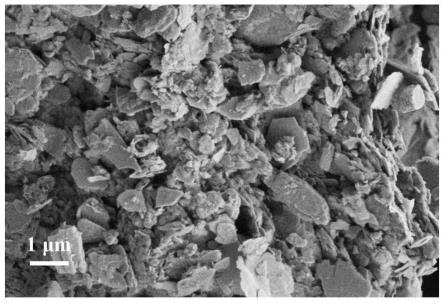
1.本发明涉及一种超浸润材料,具体地说,涉及一种全生物基超亲水/水下超疏油涂层及其制备方法。
背景技术:
2.近年来,随着社会工业和经济的发展,工业含油废水排放量大幅增加,海上石油开采和运输过程中的原油泄漏事件频繁发生,导致淡水、海洋生态遭到严重破坏,同时石油资源浪费和环境污染造成的经济损失也在逐年攀升。传统的油水分离方法包括燃烧法、重力法、生物法、气浮法等,但这些方法存在成本高、分离效率低、易造成二次污染等缺点。
3.研究表明,通过调控分离材料表面的润湿行为,制备具有特殊功能的超浸润多孔材料可以实现高效的油水分离。与超疏水/超亲油材料相比,超亲水/水下超疏油材料的制备过程更绿色环保,同时涂层具有优异的抗油污染性,可以避免吸油引起的油水分离效率和通量等性能下降。
4.为了在基底表面构造具有抗油污染性的超亲水/水下超疏油涂层,中国发明专利cn112494997b在基底上依次涂覆tio2和comoo4@zro2,烧结后制得具有较好耐久性和抗污染性、较高纯水通量和油水分离效率的多孔超亲水疏油材料;中国发明专利cn107998908b将铸膜液流延到具有微纳结构的基底内,通过凝胶浴形成具有互补微纳结构的有机膜,再在膜表面接枝聚甲基丙烯酸,最后浸泡涂覆氨基修饰的二氧化硅纳米颗粒,制得具有高通量和持久抗污染特性的超亲水膜;中国发明专利申请202110243722.x将纤维素溶液涂覆在多孔材料表面,通过氧化剂将纤维素的邻位羟基氧化为醛基,再对纤维素进行交联处理,最后在膜表面接枝亲水改性剂,制得抗污染性强、油水分离效率高的超亲水/水下超疏油膜。
5.然而,上述材料的制备过程都复杂耗时,并且多采用不可再生和降解的无机纳米颗粒或高分子材料,此外制备的超亲水涂层不具有基底普适性。更重要的是,绝大部分超亲水材料的抗油污染性仅对低粘性、低污染性的油和有机溶剂有效,使用过程中仍易被高粘度油类如植物油、硅油、原油等粘附和污染,导致材料失去超亲水和水下超疏油性能。若将此类超亲水材料用于油水分离领域,这种不佳的抗油污染性一定会导致油水分离性能大幅度下降。
技术实现要素:
6.本发明提供了一种全生物基超亲水/水下超疏油涂层及其制备方法,其能够克服现有技术中超亲水涂层制备工艺繁琐、反应条件苛刻、不可降解、基底适用性窄、仅能抵抗低粘性油污染等问题。
7.一种全生物基超亲水/水下超疏油涂层的制备方法,将壳聚糖衍生物、纤维素微纳米晶体和交联剂的混合溶液涂覆于基底表面,热交联后即制得全生物基超亲水/水下超疏油涂层。
8.作为优选,具体包括以下步骤:
9.步骤s1、将纤维素微纳米晶体超声分散于水中,得到分散液;将壳聚糖衍生物溶解于水中,得到壳聚糖衍生物溶液;
10.步骤s2、将步骤s1中的分散液与壳聚糖衍生物溶液混合后加入交联剂,搅拌5~60min得到壳聚糖衍生物、纤维素微纳米晶体和交联剂的混合溶液;
11.步骤s3、使用氧等离子体对基底进行预处理;
12.步骤s4、将步骤s2得到的混合溶液滴涂于步骤s3处理后的基底上或将步骤s3处理后的基底浸泡于步骤s2得到的混合溶液中2~10min;
13.步骤s5、将步骤s4处理后的基底置于烘箱中加热反应后得到全生物基超亲水/水下超疏油涂层。
14.作为优选,壳聚糖衍生物包括羧甲基壳聚糖、壳聚糖盐酸盐、羟丙基壳聚糖中的一种或多种。
15.作为优选,纤维素微纳米晶体为颗粒状或长棒状或纤维状中的一种或多种,颗粒状的粒径为0.2~5μm;长棒状或纤维状的直径大于0.1μm。
16.作为优选,交联剂包括戊二醛、乙二醛、京尼平、环氧氯丙烷、乙二醇二缩水甘油醚中的一种或多种。
17.作为优选,基底为平面材料或多孔材料,多孔材料孔径不超过120μm。
18.作为优选,纤维素微纳米晶体和壳聚糖衍生物的质量比为2~6,交联剂与壳聚糖衍生物的质量比为1~10wt%;
19.步骤s1中分散液的体积浓度为1~20mg/ml,壳聚糖衍生物溶液的体积浓度为1~20mg/ml。
20.作为优选,步骤s3中预处理具体为使用氧气或空气对基体表面进行等离子体处理,使基体表面转变为亲水。
21.作为优选,步骤s5中加热反应为25~80℃环境中交联反应5~360min。
22.一种全生物基超亲水/水下超疏油涂层,其采用前述的一种全生物基超亲水/水下超疏油涂层的制备方法制得。
23.本发明由于采用了以上技术方案,具有显著的技术效果:
24.(1)本发明所制备的全生物基超亲水/水下超疏油涂层具有优异的超亲水和水下超疏油性。
25.壳聚糖衍生物富含氨基与羟基,纤维素微纳米晶体富含羟基,两者在交联剂辅助下形成化学键接和氢键连接的多重交联涂层。纤维素晶体和壳聚糖衍生物构建的涂层具备丰富的亲水基团,形成化学键接和氢键连接的多重交联网络,同时纤维素微纳米晶体构建了多尺度的粗糙结构,使涂层获得长期稳定的超亲水性,并通过水相环境中涂层表面水合层的捕获使涂层呈现超疏油特性。
26.(2)本发明所制备的全生物基超亲水/水下超疏油涂层具有优异的抗高粘度油类粘附与污染性。
27.当涂层与水接触时,强亲水性的羟基、氨基、羧基等基团迅速与水作用,形成完整的氢键网络结构和稳定的水合层;同时,涂层内纤维素微纳米晶体构建的粗糙形貌使水合层内水被迅速锁定在粗糙分级结构内。在物理屏障作用和强水合能力作用下,即使高粘度油类也难以进攻并接触到基底表面,涂层展现出优异的抗油粘附和污染性,即使对高粘度
油类如植物油、原油、硅油等也展现出优异的抗粘附性。
28.(3)本发明的制备工艺简单无污染、成本低廉、容易实现大面积生产,所制备的涂层适用于多种基底包括普通平面和多孔材料,并且所制备的全生物基超亲水/水下超疏油涂层具有生物可降解性。
29.(4)本发明制备的全生物基超亲水/水下超疏油涂层能够适用于多种基底如玻璃片、铁片、塑料片、铁丝网、织物、聚氨酯海绵等,应用范围广泛。
附图说明
30.图1为实施例1的纤维素微纳米晶体的扫描电镜图(放大倍数:10000倍)。
31.图2为实施例1制备的超亲水/水下超疏油涂层表面的水接触角和水环境中的原油接触角。
32.图3为实施例1制备的超亲水/水下超疏油涂层在不同放大倍数下的扫描电镜图(放大倍数:500倍和5000倍)。
33.图4为实施例1制备的超亲水/水下超疏油涂层在水相环境中的抗硅油粘附过程。
具体实施方式
34.为进一步了解本发明的内容,结合附图和实施例对本发明作详细描述。应当理解的是,实施例仅仅是对本发明进行解释而并非限定。
35.实施例1
36.将纤维素微纳米晶体超声分散于水中,配制成体积浓度为2mg/ml的分散液,所选用的纤维素微纳米晶体为形状不规则的块状结构,尺寸分布在0.2~5μm之间。将羧甲基壳聚糖溶解于水中,配制成体积浓度为2mg/ml的羧甲基壳聚糖溶液。将30ml纤维素微纳米晶体分散液和10ml羧甲基壳聚糖溶液混合,再加入1mg戊二醛,搅拌10min后形成壳羧甲基壳聚糖、纤维素微纳米晶体和交联剂的混合溶液;随后,使用氧等离子体对玻璃片进行预处理,具体为使用氧气对玻璃片表面进行等离子体处理,使玻璃片表面转变为亲水再,将混合溶液滴涂在玻璃片上,放入烘箱60℃反应30min,制得抗高粘度油污染的全生物基超亲水/水下超疏油涂层。
37.图1为实施例1的纤维素微纳米晶体的扫描电镜图。可以看出,所选用的纤维素微纳米晶体为形状不规则的块状结构,尺寸分布在0.2~5μm之间。
38.图2为实施例1制备的超亲水/水下超疏油涂层表面的水接触角和水环境中的原油接触角。可以看出,水滴接触涂层后迅速铺展变为7.9
°
,而在水环境中,原油油滴在涂层表面呈现稳定的球形,接触角为156
°
。原油粘度在室温(25℃)下为780mpa
·
s,涂层表现出优异的超亲水和水下超疏油性。值得注意的是,涂层即使在空气或水环境中保存2个月后,水接触角和水下油接触角也基本保持不变,呈现稳定的超浸润性能。
39.图3为实施例1制备的超亲水/水下超疏油涂层在不同放大倍数下的扫描电镜图。可以看出,涂层呈现明显的微纳粗糙结构,表面由壳聚糖粘结的纤维素晶体堆积而成。涂层粗糙结构一方面可以促进表面亲水性能,另一方面有利于涂层在水相环境中捕获水合层,从而呈现超疏油特性。
40.图4为实施例1制备的超亲水/水下超疏油涂层在水相环境中的抗硅油粘附过程。
硅油粘度在室温(25℃)下高达20000mpa
·
s。可以看出,即使硅油油滴在涂层表面因挤压而严重变形,也能与涂层完全分离。这主要是由于涂层具有强大的水合能力,其粗糙结构可以稳定高效地捕获水合层,即使在高粘度硅油的攻击作用下,该水合层也难以被硅油破坏并取代,因而涂层展现出优异的抗高粘度油污染性。
41.涂层水接触角、水下原油接触角和抗高粘度硅油污染性能的测试结果如表1所示,涂层长效耐久性能的测试结果如表2所示。
42.实施例2
43.将纤维素微纳米晶体超声分散于水中,配制成体积浓度为1mg/ml的分散液,所选用的纤维素微纳米晶体为长棒状结构,直径分布在0.1~0.3μm之间。将羟丙基壳聚糖溶解于水中,配制成体积浓度为20mg/ml的羟丙基壳聚糖溶液。将80ml纤维素微纳米晶体分散液和2ml羟丙基壳聚糖溶液混合,再加入0.4mg环氧氯丙烷,搅拌5min后形成羟丙基壳聚糖、纤维素微纳米晶体和交联剂的混合溶液;随后,使用氧等离子体对铁片进行预处理,具体为使用氧气或空气对铁片表面进行等离子体处理,使铁片表面转变为亲水,再将混合溶液滴涂在铁片上,放入烘箱80℃反应5min,制得抗高粘度油污染的全生物基超亲水/水下超疏油涂层。
44.涂层水接触角、水下原油接触角和抗高粘度硅油污染性能的测试结果如表1所示,涂层长效耐久性能的测试结果如表2所示。
45.实施例3
46.将纤维素微纳米晶体超声分散于水中,配制成体积浓度为20mg/ml的分散液,所选用的纤维素微纳米晶体为纤维素纳米颗粒和纤维素纳米线的混合物,纤维素纳米颗粒的尺寸分布在0.2~1μm之间,纤维素纳米线的直径在0.1~0.2μm之间。将壳聚糖盐酸盐溶解于水中,配制成体积浓度为1mg/ml的壳聚糖盐酸盐溶液。将6ml纤维素微纳米晶体分散液和20ml壳聚糖盐酸盐溶液混合,再加入12mg乙二醛,搅拌5min后形成壳聚糖盐酸盐、纤维素微纳米晶体和交联剂的混合溶液;随后,使用氧等离子体对孔径为100μm的不锈钢网进行预处理,具体为使用氧气或空气对不锈钢网表面进行等离子体处理,使不锈钢网表面转变为亲水,再将不锈钢网浸泡于混合溶液中10min,取出25℃反应360min,制得抗高粘度油污染的全生物基超亲水/水下超疏油涂层。
47.涂层水接触角、水下原油接触角和抗高粘度硅油污染性能的测试结果如表1所示,涂层长效耐久性能的测试结果如表2所示。
48.实施例4
49.将纤维素微纳米晶体超声分散于水中,配制成体积浓度为5mg/ml的分散液,所选用的纤维素微纳米晶体为尺寸分布在0.2~1μm之间的颗粒。将羧甲基壳聚糖溶解于水中,配制成体积浓度为10mg/ml的壳聚糖盐酸盐溶液。将80ml纤维素微纳米晶体分散液和10ml壳聚糖盐酸盐溶液混合,再加入2mg京尼平,搅拌3min后形成壳聚糖盐酸盐、纤维素微纳米晶体和交联剂的混合溶液;随后,使用氧等离子体对聚酯织物进行预处理,具体为使用氧气或空气对聚酯织物表面进行等离子体处理,使聚酯织物表面转变为亲水,再将聚酯织物浸泡于混合溶液中2min,取出放入烘箱50℃反应90min,制得抗高粘度油污染的全生物基超亲水/水下超疏油涂层。
50.涂层水接触角、水下原油接触角和抗高粘度硅油污染性能的测试结果如表1所示,
涂层长效耐久性能的测试结果如表2所示。
51.对比例1
52.为了验证本发明所制备的全生物基超亲水/水下超疏油涂层中粗糙结构对实现超浸润性能和抗高粘度油类污染性能的关键作用,以较低纤维素微纳米晶体/壳聚糖衍生物质量比下制备的涂层进行对比。
53.将纤维素微纳米晶体超声分散于水中,配制成体积浓度为2mg/ml的分散液,所选用的纤维素微纳米晶体为形状不规则的块状结构,尺寸分布在0.2~5μm之间。将羧甲基壳聚糖溶解于水中,配制成体积浓度为2mg/ml的羧甲基壳聚糖溶液。将30ml纤维素微纳米晶体分散液和30ml羧甲基壳聚糖溶液混合,再加入3mg戊二醛,搅拌10min后形成混合溶液;随后,使用氧等离子体对玻璃片进行预处理,预处理具体为使用氧气或空气对玻璃片表面进行等离子体处理,使玻璃片表面转变为亲水,再将混合溶液滴涂在玻璃片上,放入烘箱60℃反应30min,制得全生物基涂层。
54.涂层的水接触角、水下原油接触角和抗高粘度硅油污染性能的测试结果如表1所示。
55.对比例2
56.为了验证本发明所制备的全生物基超亲水/水下超疏油涂层中粗糙结构对实现超浸润性能和抗高粘度油类污染性能的关键作用,以尺寸较小的纤维素纳米晶体制备的涂层进行对比。
57.将纤维素纳米晶体超声分散于水中,配制成体积浓度为2mg/ml的分散液,所选用的纤维素纳米晶体为尺寸分布在20~60nm之间的颗粒结构。将羧甲基壳聚糖溶解于水中,配制成体积浓度为2mg/ml的羧甲基壳聚糖溶液。将30ml纤维素纳米晶体分散液和10ml羧甲基壳聚糖溶液混合,再加入1mg戊二醛,搅拌10min后形成混合溶液;随后,使用氧等离子体对玻璃片进行预处理,具体为使用氧气或空气对玻璃片表面进行等离子体处理,使玻璃片表面转变为亲水,再将混合溶液滴涂在玻璃片上,放入烘箱60℃反应30min,制得全生物基涂层。
58.涂层的水接触角、水下原油接触角和抗高粘度硅油污染性能的测试结果如表1所示。
59.对比例3
60.为了验证本发明所制备的全生物基超亲水/水下超疏油涂层中多重氢键网络对实现超浸润性能和抗高粘度油类污染性能的关键作用,以四氧化三铁颗粒制备的涂层进行对比。
61.将尺寸分布在0.3~0.5μm之间的四氧化三铁颗粒超声分散于水中,配制成体积浓度为2mg/ml的分散液。将羧甲基壳聚糖溶解于水中,配制成体积浓度为2mg/ml的羧甲基壳聚糖溶液。将30ml四氧化三铁分散液和10ml羧甲基壳聚糖溶液混合,再加入1mg戊二醛,搅拌10min后形成混合溶液;随后,使用氧等离子体对玻璃片进行预处理,具体为使用氧气或空气对玻璃片表面进行等离子体处理,使玻璃片表面转变为亲水,再将混合溶液滴涂在玻璃片上,放入烘箱60℃反应30min,制得涂层。
62.涂层的水接触角、水下原油接触角和抗高粘度硅油污染性能的测试结果如表1所示。
63.对比例4
64.为了验证本发明所制备的全生物基超亲水/水下超疏油涂层对基底孔径的要求,以孔径较大的聚氨酯海绵基底制备的材料进行对比。
65.将纤维素微纳米晶体超声分散于水中,配制成体积浓度为2mg/ml的分散液,所选用的纤维素微纳米晶体为形状不规则的块状结构,尺寸分布在0.2~5μm之间。将羧甲基壳聚糖溶解于水中,配制成体积浓度为2mg/ml的羧甲基壳聚糖溶液。将30ml纤维素微纳米晶体分散液和10ml羧甲基壳聚糖溶液混合,再加入1mg戊二醛,搅拌10min后形成混合溶液;随后,使用氧等离子体对孔径分布在150~600μm之间的聚氨酯海绵进行预处理,具体为使用氧气对聚氨酯海绵进行等离子体处理,使聚氨酯海绵表面转变为亲水,再将聚氨酯海绵浸泡于混合溶液中2min,取出放入烘箱60℃反应30min,制得全生物基涂层。
66.涂层的水接触角、水下原油接触角和抗高粘度硅油污染性能的测试结果如表1所示。
67.性能测试
68.(1)扫描电镜测试
69.采用扫描电子显微镜(jsm-7610fplus,日本)进行形貌观察,加速电压设为10kv。测试前将样品用导电胶固定在试样台上,并进行喷金处理。
70.(2)接触角测试
71.采用接触角仪(sdc-200s,东莞晟鼎精密仪器有限公司)测试涂层表面的水滴接触角和水下原油接触角。水滴大小为3μl,记录水滴在涂层表面的吸附过程。原油粘度在室温(25℃)下为780mpa
·
s,测试油滴大小为10μl。接触角值取涂层表面5个位置计算平均值。
72.(3)长效耐久性测试
73.为了评价涂层的长效耐久性,将涂层置于自然环境中60天,再对涂层进行水接触角和水下原油接触角测试;此外,将涂层置于水环境中60天,取出观察涂层与基底的剥离情况,若无明显损坏,则室温干燥后再对涂层进行水接触角和水下原油接触角测试。
74.(4)抗高粘度硅油污染性测试
75.为了方便观察硅油在涂层表面的粘附和污染情况,使用油红o将硅油染成红色,硅油粘度在室温(25℃)下高达20000mpa
·
s。将涂层置于水中,用针管挤出硅油油滴,使油滴与涂层表面接触并经历挤压、变形等过程,随后抬起油滴,观察硅油在涂层表面是否有残留。
76.表1
[0077][0078]
表2
[0079][0080]
从表1和表2实施例的性能测试中可以看出,实施例1-4制得的全生物基超亲水/水下超疏油涂层具有优异的超亲水和水下超疏油性,可以抵抗高粘度油类的粘附和污染,且涂层在储存两个月后,接触角变化不大,表现出良好的长效耐久性。
[0081]
从表1对比例的性能测试中可以看出,与实施例1相比,对比例1和3仅具有水下超疏油性,对比例2不具有超亲水和水下超疏油性,对比例4仅具有超亲水性,并且四个对比例表面均有高粘度硅油残留,涂层不能抵抗高粘度油类的粘附和污染。对比例1和2主要是由于纤维素晶体构造的粗糙度不够,而对比例4是由于聚氨酯海绵孔径过大,即使海绵表面涂覆超亲水涂层,油滴仍易侵入结构内部,导致水合层被破坏。对比例3则是由于与纤维素晶体相比,四氧化三铁颗粒表面的羟基较少,在水中的分散性也较差。四氧化三铁颗粒与壳聚糖衍生物组成的涂层虽然也具有足够高的粗糙度,但涂层均匀性较差,与水作用时的氢键
网络结构也不够完善,因此涂层不具备超亲水性,并且在高粘度硅油的强烈挤压下,易被硅油侵入,导致涂层受污染。
[0082]
本发明的抗高粘度油污染的全生物基超亲水/水下超疏油涂层由壳聚糖衍生物和纤维素微纳米晶体构成,具备化学键接和氢键连接的多重交联网络,同时在多尺度粗糙结构的协同作用下,涂层获得长期稳定的超亲水性和水下超疏油特性;此外,涂层具有强大的水合能力,水合层内水被迅速、稳定地锁定在粗糙分级结构内,即使高粘度油类也难以进攻并接触到基底表面,涂层展现出优异的抗油粘附和污染性;并且本发明的制备工艺简单无污染、成本低廉、容易实现大面积生产,所制备的涂层具有生物可降解性,适用于多种基底,其中基底包括玻璃片、铁片、塑料片、陶瓷片等平面材料以及铁丝网、镍海绵、不锈钢网、聚合物海绵、聚合物织物、聚偏氟乙烯滤膜等多孔材料,当基底为多孔材料时,所述材料孔径不超过120μm。
[0083]
以上示意性的对本发明及其实施方式进行了描述,该描述没有限制性,附图中所示的也只是本发明的实施方式之一,实际的结构并不局限于此。所以,如果本领域的普通技术人员受其启示,在不脱离本发明创造宗旨的情况下,不经创造性的设计出与该技术方案相似的结构方式及实施例,均应属于本发明的保护范围。
再多了解一些
本文用于创业者技术爱好者查询,仅供学习研究,如用于商业用途,请联系技术所有人。