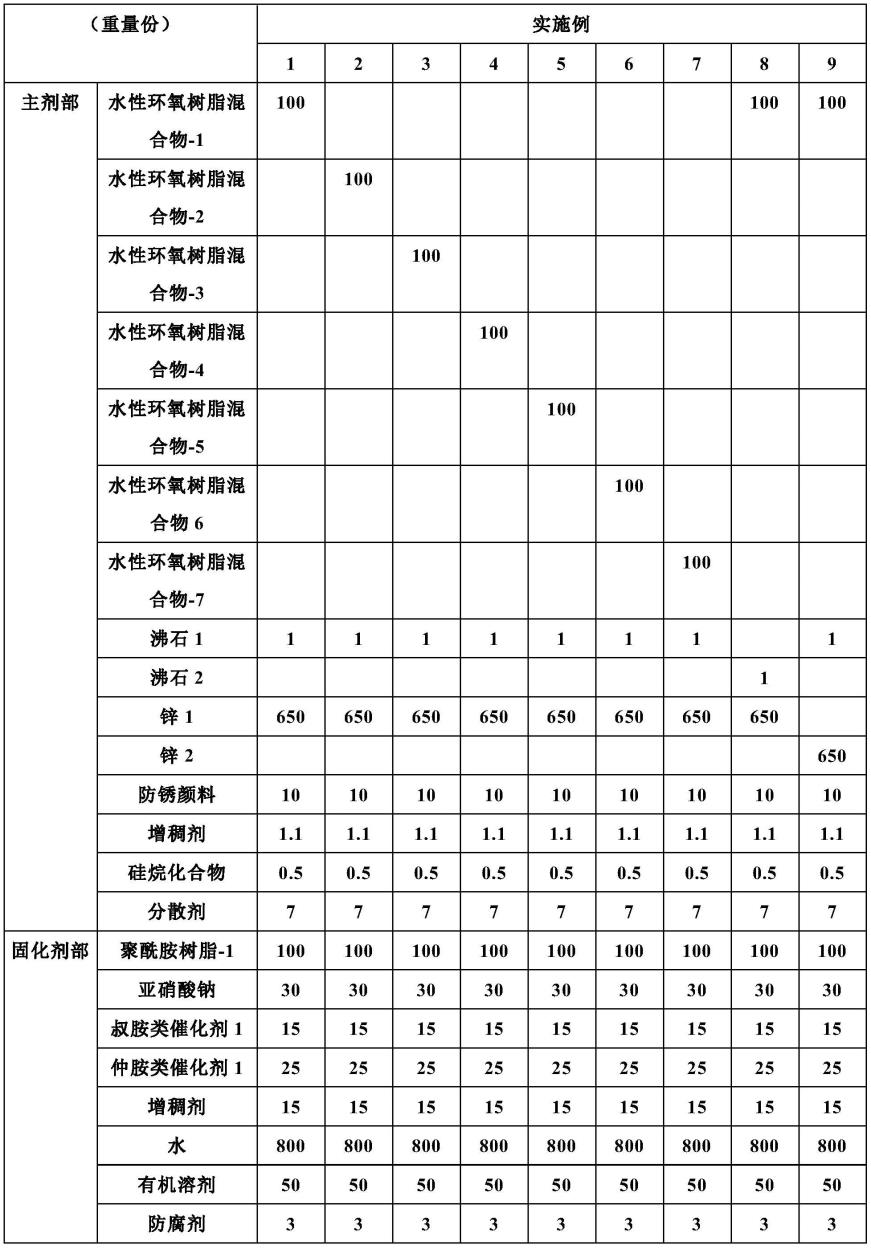
1.本发明涉及一种水性重防腐涂料组合物,在制造涂膜时,该组合物即使在未固化状态下也具有优异的耐锈性(rust resistance),从而防止涂装后初期产生锈,由此具有优异的长期防锈性。
背景技术:
2.重防腐涂装(heavy duty coating)是为了保护桥梁、铁塔、海上结构物、各种发电厂的大型结构物、船舶或处于腐蚀环境中的其他铁结构物免受腐蚀而进行的涂装,是指涂覆能够耐严重腐蚀环境的涂料的涂装。具体地,在制作集装箱箱体时,为了防止基材的腐蚀及维持机械强度,以往通常使用油性涂料。然而,由于油性涂料内挥发性有机化合物(vocs)引起的环境污染和使用涂料时作业人暴露于有机溶剂,从而存在安全性问题。与此相关,自2017年4月以后,在中国施行如下法案,即,对在中国制作的集装箱用涂料而言,都需要使用水性涂料。
3.在制作集装箱箱体时使用水性涂料的情况下,通常以常温为基准需要7天以上的干燥时间。由于涂装有水性涂料的集装箱箱体的体积较大,因此在完全固化之前,可能会暴露于雨或阳光下的外部环境,此时存在产生锈(rust)的问题。
4.另一方面,环氧树脂容易与胺或酸等发生反应,从而表现出较强的固化结构。特别地,双酚a型环氧树脂由于耐化学性、耐热性、高硬度和柔韧性等特征而被广泛用于各种工业领域。上述工业领域的例子可以举出涂料领域,上述涂料领域中环氧树脂用作主剂的主要成分。具体地,韩国授权专利第910983号(专利文献1)公开了一种二液型水性环氧锌(metal zinc)重防腐防锈涂料,作为基准包含:主剂部,包含环氧树脂、醋酸溶纤剂(cellosolve acetate)、锌(metal zinc)粉末及活性陶瓷粉末;以及固化剂部,包含聚酰胺树脂、聚胺树脂、芳香胺树脂、丁基溶纤剂及水。然而,如专利文献1所示的现有的水性环氧涂料在获得具有市场上所需的物理性质的涂膜方面存在限制。特别是,水性双酚a型环氧树脂使涂膜的抗冲击性显著地降低,因此难以用于重防腐涂装用涂料或工厂涂装用涂料。
5.因此,需要开发一种重防腐涂料组合物,在制备涂膜时,该组合物即使在未固化状态下也具有优异的耐锈性,从而防止在涂覆后的初始阶段产生锈,因水性而具有优异的环保性。
6.(现有技术文献)
7.(专利文献)
8.专利文献1:韩国授权专利第910983号(公开日期:2009.7.30)。
技术实现要素:
9.(发明所要解决的问题)
10.因此,本发明提供一种重防腐涂料组合物,在制造涂膜时,该组合物即使在未固化状态下也具有优异的耐锈性(rust resistance),从而防止涂装后初期产生锈,因水性而具
有优异的环保性。
11.(解决问题所采用的措施)
12.本发明涉及一种水性重防腐涂料组合物,该组合物包含:主剂部,包含水性环氧树脂混合物、沸石和锌(metal zinc);以及固化剂部,包含聚酰胺树脂、亚硝酸钠(nano2)及胺类催化剂。
13.(发明的效果)
14.根据本发明的水性重防腐涂料组合物在制造涂膜时,即使在未固化状态下也具有优异的耐锈性(rust resistance),从而防止涂装后初期产生锈,由此能够形成具有优异的长期防锈性的涂膜。另外,上述涂料组合物中挥发性有机化合物(voc)的产生少,并且因水性而具有优异的环保性。
具体实施方式
15.以下,详细说明本发明。
16.在本发明中,诸如“环氧当量”和“活性氢当量”之类的官能团值可以通过本领域公知的方法测定,例如,可以是通过滴定(titration)方法等测定的值。
17.另外,在本发明中,树脂的“玻璃化转变温度”是通过本领域已知的常规方法测定的,例如,可以通过差示扫描量热法(differential scanning calorimetry,dsc)等测定。
18.另外,在本发明中,树脂的“重均分子量”可以通过本领域公知的方法来测定,例如,可以表示通过gpc(gel permeation chromatograph:凝胶渗透色谱法)等方法测定的值。
19.根据本发明的水性重防腐涂料组合物,包含:主剂部,包含水性环氧树脂混合物、沸石和锌(metal zinc);以及固化剂部,包含聚酰胺树脂、亚硝酸钠(nano2)和胺类催化剂。
20.通过包含上述沸石,能够防止锌(metal zinc)与涂膜中所包含的水分的反应,从而确保防锈性。另外,通过包含上述亚硝酸钠(nano2),起到防止涂膜中所包含的水分与铁的反应所产生的点锈的作用。
21.即,上述水性重防腐涂料组合物为二液型,固化剂部及主剂部分别保管在单独的容器,然后可以在使用之前充分混合而使用。
22.主剂部
23.上述主剂部包含水性环氧树脂混合物、沸石和锌(metal zinc)。
24.水性环氧树脂混合物
25.水性环氧树脂混合物作为涂料组合物的主要树脂,与固化剂部发生反应而形成涂膜,并起到调节所制备的涂膜的特性的作用。特别地,上述水性环氧树脂混合物起到可以提高上述涂料组合物在常温下的速干和快速固化性能的作用。
26.上述水性环氧树脂混合物只要是通常可作为重防腐环氧树脂涂料的主剂使用的环氧树脂,则不受特别的限制,例如,可以举出选自双酚环氧树脂、酸酐改性环氧树脂、异氰酸酯改性环氧树脂、线型酚醛树脂(novolac)改性环氧树脂、橡胶改性环氧树脂等中的一种以上的混合物。具体地,上述水性环氧树脂混合物可以是双酚a型环氧树脂和酸酐改性环氧树脂的混合物。
27.上述双酚a型环氧树脂的环氧当量(eew)可以为900至1200g/eq或1000至1100g/
eq。当上述双酚a型环氧树脂的环氧当量小于上述范围时,难以使包含双酚a型环氧树脂的环氧树脂混合物进行水溶解,从而存储稳定性可能会降低。当上述双酚a型环氧树脂的环氧当量超过上述范围时,所制备的涂膜的防锈性可能会降低。
28.另外,上述双酚a型环氧树脂的玻璃化转变温度(tg)可以为80至110℃或90至100℃。当上述双酚a型环氧树脂的玻璃化转变温度低于上述范围时,涂膜的干燥变慢,未固化的涂膜的防锈性可能会降低,当上述双酚a型环氧树脂的玻璃化转变温度超过上述范围时,涂膜在完全形成之前被干燥,从而可能会产生针孔。
29.相对于树脂的总重量,上述双酚a型树脂可以具有固形物含量(nv)为55至80重量%或65至75重量%的水分散液形态。当上述双酚a型树脂的固形物含量小于上述范围时,难以设计最终涂料产品的高固形物含量(high solid)化,因此当涂装相同量时,涂膜的成膜性降低,存在经济性降低的问题,当上述双酚a型树脂的固形物含量超过上述范围时,涂料的粘度增加,难以确保最终涂料产品的顺畅的作业性,可能会发生流挂性降低的问题。
30.上述酸酐改性环氧树脂的环氧当量(eew)可以为300至600g/eq或400至500g/eq。当上述酸酐改性环氧树脂的环氧当量小于上述范围时,由于酸酐改性环氧树脂中亲水性物质的减少,难以使包含酸酐改性环氧树脂的环氧树脂混合物水溶解,当上述酸酐改性环氧树脂的环氧当量超过上述范围时,由于酸酐改性环氧树脂中亲水性物质的增加,可能会产生所制备的涂膜的防锈性变差的问题。
31.另外,上述酸酐改性环氧树脂的玻璃化转变温度(tg)可以为-10至10℃或-5至5℃。当上述酸酐改性环氧树脂的玻璃化转变温度低于上述范围时,涂膜的干燥变慢,未固化的涂膜的防锈性可能会降低,当上述酸酐改性环氧树脂的玻璃化转变温度超过上述范围时,涂膜在完全形成前被干燥,从而可能会产生针孔。
32.另外,相对于树脂的总重量,上述酸酐改性环氧树脂可以具有固形物含量(nv)为60至90重量%的或70至80重量%的水分散液形态。当上述酸酐改性环氧树脂的固形物含量小于上述范围时,难以设计最终涂料产品的高固形物含量(high solid)化,因此当涂装相同量时,涂膜的成膜性降低,存在经济性降低的问题,当上述酸酐改性环氧树脂的固形物含量超过上述范围时,涂料的粘度增加,难以确保最终涂料产品的顺畅的作业性,可能会发生流挂性降低的问题。
33.上述水性环氧树脂混合物可以包含重量比为1:4至1:7或者为1:5.5至1:6.5的双酚a型环氧树脂和酸酐改性环氧树脂。当双酚a型环氧树脂与酸酐改性环氧树脂的重量比小于上述范围时,即以双酚a型环氧树脂为基准包含少量酸酐改性环氧树脂时,随着抗冲击性变差,存在附着性降低和流挂性降低的问题,当双酚a型环氧树脂与酸酐改性环氧树脂的重量比超过上述范围时,即以双酚a型环氧树脂为基准包含过量酸酐改性环氧树脂时,可能会产生防锈性变差的问题。
34.另外,上述水性环氧树脂混合物的环氧当量(eew)可以为500至800g/eq或550至700g/eq。当上述水性环氧树脂混合物的环氧当量小于上述范围时,所制备的涂膜的附着性可能会变差,当上述水性环氧树脂混合物的环氧当量超过上述范围时,涂料组合物的粘度增加,可能会产生涂料的水分散性变差的问题。
35.上述水性环氧树脂混合物的玻璃化转变温度(tg)可以为1至10℃或3至8℃。当水性环氧树脂混合物的玻璃化转变温度低于上述范围时,存在所制备的涂膜的干燥性变差且
可使用时间会缩短的问题,当水性环氧树脂混合物的玻璃化转变温度高于上述范围时,可能会产生流动性降低导致的诸如粘度的增加等涂料的存储性降低的问题。
36.另外,相对于树脂的总重量,上述水性环氧树脂混合物可以具有固形物含量(nv)为60至85重量%或65至80重量%的水性分散液形态。当水性环氧树脂混合物的固形物含量小于上述范围时,挥发性有机化合物(voc)的含量可能会过多,当水性环氧树脂混合物的固形物含量超过上述范围时,可能会产生涂装作业性降低的问题。
37.沸石
38.沸石通过分子筛捕获涂料内或从外部渗透的水分,以防止锌(metal zinc)与水分的反应,从而起到提高防锈性及存储稳定性的作用。
39.此时,上述沸石只要是市场上可购买的沸石,则可以没有特别的限制地使用。
40.上述沸石的平均粒径可以为0.1至10μm或1至5μm,气孔的平均粒径可以为1至或3至当沸石的平均粒径小于上述范围时,存在水分吸收变差的问题,当沸石的平均粒径超过上述范围时,可能会发生分散状态变差的问题。
41.并且,相对于100重量份的水性环氧树脂混合物,上述沸石可以以0.1至10重量份或0.5至3重量份的含量包含于主剂部。当主剂部中沸石的含量小于上述范围时,存在涂料存储性变差的问题,当主剂部中沸石的含量超过上述范围时,可能会发生所制备的涂膜的防锈性变差的问题。
42.锌(metal zinc)
43.锌比基材的铁更先与氧气反应,从而起到提高所制备的涂膜的防锈性的作用。
44.此时,上述锌只要是通常可在重防腐涂料组合物中使用的锌,则可以没有特别的限制地使用。
45.上述锌的平均粒径可以为1.0至10.0μm或5.5至7.0μm的粉末形态。当锌的平均粒径小于上述范围时,存在涂装后涂膜断裂的问题,当锌的平均粒径超过上述范围时,可能会产生所制备的涂膜的耐水性变差的问题。
46.另外,相对于100重量份的水性环氧树脂混合物,主剂部中上述锌的含量可以为400至850重量份或500至800重量份。当在主剂部中锌的含量小于上述范围时,存在涂膜的防锈性变差的问题,当在主剂部中锌的含量超过上述范围时,可能会产生涂膜的附着力变差的问题。
47.主剂部添加剂
48.上述主剂部可以进一步包括例如分散剂、消泡剂、增稠剂、硅烷化合物和防锈颜料等主剂部添加剂。此时,上述各主剂部添加剂只要是通常可用于重防腐涂料组合物的添加剂则不受特别限制。
49.固化剂部
50.上述固化剂包括聚酰胺树脂、亚硝酸钠(nano2)和胺类催化剂。
51.聚酰胺树脂
52.聚酰胺树脂起到与水性环氧树脂混合物发生反应以使组合物固化而形成涂膜的作用。
53.上述聚酰胺树脂可以通过使二聚酸与聚胺类化合物发生反应而制备。
54.此时,二聚酸只要是通常在制备聚酰胺树脂时可使用的二聚酸,可以无特别限制
地使用,例如可以举出己二酸、辛二酸、癸二酸、壬二酸、对苯二甲酸、间苯二甲酸、2-氯对苯二甲酸、2-甲基对苯二甲酸、5-甲基间苯二甲酸、六氢邻苯二甲酸酐(hhpa)、环烷酸(naphthenic acid)及甲基四氢邻苯二甲酸酐等。
55.另外,上述聚胺类化合物可以在一个分子中包含两个以上的胺基,例如可以举出脂肪族聚胺类化合物、芳香族聚胺类化合物、杂环聚胺类化合物等。
56.上述聚酰胺树脂的活性氢当量(ahew)可以为120至160g/eq。当聚酰胺树脂的活性氢当量小于上述范围时,由于固化密度降低而存在涂膜耐久性不良的问题,当聚酰胺树脂的活性氢当量超过上述范围时,由于疏水性的酰胺含量的增加而存在难以使涂料进行水溶解的问题。
57.另外,上述聚酰胺树脂的重均分子量(mw)可以为800至1200g/mol或900至1100g/mol。当聚酰胺树脂的重均分子量小于上述范围时,存在难以使涂料水溶解的问题,当聚酰胺树脂的重均分子量超过上述范围时,存在涂膜的防锈性降低的问题。
58.上述聚酰胺树脂在25℃下的粘度可以为3000至5000cps或3500至4500cps。当聚酰胺树脂在25℃下的粘度小于上述范围时,存在由于聚酰胺树脂的低分子量而导致的涂膜的防锈性和附着性降低的问题,当聚酰胺树脂在25℃下的粘度超过上述范围时,可能会发生涂料的作业性不良的问题。
59.亚硝酸钠(nano2)
60.亚硝酸钠(nano2)起到应用于涂料而防止涂膜中包含的水分与铁反应所产生的点锈的作用。
61.此时,上述亚硝酸钠只要是市场上可购买的亚硝酸钠,则可以不受特别的限制地使用。
62.上述亚硝酸钠可以以水溶液形态使用,此时,水溶液的浓度可以为10至40重量%或20至30重量%。当亚硝酸钠的水溶液的浓度低于上述范围时,存在涂膜上产生点锈的问题,当亚硝酸钠的水溶液的浓度超过上述范围时,可能会产生涂料的存储性变差的问题。
63.另外,以上述亚硝酸钠水溶液为基准,相对于100重量份的聚酰胺树脂,可以以10至50重量份或20至40重量份的含量包含于固化剂部。当固化剂部中亚硝酸钠的含量低于上述范围时,存在涂膜上产生点锈的问题,当固化剂部中亚硝酸钠的含量超过上述范围时,可能会产生涂料的变色及存储性变差的问题。
64.胺类催化剂
65.胺类催化剂起到提高涂料组合物的固化性的作用。
66.上述胺类催化剂可以包含选自由仲胺和叔胺组成的组中的一种以上。具体地,上述胺类催化剂可以包含仲胺类催化剂和叔胺类催化剂。如上所述,当将仲胺类催化剂和叔胺类催化剂组合使用为胺类催化剂时,具有在环氧固化过程整体中提高初始固化反应速率且直接参与固化结构而提高交联密度的效果。
67.上述仲胺类催化剂可以包含例如丙二胺、二乙胺、哌啶、二苯胺等。
68.另外,上述叔胺类催化剂可以包含例如三乙二胺、三乙醇胺、1,4-重氮环辛烷、二甲基乙醇胺、乙基吗啉、二甲基氨基乙基吗啉、二甲基环己胺等。
69.上述胺类催化剂可以包括重量比为1:0.1至2.0或1:0.3至1的仲胺类催化剂和叔胺类催化剂。当仲胺类催化剂与叔胺类催化剂的重量比小于上述范围时,即以仲胺类催化
剂为基准包含少量叔胺类催化剂时,涂膜的固化干燥可能会延迟,当仲胺类催化剂与叔胺类催化剂的重量比超过上述范围时,即以仲胺类催化剂为基准包含过量叔胺类催化剂时,可能会产生在完全固化后涂膜的强度变差的问题。
70.相对于100重量份的聚酰胺树脂,上述胺类催化剂可以以15至70重量份或20至55重量份的含量包含于固化剂部。具体地,相对于100重量份的聚酰胺树脂,上述固化剂部可以包含:10至40重量份或12至35重量份的仲胺类催化剂;以及5至30重量份或7.5至20重量份的叔胺类催化剂。
71.当固化剂部内胺类催化剂的含量低于上述范围时,存在催化剂含量不足引起涂料的固化速度延迟的问题,当固化剂部内胺类催化剂的含量超过上述范围时,由于完全固化后未与环氧树脂结合的物质增加,可能会产生涂膜的强度降低的问题。另外,当固化剂部内仲胺类催化剂的含量小于上述范围时,存在涂料的固化速度延迟的问题,当固化剂部内仲胺类催化剂的含量超过上述范围时,可能会产生涂膜的强度降低的问题。另外,当固化剂部内叔胺类催化剂的含量低于上述范围时,存在涂料的固化速度延迟的问题,当固化剂部内叔胺类催化剂的含量超过上述范围时,可能会产生涂膜的强度降低的问题。
72.溶剂
73.上述涂料组合物可以进一步包含溶剂。此时,溶剂起到调节涂料组合物的粘度而提高作业性、调节干燥速度、调节挥发性有机化合物(voc)的含量的作用。
74.上述溶剂可以包含水和与水具有相容性的有机溶剂。此时,与水具有相容性的有机溶剂可以举出例如醇类和酯类。具体地,上述有机溶剂可以包含选自由n-丙醇(n-propanol)、丁氧基乙氧基乙醇(butoxy ethoxy ethanol)、二甘醇单丁醚(diethylene glycol monobutyl ether)、丁氧基乙醇(butoxy ethanol)、乙二醇单丁醚(ethylene glycol monobutyl ether)、二丙二醇丁醚(dipropylene glycol butylether,dpnb)、乙二醇单己醚(ethylene glycol monohexyl ether)、n-己二醇(n-hexyl glycol)、二丙二醇正丁醚(dipropylene glycol n-butyl ether)、甲氧基丙醇(methoxy propanol)及异丙醇(isopropyl cohol,ipa)组成的组中的一种以上。
75.另外,相对于100重量份的聚酰胺树脂,上述溶剂的含量可以为500至1600重量份或700至1000重量份。具体地,相对于100重量份的聚酰胺树脂,上述组合物可以包含500至1500重量份的水和10至100重量份的与水具有相容性的有机溶剂。
76.当上述溶剂含量小于上述范围时,组合物的粘度高,存在作业性不足的问题,当上述溶剂含量超过上述范围时,可能会产生在制备涂膜时干燥速度变慢而不能进行速干和快速固化的问题。当上述水的含量小于上述范围时,在与主剂混合时粘度高,从而存在难以均匀混合的问题,当上述水的含量超过上述范围时,由于相容性降低,可能会产生涂料的存储性变差的问题。另外,当上述有机溶剂的含量小于上述范围时,组合物的粘度高,从而存在作业性不足的问题,当上述有机溶剂的含量超过上述范围时,由于相容性降低,涂料的存储性可能会出现问题。
77.固化剂部添加剂
78.上述固化剂部可进一步包含增稠剂、防腐剂等固化剂部添加剂。此时,上述各固化剂部添加剂只要是通常可用于重防腐涂料组合物的添加剂则不受特别的限制。
79.上述涂料组合物可以包含重量比为1:3至1:6或1:3.5至1:4.5的上述固化剂部和
上述主剂部。当固化剂部和主剂部的混合比小于上述范围时,长期防锈性和耐水性等涂膜的物理性质可能会降低,当固化剂部和主剂部的混合比超过上述范围时,涂膜的干燥性可能会降低。
80.如上所述,制备涂膜时,根据本发明的水性重防腐涂料组合物即使在未固化状态下也具有优异的耐锈性(rust resistance),从而防止涂装后初期产生锈,由此能够形成具有优异的长期防锈性的涂膜。另外,上述涂料组合物的挥发性有机化合物(voc)的产生少,并且因水性而环保性优异。
81.以下,通过实施例进一步具体说明本发明。然而,这些实施例仅用于帮助理解本发明,不会在任何意义上将本发明的范围限定于这些实施例。
82.[实施例]
[0083]
实施例1至25和比较例1和4,重防腐涂料组合物
[0084]
按照表1至4所示的组成将各成分混合而制备主剂部及固化剂部。然后,以4:1的重量比混合主剂部和固化剂部,从而制备重防腐涂料组合物。
[0085]
[表1]
[0086][0087]
[表2]
[0088][0089]
[表3]
[0090]
[0091][0092]
[表4]
[0093][0094]
比较例及实施例中使用的各成分的制造商及产品名称、物理性质等如下表5所示。此时,nv是固形物含量,单位是重量%,eew是环氧当量,单位是g/eq,ahew是活性氢当量,单位是g/eq,tg是玻璃化转变温度,单位是℃,mw是重均分子量,单位是g/mol,vis是在25℃下测定的粘度,单位是cps。
[0095]
[表5]
[0096]
[0097][0098]
试验例:物理性质的评价
[0099]
将实施例和比较例的重防腐涂料组合物涂装成干膜厚度为30μm,并在常温下放置20分钟以形成涂膜。然后,通过如下方法测定实施例及比较例的重防腐涂料组合物及所制备的涂膜的物理性质,其结果如表6至9所示。
[0100]
(1)存储稳定性
[0101]
将涂料组合物在60℃下放置168小时后,用肉眼评价涂料组合物的增稠、颜料的沉淀及相分离。
[0102]
具体地,没有存储后涂料的粘度增加、颜料的沉淀及相分离时评价为优秀(
◎
),颜
料的沉淀软时评价为良好(
○
),颜料的沉淀硬时评价为一般(
△
),颜料的沉淀硬且发生相分离时评价为不良(
×
)。
[0103]
(2)未固化涂膜的防锈性(rust resistance)
[0104]
将实施例和比较例的涂料组合物涂装成干膜厚度为30μm,并在60℃下放置20分钟,然后在常温下放置5分钟,从而形成下涂涂膜。然后,将水性环氧涂料组合物(制造商:kcc,产品名:wt3600)涂装于下涂涂膜上至干膜厚度为50μm,在60℃下放置20分钟后,在常温下放置5分钟以形成上涂涂膜。然后,在40℃下放置15分钟后,在相对湿度95%及温度55℃下放置2天后,根据astm d610用肉眼评价是否产生锈及水泡的产生。
[0105]
当未产生锈(rust)时判断为“锈(rust)10”,当产生的锈面积小于0.03面积%时判断为“锈9”,当产生的锈面积为0.03面积%以上且小于0.1面积%时判断为“锈8”,当产生的锈面积为0.1面积%以上且小于0.3面积%时判断为“锈7”,当产生的锈面积为0.3面积%以上且小于1面积%时判断为“锈6”,当产生的锈面积为1面积%以上且小于3面积%时判断为“锈5”,当产生的锈面积大于3面积%时判断为“锈4”。
[0106]
(3)可使用时间(hr)
[0107]
在40℃下添加水而使涂料组合物的浓度达到15重量%后,在40℃下放置的同时,以蔡恩杯3号(zahn cup3)为基准以1小时为间隔共3小时为止测定涂料的粘度变化而测定粘度,来评价涂料的粘度变化幅度,用这种方法来测定可使用时间。以初始粘度测定时为基准,将1小时、2小时和3小时后的粘度差用“ 秒”或
“‑
秒(sec)”表示。例如,“ 3sec”表示以初始粘度为基准增加3秒,而已发生固化/干燥而涂料几乎不流动时评价为失败。与初始粘度的差异越小,则可以判断为物理性质越优异。
[0108]
(4)流挂性(sagging)
[0109]
添加稀释水而使涂料组合物的浓度达到15重量%,并用无气(airless)涂装方法在30cm
×
30cm的试片上进行涂装。此时,无气喷涂机使用泵比(pump ratio)为45:1的条件、3mpa的输入压力和tip尺寸(size)815。
[0110]
涂装成所涂装的涂膜的湿膜厚度(wet film thickness,w.f.t)达到100μm后,用肉眼观察而评价涂料的流动性。此时,w.f.t的测定使用byk w.f.t测量仪(gage),以如下基准进行评价。
[0111]
具体地,如果没有涂料的流动,则评价为1级,如果边界线部位下垂(waving),则评价为2级,如果一部分涂料流动(slight sagging),则评价为3级,如果有大量的涂料流动(severe sagging),则评价为4级,如果涂料流动非常严重而边界线部分完全重叠(collapsed),则评价为5级。
[0112]
(5)针孔(pinhole)
[0113]
添加稀释水而使涂料组合物的浓度达到15重量%,并用无气涂装方法在30cm
×
30cm的试片上进行涂装。此时,无气涂装机使用泵比为45:1的条件、3mpa的输入压力和tip尺寸815。
[0114]
涂装成涂装后的涂膜的湿膜厚度(w.f.t)达到100μm后,在常温下干燥5分钟后,在60℃烘箱中干燥30分钟,利用10倍放大镜评价涂膜表面的针孔。此时,评价标准如下。
[0115]
1:没有观察到针孔
[0116]
2:针孔的数量为1~4个
[0117]
3:针孔的数量为5~10个
[0118]
4:针孔的数量超过10个且少于20个
[0119]
5:针孔的数量为20个以上
[0120]
(6)产生锈(rust):防锈性-1
[0121]
将实施例和比较例的涂料组合物涂装成干膜厚度为30μm,在60℃下放置20分钟,然后在常温下放置5分钟,从而形成下涂涂膜。然后,将水性环氧上涂涂料(制造商:kcc,产品名:wt3600)涂装于下涂涂膜上至干膜厚度为50μm,并在60℃下放置20分钟后,在常温下放置5分钟以形成上涂涂膜。然后,将试片在常温下放置7天以完成试片。根据astm d610,将所制造的试片在盐雾(salt-fog)中经1000小时后,通过测量产生的锈来评价防锈性。此时,评价标准适用与项目(2)相同的基准。
[0122]
(7)产生水泡:防锈性-2
[0123]
根据astm d714,将5%的盐水喷雾到试片上并放置1000小时,然后,观察试片外观,用肉眼观察是否产生水泡而评价防锈性。
[0124]
水泡的大小用数字表示,数字越小,则水泡的大小越大。另外,水泡产生的频率用字母表示,以很少(few)、m(midium:中)、md(midium dense:中密)及d(dense:密)的顺序表示。
[0125]
(8)产生蠕变(creep):防锈性-3
[0126]
根据astm d1654,在试片上用刀切割1mm的切口,并在340nm的uv-a下放置3天后,将5%的盐水喷雾并放置4天,以此为1次共进行8次,然后测量锈从切口渗透的距离(mm)而评价防锈性。
[0127]
(9)附着性
[0128]
将涂膜在60℃下干燥8小时并在100%湿度条件下处理4小时,以此为1次共重复6次。然后,在30℃下干燥4小时并在40℃下干燥2小时,以此为1次共重复16次。然后,根据astm d3359胶带附着性试验方法,在试片涂膜上用刀形成25个2mm
×
2mm(横向
×
纵向)的正方形后,以上述正方形为对象进行胶带附着性试验后,测定剥离程度而评价附着性。
[0129]
此时,当25个正方形100%完全附着时评价为5b,当剩余正方形为95%以上且少于100%时评价为4b,当剩余正方形为85%以上且少于95%时评价为3b,当剩余正方形为65%以上且少于85%时评价为2b,当剩余正方形为35%以上且少于65%时评价为1b,当剩余正方形少于35%时评价为0b。
[0130]
[表6]
[0131][0132]
[表7]
[0133][0134][0135]
[表8]
[0136][0137]
[表9]
[0138][0139][0140]
从上述表6至8的结果可以确认到,当使用根据本发明的实施例1至25的涂料组合物时,物理性质在整体上表现得优异。
[0141]
与此相反,从上述表9的结果可以确认到,当使用脱离根据本发明的组合物组成的比较例1至3的涂料组合物时,与实施例的涂料相比,测定的项目在整体上表现出变差的物理性质。
再多了解一些
本文用于创业者技术爱好者查询,仅供学习研究,如用于商业用途,请联系技术所有人。