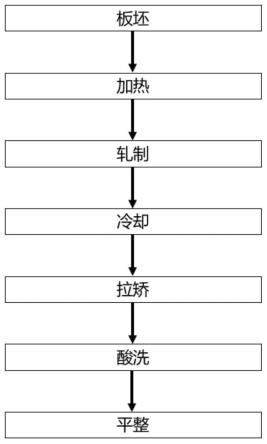
1.本发明属于钢板生产领域,更具体地说,涉及一种薄规格超高强钢板综合质量的控制方法。
背景技术:
2.随着专用车、工程机械用钢高强化趋势的发展以及轧制冷却技术尤其是超快冷冷却装备的升级,近年来相变强化型热轧超高强钢(抗拉强度rm≥1000mpa)成为研究热点,产品强化途径主要通过轧后超快冷冷却系统进行在线直接淬火实现,产品强化方式主要为相变强化。
3.相对于传统细晶强化、析出强化、位错强化等,相变强化途径对于提高材料强度的贡献最显著,可以减少合金元素的添加量,且产品屈强比较低,有利于提高冷弯性能。因此,通过相变强化途径生产的材料具有高强度、易成形、生产成本低等优点。但是,相变强化型热轧超高强钢生产或应用存在以下问题,主要以下三点:(1)为了保证产品冷却空冷段可以形成一定比例软相铁素体组织,采用高si(si含量≥1.0%)化学成分设计,材料表面均为红色氧化铁皮,表面质量较差;(2)冷却采用分段冷却模式,因冷却速率快、冷却工艺窗口窄、温度波动对相变转变影响大等因素影响,相变强化型热轧超高强钢的力学性能波动较大,屈服强度、抗拉强度波动范围高达200mpa,相变强化型热轧超高强钢的性能均匀性难以控制;(3)厚度规格薄(≤6mm),轧制压力大、轧后冷却速率快,卷取温度低(≤300℃)且卷取温度命中率较差,轧制冷却后板形问题突出,浪高高达20-30mm/m。
4.关于相变强化型热轧超高强钢(rm≥1000mpa)的申报专利,如公开号为cn103233161b、cn110331326a、cn104532126a、cn110257725a的专利,主要解决的技术问题为如何通过减量化合金成分设计并结合轧制、冷却工艺的优化实现超高强、高耐磨和易成形三者性能的协调控制,没有同时涉及到材料表面质量、性能均匀性、板形方面的技术问题。
5.公开号为cn108411203b的专利,公开了高硅高铝混凝土搅拌车用nm300耐磨钢及生产方法,其板形控制策略主要为热轧卷钢卷进行冷轧罩退回火处理,需要在现有生产线基础上增加工序,工艺流程长且未涉及到表面质量和性能均匀性控制方面。
6.公开号为cn114011885a的专利,公开了一种吉帕级热轧高强钢轧制过程板形控制方法,其主要强调采用边部加热器、精轧微中浪轧制和密集型连续冷却的思路,但一方面,其轧后直接连续冷却至150~300℃卷取,卷取温度均匀性难以控制,而卷取温度会显著影响材料的屈服强度、屈强比,进而材料的力学性能均匀性难以控制;另一方面,轧制采用连续冷却会增加带钢在冷却段停留时间、增加宽度或长度方向相变的不一致性,进而增加材料板形控制难度,且没有涉及材料表面质量、性能均匀性方面。
7.关于提高材料性能均匀性申报的专利,如公开号为cn107824614a、cn107483784b、cn104576467b、cn103031414b、cn113244557a、cn112063815a、cn103031414b的专利,则分为以下几种情况:(1)研究对象集中在细晶强化型或析出强化型热轧高强钢(rm≤700mpa)或
厚度规格较厚的中厚板,没有关于薄规格(≤6mm)相变强化型热轧超高强钢(rm≥1000mpa);2)研究对象为780mpa级相变强化型冷轧高强钢,产品强度级别较低且主要通过优化后续退火工序提高带钢长度方向性能均匀性,热轧工序参数优化以及宽度方向并未涉及;(3)通过分段头尾遮蔽或u型冷却工艺提高带钢长度方向性能均匀性,宽度方向性能均匀性并未涉及;(4)通过在卷取机后增设在线保温罩设备,但该种方法仅适用于析出强化型高强钢的性能均匀性提升,并不适用于相变强化型超高强钢,且需要新增设备投资。
8.综上所述,现有技术尚没有完善的同时涉及提高相变强化型热轧超高强钢(rm≥1000mpa,厚度≤6mm)的表面质量、性能均匀性以及板形质量的技术方案,相变强化型板坯中的薄规格超高强钢板的综合质量难以提升。
技术实现要素:
9.1、要解决的问题
10.针对现有技术难以完善地提升相变强化型薄规格超高强钢板的综合质量的问题,本发明提供一种薄规格超高强钢板综合质量的控制方法,通过合理的加热、轧制、冷却、拉矫、酸洗以及平整工艺的优化,能够有效提升钢板的综合质量,解决了相变强化型薄规格超高强热轧钢板表面质量差、力学性能波动大、板形控制难的问题。
11.2、技术方案
12.为解决上述问题,本发明采用如下的技术方案。
13.一种薄规格超高强钢板综合质量的控制方法,包括以下步骤:
14.1)加热
15.将板坯送入加热炉进行加热,板坯出炉温度为1250~1300℃;
16.2)轧制
17.采用2机架粗轧和7机架精轧热连轧机组进行轧制,精轧f7机架出口终轧温度为840~840℃,轧制对中线控制为-20~ 20mm,凸度c40=20-30μm,对称平直度为-50~0i,终轧速度≥8m/s,c40为带钢横截面中点厚度与距离两侧边部40mm位置处平均厚度的差值;
18.3)冷却
19.板坯轧制后,对板坯进行三段冷却,依次为超快速冷却、空冷和水冷,水冷后进行卷取;
20.4)拉矫
21.对卷取后冷却至室温的钢卷依次进行开卷、激光焊接和拉矫;
22.5)酸洗
23.带钢拉矫后进行酸洗,采用三段连续式盐酸酸洗,酸液温度70~80℃,酸洗速率为30-50m/min;
24.6)平整
25.酸洗后经过漂洗、烘干,然后进行在线平整,采用延伸率模式,平整延伸率为0.4-0.8%。
26.作为技术方案的进一步改进,板坯送入加热炉后,依次进入预热段、一次加热段、二次加热段和均热段,一次加热段末温度为480~1030℃,二次加热段末温度为1180~1230℃,均热段温度为1250~1300℃,均热时间为20-30min。
27.作为技术方案的进一步改进,轧制时,板坯出加热炉后进行一次高压水除鳞,除鳞水压力为180-230bar,粗轧机组r1机架第1、3道次和r2机架第2、4道次投用道次除鳞水,粗轧结束的中间坯经过保温罩后进行二次高压水除磷,除鳞水压力为300~350bar。
28.作为技术方案的进一步改进,超快速冷却段采用集中冷却且投用边部遮挡工艺,冷却速率≥80℃/s,边部遮挡距离为100~150mm,带钢上下表面的冷却水流量比为(1:1.15)~(1:1.30),侧喷水为对称交叉侧喷。
29.作为技术方案的进一步改进,空冷段空冷至640-680℃后进行水冷。
30.作为技术方案的进一步改进,水冷段采用稀疏冷却方式,带钢上下表面的冷却水流量比为(1:1.05)~(1:1.15),侧喷水为对称交叉侧喷,冷却速率为50~80℃/s。
31.作为技术方案的进一步改进,卷取温度≤100℃。
32.作为技术方案的进一步改进,拉矫机为两弯一矫型,拉矫延伸率为0.8~1.2%,拉矫机张力为50~80kn。
33.作为技术方案的进一步改进,平整机的弯辊力为400-600kn,入口张力为140~160kn,出口张力为180-200kn。
34.3、有益效果
35.(1)本发明一种薄规格超高强钢板综合质量的控制方法,超高强钢酸洗后表面质量良好,无明显色差,可免去后续下游制造企业的抛瓦工序,降低下游制造企业的制造成本。
36.(2)本发明一种薄规格超高强钢板综合质量的控制方法,在不新增设备的情况下,通过合理的加热、轧制、冷却、拉矫、酸洗以及平整工艺的优化,能够有效提升钢板的综合质量,产品屈服强度≥700mpa,抗拉强度≥1000mpa,且宽度、长度方向屈服强度波动范围≤70mpa,抗拉强度波动范围≤60mpa,开平板不平度≤6mm/m,较好的解决了相变强化型薄规格超高强热轧钢板力学性能波动大、板形控制难的问题。
附图说明
37.图1为本发明控制方法的工艺流程图;
38.图2为实施例1的带钢分别在宽度和长度方向上的力学性能波动折线图;
39.图3为实施例2的带钢分别在宽度和长度方向上的力学性能波动折线图;
40.图4为实施例3的带钢分别在宽度和长度方向上的力学性能波动折线图;
41.图5为对比例1的带钢分别在宽度和长度方向上的力学性能波动折线图;
42.图6为对比例2的带钢分别在宽度和长度方向上的力学性能波动折线图;
43.图7为对比例3的带钢分别在宽度和长度方向上的力学性能波动折线图;
44.图8为酸洗平整后超高强钢板形图。
具体实施方式
45.下文对本发明的示例性实施例进行了详细描述。尽管这些示例性实施例被充分详细地描述以使得本领域技术人员能够实施本发明,但应当理解可实现其他实施例且可在不脱离本发明的精神和范围的情况下对本发明作各种改变。下文对本发明的实施例的更详细的描述并不用于限制所要求的本发明的范围,而仅仅为了进行举例说明且不限制对本发明
的特点和特征的描述,以提出执行本发明的最佳方式,并足以使得本领域技术人员能够实施本发明。因此,本发明的范围仅由所附权利要求来限定。
46.一种薄规格超高强钢板综合质量的控制方法,针对于厚度≤6mm,抗拉强度rm≥1000mpa的相变强化型超高强钢板,能够有效提升其综合质量。其中,钢板的化学成分及其质量百分比为:c:0.08~0.13%,si:0.80-1.50%,mn:1.20~1.80%,p:≤0.015%,s:≤0.005%,als:0.30~0.50%,ti:0.015~0.040%,b:0.0006~0.0012%,其余为fe及不可避免的夹杂。下面对其过程和原理进行详细描述。
47.如图1所示,该方法包括以下步骤:
48.1)加热
49.板坯进入加热炉后,依次进入预热段、一次加热段、二次加热段和均热段,其中,预热段温度和时间不做限定,达到本领域规定的预热效果即可。一次加热段末温度为480~1030℃,二次加热段末温度为1180~1230℃,均热段温度为1250~1300℃,均热时间为20-30min。需要说明的是,一次加热段和二次加热段结束时需要保温5~10分钟,使板坯内的组织发生变化,为后续板坯轧制、冷却、酸洗以及平整工序进行铺垫,板坯在加热炉内的整体加热时间一般为180~210分钟。
50.该步骤中,采用高温加热的目的在于控制粗轧前高压水除鳞时板坯温度》1173℃,保证铁橄榄石fe2sio4为熔融态、易于去除,防止fe2sio4钉轧在钢板基体表面,难以去除。综合考虑板坯烧透、氧化铁皮生成量等因素,板坯高温均热段时间不宜过长,控制在20-30min。
51.2)轧制
52.采用2机架粗轧和7机架精轧热连轧机组进行轧制,精轧f7机架出口终轧温度为840~840℃,轧制对中线控制为-20~ 20mm,凸度c40=20-30μm,对称平直度为-50~0i,终轧速度≥8m/s,c40为带钢横截面中点厚度与距离两侧边部40mm位置处平均厚度的差值。
53.轧制时,板坯出加热炉后进行一次高压水除鳞,除鳞水压力为180-230bar,粗轧机组r1机架第1、3道次和r2机架第2、4道次投用道次除鳞水,本实施方式中,rx表示连轧机组轧制方向上的第x架机架。粗轧结束的中间坯经过保温罩后进行二次高压水除磷,除鳞水压力为300~350bar。
54.该步骤中,粗轧和精轧前投用高压水除磷、粗轧道次间除磷、提高精轧出口轧制速度,以及采用低温轧制均是为了控制减少轧制过程中氧化铁皮生成量和高压水除鳞后氧化铁皮残余量,为提高酸洗后钢板表面质量提供基础。控制轧制对中线在-20~ 20mm主要是基于控制超快冷段板宽方向两侧边部冷却水遮挡量相同、提高边部遮挡对于宽度方向温度、性能均匀性考虑。f7机架出口带钢凸度为20-30μm主要是为了避免带钢轧制出现双边浪以及提高宽度方向厚度尺寸精度,有利于带钢层流冷却宽度方向温度均匀性控制。对称平直度为-50~0i是为了采用微中浪轧制,使带钢形成微小中浪,增加带钢宽度方向中间位置变形量,避免因带钢冷却时宽度方向不均匀性变形(两侧边部变形量大、中间变形量小)导致的双边浪,进而有利于提高板形质量。
55.3)冷却
56.板坯轧制后,对板坯进行三段冷却,依次为超快速冷却、空冷和水冷。其中,超快速冷却段采用集中冷却且投用边部遮挡工艺,冷却速率≥80℃/s,边部遮挡距离为100~
150mm,带钢上下表面的冷却水流量比为(1:1.15)~(1:1.30),侧喷水为对称交叉侧喷。空冷段空冷至640-680℃后进行水冷,水冷段采用稀疏冷却方式,带钢上下表面的冷却水流量比为(1:1.05)~(1:1.15),侧喷水为对称交叉侧喷,冷却速率为50~80℃/s。水冷后进行卷取,卷取温度ct≤100℃。
57.该步骤中,采用超快冷-空冷-水冷三段冷却模式主要是为了获得铁素体 马氏体双相组织。为了控制超快冷段、水冷段带钢宽度方向的温度均匀性,主要通过采用控制上下冷却水比、交叉对称侧喷和边部遮挡等措施,超快冷段和水冷段上冷却水比下冷却水开的少的目的主要是避免上冷却水过多在带钢上表面残留、集聚导致带钢宽度方向温度分布不均匀、不利于带钢宽度方向性能均匀性。超快冷段投用边部遮挡主要为了提高带钢宽度方向温度和性能均匀性,水冷段采用稀疏冷却和水冷冷却速率为50~80℃/s,主要是为了尽可能降低冷却速率,避免因冷却速率过大产生组织应力和相变应力导致带钢产生冷却单边浪和双边浪,不利于宽度温度、性能均匀性。
58.空冷段结束温度为640~680℃,一方面是基于材料组织性能控制需要,保证材料获得一定比例铁素体组织;另一方面是控制带钢表面氧化铁皮中的疏松相feo比例,保证feo不发生共析转变,疏松相feo酸洗过程易去除,有利于酸洗后表面质量提升。此外,采用低温卷取工艺主要是为了控制带钢宽度和长度方向卷取温度的均匀性,避免宽度方向卷取温度波动对材料力学性能和板形的不利影响。
59.4)拉矫
60.卷取后冷却至室温的热卷,依次进行开卷、激光焊接、拉矫,拉矫机为两弯一矫型,拉矫延伸率为0.8~1.2%,拉矫机张力为50~80kn。
61.5)酸洗
62.带钢拉矫后进行酸洗,采用三段连续式盐酸酸洗,酸液温度70~80℃,酸洗速率为30-50m/min。
63.6)平整
64.酸洗后经过漂洗、烘干,然后进行在线平整,采用延伸率模式,平整延伸率为0.4-0.8%,弯辊力为400-600kn,平整机入口张力为140~160kn,出口张力为180-200kn,平整后带钢表面不涂油,如图2所示,最终卷取得到超高强热轧酸洗钢板成品。
65.本实施方式采用酸洗前拉矫 酸洗后在线平整工艺,主要目的是利用拉矫、平整工艺改善超高强热轧带钢板形、性能均匀性,这也是本实施方式的创新之处。带钢在拉矫机组张力作用下,连续通过上下交替布置的小辊径弯曲辊并剧烈弯曲,在拉伸应力和弯曲应力的综合作用下,带钢宽度方向上的各纵向纤维单元的长度趋于一致,进而减小内应力分布的不均匀性,有利于减少带钢双边浪、单边浪等板形缺陷。同时,酸洗后进行在线平整工艺,通过平整延伸率、弯辊力和张力的协调配合,进一步提高其板形和宽度方向性能均匀性。
66.对于薄规格高si超高强钢而言,拉矫延伸率过小,改善板形效果、破鳞效果不足,拉矫延伸率过大,不仅会造成拉矫张力增加、增加酸洗机组断带风险,而且会引起失衡造成的不均匀变形,反而不利于改善板形,综合考虑,拉矫延伸率控制在0.8~1.2%,拉矫机张力控制在50~80kn。平整后带钢表面不涂油主要为了防止带钢表面涂油后影响最终成品表面喷涂油漆的附着性以及外观美观性。
67.酸洗工艺上则主要通过拉矫延伸率、酸洗速率、酸液温度参数等控制其表面质量,
考虑到高si钢氧化铁皮厚度较厚和酸洗后平整工艺稳定性,酸洗速率控制在30-50m/min,酸洗速率不宜过快,否则表面质量、板形均难以保证。
68.综上所述,该薄规格超高强钢板综合质量的控制方法,在不新增设备的情况下,通过合理的加热、轧制、冷却、拉矫、酸洗以及平整工艺的优化,能够有效提升钢板的综合质量,产品屈服强度≥700mpa,抗拉强度≥1000mpa,且宽度、长度方向屈服强度波动范围≤70mpa,抗拉强度波动范围≤60mpa,开平板不平度≤6mm/m,且表面质量好,解决了相变强化型薄规格超高强热轧钢板表面质量差、力学性能波动大、板形控制难的问题。
69.必须说明的是,该方法强调的是从加热-轧制-冷却-卷取-拉矫-酸洗-平整全流程工序的角度进行相变强化型超高强钢板的综合质量的提高,而不是单独通过加热、轧制、冷却、卷取、拉矫、酸洗、平整中的某个工序的某个工艺参数进行优化控制。因此,必须从加热-轧制-冷却-卷取-拉矫-酸洗-平整全流程工序的角度进行相变强化型超高强钢板的综合质量控制,才能获得所需性能的钢卷。
70.下面通过具体实施例、对比例对本发明的技术方案予以说明。
71.实施例1-3和对比例1-3的化学成分及重量百分比含量均为:0.11%c、1.10%si、1.74%mn、0.011%p、0.002%s、0.45%als、0.023%ti,0.0008%b。其余为fe及不可避免的夹杂。通过加热、轧制、冷却、拉矫、酸洗、平整工艺,实施例和对比例具体工艺参数见表1-3所示。
72.力学性能均匀性评价方法如下:酸洗后带钢头部、尾部分别取1块全板宽试样,每块全板宽试样在宽度方向按等间距切取10根纵向拉伸试样,合计20根,并根据gb/t 228.1进行室温拉伸试验获得材料的屈服强度、抗拉强度指标。力学性能均匀性以宽度、长度方向的屈服强度、抗拉强度波动范围为指标,宽度方向屈服强度波动范围=max(10根拉伸试样的屈服强度)-min(10根拉伸试样的屈服强度),宽度方向抗拉强度波动范围=max(10根拉伸试样的抗拉强度)-min(10根拉伸试样的抗拉强度)。长度方向屈服强度的波动范围=max(相同宽度位置对应的头部、尾部屈服强度)-min(相同宽度位置对应的头部、尾部屈服强度),长度方向抗拉强度的波动范围=max(相同宽度位置对应的头部、尾部的抗拉强度)-min(相同宽度位置对应的头部、尾部的抗拉强度)。
73.实施例1-3和对比例1-3对应的超高强钢宽度和长度方向性能分布见图3-7所示,宽度、长度方向的屈服强度和抗拉强度波动范围见表4所示,实施例对应的超高强钢屈服强度波动范围≤70mpa、抗拉强度波动范围≤60mpa。
74.实施例1-3和对比例1-3对应的超高强钢开平板不平度见表5所示,实施例对应的超高强钢酸洗后开平板对应的不平度≤6mm/m。
75.表1实施例及对比例的加热、轧制工艺参数
76.[0077][0078]
表2实施例及对比例的冷却工艺参数
[0079][0080]
表3实施例及对比例的拉矫、酸洗、平整工艺参数
[0081][0082]
表4实施例及对比例对应的超高强钢宽度、长度方向性能波动
[0083][0084]
表4实施例及对比例的超高强钢开平板不平度
[0085]
[0086][0087]
本发明所述实例仅仅是对本发明的优选实施方式进行描述,并非对本发明构思和范围进行限定,在不脱离本发明设计思想的前提下,本领域工程技术人员对本发明的技术方案作出的各种变形和改进,均应落入本发明的保护范围。
再多了解一些
本文用于创业者技术爱好者查询,仅供学习研究,如用于商业用途,请联系技术所有人。