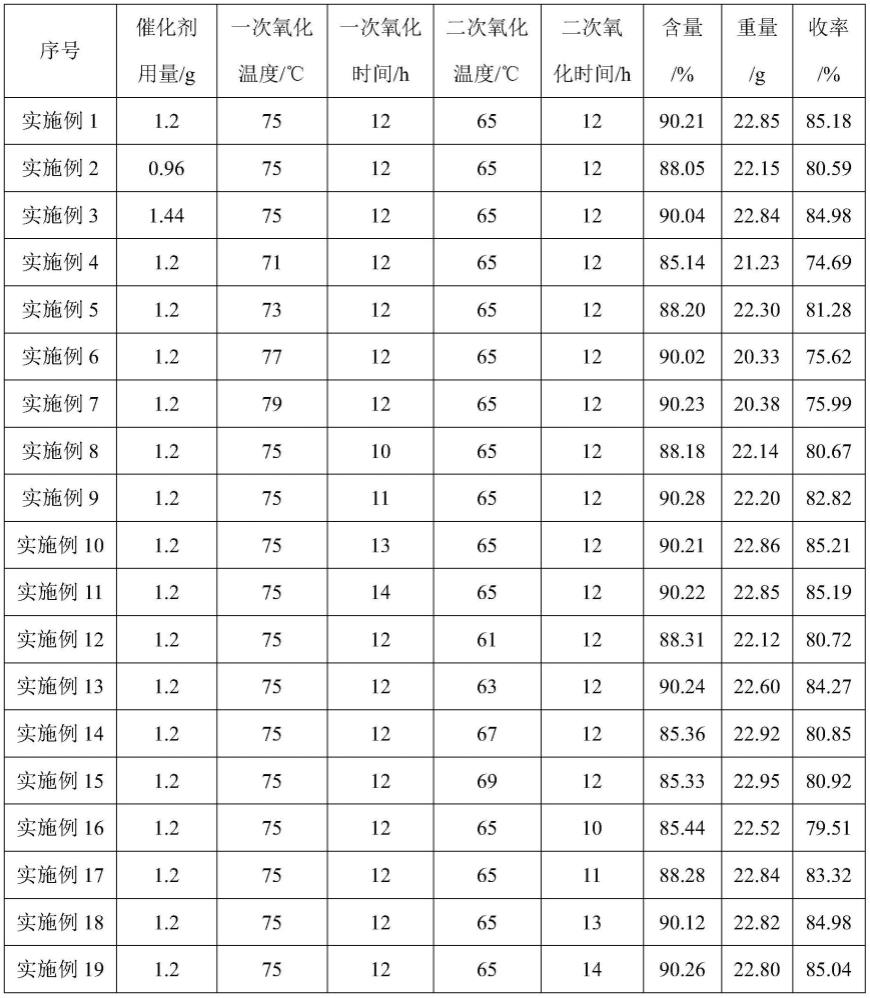
1.本发明涉及除草剂技术领域,具体涉及两步氧化制备二氯喹啉酸的方法。
背景技术:
2.二氯喹啉酸又名3,7-二氯-8-喹啉羧酸,是防治稻田稗草的特效选择性除草剂,属激素型喹啉酸类除草剂,其结构式如下:
[0003][0004]
该除草剂具有除草效果好,对作物安全,施药时间不受杂草生长阶段限制等优点,被市场广泛认可。
[0005]
目前二氯喹啉酸的合成工艺为:以3-氯-2-甲基苯胺和丙三醇为主要原料,经环合、氯化、氧化水解三步合成工艺路线。具体步骤为在硫酸介质中,经催化剂催化,3-氯-2-甲基苯胺与丙三醇进行环合反应,得到7-氯-8-甲基喹啉;得到的7-氯-8-甲基喹啉通过石油醚重结晶后,在邻二氯苯溶液中,经引发剂引发,通氯气氯化后,得到3,7-二氯-8-氯甲基喹啉的邻二氯苯溶液,脱除邻二氯苯溶剂后,加入硫酸溶液,得到氧化配置液,经硝酸氧化水解得到3,7-二氯-8-喹啉羧酸。
[0006]
由于现有的二氯喹啉酸氧化水解工艺,采用在硫酸介质中,通过滴加硝酸来氧化3,7-二氯-8-氯甲基喹啉,使用硝酸作为氧化剂时,投入量很大,每吨二氯喹啉酸产品需要消耗98%的浓硝酸1.5吨,而且使用过后的混合废酸无法回收套用,从而产生大量的废酸、废水。三废处理的成本较高,不利于产品的清洁生产,混合废酸的处理已成为该产品发展壮大的瓶颈,另外使用硝酸作为氧化剂,产品中会产生硝基物,影响产品品质。
[0007]
因此,急需寻找一种绿色环保、高收率、操作简便的氧化方法,在氧化水解工序中避免大量废酸和废水的产生,对上述除草剂的工业化生产具有重要的意义。
技术实现要素:
[0008]
本发明提出采用两步氧化制备二氯喹啉酸的方法,解决了相关技术中在氧化水解合成二氯喹啉酸工艺中产生大量的废酸、废水和二氯喹啉酸收率低的问题,避免了氧化水解合成工艺中大量废酸和废水的产生,并能够将反应溶剂回收套用。
[0009]
本发明的技术方案如下:
[0010]
两步氧化制备二氯喹啉酸的方法,包括以下步骤:
[0011]
s1.将3-氯-2-甲基苯胺与丙三醇进行环合反应,得到7-氯-8-甲基喹啉;
[0012]
s2.将7-氯-8-甲基喹啉氯化,得到3,7-二氯-8-氯甲基喹啉,与硫酸混合形成氧化物配置液;
[0013]
s3.将s2所述氧化物配置液催化氧化;
[0014]
s4.将s3得到的生成物水解后,固液分离,将固相溶解在溶剂中,滴加氧化剂,氧化
得到二氯喹啉酸。
[0015]
作为进一步的技术方案,所述s1中环合反应具体为:将3-氯-2-甲基苯胺、丙三醇和硫酸加入反应器中,进行环合反应。
[0016]
作为进一步的技术方案,所述3-氯-2-甲基苯胺与丙三醇的摩尔比1:(1.1~1.2)。
[0017]
作为进一步的技术方案,所述3-氯-2-甲基苯胺与丙三醇的摩尔比1:1.14。
[0018]
作为进一步的技术方案,所述的7-氯-8-甲基喹啉采用石油醚进行重结晶。
[0019]
作为进一步的技术方案,所述s2中氯化具体为:以偶氮二异丁腈为引发剂,邻二氯苯为溶剂,通入氯气进行氯化反应,反应后脱除溶剂,得到3,7-二氯-8-氯甲基喹啉。
[0020]
作为进一步的技术方案,所述s2中硫酸的质量为3,7-二氯-8-氯甲基喹啉质量的4~5倍。
[0021]
作为进一步的技术方案,所述s2中硫酸的质量为3,7-二氯-8-氯甲基喹啉质量的4.17倍。
[0022]
作为进一步的技术方案,所述s3中催化氧化具体为:将氧化物配置液与五水硫酸铜混合,滴加双氧水,进行催化氧化反应。
[0023]
作为进一步的技术方案,所述五水硫酸铜的质量为3,7-二氯-8-氯甲基喹啉质量的5%。
[0024]
作为进一步的技术方案,所述双氧水的质量为3,7-二氯-8-氯甲基喹啉质量的1.5~1.6倍,滴加时间为60min,反应温度为75
±
1℃,反应时间12h。
[0025]
作为进一步的技术方案,所述双氧水的质量为3,7-二氯-8-氯甲基喹啉质量的1.5625倍。
[0026]
作为进一步的技术方案,所述s4中溶剂的质量为固相质量的4倍,氧化剂的质量为固相质量的3.57倍。
[0027]
作为进一步的技术方案,所述溶剂为叔丁醇。
[0028]
作为进一步的技术方案,所述s4中氧化剂为10%亚氯酸钠溶液,氧化温度65
±
1℃,氧化时间12h。
[0029]
本发明的工作原理及有益效果为:
[0030]
通过本发明两步氧化法制备二氯喹啉酸含量达到了90%,收率达到了85%,同时避免了氧化水解阶段大量废酸和废水的产生,并且反应液溶剂能够回收套用,大大降低了三废处理成本。此外,本发明所采用的氧化反应温度低,以复合氧化剂分步氧化,洁净环保。
具体实施方式
[0031]
下面将结合本发明实施例,对本发明实施例中的技术方案进行清楚、完整地描述,显然,所描述的实施例仅仅是本发明一部分实施例,而不是全部的实施例。基于本发明中的实施例,本领域普通技术人员在没有作出创造性劳动前提下所获得的所有其他实施例,都涉及本发明保护的范围。
[0032]
实验组一
[0033]
s1.将14.15g3-氯-2-甲基苯胺、10.50g丙三醇、18.00g 80%硫酸,加入反应容器中,进行环合反应,得到7-氯-8-甲基喹啉;
[0034]
s2.将s1得到的7-氯-8-甲基喹啉用石油醚进行重结晶后与100.00g邻二氯苯、
0.20g偶氮二异丁腈混合,并通入20.00g氯气氯化,反应结束后脱除溶剂,得到24.00g3,7-二氯-8-氯甲基喹啉,将其溶解85.00g叔丁醇中,形成配置液;
[0035]
s3.取该配置液投入三口烧瓶中,采用磁力搅拌,安装有0-100℃水银温度计,冷凝器,在300rpm的搅拌转速下,滴加75.00g10%亚氯酸钠溶液,控制滴加时间60min,反应温度60℃,滴加结束后保温,计时氧化至二氯喹啉酸含量至90%所需时间。
[0036]
在此体系下氧化10天反应,无二氯喹啉酸的生成。
[0037]
实验组二
[0038]
s1.将14.15g3-氯-2-甲基苯胺、10.50g丙三醇、18.00g80%硫酸,加入反应容器中,进行缩合反应,得到7-氯-8-甲基喹啉;
[0039]
s2.将s1得到的7-氯-8-甲基喹啉用石油醚进行重结晶后与100.00g邻二氯苯、0.20g偶氮二异丁腈混合,并通入20.00g氯气氯化,反应结束后脱除溶剂,得到24.00g3,7-二氯-8-氯甲基喹啉,加入100.00g60%硫酸形成氧化物配置液;
[0040]
s3.取该配置液投入三口烧瓶中,采用磁力搅拌,安装有0-100℃水银温度计,冷凝器,在300rpm的搅拌转速下,滴加37.50g的27%双氧水,控制滴加时间60min,在该反应条件下,进行六组不同反应温度的平行实验,控制平行实验的反应温度分别为40℃、50℃、60℃、70℃、75℃、80℃,滴加结束后保温,根据不同的反应温度记录氧化至二氯喹啉酸含量至90%所需时间,结果记录在表1中。
[0041]
表1双氧水在不同反应温度下氧化至二氯喹啉酸含量到90%所需时间
[0042]
反应温度/℃405060707580氧化时间/h12010096807272
[0043]
只采用双氧水氧化反应时间较长,不利于生产推广。同时综合所有反应温度,75℃时氧化时间较短。
[0044]
实验组三
[0045]
s1.将14.15g3-氯-2-甲基苯胺、10.50g丙三醇、18.00g80%硫酸,加入反应容器中,进行缩合反应,得到7-氯-8-甲基喹啉;
[0046]
s2.将s1得到的7-氯-8-甲基喹啉用石油醚进行重结晶后与100.00g邻二氯苯、0.20g偶氮二异丁腈混合,并通入20.00g氯气氯化,反应结束后脱除溶剂,得到24.00g3,7-二氯-8-氯甲基喹啉,加入100.00g60%硫酸形成氧化物配置液;
[0047]
s3.取该配置液投入三口烧瓶中,采用磁力搅拌,安装有0-100℃水银温度计,冷凝器,在300rpm的搅拌转速下,进行三组平行实验,在平行实验中分别加入1.20g不同种类的催化剂,滴加37.50g的27%双氧水,控制滴加时间60min,反应温度75℃,滴加结束后保温,根据不同种类的催化剂计时氧化至二氯喹啉酸含量至90%所需时间,结果记录在表2中。
[0048]
表2双氧水在不同种类催化剂下氧化至二氯喹啉酸含量到90%所需时间
[0049]
催化剂种类氯化铁五水硫酸铜环烷酸钴氧化时间/h604570
[0050]
只采用双氧水氧化,在加入催化剂后,反应时间有明显的缩短,但氧化时间仍较长,不利于生产推广。通过对比氯化铁、五水硫酸铜、环烷酸钴三种催化剂,发现五水硫酸铜的催化效率明显高于其他两种,更适用于制备二氯喹啉酸。
[0051]
实验组四
[0052]
s1.将14.15g3-氯-2-甲基苯胺、10.50g丙三醇、18.00g80%硫酸,加入反应容器中,进行缩合反应,得到7-氯-8-甲基喹啉;
[0053]
s2.将s1得到的7-氯-8-甲基喹啉用石油醚进行重结晶后与100.00g邻二氯苯、0.20g偶氮二异丁腈混合,并通入20.00g氯气氯化,反应结束后脱除溶剂,得到24.00g3,7-二氯-8-氯甲基喹啉,加入100.00g60%硫酸形成氧化物配置液;
[0054]
s3.取该配置液投入三口烧瓶中,采用磁力搅拌,安装有0-100℃水银温度计,冷凝器,在300rpm的搅拌转速下,加入1.20g五水硫酸铜,滴加37.50g的27%双氧水,控制滴加时间60min,反应温度75℃,滴加结束后保温12小时;
[0055]
s4.将氧化产物水解,经固液分离,得到21.00g固相。将固相溶解在85.00g叔丁醇中,缓慢滴加75.00g的10%亚氯酸钠溶液,在该反应条件下,进行四组不同反应温度的平行实验,控制平行实验的反应温度分别为50℃、60℃、65℃、70℃,记录氧化至二氯喹啉酸含量至90%所需时间(滴加完毕后开始计时),结果记录在表3中。
[0056]
表3分步氧化亚氯酸钠在不同反应温度下氧化至二氯喹啉酸含量到90%所需时间
[0057]
反应温度/℃50606570氧化时间/h18161212
[0058]
在保证氧化时间短的反应条件下,选择较低的反应温度,当温度在65℃时,氧化时间较短,更利于生产推广。
[0059]
实施例1
[0060]
s1.将14.15g3-氯-2-甲基苯胺、10.50g丙三醇、18.00g80%硫酸,加入反应容器中,进行缩合反应,得到7-氯-8-甲基喹啉;
[0061]
s2.将s1得到的7-氯-8-甲基喹啉用石油醚进行重结晶后与100.00g邻二氯苯、0.20g偶氮二异丁腈混合,并通入20.00g氯气氯化,反应结束后脱除溶剂,得到24.00g3,7-二氯-8-氯甲基喹啉,加入100.00g60%硫酸形成氧化物配置液;
[0062]
s3.取s2得到的配置液投入三口烧瓶中,采用磁力搅拌,安装有0-100℃水银温度计,冷凝器,在300rpm的搅拌转速下,在该反应条件下,催化剂用量为3,7-二氯-8-氯甲基喹啉质量的5%,即加入1.20g五水硫酸铜,滴加37.50g的27%双氧水,控制滴加时间60min,反应温度75℃,滴加结束后保温12小时;
[0063]
s4.将氧化产物水解,经固液分离,得到21.00g的固相。将固相溶解在85.00g叔丁醇中,缓慢滴加75.00g的10%亚氯酸钠溶液,滴加时间60分钟,滴加结束后在65℃下保温12小时,得到二氯喹啉酸经水洗,得到90.21%含量的二氯喹啉酸22.85g。
[0064]
实施例2
[0065]
s1、s2与实施例1相同,s3中改变五水硫酸铜的加入量为3,7-二氯-8-氯甲基喹啉质量的4%(0.96g),相应的,s4为:将氧化产物水解,经固液分离,得到18.20g的固相。将固相溶解在85.00g叔丁醇中,缓慢滴加75.00g的10%亚氯酸钠溶液,滴加时间60分钟,滴加结束后在65℃下保温12小时,得到二氯喹啉酸经水洗,得到88.05%含量的二氯喹啉酸22.15g。
[0066]
实施例3
[0067]
s1、s2与实施例1相同,s3中改变五水硫酸铜的加入量为3,7-二氯-8-氯甲基喹啉质量的6%(1.44g),相应的,s4为:将氧化产物水解,经固液分离,得到21.05g的固相。将固
相溶解在85.00g叔丁醇中,缓慢滴加75.00g的10%亚氯酸钠溶液,滴加时间60分钟,滴加结束后在65℃下保温12小时,得到二氯喹啉酸经水洗,得到90.04%含量的二氯喹啉酸22.84g。
[0068]
实施例4
[0069]
s1、s2与实施例1相同,s3中改变反应温度为71℃,相应的,s4为:将氧化产物水解,经固液分离,得到20.80g的固相。将固相溶解在85.00g叔丁醇中,缓慢滴加75.00g的10%亚氯酸钠溶液,滴加时间60分钟,滴加结束后在65℃下保温12小时,得到二氯喹啉酸经水洗,得到85.14%含量的二氯喹啉酸21.23g。
[0070]
实施例5
[0071]
s1、s2与实施例1相同,s3中改变反应温度为73℃,相应的,s4为:将氧化产物水解,经固液分离,得到21.00g的固相。将固相溶解在85.00g叔丁醇中,缓慢滴加75.00g的10%亚氯酸钠溶液,滴加时间60分钟,滴加结束后在65℃下保温12小时,得到二氯喹啉酸经水洗,得到88.20%含量的二氯喹啉酸22.30g。
[0072]
实施例6
[0073]
s1、s2与实施例1相同,s3中改变反应温度为77℃,相应的,s4为:将氧化产物水解,经固液分离,得到20.90g的固相。将固相溶解在85.00g叔丁醇中,缓慢滴加75.00g的10%亚氯酸钠溶液,滴加时间60分钟,滴加结束后在65℃下保温12小时,得到二氯喹啉酸经水洗,得到90.02%含量的二氯喹啉酸20.33g。
[0074]
实施例7
[0075]
s1、s2与实施例1相同,s3中改变反应温度为79℃,相应的,s4为:将氧化产物水解,经固液分离,得到20.50g的固相。将固相溶解在85.00g叔丁醇中,缓慢滴加75.00g的10%亚氯酸钠溶液,滴加时间60分钟,滴加结束后在65℃下保温12小时,得到二氯喹啉酸经水洗,得到90.23%含量的二氯喹啉酸20.38g。
[0076]
实施例8
[0077]
s1、s2与实施例1相同,s3中改变反应时间为10h,相应的,s4为:将氧化产物水解,经固液分离,得到20.00g的固相。将固相溶解在85.00g叔丁醇中,缓慢滴加75.00g的10%亚氯酸钠溶液,滴加时间60分钟,滴加结束后在65℃下保温12小时,得到二氯喹啉酸经水洗,得到88.18%含量的二氯喹啉酸22.14g。
[0078]
实施例9
[0079]
s1、s2与实施例1相同,s3中改变反应时间为11h,相应的,s4为:将氧化产物水解,经固液分离,得到20.50g的固相。将固相溶解在85.00g叔丁醇中,缓慢滴加75.00g的10%亚氯酸钠溶液,滴加时间60分钟,滴加结束后在65℃下保温12小时,得到二氯喹啉酸经水洗,得到90.28%含量的二氯喹啉酸22.20g。
[0080]
实施例10
[0081]
s1、s2与实施例1相同,s3中改变反应时间为13h,相应的,s4为:将氧化产物水解,经固液分离,得到21.00g的固相。将固相溶解在85.00g叔丁醇中,缓慢滴加75.00g的10%亚氯酸钠溶液,滴加时间60分钟,滴加结束后在65℃下保温12小时,得到二氯喹啉酸经水洗,得到90.21%含量的二氯喹啉酸22.86g。
[0082]
实施例11
[0083]
s1、s2与实施例1相同,s3中改变反应时间为14h,相应的,s4为:将氧化产物水解,经固液分离,得到21.00g的固相。将固相溶解在85.00g叔丁醇中,缓慢滴加75.00g的10%亚氯酸钠溶液,滴加时间60分钟,滴加结束后在65℃下保温12小时,得到二氯喹啉酸经水洗,得到90.22%含量的二氯喹啉酸22.85g。
[0084]
实施例12
[0085]
s1、s2、s3与实施例1相同,s4.将氧化产物水解,经固液分离。将固相溶解在85.00g叔丁醇中,缓慢滴加75.00g的10%亚氯酸钠溶液,滴加时间60分钟,滴加结束后,改变反应温度为61℃,计时保温氧化12小时,得到88.31%含量的二氯喹啉酸22.12g。
[0086]
实施例13
[0087]
s1、s2、s3与实施例1相同,s4.将氧化产物水解,经固液分离。将固相溶解在85.00g叔丁醇中,缓慢滴加75.00g的10%亚氯酸钠溶液,滴加时间60分钟,滴加结束后,改变反应温度为63℃,计时保温氧化12小时,得到90.24%含量的二氯喹啉酸22.60g。
[0088]
实施例14
[0089]
s1、s2、s3与实施例1相同,s4.将氧化产物水解,经固液分离。将固相溶解在85.00g叔丁醇中,缓慢滴加75.00g的10%亚氯酸钠溶液,滴加时间60分钟,滴加结束后,改变反应温度为67℃,计时保温氧化12小时,得到85.36%含量的二氯喹啉酸22.92g。
[0090]
实施例15
[0091]
s1、s2、s3与实施例1相同,s4.将氧化产物水解,经固液分离。将固相溶解在85.00g叔丁醇中,缓慢滴加75.00g的10%亚氯酸钠溶液,滴加时间60分钟,滴加结束后,改变反应温度为69℃,计时保温氧化12小时,得到85.33%含量的二氯喹啉酸22.95g。
[0092]
实施例16
[0093]
s1、s2、s3与实施例1相同,s4.将氧化产物水解,经固液分离。将固相溶解在85.00g叔丁醇中,缓慢滴加75.00g的10%亚氯酸钠溶液,滴加时间60分钟,滴加结束后,反应温度为65℃,改变计时保温氧化时间为10小时,得到85.44%含量的二氯喹啉酸22.52g。
[0094]
实施例17
[0095]
s1、s2、s3与实施例1相同,s4.将氧化产物水解,经固液分离。将固相溶解在85.00g叔丁醇中,缓慢滴加75.00g的10%亚氯酸钠溶液,滴加时间60分钟,滴加结束后,反应温度为65℃,改变计时保温氧化时间为11小时,得到88.28%含量的二氯喹啉酸22.84g。
[0096]
实施例18
[0097]
s1、s2、s3与实施例1相同,s4.将氧化产物水解,经固液分离。将固相溶解在85.00g叔丁醇中,缓慢滴加75.00g的10%亚氯酸钠溶液,滴加时间60分钟,滴加结束后,反应温度为65℃,改变计时保温氧化时间为13小时,得到90.12%含量的二氯喹啉酸22.82g。
[0098]
实施例19
[0099]
s1、s2、s3与实施例1相同,s4.将氧化产物水解,经固液分离。将固相溶解在85.00g叔丁醇中,缓慢滴加75.00g的10%亚氯酸钠溶液,滴加时间60分钟,滴加结束后,反应温度为65℃,改变计时保温氧化时间为14小时,得到90.26%含量的二氯喹啉酸22.80g。
[0100]
采用hplc分析实施例1~19中二氯喹啉酸的含量,收率(%)=(实际所得固体质量
×
二氯喹啉酸的含量)
÷
二氯喹啉酸的理论值
×
100,各实施例的反应条件及二氯喹啉酸的含量和收率结果记录在表4中。
[0101]
表4反应条件及二氯喹啉酸的含量和收率
[0102][0103]
由表4可以看出,本发明提供一种两步氧化制备二氯喹啉酸的方法,制备的二氯喹啉酸的含量达到90%,二氯喹啉酸的收率达到85%。
[0104]
与实施例1相比,实施例2中催化剂加入较少,收率和含量较低,实施例3中增大催化剂的量,收率和含量也不如实施例1。
[0105]
与实施例1相比,实施例4~7的不同在于第一步氧化s3中反应温度分别为71℃、73℃、77℃、79℃,而实施例4中二氯喹啉酸的含量仅为85.14%、收率仅为74.69%,实施例5中二氯喹啉酸的含量仅为88.20%、收率仅为81.28%,虽然实施例6~7中二氯喹啉酸的含量达到了90%,但是收率仅为75.62和75.99%。因此,第一步氧化s3中反应温度为75℃时,得到的二氯喹啉酸的含量和收率最佳。
[0106]
与实施例1相比,实施例8~11的不同在于第一步氧化s3中反应时间分别为10、11、13、14小时,实施例8中二氯喹啉酸的含量仅为88.18%、收率仅为80.67%,虽然实施例9中
二氯喹啉酸的含量为90.28%,但是收率为82.82%,低于实施例1,因此,当第一步氧化s3中反应时间达到12小时,二氯喹啉酸的含量才能达到90%,收率才能达到85%,当延长时间到13、14小时,得到的含量与收率基本不变,因此,要想得到含量90%,收率85%的二氯喹啉酸,反应12小时是最佳的反应时间。
[0107]
与实施例1相比,实施例12~15的不同在于第二步氧化s4中反应温度分别为61℃、63℃、67℃、69℃,实施例12、实施例14、实施例15中二氯喹啉酸的含量均低于90%,收率均低于85%,虽然实施例13中二氯喹啉酸的含量达到了90.24%,但收率低于85%,因此,当第二步氧化s4中反应温度为65℃时,得到的二氯喹啉酸的含量和纯度最佳。
[0108]
与实施例1相比,实施例16~19的不同在于第二步氧化s4中反应时间分别为10、11、13、14小时,实施例16~17中二氯喹啉酸的含量和收率均低于实施例1,因此,当第二步氧化s4中反应时间达到12小时,二氯喹啉酸的含量才能达到90%,收率才能达到85%,当延长时间到13、14小时,得到的含量与收率基本不变,因此,要想得到含量90%,收率85%的二氯喹啉酸,反应12小时是最佳的反应时间。
[0109]
以上仅为本发明的较佳实施例而已,并不用以限制本发明,凡在本发明的精神和原则之内,所作的任何修改、等同替换、改进等,均应包含在本发明的保护范围之内。
再多了解一些
本文用于创业者技术爱好者查询,仅供学习研究,如用于商业用途,请联系技术所有人。