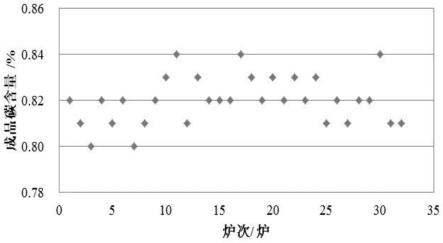
1.本发明涉及金属冶炼技术领域,尤其涉及一种拉拔性能优良的高强预应力钢绞线用钢冶炼生产方法。
背景技术:
2.预应力产品制造企业的技术水平和产品质量参差不齐,在高端产品供应一直偏紧。由于预应力钢绞线的生产工艺和生产设备相对简单,技术门槛较低,生产企业不断增多,造成同质化产品多,供大于求,市场竞争激烈。但一些重点工程用预应力产品准入门槛较高,市场应用前景广阔,而且未来随着我国铁路、公路、及建筑行业的稳步发展,对高品质预应力产品的需求将进一步增加。高强预应力钢绞线主要应用于毛利率相对较高的锚具和缆索产品,未来毛利率将保持稳定增长态势。本发明专利通过高洁净冶炼工艺、连铸工艺关键技术研究,获得拉拔性能优良的高强预应力钢绞线用钢,稳定了产品的质量,并形成了一种拉拔性能优良的预应力高强钢绞线用钢生产方法。
技术实现要素:
3.本发明的目的是提供一种拉拔性能优良的高强预应力钢绞线用钢冶炼生产方法,通过高洁净冶炼工艺、连铸工艺关键技术研究,提高预应力钢绞线用钢的拉拔性能。
4.本发明涉及的钢种为gb/t24238-2017标准中的yl72b、yl77b、yl82b、yl87b预应力钢绞线用热轧盘条,具体化学成分见标准要求。
5.为解决上述技术问题,本发明采用如下技术方案:
6.本发明一种拉拔性能优良的高强预应力钢绞线用钢冶炼生产方法,包括:
7.1)、转炉终点控制
8.合理的供氧制度、终点控制是决定终点钢水中氧含量高低的关键环节,根据过程枪位控制、含铁料的加入时机、拉碳时机以及挡渣作业有效控制氧含量;在包钢矿石原料条件下,采用高拉碳工艺保证出钢碳含量控制≥0.10%;
9.2)、精炼精准控制
10.炉外精炼吹氩控制:lf炉为保证脱氧脱硫及去夹杂效果,要求前期脱硫时进行大氩气强烈搅拌,为580-620nl/min;处理过程中均匀成分及温度时氩气搅拌强度设定为400~500nl/min;精炼末期软吹时氩气搅拌流量减少,避免裸露钢水液面,引起二次氧化;
11.对于盘条规格大于13mm的yl82b及冬季生产的yl82b要求增加vd真空脱气工序,而且vd真空过程要求氩气控制;加强vd工序软吹工艺控制,对高碳钢的处理尤为重要;合适的吹氩控制,能促进vd钢渣混合渣洗后夹杂物的上浮和去除。包钢yl82b要求软吹时间在15min以上;生产实践表明在vd破空后存在颗粒较大的mg-al系夹杂,增加5min以上镇静时间;
12.精炼炉进站温度要求1503~1533℃,钢包净空>500mm;打开工作门,调整氩气流量,控制吹开区域直径约300~400mm;进站先加入电石20kg,然后进行加热,加入石灰
200kg,石英砂60kg;白渣操作:电流平稳后,顶渣融化良好,进行造白渣操作,根据炉渣情况加入硅铁粉40kg,脱氧剂要求撒在渣子表面,待下次加热停止后蘸样观察渣子颜色,如透明玻璃色或灰白色,则视为白渣造好,否则继续撒入脱氧剂。再次脱氧操作执行以上要求。合金加入量依据内控成份要求进行调整。整个精炼过程加热时间不低于10分钟。整个精炼过程保证包内气氛为还原性气氛,加热过程略微冒烟;若取样硫高,可在加热过程中增加石灰量,按每100kg石灰脱硫0.002~0.003%考虑。软吹时间15min以上,软吹过程不得裸露钢水。若浇注过程出现塞棒上扬,可适当喂入钙线,控制喂入量<50m;精炼上钢温度如表2:
13.表2精炼上钢温度要求/℃
[0014][0015]
3)、连铸工序控制
[0016]
对于150mm小方坯断面要求使用过钢量小于5000t的结晶器,结晶器内壁镀层不许脱落;二冷水系统零段及其它二冷段输出辊均务必运转正常;各段的气雾喷嘴、水喷嘴务必畅通,确保铸坯各面冷却均匀;中包烘烤大于1000℃;其烘烤方法执行现行规程;浸入式水口烘烤后使用,大包长水口随中包烘烤进行预热、干燥。中包的六个浸入式水口务必与结晶器上口对正、对中,偏差≤5mm,并用密封垫保护;大包长水口采用氩封保护浇注,其中氩气压力:0.20~0.30mpa,流量:50-80nl/min,以中包不露出钢液面为宜;
[0017]
大包开浇:中包对中后,至少用氩气气氛置换2.5分钟,大包再开浇,当中包钢水达到12t时,关闭氩气气氛置换,加入中包覆盖剂;不许过早加入,以免造成混渣增碳;要求浇注过程中中包液面不漏红;
[0018]
中包开浇:当中包液面达到400mm时即可开浇;浇注时浸入式水口插入深度:80~120mm;起步拉速0.5m/min,拉速调整每30秒调整0.1m/min,避免拉速调整过快,造成卷渣;中包温度测定:开浇5分钟测温一次,此后每10分钟测温一次,浇次第1炉结束前,必须投入连续测温,严禁手动测温;正常浇注时中包液面不能低于800mm;振动执行190hz/分,振幅
±
4mm,必须确保负滑脱时间为0.1s;保护渣粉渣层厚度控制在25-30mm之间。
[0019]
进一步的,所述步骤1)中:
[0020]
对原辅材料严格要求:
[0021]
(1)铁水要求:si0.3~0.7%,s≤0.070%,p≤0.120%,ti≤0.10%,t≥1250℃,带渣量不得超过0.5%;
[0022]
(2)铁皮球、纯废钢等所有物料务必干燥、无夹杂,减少带进钢中[h];
[0023]
(3)石灰要求烧透率>92%,活性度≥300,过烧≤3%,氧化钙≥85%,sio2≤10%,p、s≤0.05%,水分≤0.3%,块度5~40mm,粉末不得>10%;
[0024]
(4)合金要求来源清楚,成份符合国标要求;块度10~50mm;
[0025]
(5)粉状材料要求干燥,水分小于0.5%;
[0026]
(6)萤石不得潮湿;不得混有泥沙,表面有黑色斑点的不能使用;
[0027]
转炉冶炼为了控制钢水中夹杂物的生成数量,提升钢水的纯净度,必须控制终点钢中的氧含量,转炉工序对钢水洁净度的影响,关键是炉渣控制和终点控制,确保吹炼过程中,有效去除气体含量、减少夹杂物数量;
[0028]
转炉炉渣料以石灰、白云石、铁皮球为主,根据操作规程分批次加入;第一批加入石灰1500~1800kg,铁皮球1000kg,白云石200~400kg,同时视来铁情况进行动态调整,之后小批量多次加入,渣料总耗量60~80kg/t;
[0029]
转炉装入量控制在102吨,其中铁水95吨,废钢7吨,出钢量控制在93吨左右,自由空间≥300mm。供氧制度工作氧压:0.70~0.95mpa,流量:16000~17000m3/h,底吹全程采用吹ar(底吹已堵)。造碱度渣,渣碱度控制2.8~3.5,氧化镁:约8%。采用双渣操作,倒渣面高时加入适量小粒灰石压渣,初期渣碱度目标按1.5~2.0控制。终点控制转炉采用高拉碳工艺,出钢终点成分c≥0.10%,p≤0.010%,t:1610~1630℃。出钢时大包合金、渣料配比及用量见表1(kg/t):根据终点碳调整电石加入量,即:
[0030]
c<0.08%时,加1~1.2kg/t;
[0031]
0.08%<c<0.15%时,加0.8~1.0kg/t;
[0032]
c≥0.15%时,加0.6~0.8kg/t。
[0033]
表1合金、渣料配比及用量要求
[0034][0035]
注:表中数据未考虑钢中的残余成分,算量时要剔除残余;如合金主成分与表中不符,则另做调整即可。
[0036]
出钢时大包脱氧剂及合金加入顺序:增碳剂
→
合金
→
硅钙钡
→
石灰用溜槽加入,电石、萤石手投;钢包烘烤温度大于900℃;出钢口维护良好,采用双挡渣操作,出钢时间控制在≥4min;严禁下渣,防止回磷过量,要求回磷量≤0.003%采用sicaba复合脱氧剂;
[0037]
在转炉出钢后,根据转炉终点控制情况,加入一定量的硅钙钡脱氧剂,实施动态脱氧制度,最终使钢水的氧活度小于0.0025%;出钢后在钢包内加入一定量的合成渣及白灰,合理控制顶渣;在lf精炼向钢包内分批加入小粒硅钙钡,对炉渣和钢水进行脱氧;
[0038]
为了进一步降低钢水中的氧含量、夹杂物和铝含量,在lf精炼过程中,亦采用无铝造渣,控制合适的碱度和al2o3含量,形成能够吸附夹杂的cao-sio
2-caf2精炼渣系。
[0039]
进一步的,所述步骤3)中,在浇钢过程中凡是出现以下情况,铸坯必须挑出掉队处理:
[0040]
除开浇第一炉外,正常炉次过热度>50℃以上炉次,铸坯必须挑出掉队并加密取样;
[0041]
液位波动大于5mm的炉次,铸坯必须挑出掉队;
[0042]
恒拉速1.9m/min,特殊情况下拉速波动
±
0.1m/min,不在次拉速范围内的铸坯必须掉队,拉速超过2.1m/min的铸坯判废;
[0043]
正常浇钢过程中换水口,必须将换水口产生的接痕铸坯切净;浇钢过程中出坯人员严格检查铸坯表面质量,如果发现有肉眼可见的缺陷铸坯,包括接痕、划伤及弯曲,及时
通知机长关流,缺陷铸坯进行掉队待处理;
[0044]
连浇中间包钢水小于12吨时生产的铸坯一律挑出掉队;
[0045]
结晶器液位自动控制、电磁搅拌出现异常时生产的铸坯一律挑出掉队。
[0046]
进一步的,所述步骤3)中还包括:铸坯经过取样检验热酸低倍组织,铸坯不得出现严重脱方、鼓肚、中心缩孔,每炉取铸坯热酸低倍试样进行检验,皮下裂纹、皮下气泡、角部裂纹、中间裂纹缺陷级别不得大于1.5级,其余缺陷不得大于2级,超标铸坯一律改判。
[0047]
与现有技术相比,本发明的有益技术效果:
[0048]
产品质量稳定性评价达到95分以上,用户拉拔过程中断丝率≤1次/百吨,满足用户使用要求。
附图说明
[0049]
下面结合附图说明对本发明作进一步说明。
[0050]
图1为拉速控制示意图;
[0051]
图2为成品碳含量示意图;
[0052]
图3为横向偏析取样位置。
具体实施方式
[0053]
一种拉拔性能优良的高强预应力钢绞线用钢冶炼生产方法,包括:
[0054]
1、铁水条件
[0055]
铁水要求:si0.3~0.7%,s≤0.070%,p≤0.120%,ti≤0.10%,t≥1250℃,带渣量不得超过0.5%。具体实例如表3所示。
[0056]
表3铁水状况表
[0057]
具体实例si%p%s%温度(℃)具体实例10.400.1150.0221315具体实例20.460.1100.0171322具体实例30.590.1140.0201317具体实例40.450.1220.0231322具体实例50.600.1150.0141284具体实例60.450.1200.0231321
[0058]
2、转炉出钢情况
[0059]
转炉采用高拉碳工艺,出钢终点成分c≥0.06%,p≤0.010%,目标出钢终点c大于0.10%占80%。
[0060]
表4转炉出钢情况
[0061][0062][0063]
3、连铸工序情况
[0064]
拉速控制在1.7~1.9m/min,拉速波动较小,图1所示。开浇第1炉温度≤40℃,第2炉以后温度≤30℃。
[0065]
表5过热度控制表
[0066]
具体实例过热度(℃)具体实例135具体实例227具体实例326具体实例429具体实例530具体实例628
[0067]
4、钢中氢含量
[0068]
不走vd工序,钢水中h含量要求不大于5.0ppm。
[0069]
表6气体氢含量
[0070]
具体实例h/ppm具体实例13.0具体实例22.9具体实例33.1具体实例42.9具体实例52.8具体实例62.7
[0071]
5、钢中碳含量
[0072]
要求窄成分控制,c控制在0.82%-0.84%,如图2所示。
[0073]
6、铸坯质量
[0074]
硫印、低倍缺陷级别≤1.5级
[0075]
表7铸坯热酸低倍检验结果
[0076][0077]
7、气体氧氮结果
[0078]
要求[n]≤55ppm,[o]≤20ppm。
[0079]
表8铸坯氧氮检验结果
[0080]
具体实例o(ppm)n(ppm)具体实例12520具体实例21621具体实例31922具体实例42224具体实例51828具体实例62525
[0081]
8、成分偏析检验
[0082]
碳偏析指数最大1.15,平均碳偏析指数控制≤1.08。锰、铬偏析指数最大1.05。
[0083]
表9横向碳、锰、铬、偏析指数情况
[0084][0085]
表10纵向碳、锰、铬偏析指数情况
[0086][0087]
经应用,本发明的产品质量稳定性评价达到95分以上,用户拉拔过程中断丝率≤1次/百吨,满足用户使用要求。
[0088]
以上所述的实施例仅是对本发明的优选方式进行描述,并非对本发明的范围进行限定,在不脱离本发明设计精神的前提下,本领域普通技术人员对本发明的技术方案做出的各种变形和改进,均应落入本发明权利要求书确定的保护范围内。
再多了解一些
本文用于创业者技术爱好者查询,仅供学习研究,如用于商业用途,请联系技术所有人。