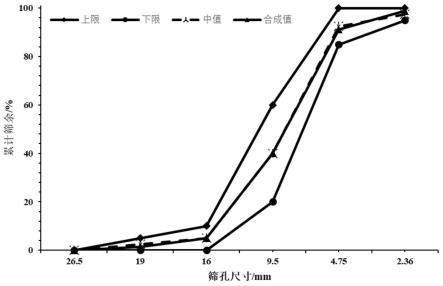
1.本发明涉及混凝土技术领域,特别地,涉及一种地聚物陶粒轻质混凝土及其制备方法。
背景技术:
2.轻质混凝土包括泡沫混凝土和轻质骨料混凝土。轻质骨料混凝土是指用胶凝材料、轻质集料和水等配制而成的表观密度不大于1950kg/m3的混凝土材料。轻质混凝土具有能够减轻制备构件的自重、保温性能好等优点,是一种具有环保特性的绿色建材。
3.在传统制备轻质混凝土过程中使用的胶凝材料为水泥,以水泥为胶凝材料制备而成轻质混凝土的抗压强度最薄弱的环节便是轻质骨料本身,低品质骨料本身又普遍存在密度低,筒压强度低等问题,当高比例使用低品质轻质骨料时,均是低品质轻质骨料被破坏导致轻质混凝土强度损失严重,以至于目前低品质轻质骨料主要用于植被种植、卫生间充填等领域。同样的,使用高品质轻质骨料(即密度低,筒压强度高的骨料)能够制备出性能好的轻质混凝土,势必造成轻质混凝土的价格过高,影响产品的推广及使用。
4.显然,目前急需一种具有抗压强度高且绿色环保的轻质骨料混凝土材料,该轻质骨料混凝土材料能提升低品质轻质骨料的利用率。
技术实现要素:
5.本发明提供了一种地聚物陶粒轻质混凝土及其制备方法,以解决现有以普通水泥为胶凝材料中高比例使用低品质轻质骨料制备的轻质混凝土强度低的技术问题。
6.根据本发明的一个方面,提供一种地聚物陶粒轻质混凝土,所述地聚物陶粒轻质混凝土包括如下质量份的原料组分:工业固废微粉280~400份、陶粒273~383份、细骨料559~933份、减水剂1.3~9.0份、缓凝剂3~10份、引气剂0.01~0.8份、激发剂78~228 份和水20~180份;
7.其中,工业固废微粉包括矿渣微粉、粉煤灰、硅灰,以及铁尾矿粉。
8.进一步地,所述地聚物陶粒轻质混凝土包括如下质量份的原料组分:工业固废微粉290~390份、陶粒300~310份、细骨料700~720份、减水剂1.5~8.0份、缓凝剂3~6 份、引气剂0.01~0.07份、激发剂100~140份和水50~150份。
9.进一步地,所述工业固废微粉中包括如下质量百分含量的原料组分:50~80%的矿渣微粉、10~50%的粉煤灰、0~15%的硅灰,以及5~20%的铁尾矿粉。
10.进一步地,所述矿渣微粉比表面不小于400m2/kg,活性等级不低于s95;和/或
11.所述粉煤灰比表面积不低于260m2/kg;和/或
12.所述铁尾矿粉比表面不小于400m2/kg;和/或
13.所述硅灰中二氧化硅含量大于92%,比表面积不低于20000m2/kg。
14.进一步地,所述陶粒的粒径分布等级为1~40,堆积密度为300~600kg/m3,筒压强度不低于0.8mpa,1小时吸水率为10~14%。
15.进一步地,所述细骨料为普通河砂或机制砂,所述细骨料的堆积密度为 1300~1600kg/m3,表观密度大于2500kg/m3,细度模数为3.0~3.4。
16.进一步地,所述减水剂为聚羧酸类减水剂、萘系减水剂和氨基磺酸盐减水剂中的一种或多种组成的混合物;和/或
17.所述缓凝剂为氯化钡和硝酸锌中的任意一种或两种组成的混合物;和/或
18.所述引气剂为十二烷基苯磺酸、十二烷基磺酸钠和松香酸钠中的一种或多种。
19.进一步地,所述激发剂为硅酸钠、硅酸钾、氢氧化钠和氢氧化钾中的一种或多种。
20.根据本发明的另一方面,还提供了一种上述地聚物陶粒轻质混凝土的制备方法,包括如下步骤:
21.步骤一、将减水剂、缓凝剂、引气剂溶解在水中,得到溶解液,向所述溶解液中引入气泡,得到混合溶液;
22.步骤二、将工业固废微粉、陶粒和细骨料搅拌混合,加入步骤一所得混合溶液,再次搅拌,至所述细骨料和工业固废微粉全部被浸湿,得到预拌合物;
23.步骤三、向所述预拌合物中加入激发剂,搅拌,制得混凝土拌合物;
24.步骤四、将所述混凝土浆料进行浇筑成型和养护,得到所述地聚物陶粒轻质混凝土。
25.进一步地,步骤二中所述搅拌混合的搅拌时间为60~90s;再次搅拌的时间为 120~180s;和/或步骤三中所述搅拌的时间为120~150s。
26.本发明具有以下有益效果:
27.本发明在工业固废微粉的原材料的配置中,选用了矿渣微粉、粉煤灰、硅灰和铁尾矿粉,工业固废微粉中的这四种原料与地聚物陶粒轻质混凝土的其他组分相互协同,能够配置出工作性能好、具有不同强度等级的地聚物陶粒轻质混凝土。其中,矿渣微粉在激发剂的作用下能加速ga
2
、alo
2-和硅酸根离子的溶解速度,并重新聚合成具有更高强度的三维网状聚硅铝酸盐凝胶及钙矾石,给地聚物轻质混凝土提供全周期强度,是地聚物陶粒轻质混凝土强度的主要来源;粉煤灰可提高地聚物陶粒轻质混凝土拌合物的和易性,并能在激发剂的作用下发生水化反应;铁尾矿微粉活性虽然低于矿渣,但依然具有一定的火山灰活性,能够参与水化反应,铁尾矿砂中铁质元素含量高,能够提升混凝土的后期强度和耐磨性,另外,铁尾矿微粉的使用相当于在胶凝材料中添加了惰性组分,能够延缓轻质混凝土的凝结时间;硅灰能够增加水化反应中的硅含量,硅灰粒径小,不仅能够均匀地填充混凝土微孔,增加轻质混凝土的早期强度和后期强度,而且硅灰粒型多数呈现球形,能够起到物理减水剂的作用,增加浆体流动性及和易性。
28.本发明所用的轻质骨料为密度低、筒压强度低的陶粒,若使用普通水泥作为胶凝材料无法达到lc20强度级别,但配合本发明中的地聚物混凝土却能制备出密度低于 1500kg/m3,抗压强度大于20mpa的轻质混凝土。
29.使用本发明的方法制备轻质混凝土材料存在凝结时间快、强度提升快的优点,不仅能过够缩短模具运转周期及养护时间,而且能够降低产品模具及养护成本的投入。
30.本发明制备地聚物陶粒轻质混凝土具有良好的耐海水腐蚀性,在沿海轻量化建筑领域,具有大的应用市场。
31.本发明制备的地聚物陶粒轻质混凝土可以用于结构件中,能够降低建筑物的自
重,产品具广泛的应用前景。
32.除了上面所描述的目的、特征和优点之外,本发明还有其它的目的、特征和优点。下面将参照图及实施例,对本发明作进一步详细的说明。
附图说明
33.构成本发明的一部分的附图用来提供对本发明的进一步理解,本发明的示意性实施例及其说明用于解释本发明,并不构成对本发明的不当限定。在附图中:
34.图1是本发明实施例中陶粒拟合曲线图。
具体实施方式
35.为了使本发明的发明目的、技术方案和有益技术效果更加清晰,以下结合实施例对本发明进行进一步详细说明。应当理解的是,本说明书中描述的实施例仅仅是为了解释本发明,并非为了限定本发明。
36.为了简便,本文仅明确地公开了一些数值范围。然而,任意下限可以与任何上限组合形成未明确记载的范围;以及任意下限可以与其它下限组合形成未明确记载的范围,同样任意上限可以与任意其它上限组合形成未明确记载的范围。此外,尽管未明确记载,但是范围端点间的每个点或单个数值都包含在该范围内。因而,每个点或单个数值可以作为自身的下限或上限与任意其它点或单个数值组合或与其它下限或上限组合形成未明确记载的范围。
37.在本文的描述中,需要说明的是,除非另有说明,“以上”、“以下”为包含本数,“一种或多种”中的“多种”的含义是两种及以上,“一个或多个”中的“多个”的含义是两个及以上。
38.本发明的第一方面提供一种地聚物陶粒轻质混凝土,所述地聚物陶粒轻质混凝土包括如下质量份的原料组分:工业固废微粉280~400份、陶粒273~383份、细骨料 559~933份、减水剂1.3~9.0份、缓凝剂3~10份、引气剂0.01~0.8份、激发剂78~228 份和水20~180份。
39.工业固废微粉中包括矿渣微粉、粉煤灰、硅灰,以及铁尾矿粉。
40.混凝土强度主要来源于胶凝材料浆体强度、骨料强度、以及骨料与浆体界面过渡区域强度。在轻质混凝土中,强度主要来源于胶凝材料浆体强度,骨料与浆体界面过渡区域强度和骨料仅提供次要的强度。地聚物陶粒轻质混凝土的制备中,单位体积内各组分材料的用量决定轻质陶粒混凝土的密度和强度。工业固废微粉、激发剂和水的用量决定了配置轻质混凝土的强度及密度,工业固废微粉用量在上述范围内能够有效的控制所制备的陶粒轻质混凝土密度低于1500kg/m3,抗压强度大于20mpa;陶粒用于调节陶粒轻质混凝土的密度,在单位体积内用量大,胶凝材料用量则低,所配置的轻质混凝土的密度低、强度也低,反之则密度高,强度也高;细骨料能够填充轻质粗骨料所产生的空隙,使得制备的轻质混凝土更加的密实,另外和胶凝材料组成砂浆,能够提升轻质混凝土的和易性和流动性,细骨料在上述范围内所制备的陶粒轻质混凝土具有良好的和易性和流动性;地聚物具有凝结时间快的特性,无法保证陶粒轻质混凝土混合料的可操作时间,在本发明中虽然能够通过工业固废微粉组成控制其凝结时间在60min以上,但在低水胶比条件下,凝结时间会进一步的缩
短,而过量的使用低活性组分虽然能够进一步延长凝结时间,同时也会造成强度损失严重。然而,本发明使用上述份数的缓凝剂可保证混凝土的可操作时间在60min以上,且对强度影响较小。使用上述份数的引气剂能够在砂浆中引入微孔径气孔,而微孔径气孔的引入能够提升陶粒轻质混凝土混合料的和易性、降低密度、改善内部养护条件,但过量使用引气剂将导致胶砂组分中含气量过高,强度损失大,而使用量过少则会导致胶砂组分中含气量低,密度大、和易性差。减水剂主要是用于调节陶粒轻质混凝土的水胶比,确保所配置的混凝土在低水胶比的条件下,依然具有良好的流动性,同时低的水胶比能够保证混凝土具有较高强度。
41.本发明提供的胶凝材料选用工业固废微粉,工业固废微粉通过激发剂水化形成强度,具有凝结时间快、强度提升快、强度高、养护周期短、耐侵蚀等优点。使用280~400 份胶凝材料制备的混凝土强度在20mpa以上、密度低于1500kg/m3,如果用量低于280 份,会导致强度无法达到20mpa;如果用量超过400份,会导致密度超过1500kg/m3。
42.本发明的地聚物陶粒轻质混凝土所用主要原材料均为工业固废,具有碳排放量低,是一种绿色环保型材料。
43.在本发明的实施例中,所述地聚物陶粒轻质混凝土包括如下质量份的原料组分:工业固废微粉290~390份、陶粒300~310份、细骨料700~720份、减水剂1.5~8.0份、缓凝剂3~6份、引气剂0.01~0.07份、激发剂100~140份和水50~150份。
44.上述水中,已添加陶粒1h的吸水量和去除激发剂包含的水量。
45.本发明中所使用的轻质骨料均为堆积密度在300~600kg/m3,筒压强度不低于 0.8mpa,而所得到的最终产品的表干密度却能维持在1500kg/m3以下,同时抗压强度在20mpa以上。混凝土抗压强度主要来源于胶凝材料浆体强度、骨料强度,并且还与骨料与浆体界面过渡区域强度有关。轻质骨料在轻质混凝土中起到填充和提供部分抗压强度的作用,轻质骨料混凝土抗压强度测试中轻质骨料是最为薄弱的部分,最先被破坏,也是导致轻质混凝土强度不高的主要原因。使用筒压强度低轻质骨料,将进一步加剧该类问题的发生,因此在相关的轻质骨料混凝土的制备中,对配置不同强度等级的轻质混凝土,对轻质骨料提出明确的密度等级及筒压强度的要求。本发明中使用市场上较为常见的低品质轻质陶粒,即密度等级低,筒压强度低的产品,旨在推动低品质轻质陶粒在高强度轻质混凝土中的应用、推进轻质混凝土的市场化和绿色化。这就需要配置具有更高强度的胶凝材料,该胶凝材料在轻质混凝土抗压强度测试中对轻质骨料能起到支撑和保护作用,能避免混凝土整体的损坏,以此提升轻质混凝土的抗压强度。
46.在本发明的实施例中,所述工业固废微粉中包括如下质量百分含量的原料组分: 50~80%的矿渣微粉、10~50%的粉煤灰、0~15%的硅灰,以及5~20%的铁尾矿粉。
47.本发明在工业固废微粉的原材料的配置中,选用了矿渣微粉、粉煤灰、硅灰和铁尾矿粉,工业固废微粉中的这四种原料与其他组分相互协同,能够配置出工作性能好、不同强度等级的地聚物陶粒轻质混凝土。其中,矿渣微粉在激发剂的作用下能加速钙、铝、硅质低聚体的生成,并重新聚合成具有更高强度的三维网状聚硅铝酸盐凝胶及钙矾石,提供地聚物轻质混凝土全周期强度,是地聚轻质混凝土强度的主要来源。粉煤灰可提高轻质混凝土拌合物的和易性,并能在激发剂的作用下发生水化反应;铁尾矿微粉具有一定的火山灰活性,虽然活性较矿渣低,但仍然能够参与水化反应,并且铁尾矿微粉中铁质元素含量高,能
过提升混凝土后期的耐磨性,另一方面,铁尾矿微粉在胶凝材料中作为惰性组分能够延缓轻质混凝土的凝结时间。硅灰能够增加水化反应中硅的含量,硅灰粒径小,能够均匀地填充混凝土微孔,增加轻质混凝土的早期强度和后期强,并且硅灰粒型多数呈现球形,能够起到物理减水剂的作用,增加浆体流动性和和易性。
48.在一些实施例中,所述矿渣微粉比表面不小于400m2/kg,活性等级不低于s95。矿渣微粉是提供强度的主要贡献组分,相同活性组分条件下,矿渣微粉的比表面越大,在激发剂作用下越有利于钙、铝、硅质低聚体的生成,促进低聚体聚合反应形成具有强度的三维网状聚硅铝酸盐凝胶及钙矾石,最终获得具有较高强度地聚物。
49.在一些实施例中,所述粉煤灰比表面积不低于260m2/kg;为二级以上粉煤灰。粉煤灰主要产于火力发电厂,一般在火力发电站直接取出的粉煤灰比表面积在260 m2/kg~400m2/kg之间,一方面,本发明中对粉煤灰的比表面及要求为粉煤灰的最低要求,确保市面上常规粉煤灰均可以使用,另一方面,之所以要求为二级粉煤灰是因为粉煤灰在激发剂的作用下发生水化反应为地聚物胶凝材料提供强度,而等级过低的粉煤灰无法保证胶凝材料的水化强度。
50.在一些实施例中,所述铁尾矿粉比表面不小于400m2/kg,所述铁矿尾砂微粉为铁矿尾砂烘干后经机械研磨至不小于400m2/kg。铁尾矿大多作为惰性组分,自身活性低,若不对铁尾矿的活性进行激发,其潜在胶凝活性无法体现,铁尾矿的颗粒细化,结晶程度降低,晶格缺陷变大,为了使其具有一定的火山灰胶凝活性,该部分使用铁尾矿粉的比表面积应不小于400m2/kg,配合本发明中使用的激发剂,应用化学激发的方式能够使其中的活性组分快速的溶解,并聚合形成具有强度的水化产物。
51.在一些实施例中,所述硅灰中二氧化硅含量大于92%,比表面积不小于20000 m2/kg。硅灰能够改变地聚物浆体的触变性,塑性黏度和屈服应力随硅灰含量的增加而减少,但当硅灰的用量超过30%时,浆体的屈服力急剧增大,在合适的激发条件下,少量的硅灰可以发挥充填作用并促进凝胶材料形成,但掺量过大反而导致负面作用,主要原因在于硅灰溶解出硅质组分能够改变激发剂的实际模数以及碱度。因此,需要对硅灰中硅质组分主要载体二氧化硅含量控制在92%以上,以及比表面积控制在大于 20000m2/kg。
52.在本发明的实施例中,所述陶粒的粒径分布等级为1~40,堆积密度为 300~600kg/m3,筒压强度不低于0.8mpa,1小时吸水率为10~14%。在现有技术中,该类陶粒主要应用于对筒压强度较低的厨卫回填、绿化、废水过滤处理和制备强度在 10mpa以下的轻质混凝土中。
53.本发明提供轻质陶粒堆积密度在300~600kg/m3,筒压强度不低于0.8mpa,1小时吸水率10~14%之间,陶粒种类可以为市面上较为常见页岩陶粒、粉煤灰陶粒、黏土陶粒、垃圾陶粒、煤矸石陶粒、生物污泥陶粒、河底泥陶粒中一种或多种,其粒径分布等级在1~40,也可由多种不同粒径等级的陶粒复配组成该级配等级的陶粒轻质骨料,常见级配类别为连续级配5~40mm、5~31.5mm、5~20mm、5~18mm、5~10mm,以及单级配10~16mm,也可以由上述级配组成而成的任意级配。
54.在本发明的实施例中,所述细骨料为普通河砂或机制砂,所述细骨料的堆积密度为1300~1600kg/m3,表观密度大于2500kg/m3,细度模数为3.0~3.4。
55.在本发明的实施例中,所述减水剂为聚羧酸类减水剂、萘系减水剂和氨基磺酸盐
减水剂中的一种或多种组成的混合物;和/或所述缓凝剂为氯化钡和硝酸锌中的任意一种或两种组成的混合物;和/或所述引气剂为十二烷基苯磺酸(sdbs)、十二烷基磺酸钠(k12)和松香酸钠(ks)中的一种或多种。
56.在本发明的实施例中,所述激发剂为硅酸钠、硅酸钾、氢氧化钠和氢氧化钾中的一种或多种。
57.所述激发剂主要用于激发工业固废微粉活性,在一些实施例中,应用的激发剂其 sio2/na2o(或k2o)摩尔比在1.0~2.1之间,固含量在30~45%之间。
58.工业固废微粉地聚物的水化反应为固液反应体系,在激发剂作用下,其中的铝硅钙类材质发生溶解形成钙、铝、硅质低聚体,低聚体则会进一步的发生聚合反应生成 [m
x
(alo2)y(sio2)z·nmoh
·mh2o]胶体,胶体很快在工业矿渣微粉颗粒表面沉淀。并将没有反应的工业矿渣微粉颗粒粘结起来,最终形成地聚物。激发剂中,存在着多种聚合度的硅氧四面体基团,并随着激发剂中sio2浓度的降低,溶液中低聚态硅氧四面体含量增加,高聚态硅氧四面体的含量减少。显然,激发剂模数的降低,其中低聚合度的硅氧四面体的含量增加,促进工业固废微粉中铝硅钙类材质的溶解,促进胶体沉淀相的形成,提高地聚物的强度,但激发剂模数进一步的降低,又会导致其中硅质低聚体的总含量的减少,而不利于胶体沉淀相的形成,对地聚物强度起到不利影响。另一方面,工业固废微粉聚合反应需要在一定固含量的激发剂溶液激发下进行,当激发剂含量较低,解聚反应较差,不利于地聚物强度的形成;增大激发剂固含量,促进聚合反应的进行从而提升地聚物强度,但当激发剂固含量过大时,在聚合反应结束后会导致过多的反应物残留,使低聚物强度降低。因此。本发明所选用激发剂模数控制在 1.0~2.1之间,固含量在30~45%之间。
[0059]
本发明的另一方面提供一种上述地聚物陶粒轻质混凝土的制备方法,包括如下步骤:
[0060]
步骤一、将减水剂、缓凝剂、引气剂溶解在水中,得到溶解液,向所述溶解液中引入气泡,得到混合溶液;
[0061]
步骤二、将工业固废微粉、陶粒和细骨料搅拌混合,加入步骤一所得混合溶液,再次搅拌,至所述细骨料和工业固废微粉全部被浸湿,得到预拌合物;
[0062]
步骤三、向所述预拌合物中加入激发剂,搅拌,制得混凝土拌合物;
[0063]
步骤四、将所述混凝土浆料进行浇筑成型和养护,得到所述地聚物陶粒轻质混凝土。
[0064]
其中减水剂、缓凝剂需在激发剂加入之前加入,否则减水剂和缓凝剂效率将降低。
[0065]
本发明中所使用的陶粒为筒压强度低的低品质轻质陶粒,制备工艺简单,轻质集料不需要进行预湿,制备的轻质混凝土干表观密度小于1500kg/m3、轴心抗压强度大于20mpa的轻质混凝土。
[0066]
在本发明的实施例中,步骤二中所述搅拌混合的搅拌时间为60~90s;再次搅拌的时间为120~180s;和/或步骤三中所述搅拌的时间为120~150s。
[0067]
在本发明的实施例中,步骤一~步骤三拌合方式为分步拌合,步骤一优先将外加剂与水进行充分的拌合和稀释,其中减水剂、缓凝剂和引气剂在稀释后分别有利于提升其减水效率、缓凝效率和引气效率,一方面能够提升外加剂作用效率,降低外加剂用量、减少外加剂的使用成本,另一方面能够避免外加剂掺量过多时对产品性能产生不利的影响;步
骤二中优先进行干料的搅拌在此过程中有利于粉料及骨料的充分混合,防止在干料制备成预拌合物时,细骨料和粉料之间的聚集成团,通过本步骤制备的预拌合物质地均匀;另外在预拌合料中未使用激发剂,使得减水剂、缓凝剂和引气剂效果能优先作用于工业固废微粉表面,能够提升三种外加剂的效果,再通过步骤三中的激发剂在确保减水剂、缓凝剂和引气剂均发生作用的前提下与工业固废微粉发生水化反应。
[0068]
在本发明的实施例中,所述工业固废微粉的制备方法为矿渣微粉、粉煤灰、硅灰,以及铁尾矿粉混合搅拌5~10min制得。
[0069]
在一些实施例中,上述地聚物陶粒轻质混凝土的制备方法包含如下步骤:
[0070]
步骤一:工业固废胶结料的制备,按照设计配合比称取矿渣微粉、粉煤灰、铁矿尾矿微粉和硅灰,将上述原料通过机械搅拌5~10min使其混合均匀,制备成工业固废微粉胶结料备用。
[0071]
步骤二:按设计配合比称取工业固废微粉胶结料、陶粒、细骨料、减水剂、缓凝剂、引气剂、激发剂和水备用;
[0072]
步骤三:将步骤二中的减水剂、缓凝剂、引气剂溶解在水中,待其添加的全部组分全部溶解后,再快速搅拌,使溶液中能够引入更多的气泡,最后静置备用。
[0073]
步骤四:将步骤二中的工业固废微粉胶结料、陶粒、细骨料置于混凝土强制搅拌器中搅拌60~90s,然后加入步骤三中配置的溶液,搅拌120~180s使骨料及胶凝材料表面全部被润湿后,倒入激发剂,再搅拌120~150s便制备成地聚物陶粒轻质混凝土拌合物;
[0074]
步骤五:将地聚物陶粒轻质混凝土拌合物浇筑模具,3~4h后拆除模具,室温覆膜养护14~28d,即完成地聚物陶粒轻质混凝土的制备。
[0075]
实施例
[0076]
下述实施例更具体地描述了本发明公开的内容,这些实施例仅仅用于阐述性说明,因为在本发明公开内容的范围内进行各种修改和变化对本领域技术人员来说是明显的。除非另有声明,以下实施例中所报道的所有份、百分比、和比值都是基于重量计,而且实施例中使用的所有试剂都可商购获得或是按照常规方法进行合成获得,并且可直接使用而无需进一步处理,以及实施例中使用的仪器均可商购获得。
[0077]
为体现本发明中胶凝材料特性,本发明设置胶砂强度试验,主要为体现本发明中各组分材料之间的相互配合,及对混合料流动性、凝结时间、抗压抗折强度参数的影响。在实施例中水胶比固定为0.5,工业固废微粉用量为450份,砂均为标准砂1350 份;激发剂模数为1.2,用量为132份。实施例1~6和对比例1~4的详细配比如表1 所示。
[0078]
表1实施例1~6及对比例1~4中工业固废微粉各组分所占质量百分比
[0079]
项目矿渣微粉粉煤灰硅灰铁尾矿粉实施例180.00%10.00%010.00%实施例260.00%30.00%010.00%实施例355.00%30.00%015.00%实施例455.00%30.00%5.00%10.00%实施例550.00%30.00%10.00%10.00%实施例670.00%10.00%10.00%10.00%对比例1100.00%000
对比例220.00%80%00对比例340.00%0060%对比例420%020%60%
[0080]
实施例1~6和对比例1~4地聚物胶砂试验方法如下:将工业固废微粉混合后通过机械搅拌7.5min,使其混合给均匀,再将激发剂与水混合并充分搅拌均匀后倒入胶砂搅拌锅中,再倒入工业固废微粉,后续试验步骤根据胶砂强度试验方法步骤参照gb/t17671-1999《水泥胶砂强度检验方法(iso法)》和gb/t2419-2005《泥胶砂流动度测定方法》执行。
[0081]
对比例5
[0082]
胶凝材料选用p.o 42.5水泥450份,水胶比为0.5,砂选用标准砂1350份。
[0083]
胶砂试验方法参照gb/t17671-1999《水泥胶砂强度检验方法(iso法)》和 gb/t2419-2005《泥胶砂流动度测定方法》执行。
[0084]
实施例1~6和对比例1~5分别测试胶砂流动度、凝结时间、抗压强度,试验结果如表2所示。
[0085]
表2实施例1~6及对比例1~5各项性能检测结果
[0086][0087]
根据表2所示,在实施例1~6中,通过调整粉煤灰、硅灰、矿渣微粉在工业固废微粉中的质量占比时,随着粉煤灰和硅灰的用量的增加、胶砂流动度增大,同时凝结时间也会相应的延长,而硅灰用量在本发明范围内的提升,对后期强度有提升作用,由于硅灰的市场价格远高于粉煤灰价格,因此,仅在配置高强度产品时才适当使用硅灰用于提升工作性能及后期强度。铁尾矿粉用量由于本身活性低于粉煤灰,在工业固废矿渣微粉溶解-聚合反过程中提供了惰性组分,缓凝效果优于粉煤灰和硅灰。激发剂在地聚物的整个反应周期内不仅提供了工业固废微粉活性组分的溶解环境,还参与地聚物空间骨架的构造。
[0088]
实施例7~13提供的是一种地聚物陶粒轻质混凝土的制备方法,实施例7~13详细配比如表4所示。
[0089]
表3实施例7~13中地聚物轻质陶粒混凝土各组分份数单位:质量份
[0090]
[0091][0092]
如表3所示,其中工业固废微粉选用的为实施例6中的配比;实施例7~13中的陶粒选用三档不同规格轻质条例具体参数如表4所示,通过对三档陶粒进行拟合获得 5-16的连续级配轻质骨料,其级配拟合曲线如图1所示,其拟合曲线基本与5-16的连续级配中值曲线相吻合,测得堆积密度为436kg/m3,筒压强度为1.2mpa,1小时吸水率为10.90%;细骨料为干河砂,堆积密度为1510kg/m3,细度模数为3.2。引气剂为 sdbs-k12-ks三者的组合、减水剂为聚羧酸减水剂-萘系减水剂-氨基磺酸盐减水剂三者的组合、缓凝剂为氯化钡-硝酸锌两者组合、激发剂模数1.5,固含量为41.79%。
[0093]
表4陶粒基本参数
[0094]
规格123堆积密度/(kg/m3)555.05462.46373.46拟合配比/%20755
[0095]
实施例7的地聚物陶粒轻质混凝土的制备方法包含如下步骤;
[0096]
步骤一:称取207.9份的矿渣微粉、29.7份的粉煤灰、29.7份的铁矿尾矿微粉和 29.7份的硅灰,将四种原料通过机械搅拌7.5min使其混合均匀,制备成工业固废微粉胶结料备用。
[0097]
步骤二:称陶粒310份、取细骨料715份、减水剂1.49份、缓凝剂2.97份、引气剂0.015份、激发剂78份和水124份备用;
[0098]
步骤三:将步骤二中的减水剂、缓凝剂、引气剂溶解在水中,慢速搅拌至全部组分全部溶解后,再快速搅拌,使溶液中能够引入更多的气泡,最后静置备用。
[0099]
步骤四:将步骤一和步骤二中的工业固废微粉胶结料、粉煤灰陶粒、细骨料置于混凝土强制搅拌器中搅拌75s,然后加入步骤三中配置的溶液,搅拌150s使骨料及胶凝材料表面全部被润湿后,加入激发剂,再搅拌135s便制备成地聚物陶粒轻质混凝土拌合物;
[0100]
步骤五:将地聚物陶粒轻质混凝土拌合物浇筑模具,5h后拆除模具,室温覆膜养护28d,即完成地聚物陶粒轻质混凝土的制备。
[0101]
实施例8~13的地聚物陶粒轻质混凝土的制备方法同实施例7,仅需将其中的组分进行更换即可。
[0102]
对比例6:
[0103]
普通硅酸盐水泥420份、减水剂4.2份、轻骨料301份、细骨料676份、水161 份。
[0104]
其中粗轻骨料和细骨料与实施例7~13相同。
[0105]
本对比例的陶粒轻质混凝土的制备方法包含如下步骤;
[0106]
步骤一:称取301份轻骨料、细骨料676份、水80.5份,将三种原料通过机械搅拌60s使其混合均匀,得到预拌合料;
[0107]
步骤二:称取420份的普通硅酸盐水泥、减水剂4.2份、水80.5份加入到步骤一种的预拌合料中,搅拌120s,得到陶粒轻质混凝土拌合物;
[0108]
步骤三:将轻质混凝土拌合物浇筑模具,养护1d后拆除模具,室温覆膜养护28d,即完成地聚物陶粒轻质混凝土的制备。
[0109]
对比例7:
[0110]
普通硅酸盐水泥354.2份、粉煤灰69份、硅灰36.8份,减水剂8.82份、轻骨料 342份、细骨料628.7份、水139份。
[0111]
粗轻质骨料和细骨料同实施例7~13。
[0112]
本对比例的陶粒轻质混凝土的制备方法同对比例6,仅需将其中的组分进行更换即可。
[0113]
对比例8~12为一种地聚物陶粒混凝土的制备方法,具体配比如表5所示。
[0114]
表5对比例8~12中地聚物轻质陶粒混凝土各组分份数
[0115][0116]
对比例8~12中使用的工业固废微粉配比与实施例6中相同,粗轻质骨料、细骨料、引气剂、减水剂、缓凝剂、激发剂与实施例7~13选择相同,仅添加份数不同。
[0117]
为进一步凸显本发明的显著性,对上述实施例和对比例进行抗压强度检测、干表观密度和耐侵蚀性测试。抗压强度检测方法参考gbt 50081-2019《混凝土物理力学性能试验方法标准》执行,干表观密度测试方法参考jgj51-2002《轻骨料混凝土技术规程》执行。耐侵蚀试验选用海水为养护液,对养护周期达到3d的试件全部浸没于海水中,与对比试件置于相同温度下养护至28天测其抗压强度,抗压强度占对比试件强度的百分比即为耐侵蚀值,测量得到的数值越大,表明材料的海水耐腐蚀性越强。
[0118]
表6实施例和对比例测试结果
[0119]
项目坍落度/mm1d抗压/mpa28d抗压/mpa耐侵蚀/%密度/(kg/m3)实施例71833.723.61021399实施例81923.925.81031410实施例91863.927.31061438实施例101964.130.11041453实施例111934.433.41081462实施例121884.834.31121484实施例131855.636.91101498对比例61620.813.6861447对比例71981.215.4851481对比例81662.321.31031450对比例91422.514.81021484
对比例101262.915.11051555对比例111480.69.81051473对比例12132-10.6961541
[0120]
由表6所示,在实施例7~13中随着工业固废微粉用量的增加其中抗压强度也随之增加,表干密度在1500kg/m3以内,其28天抗压强强度测试中的最大值可达到 36.9mpa。对比例6~7为使用普通硅酸盐水泥以及普通硅酸盐水泥配合粉煤灰和硅灰所制备的轻质混凝土其抗压强度最大可达15.4mpa,同时根据jgj51-2002《轻骨料混凝土技术规程》表5.2.1所示,轻质骨料密度等级为500可配置轻质混凝土的强度在 10mpa左右。
[0121]
虽然已经参考优选实施例对本发明进行了描述,但在不脱离本发明的范围的情况下,可以对其进行各种改进并且可以用等效物替换其中的部件,尤其是,只要不存在结构冲突,各个实施例中所提到的各项技术特征均可以任意方式组合起来。本发明并不局限于文中公开的特定实施例,而是包括落入权利要求的范围内的所有技术方案。
再多了解一些
本文用于创业者技术爱好者查询,仅供学习研究,如用于商业用途,请联系技术所有人。