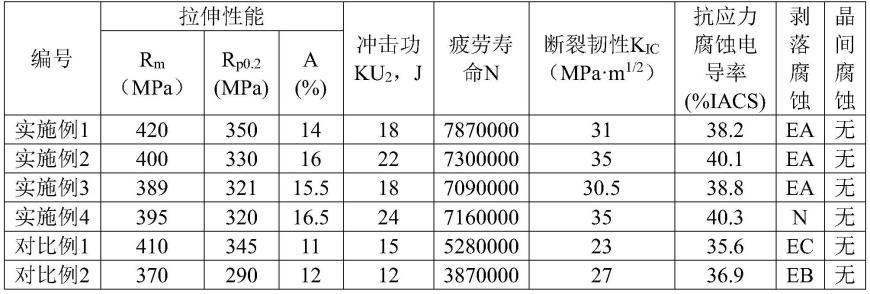
一种中强超韧耐蚀al-zn-mg系铝合金及其制备方法
技术领域
1.本发明属于铝合金技术领域,具体涉及一种中强超韧耐蚀al-zn-mg系铝合金及其制备方法。
背景技术:
2.随着现代铝制特种车辆和高速列车技术不断升级换代,车体各种结构支座和法兰等大型锻件及车体底架等大型材对铝合金新材料的减重性、抗震性、耐蚀性、可焊性及服役稳定性等方面提出越来越严苛的要求。研发一种中强超韧、疲劳性能、冲击性能、耐蚀性、可焊性、成形性及在线淬火性都好的车辆结构大型锻件和大型材用铝合金至关重要。
3.我国现有特种车辆车体各种焊接结构的支座、法兰等大型锻件采用具有自主知识产权的7a52铝合金加工制造。在各种复杂的使用工况服役过程中,多种7a52锻件发生了由强度、韧性、耐蚀性、焊接性的不匹配造成的大面积开裂失效的问题。而我国高速列车车体、框架、底架大型材采用美国研发的7005铝合金加工制造,一方面缺乏自主知识产权,另一方面7005铝合金需要进一步纯净化和去合金化以提高其断裂韧性和疲劳性能,因此无法将7005铝合金直接应用到特种车辆的锻件或型材中。
4.因此,需要对7a52、7005铝合金进行改进,适用于特种车辆车体结构锻件和高速列车车体、框架、底架等。
技术实现要素:
5.本发明所要解决的第一个技术问题是提供一种在保证一定强度的同时提高其断裂韧性和疲劳性能的中强超韧耐蚀al-zn-mg系铝合金。
6.本发明所要解决的第二个技术问题是提供一种中强超韧耐蚀al-zn-mg系铝合金的制备方法。
7.本发明解决第一个技术问题所采用的技术方案为:一种中强超韧耐蚀al-zn-mg系铝合金,其特征在于:该铝合金的质量百分比组成为zn:3.5~6wt%,mg:0.9~2.3wt%,cu:0.01~0.1wt%,mn:0.1~0.5wt%,cr:0.01~0.1wt%,ti:0.01~0.05wt%,zr:0.05~0.2wt%,v:0.05~0.09wt%,th:0.01~0.09wt%,er:0.08~0.15wt%,fe≤0.20wt%,si≤0.15wt%,其余为al和不可避免的杂质。
8.本发明解决第二个技术问题所采用的技术方案为:一种中强超韧耐蚀al-zn-mg系铝合金的制备方法,其特征在于:包括以下制备步骤:
9.1)熔铸:按照所需成分进行配料,熔炼温度为720℃~780℃,浇注获得铸锭;
10.2)均匀化退火:铸锭在450~485℃下保温12~30h;
11.3)热加工:采用热轧、热锻或者热挤压将铸锭加工成所需成品规格的热加工件;
12.4)固溶处理或者在线淬火:采用热轧、热锻将铸锭加工成所需成品规格的热加工件时,采用固溶处理,固溶处理工艺为450~485℃保温0.5~2h,常温水冷;采用热挤压将铸锭加工成所需成品规格的热加工件时,在线风淬;
13.5)双级时效工艺:
14.采用a制度:一级时效处理工艺为将热加工件在110~120℃下保温6~24h,二级时效处理工艺为将热加工件继续升温,在150~160℃下保温8~18h;
15.或者采用b制度:一级时效处理工艺为将热加工件在115~125℃下保温4~10h,二级时效处理工艺为将热加工件继续升温,在165~175℃下保温6~12h。
16.作为优选,所述步骤3)中,采用热锻将铸锭加工成所需成品规格的热锻件,热锻工艺为:铸锭加热温度400~450℃,采用自由锻和/或模锻,终锻温度350℃以上。
17.作为优选,所述步骤3)中,采用热轧将铸锭加工成所需成品规格的热轧板,热轧工艺为:热轧温度400~450℃,总加工率≥75%。
18.作为优选,所述步骤4)与步骤5)之间设置有去应力拉伸矫直,将热轧板沿轧制方向矫直拉伸1.0%~1.7%。
19.作为优选,所述步骤3)中,采用热挤压将铸锭加工成所需成品规格的热挤压型材,热挤压工艺为:铸锭加热温度400~450℃,挤压模具温度400~450℃,挤压温度400~450℃,挤压速度1~5m/min。
20.与现有技术相比,本发明的优点在于:
21.1)本发明涉及al-zn-mg系铝合金,解决本技术技术问题的关键技术手段是去合金化和纯净化,即添加少量cu、mn、cr、zr、ti、v、th、er等元素合金化。增大zn/mg比提升塑韧性,严格控制cu含量改善7xxx系中高强铝合金焊接性能,降低mn、cr、ti、fe、si等元素含量提升合金纯净度,同时,通过少量mn、cr、zr、ti、v、th、er等合金化降低淬火敏感性,提升焊接性能以及减少铸造热裂敏感性等,同时提升挤压加工性能和耐蚀性能。技术效果一:适量的zr与v元素复合作用使得本发明合金的疲劳寿命高于7a52和7005等普通材料。技术效果二:适量的th与er元素复合作用同时提升本发明合金强度、韧性及焊接性能,主因是th与er元素不形成金属间化合物,避免形成alther粗大相。技术效果三:严格控制v、cr、er和ti元素的含量避免形成粗大相牺牲本发明合金的塑韧性和疲劳性能。
22.2)通过步骤4)与步骤5)配合,实现本发明al-zn-mg系合金拉伸强度:rm≥380mpa,屈服强度:rp0.2≥315mpa,延伸率a≥8%;冲击功:ku2≥15j;疲劳极限强度≥180mpa,应用工况疲劳寿命高于7a52和7005;断裂韧性:k
ic
≥30mpa
·m1/2
;抗应力腐蚀电导率≥38%iacs;剥落腐蚀:剥蚀等级优于ea级(含ea级);晶间腐蚀:无晶间腐蚀。
23.本发明al-zn-mg系合金在应用上有着满足特种车辆技术要求的特性,即中强超韧、断裂韧性高、耐冲击性好、耐蚀性突出,成形性和在线淬火性及可焊性良好,适用于既要有较高强度又要有高断裂韧性和疲劳性能的锻件或者型材的加工。
具体实施方式
24.以下结合实施例对本发明作进一步详细描述。
25.实施例1:中强超韧耐蚀al-zn-mg系铝合金制备大型热锻件
26.该铝合金的质量百分比组成为zn:5.0wt%,mg:1.9wt%,cu:0.04wt%,mn:0.15wt%,cr:0.05wt%,zr:0.13wt%,ti:0.04wt%,v:0.09wt%,th:0.05wt%,er:0.10wt%,fe≤0.15,si≤0.12,其余为al。
27.制备步骤如下:
28.1)熔铸:按照所需成分进行配料,熔炼温度为750℃,浇注获得铸锭,规格:300mm
×
500mm
×
1000mm;
29.2)均匀化退火:铸锭在475℃下保温20h;
30.3)热锻:铸锭加热温度430℃,采用自由锻 模锻,终锻温度369℃,将铸锭加工成所需成品规格的热锻件,规格:700mm
×
600mm
×
200mm;
31.4)固溶处理:固溶处理工艺为470℃保温1h,常温水冷;
32.5)双级时效工艺:一级时效处理工艺为将热加工件在120℃下保温6h,二级时效处理工艺为将热加工件继续升温,在160℃下保温12h。
33.实施例2:中强超韧耐蚀al-zn-mg系铝合金制备大型挤压型材
34.该铝合金的质量百分比组成为zn:4.2wt%,mg:1.1wt%,cu:0.05wt%,mn:0.35wt%,cr:0.09wt%,zr:0.18wt%,ti:0.03wt%,v:0.05wt%,th:0.02wt%,er:0.15wt%,fe≤0.20,si≤0.15,其余为al。
35.制备步骤如下:
36.1)熔铸:按照所需成分进行配料,熔炼温度为760℃,浇注获得铸锭,规格:φ300mm
×
500mm;
37.2)均匀化退火:铸锭在470℃下保温24h;
38.3)热挤压:铸锭加热温度430℃,挤压模具温度450℃,挤压温度430℃,挤压速度1m/min,将铸锭加工成所需成品规格的热挤压型材,壁厚5mm~10mm。
39.4)固溶处理:在线风淬;
40.5)双级时效工艺:一级时效处理工艺为将热加工件在120℃下保温6h,二级时效处理工艺为将热加工件继续升温,在170℃下保温10h。
41.实施例3:中强超韧耐蚀al-zn-mg系铝合金制备大型挤压型材
42.该铝合金的质量百分比组成为zn:3.5wt%,mg:0.9wt%,cu:0.10wt%,mn:0.50wt%,cr:0.10wt%,ti:0.04wt%,zr:0.20wt%,v:0.09wt%,th:0.09wt%,er:0.08wt%,fe≤0.20wt%,si≤0.15wt%,其余为al。
43.制备步骤如下:
44.1)熔铸:按照所需成分进行配料,熔炼温度为750℃,浇注获得铸锭,规格:φ300mm
×
500mm;
45.2)均匀化退火:铸锭在460℃下保温24h;
46.3)热挤压:铸锭加热温度450℃,挤压模具温度450℃,挤压温度440℃,挤压速度5m/min,将铸锭加工成所需成品规格的热挤压型材,壁厚5mm~10mm。
47.4)固溶处理:在线风淬;
48.5)双级时效工艺:一级时效处理工艺为将热加工件在110℃下保温6h,二级时效处理工艺为将热加工件继续升温,在150℃下保温15h。
49.实施例4:中强超韧耐蚀al-zn-mg系铝合金制备大型热轧板
50.该铝合金的质量百分比组成为zn:5.9wt%,mg:2.2wt%,cu:0.09wt%,mn:0.50wt%,cr:0.02wt%,zr:0.08wt%,ti:0.02wt%,v:0.05wt%,th:0.01wt%,er:0.15wt%,fe≤0.20,si≤0.15,其余为al。
51.制备步骤如下:
52.1)熔铸:按照所需成分进行配料,熔炼温度为730℃,浇注获得铸锭,规格:300mm
×
600mm
×
1000mm;
53.2)均匀化退火:铸锭在485℃下保温18h;
54.3)热轧:热轧温度410℃,总加工率80%,将铸锭加工成所需成品规格的热轧板,规格:10mm
×
1000mm
×
15000mm。
55.4)固溶处理:固溶处理工艺为475℃保温1h,常温水冷;
56.5)去应力拉伸矫直:将淬火后的板材沿轧制方向矫直拉伸1.5%;
57.6)双级时效工艺:一级时效处理工艺为将热加工件在120℃下保温6h,二级时效处理工艺为将热加工件继续升温,在170℃下保温10h。
58.对比例1为7a52,7a52合金的化学成分(质量百分比%)是:zn4.80,mg2.54,cu0.15,mn0.40,cr0.18,zr0.08,ti0.11,fe0.22,si0.06,单个杂质含量≤0.05,杂质总含量≤0.15,其余为al,采用与实施例1相同的制备工艺制备大型锻件毛坯,规格:700mm
×
600mm
×
200mm。
59.对比例2为7005,7005合金的化学成分(质量百分比%)是:zn4.85,mg1.65,cu0.09,mn0.60,cr0.18,zr0.13,ti0.06,fe0.33,si0.20,单个杂质含量≤0.05,杂质总含量≤0.15,其余为al,采用与实施例1相同的制备工艺制备大型锻件毛坯,规格:700mm
×
600mm
×
200mm。
60.对实施例和对比例进行如下性能检测:
61.依据国标gb/t 16865-2013进行拉伸试验用试样加工和检测测试,依据国标gb/t229-2020进行ku2冲击功用试样加工和检测测试,依据国标gb/t 3075-2008进行200mpa加载力的疲劳寿命测试用试样加工和检测测试,依据国标gb/t 4161-2007进行断裂韧性kic试验用试样加工和检测测试。依据国标gb/t 351-2019进行电导率用试样加工和检测测试,依据国标gb/t 22639-2008进行剥落腐蚀试验用试样加工和检测测试,依据国标gb/t 7998-2005进行晶间腐蚀试验用试样加工和检测测试。以上测试结果见表1。
62.通过上述实施例,证明本发明al-zn-mg系合金的拉伸强度:rm≥380mpa,屈服强度:rp0.2≥315mpa,延伸率a≥8%;冲击功:ku2≥15j;在180mpa加载下,应用工况疲劳寿命高于7a52和7005;断裂韧性:k
ic
≥30mpa
·m1/2
;抗应力腐蚀电导率≥38%iacs;剥落腐蚀:剥蚀等级优于ea级(含ea级);晶间腐蚀:无晶间腐蚀。
63.表1本发明实施例和对比例的性能
64.
再多了解一些
本文用于创业者技术爱好者查询,仅供学习研究,如用于商业用途,请联系技术所有人。