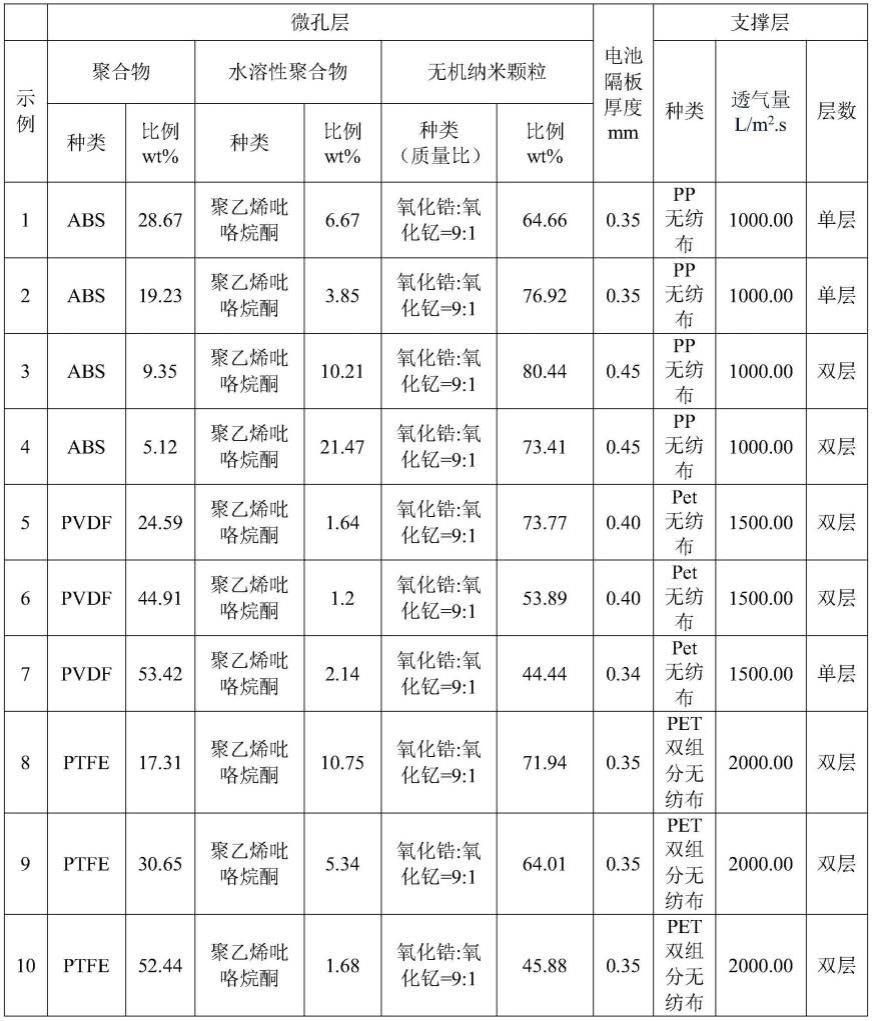
1.本发明涉及电池技术领域,更具体地讲,涉及一种电池隔板及其制备方法。
背景技术:
2.蓄电池包括阳极、阴极、电解质以及电池隔板。通常,阳极是易于氧化的活性材料,阴极是易于还原的活性材料,电子从阳极通过外部负载流向阴极,离子流过电解质从阴极到阳极。隔板位于阳极和阴极之间,存在于电解质中,一方面避免电子传输,导致内部短路放电,另一方面确保离子能够正常传输。
3.蓄电池被分类为“一次”或“充电”电池。一次电池不能通过施加反向电压再次充电使用,是常见的一次性电池。充电电池涉及相对可逆的电极反应,并且可以进行多次充电-放电循环。对于充电电池的隔板必须经受住反复的充放电循环,比一次电池隔板要求更高。
4.对于包含高氧化性阴极、高还原性阳极和碱性电解质的充电电池,例如锌-氧化银电池,隔膜要求更为严格。首先,隔板必须在强碱性溶液中化学稳定,与高氧化性阴极接触时抗氧化,与高还原性阳极接触时抗还原。此外,阴极可能衍生金属氧化物离子,在碱性电解质溶液中可能有些溶解,易在隔板表面被化学还原成金属,因此,隔板还必须抑制金属离子的传输和/或化学还原。再者,阳极在充电过程中有形成枝晶的可能,因此隔板还必须抑制枝晶生长和/或抵抗枝晶穿透,以避免由于在电极之间形成枝晶短路而导致的故障。
5.传统的隔板在碱性电解质中易发生化学分解,与银等电极可能发生化学氧化,且机械强度低,抗枝晶穿透能力差,这些都限制了电池的使用寿命。
6.为了解决传统隔板化学稳定性差、穿刺强度差的问题,亟需一种新的电池隔板。
技术实现要素:
7.针对现有技术中存在的不足,本发明的目的之一在于解决上述现有技术中存在的一个或多个问题。例如,本发明的目的之一在于提供一种化学稳定性好、穿刺强度高的电池隔板。
8.本发明的一方面提供了一种电池隔板,可以包括至少一层微孔层和位于微孔层侧面的支撑层,其中,微孔层可以abs聚合物、pvdf聚合物和ptfe聚合物中的任意一种,以及水溶性聚合物和无机纳米颗粒。
9.进一步地,按质量百分比计,微孔层可以包括5%-30%的abs聚合物、1%-25%的水溶性聚合物以及60%-85%的无机纳米颗粒。
10.进一步地,abs聚合物的熔融指数可以为5g-15g/10min。
11.进一步地,电池隔板电阻可以不大于2000ohm.cm2。
12.进一步地,按质量百分比计,微孔层可以包括20%-55%的pvdf聚合物、1%-5%的水溶性聚合物以及40%-75%的无机纳米颗粒。
13.进一步地,pvdf聚合物的分子量可以为200000amu-700000amu。
14.进一步地,电池隔板电阻可以不大于20ohm.cm2。
15.进一步地,按质量百分比计,微孔层可以包括15%-55%的ptfe聚合物、1%-12%的水溶性聚合物以及40%-75%的无机纳米颗粒。
16.进一步地,ptfe聚合物的分子量可以为500000amu-1000000amu。
17.进一步地,电池隔板电阻可以不大于35ohm.cm2。
18.进一步地,水溶性聚合物可以包括聚乙烯吡咯烷酮、聚乙烯醇、聚丙烯酸、卡波普尔、聚乙二醇和聚苯乙烯磺酸中的一种或几种组合。
19.进一步地,无机纳米颗粒可以包括氧化锆和/或氧化钇。
20.进一步地,无机纳米颗粒的bet比表面积可以不小于5m2/g,颗粒直径可以为30nm-500nm。
21.进一步地,无机纳米颗粒还可以包括二氧化钛,二氧化钛含量可以为150ppm-500ppm。
22.进一步地,电池隔板厚度可以为0.25mm-0.75mm。
23.进一步地,支撑层可以为纤维无纺结构,其材料可以为pe、pp、pet、pbt中一种或多种纤维混合湿法抄造而成。
24.进一步地,支撑层可以包含双组分纤维,双组分纤维可以为心皮结构,心层聚合物熔点温度较皮层聚合物熔点温度至少高50℃,支撑层透气量不小于500l/m2.s。
25.本发明的另一方面提供了一种电池隔板的制备方法,可以包括以下步骤:将abs聚合物或pvdf聚合物、水溶性聚合物、无机纳米颗粒按比例混入丙酮溶液中,充分搅拌至充分混合,得到混合溶液;在混合溶液中加入质量占比1%-3%的十二烷基苯磺酸和0.4%-0.8%邻苯二甲酸二丁酯,继续搅拌混合;混合后浇铸,刮涂,形成0.25-0.75mm厚的薄层;在室温下静置,并在薄层表面浇洗异丙醇,去离子水润湿后室温干燥,剥离后得微孔层;将微孔层与支撑层组装得电池隔板。
26.本发明的再一方面提供了一种电池隔板的制备方法,包括以下步骤:将ptfe聚合物、水溶性聚合物、无机纳米颗粒按比例混入丙酮溶液中,充分搅拌,成糊状混合物;将糊状混合物在40℃-50℃下加热熟化,熟化结束后压延成条状坯;将条状坯在100℃-120℃温度下纵向拉伸,得纵向拉伸膜坯;将纵向拉伸膜坯在190℃-210℃下进行横向、纵向双向拉伸,并在340℃-360℃下固化,得到微孔层;将微孔层与支撑层组装得电池隔板。
27.与现有技术相比,本发明的有益效果至少包括:本发明的电池隔板有好的化学稳定性和高的穿刺强度;制备方法简单,工艺流程短。
具体实施方式
28.在下文中,将结合示例性实施例详细地描述根据本发明的一种电池隔板及其制备方法。
29.本发明的一方面提供了一种电池隔板,在电池隔板的一个示例性实施例中,包括至少一层微孔层和位于微孔层侧面的支撑层。其中,电池隔板可以包含一层、二层、三层或者四层以上的微孔层。微孔层的一侧或者两则设置有支撑层,用于对微孔层的支撑。
30.微孔层可以包括abs聚合物(丙烯腈-苯乙烯-丁二烯共聚物)、pvdf(聚偏二氟乙烯聚合物)聚合物和ptfe聚合物(聚四氟乙烯聚合物)中的任意一种,以及水溶性聚合物和无机纳米颗粒。即微孔层可以包括水溶性聚合物、无机纳米颗粒以及abs聚合物,或者由水溶
~24ohm.cm2、20ohm.cm2~21ohm.cm2或以上范围的组合。
35.在一些实施方案中,ptfe聚合物的分子量可以为500000amu-1000000amu。例如,ptfe聚合物的分子量可以为510000amu-900000amu、580000amu-820000amu、630000amu-790000amu、660000amu-710000amu或以上范围的组合。
36.在一些实施方案中,水溶性聚合物可以包括聚乙烯吡咯烷酮、聚乙烯醇、聚丙烯酸、卡波普尔、聚乙二醇和聚苯乙烯磺酸中的一种或几种组合。当然,应当理解的是,本领域已知的其他水溶性聚合物亦可。
37.在一些实施方案中,无机纳米颗粒可以包括氧化锆和氧化钇中的一种或混合物。优选地,无机纳米颗粒包括氧化锆和氧化钇的混合物。
38.在一些实施方案中,无机纳米颗粒的bet比表面积可以不小于5m2/g。例如,比表面积可以不小于100m2/g、不小于500m2/g、不小于800m2/g、不小于1000m2/g或以上范围的组合。
39.在一些实施方案中,无机纳米颗粒直径可以为30nm-500nm。例如,无机纳米颗粒直径可以为30nm-500nm、65nm-430nm、105nm-400nm、130nm-325nm、150nm-302nm、185nm-270nm或以上范围的组合。在上述设置的无机纳米颗粒直径下,能够阻碍枝晶生长,防止隔板由于温度增加发生收缩,从而影响寿命。
40.在一些实施方案中,无机纳米颗粒还可以包括二氧化钛,二氧化钛的含量可以为150ppm-500ppm。例如,二氧化钛的含量可以为210ppm-430ppm、265ppm-410ppm、284ppm-385ppm、312ppm-352ppm或以上范围的组合。
41.在一些实施方案中,电池隔板的厚度可以为0.25mm-0.75mm。例如,电池隔板的厚度可以为0.31mm-0.72mm、0.34mm-0.69mm、0.39mm-0.64mm、0.47mm-0.60mm、0.51mm-0.59mm或以上范围的组合。优选地,电池隔板的厚度可以为0.3mm-0.5mm。
42.在一些实施方案中,支撑层可以为纤维无纺结构,其材料可以为pe、pp、pet、pbt中一种或多种纤维混合湿法抄造而成。
43.在一些实施方案中,支撑层包含双组分纤维。双组分纤维可以为心皮结构,心层聚合物熔点温度较皮层聚合物熔点温度至少高50℃,支撑层透气量不小于500l/m2.s。例如,心层聚合物熔点温度较皮层聚合物熔点温度高80℃,支撑层透气量不小于650l/m2.s。优选地,支撑层透气量为1500l/m2.s-5000l/m2.s。
44.本发明的另一方面提供了一种电池隔板的制备方法。在一些实施方案中,可以包括以下步骤:
45.步骤1,将abs聚合物、水溶性聚合物、无机纳米颗粒按比例混入丙酮溶液中,充分搅拌至充分混合,得到混合溶液;其中,按质量百分比计,混合比例5%-30%的abs聚合物、1%-25%的水溶性聚合物以及60%-85%的无机纳米颗粒。丙酮作为溶剂,可以根据原料的使用量进行添加,添加的量是本领域已知的。
46.步骤2,在混合溶液中加入质量占比1%-3%的十二烷基苯磺酸和0.4%-0.8%邻苯二甲酸二丁酯,继续搅拌混合。例如,可以加入质量占比2%的十二烷基苯磺酸和0.5%-0.7%的邻苯二甲酸二丁酯。
47.步骤3,混合后浇铸,刮涂,形成0.25-0.75mm厚的薄层。例如,混合后可以浇铸在光滑的表面上,用刮涂机刮涂以形成薄层。
48.步骤4,在室温下静置,并在薄层表面浇洗异丙醇,去离子水润湿后室温干燥,剥离后得微孔层。例如,可以每2h在膜层表面浇洗异丙醇,每次洗涤15-20min,共浇洗4-6次,用去离子水润湿,室温干燥20min用刮涂机剥离,得到微孔层。
49.步骤5,将步骤4得到的微孔层与支撑层组装得电池隔板。这里电池隔板的组装方法是本领域已知的常规方法。
50.本发明的再一方面提供了一种电池隔板的制备方法。在一些实施方案中,同样地,与以上电池隔板的制备方法相同,仅是步骤1中所使用的原料由abs聚合物改为pvdf聚合物,其各原料配比为按质量百分比计,包括20%-55%的pvdf聚合物、1%-5%的水溶性聚合物以及40%-75%的无机纳米颗粒,在此处不在赘述。
51.本发明的再一方面提供了一种电池隔板制备方法,在一些实施方案中,可以包括以下步骤:
52.步骤1,将ptfe聚合物、水溶性聚合物、无机纳米颗粒按比例混入丙酮溶液中,充分搅拌,成糊状混合物;其中,混合比例为按质量百分比计,包括15%-55%的ptfe聚合物、1%-12%的水溶性聚合物以及40%-75%的无机纳米颗粒。
53.步骤2,将糊状混合物在40℃-50℃下加热熟化,熟化结束后压延成条状坯。熟化的时间可以是8h-12h,例如,熟化时间可以为9h或10h,当然,本领域应当知晓的是,熟化时间可以根据实际情况进行调整。压延成条状坯可以在35℃-45℃加热压辊下压延成条状坯,例如,可以在40℃加热压辊下压延成条状坯。
54.步骤3,将条状坯在100℃-120℃温度下纵向拉伸,得纵向拉伸膜坯。例如,可以在110℃温度下纵向拉伸3-10倍。
55.步骤4,将纵向拉伸膜坯在190℃-210℃下进行横向、纵向双向拉伸,并在340℃-360℃下固化,得到微孔层。例如,可以将纵向拉伸膜坯在200℃下进行横向、纵向双向拉伸,并在350℃下固化。
56.步骤5,将微孔层与支撑层组装得电池隔板。这里电池隔板的组装方法是本领域已知的常规方法。
57.为了更好地理解本发明,下面结合具体示例进一步阐明本发明的内容,但本发明的内容不仅仅局限于下面的示例。
58.示例1
59.一种电池隔板制备方法,可以包括以下步骤:
60.步骤1,按表1中的质量比,将abs聚合物、水溶性聚合物、无机纳米颗粒混入丙酮溶液中,搅拌至充分混合,形成混合溶液。
61.步骤2,在混合溶液中加入质量比为2%十二烷基苯磺酸、0.6%邻苯二甲酸二丁酯,继续搅拌混合。
62.步骤3,将混合物浇铸在光滑的表面上,用刮涂机刮涂形成薄层;
63.步骤4,在室温下静置,每2h在膜层表面浇洗异丙醇,每次洗涤18min,共浇洗5次,去离子水润湿,室温干燥20min用刮涂机剥离。
64.步骤5,室温下干燥,得到微孔层。
65.步骤6,将微孔层与表1所述的支撑层进行装配,得到表1中所记载厚度电池隔板。
66.示例2~示例4
67.示例2~示例4与示例1相比,不同之处如表1所示,其他相同。
68.示例5
69.步骤1,按表1中的质量比,将pvdf聚合物、水溶性聚合物、无机纳米颗粒混入丙酮溶液中,搅拌至充分混合,形成混合溶液。
70.步骤2,在混合溶液中加入质量比为2%十二烷基苯磺酸、0.6%邻苯二甲酸二丁酯,继续搅拌混合。
71.步骤3,将混合物浇铸在光滑的表面上,用刮涂机刮涂以形成薄层;
72.步骤4,在室温下静置,每2h在膜层表面浇洗异丙醇,每次洗涤18min,共浇洗5次,去离子水润湿,室温干燥20min用刮涂机剥离。
73.步骤5,室温下干燥,得到微孔层。
74.步骤6,将微孔层与表1所述的支撑层进行装配,得到表1中所记载厚度电池隔板。
75.示例6~示例7
76.示例6~示例7与示例5相比,不同之处如表1所示,其他相同。
77.示例8
78.一种电池隔板制备方法,可以包括以下步骤:
79.步骤1,将表1中所示质量比的ptfe聚合物、水溶性聚合物、无机纳米颗粒混入丙酮溶液中,充分搅拌,成糊状。
80.步骤2,将糊状混合物45℃下加热熟化,熟化时间10h,再在40℃加热压辊下压延成条状坯。
81.步骤3,将条状坯在110℃温度下纵向拉伸4倍,得到纵向拉伸膜坯。
82.步骤4,将纵向拉伸膜坯在200℃下进行横向、纵向双向拉伸,在350℃下固化,得到微孔层。
83.步骤5,将微孔层与表1所述的支撑层进行装配,得到表1中所记载厚度电池隔板。
84.示例9~示例10
85.示例9~示例10与示例8相比,不同之处如表1所示,其他相同。
86.示例1~示例10中,所使用的无机纳米颗粒的bet比表面积为8.5g/m2,粒度为400nm。
87.表1示例1~10电池隔板组成
[0088][0089]
对比例1、对比例2和对比例3分别使用传统的聚乙烯电池隔板、聚对苯二甲酸乙二醇酯电池隔板和聚丙烯电池隔板,具体厚度如表2所示。
[0090]
表2对比例1~3的电池隔板组成
[0091]
对比例隔板类别厚度mm1聚乙烯电池隔板0.32聚对苯二甲酸乙二醇酯电池隔板0.33聚丙烯电池隔板0.3
[0092]
以上表1和表2中的厚度通过gb/t 6672-2001《塑料薄膜与薄片厚度的测定机械测量法》进行测定。
[0093]
通过以下方法对电池隔板的电阻进行测定:
[0094]
将微孔层切成2.5cm
×
2.5cm的尺寸,浸泡在1.4g/ml koh溶液中。电阻测试箱两段
放置类两个铂电极,电极之间是电解液,电阻测试使用的电解液为1.4g/ml koh溶液。测试前,对测试箱进行调试,稳定电流0.2ah。将微孔层放置在测试箱的电解液中,接入电源,30s后读取电流、电压,按下式进行计算:
[0095][0096]
其中,rs为隔板电阻,单位为欧姆
·
厘米2;vs为样品夹在支架中的电压,单位为v;vg为电压,单位为v,支架中无隔板样品;i为恒定电流(0.2ah),area为3.8cm2。
[0097]
对于电池隔板化学稳定的测试,目前化学稳定性主要是指隔膜电解液中的耐腐蚀性和尺寸稳定性。由于电解液中含有大量有机物质,因此要求隔膜在浸润时不能和电解液发生化学反应,同时要求有较好的尺寸稳定性,不发生胀缩和变形。目前尚无隔膜化学稳定性的相关测试标准,但要求用于制造隔膜的材料能够保证电池长时间正常使用。本发明化学稳定性的测试方法采用:将电池隔板置于40%koh溶液中24h,洗净干燥后观察是否有尺寸或颜色的明显变化。
[0098]
鉴于微孔层生产过程中的蜷曲缠绕和包装,电池的组装和拆卸,以及实际使用中反复充放电等因素,要求微孔层必须具备一定的物理强度以克服上述过程中的物理冲击、穿刺、磨损和压缩等作用带来的损坏,因此需要考察微孔层的穿刺强度。具体测试方法可以参照astm d3763-10《standard testm ethod for high speed puncture properties ofplastics using load and displacement sensors》。
[0099]
对示例1~10以及对比例1~3的微孔层以及电池隔板的性能进行测试,其测试结果如表3所示。
[0100]
表3示例1~10以及对比例1~3的测试结果
[0101][0102]
对比示例1~示例10与对比例1~对比例3可以发现,本发明的电池隔板化学性能更稳定,穿刺强度更高,均在320g/mil以上。
[0103]
尽管上面已经通过结合示例性实施例描述了本发明,但是本领域技术人员应该清楚,在不脱离权利要求所限定的精神和范围的情况下,可对本发明的示例性实施例进行各种修改和改变。
再多了解一些
本文用于创业者技术爱好者查询,仅供学习研究,如用于商业用途,请联系技术所有人。