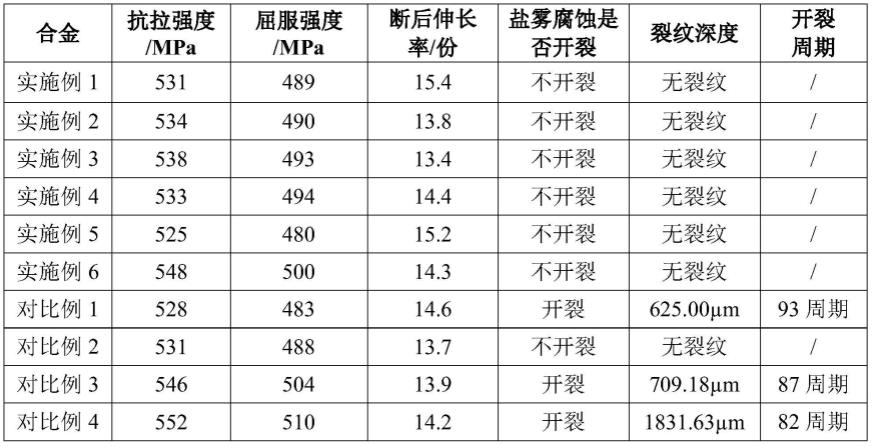
一种高强高抗应力腐蚀性能al-zn-mg铝合金及制备方法与应用
技术领域
1.本发明涉及铝合金挤压材相关技术领域,尤其是涉及一种高强高抗应力腐蚀性能al-zn-mg铝合金及制备方法与应用。
背景技术:
2.al-zn-mg铝合金因其具有良好的力学性能、易成形性、可加工性、耐腐蚀性能,被广泛应用于航空航天、轨道交通以及高端汽车制造等领域。近年来,随着新能源汽车的发展,车身零部件用铝合金挤压型材代替钢铁材料,已经成为各大汽车主机厂实现轻量化和节能减排目标的重要手段。
3.汽车用铝合金挤压型材,其一方面需要具有较高的强度,另一方面还必须具备良好的抗应力腐蚀性能。al-zn-mg铝合金以zn和mg元素为主合金成分,具有一些优点,如在高温(低于固溶温度)状态下,具有良好的塑性变形能力,可通过挤压得到各种截面形状的铝合金型材;经过在线固溶淬火及后续时效处理后析出大量的mgzn2强化相,使合金获得较高的强度。然而,现有al-zn-mg铝合金也具有一些缺点,如合金的强度与抗应力腐蚀性能的匹配度较差。当提高al-zn-mg铝合金中的zn、mg元素含量时,虽然能够保证t6时效处理后的合金获得最高的强度,但是也会增加合金的应力腐蚀开裂敏感倾向;而采用t73时效处理时,虽然能够提高合金的抗应力腐蚀性能,但却损失了合金的强度。显然,现有的al-zn-mg铝合金在强度和抗应力腐蚀性能上,难以达到综合性能的协同提高,现有的al-zn-mg铝合金制备方法均无法满足汽车零部件对高强度和高抗应力腐蚀性能al-zn-mg铝合金的需求。
4.基于此,急需一种新型的al-zn-mg铝合金,以解决上述问题。
技术实现要素:
5.本发明所要解决的第一个技术问题是:
6.提供一种al-zn-mg铝合金。
7.本发明所要解决的第二个技术问题是:
8.提供一种所述al-zn-mg铝合金的制备方法。
9.本发明所要解决的第三个技术问题是:
10.所述al-zn-mg铝合金的应用。
11.为了解决所述第一个技术问题,本发明采用的技术方案为:
12.一种al-zn-mg铝合金,按质量百分比计,包括以下组分:
13.zn:5.0%-8.0%,mg:1.50%-2.50%,cu:0.10%-0.60%,mn:0.25%-0.60%,cr≤0.15%,zr≤0.20%,ti≤0.10%,si≤0.20%,fe≤0.2%,al:85.45%-91.80%。
14.根据本发明的实施方式,所述技术方案中的一个技术方案至少具有如下优点或有益效果之一:
15.1.作为主合金元素,zn、mg含量不仅对合金的强度具有决定性的影响,同时还对合
金的耐腐蚀性能、可加工性能具有极其深远的影响,从而影响了合金的最终应用。经实验,发现zn含量与mg含量一方面共同决定了合金的强度,同时影响着合金的耐腐蚀性能,另一方面,zn含量对合金的断裂韧性具有重要影响,mg含量影响着合金的可加工性,过高的mg含量会严重降低材料的可挤压性,导致开裂、拉伤、表面质量降低等挤压缺陷。过高的zn、mg含量对应着高强度和低耐腐蚀性能,过低的zn、mg含量对应着低强度与高耐腐蚀性能。基于此,选择合适的zn、mg含量才能够使得所述al-zn-mg铝合金的各方面性能达到协同提高。
16.2.cu原子可明显提高合金抗应力腐蚀开裂性能,提高合金韧性。但过多的cu含量不仅会导致生产升本的大幅上升,降低合金经济性,也会导致合金产生晶间腐蚀与点蚀的倾向,过低的cu含量会影响合金强度。
17.3.mn含量过低时,会对合金韧性产生不利影响;而当mn含量过高时,会在合金体系中形成大量α-alfemnsi相,也会降低合金的韧性和耐蚀性能。
18.4.适当添加cr、zr元素可以形成(crfe)al7和(crmn)al
12
、al3zr相颗粒,这些颗粒可以起到细化晶粒的作用,能抑制再结晶的形核和长大,对合金的强度起到一定的提升作用,同时还可以改善合金的韧性,降低应力腐蚀开裂敏感性。
19.5.严格控制杂质元素si、fe的含量,减少合金基体中粗大alfesi结晶相的数量,有利于提高合金韧性以及耐腐蚀性能。
20.6.ti元素在铝合金中通常作为熔体变质剂使用,在铝熔体中ti与b形成大量作为形核核心的纳米级tib2颗粒,在铸造过程中起到细化晶粒的目的。
21.根据本发明的一种实施方式,所述zn的质量百分比为:5.0%-7.0%。当zn含量超过7质量百分比时,合金的抗应力腐蚀性能和断裂韧性急剧下降,尤其当zn含量超过8质量百分比时,合金的耐腐蚀性能和可焊接性能发生明显恶化,因此优选zn的质量百分比为:5.0%-7.0%。
22.根据本发明的一种实施方式,所述mg的质量百分比为:1.50%-2.0%。mg含量超过2.5质量百分比时,合金可加工性能降低,耐腐蚀性能降低,因此优选mg的质量百分比为:1.50%-2.0%。
23.根据本发明的一种实施方式,所述cu的质量百分比为:0.20%-0.40%。cu原子溶入晶内亚稳η
′
相(mgzn2相)和晶界平衡η相(mgzn2相)中可降低晶界和晶内的电位差,抑制沿晶开裂趋势,降低腐蚀环境中合金的裂纹扩展速率,可明显提高合金抗应力腐蚀开裂性能,同时cu可以细化晶界析出相,提高合金韧性。但过多的cu含量不仅会导致生产升本的大幅上升,降低合金经济性,也会导致合金产生晶间腐蚀与点蚀的倾向,尤其是cu含量超过1.5质量百分比时,合金耐腐蚀性能会明显下降。基于添加效果和经济成本的考虑,优选cu的质量百分比为:0.20%-0.40%。
24.根据本发明的一种实施方式,所述mn的质量百分比为:0.30%-0.50%。在fe含量一定时,mn含量过低或过高都会对合金产生不利影响。mn含量过低时,针状β-alfesi相不能充分向球状α-alfemnsi相转变,从而难以完全消除针状β-alfesi相对合金韧性的不利影响;而当mn含量过高时,会形成大量α-alfemnsi相,也会降低合金的韧性和耐蚀性能。除此之外,mn含量增加可显著抑制材料在挤压过程中的再结晶行为,使材料的晶粒组织呈纤维状,增加应力腐蚀裂纹沿晶扩展的难度,有利于材料抗应力腐蚀性能的提高。综合以上考虑,存在一个既可以降低针状β-alfesi相对合金耐腐蚀性能与韧性的影响,又可以尽可能
保留挤压纤维组织的mn含量范围,因此优选mn的质量百分比为:0.30%-0.50%。
25.根据本发明的一种实施方式,当所述cr的质量百分比为:0.05%-0.10%,所述zr的质量百分比为:0.10%-0.15%。适当添加cr、zr元素可以形成(crfe)al7、(crmn)al
12
和al3zr相颗粒,这些颗粒可以起到细化晶粒的作用,能抑制再结晶的形核和长大,对合金的强度起到一定的提升作用,同时还可以改善合金的韧性和应力腐蚀开裂敏感性。因此,cr、zr的含量需要搭配添加,以使得两者能够在该添加范围内起到协同效果。此外,过多的cr元素会提高合金的淬火敏感性,增加了在线淬火的冷却强度需求,提高了生产设备能力需求,应严格控制其添加量,优选cr的质量百分比为:0.05%-0.10%,所述zr的质量百分比为:0.10%-0.15%。
26.根据本发明的一种实施方式,所述si的质量百分比≤0.15%,所述fe的质量百分比≤0.15%。当合金中si、fe的含量过高,会导致合金基体中粗大alfesi结晶相的数量提高,影响合金韧性以及耐腐蚀性能,基于此,优选si的质量百分比≤0.15%,所述fe的质量百分比≤0.15%。
27.根据本发明的一种实施方式,所述ti的质量百分比为:0.02%-0.10%。ti元素在铝合金中通常作为熔体变质剂使用,在铝熔体中ti与b形成大量作为形核核心的纳米级tib2颗粒,在铸造过程中起到细化晶粒的目的。然而,过量的ti会形成容易粗化的al3ti质点,不仅不能起到细化晶粒的作用,反而会导致晶粒粗化。因此,ti含量不宜过高,优选ti的质量百分比为:0.02%-0.10%。
28.为了解决所述第二个技术问题,本发明采用的技术方案为:
29.一种制备所述al-zn-mg铝合金的方法,包括以下步骤:
30.混合所述组分,经熔炼、铸造、三级均匀化处理,得到所述al-zn-mg铝合金。
31.其中,所述三级均匀化处理包括:第一级均匀化退火温度350-355℃,第二级温度420-425℃,第三级温度480-485℃。
32.根据本发明的实施方式,所述制备所述al-zn-mg铝合金的方法,还包括以下步骤:在经过熔炼、铸造和三级均匀化处理后,再进行挤压、在线淬火冷却和人工时效处理,以得到所述al-zn-mg铝合金挤压型材。
33.根据本发明的一种实施方式,所述铸造速度为60-70mm/min,喷水冷却。
34.根据本发明的一种实施方式,所述三级均匀化处理,保温时间为1-24h,每级的升温速率控制在40-50℃/h,第三级处理保温结束后采用强风 喷雾冷却。
35.根据本发明的一种实施方式,所述挤压的工艺参数:将均匀化退火后的铸棒加热至480-500℃,放入挤压筒,通过预先加热好的模具挤压成型,得到铝合金型材半成品。模具加热温度为460-490℃,挤压速度为4-7m/min。
36.根据本发明的一种实施方式,所述在线淬火冷却工艺为:强风冷却、强风 水雾冷却或喷水冷却。
37.根据本发明的一种实施方式,所述人工时效处理制度为:采用双级时效工艺(t73),第一级时效温度为100-105℃,第二级时效温度为150-155℃,保温时间1-24h。
38.本发明的另一个方面,还涉及所述al-zn-mg铝合金在汽车制造中的应用。包括如上述第1方面实施例所述的al-zn-mg铝合金。由于该应用采用了上述实施例的al-zn-mg铝合金的全部技术方案,因此至少具有上述实施例的技术方案所带来的所有有益效果。
zn-mg铝合金。
83.实施例5
84.一种al-zn-mg铝合金,按质量百分比计,包括以下组分:
85.zn:5.0%,mg:1.50%,cu:0.10%,mn:0.25%,cr:0.15%,zr:0.20%,ti:0.10%,si:0.20%,fe:0.2%,其它元素总量≤0.15%,其余为al,总质量百分比为100%。
86.按设定比例配料,在720℃下熔炼和合金化,静置温度为700℃,随后采用半连续铸造的方法在690℃温度下浇铸出φ226的铝棒。
87.铝棒采用三级均匀化退火工艺:350℃/4h 420℃/4h 480℃/16h。
88.保温结束后,通过强风 喷雾的方式进行冷却。
89.均匀化退火后的铝棒锯切成720mm短棒并进行超声波探伤合格后,再转移到燃气炉内阶梯式升温到490℃,同时挤压筒加热温度设定为470℃。
90.随后,以5m/min的速度挤出型材,挤压比为50,采用在线强风冷却。
91.型材采用105℃/5h 155℃/10h的双级时效制度完成t73人工时效处理,得到al-zn-mg铝合金。
92.实施例6
93.一种al-zn-mg铝合金,按质量百分比计,包括以下组分:
94.zn:8.0%,mg:2.50%,cu:0.60%,mn:0.60%,cr:0.15%,zr:0.20%,ti:0.10%,si:0.20%,fe:0.2%,其它元素总量≤0.15%,其余为al,总质量百分比为100%。
95.按设定比例配料,在720℃下熔炼和合金化,静置温度为700℃,随后采用半连续铸造的方法在690℃温度下浇铸出φ226的铝棒。
96.铝棒采用三级均匀化退火工艺:350℃/4h 420℃/4h 480℃/16h。
97.保温结束后,通过强风 喷雾的方式进行冷却。
98.均匀化退火后的铝棒锯切成720mm短棒并进行超声波探伤合格后,再转移到燃气炉内阶梯式升温到490℃,同时挤压筒加热温度设定为470℃。
99.随后,以5m/min的速度挤出型材,挤压比为50,采用在线强风冷却。
100.型材采用105℃/5h 155℃/10h的双级时效制度完成t73人工时效处理,得到al-zn-mg铝合金。
101.对比例1
102.对比例1与实施例1的区别在于:组分的用量不同,其中,实施例1包括cu:0.25%,mn:0.37%,mg:1.67%,zn:6.75%。对比例1包括cu:0.15%,mn:0.25%,mg:2.10%,zn:8.30%。
103.一种合金,按质量百分比计,包括以下组分:
104.si:0.08%,fe:0.10%,cu:0.15%,mn:0.25%,mg:2.10%,cr:0.08%,zn:8.30%,zr:0.12%,ti:0.06%,其它元素总量≤0.15%,其余为al,总质量百分比为100%。
105.按设定比例配料,在720℃下熔炼和合金化,静置温度为700℃,随后采用半连续铸造的方法在690℃温度下浇铸出φ226的铝棒。
106.铝棒采用三级均匀化退火工艺:350℃/4h 420℃/4h 480℃/16h。
107.保温结束后,通过强风 喷雾的方式进行冷却。
108.均匀化退火后的铝棒锯切成720mm短棒并进行超声波探伤合格后,再转移到燃气
炉内阶梯式升温到490℃,同时挤压筒加热温度设定为470℃。
109.随后,以5m/min的速度挤出型材,挤压比为50,采用在线强风冷却。
110.型材采用105℃/5h 155℃/10h的双级时效制度完成t73人工时效处理,得到al-zn-mg铝合金。
111.对比例2
112.对比例2与实施例1的区别在于:组分用量不同。其中,实施例1的组分包括fe:0.10%,cu:0.25%,mn:0.37%,mg:1.67%,zn:6.75%。对比例2的组分包括fe:0.10%,cu:0.45%,mn:0.35%,mg:2.20%,zn:7.50%。
113.一种合金,按质量百分比计,包括以下组分:
114.si:0.08%,fe:0.10%,cu:0.45%,mn:0.35%,mg:2.20%,cr:0.08%,zn:7.50%,zr:0.12%,ti:0.06%,其它元素总量≤0.15%,其余为al,总质量百分比为100%。
115.按设定比例配料,在720℃下熔炼和合金化,静置温度为700℃,随后采用半连续铸造的方法在690℃温度下浇铸出φ226的铝棒。
116.铝棒采用三级均匀化退火工艺:350℃/4h 420℃/4h 480℃/16h。
117.保温结束后,通过强风 喷雾的方式进行冷却。
118.均匀化退火后的铝棒锯切成720mm短棒并进行超声波探伤合格后,再转移到燃气炉内阶梯式升温到490℃,同时挤压筒加热温度设定为470℃。
119.随后,以5m/min的速度挤出型材,挤压比为50,采用在线强风冷却。
120.型材采用105℃/5h 155℃/10h的双级时效制度完成t73人工时效处理,得到al-zn-mg铝合金。
121.对比例3
122.对比例3与实施例1的区别在于:组分用量不同。其中,实施例1的组分包括,cu:0.25%,mn:0.37%,mg:1.67%,zn:6.75%。对比例3的组分包括:cu:0.65%,mn:0.25%,mg:2.40%,zn:7.6%。
123.一种合金,按质量百分比计,包括以下组分:
124.si:0.08%,fe:0.10%,cu:0.65%,mn:0.25%,mg:2.40%,cr:0.08%,zn:7.6%,zr:0.12%,ti:0.06%,其它元素总量≤0.15%,其余为al,总质量百分比为100%。
125.按设定比例配料,在720℃下熔炼和合金化,静置温度为700℃,随后采用半连续铸造的方法在690℃温度下浇铸出φ226的铝棒。
126.铝棒采用三级均匀化退火工艺:350℃/4h 420℃/4h 480℃/16h。
127.保温结束后,通过强风 喷雾的方式进行冷却。
128.均匀化退火后的铝棒锯切成720mm短棒并进行超声波探伤合格后,再转移到燃气炉内阶梯式升温到490℃,同时挤压筒加热温度设定为470℃。
129.随后,以5m/min的速度挤出型材,挤压比为50,采用在线强风冷却。
130.型材采用105℃/5h 155℃/10h的双级时效制度完成t73人工时效处理,得到al-zn-mg铝合金。
131.对比例4
132.对比例4与实施例1的区别在于:组分用量不同。其中,实施例1的组分包括:cu:0.25%,mn:0.37%,mg:1.67%,zn:6.75%。对比例4的组分包括:cu:0.05%,mn:0.45%,
mg:2.80%,zn:8.50%。
133.一种合金,按质量百分比计,包括以下组分:
134.si:0.08%,fe:0.10%,cu:0.05%,mn:0.45%,mg:2.80%,cr:0.08%,zn:8.50%,zr:0.12%,ti:0.06%,其它元素总量≤0.15%,其余为al,总质量百分比为100%。
135.按设定比例配料,在720℃下熔炼和合金化,静置温度为700℃,随后采用半连续铸造的方法在690℃温度下浇铸出φ226的铝棒。
136.铝棒采用三级均匀化退火工艺:350℃/4h 420℃/4h 480℃/16h。
137.保温结束后,通过强风 喷雾的方式进行冷却。
138.均匀化退火后的铝棒锯切成720mm短棒并进行超声波探伤合格后,再转移到燃气炉内阶梯式升温到490℃,同时挤压筒加热温度设定为470℃。
139.随后,以5m/min的速度挤出型材,挤压比为50,采用在线强风冷却。
140.型材采用105℃/5h 155℃/10h的双级时效制度完成t73人工时效处理,得到al-zn-mg铝合金。
141.性能测试:
142.拉伸性能测试:按《gb/t 228.1-2010金属材料拉伸试验第1部分室温拉伸试验方法》上述进行测试,沿型材纵向截取200
×
20mm尺寸样条,采用cnc加工成a50拉伸试片,在legend 2382万能试验机上进行拉伸至断裂,读取强度数值并计算断后伸长率,原始标距为50mm。
143.抗应力腐蚀性能:将100
×
20mm的样品采用三点弯曲工装通过施加压力的方式固定,放置于ly-fh-120l复合交变循环盐雾试验机内。样品倾斜角度为20
±5°
,氯化钠盐水浓度为0.5wt.%,测试环境温度为25℃,试验反复循环100个周期,每个周期分别经过喷雾、外气导入、湿润、干燥的条件试验,并每隔10周期观察一次样品,采用目视检查的方法判断样品表面有无开裂裂纹。如观察到试样表面有裂纹,则切剖侧面进行裂纹深度记录,裂纹照片如图1所示。其中,图1的(a)为实施例3的低倍裂纹形貌、图1的(b)为实施例3的剖面高倍裂纹扩展图;图1的(c)为对比例1的低倍裂纹形貌、图1的(d)为对比例1的剖面高倍裂纹扩展图;
144.图1的(e)为对比例3的低倍裂纹形貌、图1的(f)为对比例3的剖面高倍裂纹扩展图;图1的(g)为对比例4的低倍裂纹形貌、图1的(h)为对比例4的剖面高倍裂纹扩展图。
145.表1为室温拉伸性能和抗应力腐蚀性能检测结果。
146.表1
[0147][0148]
以上仅为本发明的实施例,并非因此限制本发明的专利范围,凡是利用本发明说明书内容所作的等同变换,或直接或间接运用在相关的技术领域,均同理包括在本发明的专利保护范围内。
再多了解一些
本文用于创业者技术爱好者查询,仅供学习研究,如用于商业用途,请联系技术所有人。