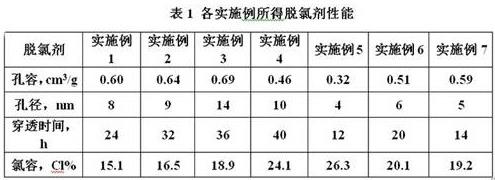
1.本发明涉及脱氯剂及制备方法技术领域,是一种重整生成油脱氯剂及其制备方法和应用。
背景技术:
2.催化重整是炼油和石油化工重要的生产工艺之一,主要反应是在双功能催化剂的作用下将环烷烃和烷烃转化为芳烃或者异构烷烃的工艺过程。目前,催化重整反应均选用含卤素氯为酸性组元的催化剂,在实际生产操作中,催化剂中氯含量受反应系统中水等的影响而逐渐流失。为了保证催化剂的活性,达到最佳水氯平衡,需要不断地注水和有机氯化物。在此过程中流失的水、氯部分积聚于重整生成油中。重整生成油在经过稳定塔(或脱戊烷塔)分馏后,塔顶得到c3、c4组分,塔底为重整汽油(或脱戊烷油)。重整生成油中少量氯的存在不仅会对塔顶产物质量产生影响,而且还会造成下游稳定系统和抽提装置的腐蚀。因此,对重整生成油进行脱氯处理是非常必要。
3.目前,工业装置中普遍采用固体脱氯剂来脱除重整生成油中的氯化氢,脱氯机理是通过脱氯剂中的活性组分与hcl发生酸碱中和反应生成稳定的金属氯化物而被固定下来,从而达到脱除hcl的目的。活性组分通常选用能与hcl反应的碱金属或碱土金属的氧化物,然后将活性组分与粘结剂通过混捏法制备形成脱氯剂,或通过浸渍法将活性组分负载到载体上制备得到。对于液相中的hcl,其扩散阻力明显比气相中的hcl分子扩散阻力大很多,因此,在制备液相脱氯剂时除了考虑活性组分外,应主要考虑脱氯剂的比表面积和孔容。现有固体脱氯剂用于重整生成油的液相脱氯时,由于其用于脱除液体油中 hcl 时,避免采用单组分碱金属或碱土金属氧化物。以共沉淀法制备的二元金属氧化物经焙烧,不仅具有具有较强的碱性,比纯组分大得多的比表面积和孔容,而且机械强度较大。比如:公开号为105542836的中国专利文献公开了一种用于重整生成油的液相脱氯的高精度液相脱氯剂,由如下组分组成:5%至20%的cuo、5%至10%的cao、4%至8%的koh、余量为改性活性炭。其制备方法是,将改性活性炭浸渍于cu-ca复合溶液中,后过滤、沥干、焙烧,将焙烧产物浸渍于koh水溶液后过滤干燥得脱氯剂。所得脱氯剂的氯容在16%以上,脱氯精度0.5ppm以下。
4.以活性炭为载体制备脱氯剂,因活性炭与活性金属组分的结合力弱,容易造成金属组分的流失。
5.公开号为110885699 的中国专利文献公开了一种大孔容孔径的脱氯剂及其制备方法和应用,由如下组分组成;碳酸钠的质量含量为5%至30%,氧化铝的质量含量为70%至95%。其制备方法是,将孔容为1.0cm3/g至1.5cm3/g、平均孔径为10nm至30nm的拟薄水铝石粉体在400℃至1000℃下焙烧,得到氧化铝粉体;将固体碳酸钠配置成碳酸钠水溶液,与所得氧化铝粉体与氢氧化铝粉体、纤维素粘结剂三者混合均匀得到混合物料;将所得的混合物料中,捏合均匀,经挤出成型、干燥、焙烧后得到脱氯剂。
6.该脱氯剂以纤维素为粘结剂,氧化铝粉体与碳酸钠混捏,存在碱性中心分布不够
均匀;碳酸钠组分质量含量≥20%时,脱氯剂松散,机械强度低。碳酸钠组分质量含量≤20%时,活性组分含量低,脱氯剂氯容低。因此,提高重整生成油液相脱氯剂的机械强度,脱氯效率及脱氯精度,是本领域需要解决的问题。
技术实现要素:
7.本发明提供了一种重整生成油脱氯剂及其制备方法,克服了上述现有技术之不足,制得的重整生成油脱氯剂活性中心分布均匀,具有较高的孔容和比表面积,液相脱氯过程中具有较高的脱氯效率及脱氯精度。
8.本发明利用酸法制取拟薄水铝石(即采用可溶性铝盐与可溶性碱进行中和反应制取拟薄水铝石),然后高温焙烧生成y-al2o3现有工艺,在此基础上,在共沉淀步骤直接引入活性组分(亚硝酸钠等),制备得到用于重整生成油的脱氯剂,由此简化了现有通过先制备出成品氧化铝再浸渍捏合生产脱氯剂的工艺步骤,有效降低生产成本,易于实现工业化生产,降低环境污染。
9.本发明的技术方案之一是通过以下措施来实现的:一种重整生成油脱氯剂的制备方法,包括下述步骤:第一步,将硝酸铝溶液与钠沉淀剂溶液在45℃至85℃下进行共沉淀反应,共沉淀反应4小时至8小时后得到含沉淀液;第二步,将含沉淀液过滤得到滤饼(含水53%至57%),将滤饼在140℃至150℃下干燥2小时至4小时;第三步,将干燥后的滤饼在450℃至700℃下焙烧4小时至6小时脱去结合水得到氧化铝粉体;第四步,将氧化铝粉体与膨润土粘结剂混合均匀得到混合物料,将混合物料经捏合、挤出成型、干燥、360℃至600℃焙烧后得到重整生成油脱氯剂。
10.在共沉淀反应过程中有硝酸钠生成,在后续过程中,滤饼中的硝酸钠分解为亚硝酸,亚硝酸钠作为碱性活性组分均匀分布在al2o3表面;氧化铝粉体中,亚硝酸钠含量为5%至35%。
11.通过调节共沉淀反应的反应液浓度来调节滤饼中硝酸钠含量,使焙烧生成的氧化铝粉体中亚硝酸钠含量达到所述要求。
12.下面是对上述发明技术方案之一的进一步优化或/和改进:上述钠沉淀剂为碳酸钠和氢氧化钠中的一种以上,当钠沉淀剂为碳酸钠和氢氧化钠两者混合物时,碳酸钠和氢氧化钠的摩尔比为0.1:1至0.6:1。
13.上述进行共沉淀反应步骤中,向反应液体中加入活性炭1%至3%(按焙烧后物料质量计)。
14.活性炭在焙烧过程中具有扩容作用同时,活性炭与部分硝酸钠反应生成碳酸钠,提高碱性组分负载在载体上的均匀度和牢固性。
15.上述混合物料在捏合过程中,加入混合物料总质量3%至10%水溶性淀粉。
16.通过捏合步骤中加入3%至10%水溶性淀粉,提高氧化铝粉体的挤出性能同时,焙烧过程中还可继续与部分亚硝酸钠反应生成碳酸钠,部分挥发有利于脱氯剂扩孔、扩容。
17.上述进行共沉淀反应步骤中,向反应液体中引入ca
2
或mg
2
。
18.为了进一步提高所述脱氯剂的氯容,改善所述脱氯剂的机械强度,在以碳酸钠或氢氧化钠或二者的混合溶液为沉淀剂,与硝酸铝溶液进行共沉淀反应的共沉淀步骤中引入ca
2
或mg
2
,通过共沉淀法制备出的前驱物具有稳定的水滑石结构,再经过高温焙烧可获得
钙铝或镁铝复合物,na
、ca
2
或na
、mg
2
作为碱性活性组分均匀分布。这类复合物不仅具有较强的碱性,而且具有大的比表面积和孔容,机械强度也较大。
19.2
可通过加入硝酸钙引入,在加入硝酸钙时,硝酸钙与硝酸铝的摩尔比为0.1:1至0.8:1;mg
2
可通过加入硝酸镁引入。
20.上述共沉淀反应的温度优选为60℃至70℃。
21.上述第三步焙烧的温度优选为550℃至650℃。
22.上述第四步干燥温度为120℃,干燥时间为2小时,焙烧的温度优选为400℃至500℃。
23.上述膨润土粘结剂加入量为氧化铝粉体与膨润土粘结剂质量之和的15%至35%。
24.上述膨润土粘结剂采用钠基或钙基膨润土。
25.本发明的技术方案之二是通过以下措施来实现的:一种根据技术方案之一所述重整生成油脱氯剂的制备方法制备得到的重整生成油脱氯剂。
26.本发明的技术方案之三通过以下措施来实现的:一种根据技术方案之二所述重整生成油脱氯剂在油品脱氯方面的应用。
27.与现有以氧化铝为载体混捏或浸渍工艺制备脱氯剂技术相比,本发明具有下述优点:(1)简化工艺步骤,有效降低生产成本,易于实现工业化生产,降低环境污染。
28.(2)本发明所述重整生成油脱氯剂以亚硝酸钠为活性中心,其结构稳定,活性中心分布均匀,具有较高的孔容和比表面,液相脱氯过程中具有较高的脱氯效率及脱氯精度。
29.(3)共沉淀步骤中引入ca
2
或mg
2
,通过共沉淀法制备出的前驱物具有稳定的水滑石结构,经过高温焙烧可获得钙铝或钙镁复合物,na
、ca
2
、mg
2
共同作为碱性活性组分,均匀分布;这类复合物不仅具有较强的碱性,而且具有大的比表面积和孔容,机械强度也较大。
30.(4)在共沉淀步骤中加入活性炭,在捏合步骤中加入水溶性淀粉,在焙烧过程中活性炭与水溶性淀粉具有扩孔、扩容作用同时,与部分硝酸钠、亚硝酸钠反应生成碳酸钠,提高碱性组分在载体上的均匀度和牢固性。
31.本发明制得的重整生成油脱氯剂的径压强度》30n/cm,可达到60n/cm;氯容15.1%至26.3%(质量);孔容0.3cm3/g至0.69cm3/g。
32.总之,本发明所述重整生成油脱氯剂适用于油品中无机氯的脱除,尤其是重整生成油中氯化氢的脱除,可将重整生成油中氯含量脱至0.5ppm(质量比)以下,具有活性高,氯容大、机械强度高,工艺简单、稳定,可操作性强等特点。
具体实施方式
33.本发明不受下述实施例的限制,可根据本发明的技术方案与实际情况来确定具体的实施方式。本发明中所提到各种化学试剂和化学用品如无特殊说明,均为现有技术中公知公用的化学试剂和化学用品;本发明中的百分数如没有特殊说明,均为质量百分数;本发明中的溶液若没有特殊说明,均为溶剂为水的水溶液,例如,盐酸溶液即为盐酸水溶液;本发明中的室温一般指15℃到25℃的温度,一般定义为25℃。
34.下面实施例制备得到的脱氯剂即为本发明所述重整生成油脱氯剂。下述实施例使
用的所述活性炭:粒度300目;亚甲基兰,ml/0.1g≥11;钠基膨润土或钙基膨润土(吸兰量≥28%,胶质价≥300ml/15g,吸水率≥150%,细度(325目)≥80%,水份≤11%)。
35.下面结合实施例对本发明作进一步描述:实施例1将固体硝酸铝(al(no3)3.9h2o)376.9g溶于1200ml去离子水中,naoh 120g溶于1100ml去离子带搅拌三口烧瓶中加入200ml去离子水做为底液。在70℃下,搅拌并流反应,1h加完,老化(即共沉淀反应)6h,抽滤。滤饼120℃干燥2小时,在马弗炉650℃下焙烧4h冷却得氧化铝粉体58.4g,na
含量9.1%(质量)。
36.实施例制1得的氧化铝粉体35.0g;钠基膨润土15.0g滴加去离子水捏合挤条(即捏合、挤出成型);120℃干燥2h;460℃焙烧4h得到脱氯剂。
37.实施例2与实施例1的不同之处在于,在共沉淀反应过程中,底液加入300目活性炭3.1g,滤饼在马弗炉中,120℃干燥2小时,450℃下焙烧2h,升温至600℃焙烧4h冷却得氧化铝粉体56.2g,na
含量9.8%(质量)。
38.实施例2制得的氧化铝粉体37.5g,钠基膨润土12.5g滴加去离子水捏合挤条;120℃干燥2h;460℃焙烧4h得到脱氯剂。
39.实施例3与实施例2的不同之处在于,将制得的氧化铝粉体37.5g,钠基膨润土12.5g,4g水溶性淀粉混合,滴加去离子水捏合挤条;120℃干燥2h;460℃焙烧4h得到脱氯剂。
40.实施例4将固体硝酸铝(al(no3)3.9h2o)(376.9g1.005mol.),ca(no3)2.4h2o (47.2g,0.2mol.)溶于800ml去离子水中;naoh 120.0g,碳酸钠21.2g溶于900ml去离子带搅拌三口烧瓶中加入200ml去离子水做为底液。在65℃下,搅拌并流反应,1h加完,老化6h,抽滤,滤饼用200ml约50℃热水洗涤。滤饼120℃干燥2小时,在马弗炉550℃下焙烧4h冷却得钙铝粉体74.1g(ca
2
%8.1;na
%4.7)。
41.实施例4制得的钙铝粉体37.5g,钙基膨润土12.5g,水溶性淀粉5g混合,滴加去离子水,捏合挤条;120℃干燥2h;460℃焙烧4h得到脱氯剂。
42.实施例5将固体硝酸铝(al(no3)3.9h2o)(376.9g1.005mol.),ca(no3)2.4h2o (141.6g,0.6mol.)溶于900ml去离子水中;naoh 120.0g,碳酸钠31.8g溶于900ml去离子带搅拌三口烧瓶中加入200ml去离子水做为底液。在65℃下,搅拌并流反应,1h加完,老化6h,抽滤,滤饼用300ml约50℃热水洗涤。滤饼120℃干燥2小时,在马弗炉550℃下焙烧4h冷却得钙铝粉体82.3g(ca
2
!.3;na
%4.1)。
43.实施例5制得的钙铝粉体37.5g,钙基膨润土12.5g,水溶性淀粉5g混合,滴加去离子水,捏合挤条;120℃干燥2h;460℃焙烧4h得到脱氯剂。
44.实施例6将固体硝酸铝(al(no3)3.9h2o)(376.9g1.005mol.),mg(no3)2.6h2o (51.3g,0.2mol.)溶于800ml去离子水中;naoh 120.0g,碳酸钠21.2g溶于900ml去离子带搅拌三口烧瓶中加入200ml去离子水做为底液。在65℃下,搅拌并流反应,1h加完,老化6h,抽滤,滤饼
用200ml约50℃热水洗涤。滤饼120℃干燥2小时,在马弗炉550℃下焙烧4h冷却得镁铝粉体70.8g(mg
2
%7.2;na
%5.4)。
45.实施例6制得的镁铝粉体37.5g,钙基膨润土12.5g,水溶性淀粉5g混合,滴加去离子水,捏合挤条;120℃干燥2h;460℃焙烧4h得到脱氯剂。
46.实施例7将固体硝酸铝(al(no3)3.9h2o)(376.9g1.005mol.),mg(no3)2.6h2o (153.9g,0.6mol.)溶于900ml去离子水中;naoh 120.0g;碳酸钠21.2g溶于900ml去离子带搅拌三口烧瓶中加入200ml去离子水做为底液。在65℃下,搅拌并流反应,1h加完,老化6h,抽滤,滤饼用300ml约50℃热水洗涤。滤饼120℃干燥2小时,在马弗炉550℃下焙烧4h冷却得镁铝粉体79.7g(mg
2 %7.2;na
%5.1)。
47.实施例7制得的镁铝粉体37.5g,钙基膨润土12.5g,水溶性淀粉5g混合,滴加去离子水,捏合挤条;120℃干燥2h;460℃焙烧4h得到脱氯剂。
48.将上述实施例1至7制得的脱氯剂进行脱氯活性、氯容评价。
49.本发明液相脱氯剂脱氯活性评价方法:将20目至40目的液相脱氯剂(即本发明的重整生成油脱氯剂)装填到内径φ8mm吸附柱中,髙径比选为8:1,温度75℃,压力选为0.8mpa,使氯含量约为5ppm的重整生成油以液空速为4h-1
(体积)进入吸附柱中(上进下出),测定流出重整生成油中的氯含量,当氯含量大于0.5ppm时,可视为穿透,记录反应时间。用时长的脱氯剂表示脱氯活性好。
50.本发明液相脱氯剂氯容评价方法:将20目至40目的液相脱氯剂装填到内径φ8mm吸附柱中,髙径比选为8:1,温度室温,压力常压,含hcl0.1% n2由流量计控制流量,空速为1000h-1
进入吸附柱,原料气从上至下经过床层,与填料接触反应,出口 hcl 浓度达到 0.5ppm 时判定实验结束。实验结束后,将反应器中的脱氯剂取出并进行氯容分析。脱氯剂的穿透氯容量(cl%)指的是评价系统的尾气中检测到0.5ppmhcl 时,单位质量的脱氯剂中所含的氯的含量。穿透氯容的计算公式如下:cl%=m
氯
/m
脱氯剂
×
100%实施例1至7制得的脱氯剂的孔容、孔径、穿透时间、氯容数据见表1。
51.表1数据表明,各实施例制得的脱氯剂具有大的比表面积、孔容和氯容。
52.以上技术特征构成了本发明的实施例,其具有较强的适应性和实施效果,可根据实际需要增减非必要的技术特征,来满足不同情况的需求。
再多了解一些
本文用于创业者技术爱好者查询,仅供学习研究,如用于商业用途,请联系技术所有人。