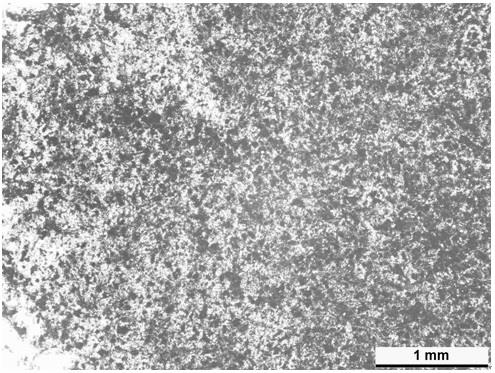
1.本发明属于金属基复合材料制备加工及粉末成形领域,特别提供一种基于粉末搅拌摩擦加工制备铜基金刚石复合材料的方法。
背景技术:
2.随着半导体器件的集成度和功率的不断提高,其工作中的散热也越来越受到重视,提高电子元器件的散热效率、提高性能稳定性已经成为了电子工业领域至关重要的环节。
3.铜基金刚石复合材料因具备高热导率、低膨胀系数,在热管理和电子封装领域受到广泛关注。然而,铜(及其合金)的热膨胀系数是金刚石的十倍以上,导致液相法(压力浸渗、无压浸渗、搅拌铸造等)制备出的铜基金刚石复合材料,在从高温冷却到室温的过程中容易产生微区的热残余应力,导致在基体中形成微区疏松甚至裂纹,从而极大的影响复合材料整体的导热性能。此外,因为铜和金刚石的密度差异大,导致使用铸造法容易出现成分偏析,而浸渗方法只能制备特定金刚石体积分数的复合材料,局限性较大。
4.以传统粉末冶金热压方法为代表的固相法,能够方便调控金刚石的体积分数,并且不容易出现金刚石的偏析。然而,传统粉末冶金方法,依然需要在较高的温度下进行热压,微区残余应力难以改善。并且由于粉末冶金过程中粉末流动性不足,容易出现热压不致密,存在未被压实孔洞,导致材料的性能下降。
5.综上所述,现有常用的液相法和固相法制备铜基金刚石复合材料存在热残余应力大、成分偏析、微观孔洞缺陷等问题,严重影响材料的服役性能。并且传统方法往往需要专用的设备,成本高,加工过程周期长,生产效率低。
6.搅拌摩擦方法具有低温固态成形、搅拌均匀化和热压致密化特点,有望克服铜基金刚石复合材料制备过程中特有的问题。近些年已有部分研究和专利开始采用搅拌摩擦加工方法对粉末进行加工或者制备复合材料,但是这些研究和技术均不是针对含有金刚石等硬质颗粒的铜基复合材料的加工问题,没有解决硬质金刚石颗粒在铜及其合金粉末中的流动和冶金行为控制所需要的工艺调控问题,也没有解决电子封装用铜基金刚石复合材料的快速制备问题。
7.例如专利cn202010618363.7,利用搅拌摩擦焊接接头上的粉末,从而实现改善焊接接头为目的,不涉及铜基金刚石复合材料和材料的快速制备。专利cn201811587764.x利用对粉末/颗粒的搅拌摩擦加工实现增材,但是增材加工方法对材料的流动性需求较高,难以制备高体积分数的复合材料,并且该类方法制备过程中可能需要金属粉末的融化,难以解决低温固态成形的需求。部分利用粉末搅拌摩擦加工制备复合材料的专利主要侧重于对专用设备的开发(如cn202010611032.0),尚无针对铜基金刚石复合材料粉末摩擦加工的研究论文和专利。有专利利用搅拌摩擦加工技术对已经完成复合的金属基复合材料的二次加工,侧重于改善金属基体组织和增强体分布(如cn201110338421.1,cn201910991330.4),而非本发明涉及的直接制备铜基复合材料。有利用搅拌摩擦加工直接制备石墨烯增强铝基复
合材料片状样品的论文(acs appl. mater. interfaces 2021, 13, 27, 32161),主要利用搅拌摩擦加工技术解决纳米尺寸石墨烯增强体的分散难题,与本发明所要解决的主要问题不同,且涉及的复合材料基体(铝)和增强体(石墨烯)也与本发明所采用的完全不同。还有部分专利在打孔或多孔的金属基体内填充增强体粉末,然后进行搅拌摩擦加工(如cn200910248824.x,cn201911337730.x,cn201510473097.2),该种方法对增强体的体积分数有限制,难以制备任意体积分数的复合材料,而且相较于本发明中直接使用基体粉末,此类方法中基体在搅拌摩擦作用下的流动性较差,会一定程度上限制基体与增强体的混合效果。
技术实现要素:
8.本发明的目的在于提供一种基于粉末搅拌摩擦加工制备铜基金刚石复合材料的方法,该方法通过搅拌摩擦加工工具与模具配合,直接对铜粉和金刚石粉末进行搅拌摩擦加工,在固态下进行铜基金刚石复合材料的成形,通过时间、转速等工艺参数的控制,可以有效降低制备加工过程中的热输入量,实现在远低于液相的温度下固结成形,从而有效控制微区的热残余应力;又因为搅拌摩擦对粉末流动的促进作用,可以改善粉末冶金过程中的粉末流动性不足,进而提高材料致密度,减少孔洞形成。该方法使用常规的搅拌摩擦加工工具即可进行,不需要开发专用的设备,从而可大幅降低材料的制备加工成本;因为搅拌摩擦的过程也是一个促进粉末均匀混合的过程,所以该方法对粉末初步混合均匀程度的要求低,整个制备过程的效率显著高于液相法和传统粉末冶金方法。
9.本发明技术方案如下:一种基于粉末搅拌摩擦加工制备铜基金刚石复合材料的方法,其特征在于:将混合后的铜粉、合金元素粉和金刚石粉末/颗粒放入模具中,在搅拌摩擦设备上固定模具,利用搅拌头的下压力、摩擦力和搅拌力实现铜基金刚石复合材料的制备。
10.作为优选的技术方案:在铜、合金元素和金刚石的混合粉末中,金刚石所占的体积分数为10%~70%,其余皆为铜和合金元素;铜和合金元素中,铜的质量分数大于等于50%,合金元素的质量分数小于50%。
11.所述合金元素为锌、银、铅、锡、钛、铝、镍、锆之一种或多种。
12.所述金刚石粉末/颗粒的尺寸在1~150微米之间,铜粉与合金粉末的尺寸小于200微米。
13.所用搅拌头轴肩直径在10~50毫米之间,搅拌针直径小于10毫米,也可以不使用搅拌针。搅拌头材质选择钨铼合金、立方碳化硼、钼基合金、高温合金、合金钢中的一种。
14.搅拌头在接触粉末之后的下压速度小于每分钟10毫米,搅拌头的转速在每分钟100-800转之间。
15.在使用无针搅拌头的条件下,单次加入混合粉末的量,要保证其致密后复合材料的厚度不大于10毫米;在采用带针搅拌头的条件下,要保证其致密后复合材料的厚度减去搅拌针长度的值小于10毫米;搅拌头到位后保压15秒钟以内,也可不保压。
16.上述方法可用于制备片状或块体铜基金刚石复合材料,尤其适用于制备电子封装用铜基金刚石复合材料片状零件。
17.本发明所述基于粉末搅拌摩擦加工制备铜基金刚石复合材料的方法,其特征在于,具体步骤如下:(1)粉末初步混合;需要根据合金成分设计,计算出铜、合金元素和金刚石的比例,根据对合金熔点、热导率、电阻率、耐磨性的要求,可选择添加适量合金元素;混合粉末中的合金元素可以是将元素粉末按照比例添加进入的,也可以通过直接使用铜合金粉末来加入。
18.粉末的混合对混料方式没有严格的要求,可以使用球磨混合、旋转混料等不同的方式进行,粉末的混合过程对混合均匀程度的要求较低,也可以选用效率较高的桨叶搅拌混料方式。
19.(2)模具装粉,确定搅拌摩擦压下量;根据模具和搅拌头的尺寸,确定需要装粉的量,需要保证复合材料致密后各部分的粉末均能够得到充分的摩擦搅拌和热量的输入。
20.(3)搅拌摩擦加工;在进行搅拌摩擦加工之前,需要事先对模具和搅拌头进行对中操作;对铜基金刚石复合材料粉末进行搅拌摩擦加工,在该过程中,需要根据搅拌头距粉末、模具的距离,确定下压速度和转速;在搅拌头未达到模具顶端时,可采用大压下速度,提高整体加工效率;在搅拌头进入模具内或接触到复合粉末时,应适当降低下压速度,以保证搅拌摩擦过程的充分进行。通过控制搅拌摩擦的转速、保压时间等参数,调控复合材料成形过程中的温度,从而实现对热残余应力的调控。可以采用无搅拌针的搅拌头进行加工,从而获得无搅拌针孔的铜基复合材料。通过搅拌摩擦加工,将混合粉末制备成形为片状铜基金刚石复合材料。
21.(4)继续加入粉末,重复步骤(1)-(3),可实现不同厚度铜基金刚石复合材料的制备。
22.为了获得大尺寸的块体铜基金刚石复合材料,可将搅拌头从模具撤出,重复步骤(1)-(3),从而可以实现铜基金刚石复合材料的分层增材制造,获得厚度更大的块体复合材料。
23.本发明的有益效果为:1)本发明所述方法不需要将铜及其合金进行熔化,可以大幅度降低材料制备加工过程中出现问题的概率,从而降低温度变化过程中铜和金刚石的热错配量,降低铜和金刚石间的热残余应力,以及坯料整体的热残余应力,解决铜基金刚石复合材料基体中的微区疏松、孔洞等问题,提高材料的性能。
24.2)本发明所述方法不需要研发和搭建专用的设备和工具,能够显著降低生产的投入;本发明在复合材料成形过程中,有剧烈的搅拌作用,可以进一步促进金刚石和铜的混合,对前期粉末混合的均匀度要求低,生产过程更加简洁可控;本发明核心过程采用搅拌摩擦加工技术,可以在数分钟至数十分钟内完成铜基复合材料从粉末到致密材料的制备,提高生产效率,生产成本低,能够实现针对电子封装用铜基金刚石复合材料小型片状零件的快速成型。
25.3)相较于液相法,采用本发明所述方法制备的铜基金刚石复合材料具有更低的热残余应力和可控的金刚石体积分数。相较于传统粉末冶金热压法,本发明所述方法热输入量可控,较低的成形温度也导致复合材料热残余应力更低,利用搅拌摩擦引入大变形促进
粉末流动,解决粉末冶金过程中材料流动、填充不足的问题,提高材料的致密度,从而提高复合材料整体性能。相较于液相法和传统粉末冶金热压法,本发明所述方法制备效率显著提升,且不需要搭建专用成形设备,对设备的要求更低。
附图说明
26.图1 实施例1所得复合材料金相图。
27.图2 对比例1所得复合材料金相图。
28.图3 对比例2所得复合材料金相图。
具体实施方式
29.实施例1制备体积分数为50%的金刚石增强纯铜复合材料,选用的金刚石尺寸约为40微米,单次装粉3.91克,其中金刚石1.10克,纯铜粉2.81克,采用搅拌棒机械混合。
30.模具内径20毫米,深度15毫米,模具采用2系铝合金;选用搅拌头为无针平底搅拌头,直径与模具内径相等,材质为钨铼合金。将粉末装入模具中,模具固定到搅拌摩擦焊机加工平台上,将搅拌头与模具中心对中。
31.设定搅拌头下压速度每分钟10毫米,搅拌头转速每分钟600转,在搅拌头底部距模具内腔底部5毫米时,下压速度降低为每分钟4毫米,继续下压3毫米,压到位后,保压10秒,然后抬起搅拌头。
32.使用线切割,将固化后的复合材料与搅拌头分离,获得尺寸约为2毫米厚,直径20毫米的片状铜基金刚石复合材料,通过金相观察(如图1所示),从照片中能够发现铜基金刚石复合材料中金刚石分布均匀,不存在明显的偏析,复合材料中不存在明显空洞,致密度好。
33.实施例2制备体积分数为10%的金刚石增强纯铜复合材料,选用的金刚石尺寸约为150微米,采用机械混料机进行混合。
34.搅拌头尺寸、模具尺寸和装配均与实施例1相同。
35.设定搅拌头下压速度每分钟10毫米,搅拌头转速每分钟800转,在搅拌头接触到粉末后,下压速度降低为每分钟4毫米,继续下压至压实,保压1秒,然后抬起搅拌头。
36.使用线切割,将固化后的复合材料与搅拌头分离,获得金刚石分布均匀、无明显的偏析、无明显空洞,致密度好的片状铜基金刚石复合材料。
37.实施例3制备体积分数为70%的金刚石增强纯铜复合材料,选用尺寸约10微米和40微米的金刚石颗粒各一半,采用机械混料机进行混合。
38.搅拌头尺寸、模具尺寸和装配均与实施例1相同。
39.设定搅拌头下压速度每分钟10毫米,搅拌头转速每分钟100转,在搅拌头接触到粉末后,下压速度降低为每分钟1毫米,继续下压至压实,保压10秒,然后抬起搅拌头。
40.使用线切割,将固化后的复合材料与搅拌头分离,获得金刚石分布均匀、无明显的偏析、无明显空洞,致密度好的片状铜基金刚石复合材料。
41.对比例1粉末成分含量、搅拌头和模具尺寸均与实施例1相同。
42.设定搅拌头转速每分钟90转,搅拌头下压速度每分钟10毫米,在搅拌头底部距模具内腔底部5毫米时,下压速度降低为每分钟4毫米,继续下压3毫米,压到位后,保压10秒,然后抬起搅拌头。
43.获得的铜基金刚石复合材料的显微照片如图2所示,能够看到由于搅拌速度低,流动不够充分导致的大片区域未实现粉末的冶金结合,出现了大量未结合的粉末。
44.对比例2粉末成分含量、搅拌头和模具尺寸均与实施例1相同。
45.设定搅拌头转速每分钟800转,搅拌头下压速度每分钟15毫米,一次压到致密位置,保压2秒,然后抬起搅拌头。
46.获得的铜基金刚石复合材料的显微照片如图3所示,能够看到由于搅拌速度高、粉末流动充分,大片区域能够实现粉末的冶金结合,但是由于下压速度较大,保压时间较短,出现了少量区域粉末结合差。
47.本发明未尽事宜为公知技术。
48.上述实施例只为说明本发明的技术构思及特点,其目的在于让熟悉此项技术的人士能够了解本发明的内容并据以实施,并不能以此限制本发明的保护范围。凡根据本发明精神实质所作的等效变化或修饰,都应涵盖在本发明的保护范围之内。
再多了解一些
本文用于创业者技术爱好者查询,仅供学习研究,如用于商业用途,请联系技术所有人。