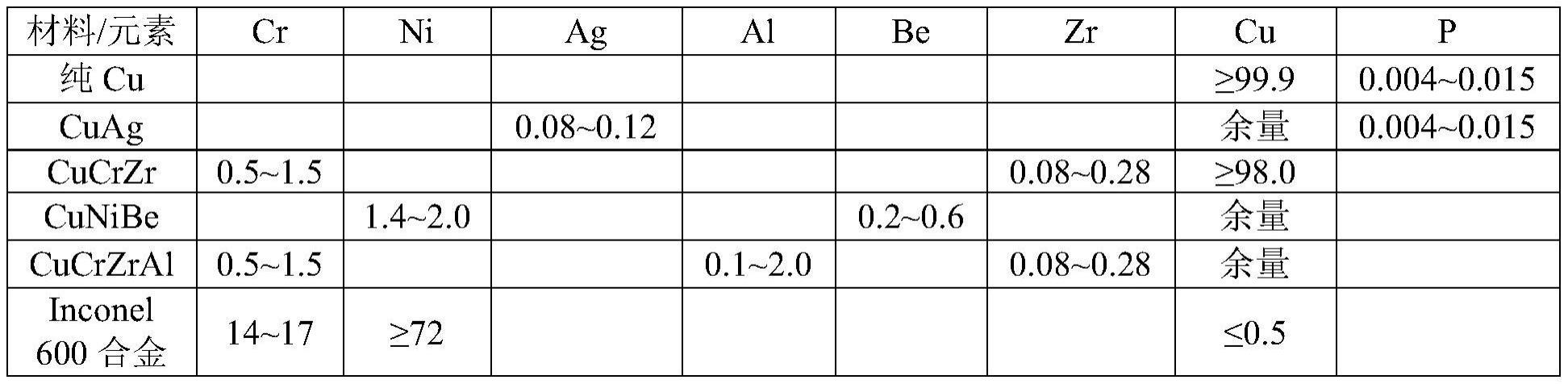
1.本发明涉及一种高碳钢无缺陷连铸坯的热送方法,目的是为了满足铸坯不进热轧加热炉直接轧制的工艺要求,属于冶金技术领域。
背景技术:
2.碳含量高于0.77wt%以上的高碳钢,钢种熔点偏低,液相线温度比普通低碳钢低100℃以上,连铸保护渣熔化困难,铸坯和结晶器之间摩擦力显著上升,因此,高碳钢连铸坯表面发生凹陷与纵裂乃至漏钢,严重影响了产品的后续质量。高碳钢铸坯因缺陷导致被迫下线,严重影响了产品的热轧热送和热装率。
3.结晶器是连铸机的关键设备,大部分铸坯的表面缺陷均产生于结晶器。结晶器工作面既要承受高温钢水的冲刷、热蚀,又要承受初凝坯壳运动而产生的磨损和应力作用,容易发生磨损、热裂纹、腐蚀、变形等现象。因此,要求工作面材质具有良好的导热性、高的强度和硬度、较高的再结晶温度、抗蠕变性能、热疲劳强度和耐腐蚀性。
4.结晶器工作面最初常用的材料是纯铜,纯铜由于具有良好的热传导率,在最初被广泛应用,但一般只适用于拉速低于1.0m/min的低拉速连铸机,且结晶器工作面温度低于230℃的情况,主要是在230℃以上温度长时间使用的话,材料的强度会明显下降。随后通过添加ag以提高铜板的软化温度,但使用温度必须控制在350℃以下。随着连铸机拉速的提高及结晶器高寿命的要求,对铜板材料的性能要求也越来越高,随后出现了cucr、cucrzr、cunibe等析出强化型铜合金材料,这些材料具有更高的强度和硬度,软化温度可达到450℃。
5.cucr材料具有高电导率,其在常温和高温时具有较高的强度,但是由于高温延展性较差,在结晶器工作面温度达到400℃时,容易产生热裂纹。
6.cucrzr材料既维持了cucr材料的高电导率,又改善了材料的高温伸展性,具有较强的高温强度,其抗变形能力较好,可延长铜板的使用寿命。而随着连铸高拉速要求,结晶器的使用条件更加苛刻。为了满足这一要求,采用强度比cucrzr材料更高的cunibe材料,cunibe材料一般应用于热负荷强度特别高的结晶器上,如薄带连铸结晶器。
7.另外,结晶器工作面使用过程中主要存在边缘磨损、宽面热裂纹、窄面收缩、腐蚀等问题。以往,对结晶器铜板研究重点是采用合适的表面处理技术在铜板表面覆盖一种或几种材料,以获得特殊功能表面,在保证其导热性受镀层影响不大的情况下,获得与基体结合牢固、耐磨性好、抗热腐蚀性强的各种镀层。电镀、化学镀、电铸、热喷涂和高温自蔓延、复合镀等表面改性技术在连铸结晶器上的采用,可以解决结构件的耐腐蚀、耐磨损等问题。各种镀层特点及不足如下:
8.镀cr层:镀cr层表面形成的极薄一层氧化膜对开浇时产生的飞溅钢水粒被凝固后的脱落是很有益的,一般采用0.1mm左右厚的镀层。但是由于cu和cr的膨胀系数相差很大,镀层较厚时容易剥落,而且结晶器镀cr工艺复杂,产生化学废酸造成严重的环境污染。
9.ni cr复合镀层:由于ni的膨胀系数接近cu,剥离问题大大改善,厚度增加。ni解决
了附着力和厚度问题,cr解决了喷溅性和表面硬度问题。为了解决ni热传导率较差问题,引入斜面层工艺,弯月面处的ni层厚度可控制在0.2mm左右,出口处ni层厚度控制在3mm左右。cr层极薄,较厚ni层又很软,未能圆满解决结晶器下部耐磨耗问题。一方面由于浇铸速度的提高,较薄的坯壳在钢水静压力作用下紧贴铜板表面,增加了机械摩擦负荷;另一方面,无缺陷铸坯工艺对结晶器形状精度的要求越来越严格,结晶器更换周期取决于下部磨耗量。
10.ni-fe镀层:在ni中加入fe或加入w和fe时,镀层的硬度明显提高,按fe含量不同,可调节硬度在hv250~550范围内,高温强度(400℃)是ni的2.5倍,单层电镀就可实现较厚镀层。虽然ni-fe镀层耐磨性和通钢量较ni镀层都得到了大幅提高,但电镀效率低,工艺复杂,环境污染严重。
11.ni-co或co-ni镀层:ni-co镀层和co-ni镀层进一步提高了镀层的耐磨性,提高结晶器铜板的使用寿命。这其实是两种不同基体的高温合金,ni-co是含co的镍基合金,co-ni是含ni的钴基合金。其性能较ni-fe层有了进一步的提高,co-ni镀层的性能更好一些,但电镀效率低,工艺复杂,环境污染严重。
12.ni-cr合金喷涂层:在板坯结晶器使用中,窄边铜板的磨损比宽边铜板更严重,为了提高窄边铜板的使用寿命,在窄边铜板表面用超音速火焰喷涂一层ni-cr合金层,代替电镀层,其使用寿命可与宽边铜板的co-ni镀层寿命相当。但该技术易产生较大的热应力;并且由于热喷涂过程中形成新的热处理制度而使组织不均匀,易于造成热变形。热喷涂过程中金属的熔化和再凝固容易发生氧化,氧含量的增加会大大降低材料的热导率,而且这些氧元素在以后的加工过程中也难以除去。真空喷涂可以在一定程度上缓解氧化程度,但真空喷涂成本高,并且难以控制。
13.复合镀层:如早期的ni-p-氟化石墨,采用化学镀的方法获得氟化石墨体积分数达9%的自润滑镀层,摩擦系数显著降低,延长了结晶器使用寿命。但复合镀层中固体颗粒与基体的结合问题难以掌控。
14.陶瓷镀层:采用陶瓷喷涂技术,陶瓷镀层与钢水亲和力较大,容易被黏结和磨损,发生黏结漏钢事故。
15.在连铸生产高碳钢种时,因结晶器的内壁与坯壳之间的保护渣流入不均匀,引起坯壳的传热不均匀和坯壳的生长速度不均匀,在铸坯上产生纵向凹陷及纵向裂纹是连铸生产这类钢种时遇到的主要问题之一。通过降低传热速度减缓结晶器传热,形成“弱冷”。可以提高铸坯表面温度,迟滞坯壳的生长速度,进而促进坯壳生长的均匀性,降低纵裂、凹陷等铸坯缺陷的形成倾向。然而,上述提到的传统的结晶器铜板工作面材质和涂镀层,很难满足高碳钢连铸生产。
技术实现要素:
16.本发明所要解决的技术问题在于克服现有技术中连铸生产高碳钢种时因冷却强度大引起的铸坯纵向凹陷及纵向裂纹的不足;通过改进结晶器工作面材质,并配合相应的涂层材料和连铸工艺,通过降低传热速度减缓结晶器传热,形成“弱冷”。以此提高铸坯表面温度,迟滞坯壳的生长速度,进而促进坯壳生长的均匀性,降低纵裂、凹陷等铸坯缺陷的形成倾向;进一步提供一种在连铸工艺中起着非常重要作用提升高碳钢连铸坯表面质量与热送的技术方法;进一步满足铸坯不进热轧加热炉直接轧制的工艺要求。
17.本发明所要解决的技术问题可以通过以下技术方案来实施。
18.一种高碳钢无缺陷连铸坯的热送方法,目的是为了满足铸坯不进热轧加热炉直接轧制的工艺要求,其特点为,板坯连铸工序中,结晶器材质采用inconel600合金,厚度范围为10~20mm。
19.为了提高结晶器寿命,在结晶器靠近钢水侧附加镀层。传统结晶器镀层厚度是上部镀层薄、下部镀层厚,结晶器镀层从上部至下部呈逐渐增厚趋势。而对于本发明生产高碳钢使用的结晶器来说,原设计无法满足缓冷需求。本发明结晶器靠近钢水侧的镀层厚度范围为2.5~5.0mm,镀层材质为纯ni、ni-cr、ni-co或co-ni合金中的一种。
20.其中,本发明结晶器所采用的inconel 600合金与结晶器工作面常用铜基材料的化学成分如下表1所示。
21.表1:wt%
[0022][0023]
结晶器工作面常用铜基材料与inconel 600合金的力学性能如表2所示;inconel 600合金的强度和塑性均优于铜基材料。
[0024]
表2:
[0025][0026][0027]
inconel 600合金导热系数为铜材料的1/20,与结晶器工作面常用铜材料的物理性能对比如表3所示。
[0028]
表3:
[0029][0030]
在所述连铸工序中,中间包内钢液的过热度控制在50~100℃,高碳钢常规连铸拉速控制在1.8~2.6m/min,结晶器宽面水量5000~6000l/min,连铸结晶器水口插入深度控制在80~150mm,结晶器窄面锥度1.25~1.35%,二冷区冷却比水量0.10~0.30l/kg,高碳钢热送铸坯表面温度为1100℃以上。
[0031]
作为优选方案,整个结晶器镀层的厚度范围为2.5~4.5mm。
[0032]
作为优选方案,所述中间包内钢液过热度控制在50~80℃,拉速控制在2.0~2.4m/min。
[0033]
作为优选方案,所述结晶器宽面水量为5250~5750l/min。
[0034]
作为优选方案,所述连铸结晶器水口插入深度控制在80~120mm。
[0035]
作为优选方案,所述结晶器窄面锥度1.25~1.30%。
[0036]
作为优选方案,所述二冷区冷却比水量0.15~0.3l/kg。
[0037]
作为优选方案,所述高碳钢热送铸坯表面温度为1100~1200℃。
[0038]
本发明的技术方案机理及其限定原因如下:
[0039]
结晶器工作面材质:inconel 600合金具有良好的耐应力腐蚀开裂性能、耐点腐蚀和缝隙腐蚀性能、抗氧化性和非氧化性热酸性能,在高达550℃的高温时都具有很好的机械性能。其导热系数仅为铜材料的1/20,完全可以满足结晶器弱冷的要求。经过大量的实验验证,低于10mm难以抵御钢水静压力;高于20mm影响传热速度,铸坯坯壳太薄;故本发明结晶器工作面材质厚度范围为10~20mm。
[0040]
靠近钢水侧镀层材料:纯ni或ni-cr或ni-co或co-ni合金的膨胀系数与inconel 600合金接近,且通过控制电镀工艺容易精确控制镀层厚度,使用过程中的磨损小,使用寿命长。本发明选用镀层材质为纯ni、ni-cr、ni-co或co-ni合金中的一种。
[0041]
镀层厚度:镀层厚度小于2.5mm时,镀层耐磨强度不够,铸坯对结晶器镀层磨损、导致结晶器寿命降低。当镀层厚度大于5.0mm时,降低结晶器弯月面的传热速度,连铸坯壳过薄,在坯壳收缩力的作用下,产生塌陷,造成铸坯表面重皮。本发明镀层的厚度范围为2.5~5.0mm。
[0042]
中间包内过热度:以往高碳钢连铸为了保证凝固坯壳厚度均匀性,倾向于低过热度,即过热度控制在30℃以内。采用inconel 600合金作为结晶器工作材质,由于导热系数仅为铜材料的1/20,实现了结晶器弱冷效果、保证了结晶器坯壳厚度的均匀性。连铸过热度一直是炼钢连铸界面最难管控技术,采用本发明方案可放开对过热度的管控,将过热度的温度放开,提高生产效率,还可保证高碳钢的冷却和凝固效果。但过热度也不能无限放开,如果钢水过热度高于100℃,连铸结晶器内初生坯壳太薄、裂纹倾向性太大,并造成高碳钢凝固时间长、选分结晶充分,加剧铸坯偏析与疏松。本发明中间包内钢液的过热度控制在50~100℃。
[0043]
连铸拉速:本发明的拉速设计考虑了高碳钢热送直接轧制。经过本发明实验与现场测温,发现如果拉速低于1.8m/min,出铸机铸坯表面温度低于1100℃,无法满足直接轧制要求。由于铸机冶金长度限制,常规板坯连铸拉速上限为2.6m/min。本发明连铸拉速控制在1.8~2.6m/min。
[0044]
结晶器水量:结晶器宽面出口的坯壳厚度需要大于12mm,考虑高过热度和inconel 600合金的低导热系数特性,为了保证高碳钢在结晶器出口的坯壳厚度需要采用强冷措施,经过大量实验分析,结晶器宽面水量不低于5000l/min;同时为了提高传热和坯壳厚度均匀性,结晶器宽面水量不高于6000l/min。本发明的结晶器宽面水量为5000~6000l/min。
[0045]
结晶器水口插入深度:结晶器水口插入深度过浅的话,水口流股对钢渣界面的冲击较强,增加钢液与结晶器保护渣反应几率,同时增加弯月面卷渣概率;结晶器水口插入过
深的话,铸坯易产生裂纹。考虑到高碳钢裂纹浇注温度低、化渣困难,本发明的结晶器水口插入深度控制在80~150mm。
[0046]
二次冷却:在高碳钢(c》0.77wt%)成分体系下,高碳钢连铸坯在二冷区是纯奥氏体、塑性很高。考虑到直接轧制需要铸坯表面温度高于1100℃,经过大量计算、测温验证,二冷区比水量不能超过0.30l/kg;同时在高温条件下防止铸机损坏,二冷区比水量不能低于0.10l/kg。本发明的二冷比水量为0.1~0.3l/kg。
[0047]
结晶器锥度:凝固过程中结晶器/铸坯间产生气隙,会使传热不均匀,导致坯壳生长厚度不均,容易形成表面凹陷或裂纹,故设置一个倒锥度以补偿凝固坯壳的收缩。若结晶器锥度太小,坯壳容易鼓胀;若锥度太大,坯壳与结晶器铜板摩擦力增加。本发明的结晶器窄面锥度1.25~1.35%。
[0048]
与现有技术相比,本发明具有如下有益效果:
[0049]
1、无缺陷制造技术。
[0050]
本发明通过改善结晶器材质,以及在结晶器附加镀层,配合连铸关键工艺参数,降低传热速度减缓结晶器传热,形成“弱冷”,迟滞坯壳的生长速度,进而促进坯壳生长的均匀性,达到消除高碳钢铸坯表面凹陷和裂纹的目的,实现了高碳钢无缺陷铸坯生产。
[0051]
2、降本减碳效果。
[0052]
本发明高碳钢铸坯出铸机温度高于1100℃,实现了高碳钢铸坯直接轧制,显著降低了制造成本和减少碳排放。现有的高碳钢连铸板坯的热装温度为200~600℃,按每提高100℃热装温度,节约3kg/t标煤、减少8kg/t co2计。至少提高500℃计算,本发明的高碳钢直轧可节约15kg/t标煤、减少40kg/t co2。
[0053]
3、具有显著的经济效益。
[0054]
现有的铜基结晶器铜板一个服役周期内钢产量10万吨,采用本发明的inconel 600合金显著提升了服役寿命和周期,钢产量可达30万吨以上,减少了下线更换次数、提高了作业率。铜基结晶器成本约7万元/吨,inconel 600合金成本约14万元/吨。可见,虽然inconel 600合金成本是铜结晶器的2倍,但inconel 600合金的钢产量是铜基结晶器的3倍,且能显著提高作业率、铸坯质量、热送率和直接轧制效果。
具体实施方式
[0055]
下面结合具体实施例来对本发明的具体实施方式进行进一步的详细说明。
[0056]
以下实施例将有助于本领域的技术人员进一步理解本发明,但不以任何形式限制本发明。应当指出的是,对本领域的普通技术人员来说,在不脱离本发明构思的前提下,还可以做出若干变形和改进。这些都属于本发明的保护范围。
[0057]
下表4中给出了本发明各实施例的具体技术细节及效果。
[0058]
表4:本发明的实施例与效果
[0059][0060]
采用本发明的高碳钢无缺陷连铸坯及热送方法,可以实现高碳钢的无缺陷铸坯,本发明高碳钢铸坯出铸机温度高于1100℃,实现了高碳钢铸坯直接轧制,显著降低了制造成本和减少碳排放。
[0061]
最后应说明的是:以上实施例仅用以说明本发明而并非限制本发明所描述的技术方案;因此,尽管本说明书参照上述的各个实施例对本发明已进行了详细的说明,但是,本领域的普通技术人员应当理解,仍然可以对本发明进行修改或等同替换;而一切不脱离本发明的精神和范围的技术方案及其改进,其均应涵盖在本发明的权利要求范围中。
再多了解一些
本文用于创业者技术爱好者查询,仅供学习研究,如用于商业用途,请联系技术所有人。