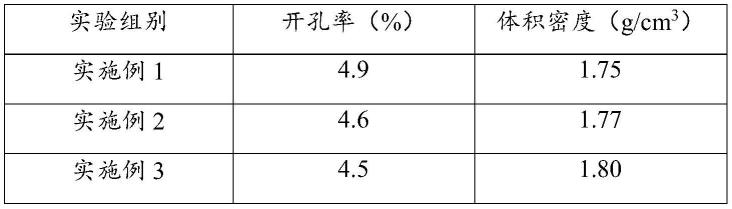
c/c复合材料及其制备方法、刹车片和偏航制动器
技术领域
1.本发明涉及复合材料技术领域,尤其是涉及一种c/c复合材料及其制备方法、刹车片和偏航制动器。
背景技术:
2.c/c复合材料是一种由碳纤维和碳基体复合而成的新型复合材料,c/c复合材料强度高,在超高温环境下能保持高强度,并具有良好的烧蚀性能,因而在航空航天、医疗、汽车、船舶等领域得到重要应用。但是现有的c/c复合材料密度低,抗高负载能力差,尤其是作为风力发电机组不同工况下滑动摩擦摩擦片(用于制动阻尼摩擦片)、滑动衬垫(用于滑动轴承)使用时,无法满足适配性能、摩擦学性能,无法满足风力发电偏航制动系统对于制动阻尼摩擦片或滑动轴承的使用要求。
3.有鉴于此,特提出本发明。
技术实现要素:
4.本发明的目的之一在于提供一种c/c复合材料,以改善现有的c/c复合材料密度低,在高负载工况下耐磨擦能力差,无法满足风力发电偏航制动系统的技术问题。
5.本发明提供的c/c复合材料,所述c/c复合材料的密度为1.7-2.1g/cm3,磨擦系数为0.04-0.4,其在50mpa压力下的磨耗≤0.0060mm/h,优选≤0.0033mm/h。
6.本发明的目的之二在于c/c复合材料的制备方法,按照以下步骤进行:
7.(a)将三维碳纤维预制体采用气相沉积和/或液相浸渍进行增密处理,得到c/c多孔预制体;
8.(b)将c/c多孔预制体进行炭化处理和石墨化处理,得到c/c复合材料;
9.其中,所述c/c复合材料的磨擦系数为0.04-0.4,密度为1.7-2.1g/cm3,动荷载为130-180mpa,静荷载为240-280mpa,其在50mpa压力下的磨耗≤0.0060mm/h,优选≤0.0033mm/h。
10.进一步的,炭化处理的温度为650-1000℃,炭化时间为900-1500h;
11.优选地,石墨化处理的温度为2300-2800℃,石墨化处理的时间为2-4h。
12.进一步的,炭化处理包括第一炭化阶段、第二炭化阶段和第三炭化阶段,其中,其一炭化阶段,从室温升温至650℃,升温速度为9-11℃/h,升温至650℃保温680-720h;
13.优选地,第二炭化阶段,从650℃升温至850℃,升温速度为9-11℃/h,升温至850℃保温80-120h;
14.优选地,第三炭化阶段,从850℃升温至900℃,升温速度为9-11℃/h,升温至900℃保温80-120h。
15.进一步的,炭化处理还包括第四炭化阶段,所述第四炭化阶段从900℃升温至1000℃,升温速度为9-11℃/h,升温至1000℃保温80-120h。
16.进一步的,从炭化温度升温至石墨化温度的升温速度为10-30℃/h,温升时间为
40-200h。
17.进一步的,三维碳纤维预制体的密度为0.3-0.4g/cm3;
18.优选地,所述三维碳纤维预制体主要由碳纤维编织而成,所述碳纤维包括t700、t800或t900中的至少一种。
19.进一步的,步骤(a)中,采用液相浸渍方式制备c/c多孔预制体时,采用的液相树脂包括糖醛树脂、酚醛树脂或呋喃树脂中的至少一种;
20.优选地,液相树脂的质量浓度为50%-80%;
21.优选地,液相浸渍在真空加压下进行,压力为3-5mpa。
22.本发明目的之三在于提供一种刹车片,主要由本发明目的之一提供的c/c复合材料或按照本发明目的之二提供的c/c复合材料的制备方法制备得到的c/c复合材料制备得到。
23.本发明提供的c/c复合材料密度为1.7-2.1g/cm3,磨擦系数为0.04-0.4,其在50mpa压力下的磨耗≤0.0060mm/h,甚至≤0.0033mm/h,其密度高,在高负载工况下耐磨擦能力强,能够有效满足风力偏航制动系统的要求。
24.本发明提供的c/c复合材料的制备方法,采用气相沉积或液相浸渍三维碳纤维预制体的方式制备得到c/c多孔预制体,将多孔预制体进行炭化处理和石墨化处理,制备得到密度为1.7-2.1g/cm3,磨擦系数为0.04-0.4,其在50mpa压力下的磨耗≤0.0060mm/h,甚至≤0.0033mm/h,其密度高,在高负载工况下耐磨擦能力强,能够有效满足风力偏航制动系统的要求。
具体实施方式
25.下面将结合实施例对本发明的技术方案进行清楚、完整地描述,显然,所描述的实施例是本发明一部分实施例,而不是全部的实施例。基于本发明中的实施例,本领域普通技术人员在没有做出创造性劳动前提下所获得的所有其他实施例,都属于本发明保护的范围。
26.根据本发明的第一个方面,本发明提供了一种c/c复合材料,所述/c复合材料的磨擦系数为0.04-0.4,密度为1.7-2.1g/cm3,动荷载为130-180mpa,静荷载为240-280mpa,其在50mpa压力下的磨耗≤0.0060mm/h,甚至≤0.0033mm/h。
27.典型但非限制性的,本发明提供的c/c复合材料的磨擦系数如为0.04、0.06、0.08、0.1、0.12、0.15、0.2、0.22、0.25、0.28、0.3、0.32、0.35、0.38或0.4,密度如为1.7g/cm3、1.8g/cm3、1.9g/cm3、2.0g/cm3或2.1g/cm3,动荷载如为130mpa、140mpa、150mpa、160mpa、170mpa或180mpa,静荷载如为240mpa、250mpa、260mpa、270mpa或280mpa,其在50mpa压力下磨耗如为0.0030mm/h、0.0031mm/h、0.0033mm/h、0.0034mm/h、0.0035mm/h、0.0036mm/h、0.0040mm/h、0.0042mm/h或0.0060mm/h。
28.本发明提供的c/c复合材料密度高达1.7-2.1g/cm3,磨擦系数为0.04-0.4,其在50mpa压力下的磨耗≤0.0060mm/h,甚至≤0.0033mm/h,高负载工况下耐磨擦能力强,适配性良好,能够有效满足风力偏航制动系统的技术要求。
29.根据本发明的第二个方面,本发明提供了一种c/c复合材料的制备方法,按照以下步骤进行:
30.(a)将三维碳纤维预制体采用气相沉积和/或液相浸渍的方式制备得到c/c多孔预制体;
31.(b)将c/c多孔预制体进行炭化处理和石墨化处理,得到c/c复合材料;
32.其中,所述c/c复合材料的磨擦系数为0.04-0.4,密度为1.7-2.1g/cm3,动荷载为130-180mpa,静荷载为240-280mpa,其在50mpa压力下的磨耗≤0.0060mm/h,优选≤0.0033mm/h。
33.在本发明中,制备c/c多孔预制体包括三种方式,第一种方式为气相沉积法,第二种方式为液相浸渍法,第三种方式为气相沉积法与液相浸渍相结合的方式进行增密。
34.在本发明中,气相沉积、液相浸渍、炭化处理和石墨化处理可各自独立的多次进行以使得制备得到的c/c复合材料的密度达到1.7-2.1g/cm3。
35.[气相沉积]
[0036]
气相沉积是把易挥发的低分子碳氢化合物通过热解沉积在热的基体表面孔隙中,以达到增密的目的。
[0037]
在本发明的一种方案中,采用丙烷为热解气体,氮气为载气,丙烷和氮气的流量比为(0.5-1.5):1,优选为1:1。
[0038]
典型但非限制性的,丙烷和氮气的流量比如为0.5:1、1:1或1.5:1。
[0039]
优选地,氮气的流量为0.5-1.5m3/h,优选为1m3/h。
[0040]
典型但非限制性的,氮气的流量如为0.5、0.8、1、1.2或1.5m3/h。
[0041]
优选地,进行气相沉积的温度为900-1100℃,压力为0.3-10kpa时,更利于在三维碳纤维预制体的骨架内部沉积基体碳,提高增密效率。
[0042]
典型但非限制性的,气相沉积的温度如为900℃、950℃、1000℃、1050或1100℃,压力如为0.3kpa、0.5kpa、0.8kpa、1kpa、1.5kpa、2kpa、2.5kpa、3kpa、5kpa、8kpa或10kpa。
[0043]
气相沉积处理后的c/c多孔预制体可以直接进行石墨化处理,得到c/c复合材料,但是这种方式得到的c/c复合材料的密度时间较长,效率偏低,需满足批次性、大数量、高时效、高工业化效率要求,难以满足风力发电机组偏航制动系统的多样性、高时效要求,因此,在本发明的一些实施例中,将气相沉积处理后的c/c多孔预制体结合液相浸渍相工艺,通过液相浸渍的方式进一步达到增密的目的,然后再采用特定的炭化处理和石墨化处理,制备得到密度高,耐磨擦能力强的c/c复合材料。
[0044]
[液相浸渍]
[0045]
液相浸渍是将三维碳纤维预制体置于浸渍罐中,使得树脂渗入到三维碳纤维预制体的孔隙,然后将浸渍树脂的三维碳纤维预制体取出进行固化处理,抑制树脂从三维碳纤维预制体中流出,再将固化后得到的c/c多孔预制体进行炭化处理和石墨化处理。
[0046]
三维碳纤维预制体可以单独采用液相浸渍的方式进行增密处理,也可以将气相沉积后得到的三维多孔预制体再进行液相浸渍处理来达到增密的目的。
[0047]
在本发明的一种优选方案中,为了加快树脂渗入到三维碳纤维预制体孔隙的效率,可在真空加压下处理。
[0048]
优选地,真空加压的压力为3-5mpa,温度为45-55℃,更能够有效保证树脂渗入三维碳纤维预制体的孔隙。
[0049]
典型但非限制性的,进行浸渍处理时的温度如为45℃、50℃或55℃,压力如为
3mpa、3.2mpa、3.5mpa、4mpa、4.2mpa、4.5mpa、4.8mpa或5mpa。
[0050]
在本发明的一种优选方式中,为了加快浸渍树脂的三维碳纤维预制体的固化进程,可采用真空加压加温固化。
[0051]
优选地,固化时的压力为0.8-1.2mpa,温度为250-350℃,以加快固化进程,将固化时间缩短至2.5h内。
[0052]
典型但非限制性的,固化时的压力如为0.8mpa、0.9mpa、1mpa、1.1mpa或1.2mpa,温度如为250℃、260℃、270℃、280℃、290℃、300℃、310℃、320℃、330℃、340℃或350℃。
[0053]
在本发明的一种优选方案中,浸渍三维碳纤维预制体或气相沉积后的c/c多孔预制体采用的液相树脂选自糖醛树脂、酚醛树脂或呋喃树脂中的一种或几种。
[0054]
在本发明的一种优选方案中,为了便于树脂浸渍进入三维碳纤维预制体或c/c多孔预制体内部的孔隙,需要控制液相树脂的浓度在合适的范围。
[0055]
优选地,液相树脂的质量浓度为50%-80%,以保证液相树脂具备优异流动性能能够渗入三维碳纤维预制体或c/c多孔预制体内部的孔隙的同时,又具备适宜的粘度,能够更多的保留在三维碳纤维预制体或c/c多孔预制体内部的孔隙中。
[0056]
典型但非限制性的,液相树脂的质量浓度为50%、55%、60%、65%、70%、75%或80%。
[0057]
在本发明的优选方案中,液相浸渍可多次进行,以利于更好的增密。
[0058]
[三维碳纤维预制体]
[0059]
在本发明中,三维碳纤维预制体由碳纤维制备而成。
[0060]
在本发明的一种优选方案中,三维碳纤维预制体的密度为0.3-0.4g/cm3,以利于后续通过增密处理,得到密度高,耐磨性能强的c/c复合材料。
[0061]
典型但非限制性的,三维碳纤维预制体的密度如为0.3、0.32、0.35、0.38或0.4g/cm3。
[0062]
在本发明的一种优选方案中,制备三维碳纤维预制体的碳纤维选自t700、t800或t900中的一种或几种,优选为t800。
[0063]
优选地,三维碳纤维预制体以或碳毡为胎体,采用t800单丝进行编织而成。
[0064]
[炭化处理]
[0065]
在本发明的一种优选方案中,炭化处理的温度为650-1000℃,炭化时间为900-1500h,以使得c/c多孔预制体炭化的更加完全,炭化处理初期-后期c/c多孔预制体随炭化时间推进,外部(表面或次表面)孔隙率高于内部,内部密度低,孔隙率降低,为更好的使c/c多孔预制体内、外部密度均匀,可通过阶梯式增温加压(有利于开通空隙)方式进行,从而使c/c预制体密度由内而外逐步增加,增密均匀、效果佳。
[0066]
典型但非限制性的,炭化处理的温度如为650℃、700℃、750℃、800℃、850℃、900℃、950℃、或1000℃,炭化时间如为900h、950h、1000h、1050h、1100h、1150h、1200h、1250h、1300h、1400h或1500h。
[0067]
在本发明的一种优选方案中,炭化处理包括至少三个炭化阶段,分别为第一炭化阶段、第二炭化阶段和第三炭化阶段,以通过梯度升高炭化温度的方式进一步提高增密效果。
[0068]
优选地,在第一炭化阶段,将c/c多孔预制体放入炭化炉中,将温度从室温升温至650℃,控制升温速度为9-11℃/h,以使得炭化进行的更均匀,各部分炭化的更完全,孔洞也更均匀,尤其是以控制升温速度为10℃/h,炭化均匀度更佳。当升温至650℃后保温680-720h,以进一步提高炭化效果。
[0069]
需要说明的是,第一炭化阶段中,在650℃进行保温处理,该温度如存在仪器误差,则在仪器误差范围内如650
±
10℃也属于本发明的保护范围。
[0070]
典型但非限制性的,第一炭化阶段在650℃保温的时间如为680h、690h、700h、710h或720h,升温速度如为9℃/h、9.5℃/h、10℃/h、10.5℃/h或11℃/h。
[0071]
如升温速度低于9℃/h,则炭化处理时间过长,不利于提高炭化效率,如升温速度高于11℃/h,则温升速度过快,不利于生成孔洞均匀致密的碳化物。
[0072]
优选地,在第二炭化阶段,从650℃升温至850℃,升温速度为9-11℃/h,升温至850℃保温80-120h。通过控制升温速度为9-11℃/h,以保证炭化过程的均匀稳定性,进一步提高样品各位置增密效果的均匀性,从而进一步保证c/c复合材料各部位具备稳定均匀的密度。
[0073]
典型但非限制性的,在第二炭化阶段中,在850℃保温的时间如为80h、85h、90h、95h、100h、105h、110h、115h或120h,升温速度如为9℃/h、9.5℃/h、10℃/h、10.5℃/h或11℃/h。
[0074]
关于温升速度的说明如前所述,在此不再赘述。
[0075]
优选地,在第三炭化阶段,从850℃升温至900℃,升温速度为9-11℃/h,升温至900℃保温80-120h,以保证炭化进行的更均匀,得到的炭化物更为致密。
[0076]
典型但非限制性的,在第三炭化阶段中,在900℃保温的时间如为80h、85h、90h、95h、100h、105h、110h、115h或120h,升温速度如为9℃/h、9.5℃/h、10℃/h、10.5℃/h或11℃/h。
[0077]
关于温升速度的说明如前所述,在此不再赘述。
[0078]
在本发明的一种优选方式中,炭化处理还包括第四炭化阶段,该第四炭化阶段从900℃升温至1000℃,升温速度为9-11℃/h,升温至1000℃保温80-120h,以进一步提高炭化效果,提高炭化产物的致密性。
[0079]
典型但非限制性的,在第四炭化阶段中,在1000℃保温的时间如为80h、85h、90h、95h、100h、105h、110h、115h或120h,升温速度如为9℃/h、9.5℃/h、10℃/h、10.5℃/h或11℃/h。
[0080]
关于温升速度的说明如前所述,在此不再赘述。
[0081]
优选地,炭化处理还可以包括第五炭化阶段,所述第五炭化阶段从1000℃升温至1100℃,升温速度为9-11℃/h,升温至1100℃保温80-120h,以进一步提高炭化效果,提高炭化产物的致密性。
[0082]
典型但非限制性的,在第五炭化阶段中,在1100℃保温的时间如为80h、85h、90h、95h、100h、105h、110h、115h或120h,升温速度如为9℃/h、9.5℃/h、10℃/h、10.5℃/h或11℃/h。
[0083]
关于温升速度的说明如前所述,在此不再赘述。
[0084]
[石墨化处理]
[0085]
通过将炭化产物进行石墨化处理,使得六角碳原子平面网络从二维空间的无序重迭转变为三维空间的有效重迭,从而提高材料的热传导性、电传导性、热稳定性、化学稳定性、耐磨擦性以及提高纯度,降低硬度。
[0086]
在本发明的一种优选方案中,石墨化处理的温度为2300-2800℃,石墨化处理的时间为2-4h,以利于将炭化产物完全石墨化,尤其是当是石墨化温度为2500℃,生成的c/c复合材料的密度更高,耐热性更佳。但石墨化温度过高一方面会造成能源的浪费,另一方面也会造成石墨化度过高,影响材料的强度性能,因此优选石墨化处理的温度为2300-2800℃。
[0087]
典型但非限制性的,石墨化处理的温度如为2300℃、2400℃、2500℃、2600℃、2700℃或2800℃,石墨化处理的时间如为2h、2.5h、3h、3.5h或4h。
[0088]
优选地,从炭化温度升温至石墨化温度的升温速度为10-30℃/h,温升时间为40-200h,以避免温升速度过快影响生成的c/c复合材料的致密度。
[0089]
典型但非限制性的,从炭化温度升温至石墨化温度的升温速度如为10℃/h、12℃/h、15℃/h、18℃/h、20℃/h、22℃/h、25℃/h、28℃/h或30℃/h,温升时间如为40h、50h、80h、100h、120h、150h、180h或200h。
[0090]
需要说明的是,液相浸渍—炭化处理—石墨化处理可以多次循环进行,以使得生成的c/c复合材料的密度达到1.7-2.1g/cm3,同时具有优异的耐磨擦能力。
[0091]
根据本发明的第三个方面,本发明提供了一种刹车片,主要由本发明第一个方面提供的c/c复合材料或按照本发明第二个方面提供的c/c复合材料的制备方法得到的c/c复合材料制备得到。
[0092]
根据本发明的第四个方面,本发明提供了一种偏航制动器,包括本发明第三个方面提供的刹车片。
[0093]
为了便于本领域技术人员理解本发明的技术方案,下面结合实施例和对比例对本发明提供的技术方案做进一步的描述。
[0094]
实施例1
[0095]
本实施例提供了一种c/c复合材料,其按照如下步骤制备得到:
[0096]
(1)选择t800碳纤维通过三维针刺工艺制成的碳毡,碳毡的密度为0.4g/cm3;
[0097]
(2)将碳毡放入盛满酚醛树脂溶液的浸渍罐中,酚醛树脂溶液的质量浓度为80%,在4mpa,50℃下进行真空浸渍,浸渍后,将样品放入固化罐中,在1mpa,300℃进行固化处理2h;
[0098]
(3)将固化后的样品放入炭化炉中,先将温度从室温升温至650℃,升温速度为10℃/h,升温至650℃后保温700h,然后继续升温至850℃,升温速度为10℃/h,升温至850后保温100h,再升温至900℃,升温速度为10℃/h,升温至900℃后保温100h,结束炭化处理。
[0099]
(4)将炭化结束后的样品升温至2500℃进行石墨化处理,升温速度为10℃/h,升温至2500℃后保温2h,冷却后,得到c/c复合材料。
[0100]
实施例2
[0101]
本实施例提供了一种c/c复合材料,其与实施例1不同之处在于,在步骤(3)中,在升温900℃保温100h后,继续升温至1000℃,升温速度为10℃/h,升温至1000℃后保温100h,再结束炭化处理。其余步骤均同实施例1,在此不再赘述。
[0102]
实施例3
[0103]
本实施例提供了一种c/c复合材料,其与实施例2不同之处在于,在步骤(3)中,在升温1000℃保温100h后,继续升温至1100℃,升温速度为10℃/h,升温至1100℃后保温100h,再结束炭化处理。其余步骤均同实施例1,在此不再赘述。
[0104]
实施例4
[0105]
本实施例提供了一种c/c复合材料,其与实施例1的不同之处在于,在步骤(4)中,石墨化温度为2300℃。
[0106]
实施例5
[0107]
本实施例提供了一种c/c复合材料,其与实施例1的不同之处在于,在步骤(4)中,石墨化温度为2800℃。
[0108]
实施例6
[0109]
本实施例提供了一种c/c复合材料,其与实施例1的不同之处在于,在步骤(1)中,碳毡的密度为0.3g/cm3,且在步骤(4)中石墨化结束后,继续返回步骤(2)循环进行液相浸渍-炭化和石墨化处理,共计循环3次后,得到c/c复合材料。
[0110]
实施例7
[0111]
本实施例提供了一种c/c复合材料,其与实施例1的不同之处在于,在步骤(4)中,从炭化温度升温至石墨化温度的温升速度为30℃/h。
[0112]
实施例8
[0113]
本实施例提供了一种c/c复合材料,其与实施例1的不同之处在于,在步骤(3)中,三个升温阶段中,升温速率均为50℃/h。
[0114]
实施例9
[0115]
本实施例提供了一种c/c复合材料,其与实施例1的不同之处在于,在步骤(4)中,从炭化温度升温至石墨化温度的温升速度为50℃/h。
[0116]
实施例10
[0117]
本实施例提供了一种c/c复合材料,其与实施例1的不同之处在于,在步骤(3)中,将温度从室温直接升温至900℃,升温速度为10℃/h,保温900h,结束炭化处理。
[0118]
实施例11
[0119]
本实施例提供了一种c/c复合材料,其与实施例1的不同之处在于,在步骤(3)中,将温度从室温直接升温850℃,升温速度为10℃/h,保温800h,再升温至900℃,升温速度10℃/h,保温100h,结束炭化处理。
[0120]
实施例12
[0121]
本实施例提供了一种c/c复合材料,其与实施例1的不同之处在于,在步骤(3)中,将温度从室温升温至650℃,升温速度为10℃/h,保温700h,再升温至900℃,升温速度10℃/h,保温200h,结束炭化处理。
[0122]
试验例1
[0123]
按照jb/t8133.15-2003测定实施例1-12提供的c/c复合材料的开孔率和体积密度,结果如下表1所示。
[0124]
表1
[0125][0126][0127]
从表1可以看出,采用梯度升温制备得到的c/c复合材料的体积密度更大,开孔率更低,致密度更高。这说明通过控制升温速度可以进一步提高材料的致密度,石墨化温度对于开孔率以及体积密度的影响并不明显,在石墨化过程中,有些闭孔会打开,使得致密度进一步增加,体积密度稍有增大。
[0128]
试验例2
[0129]
依照gb/t 11834-2011和nb/t 31144-2018分别测定实施例1-12提供的c/c复合材料的静摩擦系数、动摩擦系数、垂直压缩强度、平行压缩强度以及在50mpa压力下的磨耗,结果如下表2所示。
[0130]
表2
[0131]
[0132][0133]
从表2可以看出,本发明提供的c/c复合材料的制备方法,采用气相液相浸渍三维碳纤维预制体的方式制备得到c/c多孔预制体,将多孔预制体进行炭化处理和石墨化处理,制备得到的c/c复合材料密度为1.7-2.1g/cm3,磨擦系数为0.04-0.4,其在50mpa压力下的磨耗≤0.0060mm/h,甚至通过控制炭化参数以及石墨化参数达到≤0.0033mm/h,在高负载工况下具有优异的耐磨擦能力,能够有效满足风力偏航制动系统的要求。
[0134]
最后应说明的是:以上各实施例仅用以说明本发明的技术方案,而非对其限制;尽管参照前述各实施例对本发明进行了详细的说明,本领域的普通技术人员应当理解:其依然可以对前述各实施例所记载的技术方案进行修改,或者对其中部分或者全部技术特征进行等同替换;而这些修改或者替换,并不使相应技术方案的本质脱离本发明各实施例技术方案的范围。
再多了解一些
本文用于创业者技术爱好者查询,仅供学习研究,如用于商业用途,请联系技术所有人。