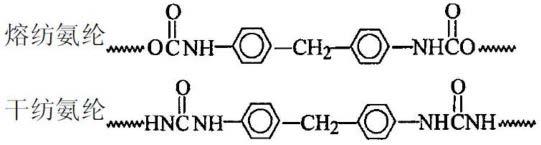
1.本发明涉及无纺布技术领域,具体涉及一种弹性复合材料的制备方法及其弹性复合材料。
背景技术:
2.目前,随着一次性吸收制品朝着舒适化、透气性以及适身性的趋势发展,弹性复合材料如弹性无纺布、弹性片材、弹性膜等在一次性吸收制品中得到了广泛的应用,这些弹性材料用于一次性吸收制品的弹性腰围,也可以将弹性材料裁剪为拉拉裤样式。
3.现有弹性复合材料均采用三层复合结构,并大多以氨纶丝为弹性材料,即由无纺布上层、无纺布下层以及位于无纺布上层、无纺布下层之间的氨纶丝通过热熔胶复合而成,其中,无纺布上层、无纺布下层均具有沿纵向方向延伸的皱褶结构。如公开号为cn113017991a的现有技术公开了一种新型弹性腰围无纺布,如附图1所示,包括上层弹性无纺布1、下层弹性无纺布2以及夹设在两者之间的弹性元件3(橡筋),所述上层弹性无纺布1沿其厚度方向呈具有交错设置的上层波峰部11及上层波谷部12的波浪线状结构,所述下层弹性无纺布2沿其厚度方向呈具有交错设置的下层波峰部22及下层波谷部21的波浪线状结构,制备时在所述上层弹性无纺布与橡筋、橡筋与下层弹性无纺布之间设置热熔胶而后进行粘合,形成所述新型弹性腰围无纺布。
4.可见,现有弹性复合材料大多以橡筋为弹性材料,使弹性复合材料具有伸缩回复性。具体地,本领域均选择氨纶丝为所述橡筋。然而,本领域技术人员所熟知的是,氨纶是一种由氨基甲酸酯嵌段共聚物组成的聚氨酯弹性纤维,氨纶具有优异的回弹性和极高的变形性,得到广泛地应用和迅速地发展,目前氨纶主要采用以下四种方法制备:
①
干法纺丝(干纺);
②
湿法纺丝;
③
熔融纺丝(熔纺);
④
化学纺丝。其中,本领域普遍应用的多为干法纺丝制成的氨纶丝,用干法纺丝纺制的氨纶高分子主链中含有脲键基团,其氢键结合力强,软硬链段分离程度高。氨纶的干法纺丝具体为首先采用低分子量聚酯二醇或聚醚二醇与过量的二异氰酸酯进行预聚,生成分子量约为3000至5000两端为异氰酸酯的预聚体;然后用溶剂将预聚体溶解,采用二胺作为扩链剂进行扩链,生成分子量为40000至100000的聚氨酯脲嵌段共聚物纺丝原液;最后经喷丝板喷出原液细流,经甬道蒸发溶剂,固化形成氨纶纤维。氨纶的变形性能和回弹性能良好。
5.继干纺氨纶丝之后,熔纺氨纶也是目前世界上材料领域的研究热点之一,且从目前熔纺氨纶丝的性能来看,熔纺氨纶丝的产品性能与干纺氨纶丝的性能相当。熔融纺丝是利用聚氨酯熔融流体进行纤维成形的一种方法。熔融纺丝采取本体预聚和扩链的方法制备纺丝切片,然后采用熔融纺丝机进行纺丝、即将聚酯或聚醚二元醇、二异氰酸酯、扩链剂按一定配比在挤出机中聚合、熔融,直接纺制氨纶。该方法与干纺氨纶丝的区别在于,熔融纺丝纺制的氨纶不能采用二胺作为扩链剂,通常采用二醇作为扩链剂,形成氨酯键的结构,二者结构上的差别如下所示:
[0006][0007]
可见,用熔融纺丝纺制的氨纶高分子主链中只含有氨基甲酸酯基团,其原因在于,若采用二胺(如乙二胺、丙二胺)作为扩链剂,在扩链产物聚氨基甲酸酯脲分子主链中就会形成脲键基团,而脲键基团的熔点高于其热分解温度。
[0008]
综上,无论干纺氨纶丝还是熔纺氨纶丝均可以采用胶黏剂(热熔胶)与无纺布等基材进行复合,但是,采用胶黏剂复合也存在如下问题:其一、胶黏剂的性能及其施工工艺均影响弹性复合材料的拉伸回复性能,主要表现在:(1)若胶黏剂的内聚强度不足,容易导致氨纶丝的回缩蠕变;(2)施胶量是否均匀;(3)热胶剂的开放时间,开放时间过短难以实现复合,而开放时间过长,则在弹性复合材料收卷过程中将产生黏连现象,直接影响使用性能;(4)胶黏剂的耐候性,特别在严寒的冬季可能发生失粘现象,等。
[0009]
针对本领域胶黏复合工艺存在的问题,本技术的发明人在无数次的研发、试验过程中发现:对于熔纺氨纶丝可以采用熔融粘合的复合方式,将上层弹性无纺布(第一基材层)与橡筋(熔纺氨纶丝)与下层弹性无纺布(第二基材层)直接进行熔融粘合,形成新型弹性复合材料。此外,本技术的发明人在试验过程中还发现:对于干纺氨纶丝无法通过熔融粘合或超声波焊接的复合方式进行熔融粘合,其必须采用胶黏复合方式,这可能是由于熔纺氨纶丝与干纺氨纶丝存在不同的分子基团导致。
[0010]
此外,需要指出的时,虽然公开号为cn113017991a的现有技术公开也提出,该现有技术的新型弹性腰围无纺布也可以采用将所述上层弹性无纺布、橡筋与下层弹性无纺布进行超声波焊接或者热压合。但是,如前所述,对于干纺氨纶丝是无法通过熔融粘合或超声波焊接的复合方式进行熔融粘合,因此,该现有技术对于其新型弹性腰围无纺布所声称的超声波焊接或者热压合仅仅为一种复合工艺的设想,缺乏必要的技术手段,因此,无法实现该设想。
技术实现要素:
[0011]
本发明所要解决的技术问题在于,针对现有弹性材料(弹性无纺布)采用胶黏剂的复合方式存在的问题提供一种新型复合方式,即采用熔融粘合的复合方式将氨纶丝与基材层连接为一体。
[0012]
为解决上述问题,本技术采用以下的技术方案:所述弹性复合材料的制备方法包括氨纶丝以及连接所述氨纶丝的基材层,然后采用熔融粘合的复合方式将氨纶丝与基材层连接为一体,所述熔融粘合的复合步骤如下:
[0013]
步骤一、氨纶丝类型选择及其熔点参数的测试步骤:选择熔纺氨纶丝,检测所述熔纺氨纶丝的熔点,记为t1。
[0014]
步骤二、基材层熔点参数的测试步骤:测试基材层材料的熔点,记为t2。
[0015]
步骤三、基材层熔点与熔纺氨纶丝熔点的适配性选择:当t2与t1相同或相近时,即可选择熔融粘合的复合方式将氨纶丝与基材层连接为一体。
[0016]
步骤四、熔融粘合的熔点选择:在步骤三的基础上,基于t1、t2选择若干温度对基
材层与熔纺氨纶丝进行预熔融粘合,并依预制的弹性复合材料的性能选择适配的粘合熔点。
[0017]
步骤五、熔融粘合:基于粘合熔点设定熔融温度;将所述基材层通过成型辊形成褶裥结构,并在基材层上铺设熔纺氨纶丝,然后将熔纺氨纶丝与基材层在熔融温度下熔融粘合为一体,从而使得弹性复合材料具有拉伸回复性。
[0018]
在一些实施例中,所述熔融粘合为热压熔融粘合,并通过采用成型辊、热压装置进行热压熔融粘合,其中,所述成型辊由凸辊和凹辊组成,且沿凸辊的外侧周向地设有成型凸台,而沿凹辊的外侧周向地设有与所述成型凸台相适配的成型凹槽,在所述成型凸台的顶部、成型凹槽的底部分别设置有温度达到所述熔融温度的热压装置而形成热压成型辊,所述基材层经成型辊形成褶裥结构后,通过热压装置将熔纺氨纶丝与基材层进行热压熔融粘合为一体。
[0019]
在其他实施例中,所述熔融粘合为超声波熔融焊接。所述熔融粘合采用成型辊、超声波装置进行超声波熔融焊接,其中,所述成型辊由凸辊和凹辊组成,沿凸辊的外侧周向地设有成型凸台,而沿凹辊的外侧周向地设有与所述成型凸台相适配的成型凹槽,所述基材层经成型辊形成褶裥结构后,通过超声波装置与熔纺氨纶丝超声波熔融焊接为一体。
[0020]
本技术上述熔融粘合的复合方式可以应用在双层结构弹性复合材料中。所述弹性复合材料采用由基材层、熔纺氨纶丝弹性层组成的双层结构弹性复合材料,所述基材层具有由波峰部以及连接波峰部的波谷部组成、并沿基材层的纵向方向依次交替延展的所述褶裥结构,然后沿基材层的幅宽横向方向在基材层上间隔地设有复数根的熔纺氨纶丝,每一熔纺氨纶丝的两端部均沿着基材层的纵向方向平行铺展而形成所述熔纺氨纶丝弹性层,并通过熔融粘合的复合方式将所述熔纺氨纶丝与波谷部复合连接,使得弹性复合材料在其纵向方向上具有拉伸回复性。
[0021]
本技术上述熔融粘合的复合方式也可以应用在三层结构弹性复合材料中。所述基材层包括第一基材层、第二基材层组成,所述弹性复合材料采用第一基材层、第二基材层以及位于所述第一基材层、第二基材层之间的熔纺氨纶丝弹性层组成,所述第一基材层、第二基材层均具有由波峰部以及连接波峰部的波谷部组成、并沿基材层的纵向方向依次交替延展的所述褶裥结构,然后沿基材层的幅宽横向方向,在所述第一基材层、第二基材层之间间隔地设有复数根的熔纺氨纶丝,每一熔纺氨纶丝的两端部均沿着基材层的纵向方向平行铺展而形成所述熔纺氨纶丝弹性层,并通过熔融粘合的复合方式将所述熔纺氨纶丝分别与第一基材层的波谷部、第二基材层的波峰部复合连接,使得弹性复合材料在其纵向方向上具有拉伸回复性。
[0022]
优选地,所述基材层选自纺粘无纺布、双组份无纺布、热风无纺布、透气膜、涤纶面料、锦纶面料或流延膜。
[0023]
优选地,所述熔纺氨纶丝采用10-2000denier的氨纶丝,两相邻的熔纺氨纶丝之间的间距为0.5-6mm,其拉伸倍率为1.1-6.0。
[0024]
在上述技术方案的基础上申请继续提供一种弹性复合材料,所述弹性复合材料采用前述的制备方法制备而成。
[0025]
本发明实现的技术效果如下:
[0026]
1、由于采用熔融粘合的复合方式将熔纺氨纶丝与基材层复合连接,避免了胶黏复
合工艺存在的问题,诸如氨纶丝在拉伸使用状态下的回缩蠕变、施胶不均的问题以及胶黏剂开放时间不匹配导致的弹性复合材料收卷过程中将产生黏连现象。
[0027]
2、将熔融粘合的复合方式替代现有的胶黏复合工艺,减少了胶黏剂耗材的费用,降低生产成本。
[0028]
3、在产品结构、材料一致的情况下,采用熔融粘合的复合方式获得弹性复合材料,比胶黏复合工艺的弹性材料更加柔软,具有更优的柔软度和手感体验。
附图说明
[0029]
图1是现有的弹性腰围无纺布结构示意图。
具体实施方式
[0030]
为了使本发明所要解决的技术问题、技术方案及有益效果更加清楚、明白,以下结合实施例,对本发明进行进一步详细说明。应当理解,此处所描述的具体实施例仅用以解释本发明,并不用于限定发明。
[0031]
为解决现有弹性材料(弹性无纺布)采用胶黏剂的复合方式存在的问题,本技术的发明人经过无数次的试验与验证发现,对于熔纺氨纶丝可以采用熔融粘合的复合方式,即将热熔性材料(基材层)与熔纺氨纶丝直接进行熔融粘合,形成新型弹性复合材料,而对于干纺氨纶丝则无法通过熔融粘合或超声波焊接的复合方式进行熔融粘合,其必须采用胶黏复合方式,这可能是由于熔纺氨纶丝与干纺氨纶丝存在不同的分子基团导致。
[0032]
本技术根据以上试验现象提供一种热熔性材料(基材层)与熔纺氨纶丝之间的新型复合方式,即采用熔融粘合的复合方式将氨纶丝与基材层连接为一体,具体为:所述弹性复合材料的制备方法包括氨纶丝以及连接所述氨纶丝的基材层,然后采用熔融粘合的复合方式将氨纶丝与基材层连接为一体,所述熔融粘合的复合步骤如下:
[0033]
步骤一、氨纶丝类型选择及其熔点参数的测试步骤:选择熔纺氨纶丝,检测所述熔纺氨纶丝的熔点,记为t1。
[0034]
步骤二、基材层熔点参数的测试步骤:测试基材层材料的熔点,记为t2。
[0035]
步骤三、基材层熔点与熔纺氨纶丝熔点的适配性选择:当t2与t1相同或相近时,即可选择熔融粘合的复合方式将氨纶丝与基材层连接为一体。
[0036]
步骤四、熔融粘合的熔点选择:在步骤三的基础上,基于t1、t2选择若干温度对基材层与熔纺氨纶丝进行预熔融粘合,并依预制的弹性复合材料的性能选择适配的粘合熔点。
[0037]
步骤五、熔融粘合:基于粘合熔点设定熔融温度;将所述基材层通过成型辊形成褶裥结构,并在基材层上铺设熔纺氨纶丝,然后将熔纺氨纶丝与基材层在熔融温度下熔融粘合为一体,从而使得弹性复合材料具有拉伸回复性。
[0038]
在具体实施方式中,所述熔融粘合为热压熔融粘合或超声波熔融焊接。其中:
[0039]
在一些实施例中,所述熔融粘合为热压熔融粘合。所述熔融粘合采用成型辊、热压装置进行热压熔融粘合,其中,所述成型辊为热压成型辊,所述热压成型辊由凸辊和凹辊组成,其中,沿凸辊的外侧周向地设有成型凸台,而沿凹辊的外侧周向地设有与所述成型凸台相适配的成型凹槽;在所述成型凸台的顶部、成型凹槽的底部分别设置有温度达到所述熔
融温度的热压装置,所述基材层经成型辊形成褶裥结构后,通过热压装置将熔纺氨纶丝与基材层进行热压熔融粘合为一体。
[0040]
在其他实施例中,所述熔融粘合为超声波熔融焊接。所述熔融粘合采用成型辊、超声波装置进行超声波熔融焊接,其中,所述成型辊由凸辊和凹辊组成,沿凸辊的外侧周向地设有成型凸台,而沿凹辊的外侧周向地设有与所述成型凸台相适配的成型凹槽,所述基材层经成型辊形成褶裥结构后,通过超声波装置与熔纺氨纶丝超声波熔融焊接为一体。
[0041]
需要说明书的是,本技术上述熔融粘合的复合方式可以应用在双层结构弹性复合材料中,也可以应用在三层结构弹性复合材料中,甚至更多层(如四层或五层)的弹性复合材料中。
[0042]
以下通过实施例的方式对上述方法进行说明。
[0043]
实施例1
[0044]
本实施例的弹性复合材料采用由基材层、熔纺氨纶丝弹性层组成的双层结构弹性复合材料。其中,基材层采用平方克重22g/m2的纺粘无纺布,熔纺氨纶丝弹性层内的熔纺氨纶丝480d,两相邻氨纶丝之间的间距为3mm。该纺粘无纺布、熔纺氨纶丝均为市售商品。
[0045]
本实施例采用熔融粘合的复合方式将氨纶丝与纺粘无纺布连接为一体,所述熔融粘合的复合步骤如下:
[0046]
步骤一、选择熔纺氨纶丝,检测熔纺氨纶丝的熔点为168℃(记为t1)。
[0047]
步骤二、测试纺粘无纺布材料的熔点为172℃(记为t2)。
[0048]
步骤三、由于t2与t1相近时,即可选择熔融粘合的复合方式将熔纺氨纶丝与纺粘无纺布连接为一体。
[0049]
在步骤三的基础上,基于t1、t2选择若干温度对纺粘无纺布与熔纺氨纶丝进行预熔融粘合,并依预制的弹性复合材料的性能选择适配的粘合熔点168-169℃。
[0050]
步骤四、熔融粘合的步骤:所述熔融粘合采用成型辊、热压装置进行热压熔融粘合,其中,所述成型辊为现有设备,其为本领域技术人员所熟悉掌握,本领域技术人员也可以根据现有技术如cn113017991a进行实施,如由凸辊和凹辊组成,且沿凸辊的外侧周向地设有成型凸台,而沿凹辊的外侧周向地设有与所述成型凸台相适配的成型凹槽。
[0051]
本实施例在于在现有成型辊的基础上设置热压装置,在所述成型凸台的顶部、成型凹槽的底部分别设置有温度可达到熔融温度的热压装置,使成型辊具有加热使得熔纺氨纶丝、纺粘无纺布熔融并经热压粘合(熔融粘合)的热压成型辊。
[0052]
设定熔融温度168或169℃,采用热压成型辊将纺粘无纺布加工成具有由波峰部以及连接波峰部的波谷部组成、并沿纺粘无纺布的纵向方向依次交替延展的褶裥结构;然后,沿纺粘无纺布的幅宽横向方向在纺粘无纺布上间隔地设有复数根的熔纺氨纶丝。间距为0.5-6mm。
[0053]
每一熔纺氨纶丝的两端部均沿着纺粘无纺布的纵向方向平行铺展而形成所述熔纺氨纶丝弹性层。其中,本实施例对氨纶丝的旦数、拉伸倍率不作具体的限制,但可优选拉伸倍率1.1-6.0、旦数10-2000denier。本实施例氨纶丝的拉伸倍率为1.4倍,旦数为140d,间距为3mm。
[0054]
在褶裥结构成型的过程中,热压装置对波谷部的纺粘无纺布或熔纺氨纶丝进行加热,实现熔融粘合的复合方式,使得熔纺氨纶丝与波谷部复合连接而获得弹性复合无纺布,
该复合无纺布在其纵向方向上具有拉伸回复性。
[0055]
实施例2
[0056]
本实施例与实施例1的区别在于,本实施例的弹性复合材料采用第一纺粘无纺布、第二纺粘无纺布以及位于二者之间的熔纺氨纶丝弹性层组成的三层结构弹性复合材料。其中,第一纺粘无纺布(上层)、第二纺粘无纺(下层)均采用22g/m2的纺粘无纺布。其他参数及其实施方式同实施例1。
[0057]
采用热压成型辊分别将第一纺粘无纺布、第二纺粘无纺布加工成具有由波峰部以及连接波峰部的波谷部组成、并沿纺粘无纺布的纵向方向依次交替延展的褶裥结构。然后沿纺粘无纺布的幅宽横向方向设有复数根的熔纺氨纶丝。最后,在褶裥结构成型的过程中,热压装置分别对第一纺粘无纺布、第二纺粘无纺布和熔纺氨纶丝进行加热处理,实现熔融粘合的复合方式,使得熔纺氨纶丝与波谷部复合连接而获得弹性复合无纺布,该复合无纺布在其纵向方向上具有拉伸回复性。
[0058]
实施例3
[0059]
本实施例与实施例1的区别在于,本实施例的熔融粘合采用成型辊、超声波装置进行超声波熔融焊接,其他参数及步骤与实施例1相同。其中,所述成型辊由凸辊和凹辊组成,沿凸辊的外侧周向地设有成型凸台,而沿凹辊的外侧周向地设有与所述成型凸台相适配的成型凹槽。本实施例的超声波装置为市售设备,采用超声波装置对热熔性聚合物进行热熔焊接为本领域技术人员所掌握。
[0060]
本实施例采用超声波装置对熔纺氨纶丝、纺粘无纺布分别加热熔融,经过成型辊的压合作用进行热焊接而获得弹性复合无纺布,该复合无纺布在其纵向方向上具有拉伸回复性。
[0061]
实施例4
[0062]
本实施例与实施例2的区别在于,本实施例的熔融粘合采用成型辊、超声波装置进行超声波熔融焊接而获得弹性复合无纺布,该复合无纺布在其纵向方向上具有拉伸回复性。其他参数及步骤与实施例2相同。
[0063]
需要说明的是,上述实施例中的纺粘无纺布可以选择双组份无纺布、热风无纺布、透气膜、涤纶面料、锦纶面料或流延膜进行替代。
[0064]
性能测试:
[0065]
测试样品:由于现有弹性无纺布均为三层结构弹性无纺布,为便于对比,将实施例2、4制得三层结构的弹性复合无纺布为测试样品。
[0066]
对比样品:以市购的三层结构弹性复合无纺布为对比样。经分析,该对比样的纺粘无纺布为20g/m2,本实施例氨纶丝的拉伸倍率为1.38倍,旦数为160d,间距为3.2mm。
[0067]
测试方法:
[0068]
柔软度测试:参照gb/t 8942-2016《纸柔软度的测定》。
[0069]
耐蠕变性能测试:准备测试硬纸板,然后将测试样品和对比样品完全拉伸后用订书钉等将样品固定在硬纸板上,然后量取氨纶丝的测试段25cm,在每一根氨纶丝对应于测试段的两端采用记号笔作标记。然后将上述样品置于40℃的恒温烘箱中12h后,取出氨纶丝的标记蠕变即回缩后的长度,蠕变率计算方式如下:蠕变率(%)=(25-l1)/25*100%,其中,l1为氨纶丝标记段回缩后的长度,取三次测试的平均值作为测试结果。
[0070]
测试结果:
[0071]
表1弹性无纺布柔软度
[0072][0073]
以上试验数据表明,采用熔融粘合的复合方式将熔纺氨纶丝与基材层(纺粘无纺布等)复合而成的弹性无纺布比胶黏复合工艺的弹性材料更加柔软,具有更优的柔软度和手感体验,且熔融粘合的复合方式可以有效提高氨纶丝在拉伸使用状态下的回缩蠕变的问题。
[0074]
上述说明示出并描述了本发明的优选实施例,如前所述,应当理解本发明并非局限于本文所披露的形式,不应看作是对其他实施例的排除,而可用于各种其他组合、修改和环境,并能够在本文所述发明构想范围内,通过上述教导或相关领域的技术或知识进行改动。而本领域人员所进行的改动和变化不脱离本发明的精神和范围,则都应在本发明所附权利要求的保护范围内。
再多了解一些
本文用于创业者技术爱好者查询,仅供学习研究,如用于商业用途,请联系技术所有人。