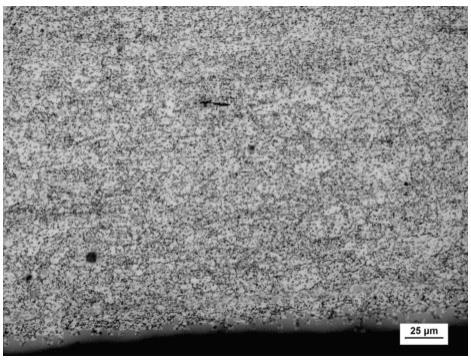
1.本发明属于中碳高合金钢技术领域,尤其涉及一种超高强冷轧钢板的制造方法,是一种具有高质量、高效率、环保的超高强冷轧钢板的生产方法。
背景技术:
2.35si2mncrmove是钢板厚度不大于6mm的冷轧钢板。材料主要特点为超高强度、高纯净度、冲压性能好、耐压性能好,属于“淬火 回火”状态使用的马氏体超高强度钢,对钢的强韧性能,尤其是断裂韧性有较高要求,对钢的内在和表面质量方面的要求较高,冷轧钢板头尾极易开裂,生产组织难度极大。该钢种传统工艺为模铸 开坯 单张热轧 单张冷轧。生产工艺复杂,冷轧变形抗力大冷轧易发生开裂,要求较高的钢质纯净度以及退火充分。
3.多年来该钢种冷轧钢板传统制造方法为:冶炼:碳钢线电炉—lf精炼—vd真空处理—模注扁锭—红送;开坯:均热—开坯—红退火—钢坯修磨;热轧:坯料加热—中板2300轧机单张轧制—热矫—定尺剪切;冷轧:坯料剪切—预退火—酸洗—2300冷轧机单张冷轧—成品退火—取样检验—矫直—探伤—精整(切边、切头尾)—外观检验—涂油—包装—入库。该传统制造方法特点为:
①
生产效率低,从模铸钢锭、开坯、热轧、冷轧均为单张轧制,全线成材率仅为40~45%;
②ꢀ
工艺流程长,生产周期长,订货周期≥3个月;
③ꢀ
生产设备老旧、功能精度差。该工艺涉及的开坯、热轧、冷轧轧机均为上世纪50-60年代设备,设备特点为单张往复轧制,轧制力小(1000-2700吨),公差保证能力弱(406公差要求为
±
0.3mm)。
4.35si2mncrmove钢属于“淬火 回火”状态使用的马氏体超高强度钢,对钢的强韧性能,尤其是断裂韧性有较高要求,对钢的内在和表面质量方面的要求较高,冷轧钢板头尾极易开裂,生产组织难度极大,传统工艺不仅成本较高,而且材料制造周期长,客户需提前至少三个月订货。
5.本发明为一种具有高质量、高效率、环保的超高强冷轧钢板的制造方法,采用连铸
→
热连轧
→
宽幅冷卷连轧工艺实现超高强冷轧钢板的制造,质量优于传统(模铸
→
开坯
→
单张热轧
→
单张冷轧)工艺,主要优点如下:
①ꢀ
钢质纯净度提高,原料采用铁水纯净度高,钢水经lf、rh、连铸可实现低p、s、低夹杂物含量控制;
②ꢀ
该工艺为热连轧 冷连轧,工艺周期短,全线成材率≥75%。
③ꢀ
该工艺采用设备为国内高水平热连轧 宽幅冷连轧技术生产,钢板板形以及精度控制水平大幅提升。
④
eps表面处理技术,取代酸洗工序,无污染及后续酸处理,满足环保要求,实现可持续发展。
技术实现要素:
6.本发明的目的就是针对上述问题,提供一种超高强冷轧钢板的制造方法。
7.本发明的目的是这样实现的:一种超高强冷轧钢板的制造方法,包括如下步骤:铁水预处理
→
转炉冶炼
→
炉外精炼
→
板坯连铸
→
热送热装
→
板坯加热
→
高压水除鳞
→
粗轧机组轧制
→
高压水除鳞
→
2250机组连轧
→
卷取
→
软化退火
→
eps表面处理
→
宽幅冷卷轧机
→
eps表面处理
→
退火
→
横切。
8.炉外精炼为lf深脱硫、rh真空脱气和ca处理球化夹杂物;lf炉精炼过程中,将钢水脱硫至s≤0.003%、保证低p≤0.009%;在rh精炼中,真空脱气处理结束,h≤2ppm;破真空后,对钢水进行ca处理,喂线量200~400m,对夹杂物进行变性。
9.板坯连铸中连铸浇注温度:1490-1520℃;目标拉速:0.8-1.4m/min;钢水过热度:15℃-45℃;铸坯轻压下:0-5mm;电磁搅拌:频率2.5-2.8hz。
10.板坯热送热装中,板坯热送热装温度:400-780℃。
11.板坯加热中,板坯加热温度1180-1290℃。
12.粗轧机组轧制中,粗轧终止温度:1000℃-1200℃,中间坯厚度:20-45mm。
13.精轧机组轧制中,精轧终止温度:780-950℃。
14.卷取中,带钢卷取温度:650-810℃,热轧卷板热处理温度:550-770℃。
15.eps表面处理中,eps生产速度设定3-10m/min;宽幅冷卷轧机压下率为30-65%。
16.退火中,冷轧卷罩式炉退火温度550-770℃。
17.本发明的有益效果是:1、本发明通过采用炉外精炼-lf合金化 rh真空脱气、ca处理球化夹杂物技术、冶炼过程各节点温度控制及全流程氧氮控制、轻压下和电磁搅拌技术的合理应用获得纯净钢质;开发了热送热装、轧后冷却及热处理工艺,实现了钢热轧衔接工序中可能产生的板坯裂纹缺陷的有效控制,获得了钢质纯净度高、组织均匀、脱碳倾向小的超高强冷轧钢板。
18.2、本发明的超高强冷轧钢板具有高表面质量、高纯净度、短生产周期及高成材率等特点。。
19.3、本发明的超高强冷轧钢板采用较高加热温度 控轧工艺生产,获得的热轧态组织为铁素体和珠光体,软化退火态组织为铁素体和球化珠光体。
附图说明
20.下面结合附图对本发明作进一步的描述。
21.图1是退火态组织图。
具体实施方式
22.本发明提出一种具有高质量、高效率、环保的超高强冷轧钢板的生产方法,较传统单张轧制的35si2mncrmove成材率提升20%以上,生产周期大幅缩短。其工艺路线为:铁水预处理
→
转炉冶炼
→
炉外精炼(lf rh)
→
板坯连铸
→
热送热装
→
板坯加热
→
高压水除鳞
→
热连轧控轧
→
卷取
→
罩式炉退火
→
eps表面处理
→
宽幅冷卷轧机
→
eps表面处理
→
罩式炉退火
→
横切。
23.在lf炉精炼过程中,将钢水脱硫至s≤0.003%、保证低p≤0.009%;在rh精炼中,真空脱气处理结束,h≤2ppm。破真空后,对钢水进行ca处理,喂线量200~400m,对夹杂物进行变性;在板坯连铸中,连铸浇注温度:1490-1520℃;目标拉速:0.8-1.4m/min;钢水过热度:15℃-45℃;铸坯轻压下:0-5mm;电磁搅拌:频率2.5-2.8hz;在板坯热送热装中,板坯热送热装温度≥ 400℃;在板坯加热中,板坯加热温度:1200℃-1290℃;在粗轧机组轧制中,粗轧机组终止温度:1000℃-1200℃,中间坯厚度:20~45mm;在精轧机组轧制中,精轧机组终止温度:780℃-950℃;在卷取中,钢带卷取温度:680℃-810℃;热轧钢带热处理温度:550-770
℃;eps表面处理,eps生产速度设定3-10m/min;宽幅冷卷轧机压下率为30-65%;eps表面处理,eps生产速度设定3-10m/min;冷轧卷罩式炉退火温度550-770℃;按照客户要求横切钢板。
24.所述转炉冶炼是将符合转炉冶炼的80~95%的预处理铁水、废钢([s]≤0.03%)加入转炉中,随炉装入钼铁50~65kg/吨、镍板0.28-0.30kg/吨。转炉出钢时,向钢水中加入碳粉3~5kg/吨钢,加入铝铁5~13kg/吨钢、高碳锰铁10~15kg/吨钢、硅锰合金15~20kg/吨钢、低p铬铁12~15kg/吨钢以及钒铁10~15kg/吨钢进行合金化。
[0025]
所述钼铁品位是mo≥60%;铝铁品位是al:36-46%;铬铁品位是cr≥65%;高碳锰铁品位是mn≥80%;硅锰合金品位是si≥18%、mn≥65%。
[0026]
所述lf精炼时加入石灰石,每吨钢水加石灰4.5~8kg脱s,将s脱至不大于0.003%。之后,加入v铁、nb铁、cr铁进行合金化,每吨钢水加v铁10~15kg、cr铁12~15kg。
[0027]
所述si-ca线芯粉中ca含量是25-35%;钒铁品位是v≥50%;铌铁品位是nb≥60%;铬铁品位是cr≥65%。
[0028]
所述rh精炼中,在真空压强值不大于4mbar状态下,循环时间不小于10分钟。破真空后,对钢水进行ca处理,喂入量200~400m对夹杂物变性,并以底吹氩流量100~200l/min进行弱搅,吹氩时间不小于8分钟。
[0029]
经化验分析,钢水的成分重量百分比为:c:0.34~0.38;si:1.40~1.70;mn:0.70~1.00;al:0.020~0.040;p:≤0.020;s:≤0.010;cr:1.00~1.30;mo:0.40~0.55;ni:0.25;v:0.08~0.15; n≤100ppm;o≤5ppm,h≤2ppm。
[0030]
板坯连铸中将钢包中的钢水加入到中间包中,通过结晶器连铸成板坯,连铸坯拉速0.8-1.40m/min,连铸浇注温度1490-1520℃,铸坯轻压下:0-5mm,钢水过热度:15-45℃,电磁搅拌:频率2.5-2.8hz。
[0031]
下面对本发明的一种超高强冷轧钢板的制造方法机理进行说明。
[0032]
本发明中为保证超高强冷轧钢板具有优异的断裂韧性,须保证高的钢质纯净度,对p、s及h、o含量的控制有严格要求。需选用优质废钢,铁水预处理时扒渣干净,铁水预处理至s≤0.005%,进入转炉冶炼,后采用lf深脱硫,脱至s≤0.003%,保证p≤0.009%。需进行rh深真空脱气处理,破真空后,还对钢水进行ca处理,对夹杂物变性。
[0033]
本发明中连铸坯拉速0.8-1.4m/min。板坯加热温度控制在1180℃-1290℃;轧制工艺为粗轧终止温度1000℃-1200℃,中间坯厚度20-60mm;精轧终止温度780℃-960℃;钢带卷取温度680℃-810℃;卷取后冷却工艺控制;进行软化退火,采用全氮气氛保护,退火温度550℃-770℃;eps表面处理,eps生产速度设定3-10m/min;宽幅冷卷轧机压下率为30-65%;eps表面处理,eps生产速度设定3-10m/min;冷轧卷罩式炉采用全氢气氛保护,退火温度550-770℃;本方法生产的超高强冷轧钢板获得的组织为铁素体和珠光体。
[0034]
本发明通过炉外精炼工艺、轻压下和电磁搅拌工艺、结合板坯热送热装、轧后冷却工艺控制、加热、轧制、卷取及退火工艺的制定,获得了一种高表面质量短生产周期的超高强冷轧钢板的理想组织和性能。
[0035]
本发明提供一种具有高质量、高效率、环保的超高强冷轧钢板的制造方法。较传统单张轧制的35si2mncrmove成材率提升20%以上,生产周期大幅缩短。本发明针对超高强冷
轧钢板35si2mncrmove提出通过钢水精炼、连铸控制、加热连续轧制、卷取、软化退火、eps及整卷冷轧、横切的方式,获得钢质纯净、具有优良性能的35si2mncrmove冷轧钢板的制造方法。包括如下步骤:铁水预处理
→
转炉冶炼
→
炉外精炼(lf rh)
→
板坯连铸
→
热送热装
→
板坯加热
→
高压水除鳞
→
粗轧机组轧制
→
高压水除鳞
→
2250机组连轧
→
卷取
→
软化退火
→
eps表面处理
→
宽幅冷卷轧机
→
eps表面处理
→
退火
→
横切。炉外精炼:lf深脱硫 rh真空脱气、ca处理球化夹杂物。b、板坯热送热装温度:≥400℃。c、板坯加热温度1180-1290℃。d、粗轧终止温度:1000℃-1200℃。e、精轧终止温度:780-950℃。f、带钢卷取温度:650-810℃。g、热轧卷板热处理温度:550-770℃。h、冷轧卷板热处理温度550-770℃。
[0036]
下面结合实施例详细说明本发明的具体实施方式,但本发明的具体实施方式不局限于下述的实施例。
[0037]
实施例一下面以本实施例详细说明本发明的冷轧钢板的技术特征。本实施例的超高强冷轧钢板的化学成分的质量百分比为:c:0.36si:1.62mn:0.94p:0.01s:0.0012al:0.041cr:1.20mo:0.53ni:0.24v:0.12n:0.0046o:9.0ppm;h:1.2ppm;余量为fe及不可避免的杂质元素。
[0038]
本实施例的冷轧板厚5.2mm,宽1930mm,长355m。
[0039]
其冷轧后退火态的屈服强度为448mpa,抗拉强度为693mpa,伸长率为26.5%,硬度hb 194/203/208,单面总脱碳层深度0.02mm。试样按照标准调质热处理后规定残余生产应力σr0.2为1486mpa,抗拉强度 σb,1816mpa ,断后延伸率为9% 。
[0040]
冷轧钢板在交货状态下进行室温180
°
弯曲,弯心直径为公称厚度2倍,冷弯结果如下,不裂,合格完好。
[0041]
钢板的显微组织中不允许有片状珠光体,如图1。
[0042]
满足超高强度冷轧钢板的性能需求。
[0043]
本实施例是在180吨顶底复吹转炉、2250mm热连轧机、2100mm单机架宽幅冷卷轧机组上进行的。它包括下述依次的步骤:ⅰ铁水预处理铁水预处理时扒渣干净,铁水预处理后,将铁水中的s脱到0.003%;ⅱ转炉冶炼将符合转炉冶炼的预处理铁水170吨、废钢([s]≤0.03%)30吨、镍铁加入转炉中。转炉出钢时,转炉出钢时,每吨钢水加入碳粉3kg,随炉装入钼铁60kg/吨、镍板0.29kg/吨。转炉出钢时,向钢水中加入碳粉4kg/吨钢,加入铝铁8kg/吨钢、高碳锰铁12kg/吨钢、硅锰合金18kg/吨钢、低p铬铁14kg/吨钢以及钒铁12kg/吨钢进行合金化。经铁水预处理、转炉冶炼后,钢水成分达到下述成分质量百分比,即可出钢。
[0044]
c:0.35si:1.51mn:0.94p:0.008s:0.003mo:0.53ni:0.24cr:0.62v:0.0.07al:0.045。余量为fe及不可避免的杂质元素。
[0045]
转炉终点温度:1680℃。
[0046]
余量为fe及不可避免的杂质元素。
[0047]
ⅲꢀ
lf精炼将经铁水预处理、转炉冶炼后,进入lf炉工序:lf加入定量脱硫剂石灰石每吨钢水加石灰6kg脱s,将s脱至不大于0.003%。之后,加入v铁、nb铁、cr铁进行合金化,每吨钢水加v铁10kg、cr铁13kg,微调成分。并以底吹氩流量100l/min弱搅时间8分钟。
[0048]
钢水成分的质量百分比达下述值即可:c:0.36si:1.62mn:0.94p:0.01s:0.0012mo:0.53ni:0.24cr:1.20v:0.12al:0.045。余量为fe及不可避免的杂质元素。
[0049]
余量为fe及不可避免的杂质元素。
[0050]
出站温度1590℃。
[0051]
ⅳꢀ
rh精炼在真空压强值4mbar状态下,循环20分钟。破真空后,喂入360m ca-si线,之后弱搅拌10分钟,氩气流量150nl/min,对钢水进行ca处理,进行夹杂物变性处理。
[0052]
钢水成分的重量百分比为:c:0.36si:1.62mn:0.94p:0.01s:0.0012mo:0.53ni:0.24cr:1.20v:0.12al:0.045。余量为fe及不可避免的杂质元素。
[0053]
ⅴ
板坯连铸将钢包中的钢水加入到中间包中,通过结晶器,连铸成板坯,连铸坯拉速1.1m/min,连铸浇注温度1506℃,铸坯轻压下:2.5mm,电磁搅拌:频率2.7hz。
[0054]
板坯规格:厚度230mm,宽度1930mm,长度8700mm;板坯数量:6块;
ⅵꢀ
板坯热送热装板坯热送热装:板坯热送热装温度430℃。
[0055]
ⅶꢀ
板坯加热将板坯在步进式加热炉中加热,加热时间为200min,加热温度1290
±
20℃。
[0056]
ⅷ
粗轧高压水除鳞将加热的板坯通过粗轧高压水除鳞去除钢坯表面生成的氧化铁皮。
[0057]
ⅸ
粗轧机组轧制将板坯在四辊可逆式粗轧机组往复轧制7道次,轧制成厚度40mm,宽度1930mm,长度49520mm的中间带坯,粗轧终轧温度:1050
±
20℃。
[0058]
ⅹ
精轧高压水除鳞精轧前,通过精轧高压水除鳞箱除去中间坯表面的二次氧化铁皮。
[0059]
ⅺ
精轧机组轧制将板坯在7机架精轧机组制成厚度8.2mm,宽1930mm,长225 m的钢带,精轧机组终轧温度:950
±
20℃。
[0060]
ⅻ
卷取用全液压移动式卷取机,在780
±
20℃温度下卷成钢卷。
[0061]
ⅹⅲ
热处理热处理温度:710
±
20℃,采用氮气保护。
[0062]
经质量和性能检验,本实施例的检验结果如下:其可达力学性能如下:其退火态的屈服强度为437mpa,抗拉强度为691mpa,伸长率为26.5%。
[0063]
ⅹⅳ
eps表面处理,eps生产速度设定3-10m/min;
ⅹⅴ
宽幅冷卷轧机压下率为36.5%;
ⅹⅵ
eps表面处理,eps生产速度设定3-10m/min;
ⅹⅶ
冷轧卷罩式炉采用全氢气氛保护,退火温度550-770℃;出厂前要贴包装标志并入库。
[0064]
其它实施例其它实施例的成分见表1 热轧钢带其它制造方法实施例的工艺参数与带钢性能见表2以上所述仅为本发明的具体实施例,但本发明所保护范围的结构特征并不限于此,任何本领域的技术人员在本发明的领域内,所作的变化或修饰皆涵盖在本发明的专利范围内。
再多了解一些
本文用于创业者技术爱好者查询,仅供学习研究,如用于商业用途,请联系技术所有人。