层叠膜>
作为利用本发明的切缝方法来进行切缝的层叠膜30,例如,如图4所示,能够列举厚度12-75μm(特别地,25-75μm)的基材膜31、厚度5-40μm(特别地,5-25μm)的粘附层32、厚度比基材膜更薄或厚度10-50μm的覆盖膜33依次可剥离地层叠的层叠膜。在此,可剥离指的是,通过将赛璐玢带黏贴于基材膜31或覆盖膜33并剥除或利用膜用镊子(以下,镊子)来将基材膜31或覆盖膜33的端捏住并剥除,能够容易地将基材膜31或覆盖膜33从粘附层32剥离。
如图4所示,在切缝时,也可以将基材膜31配置于切缝刀11的侵入侧,也可以将覆盖膜33配置于切缝刀11的侵入侧。
此外,取决于对层叠膜进行切缝而得到的层叠带的用途,也可以并非在层叠膜30设有覆盖膜33。由于如果使承载膜4叠合于层叠膜30,则膜整体的刚性变高,因而即使不存在覆盖膜33,在刚刚切缝之后,粘附层32粘贴于切缝刀11,由此也能够排除粘附层32从基材膜31剥除的情况。另一方面,出于防止层叠带污染的点,优选为存在覆盖膜33,特别地,在得到宽度窄的层叠带的情况下,优选为存在覆盖膜33。作为卷绕安装体(其是最终用作粘接材料的方式),为了防止污染,也可以具有覆盖膜,为了提高操作性,也可以不具有覆盖膜。
(基材膜、覆盖膜)
基材膜31能够列举由聚乙烯、聚丙烯、PET等聚酯等热塑性树脂形成的膜。覆盖膜33为了防止粘附层32被污染而设置,能够由与基材膜31同样的材料形成。基材膜31或覆盖膜33的表面优选被进行剥离处理。因为,能够与粘附层分离。为了在切缝后首先使覆盖膜剥除,优选使用在覆盖膜33中比基材膜31更容易剥离的材料。
在本发明中,对刚性较低的粘附层32和刚性较高的基材膜31同时进行切缝且在切缝时不分离,在使用切缝后的层叠带时,能够将粘附层32和基材膜31剥离。在此,由于聚乙烯、聚丙烯、PET等聚酯的拉伸弹性模量是大约1100-4200MPa,因而将由这样的热塑性树脂形成的膜和刚性与膜不同的粘附层32同时切缝成宽度0.5mm以下的细宽度,而且,在切缝时抑制膜与粘附层的分离或剥离是难易程度高的技术,但依据本发明,能够进行这样的切缝。
(粘附层)
作为粘附层32,也可以层叠有粘附膜,也可以层叠有粘附剂的涂膜。根据对层叠膜30进行切缝而得到的带的用途,粘附层32也可以由单一树脂层构成,也可以由多个树脂层的层叠体或多层体构成。另外,在粘附层32中,也可以根据需要而含有填料。
(粘附层的填料)
在致使在粘附层中含有填料的情况下,根据对层叠膜30进行切缝而得到的带的用途,该填料根据用途而从众所周知的无机类填料(金属、金属氧化物、金属氮化物等)、有机类填料(树脂、橡胶等)、有机类材料与无机类材料混在一起的填料等适当选择。例如,在光学用途或消光用途中,能够使用二氧化硅填料、氧化钛填料、苯乙烯填料、丙烯填料、三聚氰胺填料或各种钛酸盐等。在聚光镜(condenser)用膜的用途中,能够使用氧化钛、钛酸镁、钛酸锌、钛酸铋、氧化镧、钛酸钙、钛酸锶、钛酸钡、钛酸锆酸钡、钛酸锆酸铅和这些材料的混合物等。在作为粘接材料的用途中,能够致使含有聚合物类橡胶粒子、硅树脂橡胶粒子等。在电子零件的封装的用途中,填料也可以具有导电性,也可以具有绝缘性。在填料具有绝缘性的情况下,能够将例如填料用作间隔物。
填料的粒径能够根据对层叠膜30进行切缝来得到的带的用途而确定。例如,在将该带用于电子零件的封装的情况下,填料的粒径优选为1μm以上,更优选为2.5μm以上且30μm以下。
在此,粒径意味着平均粒径。平均粒径能够从层叠膜30的粘附层32的俯视图像或截面图像求出。另外,作为致使在层叠膜30的粘附层32中含有填料之前的原料粒子的填料的平均粒径能够使用湿式流动式粒径/形状分析装置FPIA-3000(马尔文(Malvern)公司)来求出。N数是1000以上,优选为2000以上,更优选为5000以上。另一方面,在填料中,也可以包括粒径不到1μm的填料。作为粒径不到1μm的填料(所谓的纳米填料),能够列举粘度调整用填充剂等。该大小能够通过电子显微镜(TEM、SEM)的观察来求出。N数优选为200以上。
作为填料,也可以包括如量子点那样具有功能性的填料。作为这样的填料的大小,未特别地限定,但优选为2nm以上,更优选为10nm以上。该大小也能够通过电子显微镜(TEM、SEM)的观察来求出。N数优选为200以上。
在本发明中,只要事先未特别告知,以下所叙述的填料就指前述的粒径1μm以上的填料。即,用作表面改性剂或填充剂的纳米填料被排除。
在粘附层中,填料也可以在树脂中混炼并随机地分散,也可以在俯视下各自不接触,也可以成为在俯视下重复进行既定排列的有规律的配置。填料的个数密度在不影响到膜的切缝的范围内适当调整,在面的视野中,能够作为例如30-100000个/mm 2。该个数密度优选以如下的方式计量:在俯视下使用光学显微镜或金属显微镜来观察粘附层中的填料,使10处以上的区域成为合计2mm 2以上,填料数合计成为200以上。
(形成粘附层的树脂组合物)
另一方面,形成粘附层32的树脂组合物根据对层叠膜30进行切缝而得到的带的用途、填料的有无等而适当选择表现出粘附性或粘接性的填料,能够由热塑性树脂组合物、高粘度粘附性树脂组合物或固化性树脂组合物等形成。例如,在作为将带用于电子零件的封装等的粘接材料的情况下,与形成WO2018/074318A1公报所记载的绝缘性树脂层的树脂组合物同样地,能够将形成粘附层的树脂组合物作为含有聚合性化合物和聚合引发剂的固化性树脂组合物。也可以是不含有固化性树脂组合物的所谓的热熔型粘接材料。
作为固化性树脂组合物的聚合引发剂,也可以使用热聚合引发剂,也可以使用光聚合引发剂,也可以将它们并用。例如,作为热聚合引发剂,使用热阳离子类聚合引发剂,作为热聚合性化合物,使用环氧树脂,作为光聚合引发剂,使用光游离基聚合引发剂,作为光聚合性化合物,使用丙烯酸酯化合物。作为热聚合引发剂,也可以使用热阴离子类聚合引发剂。作为热阴离子类聚合引发剂,优选使用将咪唑变性体作为核并以聚氨酯遮盖其表面而成的微胶囊型潜伏性固化剂。
作为由这样的绝缘性树脂组合物形成的粘附层整体的最低溶融粘度未特别地限制,但出于膜形成的点,能够作为100Pa·s以上,为了抑制在将粘附层32热压接于物品时的填料的无用的流动,优选为1500Pa·s以上。另一方面,对于最低溶融粘度的上限,未特别地限制,但作为一个示例,优选为15000Pa·s以下,更优选为10000Pa·s以下。作为一个示例,该最低溶融粘度能够使用旋转式流变仪(TA instrument(TA仪器)公司制)并使用以测定压力5g保持一定且直径8mm的测定板来求出,更具体而言,能够通过在温度范围30-200℃内作为升温速度10℃/分钟、测定频率10Hz、针对前述测定板的负荷变动5g来求出。此外,最低溶融粘度的调整能够通过作为溶融粘度调整剂而含有的微小固态物质的种类或配合量、树脂组合物的调整条件的变更等来进行。
(粘附层的粘附力)
·可剥离性
粘附层32对基材膜31和覆盖膜33的粘附力比在依照该带的用途而将粘附层32贴附于既定物品的情况下的粘附层32的粘附力更弱,基材膜31和覆盖膜33能够从粘附层32剥离。通常,在将覆盖膜33剥离之后,将粘附层32粘贴于物品并评价基材膜31的可剥离性。基材膜31和覆盖膜33能够从粘附层32剥离指的是,如前所述,通过将赛璐玢带黏贴于基材膜31或覆盖膜33并剥除,或通过用镊子将基材膜31或覆盖膜33的端捏住并剥除,能够容易地将这些膜从粘附层32剥离,但作为该具体指标,在将切缝前的层叠膜切割成宽度5cm、长度15cm且作为剥离试验而进行T型剥离试验(JIS K 6854)的情况下,列举粘接强度为0.005-0.2N。取决于基材膜31的材质或厚度等,也可以通过180°剥离试验或90°剥离试验来评价。一般使用赛璐玢带来先将覆盖膜33从基材膜31和粘附层32剥除,在将粘附层32粘贴于物品之后,用镊子将基材膜31剥除。
·稳定性
另一方面,在将层叠膜30切缝成带并利用缠绕装置来将带缠绕成卷轴而作为卷绕安装体时,或当在将成为卷绕安装体的带用作粘接材料时将卷绕安装体装配于连接装置并将带从卷绕安装体拉出的时候,拉力(张力)沿带的长度方向施加至带。于是,在这样的拉力施加至带的情况下,优选的是,基材膜31和粘附层32不剥离。即,以往,在连接装置中,卷绕安装体所要求的带长通常为5m以上,优选为10m以上,在将带从卷绕安装体拉出时沿带的长度方向施加的拉力一般是1N-5N左右。而且,在连接装置的运转中发生不良状况的情况下,有时候对卷轴施加锁定,5-6N的拉力施加至带。因此,有必要设想5N左右的负荷施加至带。于是,优选在该拉力下维持基材膜与粘附层的贴附状态或卷轴与基材膜的连接(超声波熔敷或从卷轴伸出的引线与基材膜的通过硅带等粘接膜进行的连接)。
然而,在使带成为细宽度的情况下,取决于情况,顾虑的是,如果将先前的拉力施加至带,则基材膜断裂,或基材膜与粘附层剥离。于是,在尽可能地有效利用原有的设备来进行细宽度的带的缠绕或拉出的情况下沿带的长度方向施加的拉力为0.5N左右即可,优选为不到1N。对于上限,更优选为0.7N以下,进一步优选为0.3N以下。
出于能够进行这样的缠绕或拉出的在实际使用方面的请求,对于粘附层32,在沿长度方向将0.5N以上,优选为1N,更优选为5N的张力施加至利用本发明的方法来切缝成宽度0.1mm以上且0.5mm以下的层叠带的长度1m以上,优选为5m以上的粘附层32的情况下,要求基材膜31和覆盖膜33不从粘附层32剥离这一稳定性。此外,前述的可剥离性是与粘附层32对基材膜31和覆盖膜33的粘附力的上限有关的性质,但该稳定性是与粘附力的下限有关的性质。
稳定性试验优选简易地进行。于是,作为试验方法,能够列举如下的试验:使层叠带的试验长度成为1m,将裁断成长度1m的层叠带的一端固定,在另一端负荷0.5N,优选为1N,更优选为5N,观察基材膜31与粘附层32的剥离的有无。另外,作为更实用的试验方法,能够列举如下的试验:将带从卷绕安装体拉出1m以上,在带的端部负荷0.3N、0.5N、1N或5N,观察剥离的有无。另外,也可以将带的全长从卷绕安装体拉出并在任意的20处以上,优选为50处以上观察剥离的有无。在这样的试验中,作为在实际使用方面需要的粘附力的指标的一个示例,能够列举:(i)在利用本发明的方法来将层叠膜切缝成宽度0.1mm以上且0.5mm以下的层叠带,将覆盖膜剥除并作为粘附层与基材膜的带的卷绕安装体,将带从卷绕安装体拉出长度1m并将卷轴的卷芯与带的连结位置固定,将连结位置角α(日本特开2017-137188号公报)作为90°并通过对带端部的静负荷的负荷来施加0.3N,优选0.5N,更优选1N,进一步优选5N的拉力的情况下,基材膜不从粘附层剥离,另外,不发生影响到拉出的程度的挤出;(ii)在利用本发明的方法来将层叠膜从切缝成宽度0.1mm以上且0.5mm以下的层叠带任意地切除的试验长度1m的试验片中,在沿该试验片的长度方向施加0.5N,优选1N,更优选5N的张力的情况下,基材膜31不从粘附层32剥离;(iii)在用手将带全部从以0.5N将粘附层和基材膜的带缠在卷芯达5m以上的卷绕安装体拉出的情况下,并非遍及带的全长通过目视确认粘附层与基材膜的剥除(详细情况在后述的实施例中记载)。出于简易地进行试验的点,优选为(iii)的方法。在裁断成试验长度1m左右并用手在两端施加负荷(大约1N-5N左右)的情况下,也可以确认不发生基材膜与粘附层的剥离。
如果层叠带具有上述的粘附力,则将该层叠带卷绕于优选为长度5m以上,10m以上,50m以上,进而长度100m以上的卷绕安装体,即使在将带从该卷绕安装体拉出优选1m以上,更优选5m以上的情况下,在拉出的带中,基材膜31也能够不从粘附层32剥离,能够将该带用于电子零件的封装。
·对连接对象物的粘附力
另一方面,作为出于对电子零件、基板等的连接对象物的粘附力这一观点而对粘附层要求的粘附力的试验方法,能够列举如下的方法:进行将从层叠带任意地采取的长度2cm的小片(也可以是将上述的(ii)的1m的层叠带的试验片裁断的小片)从粘附层侧暂时黏贴(例如在45℃下粘贴)于未加工玻璃并用镊子仅将基材膜31(或覆盖膜33)的端捏住并去除的剥离试验,在该剥离试验中,能够仅将基材膜31(或覆盖膜33)去除,将粘附层能够依然形状不变化地贴附于未加工玻璃的情况作为成功。在该剥离试验中,N数为20以上且75%以上的成功是优选的,80%以上的成功是更优选的,90%以上的成功是进一步优选的。
(连结带的贴附)
为了在层叠膜30安装当卷绕安装体开始卷绕或退绕时的引线,或为了将第一层叠膜和第二层叠膜贴合而长尺寸化,也可以在层叠膜30贴附连结带。连结部位能够有规律地或随机地成为多个部位。另外,在层叠膜和引线的安装中,能够由连结带使层叠膜30的基材膜31和引线连结在一起。将层叠膜安装到引线也可以是超声波熔敷等众所周知的方法。
作为连结带,能够使用剥离性高且总厚度较薄的带有基材的粘附带(例如,硅带)。连结带的厚度未特别地限制,但作为一个示例,列举5-75μm。
当对在层叠膜30贴附有连结带的部分进行切缝时,如图5所示,切缝刀11深深地进入至层叠膜30和连结带35的层叠体。因此,依据先前的切缝装置,关于切缝刀11的侵入侧的层叠体的面,邻接的刀刃彼此的间隔显著地变窄,相对于其相反侧的面从切缝刀11的侧面受到强压缩力F,覆盖膜33或基材膜31与粘附层32变得容易剥离,或粘附层32变得容易从切缝的层叠体的侧面挤出。与此相对的是,依据本发明,即使在层叠膜30贴附有连结带35,也能够抑制产生这样的剥离或挤出。
<层叠带>
本发明的层叠带是利用上述的切缝方法来对层叠膜30进行切缝而得到的带。因此,该带是粘附层可剥离地层叠于基材膜的层叠带,对于带宽的上限,为0.5mm以下,特别地不到0.5mm,更优选为0.4mm以下,进一步更优选为0.3mm以下。对于下限,为0.1mm以上,优选为0.15mm以上,更优选为0.2mm以上。
该层叠带具有如下的这一特征:在以成为从该带任意地切除的试验长度1m的方式将试验片的一端固定并将0.3N、0.5N或1N的张力施加至另一端的情况下,基材膜与粘附层不剥离,另外,在卷绕安装体中,不发生粘附层32的挤出。另外,在将该带切成长度2cm的小片并将粘附层32黏贴于未加工玻璃且用镊子仅将基材膜31的端捏住并去除的情况下,该层叠带满足粘附层难以从未加工玻璃剥离的这一在实际使用方面的请求,能够进行所谓的贴附或转附。
出于处置性的点,优选为将该带卷绕于卷轴的卷绕安装体。出于在实际使用方面的点,卷绕安装体中的带长优选为5m以上且5000m以下,更优选为50m以上且1000m以下,进一步优选为500m以下。一般而言,如果带宽成为细宽度,则在卷绕安装体中,变得容易产生阻塞,但依据本发明的层叠带,难以在卷绕安装体中产生阻塞,即使将带从卷绕安装体拉出5m以上,在拉出的带中,也不在基材膜31或覆盖膜33与粘附层32之间产生剥离。
此外,一般而言,有时在成为对层叠膜进行切缝而得到的层叠带的切缝的切口的端部在目视下产生浮起(变色部分)。如果带宽为0.5mm以下而成为细宽度,则层叠带的两端的浮起很有可能成为致使产生基材膜与粘附层的无用的剥离的主要原因。然而,依据本发明,由于利用尖锐双刃来对层叠膜进行切缝,因而即使通过目视观察来从形成卷绕安装体的带全长任意地在20处以上,优选50处以上调查浮起的有无,也难以观察到浮起。即使在沿着层叠带的切缝的切口的端部观察到浮起的情况下,浮起也为长度不到5cm,宽度相对于带宽为40%以下,特别地为1/3以下,能够抑制基材膜与粘附层的剥离。
照此,依据本发明的层叠带,基材膜和粘附层难以偏离,难以产生阻塞或浮起,因而卷绕安装体的缠绕、拉出的操作性优良,在将从卷绕安装体拉出并切除的带粘贴于对象部件时,难以在粘贴位置产生偏离。因而,本发明的层叠带能够作为细宽度的粘附材料或粘接材料在各种用途中使用。在此情况下,构成粘附层32的树脂组合物的种类等根据粘贴带的对象部件而适当选择。
实施例
实施例1
基材膜由厚度38μm的被剥离处理的PET膜形成,粘附层由厚度10μm的丙烯类热固化性树脂(粘接性膜,迪睿合(Dexerials)制)形成,使用图2所示的切削刀来1次将覆盖膜由厚度12μm的PET膜形成的层叠膜切缝成宽度0.3mm、长度100m的带,覆盖膜剥除,将张力(缠绕拉力)0.3-0.6N施加至φ90mm的带有凸缘的卷芯(凸缘间距离0.4mm)并将基材膜和粘附层缠绕,由此作为卷绕安装体,进行以下的评价。
(1)浮起
将作为卷绕安装体的100m的带全部用手拉出,对拉出的带的任意位置处的长度10cm的试验区域20处进行目视观察,基于关于浮起的有无的以下的项目a、b、c来在以下的基准下评价。
a:不存在长度5cm以上的浮起
b:不存在宽度超过带宽的1/3的浮起
c:长度不到5cm的浮起或宽度为带宽的1/3以下的浮起的存在部位是5处以下
评价A:满足abc全部的情况
评价B:同时满足ab的情况
评价C:除了上述的评价A和评价B以外
该评价结果是评价A。此外,在实际使用方面,如果满足评价B,则不存在问题,进一步优选满足c。
(2)剥离
在上述试验中,在进行浮起的目视观察的部位和除此以外的30处的共计50处,确认不发生剥离。在试验中,将全长拉出并同时进行目视观察,但大体上不发生剥离。
另外,不发生给操作性带来障碍的粘附层的挤出,也不能确认粘附层附着到凸缘。
此外,上述的(1)、(2)的结果不限定于由切削刀进行的切缝。
符号说明
1 切缝装置
2 膜退绕装置
3 膜
4 承载膜
5 承载膜退绕装置
6 层压辊
10 带刀辊
11 切缝刀、圆刀
12 辊
13 区域
14 大直径部分
15 轴承
16 齿轮
17 导向部
18 调整螺钉
19 螺栓
20 砧辊
25 轴承
26 齿轮
30 层叠膜
31 基材膜
32 粘附层
33 覆盖膜
35 连结带
α 切缝刀的刃角
d1 切缝刀的刀尖与砧辊的间隙
d2 切缝刀向承载膜切入的量
F 压缩力
h 切缝刀的刃高
L1、L2 旋转轴
p 切缝刀的间距。
本文用于企业家、创业者技术爱好者查询,结果仅供参考。