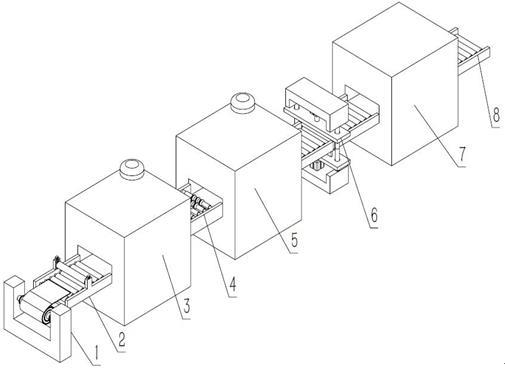
1.本发明涉及钢材成型加工技术领域,尤其是涉及一种热成型加工工艺。
背景技术:
2.现有的钢材成型加工工艺在生产高速路护板和角钢时采用传统熔铸工艺,即采用将铁矿石融化灌注入特定模具中铸造成型的方法,这种传统的熔铸工艺生产能耗高,成品强度低重量大,并且熔铸工艺会产生大量污染物,不符合现代钢材成型加工工艺轻量化无污染化的要求。
技术实现要素:
3.针对现有技术存在的不足,本发明的目的是提供一种热成型加工工艺,通过加热设备将22mnb5钢材加热至850℃~930℃使其形成奥氏体,通过滚压成型设备对其进行塑形,通过淬火冷却设备以50~100℃/s的冷却速度进行淬火使其形成马氏体,使得成品强度达到1500mpa~1600mpa,维氏硬度达到400hv~510hv,可承受10~30吨(1000~3000n/mm2)的压力,摒弃传统铁矿石熔融铸造的方法采用钢卷料进行加热成型的方式,提高成品强度的同时降低了生产能耗,减少了污染物的排放。
4.上述发明是通过以下技术方案得以实现的:一种热成型加工工艺,其步骤包括: s1:将22mnb5钢卷材放置于上料机构内,通过上料机构将钢卷材输送到平整装置上进行挤压平整处理;s2:将平整处理后的钢卷通入加热设备内将钢材加热到850℃~930℃范围内使其形成奥氏体;s3:将加热后的钢材运输至滚压成型设备,使其根据实际需要塑形;s4:将塑形后的钢材运输至淬火冷却装置,以50~100℃/s的冷却速度进行淬火使其形成马氏体;s5:淬火冷却后的钢材通过输送机构传递至截料装置进行定长截取;s6:将定长截取后的钢材通过输送机构传输至后处理装置进行激光裁剪、毛刺处理,表面喷涂。
5.通过采用上述技术方案,所述加热设备将22mnb5钢材加热至850℃~930℃使得22mnb5钢材形成奥氏体,从而增加钢材的韧性,通过淬火冷却装置以50~100℃/s的冷却速度进行淬火使其形成马氏体,相对于传统熔铸成型加工工艺而言,通过热成型加工工艺钢材经过加热形成奥氏体和淬火冷却形成马氏体的过程,使得成品的韧性和强度均有所提高。
6.进一步的所述平整装置两侧设置有气缸,所述平整装置上方通过滑轨安装有压辊,所述滚压成型装置安装有5-10根成型辊,所述成型辊上设置有3个凸轮,可将所述成型辊替换为成角辊用于角钢成型加工,所述成角辊上设置有角轮,所述截料装置设置有上下两个液压缸,所述液压缸上安装有刀头。
7.通过采用上述技术方案,所述压辊的设置可平整钢卷料卷曲所产生的凸起,使得后续加热设备可对钢材进行充分均匀加热,使其良好的形成奥氏体,所述成型辊的设置使得钢材形成奥氏体之后对其进行塑形,所液压缸和所述刀头的设置可使得所述截料装置连续上下开合截取钢材,提高了热成型加工工艺的自动化程度。
8.综上所述,本发明具有以下有益效果:1. 所述加热设备将22mnb5钢材加热至850℃~930℃使得22mnb5钢材形成奥氏体,从而增加钢材的韧性,通过淬火冷却装置以50~100℃/s的冷却速度进行淬火使其形成马氏体,相对于传统熔铸成型加工工艺而言,通过热成型加工工艺钢材经过加热形成奥氏体和淬火冷却形成马氏体的过程,使得成品强度达到1500mpa~1600mpa,维氏硬度达到400hv~510hv,可承受10~30吨(1000~3000n/mm2)的压力,使得成品的韧性和强度均有所提高;2. 摒弃传统铁矿石熔融铸造的方法采用钢卷料进行加热成型的方式,提高成品强度和韧性的同时降低了生产能耗,减少了污染物的排放;3. 所述压辊的设置可平整钢卷料卷曲所产生的凸起,使得后续加热设备可对钢材进行充分均匀加热,使其良好的形成奥氏体,所述成型辊的设置使得钢材形成奥氏体之后对其进行塑形,所液压缸和所述刀头的设置可使得所述截料装置连续上下开合截取钢材,提高了热成型加工工艺的自动化程度。
附图说明
9.图1是本发明的工艺流水线结构示意图;图2是图1中平整设备的结构示意图;图3是图1中滚压成型设备的结构示意图;图4是图1中截料装置的结构示意图;图5是实施例三中成角辊的结构示意图;图6是实施例二中高速路护板的结构示意图。
10.图中,1、上料机构;2、平整装置;3、加热设备;4、滚压成型设备;5、淬火冷却装置;6、截料装置;7、后处理装置;8、输送装置;9、气缸;10、压辊;11、成型辊;12、凸轮;13、液压缸;14、刀头;15、成角辊;16、角轮。
具体实施方式
11.下面将结合本发明实施例中的附图,对本发明实施例中的技术方案进行清楚、完整地描述,显然,所描述的实施例仅仅是本发明一部分实施例,而不是全部的实施例。
12.以下结合附图和实施例对本发明作进一步详细描述。
13.实施例一一种热成型加工工艺,其步骤包括: s1:将22mnb5钢卷材放置于上料机构1内,通过上料机构1将钢卷材输送到平整装置2上进行挤压平整处理;s2:将平整处理后的钢卷通入加热设备3内将钢材加热到850℃~930℃范围内使其形成奥氏体;s3:将加热后的钢材运输至滚压成型设备4,使其根据实际需要塑形;
s4:将塑形后的钢材运输至淬火冷却装置5,以50~100℃/s的冷却速度进行淬火使其形成马氏体;s5:淬火冷却后的钢材通过输送机构传递至截料装置6进行定长截取;s6:将定长截取后的钢材通过输送机构传输至后处理装置7进行激光裁剪、毛刺处理,表面喷涂。
14.本具体实施例实施原理为:通过所述加热设备3使得钢材加热至850℃~930℃范围内使其形成奥氏体,增加了钢材的韧性,通过所述滚压成型设备4对钢材进行塑形,通过所述淬火冷却装置5以50~100℃/s的冷却速度进行淬火使钢材形成马氏体,增加了钢材的强度,通过所述截料装置6进行定长截取,最后通过所述输送机构传输至所述后处理装置7进行激光裁剪、毛刺处理,表面喷涂得到最终产品。
15.实施例二本实施例是将实施例一中的加工工艺应用于高速路护板加工上,其步骤包括:将22mnb5钢卷材放置于上料机构1内,通过所述上料机构1将钢卷材输送到所述平整装置2上,此时所述气缸9下压带动所述压辊10挤压钢材使其平整,将平整处理后的钢材通入所述加热设备3内升温,将钢材加热到900℃使其形成奥氏体;再将加热后的钢材运输至所述滚压成型设备4,此时所述成型辊11上设置的所述凸轮12挤压钢材使其形成如图6所示的波浪形纹路,再将塑形后的钢材运输至所述淬火冷却装置5,以75℃/s的冷却速度进行淬火使其形成马氏体,淬火冷却后的钢材通过所述输送机构传递至所述截料装置6进行定长截取,最后将定长截取后的钢材通过所述输送机构传输至所述后处理装置7进行激光裁剪、毛刺处理,表面喷涂。
16.实施例三本实施例与实施例二的区别在于加工产品不同,本实施例是将热成型加工工艺应用于角钢加工上,其步骤包括:将22mnb5钢卷材放置于上料机构1内,通过所述上料机构1将钢卷材输送到所述平整装置2上,此时所述气缸9下压带动所述压辊10挤压钢材使平整,将平整处理后的钢材通入所述加热设备3内升温,将钢材加热到930℃使其形成奥氏体;再将加热后的钢材运输至所述滚压成型设备4,此时所述成角辊15上设置的所述角轮16挤压钢材使其形成直角,再将塑形后的钢材运输至所述淬火冷却装置5,以83℃/s的冷却速度进行淬火使其形成马氏体,最终将淬火冷却后的钢材通过所述输送机构传输至所述后处理装置7进行激光裁剪、毛刺处理,表面喷涂。
17.以上所述,仅为本发明较佳的具体实施方式,但本发明的保护范围并不局限于此,任何熟悉本技术领域的技术人员在本发明揭露的技术范围内,根据本发明的技术方案及其发明构思加以等同替换或改变,都应涵盖在本发明的保护范围之内。
再多了解一些
本文用于创业者技术爱好者查询,仅供学习研究,如用于商业用途,请联系技术所有人。