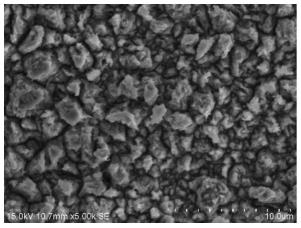
1.本发明涉及铜表面加工用化学品领域,尤其涉及一种用于印制线路板、ic载板和半导体构件等产品的铜表面的粗化微蚀液。
背景技术:
2.随着近年的电子仪器的小型化、轻量化、高功能化,对印刷线路板的铜布线的线宽和线距要求越来越小,导电图形的密度越来越大。在制造印制线路板生产的过程中,导体铜与光致抗蚀剂之间的附着力是影响印制线路板良率和质量的关键。
3.铜表面被抗蚀剂或焊锡抗蚀剂覆盖时,为了提高其结合力,需要对铜表面进行粗化。该粗化方法包括擦拭等物理粗化法和微蚀(又称蚀刻)等化学粗化法。其中硫酸/双氧水型中粗化微蚀液作为化学粗化法是环保型铜表面中粗化微蚀液之一,并已经在细线宽hdi板和封装载板等领域中生产应用。在目前各线路板厂所应用的工艺制程中,采用硫酸/双氧水体系的粗化液工作的同时,其含铜废液的处理一直困扰着生产厂家,若直接排放会对生态产生严重影响,且该含铜废液的后处理也会产生的大量的成本。因而含铜废液的资源利用成为了重要的发展方向,其业界目前主要采用的方法有废液的电解回收铜技术和冷却回收硫酸铜的技术,其中主要采用冷却回收硫酸铜技术。冷却回收硫酸铜的技术主要是通过提高微蚀液中硫酸的浓度(正常90g/l,提高使其大于90g/l),由于同离子效应的存在,可以降低硫酸铜在微蚀液中的溶解度,接着通过降温加速了硫酸铜晶体的析出,再通过固液分离技术使微蚀液和硫酸铜晶体进行分离;分离出的微蚀液回到微蚀槽继续工作,分离出的硫酸铜晶体收集起来以备它用。该技术不仅可以降低废液的排放,也可以降低生产成本,因此应用比较普遍。
4.然而目前在蚀刻中,随着做板量的增加,会使得槽液中铜含量越来越高,通常会达到至少40g/l,随后循环往复,稳定在40g/l上下,同时由于冷却回收硫酸铜需要提升蚀刻槽中的酸度,随着酸度的逐渐增加,当到200g/l(以硫酸计)时,在此条件下,覆铜板经过蚀刻后,会出现板面发白、粗化减弱、与抗蚀剂的表面结合力降低等问题。
技术实现要素:
5.本发明主要解决的技术问题是提供一种可回用的铜面粗化微蚀液,可在高酸度的条件下,依然保持较高的粗化程度,与抗蚀层较好的结合能力,硫酸/双氧水型中粗化微蚀液是环保型铜表面中粗化微蚀液之一,并已经在细线宽hdi板和封装载板领域中生产应用。
6.为解决上述技术问题,本发明采用的一个技术方案是:本发明提供了一种可回用的铜面粗化微蚀液,包括双氧水、硫酸、双氧水稳定剂、润湿剂、粗化添加剂、络合剂和去离子水,各组分的浓度如下:
7.双氧水的浓度范围为5-35g/l;
8.硫酸的浓度范围为180-250g/l;
9.双氧水稳定剂的浓度范围为0.01-5g/l;
10.润湿剂的浓度范围为0.1-10g/l;
11.粗化添加剂的浓度范围为0.5-10g/l;
12.络合剂的浓度范围为0.2-20g/l;
13.其余为去离子水。
14.进一步地说,双氧水稳定剂选自对羟基苯磺酸钠、硅酸镁、硅酸钠和聚丙烯酰胺中的至少一种。
15.进一步地说,润湿剂选自peg4000(聚乙二醇4000)、十二烷基硫酸钠和np-10(壬基酚聚氧乙烯醚的一种)中的至少一种。
16.进一步地说,粗化添加剂选自苯并三氮唑、5-氨基四唑、5-苯基四唑和苯并咪唑中的至少一种。
17.进一步地说,络合剂选自二乙烯三胺、乙二胺四乙酸二钠、葡萄糖酸钠和海藻酸钠中的至少一种。
18.本发明还提供了一种所述的可回用的铜面粗化微蚀液的使用方法,包括如下步骤:
19.步骤一、通过机械方式去除铜板表面的杂质(包括氧化物和手指印,但不限于此);
20.步骤二、排放缸中用去离子水清洗15-45分钟,再用硫酸清洗15-45分钟,后用去离子水冲洗;
21.步骤三、制备微蚀液;
22.步骤四、用步骤三制备的微蚀液对铜板进行蚀刻处理;
23.步骤五、将蚀刻后的铜板用硫酸清洗后再用去离子水冲洗干净。
24.进一步地说,还包括步骤六、做切片进行电镜检测和粗糙度检测。对蚀刻后的产品抽样检测。
25.进一步地说,步骤三具体为:先加入部分去离子水,再加入硫酸、双氧水、双氧水稳定剂、润湿剂、粗化添加剂和络合剂,搅拌均匀,再加入剩余的去离子水。
26.进一步地说,步骤四采用喷淋的方式对铜板进行蚀刻处理,处理时间为45-75s,喷淋压力为10-30psi。
27.较佳的是,喷淋处理时间为60s,喷淋压力为20psi。
28.进一步地说,步骤五为:将蚀刻后的铜板用5%硫酸清洗后再用去离子水冲洗干净。
29.本发明的有益效果是:
30.本发明的粗化微蚀液可在高酸度的条件下,依然保持较高的粗化程度,与抗蚀层较好的结合能力,硫酸/双氧水型中粗化微蚀液是环保型铜表面中粗化微蚀液之一,并已经在细线宽hdi板和封装载板领域中生产应用,它在使用过程中具有以下优点:
31.(1)蚀铜量小,清洗效果好:由于镀铜成本较高,因此蚀铜量小,可以降低镀铜成本,并降低环境污染风险;
32.(2)可以与硫酸铜回收机配合使用:铜回收是目前印制线路板清洁生产的重要组成部分,本发明充分考虑了这一因素,该发明产品可以与铜回收机配合使用,循环使用的硫酸/双氧水粗化液仅需添加在过程中消耗的硫酸和双氧水及少量添加剂,降低了使用成本,同时降低了环境风险;
33.(3)工艺宽容度高,操作简单:使用时,硫酸和双氧水的控制范围较宽,因此可以采用自动添加系统,操作简便,减少人力。
34.(4)应用成本低,仅为有机酸型超粗化液应用成本的三分之一。
35.上述说明仅是本发明技术方案的概述,为了能够更清楚了解本发明的技术手段,并可依照说明书的内容予以实施,以下以本发明的较佳实施例并配合附图详细说明如后。
附图说明
36.图1是本发明的实施例的sem图;
37.图2是本发明的对比例的sem图。
具体实施方式
38.以下通过特定的具体实施例说明本发明的具体实施方式,本领域技术人员可由本说明书所揭示的内容轻易地了解本发明的优点及功效。本发明也可以其它不同的方式予以实施,即,在不背离本发明所揭示的范畴下,能予不同的修饰与改变。
39.实施例:一种可回用的铜面粗化微蚀液,包括双氧水、硫酸、双氧水稳定剂、润湿剂、粗化添加剂、络合剂和去离子水,各组分的浓度如下:
40.双氧水的浓度范围为5-35g/l;
41.硫酸的浓度范围为180-250g/l;
42.双氧水稳定剂的浓度范围为0.01-5g/l;
43.润湿剂的浓度范围为0.1-10g/l;
44.粗化添加剂的浓度范围为0.5-10g/l;
45.络合剂的浓度范围为0.2-20g/l;
46.其余为去离子水。
47.双氧水稳定剂选自对羟基苯磺酸钠、硅酸镁、硅酸钠和聚丙烯酰胺中的至少一种。
48.润湿剂选自peg4000(聚乙二醇4000)、十二烷基硫酸钠和np-10(壬基酚聚氧乙烯醚的一种)中的至少一种。
49.粗化添加剂选自苯并三氮唑、5-氨基四唑、5-苯基四唑和苯并咪唑中的至少一种。
50.络合剂选自二乙烯三胺、乙二胺四乙酸二钠、葡萄糖酸钠和海藻酸钠中的至少一种。
51.本发明中高酸度环境是指硫酸的浓度范围可达到180-250g/l。
52.本发明的铜面粗化微蚀液回收时铜的浓度稳在40g/l左右,比如35-45g/l;铜的回收效率高。
53.以下为具体的实施例:
54.实施例1:一种可回用的铜面粗化微蚀液,其中,双氧水的浓度范围为15g/l;硫酸的浓度范围为200g/l;硅酸钠的浓度范围为1.0g/l;peg4000的浓度范围为1.0g/l;5-氨基四唑的浓度范围为2g/l;二乙烯三胺的浓度范围为3g/l;其余为去离子水。
55.实施例2:一种可回用的铜面粗化微蚀液,其中,双氧水的浓度范围为5g/l;硫酸的浓度范围为250g/l;硅酸镁的浓度范围为0.01g/l;peg4000的浓度范围为2g/l;5-氨基四唑的浓度范围为0.5g/l;二乙烯三胺的浓度范围为5g/l;其余为去离子水。
56.实施例3:一种可回用的铜面粗化微蚀液,其中,双氧水的浓度范围为35g/l;硫酸的浓度范围为180g/l;聚丙烯酰胺的浓度范围为5g/l;十二烷基硫酸钠的浓度范围为0.1g/l;苯并三氮唑的浓度范围为5g/l;乙二胺四乙酸二钠的浓度范围为0.2g/l;其余为去离子水。
57.实施例4:一种可回用的铜面粗化微蚀液,其中,双氧水的浓度范围为10g/l;硫酸的浓度范围为200g/l;对羟基苯磺酸钠的浓度范围为0.5g/l;十二烷基硫酸钠的浓度范围为3g/l;苯并三氮唑的浓度范围为10g/l;乙二胺四乙酸二钠的浓度范围为20g/l;其余为去离子水。
58.实施例5:一种可回用的铜面粗化微蚀液,其中,双氧水的浓度范围为20g/l;硫酸的浓度范围为210g/l;对羟基苯磺酸钠的浓度范围为2g/l;np-10浓度范围为5g/l;5-苯基四唑的浓度范围为6g/l;葡萄糖酸钠的浓度范围为15g/l;其余为去离子水。
59.实施例6:一种可回用的铜面粗化微蚀液,其中,双氧水的浓度范围为22g/l;硫酸的浓度范围为220g/l;硅酸镁的浓度范围为2.5g/l;np-10的浓度范围为10g/l;5-苯基四唑的浓度范围为7g/l;葡萄糖酸钠的浓度范围为17g/l;其余为去离子水。
60.实施例7:一种可回用的铜面粗化微蚀液,其中,双氧水的浓度范围为28g/l;硫酸的浓度范围为230g/l;硅酸钠的浓度范围为3g/l;十二烷基硫酸钠的浓度范围为4g/l;苯并咪唑的浓度范围为8g/l;海藻酸钠的浓度范围为18g/l;其余为去离子水。
61.实施例8:一种可回用的铜面粗化微蚀液,其中,双氧水的浓度范围为32g/l;硫酸的浓度范围为240g/l;聚丙烯酰胺的浓度范围为3.5g/l;peg4000的浓度范围为6g/l;苯并咪唑的浓度范围为9g/l;海藻酸钠的浓度范围为19g/l;其余为去离子水。
62.以下为具体的对比例;
63.对比例1:作为对比的硫酸/双氧水型蚀刻液,其主要成分为硫酸200g/l,双氧水15g/l,5-氨基四唑0.2g/l,氯离子0.5ppm,剩余用去离子水补齐。
64.对比例2:作为对比的硫酸/双氧水型蚀刻液,其主要成分为硫酸180g/l,双氧水20g/l,5-氨基四唑0.4g/l,氯离子0.8ppm,剩余用去离子水补齐。
65.实施例1到8的一种所述的可回用的铜面粗化微蚀液的使用方法,包括如下步骤:
66.步骤一、通过机械方式去除铜板表面的杂质(包括氧化物和手指印,但不限于此);
67.步骤二、排放缸中用去离子水清洗15-45分钟,再用硫酸清洗15-45分钟,后用去离子水冲洗;
68.步骤三、制备微蚀液:先加入部分去离子水,再加入硫酸、双氧水、双氧水稳定剂、润湿剂、粗化添加剂和络合剂,搅拌均匀,再加入剩余的去离子水定容到一定体积,比如1l;
69.步骤四、用步骤三制备的微蚀液对铜板进行蚀刻处理;
70.比如:采用喷淋的方式对铜板进行蚀刻处理,处理时间为45-75s,喷淋压力为10-30psi;
71.较佳的是,喷淋处理时间为60s,喷淋压力为20psi。
72.步骤五、将蚀刻后的铜板用5%硫酸清洗后再用去离子水冲洗干净。
73.进一步地说,还可以包括步骤六、做切片进行电镜检测和粗糙度检测,对蚀刻后的产品抽样检测。
74.对比例1和2除了上述步骤三不同,其它步骤一样对铜板进行蚀刻。
75.实施例1到实施例8的蚀刻后的表面(sem)如图1所示,图1是选用的实施例1对应的sem图,粗糙度范围为0.4-0.6微米,且主要集中0.5微米左右,粗化均匀,蚀刻量适中;对比例1和对比例2的蚀刻后的表面(sem)如图2所示,图2是选用的对比例1对应的sem图,粗糙度范围为0.23-1.0微米,粗糙度范围跨度较大,粗化不均匀,蚀刻量较小,粗糙度跟最后的结合力十分相关,通过上述对比,可以看出,本实施例的微蚀液能够提供高的附着力和均匀的粗化效果。
76.以上所述仅为本发明的实施例,并非因此限制本发明的专利范围,凡是利用本发明说明书及附图内容所作的等效结构,或直接或间接运用在其他相关的技术领域,均同理包括在本发明的专利保护范围内。
再多了解一些
本文用于创业者技术爱好者查询,仅供学习研究,如用于商业用途,请联系技术所有人。