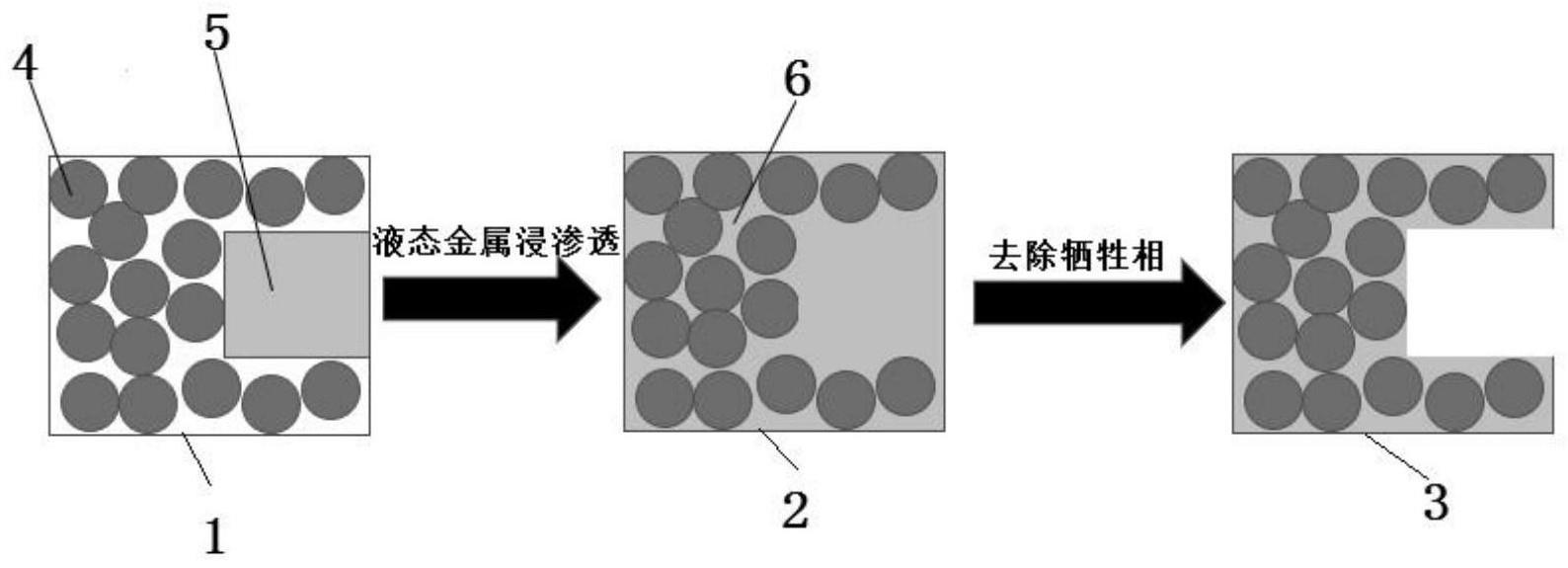
1.本发明涉及异形金属基复合材料技术领域,具体涉及一种基于直写成型技术制备异形金属基复合材料预制体、制备方法及其应用。
背景技术:
2.金属基复合材料(metalmatrixcomposites,简称mmcs),是以金属或合金材料作为基体,以不同材料的颗粒或者纤维作为增强相的复合材料【shangm,lingm.mechanicalpropertiesanalysisand applicationofmetalmatrixcomposites[j].appliedmechanicsand materials,2014,599-601:63-6.】,综合了金属基体与增强相的特性,具有高耐热、强耐磨、低密度和高强度等优异性能,广泛应用于航空航天【崔岩.碳化硅颗粒增强铝基复合材料的航空航天应用[j].材料工程,2002,(06):3-6.】、交通运输【chawlak.metal-matrixcomposites ingroundtransportation[j].jom,2006,58:67-70.】以及国防军工【胥锴,刘政,刘萍.金属基复合材料的发展及其应用[j].南方金属,2005,(06):1-6.】等领域。金属基复合材料的传统制备方法有粉末冶金法【satishj,satishkg.preparationofmagnesiummetalmatrix compositesbypowdermetallurgyprocess[j].iopconferenceseries:materialsscienceandengineering,2018,310(1):012130.】、铸造法【hashimj,looneyl,hashmimsj.metalmatrixcomposites:productionbythestircastingmethod[j].journalofmaterialsprocessing technology,1999,92-93:1-7.】、原位反应合成法【royd,ghoshs,basumallicka,etal.preparationoffe-aluminidereinforcedinsitu metalmatrixcompositesbyreactivehotpressing[j].materialsscience andengineering:a,2006,415(1):202-6.】、喷射成型法【sunyp,yan hg,sub,etal.microstructureandmechanicalpropertiesofspray depositional/sicpcompositeafterhotextrusion[j].journalof materialsengineeringandperformance,2011,20(9):1697-702.】以及液态浸渗法【刘文娜,王晓东,余欢,等.高体分sicp/mg复合材料真空压力浸渗制备工艺与微观形貌[j].金属加工(热加工),2010,no.616(13):30-2.】等,这些制备方法得到的金属基复合材料多为块状,难以直接获取复杂形状的构件。传统制备方法获得的金属基复合材料块体需要通过机加工才能形成复杂异形结构金属基复合材料构件,但由于金属基复合材料具有较强耐磨性,它的机加工面临着刀具易磨损,甚至因而影响加工质量的难题。
[0003]
液态浸渗法制备金属基复合材料过程如图1【秦振凯.无压浸渗制备双尺寸颗粒sicp/al电子封装材料的研究[d];西北工业大学,2005.】所示。使用该方法制备金属基复合材料的一个关键因素是预制体的制备。预制体的传统制备方法有有机泡沫浸渍-高温处理法、添加剂法、溶胶-凝胶法、固相烧结法和生物模板法等【王琼.基于3d打印网络结构预制体的sic/al-mg复合材料制备工艺[d];兰州理工大学,2022.】。3d打印技术因能实现一些复杂形状构件的制备,正在成为金属基复合材料预制体制备的新兴热点。直写成型技术作为3d打印技术中的一种,因具有步骤简单【gaddama,brazeteds,netoas,etal.robocastingandsurfacefunctionalizationwithhighlybioactiveglass ofzro2scaffoldsforloadbea
ringapplications[j].journalofthe americanceramicsociety,2022,105(3):1753-64.】和制料方便【cepollaroem,bottir,franching,etal.cu/zsm5-geopolymer3d-printedmonolithsforthenh3-scrofnox[j].catalysts,2021,11(10):1212.】的优点而被广泛应用在各个领域。利用直写成型技术制备预制体可实现对金属基复合材料中增强相结构和分布的控制【王琼.基于3d打印网络结构预制体的sic/al-mg复合材料制备工艺[d];兰州理工大学,2022.】,但所得预制体经过液态浸渗后得到的金属基复合材料仍需通过机加工来形成复杂形状。
技术实现要素:
[0004]
鉴于目前存在的上述不足,本发明提供一种基于直写成型技术制备异形金属基复合材料预制体、制备方法及其应用,本发明采用双头直写成型技术成型牺牲相与增强相的复合结构,即复杂形状结构金属基复合材料的预制体。其中,石膏作为牺牲相,可在完成金属浸渗工艺之后除去,进而获得复杂形状的异形构件,陶瓷粉体作为增强相,保留在金属内与之复合。本发明解决了金属基复合材料传统工艺难以制备复杂异形结构金属基复合材料的难题,克服了石膏浆料因凝结时间短和泌水性大等问题而造成难以进行直写成型的困难。本发明制备的复杂异形结构金属基复合材料预制体尺度范围广、适用范围广,通过针头孔径可简单实现分米级、厘米级、毫米级、微米级的控制。
[0005]
为了达到上述目的,本发明提供一种基于直写成型技术制备异形金属基复合材料预制体的方法,包括以下步骤:
[0006]
步骤1:牺牲相浆料的制备:
[0007]
在室温下,按照一定比例将包含溶剂、缓凝剂、增稠剂、保水剂和消泡剂的辅助剂充分混合溶解后,再加入适量的石膏粉进行充分搅拌,获得石膏浆料;
[0008]
步骤2:增强相浆料的制备:
[0009]
在室温条件下,将一定量的分散剂溶于适量的水中,调节适宜的ph值后,再加入陶瓷粉末进行搅拌混合,制得增强相浆料;
[0010]
步骤3:牺牲相和增强相的直写成型:
[0011]
将石膏浆料和增强相浆料装入两个针筒内,并将其安装在双头直写成型设备的两个打印头上,基于计算机预设的预制体模型进行打印,经干燥处理后,获得复杂异性结构的金属基复合材料预制体。
[0012]
依照本发明的一个方面,在步骤1中,所述石膏浆料中粉体的固含量为0.01%~89%,所述缓凝剂的加入量为粉体质量的0.001%~30%,所述增稠剂加入量为粉体质量的0.1%~40%;所述保水剂加入量为0.01%~99%;所述消泡剂加入量为粉体质量的0.01%~99%。
[0013]
依照本发明的一个方面,所述陶瓷粉末包括碳化硅、氮化硅、氧化铝粉末中的任意一种或多种。
[0014]
依照本发明的一个方面,在步骤2中,所述增强相浆料中的粉体的固含量为0.01%~99%,所述分散剂的加入量为粉体质量的0.001%~10%,所述增稠剂和所述消泡剂的加入量均为粉体质量的0.001%~1000%。
[0015]
依照本发明的一个方面,在步骤3之前,还需对双头直写成型设备进行双头直写成
型前处理,具体为:室温下将石膏浆料和增强相浆料进行搅拌和除气处理。
[0016]
依照本发明的一个方面,在步骤3中,所述打印具体为:计算机自动控制安装在z轴上的针筒的压力,使浆体从针嘴流出,并沉积在按照程序移动的x-y轴成型平台上,从而获得第一层结构;然后,z轴精确地向上移动或旋转到结构方案确定的高度,第二层成型将在第一层结构上进行;随后,通过逐层叠加的方式,获得复杂异形结构金属基复合材料预制体。
[0017]
依照本发明的一个方面,所述干燥处理为烘房干燥或微波干燥;所述干燥处理的湿度为20%~90%,温度为小于100℃。
[0018]
基于同一发明构思,本发明还提供了上述方法制备得到的复杂异形金属基复合材料预制体。
[0019]
基于同一发明构思,本发明还提供了上述方法制备得到的复杂异形金属基复合材料预制体的应用,包括以下步骤:
[0020]
步骤1:将金属液体浸渍在复杂异性结构的金属基复合材料预制体中,经固化后,获得含牺牲相的金属基复合材料;
[0021]
步骤2:将含牺牲相的金属基复合材料浸入水中,去掉牺牲相,获得复杂异性结构的金属基复合材料。
[0022]
依照本发明的一个方面,所述金属包括al、mg、cu、fe、zn、ti等中的任意一种及其合金。
[0023]
本发明的有益效果:
[0024]
本发明的突出之处在于提出采用石膏作为牺牲相,结合碳化硅、氮化硅、氧化铝等无机材料(陶瓷材料)作为增强相,制备相应可打印浆料后,运用双头直写成型技术制备复杂异形结构金属基复合材料预制体。本发明是一种新颖、简便且低成本获得复杂异形结构金属基复合材料预制体的方法,其优点在于:
[0025]
(1)提出将增强相浆料与牺牲相浆料相结合,通过双头直写成型方式直接制备获得带牺牲相的金属基复合材料预制体;
[0026]
(2)制备金属基复合材料预制体的成本低;将调好的无机浆料按照打印路径进行出料即可;
[0027]
(3)制备金属基复合材料预制体结构可控,即牺牲相的分布可控;
[0028]
(4)所制备的包含牺牲相和增强相的金属基复合材料预制体进行烧结、金属浸渗后,将牺牲相石膏除去,即可得到具异形复杂形状的金属基复合材料;
[0029]
(5)采用本发明提出的石膏打印方式可使石膏充分进行水化反应,所获得的石膏支撑结构强度较强;
[0030]
(6)本发明制备的三维周期结构的尺度范围广,通过针头孔径可简单实现分米级、厘米级、毫米级、微米级或纳米级的控制。
附图说明
[0031]
图1为本发明背景技术所述的液态浸渗法(气压浸渗)制备金属基复合材料示意图;
[0032]
图2为本发明实施例所述的异形金属基复合材料的制备工艺流程示意图;
[0033]
图3为本发明实施例打印的不同的所述的含增强相和牺牲相的金属基复合材料预制体的示例。
[0034]
附图标记说明:
[0035]
1、含增强相和牺牲相的金属基复合材料预制体;2、含牺牲相的金属基复合材料;3、异形金属基复合材料;4、增强相颗粒;5、牺牲相;6、金属基体。
具体实施方式
[0036]
为使本发明更加容易理解,下面结合具体实施例,进一步阐述本发明。应理解,这些实施例仅用于说明本发明而不用于限制本发明的范围,显然,所描述的实施例仅仅是本发明一部分实施例,而不是全部的实施例。基于本发明中的实施例,本领域普通技术人员在没有做出创造性劳动前提下所获得的所有其他实施例,都属于本发明保护的范围。除非另有定义,下文所用专业术语和本领域专业技术人员所理解的含义一致;除非特殊说明,本文所涉及的原料、试剂均可从市场购买,或通过公知的方法制得。
[0037]
为了解决背景技术的技术问题,本发明提供一种基于直写成型技术制备异形金属基复合材料预制体的方法,包括以下步骤:
[0038]
步骤1:牺牲相浆料的制备:
[0039]
在室温下,按照一定比例将包含溶剂、缓凝剂、增稠剂、保水剂和消泡剂的辅助剂充分混合溶解后,再加入适量的石膏粉进行充分搅拌,获得石膏浆料;
[0040]
优选的,所述石膏浆料中粉体的固含量为0.01%~89%,所述缓凝剂的加入量为粉体质量的0.001%~30%,所述增稠剂加入量为粉体质量的0.1%~40%;所述保水剂加入量为0.01%~99%;所述消泡剂加入量为粉体质量的0.01%~99%。
[0041]
优选的,所述溶剂优选为水;所述缓凝剂优选为三磷聚酸钠、蛋白质类缓凝剂、柠檬酸、水杨酸中的任意一种或多种;所述增稠剂为甲基纤维素;所述保水剂为聚丙烯酸钠;所述消泡剂为月桂酸。
[0042]
步骤2:增强相浆料的制备:
[0043]
在室温条件下,将一定量的分散剂溶于适量的水中,调节适宜的ph值后,再加入陶瓷粉末进行搅拌混合,制得增强相浆料;
[0044]
优选的,所述陶瓷粉末包括碳化硅、氮化硅、氧化铝粉末中的任意一种或多种。
[0045]
优选的,ph值为10。
[0046]
优选的,调节ph值后还需要加入增稠剂。
[0047]
优选的,所述增强相浆料中的粉体的固含量为0.01%~99%,所述分散剂的加入量为粉体质量的0.001%~10%,所述增稠剂和所述消泡剂的加入量均为粉体质量的0.001%~1000%。
[0048]
步骤3:牺牲相和增强相的直写成型:
[0049]
将石膏浆料和增强相浆料装入两个针筒内,并将其安装在双头直写成型设备的两个打印头上,基于计算机预设的预制体模型进行打印,经干燥处理后,获得复杂异性结构的金属基复合材料预制体。
[0050]
优选的,在步骤3之前,还需对双头直写成型设备进行双头直写成型前处理,具体为:室温下将石膏浆料和增强相浆料进行搅拌和除气处理。需要说明的是,搅拌和除气处理
是为了保证装入针筒的浆体均质、无气泡,能够连续出料。
[0051]
优选的,搅拌处理为将针筒放置在行星搅拌仪中进行搅拌;除气处理为室温下真空除气,除气时间为1min~60min。
[0052]
优选的,所述打印具体为:计算机自动控制安装在z轴上的针筒的压力(压力范围为1~1000psi,具体视打印浆体而定),使浆体从针嘴流出,并沉积在按照程序移动(移动的速度为0.1~500mm/sec,具体视浆体而定)的x-y轴成型平台上,从而获得第一层结构;然后,z轴精确地向上移动或旋转到结构方案确定的高度,第二层成型将在第一层结构上进行;随后,通过逐层叠加的方式,获得复杂异形结构金属基复合材料预制体。
[0053]
优选的,所述干燥处理为烘房干燥或微波干燥;所述干燥处理的湿度为20%~90%,温度为小于100℃。
[0054]
本发明还公开了上述异形金属基复合材料预制体制备异形金属基复合材料,包括以下步骤:
[0055]
步骤1:将金属液体浸渍在复杂异性结构的金属基复合材料预制体中,经固化后,获得含牺牲相的金属基复合材料;
[0056]
步骤2:将含牺牲相的金属基复合材料浸入水中,去掉牺牲相(石膏),获得复杂异性结构的金属基复合材料。
[0057]
优选的,所述金属包括al、mg中的任意一种。
[0058]
本技术的原理如图2所示,将增强相颗粒4和牺牲相5通过双头直写成型含增强相和牺牲相的金属基复合材料预制体1;对含增强相和牺牲相的金属基复合材料预制体1进行金属液态浸渗,金属基体6浸渗到增强相颗粒4的间隙中,得到含牺牲相的金属基复合材料2;随后将牺牲相石膏除去,即可得到复杂异形金属基复合材料3。本技术可克服传统制备工艺难以直接制备复杂形状构件的困难,省去金属基复合材料的机加工过程,在简单工艺基础上实现复杂形状金属基复合材料构件的制备。本发明使用多头直写成型方式进行多材料3d打印,不止需要对单个浆料的流变性能做出评估,更多的是实现不同种类可打印浆料之间的剪切弹性模量以及屈服应力的相互匹配,通过浆料流变性能和打印速度、挤出压力等参数的调节实现增强相浆料与牺牲相浆料之间的打印适配性。
[0059]
下面结合具体的实施例进一步阐述。
[0060]
实施例1-4为采用不同量/种类的外加剂来制备石膏/碳化硅复杂异形结构金属基复合材料预制体。
[0061]
实施例1
[0062]
室温下,先将缓凝剂(三磷聚酸钠,0.67g)、增稠剂(甲基纤维素,0.72g)、保水剂(聚丙烯酸钠,0.22g)、消泡剂(月桂酸,0.45g)和蒸馏水(40g)进行混合并搅拌至完全溶解后加入α-半水石膏粉(100g)进行充分搅拌和去气脱泡处理获得较为均质的石膏浆体;再通过将溶解分散剂(聚丙烯酸,0.0192g)于水中,调节ph值为10后,加入碳化硅粉末(40g)进行搅拌混合获得均质分散的碳化硅悬浮液,并加入增稠剂(甲基纤维素,0.2g)获得均质的碳化硅浆体;最后将浆体装入对应针筒并进行搅拌去气处理5min。石膏浆料的挤出压力设置为35psi,移动速度设置为5mm/s,碳化硅浆料的挤出压力设置为38psi,移动速度设置为4mm/s,打印完成之后将样品进行干燥处理,置于湿度为30%,温度为60℃的条件下保温24小时,使样品完全干燥。其打印出的多个含增强相和牺牲相的金属基复合材料预制体的实
物图如图3所示。
[0063]
实施例2
[0064]
室温下,先将缓凝剂(蛋白质类缓凝剂,0.75g)、增稠剂(甲基纤维素,0.72g)、保水剂(聚丙烯酸钠,0.22g)、消泡剂(月桂酸,0.45g)和蒸馏水(42g)进行混合并搅拌至完全溶解后加入α-半水石膏粉(100g)进行充分搅拌和去气脱泡处理获得较为均质的石膏浆体;再通过将溶解分散剂(聚乙烯亚胺,0.0392g)于水中,调节ph值为10后,加入碳化硅粉末(40g)进行搅拌混合获得均质分散的碳化硅悬浮液,并加入增稠剂(甲基纤维素,0.25g)获得均质的碳化硅浆体;最后将浆体装入对应针筒并进行搅拌去气处理5min。石膏浆料的挤出压力设置为32psi,移动速度设置为3mm/s,碳化硅浆料的挤出压力设置为34psi,移动速度设置为5mm/s,打印完成之后将样品进行干燥处理,置于湿度为30%,温度为60℃的条件下保温24小时,使样品完全干燥。
[0065]
实施例3
[0066]
室温下,先将缓凝剂(柠檬酸,0.251g)、增稠剂(甲基纤维素,0.77g)、保水剂(聚丙烯酸钠,0.2g)、消泡剂(月桂酸,0.54g)和蒸馏水(42g)进行混合并搅拌至完全溶解后加入α-半水石膏粉(100g)进行充分搅拌和去气脱泡处理获得较为均质的石膏浆体;再通过将溶解分散剂(聚丙烯酸,0.02g)于水中,调节ph值为10后,加入碳化硅粉末(50g)进行搅拌混合获得均质分散的碳化硅悬浮液,并加入增稠剂(甲基纤维素,0.3g)获得均质的碳化硅浆体;最后将浆体装入对应针筒并进行搅拌去气处理5min。石膏浆料的挤出压力设置为35psi,移动速度设置为6mm/s,碳化硅浆料的挤出压力设置为40psi,移动速度设置为3mm/s,打印完成之后将样品进行干燥处理,置于湿度为30%,温度为60℃的条件下保温24小时,使样品完全干燥。
[0067]
实施例4
[0068]
室温下,先将缓凝剂(水杨酸,0.75g)、增稠剂(甲基纤维素,0.41g)、保水剂(聚丙烯酸钠,0.19g)、消泡剂(月桂酸,0.45g)和蒸馏水(50g)进行混合并搅拌至完全溶解后加入α-半水石膏粉(100g)进行充分搅拌和去气脱泡处理获得较为均质的石膏浆体;再通过将溶解分散剂(聚乙烯亚胺,0.2g)于水中,调节ph值为10后,加入碳化硅粉末(40g)进行搅拌混合获得均质分散的碳化硅悬浮液,并加入增稠剂(甲基纤维素,0.4g)获得均质的碳化硅浆体;最后将浆体装入对应针筒并进行搅拌去气处理5min。石膏浆料的挤出压力设置为35psi,移动速度设置为3mm/s,碳化硅浆料的挤出压力设置为45psi,移动速度设置为4mm/s,打印完成之后将样品进行干燥处理,置于湿度为30%,温度为60℃的条件下保温24小时,使样品完全干燥。
[0069]
实施例5-7为采用不同量/种类的外加剂来制备石膏/氮化硅复杂异形结构金属基复合材料预制体。
[0070]
实施例5
[0071]
室温下,先将缓凝剂(蛋白质类缓凝剂,0.75g)、增稠剂(甲基纤维素,0.72g)、保水剂(聚丙烯酸钠,0.22g)、消泡剂(月桂酸,0.45g)和蒸馏水(42g)进行混合并搅拌至完全溶解后加入α-半水石膏粉(100g)进行充分搅拌和去气脱泡处理获得较为均质的石膏浆体;再通过将分散剂(聚乙烯亚胺,0.2g)、溶剂(蒸馏水,8g)和氮化硅粉末(30g)混合并调节ph值为10,获得均质分散的氮化硅悬浮液,并加入增稠剂(甲基纤维素,0.4g)获得均质的氮化硅
浆体;最后将浆体装入对应针筒并进行搅拌去气处理5min。石膏浆料的挤出压力设置为32psi,移动速度设置为3mm/s,氮化硅浆料的挤出压力设置为45psi,移动速度设置为4mm/s,打印完成之后将样品进行干燥处理,置于湿度为30%,温度为60℃的条件下保温24小时,使样品完全干燥。
[0072]
实施例6
[0073]
室温下,先将缓凝剂(三磷聚酸钠,0.67g)、增稠剂(甲基纤维素,0.72g)、保水剂(聚丙烯酸钠,0.22g)、消泡剂(月桂酸,0.45g)和蒸馏水(40g)进行混合并搅拌至完全溶解后加入α-半水石膏粉(100g)进行充分搅拌和去气脱泡处理获得较为均质的石膏浆体;再通过将分散剂(聚乙烯亚胺,0.21g)、溶剂(蒸馏水,10g)和氮化硅粉末(30g)混合并调节ph值为10获得均质分散的碳化硅悬浮液,并加入增稠剂(甲基纤维素,0.4g)获得均质的氮化硅浆体;最后将浆体装入对应针筒并进行搅拌去气处理5min。石膏浆料的挤出压力设置为35psi,移动速度设置为5mm/s,氮化硅浆料的挤出压力设置为38psi,移动速度设置为4mm/s,打印完成之后将样品进行干燥处理,置于湿度为30%,温度为60℃的条件下保温24小时,使样品完全干燥。
[0074]
实施例7
[0075]
室温下,先将缓凝剂(柠檬酸,0.251g)、增稠剂(甲基纤维素,0.77g)、保水剂(聚丙烯酸钠,0.2g)、消泡剂(月桂酸,0.54g)和蒸馏水(42g)进行混合并搅拌至完全溶解后加入α-半水石膏粉(100g)进行充分搅拌和去气脱泡处理获得较为均质的石膏浆体;再通过将分散剂(四甲基氢氧化铵,0.21g)、溶剂(蒸馏水,10g)和氮化硅粉末(30g)混合并调节ph值为10,获得均质分散的碳化硅悬浮液,并加入增稠剂(甲基纤维素,0.4g)获得均质的氮化硅浆体;最后将浆体装入对应针筒并进行搅拌去气处理5min。石膏浆料的挤出压力设置为35psi,移动速度设置为6mm/s,氮化硅浆料的挤出压力设置为38psi,移动速度设置为4mm/s,打印完成之后将样品进行干燥处理,置于湿度为30%,温度为60℃的条件下保温24小时,使样品完全干燥。
[0076]
实施例8-10为采用不同量/种类的外加剂来制备石膏/氧化铝复杂异形结构金属基复合材料预制体。
[0077]
实施例8
[0078]
室温下,先将缓凝剂(水杨酸,0.75g)、增稠剂(甲基纤维素,0.41g)、保水剂(聚丙烯酸钠,0.19g)、消泡剂(月桂酸,0.45g)和蒸馏水(50g)进行混合并搅拌至完全溶解后加入α-半水石膏粉(100g)进行充分搅拌和去气脱泡处理获得较为均质的石膏浆体;再通过将分散剂(四甲基氢氧化铵,0.21g)、溶剂(蒸馏水,10g)和氧化铝粉末(30g)混合并调节ph值为10,获得均质分散的氧化铝悬浮液,并加入增稠剂(甲基纤维素,0.4g)获得均质的氧化铝浆体;最后将浆体装入对应针筒并进行搅拌去气处理5min。石膏浆料的挤出压力设置为35psi,移动速度设置为3mm/s,氧化铝浆料的挤出压力设置为40psi,移动速度设置为4mm/s,打印完成之后将样品进行干燥处理,置于湿度为30%,温度为60℃的条件下保温24小时,使样品完全干燥。
[0079]
实施例9
[0080]
室温下,先将缓凝剂(柠檬酸,0.251g)、增稠剂(甲基纤维素,0.77g)、保水剂(聚丙烯酸钠,0.2g)、消泡剂(月桂酸,0.54g)和蒸馏水(42g)进行混合并搅拌至完全溶解后加入
α-半水石膏粉(100g)进行充分搅拌和去气脱泡处理获得较为均质的石膏浆体;再通过将分散剂(聚乙烯亚胺,0.12g)、溶剂(蒸馏水,10g)和氧化铝粉末(30g)混合并调节ph值为10,获得均质分散的氧化铝悬浮液,并加入增稠剂(甲基纤维素,0.4g)获得均质的氧化铝浆体;最后将浆体装入对应针筒并进行搅拌去气处理5min。石膏浆料的挤出压力设置为35psi,移动速度设置为6mm/s,氧化铝浆料的挤出压力设置为38psi,移动速度设置为4mm/s,打印完成之后将样品进行干燥处理,置于湿度为30%,温度为60℃的条件下保温24小时,使样品完全干燥。
[0081]
实施例10
[0082]
室温下,先将缓凝剂(蛋白质类缓凝剂,0.75g)、增稠剂(甲基纤维素,0.72g)、保水剂(聚丙烯酸钠,0.22g)、消泡剂(月桂酸,0.45g)和蒸馏水(42g)进行混合并搅拌至完全溶解后加入α-半水石膏粉(100g)进行充分搅拌和去气脱泡处理获得较为均质的石膏浆体;再通过将分散剂(聚乙烯吡咯烷酮,0.21g)、溶剂(蒸馏水,10g)和氧化铝粉末(30g)混合并调节ph值为10获得均质分散的氧化铝悬浮液,并加入增稠剂(甲基纤维素,0.4g)获得均质的氧化铝浆体;最后将浆体装入对应针筒并进行搅拌去气处理5min。石膏浆料的挤出压力设置为32psi,移动速度设置为3mm/s,氧化铝浆料的挤出压力设置为38psi,移动速度设置为4mm/s,打印完成之后将样品进行干燥处理,置于湿度为30%,温度为60℃的条件下保温24小时,使样品完全干燥。
[0083]
以上所述,仅为本发明的具体实施方式,但本发明的保护范围并不局限于此,任何熟悉本领域技术的技术人员在本发明公开的技术范围内,可轻易想到的变化或替换,都应涵盖在本发明的保护范围之内。因此,本发明的保护范围应以所述权利要求的保护范围为准。
再多了解一些
本文用于创业者技术爱好者查询,仅供学习研究,如用于商业用途,请联系技术所有人。