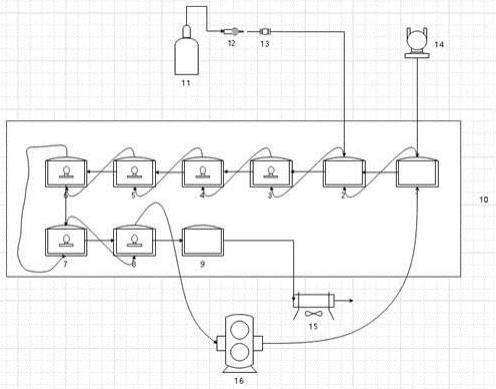
1.本发明属于化工技术领域,具体涉及一种微反应连续光催化邻氯甲苯制备邻氯三氯甲苯的方法。
背景技术:
2.邻氯三氯甲苯在工业上主要用于有机合成,是克霉唑和邻氯苯甲酸的中间体,工业上制备邻氯三氯甲苯多采用间歇釜生产工艺。间歇釜生产工艺,将反应原料添加入反应釜后在适宜条件下发生反应,一方面间歇釜设备并不封闭因此存在污染严重、危险系数高的缺陷,另一方面采用间歇釜生产工艺,所有反应物一次性添加到反应釜中进行反应,催化制备反应的效率低,而且光催化反应过程中剧烈放热,并且反应物与产物都集中于反应釜内,所以温度也不易控制,导致最终产物的纯度和收率都较低。
技术实现要素:
3.为了解决上述问题,本技术的目的在于提供一种微反应连续光催化邻氯甲苯制备邻氯三氯甲苯的方法,可以提高光催化反应的转化率和产物纯度。
4.为了实现上述目的,特提出以下技术方案,一种微反应连续光催化邻氯甲苯制备邻氯三氯甲苯的方法,包括以下步骤:提供微反应器,所述微反应器包括混合腔和反应腔,所述反应腔至少为3个,所述反应腔外均设置有紫外灯;(1)将预热后的邻氯甲苯输送至所述混合腔,并将氯气通入所述混合腔得到反应液;(2)所述反应液依次流过所述反应腔,并在所述紫外灯下进行连续光催化反应,后处理之后得到所述邻氯三氯甲苯。
5.本技术提供的连续光催化邻氯甲苯制备邻氯三氯甲苯的方法,反应阶段处于完全密闭状态,邻氯甲苯与氯气在微反应器内实现高效混合,并且反应量少,反应物停留时间短,反应物和产物不会过久堆积在微反应器中,可以避免在反应后期发生反应速率下降的问题,有效提高反应转化率,并且生产过程安全无污染、操作自动化、反应速度快、产品含量高。
6.可选地,所述反应腔的温度为90~140℃,且所述反应腔之间的温度差不大于3℃,通过精准控温,可以有效避免副反应的发生,减少反应产生的杂质,提高产品的纯度。
7.可选地,所述反应腔外侧设置热交换层,所述热交换层中的热交换介质为油,采用油作为热交换介质,并将其设置在反应腔外侧作为热交换层,可以导热效率高,并且控温精准,可以有效保证微反应中反应腔之间的温度差不会过大,稳定连续的反应温度更加有利于微反应的进行,提高反应的转化率和产品的纯度,避免因温差过大而导致副反应的发生。
8.可选地,所述氯气与邻氯甲苯的摩尔比为3.1~4.2:1。通过控制上述氯气与邻氯甲苯的摩尔比,氯气用量稍过量,可以有效促进反应的正向进行,又可以避免因过量通入氯气导致成本的提高,而且如果氯气含量过高,还会促进邻氯三氯甲苯向邻氯苯甲酰率转化,导致酰氯杂质含量升高。
9.可选地,所述紫外灯波长为360~370nm,功率为15~80w,本技术提供的方法中,采用低功率的紫外灯起到催化作用,若功率过低,则催化的效果不佳,若功率过高,又会因紫外灯能量过高导致反应过程中发生碳化,既影响产物的转化率,又会提高杂质的含量。
10.可选地,所述反应腔外的紫外灯的功率随反应液流动方向呈增大趋势,由于反应混合液在微反应器中随着流动方向反应,沿流动方向,反应物占比越来越小,而产物越来越高,通过将反应腔外的紫外灯的功率设置为随反应液流动方向呈增大趋势,可以进一步促进反应向生成产品的方向进行,提高反应的转化率。
11.可选地,所述反应腔为6个,分别为第一反应腔、第二反应腔、第三反应腔、第四反应腔、第五反应腔、第六反应腔,所述反应液依次流过第一反应腔、第二反应腔、第三反应腔、第四反应腔、第五反应腔、第六反应腔进行连续光催化反应;所述第一反应腔、第二反应腔、第三反应腔紫外灯功率为15~50w,第四反应腔紫外灯功率为55~60w,第五反应腔紫外灯功率为65~70w,第六反应腔紫外灯功率为75~80w。
12.可选地,所述反应液在反应腔中的总停留时间为80~150s,反应液在反应腔中的总停留时间相较于传统反应方式非常短,微量的反应物在较短的反应停留时间内,可以高效地向生成反应产物的方向进行,同时反应液以流动的方式经过微反应器,虽然微量但是可以实现高通量地进行反应。反应停留时间过短则反应不充分,催化反应的产品产率低,若反应停留时间过长,则会对反应的效率产生较大的影响,选择上述的反应液在反应腔中的总停留时间,既能保证反应充分进行,又能保证较高的生产效率。
13.可选地,所述混合腔和反应腔内设置有心形微反应通道,所述邻氯甲苯与氯气在心形微反应通道中混合后得到所述反应液,所述反应液在所述反应腔内的心形微反应通道流动并进行光催化反应,将反应通道设置为串联的心形反应通道,可以有效增加反应液与反应通道的接触面积,并且心形反应通道中宽、窄交错的形状可以促进反应液在流动过程中发生碰撞,流动性更高,从而促进反应的高效进行。
14.可选地,每个反应腔中的所述心形微反应通道内包括至少40个心形微腔,所述心形微腔内设置有反应液挡板,所述反应液挡板位于心形微腔宽侧,反应液的流动方向为由心形微腔宽侧流入,经反应液挡板均匀混合后,至心形微腔窄侧流出,并流入下一个心形微腔宽侧,通过设置反应液挡板,可以进一步地提高反应液在反应通道内的碰撞混合效果,反应液在碰撞后与反应腔壁接触,再流向心形微腔宽侧,最后流出此心形微腔并进入下一个心形微腔内,这可以延长反应液在反应腔内的停留时间,既能提高反应的效率,又能使反应液充分附着在反应腔壁上,提高紫外灯光催化效果,提高反应转化率。
15.可选地,所述微反应器还包括预热腔,步骤(1)中邻氯甲苯经过所述预热腔进行预热后,在所述混合腔与氯气混合,所述预热腔的温度为90~140℃,通过添加预热步骤,对邻氯甲苯进行预热,预热之后的邻氯甲苯流动性更高,能量更高因此热运动更加活跃,不仅可以促进与氯气的充分混合,也能提高反应液在预热后进入反应腔内的反应效率,避免反应早期邻氯甲苯温度上升缓慢而导致反应初期的反应速率过慢影响反应转化率,由于本技术中反应液在反应腔内的停留时间很短,让刚进入反应腔内的反应液就处于催化反应的最佳条件,也能进一步提高生产的效率。
16.可选地,步骤(1)中所述氯气经氯化钙干燥进入混合腔,所述干燥剂为无水氯化钙干燥剂。
17.可选地,所述微反应器还包括冷却腔,步骤(2)中经光催化反应后的反应液由反应腔进入冷却腔,反应液可以在冷却腔内继续进行反应,生成少量的反应物,在冷却后再进行后处理操作。
18.可选地,步骤(2)中所述后处理操作包括对反应液进行氮气吹扫、碱液吸收和精馏。
19.可选地,所述碱液的质量浓度为10%~30%,所述碱液为氢氧化钠溶液。
20.可选地,制备的邻氯三氯甲苯的纯度为97.5~99.5%,转化率不低于98%。
21.本技术的有益效果至少包括以下几方面:1. 使用微反应装置的连续光催化邻氯甲苯制备邻氯三氯甲苯,代替使用传统间歇釜反应的方法,一方面,由于光氯化反应过程中的反应中间体和最终产品易和水反应生成杂质,本技术方案的反应阶段处于完全密闭状态,隔绝空气,从而减少与空气中水分的接触,降低了杂质的生成,另一方面,反应物在紫外光的催化下高效微量地进行氯化反应,可以降低苯环氯代副产物生成,提高侧链二氯代物的利用效率,从而减少二氯代物的剩余量,提高反应的转化率,另外采用安全环保无污染的低功率紫外光为催化剂,在生产过程更加安全且无污染。
22.2. 由于光催化反应的后期存在反应速率下降的问题,本技术方案通过设置微反应通道,使得反应物微量且高效的在微反应器中进行光催化反应,可以提高光催化反应在后期的反应速率,从而可以有效提高反应的转化率。
23.3.常规釜式反应中氯原子的利用率不高,导致需要消耗大量的氯气,造成生产成本的提升,本技术方案通过使用微反应装置,并进一步优化邻氯甲苯与氯气的比例,从而有效减少氯气的浪费,提高氯气原子的利用率。
24.4. 通过控制反应腔外紫外灯的功率,具体的设置反应腔外的紫外灯的功率随反应液流动方向呈增大趋势,尤其是针对性地提高微反应器中反应液流出前的几个反应腔外的紫外灯功率,可以进一步提高反应后期的反应速率,从而提高产物的转化率。
附图说明
25.图1为本技术实施例使用的反应装置的结构示意图;图2为本技术实施例使用的微反应装置心形微反应通道的结构示意图。
26.图中标注与名称对应如下:1-预热腔,2-混合腔,3-第一反应腔,4-第二反应腔,5-第三反应腔,6-第四反应腔,7-第五反应腔,8-第六反应腔,9
–
冷却腔,10-微反应器,11-氯气储存罐,12-氯化钙干燥剂,13-流量计,14-平流泵,15-后处理装置,16-控温系统,17-心形微反应通道,18-反应液挡板,19-心形微腔宽侧,20-心形微腔窄侧。
具体实施方式
27.为进一步阐述本发明所采取的技术手段及其效果,以下结合实施例对本发明作进一步地说明。可以理解的是,此处所描述的具体实施方式仅仅用于解释本发明,而非对本发明的限定。
28.实施例中未注明具体技术或条件者,按照本领域内的文献所描述的技术或条件,或者按照产品说明书进行。所用试剂或仪器未注明生产厂商者,均为可通过正规渠道商购
获得的常规产品。
29.实施例1如图1所示,本技术中连续光催化制备邻氯三氯甲苯的方法,所使用的微反应设备包括:微反应器10,微反应器10的预热腔1一端设有邻氯甲苯进口,微反应器10的混合腔2设有邻氯甲苯进口和氯气进口,并与第一反应腔3、第二反应腔4、第三反应腔5、第四反应腔6、第五反应腔7、第六反应腔8、冷却腔9连通,冷却腔9之后与后处理装置15连通,反应液在经后处理装置15处理后,可获得产品邻氯三氯甲苯;氯气进口连通有氯气储罐11,氯气储罐11依次经过氯化钙干燥剂12和流量计13后通入氯气进口进入混合腔2中,邻氯甲苯进口连通有平流泵14,通过平流泵14,邻氯甲苯进入至预热腔1预热,预热后的邻氯甲苯通过邻氯甲苯进口进入混合腔2中;微反应器10中的预热腔1、混合腔2、第一反应腔3至第六反应腔8、冷却腔9外侧设有换热层,换热层内灌装高效换热油作为导热介质,通过控温系统16可以控制微反应器10中预热腔1、混合腔2、第一反应腔3至第六反应腔8的温度,第一反应腔3至第六反应腔8外均设有紫外光灯。
30.如图2所示,心形微反应通道17由心形微腔串联而成,心形微腔还包括反应液挡板18,反应液挡板位于心形微腔宽侧19,反应液的流动方向为由心形微腔宽侧19流入,经反应液挡板18均匀混合后,至心形微腔窄侧20流出,流入下一个心形微腔宽侧19。
31.实施例2本实施例设计一种微反应连续光催化邻氯甲苯制备邻氯三氯甲苯的方法,包括以下步骤:提供微反应器,微反应器包括预热腔、混合腔和反应腔,反应腔设置为6个,分别为第一反应腔、第二反应腔、第三反应腔、第四反应腔、第五反应腔和第六反应腔,上述第一反应腔至第六反应腔外均设置有紫外灯;(1)采用预热腔在90-140℃下对邻氯甲苯进行预热,将预热后的邻氯甲苯输送至混合腔,并将除水后的氯气通入混合腔得到反应液,氯气与邻氯甲苯的摩尔比为3.1~4.2:1;(2)反应液依次流过第一至第六反应腔,并在紫外灯下进行连续光催化反应,后处理之后得到邻氯三氯甲苯,其中紫外灯波长为360~370nm,功率为15~80w,反应液在反应腔中的总停留时间为80~150s,由于反应腔是多个串联在一起的,之间还包含小段的通道,因此此处反应液在反应腔中的总停留时间准确来讲具体包括反应液在多个反应腔中的总时间以及反应腔之间连接的小段管道中的通过时间。
32.根据上述制备方法制备得到邻氯三氯甲苯1#-3#和对比邻氯三氯甲苯d1#-d3#,具体不同之处如下:邻氯三氯甲苯1#(1)邻氯甲苯通过平流泵进入微反应器中的预热腔,预热110℃;(2)按照氯气与邻氯甲苯的反应摩尔比为3.6:1,设置邻氯甲苯和氯气柱塞泵流量分别为42ml/min和24.7l/min,分别连续输送至微反应器中;(3)氯气和预热后的邻氯甲苯进入混合腔进行混合;(4)反应液依次经过第一反应腔至第六反应腔,在365nm、50w的紫外光催化下进行光催化反应,控制反应腔温度为110℃,反应液在反应腔中的总停留时间为105s。
33.(5)反应液流经冷却腔冷却后,进入后处理装置,依次进行氮气吹扫、碱液吸收尾气处理,所用碱液为氢氧化钠溶液,质量浓度为20%,最后精馏获得产品邻氯三氯甲苯1#。
34.邻氯三氯甲苯2#(1)邻氯甲苯通过平流泵进入微反应器中的预热腔,预热到90℃;(2)按照氯气与邻氯甲苯的反应摩尔比为3.1:1,设置邻氯甲苯和氯气柱塞泵流量分别为53.6ml/min和36.6l/min,分别连续输送至微反应器中;(3)氯气和预热后的邻氯甲苯进入混合腔进行混合;(4)反应液依次经过第一反应腔至第六反应腔,在360nm、15w的紫外光催化下进行光催化反应,控制反应腔温度为90℃,反应液在反应腔中的总停留时间为80s。
35.(5)反应液流经冷却腔冷却后,进入后处理装置,依次进行氮气吹扫、碱液吸收尾气处理,所用碱液为氢氧化钠溶液,质量浓度为20%,最后精馏获得产品邻氯三氯甲苯2#。
36.邻氯三氯甲苯3#(1)邻氯甲苯通过平流泵进入微反应器中的预热腔,预热到140℃;(2)按照氯气与邻氯甲苯的反应摩尔比为4.2:1,设置邻氯甲苯和氯气柱塞泵流量分别为24.5ml/min和12.35l/min,分别连续输送至微反应器中;(3)氯气和预热后的邻氯甲苯进入混合腔进行混合;(4)反应液依次经过第一反应腔至第六反应腔,在370nm、80w的紫外光催化下进行光催化反应,控制反应腔温度为140℃,反应液在反应腔中的总停留时间为150s。
37.(5)反应液流经冷却腔冷却后,进入后处理装置,依次进行氮气吹扫、碱液吸收尾气处理,所用碱液为氢氧化钠溶液,质量浓度为20%,最后精馏获得产品邻氯三氯甲苯3#。
38.对比邻氯三氯甲苯d1#与邻氯三氯甲苯1#相比,反应液至只流经一个反应腔,通过控制邻氯甲苯和氯气柱塞泵流量保持反应液在反应腔中的总停留时间为105s,其他步骤和条件与实施例1相同,最后获得产品对比邻氯三氯甲苯d1#。
39.对比邻氯三氯甲苯d2#与邻氯三氯甲苯1#相比,邻氯甲苯通过平流泵直接进入混合腔与氯气混合,不进入预热腔进行预热,其他步骤和条件与实施例1相同,最后获得产品对比邻氯三氯甲苯d2#。
40.对比邻氯三氯甲苯d3#与邻氯三氯甲苯1#相比,邻氯甲苯通过平流泵进入预热腔进行预热后,不经混合腔与氯气混合直接进入反应腔进行光催化反应,其他步骤和条件与实施例1相同,最后获得产品对比邻氯三氯甲苯d3#。
41.实施例3本实施例涉及制备邻氯三氯甲苯4#-11#的制备,其制备过程和条件如表1所示,其他条件均与实施例2中邻氯三氯甲苯1#的制备条件相同。
42.实施例4本实施例涉及邻氯三氯甲苯12#的制备,其制备过程中设置反应腔内紫外灯的功率随反应液流动方向呈增大趋势,具体的:所述第一反应腔、第二反应腔、第三反应腔紫外灯功率为50w,第四反应腔紫外灯功率为55w,第五反应腔紫外灯功率为65w,第六反应腔紫外灯功率为75w,其他条件与实施例2中邻氯三氯甲苯1#的制备条件相同。
43.实验例1对实施例2-4制备的邻氯三氯甲苯1#~12#和对比邻氯三氯甲苯d1#~d3#进行邻氯三氯甲苯转化率、酰氯杂质含量、其他杂质含量和产品纯度的检测与计算,结果如下表2所示。
44.根据表2中的数据可知,由1#、4#、5#可知,氯气与邻氯甲苯的比例过低会使邻氯甲苯的反应不完全,导致邻氯甲苯剩余量过多,反应物的转化率很低,而氯气与邻氯甲苯比例过高的实施例5#与实施例1#相比不仅没有提升邻氯三氯甲苯转化率,还会因促进了邻氯三氯甲苯向邻氯苯甲酰的转化,而导致酰氯杂质含量升高,但是氯气与邻氯甲苯的比例过高
的实施例5#相比氯气与邻氯甲苯的比例过低的实施例4#,邻氯三氯甲苯反应更加完全,因此邻氯三氯甲苯转化率更高;由1#、6#、7#可知,温度过低时,反应的转化率较低,而温度过高时反应转化率虽然比较高,但过高的温度却会导致杂质含量也会相应升高,这是由于反应温度过高会引起反应物的碳化。由1#、8#、9#可知,停留时间过短,反应物的反应不充分,导致反应的转化率偏低,而停留时间长,虽然反应物的反应更加彻底,反应转化率也高,但是由于本技术中的光催化反应每次反应都是微量反应,反应时间过长导致通量会大大降低,从而会对生产效率产生较大的影响。由1#、10#、11#可知,紫外灯的功率过低,光催化的效果较差,导致反应转化率过低,而紫外灯的功率过高,虽然反应转化率提高,但是紫外光功率过高,能量过强会引起反应物发生碳化,导致杂质含量升高,并且降低反应的转化率。
45.本说明书中未作详细描述的内容属于本领域专业技术人员公知的现有技术。以上所述仅为本技术的实施例而已,并不用于限制本技术。对于本领域技术人员来说,本技术可以有各种更改和变化。凡在本技术的精神和原理之内所作的任何修改、等同替换、改进等,均应包含在本技术的权利要求范围之内。
再多了解一些
本文用于创业者技术爱好者查询,仅供学习研究,如用于商业用途,请联系技术所有人。