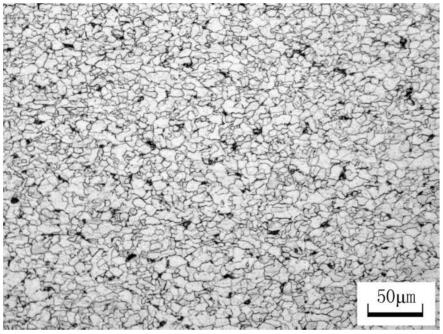
1.本发明涉及带钢生产技术领域,具体地指一种高表面高精度的高强搪瓷钢及生产方法。
背景技术:
2.搪瓷钢广泛地应用于轻工、家电、冶金、化工、建筑等行业。搪瓷用钢的性能要求主要包括:1)良好的成型性能和抗减薄能力;2)优良的涂搪性能,包括抗鳞爆性能、钢板与瓷釉之间的密着性能和抗针孔、气泡缺陷等;3)优良的焊接性能,要求焊缝及热影响区具有较高的强度和良好的塑性,同时还应具有优良的涂搪性能;4)对于电热水器内胆用钢等承压容器来说,钢板经过高温烧成后仍要保持较高的屈服强度,以满足搪瓷内胆的打压和疲劳性能要求。应家电、建筑等行业的轻量化需求,搪瓷钢逐渐向高强、减薄方向发展。
3.专利“地铁装饰用薄板搪瓷钢及其制造方法”(cn201510398485.9)介绍了一种地铁装饰用薄板搪瓷钢及制造方法,搪瓷钢的厚度为1.0-2.0mm,搪瓷钢的化学成分重量百分比如下:c:0.001-0.003%;si≤0.10%;mn:0.05-0.10%;p≤0.010%;s≤0.005%;als:0.01-0.02%;ti:0.20~0.25%;n:0.010~0.020%,其余为fe及不可避免的杂质。其生产步骤包括铁水脱硫、转炉顶底复合吹炼、板坯连铸、均热炉均热、热连轧控轧控冷、卷取、酸洗、质量检测、加工成形、喷丸、碱洗、喷搪、烧搪。产品厚度为1.0~2.0mm,屈服强度≥460mpa,抗拉强度≥550mpa,伸长率为37~42%,r值为1~1.5,n值为0.2~0.3。
4.专利“一种地铁装饰用热轧搪瓷钢板及其制造方法”(cn201710064842.7)介绍了一种地铁装饰用热轧搪瓷钢板及其制造方法,化学成分质量百分比为:c:0.05~0.09%、si:0.10~0.20%、mn:0.65~0.95%、p≤0.012%、s≤0.015%、ti:0.05~0.10%、als:0.015~0.045%、cr:0.10~0.20%。铸坯均热温度为1180~1250℃,均热后经高压水除鳞,粗轧成中间坯;精轧开轧温度设定在980~1100℃,终轧温度设定在880~950℃;通过层流冷却后,在580~650℃的温度区间内进行卷取。产品厚度为1.5~2.75mm,屈服强度达390mpa以上,断后延伸率达40%以上。
5.ti是一种低成本地改善搪瓷钢性能的元素,搪瓷钢加ti不仅可以提高抗鳞爆性能和密着性能,同时还能显著提高强度。但由于ti性质活泼,易与钢中的o、s、n等元素结合,导致与c结合形成tic的有效ti不稳定,造成强度、延伸率波动较大。同时,薄规格板形难以控制,易产生厚度精度差、拱北、浪形等板形问题。强度波动、板形差会造成零件加工精度差。此外,薄规格搪瓷钢在生产过程中容易因轧辊剥落形成氧化铁皮压入缺陷,酸洗后形成麻点、麻坑,表面质量较差,使鳞爆和密着性能劣化。
技术实现要素:
6.本发明的目的就是要解决上述背景技术的不足,提供一种高表面高精度的高强搪瓷钢及生产方法,产品屈服强度为420~470mpa,抗拉强度为560~630mpa,延伸率≥38%,屈服强度波动范围为50mpa,厚度精度为
±
30μm,不平度≤8mm,可满足高精度零件成形的要
求。
7.本发明的技术方案为:一种高表面高精度的高强搪瓷钢,其特征在于,包括以下按重量百分比的化学成分,
8.c:0.04~0.07%,si:0.05~0.1%,mn:0.8~1.2%,ti:0.04~0.08%,n≤0.004%,p≤0.015%,s≤0.003%,mg:0.001~0.004%,余量为fe及不可避免的杂质。
9.优选的,包括以下按重量百分比的化学成分,
10.c:0.04~0.045%,si:0.05~0.07%,mn:1.0~1.2%,ti:0.06~0.08%,n:0.003~0.004%,p≤0.012%,s:0.002~0.003%,mg:0.003~0.004%,余量为fe及不可避免的杂质。
11.进一步的,所述高表面高精度的高强搪瓷钢的厚度为0.8~3mm,屈服强度为420~470mpa,抗拉强度为560~630mpa,延伸率≥38%。
12.更进一步的,所述高表面高精度的高强搪瓷钢的抗鳞爆敏感性th值≥25min/mm2,密着等级为1级。
13.本发明还提供一种上述高表面高精度的高强搪瓷钢的生产方法,为第一生产方法或第二生产方法,
14.所述第一生产方法包括以下步骤:
15.(1)精炼:将c、si含量符合目标要求的钢水采用lf-rh双联精炼工艺,精炼过程中控制s、n、p残余元素含量,并添加锰合金和钛合金,确保mn、ti元素满足目标成分要求,精炼结束后喂mg-al合金或ni-mg合金用于保证钢中mg含量;
16.(2)浇铸:控制铸坯厚度为55~65mm,拉速为3.8~5.5m/min;
17.(3)铸坯除鳞:控制除鳞压力为15~30mpa;
18.(4)铸坯加热:控制铸坯加热温度为1130~1180℃;
19.(5)精轧:控制精轧除鳞压力为20~35mpa,f1压下率为55~65%、f2压下率为45~55%、f3压下率为35~45%,精轧过程中需投入润滑轧制,终轧温度为840~880℃;
20.(6)层流冷却:采用两段式动态冷却;
21.(7)卷取:控制卷取温度为680~740℃/s;
22.(8)酸洗去除表面氧化铁皮;
23.所述第二生产方法包括以下步骤:
24.(1)精炼:将c、si含量符合目标要求的钢水采用lf-rh双联精炼工艺,精炼过程中控制s、n、p残余元素含量,并添加锰合金和钛合金,确保mn、ti元素满足目标成分要求,精炼结束后喂mg-al合金或ni-mg合金用于保证钢中mg含量;
25.(2)浇铸:控制铸坯厚度为70~110mm,拉速为4.5~6m/min;
26.(3)铸坯除鳞:控制除鳞压力为15~30mpa;
27.(4)粗轧:控制粗轧总压下率为75~85%,中间坯厚度为15~25mm;
28.(5)中间坯加热:控制中间坯加热温度为1150~1210℃;
29.(6)精轧:控制精轧除鳞压力为25~35mpa;f1压下率为55~65%、f2压下率为45~55%,f3压下率为35~45%,精轧过程中需投入润滑轧制,终轧温度为840~880℃;
30.(7)层流冷却:采用两段式动态冷却;
31.(8)卷取:控制卷取温度为680~740℃/s;
32.(9)酸洗去除表面氧化铁皮。
33.优选的,所述第一生产方法的步骤(6)中,两段式动态冷却具体为:计算ti
有效
=ti-3*s-3.42*n,
34.当0.017%≤ti
有效
≤0.03%时,以15~25℃/s冷速冷却至740~760℃,空冷时间为1~3s,随后以10~15℃/s冷却至卷取温度;
35.当0.03%<ti
有效
≤0.05%时,以15~25℃/s冷速冷却至761~780℃,空冷时间为1~3s,随后以10~15℃/s冷却至卷取温度;
36.当0.05%<ti
有效
≤0.07%时,以15~25℃/s冷速冷却至781~800℃,空冷时间为1~3s,随后以10~15℃/s冷却至卷取温度;
37.上下表面水比为0.7~0.9。
38.优选的,所述第二生产方法的步骤(7)中,两段式动态冷却具体为:计算ti
有效
=ti-3*s-3.42*n,
39.当0.017%≤ti
有效
≤0.03%时,以15~25℃/s冷速冷却至740~760℃,空冷时间为1~3s,随后以10~15℃/s冷却至卷取温度;
40.当0.03%<ti
有效
≤0.05%时,以15~25℃/s冷速冷却至761~780℃,空冷时间为1~3s,随后以10~15℃/s冷却至卷取温度;
41.当0.05%<ti
有效
≤0.07%时,以15~25℃/s冷速冷却至781~800℃,空冷时间为1~3s,随后以10~15℃/s冷却至卷取温度;
42.上下表面水比为0.7~0.9。
43.本发明中,lf-rh双联精炼工艺指精炼工艺包括lf和rh,且生产顺序为先lf、后rh。
44.上下表面水比指带钢上下表面水的流量之比。
45.本发明搪瓷钢的生产方法有两种,可根据产线装备和布置方式是选择第一生产方法或第二生产方法。
46.本发明的高表面高精度的高强搪瓷钢基于如下理由选择合金种类及其含量:
47.c:固溶c会使钢的屈服强度和抗拉强度提高,与ti结合形成tic作为有效氢陷阱,提高搪瓷钢的抗鳞爆性能。但碳含量提高,塑性会下降,同时固溶c对搪瓷钢的涂搪性能不利,一方面,碳含量越高,珠光体含量越高,珠光体是铁素体和片层渗碳体两相组织,渗碳体与搪层不发生反应,使基体与搪层的结合力降低;另一方面,固溶碳含量越高,在烧搪过程中产生的co、co2气体越多,这些气体破坏搪层的致密性,严重时将产生针孔缺陷。此外,c含量超过0.07%时进入包晶钢范围,浇铸过程中易产生裂纹,严重时甚至漏钢。为平衡力学性能、涂搪性能和易浇铸性,本发明控制钢中c含量为0.04~0.07%。
48.si:搪瓷粉的主要成分是sio2,在烧搪过程中,基体氧化形成的feo和搪层中的sio2结合生成fe2sio4,形成化学键力,这种化学健力是基体与搪层密着的主要机理之一。钢中si会形成sio2,使基体与搪层的化学反应变慢,对基体与搪层的密着性不利。但是,si含量过低时,轧制过程中氧化铁皮生长速度过快,铁皮氧化应力和热应力较大,铁皮易鼓泡、粉碎,压入钢基造成麻点缺陷。综合考虑,si重量百分含量控制为0.05~0.1%。
49.mn:mn固溶于铁素体和奥氏体中,可提高强度,并使塑性下降,而锰含量过低会导致fes析出,降低钢的热塑性,综合考虑,mn重量百分含量控制为0.8~1.2%。
50.ti:ti可与钢中的c、n、s等元素化合形成细小的第二相粒子,成为良好的储氢陷
阱,提高钢板的抗鳞爆性能,但ti含量过高会提高材料的强度、降低材料的塑性,使材料成型和加工性能变差。综合考虑,ti重量百分含量控制为0.04~0.08%。
51.n:n元素会消耗ti,使更细小、弥散的tic生成数量变少,不利于提高钢板的抗鳞爆性能和强度,同时,钢中n元素的变化会显影响强度、延伸率等性能指标,因此n含量控制为≤0.004%。
52.p是钢中有害的杂质元素,钢中p易在钢中形成偏析,降低钢的韧性和焊接性能,故p含量越低越好,综合考虑,p含量≤0.015%。
53.s:当钢中s含量高时,tic析出数量会减少,不利于提高材料的强度。同时,钢中s元素的变化会显影响强度、延伸率等性能指标,因此s含量控制为≤0.003%。
54.mg:目前炼钢采用al作为主要脱氧元素,铝脱氧后形成尺寸较大的al2o3,这种夹杂物储氢作用较差。采用mg脱氧时,mgo与铁液有较小的润湿性,不易碰撞和凝聚长大,弥散分布的mgo具有良好的储氢性能,提高钢板的抗鳞爆性能。mg会优先形成尺寸较大的铝镁尖晶石夹杂物,需超过一定量后才会形成细小弥散的mgo。由于镁的蒸汽压较大,镁含量过高时,炼钢时易喷溅、爆炸,安全性较差,综合考虑,钢中mg含量控制为0.001~0.004%。
55.本发明一种高表面高精度的高强搪瓷钢及生产方法,技术上存在以下特点:
56.通过对n、s等显著影响有效ti含量、造成性能波动的元素进行限制,同时结合两段式动态冷却工艺,使不同成分下tic析出物数量和尺寸控制稳定,实现高ti钢屈服强度的波动范围控制在50mpa以内,抗拉强度的波动范围控制在70mpa以内。此外,通过控制上下表面水比,使上下表面应力均匀,不平度≤8mm。
57.通过在钢中添加一定量的镁合金,使钢中mg含量为0.001~0.004%,形成尺寸0.1~3μm的细小弥散夹杂物,这些尺寸细小的夹杂物具有良好的储氢作用,避免烧搪冷却时钢中溶解的氢气溢出基体形成鳞爆。
58.通过除鳞压力为15~30mpa的铸坯除鳞,去除铸坯表面黏附的保护渣,避免保护渣中的碳扩散至基体中造成表面增碳,表面增碳会恶化钢基的涂搪性能。
59.通过添加0.05~0.1%si,加热和精轧过程中生成fesio4,抑制fe离子和o离子的扩散,降低氧化铁皮的生长速度,同时控制第一生产方法中浇铸的铸坯厚度为55~65mm、第二生产方法中粗轧的中间坯厚度为15~25mm,精轧过程中f1压下率为55~65%、f2压下率为45~55%、f3压下率为35~45%,控制轧制负荷向高温区前移、投入润滑油,降低轧制负荷,避免辊面剥落、氧化铁皮压入形成麻点缺陷。
60.通过控制卷取温度为680~740℃,使钢中的c以游离状渗碳体析出,避免形成片层珠光体,降低基体与搪层的密着性能。
61.本发明的两种生产方法均采用了两段式动态冷却,其优点为可稳定控制tic析出物数量和尺寸。
62.本发明具有以下有益效果:
63.(1)通过合理的成分设计和轧后两段式动态冷却,实现高ti钢中tic析出物数量和尺寸稳定控制,在保证屈服强度≥420mpa时,屈服强度波动范围≤50mpa,抗拉强度波动范围≤70mpa,结合薄板坯连铸连轧使厚度精度控制为
±
30μm,上下水比控制使不平度≤8mm,可满足高精度零件成形的要求。
64.(2)通过添加少量的si元素,降低氧化铁皮生长速度,采用薄板坯轧制、轧制负荷
前移、润滑轧制等技术措施,减少轧制负荷、减轻辊面磨损,避免氧化铁皮压入、轧辊剥落等造成表面麻点缺陷,实现薄规格高强搪瓷钢的批量稳定生产,厚度最薄可达0.8mm。
65.(3)通过采用mg脱氧,钛微合金化和轧后两段式冷却,使钢中形成大量细小、弥散的mgo和tis或ti4c2s2粒子,作为有效氢陷阱提高材料的抗鳞爆性能,实现抗鳞爆敏感性th值≥25min/mm2。
66.(4)通过高温卷取,使钢中的c以游离状渗碳体析出,避免形成片层珠光体损害基体与搪层的密着性能,实现搪层与基体的密着性达到1级。
附图说明
67.图1为本发明实施例制得高强搪瓷钢的显微组织
具体实施方式
68.下面具体实施例对本发明作进一步的详细说明。
69.本发明的高表面高精度的高强搪瓷钢,包括以下按重量百分比的化学成分:c:0.04~0.07%,si:0.05~0.1%,mn:0.8~1.2%,ti:0.04~0.08%,n≤0.004%,p≤0.015%,s≤0.003%,mg:0.001~0.004%,余量为fe及不可避免的杂质。
70.本发明的高表面高精度的高强搪瓷钢的制备方法,可根据产线设置选择第一生产方法或第二生产方法,
71.第一生产方法具体为:
72.(1)精炼:将c、si含量符合目标要求的钢水采用lf-rh双联精炼工艺,精炼过程中控制s、n、p元素含量,并添加锰合金和钛合金,确保mn、ti元素满足目标成分要求,精炼结束后喂mg-al合金或ni-mg合金,喂线前开始软吹,使钢水循环流动、钢包中心渣面被吹开,从裸漏钢液处加入镁合金,镁合金添加量为保证钢中mg含量为0.001~0.004%;
73.(2)浇铸:控制铸坯厚度为55~65mm,拉速为3.8~5.5m/min;
74.(3)铸坯除鳞:控制除鳞压力为15~30mpa;
75.(4)铸坯加热:控制铸坯加热温度为1130~1180℃;
76.(5)精轧:控制精轧除鳞压力为20~35mpa,f1压下率为55~65%、f2压下率为45~55%、f3压下率为35~45%,精轧过程中需投入润滑轧制,终轧温度为840~880℃;
77.(6)层流冷却:采用两段式动态冷却,计算ti
有效
=ti-3*s-3.42*n,式中ti、s、n表示各元素的质量百分含量(wt%)
78.当0.017%≤ti
有效
≤0.03%时,以15~25℃/s冷速冷却至740~760℃,空冷时间为1~3s,随后以10~15℃/s冷却至卷取温度;
79.当0.03%<ti
有效
≤0.05%时,以15~25℃/s冷速冷却至761~780℃,空冷时间为1~3s,随后以10~15℃/s冷却至卷取温度;
80.当0.05%<ti
有效
≤0.07%时,以15~25℃/s冷速冷却至781~800℃,空冷时间为1~3s,随后以10~15℃/s冷却至卷取温度;
81.上下表面水比为0.7~0.9;
82.(7)卷取:卷取温度为680~740℃/s;
83.(8)酸洗去除表面氧化铁皮。
84.第二生产方法具体为:
85.(1)精炼:将c、si含量符合目标要求的钢水采用lf、rh双联工艺,精炼过程中控制s、n、p元素含量,并添加锰合金和钛合金,确保mn、ti元素满足目标成分要求,精炼结束后喂mg-al合金或ni-mg合金,喂线前开始软吹,使钢水循环流动、钢包中心渣面被吹开,从裸漏钢液处加入镁合金,镁合金添加量为保证钢中mg含量为0.001~0.004%;
86.(2)浇铸:控制铸坯厚度为70~110mm,拉速为4.5~6m/min;
87.(3)铸坯除鳞:控制除鳞压力为15~30mpa;
88.(4)粗轧:控制粗轧总压下率为75~85%,中间坯厚度为15~25mm;
89.(5)中间坯加热:控制中间坯加热温度为1150~1210℃;
90.(6)精轧:控制精轧除鳞压力为25~35mpa;f1压下率为55~65%、f2压下率为45~55%,f3压下率为35~45%,精轧过程中需投入润滑轧制,终轧温度为840~880℃;
91.(7)层流冷却:采用两段式动态冷却,计算ti
有效
=ti-3*s-3.42*n
92.当0.017%≤ti
有效
≤0.03%时,以15~25℃/s冷速冷却至740~760℃,空冷时间为1~3s,随后以10~15℃/s冷却至卷取温度;
93.当0.03%<ti
有效
≤0.05%时,以15~25℃/s冷速冷却至761~780℃,空冷时间为1~3s,随后以10~15℃/s冷却至卷取温度;
94.当0.05%<ti
有效
≤0.07%时,以15~25℃/s冷速冷却至781~800℃,空冷时间为1~3s,随后以10~15℃/s冷却至卷取温度;
95.上下表面水比为0.7~0.9;
96.(8)卷取:卷取温度为680~740℃/s;
97.(9)酸洗:采用常规酸洗工艺去除表面氧化铁皮。
98.实施例1-10的化学成分如下表1所示。
99.表1实施例1-10的化学成分(wt%)
[0100] csimntinpsmgti
有效
实施例10.0580.0941.010.0800.00340.0110.0020.00170.062实施例20.050.100.940.0470.00310.0130.00070.00130.034实施例30.0630.0860.800.0470.00260.0060.00150.00220.034实施例40.0490.0711.200.0720.0020.0110.00030.00220.064实施例50.040.051.10.0650.00350.0090.00250.00380.046实施例60.0460.07810.0520.00400.00820.00300.00310.029实施例70.0410.0501.020.0680.00240.00890.00040.0010.059实施例80.0540.0660.990.0510.00230.0150.00080.0040.041实施例90.0700.0861.050.0560.00290.00510.00060.00260.044实施例100.0450.061.120.0760.00380.00940.0030.00320.054
[0101]
实施例1-5的搪瓷钢制备均采用第一生产方法,生产工艺参数如下表2-3所示。
[0102]
表2实施例1-5生产工艺参数(浇铸至精轧)
[0103][0104]
表3实施例1-5生产工艺参数(精轧至卷取)
[0105][0106]
实施例6-10的搪瓷钢制备均采用第二生产方法,生产工艺参数如下表4-5所示。
[0107]
表4实施例6-10生产工艺参数(浇铸至精轧)
[0108][0109]
表5实施例6-10生产工艺参数(精轧至卷取)
[0110][0111]
实施例1-10生产钢材典型性能指标如下表6所示。
[0112]
表6实施例1-10生产钢材的典型性能指标
[0113][0114]
从表6可以看出,本发明制得的搪瓷钢强度、伸长率、抗鳞爆敏感性th值和密着等级各性能指标良好,因此本发明产品具有高强度、高塑性、强度稳定以及良好的抗鳞爆性能和密着性能的优点。本发明实施例制得高强搪瓷钢的显微组织如图1所示,从图1可以看出,本发明的产品具有组织均匀、细小弥散的优点。
再多了解一些
本文用于创业者技术爱好者查询,仅供学习研究,如用于商业用途,请联系技术所有人。