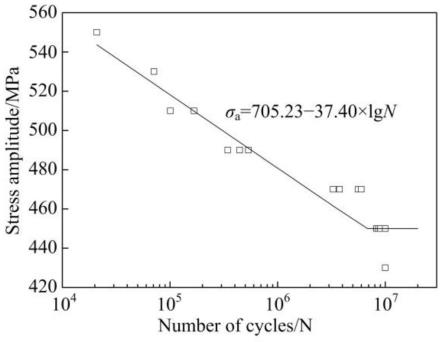
1.本发明属于高强度合金钢生产技术领域,具体涉及一种超厚高强韧高均质水电用特厚钢板及其制造方法。
背景技术:
2.水电是清洁可再生能源,无污染、运行费用低,也便于进行电力储能及调峰,具有较高的经济社会综合效益,是未来实现“碳达峰、碳中和”等节能减排目标的重要发展方向。随着国家特大型水电站的建设,800mpa级高强水电钢逐渐占据设计主导,且钢材需求量呈逐渐增加趋势。
3.水电用800mpa级高强钢主要用在高压引水管段、月牙肋、岔管、水轮机组蜗壳、法兰、座环等关键部位制作,对钢板的强塑性、低温韧性、抗层状撕裂、低焊接裂纹敏感性等要求较高。受水电设备的大型化、轻量化的发展需要,水电站等核心零部件需要更高厚度、强度的特厚板,部分大型水电机组对钢材要求最大厚度可达300mm。目前厚度大于100mm水电用特厚板,投入工业实用以700mpa级别的s500q、s550q(z35)为主,800-1000mpa级别的高强韧水电用特厚钢板,因其技术含量水平高,制造工艺存在较大的难度,目前还未投入工业使用。因此,厚度大于100mm的800~1000mpa级别特厚高强水电钢开发及应用,是中厚板产品研发的一个新课题及方向。
4.厚度大于120mm的水电用特厚板,受压缩比大于3的限制要求,一般要选择的坯料类型是大型钢锭、特厚连铸坯(400mm及以上)、电渣重熔锭或者锻件生产。目前已经开发700~800mpa水电用特厚钢板,一般均采用crnimo合金化的成分设计,工艺选择总体是“淬火 回火”热处理工艺生产,制造工艺复杂,生产成本也比较高。不同的企业的化学成分设计各有其特点,各有不同。
5.专利号“cn 103014283 a”公布一种连铸坯生产水电站用特厚钢板的制造方法,采用“400mm连铸
→
轧制
→
轧后冷却
→
奥氏体淬火
→
亚温淬火
→
高温回火”的工艺步骤,生产100~150mm的高强度水电钢,采用冶炼成分为:c:0.05~0.15%,si:0.15~0.40%,mn:0.90~1.60%,p<0.010%,s<0.01%,ni:1.0~2.0%,mo:0.1~0.50%,b:0.0008~0.0015%,v:0.01~0.08%,余量为fe;经过多道次复杂的轧制热处理工艺处理后,制备出150mm厚的屈服强度为500~550mpa,抗拉强度为600~650mpa的700mpa级高强钢。
6.专利号“cn 109881086 a”公布了“一种厚度300mm高强调质钢板q550ez35及其生产方法”,采用水冷模铸生产,采用冶炼成分为:c:0.10~0.14%、si:≤0.20%、mn:1.00~1.60%、p:≤0.015%、s:≤0.005%、nb:0.030~0.055%、v:0.050~0.070%、ti:≤0.010%、mo:0.35~0.60%、ni:0.90~1.50%、cr:0.50~0.80%、als:0.040~0.060%,b:≤0.00040%、cu:≤0.020%,其它为fe和残余元素;该高强调质钢板采用cr-ni-mo成分设计,坯料采用水冷模铸钢锭,生产工艺采用热轧 轧后回火 预正火 亚温淬火 回火等多道次热处理的工艺生产,制备出300mm厚度屈服强度达到540~580mpa,抗拉强度650~680mpa,延伸率19~23%的700mpa级的高强钢。
7.专利号“cn 101709432 a”公布了“大厚度调质型海洋平台用钢及其生产方法”,其成分设计:c:0.16~0.18%;si:0.15~0.35%;mn:1.10~1.15%;p:≤0.015%;s:≤0.005%;cu:0.05~0.10%;ni:1.30~1.40%;cr:1.20~1.30%;mo:0.45~0.55%;nb:0.03~0.04%;v:0.05~0.06%;n:≤0.0060%;ti:0.020~0.025%;als:0.020~0.040%;b:0.0014~0.0023%;该高强调质钢板也采用cr-ni-mo-v-b成分设计,采用电渣重熔坯料,工序多流程长,成本较高;采用淬火 回火工艺,生产出厚度152mm的800mpa级别的高强调质钢,延伸率只有18-21%,-60℃低温冲击试验达到100j;该钢化学成分c含量相对较高(0.16~0.18%),cr含量达到1.2~1.3%,mo也比较高,采用高ni(1.30%~1.40%)成分,还添加b元素提高淬透性,总合金含量达到5%,焊接裂纹敏感性指数pcm达到0.37,焊接性也不好,厚度最厚只有152mm;若进一步提高厚度,为了保证淬透性,势必进一步增加c含量,这样低温韧性和钢板的延性恐难以保证。
8.专利号“cn 106544590 a”公布了“1000mpa级高韧性高性能均匀性易焊接特厚钢板及其制造方法”,其成分设计:c:0.12~0.15%;si:0.15~0.35%;mn:0.95~1.20%;p:≤0.010%;s:≤0.002%;cu:0.20~0.40%;ni:2.40~3.00%;cr:0.50~0.80%;mo:0.40~0.60%;nb≤0.04%;v:0.03~0.06%;n:≤0.0060%;ti:0.020~0.025%;als:0.060~0.090%;b:0.0010~0.0020%;该专利所述的钢板采用450mm的特厚连铸坯作为坯料,采用高c、高ni的成分设计,ni含量最低为2.4%,焊接裂纹敏感性指数pcm达到0.34,合金成本较高。热处理工艺采取低温“淬火 回火”生产,抗拉强度达到1100mpa级别,但是延伸率只有10.2~14.5%,厚度1/4、1/2处的-40℃冲击功平均只有69~76j。该专利所述的钢板虽然强度达到1100mpa级别,但是延伸率及低温韧性都无法满足q690d的标准要求,难以工业化应用。
9.专利号“cn 101962741 a”公布了“一种调质钢板及其制造方法”,其成分设计:c:0.10~0.16%;si:≤0.20%;mn:0.85~1.25%;p:≤0.013%;s:≤0.003%;cu:0.20~0.45%;ni:0.90~1.50%;cr:0.45~0.75%;mo:0.40~0.65%;nb:0;v:0.03~0.06%;n:≤0.0060%;ti:0.006~0.012%;als:0.045~0.070%;b:0.0006~0.0012%;该钢板采用cr-ni-mo-cu-v合金化成分设计,以模铸钢锭为坯料,采用“淬火 回火”工艺,生产出厚度100~150mm,屈服强度≧690mpa,抗拉强度≧800mpa,-40℃的平均冲击功157~190j的800mpa级高强钢;但是该方案生产钢板最大厚度只有150mm,钢板延伸率只有19~22%。
10.专利号“cn 106319380 a”公布了“一种低压缩比690mpa级特厚钢板及其生产方法”,其成分设计:c:0.05~0.14%;si:0.12~0.45%;mn:0.70~1.40%;p:≤0.010%;s:≤0.005%;cu:0.10~0.50%;ni:0.50~1.00%;cr:0.10~0.40%;mo:0.10~0.40%;nb:0;v:0.03~0.08%;n:≤0.0050%;ti:0.005~0.030%;als:0.025~0.065%;b:0.0008~0.0040%。该方案以300mm连铸坯为原料,轧制厚度100~115mm钢板,采用“正火 淬火 高温回火”工艺,生产出80~115mm的屈服强度为690~720mm,抗拉强度为740~808mpa,延伸率只有16.5~20.0%,-40℃冲击功96~180j的800mpa级高强钢。该方案生产的钢板最大厚度有限,延伸率及低温冲击功不稳定且比较低。
11.专利号“cn 102605282 a”公布了“80公斤级超高韧性、极厚钢板及其制造方法”,其成分设计:c:0.08~0.13%;si:≤0.10%;mn:0.80~1.20%;p:≤0.013%;s:≤0.003%;cu:0.20~0.45%;ni:1.00~1.60%;cr:0.35~0.65%;mo:0.30~0.60%;nb:
0.010~0.030%;v:0.03~0.06%;n:≤0.0050%;ti:0.004~0.010%;als:0.040~0.070%;b:0.0008~0.0016%;该钢板采用cr-ni-mo-cu-v合金化成分设计,以模铸钢锭为坯料,采用“淬火 淬火 高温回火”工艺生产100~190mm特厚钢板,生产出钢板的屈服强度718~816mpa,抗拉强度为785~964mpa,延伸率18~20%,-60℃冲击功60~100j的800mpa级高强钢。但是该方案生产钢板延伸率只有18~20%,-60℃冲击功也比较低,190mm钢板强度存在明显下降,更大厚度的钢板可能也存在淬透性的难题。
12.从上述专利可以看出传统的700~800mpa级别调质钢成分体系均采用cr-ni-mo-v合金化成分体系,组织以贝氏体为主,生产的钢板最高强度一般都在700~800mpa级别,钢板越厚强度越低,生产最大厚度受到限制,而且生产钢板低温韧性及延伸率等技术指标虽然能够满足用户的要求,但是钢板延伸率普遍偏低(≤20%),-40℃及以下的冲击功普遍偏低。除此之外,钢板沿厚度方向的力学性能均匀性也不太理想,即钢板上下表面硬度高、中心部位硬度低,厚度方向性能、硬度、组织均匀性性差,超厚规格(大于150mm)的调质钢板厚度方向性能不均匀的现象更为严重,较低的延伸率及冲击韧性不仅不利于钢板冷加工性能,而且对钢板的抗疲劳性能、抗应力集中敏感性及结构稳定性影响较大。在水电工程中的压力水管和涡壳、火电汽轮发电机及海洋采油平台结构等疲劳重载结构上使用时,存在一定的安全隐患。因此,大型疲劳重载钢结构采用高强钢时,一般希望800mpa级高强钢具有优良的强韧性、强塑性匹配,较好的低温韧性,延伸率在20%以上,具有优良的抗疲劳性能的高强钢。
13.从以上所述的专利来看,目前100mm~200mm的高强度调质钢的抗拉强度一般在700~800mpa级别,大于200mm的钢板只能达到700mpa级别,更高厚度、更高强度级别(800~1000mpa)的高强度水电用钢,目前还未研发出来。钢铁行业一直致力于开发高强度钢,通过进一步提高强度以此来实现减少钢材使用量,以实现大型化、轻量化的目的。100mm以上的调质高强钢的抗拉强度进一步提高到800~1000mpa级,若采用传统的crnimo合金化设计,受钢板的淬透性及特厚板的淬火冷却速率的制约,生产存在较大的生产难度。虽然通过增加c含量可以提高淬透性,但是也会造成钢板低温韧性、延伸率、焊接性的大幅度下降,需通过增加ni含量可以提高韧性,但是ni价格比较昂贵,ni元素对淬透性影响较小,而且随着c含量的增加,大型钢锭凝固过程的热溶质对流(热浮力)随之增加,大型钢锭c元素宏观偏析越发严重,后续均匀化处理也难以完全消除。传统的crnimo调质钢的淬火组织为贝氏体组织为主,特厚板不同厚度区域的不仅冷速不同,而且c含量的不同,造成不同区域的淬火组织的差异巨大,宏观偏析严重区域(钢板心部)会产生局部异常的马氏体组织,造成传统的调质高强钢组织、性能均匀性差,影响最终使用性能。
技术实现要素:
14.本发明的目的在于提供一种超厚高强韧高均质水电用特厚钢板及其制造方法,通过钢板合金元素的优化设计与特殊热处理工艺相结合,获得超厚规格(120~300mm),抗拉强度800~1000mpa级别,优良强度、低温韧性及强韧性匹配的同时,焊接性优异,高强韧、高均质的水电用高强度特厚板,解决传统的高强度调质特厚板普遍存在热处理工艺复杂、高强度与延伸率不匹配、低温韧性差、厚度方向强韧性不均匀、组织均匀性差等世界性难题,制成超低碳、高强韧、高均质的800~1000mpa级的水电用高强度特厚板。
15.本发明的超厚高强韧高均质水电用特厚钢板的成分按质量百分比含c 0.02~0.10%,si≤0.30%,mn 4.0~8.0%,p≤0.015%,s≤0.005%,als 0.015~0.040%,cr≤0.4%,mo≤0.40%,ni≤1.0%,cu≤0.3%,nb≤0.030%,v 0.04~0.12%,ca 0.001~0.005%,b≤0.002%,稀土0.01~0.04%,余量为fe和不可避免杂质;并且cr ni mo cu v≤2.0%;其中稀土为ce或la。
16.上述的超厚高强韧高均质水电用特厚钢板的厚度为120~300mm;抗拉强度850~1100mpa,屈服强度≥650~800mpa,屈强比小于0.85,具有优异的强塑性。
17.上述的超厚高强韧高均质水电用特厚钢板的延伸率≥20%。
18.上述的超厚高强韧高均质水电用特厚钢板的-60℃纵横向夏比冲击功≥120j,-80℃纵横向夏比冲击功≥80j,具有优异的低温韧性。
19.上述的超厚高强韧高均质水电用特厚钢板的组织为板条状的回火马氏体 逆转奥氏组织的双相组织,及少量的纳米状碳化物。
20.本发明的超厚高强韧高均质水电用特厚钢板的制造方法包括以下步骤:
21.(1)高炉铁水冶炼;
22.(2)kr预脱硫;
23.(3)转炉出钢:
24.(4)vd/rh真空脱碳;
25.(5)lf精炼;
26.(6)vd/rh真空脱气;
27.(7)模铸;
28.(8)热清热装;
29.(9)钢锭加热;
30.(10)轧制;
31.(11)acc冷却;
32.(12)堆冷;
33.(13)淬火;
34.(14)临界回火。
35.上述方法中,kr预脱硫后的转炉入炉铁水中,按质量百分比含s≤0.010%,p≤0.080%。
36.上述方法中,转炉出钢时,钢水中按质量百分比含c≤0.05%,p≤0.010%,n含量小于30ppm,出钢温度大于1620℃。
37.上述方法中,转炉出钢时,出钢液面渣层厚度≤200mm。
38.上述方法中,转炉出钢后,在10分钟内将钢包转移至vd/rh工位。
39.上述方法中,vd/rh真空脱碳时,真空度《100pa,保压时间在10~15min;真空脱碳完成后,钢水中按质量百分比含c≤0.020%。
40.上述方法中,vd/rh真空脱碳后,向钢包中先加入铝粒和锰合金,铝粒的加入量按钢包钢水总重量0.02~0.05%的质量比例加入;锰合金的首次加入量按钢包钢水总重量1.0~1.5%的质量比例加入,合金加入后转移至lf精炼炉,进行lf精炼脱硫。
41.上述方法中,lf精炼脱硫时,到站后加入石灰或萤石等造高碱度泡沫渣,所述的高
碱度为碱度》3;采用大功率冶炼,精炼全过程软吹氩,加快合金的熔化速度,缩短加热时间,减少精炼环节增c。
42.上述方法中,lf精炼过程中,每次加入的精炼渣及合金完全熔化后,钢水温度升温至1580~1620℃,然后再次分批次加入合金;每次合金量不超过钢水总重量的1.5%;根据设计合金成分,分批次加入各类合金,最终微调各类合金成分至设计成分范围内,精炼结束时al和mn含量按照设计成分上限控制;精炼结束后,升温至1620~1650℃,然后送至vd/rh炉,进行二次真空脱气处理。
43.上述方法中,加入的mn合金采用高纯度的电解锰或者超低碳锰铁;加入ni采用电解镍板;加入cr采用低碳铬铁;其中锰合金采用多批次加入,每次加入量为钢包钢水总重量的1~1.5%,共分成3~6批次加入。
44.上述方法中,vd/rh真空脱气时,到站温度大于1620℃,脱气过程全程软吹氩,真空度《100pa,保压时间≥15min,脱气后钢水的氢含量≤1.5ppm;破空后加入覆盖剂,然后测温取样;成分及温度不足的炉次,转移至lf炉调温,微调合金成分至设计成分;成分合格的炉次,按照稀土的质量百分比为0.01~0.02%加入;加入稀土用铝箔包裹并与洁净钢块捆绑后,拨开渣层直接沉入钢包中,避免稀土与渣层接触;模铸时,按开始浇注温度为1550~1570℃进行,lf炉按照此控制离站温度。
45.上述方法中,模铸时,钢锭采用上大下小的扁钢锭结构,模具采用钢锭模或者水冷模,钢锭采用下注法进行浇注,钢锭重量在10~50吨;钢锭的锭身锥度要求在4
°
~6
°
,冒口比控制在15~20%,厚度控制在600~1100mm,保证轧制钢板压缩比大于3。
46.上述方法中,钢锭浇注前,清理好浇道及模具内壁,修补流道并铺设冒口绝热板,绝热板与模具之间的缝隙也需要用耐火泥修补光滑,防止钢水侵入;绝热板必须采用导热系数小于0.1w/(m.k)的耐火材料,保证隔热效果;模具摆放到位后,提前在模具内放置稀土棒,具体方法按照行业标准yb/t048-1993《钢锭模中稀土棒吊挂方法》进行,稀土加入量按照稀土质量百分比为0.01~0.04%控制,稀土棒放置模铸的中心位置;模铸开始浇注前,在模具内通入氩气置换出内部的空气,减少浇注过程的氧化。
47.上述方法中,模铸时,模铸开始浇注温度为1550~1570℃,浇注流量按照钢锭内的液面上升速度进行控制,浇注速度应该按照先快后慢的原则进行控制,锭身下部分的液面上升速度按照20~30cm/min控制,锭身上部分的液面上升速度按照10~20cm/min控制;钢锭的冒口部分的浇注速度按照5~10cm/min进行。
48.上述方法中,模铸时,模铸锭身浇注500mm以上时,加入保护渣及覆盖剂,减少温降及氧化;随着模铸内的液面上升,稀土棒逐步熔化,当液面上升至冒口部位时,稀土棒及固定钢架熔化完毕;当模铸冒口充满后,向冒口中加入发热剂,减缓冒口的凝固速度。
49.上述方法中,模铸浇注完毕后应自然风冷,开模时间需大于12h;模铸开模后应立即检查裂纹情况。若有裂纹应在300℃以上进行热清;若无裂纹,直接转移至加热炉进行加热,装炉温度必须大于200℃。
50.上述方法中,钢锭加热过程分为预热、升温、闷钢、升温和保温五个阶段,其中预热温度420℃,预热时间为6~8h;之后以≤60℃/h的速度升温至830℃闷钢10~15h,然后以100~150℃/h快速升温至1180~1200℃,并保温20~30h;整体加热时间2.5~3min/mm控制。
51.上述方法中,轧制过程分两个阶段进行,一阶段热轧开轧温度大于1050℃;轧制前期总压下率≤40%时,单道次轧制压下量≤7%,轧制平均变形速率≤2s-1
;前期压下量逐步增加,初始轧制压下量为10~40mm;当轧制总压下率超过40%时,采用大压下率进行轧制,轧制变形速率≤2s-1
;轧制厚度至400~450mm时,晾钢控温;当钢锭表面温度《980℃时,开始第二阶段轧制,该阶段轧制保证至少两道次轧制压下率》15%,轧制平均变形速率≤2s-1
,终轧温度在880~950℃。
52.上述方法中,轧制过程的轧制压下率ε%及轧制平均变形速率的计算公式如下:
[0053][0054]
式中h0为轧制初始厚度,单位为mm;h1为轧制出口厚度,单位为mm;ν为轧辊圆周速度,即轧制速度,单位为mm/s;ld为轧制过程的接触弧长,单位为mm;r为轧辊半径,单位为mm。
[0055]
上述方法中,轧制完成后,钢板应采用acc进行均匀冷却,冷却速度<5℃/s,终冷温度为380~400℃;然后在冷床上降温至300~350℃,待钢板有磁性后,吊入缓冷坑进行缓冷,入坑温度》250℃,堆冷时间》72h;拆垛后取样检测性能,若性能合格,完成堆冷处理。
[0056]
上述方法中,因钢板较厚,为了确保钢板性能的稳定性,完成堆冷处理的钢板采取淬火 临界回火工艺进行热处理;淬火工艺如下:完成堆冷处理的钢板先400~450℃进行预热,预热时间为6~8h,然后快速升温至820~850℃保温,保温时间3~5min/mm,保温后入水快速冷却,入水温度≥700℃,终冷温度≤80℃,获得淬火钢板;获得淬火钢板在淬火后进行四切精整,仅留取样位置在获得淬火钢板上,避免回火后火切对性能稳定性的影响;临界回火热处理工艺如下:获得淬火钢板先450~500℃进行预热保温,保温时间按照淬火钢板的厚度2~3min/mm计算,然后快速升温至630~650℃,保温时间按照淬火钢板的厚度1~2min/mm计算。
[0057]
本发明所述钢种采用高炉铁水冶炼,杂质元素含量低;铁水先经kr铁水预脱硫处理,转炉入炉铁水s≤0.010%、p≤0.080%,减少lf精炼脱硫负担;转炉冶炼环节,采用优质重废,严禁采用来源复杂的劣质废钢,严控cu、pb、sb、sn、zn、bi等杂质元素的来源;转炉吹炼过程确保一次拉c到终点,严禁多次点吹;转炉出钢终点c≤0.05%,p≤0.010%,n含量小于30ppm,出钢温度大于1620℃;转炉出钢过程中要求全程吹氩,出钢过程不加入任何合金或者脱氧剂,可顺流加入适量的石灰,严控出钢挡渣工艺,确保出钢液面渣层厚度≤200mm;
[0058]
真空脱气环节,到站温度大于1620℃,脱气过程全程软吹氩,真空度必须达到100pa以下,保压时间必须≥15min,脱气后氢含量≤1.5ppm;破空后加入覆盖剂,然后测温取样;成分及温度不足的炉次,转移至lf炉调温,微调合金成分至设计成分;成分合格的炉次,加入稀土,稀土需要用铝箔包裹并与洁净钢块捆绑后,拨开渣层直接沉入钢包中,避免稀土与渣层接触。模铸开始浇注温度按照1550~1570℃进行,lf炉按照此控制离站温度;
[0059]
钢锭浇注前,应该清理好浇道及模具内壁,修补流道并铺设冒口绝热板,绝热板与模具之间的缝隙也需要用耐火泥修补光滑,防止钢水侵入;
[0060]
模铸浇注过程应平稳进行,浇注流量不能忽高忽低,浇注液面应该平稳上升,不得剧烈波动,尽量避免浇注过程的卷渣;
[0061]
模铸浇注完毕后应自然风冷,不得移动模具;
[0062]
本发明的成分设计原理是:采取的以“低c高mn”为基础的合金成分,其中c含量小于0.10%,mn含量在4-8%,同时加入少量cr、ni、mo、nb、v、cu等合金元素的新型调质钢成分体系,采用常规模铸生产坯料,通过热轧 淬火 临界回火生产工艺,获得具有优良的强塑性、强韧性匹配、高均质的水电用高强度特厚板。
[0063]
本发明的钢板的各化学成分的作用说明如下:
[0064]
c:对调质钢板的强度、低温韧性、延伸率及焊接性影响很大。从改善特厚调质钢板低温韧性和焊接性的角度考虑,钢板中c含量控制得越低越好;从调质钢板的淬透性、强韧性匹配、厚板的淬火冷却速率限制、显微组织控制及制造成本的角度考虑,c含量不宜控制得过低。此外,从大型钢锭的铸造特性考虑,c元素凝固平衡配分系数小(0.15~0.35),对凝固过程的微观偏析引起热溶质对流作用大,c元素在大型钢锭的凝固组织中的宏观偏析尤为严重,偏析范围一般在设计c含量的80~170%之间波动,设计c元素越高,c元素宏观偏析的波动范围越大。大型钢锭c元素的宏观偏析一般难以通过均匀化退火消除,是造成调质钢板性能不均匀的一个关键因素。因此,本专利所述的方案采用较低的c含量,c含量的范围为0.02%~0.10%;
[0065]
si:促进钢水脱氧并能够提高钢板强度,但是si元素的密度低,凝固过程平衡配分系数小,对溶质浮力的贡献的作用仅次于c,加剧凝固过程的热溶质对流,对大型钢锭的凝固组织的宏观偏析造成不利影响,而且si严重损害钢板的低温韧性、延伸率及焊接性,尤其在较大线能量焊接的条件下;si不仅促进m-a岛形成,而且形成的m-a岛尺寸较为粗大、分布不均匀,严重损害焊接热影响区(haz)韧性和焊接接头性能。因此,钢中的si含量应尽可能控制得低;考虑到炼钢过程的经济性和可操作性,si含量控制在0.30%以下;
[0066]
mn:作为最重要的合金元素,具有显著的扩大奥氏体相区、降低ar3点温度、提高钢的淬透性的作用,mn还能细化调质钢板晶团,改善钢板低温韧性以及促进低温相变组织形成而提高钢板强度的作用;但是mn在钢水凝固过程中容易发生偏析,容易与c、p、s、mo、cr等元素发生共轭偏析现象,尤其是钢板中c含量较高时,会加重铸坯中心部位的宏观偏析与疏松。严重的铸坯或者钢锭中心区域偏析在后续的轧制、热处理及焊接过程中易形成局部的贝氏体、马氏体等异常组织,导致调质钢板低温韧性低下。本专利所述的方案采用远高于常规的mn含量,mn含量在4.0~8.0%,但是采用极低的c含量,mn含量的偏析问题一定程度得到缓解。mn对钢板的淬透性的作用非常明显,4.0~8.0%mn钢的空冷组织(常规厚度钢板)都是马氏体组织,与mn的中心偏析区域产生的马氏体组织是一样的组织,因此钢板中也不存在“异常”组织的危害。疏松可以通过大压下量轧制予以消除,mn的微观及宏观偏析问题,可以通过临界回火工艺,将多余c、mn元素扩散到逆转奥氏体组织中,形成高塑性的逆转奥氏体组织,增加钢的塑性和韧性;因此,通过高锰成分设计,不仅mn的危害也得以消除,而且mn的高淬透性优势得以发挥,有利于超厚调质板的热处理;
[0067]
p:作为钢中有害杂质,对钢板的机械性能,尤其是低温冲击韧性、延伸率、焊接性及焊接接头性能具有巨大的损害作用。理论上要求p含量越低越好,但考虑到炼钢可操作性和炼钢成本,对于要求优良焊接性、-40℃韧性及优良强韧性匹配的特厚调质钢板,p含量需要控制在≤0.015%;
[0068]
s:作为钢中有害杂质,对钢板的低温韧性具有很大的损害作用,更重要的是s在钢中与mn结合,形成mns夹杂物。在热轧过程中,mns的可塑性使mns沿轧向延伸,形成沿轧向
mns夹杂物带,严重损害钢板的低温冲击韧性、延伸率、z向性能、焊接性能及焊接接头性能。同时,s还是热轧过程中产生热脆性的主要元素,理论上要求越低越好,但考虑到炼钢可操作性、炼钢成本和物流顺畅原则,s含量需要控制在≤0.005%;
[0069]
cr:作为弱碳化物形成元素,添加cr不仅可以提高钢板的淬透性、促进马氏体/贝氏体形成,而且马氏体/贝氏体板条间位向差增大,增大裂纹穿过马氏体/贝氏体晶团的阻力,在提高钢板强度的同时,具有一定的改善钢板韧性的作用。本专利所述的方案采用的高mn成分,淬透性很好,但是考虑到cr有较好的抗氧化、抗腐蚀作用,因此cr含量控制在0.40%以下;
[0070]
mo:mo作为强碳化物形成元素,具有较好的相变强化作用,同时提高钢板的淬透性,促进马氏体/贝氏体形成;mo还能够抑制p、s、bi等晶界杂质元素的回火脆性,提高钢的抗回火软化性能。但是mo在大幅度提高调质钢板强度的同时,降低了调质钢板的低温韧性和延伸率,而且会增加钢板生产成本;因此,综合考虑mo的相变强化作用及对母材钢板低温韧性、延伸率和焊接性的影响,mo含量控制在0.30%以下;
[0071]
ni:不仅可以提高铁素体相中位错可动性,促进位错交滑移,而且增大马氏体/贝氏体板条间位向差;ni作为奥氏体稳定化元素,降低ar3点温度,提高淬透性,细化马氏体/贝氏体晶团尺寸;ni具有同时提高调质钢板强度、延伸率和低温韧性的功能;钢中加ni还可以降低含铜钢的铜脆现象,减轻热轧过程的晶间开裂,提高钢板的耐大气腐蚀性。因此从理论上讲,钢中ni含量在一定范围内越高越好,但是ni价格昂贵;本发明采用高mn成分,淬透性及低温韧性都能保证,因此处于经济性的考虑,不需要添加较高的ni含量;
[0072]
cu:也是奥氏体稳定化元素,添提高钢板的淬透性和钢板的耐大气腐蚀性。cu元素还有较好的纳米析出强化效果,但是cu添加量过多,高于0.45%时,容易造成铜脆、铸坯表面龟裂、内裂问题及尤其特厚钢板焊接接头性能劣化;cu、ni的复合添加可降低含铜钢的铜脆现象、减轻热轧过程的晶间开裂的作用。cu添加量过少,低于0.20%时,所起作用很小。本发明所述的方案cu含量控制在0.30%以下;
[0073]
b:显著提高钢板淬透性,但是b含量过高,会损害钢板的焊接性、haz韧性,恶化板坯表面质量。因此本发明所述的方案中b含量控制在0.0020%以下;
[0074]
als:酸溶铝,能够固定钢中的自由[n],除降低焊接热影响区(haz)自由[n],改善焊接haz的低温韧性作用之外,更重要的是保证钢中稀土元素的收得率。因此,als含量控制在0.015~0.040%;
[0075]
n:该钢添加合金较多,mn元素增加n的溶解度,lf精炼时间长,并且采用模铸浇注时,钢中的n含量控制难度较大,为了防止大量aln沿原奥氏体晶界析出,损害钢板的冲击韧性尤其横向低温冲击韧性,钢中的n含量不得超过0.010%;
[0076]
v:添加v的目的是为了固氮,通过v(c,n)在贝氏体/马氏体板条中析出,提高调质钢板的强度。v含量小于0.04%时,提高强度作用有限。v添加量过多,高于0.12%,会损害钢板低温韧性、延伸率、焊接性及焊接性能。考虑到钢板厚度较厚,热处理冷却速率较低,钢板强度衰减明显,v含量控制在0.040%~0.12%之间;
[0077]
ca:进行ca处理,一方面可以进一步纯洁钢液,另一方面对钢中硫化物进行变性处理,使之变成不可变形的、稳定细小的球状硫化物,抑制s的热脆性,提高钢板的低温韧性、延伸率及z向性能,改善钢板韧性的各向异性;ca加入量的多少,取决于钢中s含量的高低,
ca加入量过低,处理效果不大;ca加入量过高,形成ca(o,s)尺寸过大,脆性也增大,可成为断裂裂纹起始点,降低钢的低温韧性和延伸率,同时还降低钢质纯净度、污染钢液。ca含量一般这样控制,按质量百分比计算,essp=ca(1~1.24)/1.25s,其中essp为硫化物夹杂形状控制指数,取值范围0.5~5之间为宜,因此ca含量的合适范围为0.001%~0.005%;
[0078]
稀土:稀土ce或者la与s元素的结合力高于mn,能够抑制mns的形成;将al2o3、mns、cas等夹杂物改性成球状夹杂物,降低夹杂物的危害;一般稀土与s含量的比值大于3采有比较明显的效果;稀土还可以提高钢凝固过程的异质形核率,降低c、mn等元素微观偏析程度,提高钢的等轴晶区的面积,抑制宏观偏析。同时,稀土能够与杂质元素p、sn、bi等元素相互作用,降低这些微量残余元素的危害,提高钢的高温热塑性。稀土还可以增强钢的抗腐蚀及抗氧化能力;稀土与氢原子在低温下能够形成化学键,提高钢的抗氢脆能力;本发明中mn含量较高,凝固过程的微观偏析会导致树枝晶凝固末期液相中会析出mns夹杂,降低钢的热塑性,造成凝固、锻造或者轧制过程产生裂纹;同时考虑高锰钢的mn含量高,mn元素活性较大,耐腐蚀性差,添加稀土有助于提高钢的耐腐蚀性能;稀土ce或者la价格相对经济,添加少量稀土元素就有比较明显的效果,因此要求稀土加入量控制在0.01~0.04%之间。
[0079]
本发明的有益效果在于,采用该技术方案,生产出100~300mm厚度的抗拉强度在800~1000mpa级别高强韧调质水电钢板,与传统的调质高强钢相比具有以下显著特征:
[0080]
①
该方案所生产的钢板的强塑性、强韧性、延伸率、低温韧性等性能远好于传统crnimo合金的调质高强钢;钢板抗拉强度最高可达1000~1100mpa,延伸率最高可达30%以上,-80℃低温韧性可达100j以上,强韧性、强塑性匹配好于传统的调质高强钢。钢板的组织中含有逆转奥氏体组织,塑性变形过程有trip效应,具有较好的耐疲劳性能及断裂韧性;
[0081]
②
该方案所生产的钢板成品组织为板条状的回火马氏体 逆转奥氏组织的双相组织及少量的纳米状碳化物,钢板厚度方向的组织、性能均匀性更好;传统的crnimo调质高强钢的淬火组织为贝氏体和马氏体的混合组织,贝氏体又分为上贝氏体或者下贝氏体,不同组织性能差异比较大;特厚板淬火冷却过程,表面和心部的冷却速率相差达到几十倍,冷却速率的差异导致不同厚度处的淬火组织差异巨大,回火后仍然难以消除,因此,传统的调质高强钢特厚板往往厚度方向的性能差异巨大。本发明的钢板,采用低碳高mn成分设计,钢的淬透性极佳,如图1所示,成分中含0.05%(wt)的c元素和5%(wt)mn元素的低碳中锰钢,冷却速度在0.1℃/s以上均可以获得马氏体组织,这能够确保特厚板淬火过程中,不同厚度部位在不同冷却的情况下,均能得到淬火马氏体组织,经过临界回火热处理后,可获得回火马氏体 逆转奥氏体的双相组织,制备特厚板的厚度方向均匀性更好;
[0082]
③
该方案可以生产200~300mm抗拉强度在800~1000mpa的调质高强钢;传统的crnimo成分的调质高强钢,提高200mm以上调质特厚板的强度面临较大的难度;从已经公布的发明及资料来看,厚度超过200mm的调质高强钢板,很少有抗拉强度超过800mpa,主要原因在于,钢板越厚,蓄热能力越好,淬火过程冷却速度越低,200mm以上的特厚板淬火过程中,很难达到较高的冷却速率,特别是钢板心部,传统的crnimo成分的调质钢往往面临钢板心部“淬不透”的难题,无法获得贝氏体或者马氏体组织,因强度难以提高;本方明的钢板的淬透性极佳,冷却速度在0.1℃/s以上均可以获得马氏体组织,这能够确保特厚钢板心部能轻松淬透,为提高特厚板的强度提高创造了条件;
[0083]
④
本发明所述的钢板能够缓解或者消除大型铸坯、钢锭凝固的宏观偏析的危害;
传统的高强度调质钢板一般通过提高c含量来增强钢的淬透性,满足特厚板心部淬透的要求;但是大型钢锭各溶质元素一般都存在一定程度的宏观偏析问题,c元素的宏观偏析尤为严重,会加重铸坯或者钢锭中心部位的宏观偏析与疏松,在后续的轧制、热处理及焊接过程中易形成局部的马氏体等异常组织,导致调质钢板低温韧性低下、淬火开裂等现象;本发明所述成分的钢板采用低c高mn的成分设计,c含量在0.10%以下,mn含量在4~8%,cr、ni、mo、v等元素含量较低;c元素宏观偏析波动最大范围为0.08~0.20%,mn元素的宏观偏析范围一般在设计成分的90~140%,即4~10%,c、mn宏观偏析范围内的淬火组织均为马氏体组织,因此也不会因宏观偏析产生“异常”组织;c、mn等元素凝固组织宏观偏析区域(如钢坯心部或者钢锭冒口部位)淬透性更好。该钢成品组织为回火马氏体 逆转奥氏组织;在临界回火过程中,过高的c、mn元素会进入板条马氏体之间逆转奥氏体组织中,增加逆转奥氏体的含量,不仅消除了c、mn元素偏析的危害,而且增加成分偏析区域的韧性;
[0084]
⑤
本发明的钢板具有较好的焊接性能及耐疲劳性能;该钢虽然mn含量很高,但是c含量较低,在预热情况下进行焊接,在焊缝或者热影响区都有较好的焊接性能,经过焊后热处理,各项性能指标更加优异;附图4显示了低碳中锰钢的耐疲劳实验结果的s-n曲线,结果显示出该钢的疲劳极限强度450mpa以下,钢板具有接近“无限”的耐疲劳寿命,这主要得益于中锰钢的组织中逆转奥氏体组织中的trip效应的贡献;
[0085]
⑥
本发明的低碳中锰钢具有低电导率及低磁性的特性,有利于降低发电过程的磁滞损耗,实现节能减排;一般在频率不变的情况下,提高材料的电阻率、降低材料的磁导率都能使得趋肤深度增大,从而能使涡流自身感应出的磁场对激励磁场的削弱作用增大,降低涡流损耗。一般奥氏体组织(如铝、铜、不锈钢等元素)没有磁性,都是良好的电磁屏蔽材料,但是一般价格昂贵。该钢成品组织还有10~30%的逆转奥氏体组织,可以降低钢的磁导率,理论上比常用低合金结构钢的磁导率降低30%以上;该钢种mn含量较高,jmatpro理论计算表明,该钢电阻率是低合金结构钢的200~300%,更加适合在电气设备部件上的使用。
[0086]
本发明所述的超厚规格的800~1000mpa级高强韧、高均质水电用特厚钢板,具有高强韧、高强塑、高均质、超低温韧性、高淬透性的特点,不仅可以作为制造水电工程的调质高强特厚板,而且在大型工程机械结构及海洋石油平台等结构也可以应用,也属于本发明的保护范围。
附图说明
[0087]
图1为本发明的不同成分超厚高强韧高均质水电用特厚钢板的静态cct曲线图;
[0088]
图2为本发明实施例1中的200mm高强韧高均质水电用特厚钢板淬火后的sem显微组织图;图中,(a)为表面处,(b)为1/4厚度处,(c)为1/2厚度处;
[0089]
图3为本发明实施例1中的200mm高强韧高均质水电用特厚钢板淬火 临界回火热处理后的sem显微组织图;
[0090]
图4为本发明实施例1中的超厚高强韧高均质水电用特厚钢板耐疲劳试验的s-n曲线图。
具体实施方式
[0091]
本发明实施例中,120~300mm厚高强韧高均质水电用特厚钢板的屈服强度在650
~800mpa,抗拉强度在850~1050mpa,屈强比在0.75~0.85之间,钢板强塑性较好。
[0092]
本发明实施例中,120~300mm厚高强韧高均质水电用特厚钢板的延伸率≥20%。
[0093]
本发明实施例中,120~300mm厚高强韧高均质水电用特厚钢板的-60℃纵横向的夏比冲击功≥120j,-80℃纵横向夏比冲击功≥80j,钢板具有优异的低温韧性。
[0094]
实施例1
[0095]
200mm厚高强韧高均质水电用特厚钢板(q690zmz35钢板)的冶炼成分按质量百分比含c 0.06%,si 0.13%,mn 5.6%,p 0.012%,s 0.003%,als 0.026%,cr 0.26%,mo 0.24%,ni 0.52%,cu 0.25%,nb 0.018%,v 0.085%,ca 0.002%,b 0.002%,ce0.027%,n 0.0056%,余量为fe;并且cr ni mo cu v=0.26% 0.52% 0.24% 0.25% 0.085%=1.355%≤2.0%;
[0096]
制备的200mm的q690zmfz35钢板各项力学性能分别如表1所示;
[0097]
表1
[0098][0099][0100]
通过本方案制备的200mm厚高强韧高均质水电用特厚钢板,屈服强度为700~740mpa,抗拉强度为896~938mpa,屈强比在0.78~0.82之间,延伸率在24.6~28.8%,-60℃纵横向冲击功大于150j,-80℃纵横向冲击功大于98j,具有极佳的强韧性;
[0101]
通过本方案制备的200mm厚高强韧高均质水电用特厚钢板的组织为板条状的回火马氏体 逆转奥氏组织的双相组织,及少量的纳米状碳化物;
[0102]
具体制造方法包括以下步骤:
[0103]
(1)高炉铁水冶炼;
[0104]
(2)kr预脱硫;
[0105]
(3)转炉出钢:
[0106]
(4)vd/rh真空脱碳;
[0107]
(5)lf精炼;
[0108]
(6)vd/rh真空脱气;
[0109]
(7)模铸;
[0110]
(8)热清热装;
[0111]
(9)钢锭加热;
[0112]
(10)轧制;
[0113]
(11)acc冷却;
[0114]
(12)堆冷;
[0115]
(13)淬火;
[0116]
(14)临界回火;
[0117]
kr预脱硫后的转炉入炉铁水中,按质量百分比含s≤0.010%,p≤0.080%;
[0118]
转炉出钢时,钢水中按质量百分比含c≤0.05%,p≤0.010%,n含量小于50ppm,出钢温度1625℃;
[0119]
转炉出钢时,出钢液面渣层厚度≤200mm;
[0120]
转炉出钢后,在10分钟内将钢包转移至vd/rh工位;
[0121]
vd/rh真空脱碳时,真空度《100pa,保压时间10min;真空脱碳完成后,钢水中按质量百分比含c≤0.020%;vd/rh真空脱碳后,向钢包中先加入铝粒和锰合金,铝粒的加入量按钢包内钢水总重量的0.03%质量百分比加入;锰合金的首次加入量按钢包钢水总重量的1.5%质量百分比加入,合金加入后转移至lf精炼炉,进行lf精炼脱硫;
[0122]
lf精炼时,到站后加入石灰或萤石等造高碱度泡沫渣,所述的泡沫碱度大于3;采用大功率冶炼,精炼全过程软吹氩,用于加快合金的熔化速度,缩短加热时间,减少精炼环节增c;每次待加入的精炼渣及合金完全熔化后,钢水温度升温至1600~1620℃,然后再次加入合金;根据设计合金成分,分批次加入各类合金,最终微调各类合金成分至设计成分范围内,精炼结束时al和mn含量按照设计成分上限控制;精炼结束后,升温至1620~1650℃,然后送至vd/rh炉,进行二次真空脱气处理;
[0123]
lf精炼过程中,加入mn元素采用高纯度的电解锰;加入ni采用电解镍板;加入cr采用低碳铬铁;其中合金采用多批次加入,每次合金加入量为钢包钢水总重量的1~1.5%,共分成5批次,每次合金量不超过钢水总重量的1.50%;
[0124]
vd/rh真空脱气时,到站温度1625℃,脱气过程全程软吹氩,真空度《100pa,保压时间20min,脱气后钢水的氢含量≤1.5ppm;破空后加入覆盖剂,然后测温取样;成分及温度不足的炉次,转移至lf炉调温,微调合金成分至设计成分;成分合格的炉次,按照稀土的质量百分比为0.01~0.02%加入;加入稀土用铝箔包裹并与洁净钢块捆绑后,拨开渣层直接沉入钢包中,避免稀土与渣层接触;模铸时,按开始浇注温度为1550~1570℃进行,lf炉按照此控制离站温度;
[0125]
模铸时,钢锭采用上大下小的扁钢锭结构,模具采用钢锭模或者水冷模,钢锭采用下注法进行浇注,钢锭重量在40吨;钢锭的锭身锥度要求在4.5
°
,冒口比控制在15%,钢锭最大厚度为1100mm,保证轧制钢板压缩比大于3;
[0126]
钢锭浇注前,清理好浇道及模具内壁,修补流道并铺设冒口绝热板,绝热板与模具之间的缝隙也需要用耐火泥修补光滑,防止钢水侵入;绝热板必须采用导热系数小0.1w/(m.k)的耐火材料,保证隔热效果;模具摆放到位后,提前在模具内放置稀土棒,具体方法按照行业标准yb/t048-1993《钢锭模中稀土棒吊挂方法》进行,稀土加入量按照稀土质量百分比为0.02~0.03%控制,稀土棒放置模铸的中心位置;模铸开始浇注前,在模具内通入氩气置换出内部的空气,减少浇注过程的氧化;
[0127]
模铸时,模铸开始浇注温度为1550~1570℃,浇注流量按照钢锭内的液面上升速度进行控制,浇注速度应该按照先快后慢的原则进行控制,锭身下部分的液面上升速度按照20~30cm/min控制,锭身上部分的液面上升速度按照10~20cm/min控制;钢锭的冒口部分的浇注速度按照5~10cm/min进行;
[0128]
模铸时,模铸锭身浇注500mm以上时,加入保护渣及覆盖剂,减少温降及氧化;随着
模铸内的液面上升,稀土棒逐步熔化,当液面上升至冒口部位时,稀土棒及固定钢架熔化完毕;当模铸冒口充满后,向冒口中加入发热剂,减缓冒口的凝固速度;
[0129]
模铸浇注完毕后自然风冷,开模时间需大于12h;模铸开模后应立即检查裂纹情况。若有裂纹应在300℃以上进行热清;若无裂纹,直接转移至加热炉进行加热,装炉温度必须大于200℃;
[0130]
钢锭加热过程分为预热、升温、闷钢、升温和保温五个阶段,其中预热温度420℃,预热时间为6h;之后以60℃/h的速度升温至830℃闷钢10h,然后以100~150℃/h快速升温至1190℃,并保温24h;
[0131]
轧制过程分两个阶段进行,一阶段热轧开轧温度大于1050℃;轧制前期总压下率≤40%时,单道次轧制压下量5~8%,轧制平均变形速率1~2s-1
;前期压下量逐步增加,初始轧制压下量为10~40mm;当轧制总压下率超过40%时,采用大压下率进行轧制,轧制变形速率1~2s-1
;轧制厚度至400~450mm时,晾钢控温;当钢锭表面温度《980℃时,开始第二阶段轧制,该阶段轧制保证至少两道次轧制压下率》15%,轧制平均变形速率1~2s-1
,终轧温度在880~950℃;
[0132]
轧制过程的轧制压下率ε%及轧制平均变形速率的计算公式1如下:
[0133][0134]
式中h0为轧制初始厚度,单位为mm;h1为轧制出口厚度,单位为mm;ν为轧辊圆周速度,即轧制速度,单位为mm/s;ld为轧制过程的接触弧长,单位为mm;r为轧辊半径,单位为mm;
[0135]
200mm的钢板采用厚度1100mm钢锭轧制,轧制至400mm晾钢;晾钢前热轧采用小压下量轧制,轧制压下率不超过8%,晾钢后热轧采用大压下率轧制,保证至少两道次轧制压下率大于15%。晾钢后的轧制压下规程按照400-360-305-250-200的规程进行轧制,终轧温度在920~930℃;
[0136]
轧制完成后,钢板应采用acc进行均匀冷却,冷却速度0.5~5℃/s,终冷温度为380℃;然后在冷床上降温至300℃,待钢板有磁性后,吊入缓冷坑进行缓冷,入坑温度290℃,堆冷时间80h;拆垛后取样检测性能,若性能合格,完成堆冷处理;
[0137]
堆冷后的钢板采用淬火 临界回火工艺进行热处理;淬火工艺如下:堆冷钢板先400℃进行预热,预热时间为8h,然后快速升温至820℃保温,保温时间3min/mm,保温后入水快速冷却,入水温度≥700℃,终冷温度≤80℃,获得淬火钢板;获得淬火钢板在淬火后进行四切精整,仅留取样位置在获得淬火钢板上,避免回火后火切对性能稳定性的影响;临界回火热处理工艺如下:获得淬火钢板先450℃进行预热保温,保温时间按照淬火钢板的厚度2~3min/mm计算,然后快速升温至630℃,保温时间按照淬火钢板的厚度1~2min/mm计算;
[0138]
通过上述工艺即可获得200mm厚高强韧水电用特厚q690zmz35钢板,具有较好的强韧性,强塑性,各项性能如表1所示;
[0139]
制备的200mm厚高强韧水电用特厚q690zmz35钢板在厚度方向性能均匀性较好,具有高均质的特点。图2显示了200mm厚的q690zmfz35钢板淬火后不同厚度处的sem形貌显微组织;从图中可以明显看出不同厚度位置处都是以板条状马氏体为主,这是因为中锰钢mn含量较高,淬透性好,在随后的冷却过程中仅发生马氏体转变,因此不同厚度处的组织形貌
并无明显的差异,组织均匀性较好;图3显示了q690zmfz35钢板淬火 临界回火后的sem形貌显微组织,显微组织主要由亚微米级板条状分布的回火马氏体 逆转奥氏体双相组织及少量弥散分布的纳米级碳化物,形成以大角度晶界配合的板条状混合双相组织,逆转奥氏体组织含量在10~30%之间;
[0140]
不同微观组织的相对初始磁导率数值差别巨大,奥氏体组织的相对初始磁导率在1~1.1之间,铁素体组织的相对初始磁导率大于200,马氏体、贝氏体、回火马氏体等组织的相对初始磁导率在50~100之间;因此,该钢中含有逆转奥氏体组织,可以降低钢的磁导率,有利于降低交变磁场环境下的磁滞损耗;钢的电阻率一般与钢的合金成分含量关系最密切,mn元素有明显提高钢的电阻率的作用,jmatpro理论计算表明,该钢的电阻率在4.5
×
10-7
ω
·
m,是常规结构钢q345b的电阻率(2.0
×
10-7
ω
·
m)的225%,钢的电阻率的提高有助于降低交变磁场环境下的涡流损耗及趋肤深度,降低发电过程的内耗,有利于节能减排;
[0141]
图4显示了中锰钢光滑圆棒试样的轴向拉-压载荷的高周疲劳实验的s-n曲线。试验条件:应力比r=-1,循环应力振幅为常规正弦波,工作频率为150hz,实验温度为室温,设定107次循环数为最大循环数;当材料经受107次交变载荷而不发生断裂时的最大应力即被定义为该材料的高周疲劳极限,意味着材料在该循环应力下具有无限寿命;通常把材料的疲劳应力与疲劳寿命之间的关系曲线叫做疲劳曲线,即s-n曲线,s-n曲线的水平直线段即为材料的疲劳极限;疲劳极限强度代表着在此应力大小下能经受无限次疲劳循环而不发生断裂;结果表明,低碳中锰钢的疲劳极限强度约450mpa,而潜艇用钢10ni5crmov高强钢在相同应力水平,疲劳循环次数只有106次,中锰钢具有更好的耐疲劳性能,这主要得益于中锰钢的显微组织中含有高含量的大角度晶界及逆转奥氏体组织的复合层状组织,在疲劳裂纹扩展过程中,大角度晶界有效阻碍疲劳裂纹的扩展,逆转奥氏体发生trip效应,吸收大量应变能,钝化裂纹,减缓裂纹的扩展速率,因此具有优异的抗疲劳性能。
[0142]
实施例2
[0143]
方法同实施例1,不同点在于:
[0144]
(1)300mm厚高强韧高均质水电用特厚钢板的冶炼成分按质量百分比含c 0.07%,si 0.15%,mn 6.80%,p 0.014%,s 0.001%,als 0.019%,cr 0.32%,mo 0.30%,ni 0.80%,cu 0.25%,nb0.025%,v 0.10%,ca 0.003%,b 0.001%,n 0.0065%,ce la 0.032%,cr ni mo cu v≤2.0%,余量为fe,其余为不可避免的杂质元素。
[0145]
(2)制备成品钢板厚度为300mm,300mm的q690zmfz35钢板各项力学性能分别如表2所示;成品钢板的屈服强度为660~700mpa,抗拉强度为860~900mpa,屈强比在0.76~0.80之间,延伸率在24.5~30.5%,-60℃纵横向冲击功大于120j,-80℃纵横向冲击功大于80j,z向性能满足z35要求,具有较好的强韧性和z向性能,但是各项强度和韧性低于200mm的q690zmfz35;
[0146]
表2
[0147][0148]
(3)转炉出钢温度1640℃;vd/rh真空脱碳时,保压时间在15min;
[0149]
(4)lf精炼过程配置合金时,共分成6批次加入。
[0150]
(5)vd/rh真空脱气时,到站温度1630℃,保压时间19min;
[0151]
(6)采用40吨的大钢锭,钢锭的锭身锥度要求在5
°
,钢锭上部最大厚度为1100mm。冒口比控制在16%;
[0152]
(7)钢锭热清热装,装炉温度大于200℃。加热炉预热温度420℃,时间为8h;之后以50~60℃/h的速度升温至840℃闷钢15h,然后以100~150℃/h快速升温至1200℃,并保温30h;
[0153]
(8)300mm的钢板采用1100mm钢锭轧制,轧制过程分两个阶段进行,一阶段热轧开轧温度1060℃;轧制至500mm晾钢;晾钢前热轧采用小压下量轧制,晾钢后热轧采用大压下率轧制,轧制压下规程按照500-460-410-350-300的规程轧制,终轧温度在900~950℃,保证至少两道次轧制压下率大于15%;
[0154]
(9)轧制完成后,钢板应采用acc进行均匀冷却,冷却速度0.1~2℃/s,终冷温度为350℃;然后在冷床上降温至310℃,待钢板有磁性后,吊入缓冷坑进行缓冷,入坑温度285℃;
[0155]
(10)300mm钢板淬火工艺如下:完成堆冷处理的钢板先480℃进行预热,预热时间为12h,然后快速升温至830℃保温,保温时间3.6min/mm,保温时间18h;保温结束后在淬火水槽中淬火至室温;临界回火热处理工艺如下:获得淬火钢板先在480℃进行预热保温,保温时间按照2~3min/mm控制,保温时间14h,然后快速升温至630℃,保温时间1~1.5min/mm控制,保温时间为6h,保温结束后风冷至室温。
[0156]
实施例3
[0157]
方法同实施例1,不同点在于:
[0158]
(1)120mm厚高强韧高均质水电用特厚钢板的成分按质量百分比含c 0.05%,si 0.15%,mn 4.80%,p 0.011%,s 0.002%,als 0.025%,cr 0.24%,mo 0.19%,ni 0.41%,cu 0.20%,nb0.025%,v 0.085%,ca 0.004%,b 0.002%,n 0.0066%,ce 0.026%,余量为fe;并且cr ni mo cu v≤1.50%;
[0159]
表3
[0160][0161]
(2)120mm的q690zmfz35钢板各项力学性能分别如表3所示;成品钢板的屈服强度为760~820mpa,抗拉强度为960~1040mpa,屈强比在0.76~0.81之间,延伸率在25.6~30.8%,-60℃纵横向冲击功大于160j,-80℃纵横向冲击功大于100j,z向性能满足z35要求,具有较好的强韧性,但是各项强度和韧性高于200mm的q690zmfz35;
[0162]
(3)出钢温度1635℃;vd/rh真空脱碳时,保压时间在12min;
[0163]
(4)vd/rh真空脱气时,到站温度1635℃,保压时间18min;
[0164]
(5)采用25吨的钢锭,锭高2800mm,冒口高度500mm,钢锭的锭身锥度要求在4.5
°
,钢锭上部最大厚度为720mm。冒口比控制在15-16%;
[0165]
(6)钢锭热清热装,装炉温度大于200℃,钢锭预热温度420℃,预热时间为6h;以56℃/h的速度升温至830℃闷钢12h,然后以100~150℃/h快速升温至1190℃,并保温26h;
[0166]
(7)120mm的钢板采用720mm钢锭轧制,轧制过程分两个阶段进行,一阶段热轧开轧温度1060℃,轧制至300mm晾钢;晾钢前热轧采用小压下量轧制,轧制压下率在8%以下;晾钢后热轧采用大压下率轧制,保证至少两道次轧制压下率大于15%。轧制压下规程按照300-260-210-160-120的规程轧制,终轧温度在900~930℃;
[0167]
(14)轧制完成后,钢板应采用acc进行均匀冷却,冷却速度1~5℃/s,终冷温度为400℃;然后在冷床上降温至320℃,待钢板有磁性后,吊入缓冷坑进行缓冷,入坑温度260℃;
[0168]
(15)120mm钢板淬火工艺如下:完成堆冷处理的钢板先420℃进行预热,预热时间为6h,然后快速升温至840℃保温,保温时间8h;保温结束后在淬火水槽中淬火至室温;临界回火热处理工艺如下:获得淬火钢板先在450℃进行预热保温,保温时间6h,然后快速升温至630℃,保温时间1~1.5min/mm控制,保温时间为3h,保温结束后空冷至室温。
[0169]
实施例4
[0170]
方法同实施例1,不同点在于:
[0171]
(1)150mm厚高强韧高均质水电用特厚钢板的冶炼成分按质量百分比含c 0.05%,si 0.16%,mn 5.20%,p 0.012%,s 0.002%,als 0.033%,cr 0.23%,mo 0.18%,ni 0.62%,cu 0.18%,nb 0.019%,v 0.08%,ca 0.004%,b 0.0010%,n 0.0075%,la 0.028%,余量为fe;并且cr ni mo cu v≤2.0%;
[0172]
(2)转炉出钢温度1635℃;vd/rh真空脱碳时,保压时间在13min;
[0173]
(3)lf精炼环节,每次合金加入量为钢水总重量的1~1.5%,共分成5批次加入合金;
[0174]
(4)vd/rh真空脱气时,到站温度1635℃,保压时间17min;
[0175]
(5)采用35吨的钢锭,钢锭的锭身锥度5
°
,钢锭上部最大厚度为1000mm。冒口比控
制在16%;
[0176]
(6)钢锭热清热装,装炉温度大于200℃,预热温度420℃,预热时间为7h;之后以≤60℃/h的速度升温至830℃闷钢12h,然后以100~150℃/h快速升温至1190℃,并保温28h。
[0177]
(7)150mm的钢板采用1000mm钢锭轧制,轧制过程分两个阶段进行,一阶段热轧开轧温度1060℃,轧制至400mm晾钢;晾钢前热轧采用小压下量轧制,轧制压下率在8%以下;晾钢后热轧采用大压下率轧制,保证至少两道次轧制压下率大于15%。轧制压下规程按照400-360-320-280-240-195-150的规程轧制,终轧温度在900~950℃。
[0178]
(8)轧制完成后,钢板应采用acc进行均匀冷却,冷却速度0.2~3℃/s,终冷温度为380℃;然后在冷床上降温至300℃,待钢板有磁性后,吊入缓冷坑进行缓冷,入坑温度270℃;
[0179]
(9)150mm钢板淬火工艺如下:完成堆冷处理的钢板先430℃进行预热,预热时间为7h,然后快速升温至830℃保温,保温时间10h;保温结束后在淬火水槽中淬火至室温;临界回火工艺如下:获得淬火钢板先在440℃进行预热保温,保温时间7h,然后快速升温至630℃,保温时间1-1.5min/mm控制,保温时间为3.5h,保温结束后空冷至室温。
[0180]
(10)150mm的q690zmfz35钢板各项力学性能分别如表4所示;
[0181]
表4
[0182][0183]
成品钢板的屈服强度为700~750mpa,抗拉强度为920~980mpa,屈强比在0.74~0.80之间,延伸率在24.0~30.0%,-60℃纵横向冲击功大于160j,-80℃纵横向冲击功大于80j,z向性能满足z35要求,具有较好的强韧性和低温韧性。
[0184]
实施例5
[0185]
方法同实施例1,不同点在于:
[0186]
(1)180mm厚高强韧水电用特厚钢板的冶炼成分按质量百分比含c 0.05%,si 0.12%,mn 5.5%,p 0.013%,s 0.003%,als 0.024%,cr 0.22%,mo 0.15%,ni 0.51%,cu 0.20%,nb 0.028%,v 0.10%,ca 0.003%,b 0.002%,n 0.0054%,ce 0.029%,余量为fe;并且cr ni mo cu v≤2.0%;
[0187]
(2)采用40吨的钢锭,钢锭的锭身锥度5
°
,钢锭上部最大厚度为1100mm。冒口比控制在16%;
[0188]
(6)钢锭热清热装,装炉温度大于200℃,预热温度450℃,预热时间为8h;之后以≤60℃/h的速度升温至830℃闷钢15h,然后以100~150℃/h快速升温至1200℃,并保温30h。
[0189]
(7)180mm的钢板采用1100mm钢锭轧制,轧制过程分两个阶段进行,一阶段热轧开轧温度大于1060℃,轧制至400mm晾钢;晾钢前热轧采用小压下量轧制,轧制压下率控制在8%以下;晾钢后热轧采用大压下率轧制,保证至少两道次轧制压下率大于15%。轧制压下
规程按照400-360-320-275-230-180的压下规程轧制,终轧温度在900~950℃。
[0190]
(8)轧制完成后,钢板应采用acc进行均匀冷却,冷却速度0.5~4℃/s,终冷温度为360℃;然后在冷床上降温至300℃,待钢板有磁性后,吊入缓冷坑进行缓冷,入坑温度270℃;
[0191]
(9)180mm钢板淬火工艺如下:完成堆冷处理的钢板先440℃进行预热,预热时间为8h,然后快速升温至830℃保温,保温时间12h;保温结束后在淬火水槽中淬火至室温;临界回火工艺如下:获得淬火钢板先在440℃进行预热保温,保温时间8h,然后快速升温至630℃,保温时间1~1.5min/mm控制,保温时间为4h,保温结束后空冷至室温。
[0192]
(10)180mm的q690zmfz35钢板各项力学性能分别如表5所示;
[0193]
表5
[0194][0195]
成品钢板的屈服强度为680~730mpa,抗拉强度为900~950mpa,屈强比在0.74~0.80之间,延伸率在24.0~28.0%,-60℃纵横向冲击功大于160j,-80℃纵横向冲击功大于80j,z向性能满足z35要求,具有较好的强韧性和低温韧性。
[0196]
实施例6
[0197]
方法同实施例1,不同点在于:
[0198]
(1)240mm厚高强韧高均质水电用特厚钢板的冶炼成分按质量百分比含c 0.04%,si 0.10%,mn 7.1%,p 0.011%,s 0.001%,als 0.023%,cr 0.22%,mo 0.20%,ni 0.68%,cu 0.24%,nb 0.022%,v 0.090%,ca 0.002%,b 0.001%,n 0.0062%,ce 0.029%,余量为fe;并且cr ni mo cu v≤2.0%;
[0199]
(2)采用40吨的钢锭,钢锭的锭身锥度5
°
,钢锭上部最大厚度为1100mm。冒口比控制在16%;轧制压缩比大于3;
[0200]
(6)钢锭热清热装,装炉温度大于200℃,预热温度450℃,预热时间为8h;之后以≤60℃/h的速度升温至830℃闷钢15h,然后以100~150℃/h快速升温至1200℃,并保温30h。
[0201]
(7)240mm的钢板采用1100mm钢锭轧制,轧制过程分两个阶段进行,一阶段热轧开轧温度大于1060℃,轧制至450mm晾钢;晾钢前热轧采用小压下量轧制,轧制压下率控制在8%以下;晾钢后热轧采用大压下率轧制,保证至少两道次轧制压下率大于15%。轧制压下规程按照450-420-380-340-295-240的压下规程轧制,终轧温度在900~950℃。
[0202]
(8)轧制完成后,钢板应采用acc进行缓慢均匀冷却,冷却速度0.1~3℃/s,终冷温度为350℃;然后在冷床上降温至280℃,待钢板有磁性后,吊入缓冷坑进行缓冷,入坑温度大于250℃;
[0203]
(9)240mm钢板淬火工艺如下:完成堆冷处理的钢板先440℃进行预热,预热时间为8h,然后快速升温至830℃保温,保温时间12h;保温结束后在淬火水槽中淬火至室温;临界
回火工艺如下:获得淬火钢板先在440℃进行预热保温,保温时间8h,然后快速升温至630℃,保温时间1~1.5min/mm控制,保温时间为4h,保温结束后空冷至室温。
[0204]
(10)240mm的q690zmfz35钢板各项力学性能分别如表6所示;
[0205]
表6
[0206][0207]
成品钢板的屈服强度为670~720mpa,抗拉强度为880~930mpa,屈强比在0.75~0.80之间,延伸率在24.0~28.0%,-60℃纵横向冲击功大于150j,-80℃纵横向冲击功大于80j,z向性能满足z35要求,具有较好的强韧性和低温韧性。
[0208]
实施例7
[0209]
方法同实施例1,不同点在于:
[0210]
(1)140mm高强韧高均质水电用特厚钢板的成分按质量百分比含c 0.04%,si 0.28%,mn4.6%,p 0.012%,s 0.003%,als 0.022%,cr 0.20%,mo 0.2%,ni 0.31%,cu 0.25%,nb 0.020%,v 0.065%,ca 0.003%,b 0.0005%,n 0.0055%,ce0.025%,余量为fe;并且cr ni mo cu v≤1.5%;
[0211]
(2)出钢温度1645℃;vd/rh真空脱碳时,保压时间在15min;
[0212]
(3)lf精炼过程中,每次合金加入量为钢水总重量的1~1.5%,共分成3批次加入。
[0213]
(4)vd/rh真空脱气时,到站温度1630℃,保压时间15min;
[0214]
(5)采用30吨的钢锭,锭高2800mm,冒口高度500mm,钢锭的锭身锥度要求在4.5
°
,钢锭上部最大厚度为900mm。冒口比控制在15~16%;
[0215]
(6)钢锭热清热装,装炉温度大于200℃,钢锭预热温度420℃,预热时间为7h;以50℃/h的速度升温至830℃闷钢15h,然后以100~150℃/h快速升温至1200℃,并保温26h;
[0216]
(7)140mm的钢板采用900mm钢锭轧制,轧制过程分两个阶段进行,一阶段热轧开轧温度大于1050℃,轧制至360mm晾钢;晾钢前热轧采用小压下量轧制,轧制压下率在8%以下;晾钢后热轧采用大压下率轧制,保证至少两道次轧制压下率大于15%。轧制压下规程按照360-320-280-230-185-140的规程轧制,终轧温度在900~930℃。
[0217]
(8)轧制完成后,钢板应采用acc进行均匀冷却,冷却速度1~5℃/s,终冷温度为390℃;然后在冷床上降温至300℃,待钢板有磁性后,吊入缓冷坑进行缓冷,入坑温度270℃;
[0218]
(9)140mm钢板淬火工艺如下:完成堆冷处理的钢板先430℃进行预热,预热时间为7h,然后快速升温至840℃保温,保温时间8.5h;保温结束后在淬火水槽中淬火至室温;临界回火热处理工艺如下:获得淬火钢板先在440℃进行预热保温,保温时间7.5h,然后快速升温至630℃,保温时间1~1.5min/mm控制,保温时间为3.5h,保温结束后空冷至室温。
[0219]
(10)140mm的q690zmfz35钢板各项力学性能分别如表7所示;
[0220]
表7
[0221][0222]
成品钢板的屈服强度为750~800mpa,抗拉强度为960~1005mpa,屈强比在0.78~0.82之间,延伸率在24.0~30.0%,-60℃纵横向冲击功大于160j,-80℃纵横向冲击功大于100j,z向性能满足z35要求,具有较好的强韧性和低温韧性。
再多了解一些
本文用于创业者技术爱好者查询,仅供学习研究,如用于商业用途,请联系技术所有人。