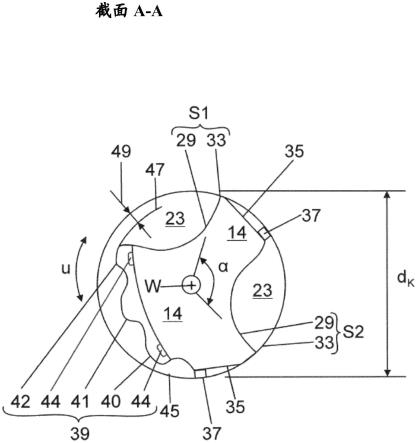
1.本发明涉及一种根据权利要求1的前序部分所述的用于加工工件螺纹孔的方法以及一种根据权利要求19所述的钻螺纹孔工具。
背景技术:
2.在这种类型的方法中,在加工工件螺纹孔时,首先进行钻孔行程,在钻孔行程中使旋转的钻螺纹孔工具在钻孔方向上攻入没有底孔的工件中直至额定孔深,确切的说在形成无螺纹的底孔的情况下。此外,在该方法中进行攻丝行程,在攻丝行程中,钻螺纹孔工具以攻丝进给量以及与此同步的攻丝转速在底孔中加工出内螺纹。
3.例如,该方法可实现成所谓的攻入式钻螺纹孔工艺,在其中,在公共的工具行程中进行预钻孔(也就是说钻底孔)以及加工内螺纹。在这种情况中,钻孔行程和攻丝行程在时间上彼此重叠。这导致高的工具负载并且可能导致工具使用寿命缩短。
4.从wo 2019/029850 a1中已知这种攻入式钻螺纹孔工艺。在钻螺纹孔行程结束时,使旋转的工具的旋转方向反转。紧接着,工具在逆向行程中无负载地从螺纹孔中引导出来,确切的说在与逆向进给量同步的逆向转速下,在该逆向转速下,钻螺纹孔工具的螺纹加工齿无负载在工件螺纹孔的牙间槽中运动。
技术实现要素:
5.本发明的目的在于,提供一种用于加工工件螺纹孔的方法以及一种钻螺纹孔工具,在其中,与现有技术相比降低了工具负载并且可以更短的过程时间加工螺纹孔。
6.该目的通过权利要求1或19所述的特征实现。在从属权利要求中公开了本发明的优选的改进方案。
7.与上述wo 2019/029850 a1不同地,根据本发明,在钻孔行程中不再不仅加工底孔而且同时加工内螺纹,这带来高的工具负载。相反地,在本发明中,钻螺纹孔工具设计成,在钻孔行程中仅仅进行底孔加工。随后,在与此无关的攻丝行程中,加工内螺纹。根据权利要求1的特征部分的特征,为了准备攻丝行程,在钻孔行程之后进行逆向行程,在逆向行程中,钻螺纹孔工具在与钻孔方向相反的逆向方向上完全从底孔中引导出来。在偏移行程中,将从底孔中引导出来的钻螺纹孔工具径向向外调整径向偏移量。紧接着,在沿着绕孔轴线的圆形轨迹的圆周转动运动中引导径向被调整的钻螺纹孔工具,随后开始攻丝行程。
8.应强调的是,根据本发明,不是在逆向行程中进行内螺纹加工。在这种情况中,为了准备内螺纹加工,需花时间进行钻螺纹孔工具的转速调整,在该转速调整时,必须将钻螺纹孔工具从钻孔转速(上述钻孔行程的)调整到攻丝转速(用于随后的内螺纹加工)。此外,在这种内螺纹加工时,以拉力加载钻螺纹孔工具,由此工具受到更少的负载。
9.根据本发明,攻丝行程和钻孔行程可具有相同的行程方向。在钻孔行程中,钻螺纹孔工具绕其旋转的工具轴和孔轴线彼此同轴。此外,在钻孔行程中,钻螺纹孔工具的钻孔区段与工件切削接合,而无负载地一起引导螺纹加工区段。
10.在一种优选的实施变型方案中,随着达到额定螺纹深度,可使攻丝行程延长自由切削行程。在自由切削行程中,钻螺纹孔工具的进给量和转速不再彼此同步,由此在没有螺距的情况下加工紧接着内螺纹的环绕的退刀槽。在攻丝行程中,工具轴和孔轴线彼此轴平行,确切的说彼此具有相应于径向偏移的轴距离,在偏移行程中径向地将钻螺纹孔工具调整该径向偏移。
11.在自由切削行程期间加工环绕的退刀槽之后,可进行第二偏移行程。在第二偏移行程中,使钻螺纹孔工具在径向上从内螺纹或退刀槽中自由移出径向偏移量。由此实现,在随后的逆向行程中,钻螺纹孔工具可无负载地、也就是说在没有螺纹接合或者没有切削接合的情况下从工件螺纹孔中引导出来。
12.为了准备攻丝行程,可根据需要进行钻螺纹孔工具的旋转方向反转。例如,可在执行第一逆向行程时进行旋转方向反转。
13.必要时,在进行钻孔行程之后,可将钻螺纹孔工具的转速减速到零并且开始第一逆向行程。
14.在攻丝行程中,通过在xy平面中绕螺纹外直径da的中心同步内推并且通过以每转一圈一个螺距的进给量沿着孔轴线(或工具轴)同时同步运动,进行螺纹切割。钻螺纹孔工具转一圈的时间(nw)相应于绕螺纹外直径的中心转一圈的时间(ng)。在该时间中进行的沿着孔轴线的进给(螺纹进给量)相应于螺距。
15.在第一偏移行程中(也就是说在第一逆向行程和攻丝行程之间),将旋转的钻螺纹孔工具调整一径向偏移量并且在沿着绕孔轴线的圆形轨迹的圆周转动运动中引导。
16.钻螺纹孔工具设计成,在钻孔行程中,工具螺纹加工区段(用于加工内螺纹所需的)保持无负载并且与底孔壁脱开接合。相反地,在紧接着的攻丝行程中,工具孔钻区段(用于加工底孔所需的)保持无负载并且与加工出的内螺纹脱开接合。在攻丝行程中,工具孔钻区段利用其钻孔切削部在内螺纹的径向内部的螺纹顶部之内径向运动。在工具轴与孔轴线轴平行的情况下进行攻丝行程。
17.钻螺纹孔工具具有至少一个第一钻孔切削部和第二钻孔切削部,其在工具周向上彼此间隔楔角。如此设计楔角的大小,使得两个钻孔切削部在攻丝行程中无负载地并且与加工出的内螺纹脱开接合地从工件螺纹孔中引导出来。
18.在一种技术实现方案中,构造在钻螺纹孔工具上的螺纹加工区段在工具周向上布置在由两个钻孔切削部包夹的旋转角区域之外。
19.两个钻孔切削部的外部的切割轮廓在工具旋转时在钻孔切削部圆形轨迹上运动。以相同的方式,在工具旋转时,工具螺纹加工区段的齿廓在具有齿廓直径的齿廓圆形轨迹上运动。为了辅助钻螺纹孔工具在径向上以及在第二逆向行程中在轮廓不干涉的情况下退刀,齿廓直径设计成小于切割轮廓直径。以这种方式,在钻孔切削部圆形轨迹和齿廓圆形轨迹之间得到径向的工具自由空间。在退刀时,在径向上部分地利用该工具自由空间。
20.在第一钻孔切削部和第二钻孔切削部之间包夹的楔角可仅仅示例性地设计成小于180
°
并且例如在120
°
的范围内。
21.钻孔切削部中的每一个可具有至少一个构造在工具顶端上的端侧的横向切削棱。每个钻孔切削部的横向切削棱可在径向外部的刀尖处过渡到钻孔切削部的纵向切削棱中。此外,在一种具体的实施变型方案中,钻孔切削部可分别构造在工具纵向上伸延的孔钻桥
接部。两个孔钻桥接部可在工具周向上通过容屑槽彼此间隔开。限定容屑槽的切削面可(在工具周向上)在纵向切削棱处过渡到周侧的孔钻桥接部自由面中。径向向外的导向边可分别从两个孔钻桥接部自由面中的每一个中伸出。此外,在两个周侧的孔钻桥接部自由面中的每一个上可构造工具螺纹加工区段。
22.在钻螺纹孔工具的工具顶端上,限定容屑槽的切削面可在端侧的横向切削棱处过渡到端侧的自由面中,端侧的自由面朝着工具轴的方向上锥形地收缩。在均匀的钻孔切削部负载方面优选的是,第一和第二钻孔切削部在工具轴向上布置在不同的高度位置中,也就是说彼此轴向地高度错移量。可如此设计在两个钻孔切削部(尤其是其具有从属的刀尖的横向切削棱)之间的轴向高度错移量,即,在钻孔行程中每个钻孔切削部的钻孔切削部负载几乎相同。在钻孔切削部轴向高度错移量时,可实现几乎均匀的钻孔切削部负载,虽然尽管钻孔切削部不是相对于工具轴对角相对(例如在传统的钻螺纹孔工具中是这种情况),从而每个钻孔切削部的齿进给量几乎同样大。尤其是,钻孔切削部的两个端侧的横向切削棱可在工具轴向上彼此高度错移。
附图说明
23.接下来根据附图描述本发明的实施例。
24.其中:
25.图1以侧截面图示出了在工件中构造的螺纹盲孔-孔;
26.图2和图3示出了钻螺纹孔工具的不同视图;
27.图4至图8分别示出了说明在一个工艺过程中加工在图1中示出的螺纹盲孔-孔的视图;
28.图9和10以不同的视图示出了传统的钻孔工具;
29.图11至14示出了本发明的实施例;以及
30.图15至18示出了本发明的另一实施例。
具体实施方式
31.在图1中示出了完成的螺纹盲孔-孔1。借助于一个工艺过程将具有其孔底3的孔1加工到工件5中直至额定孔深tb,这稍后根据图4至8解释。螺纹孔1在其孔开口上具有环绕的螺纹下沉部7,螺纹下沉部在继续的延伸中向下过渡到内螺纹9中。内螺纹9沿着孔轴线a延伸到可用的额定螺纹深度tg。如还可从图1中得到的那样,内螺纹9的牙间槽通入环形环绕的自由通道或退刀槽13中。在图1中,内螺纹9的螺纹芯在底孔直径dk上。内螺纹9的螺纹牙底在螺纹外直径da上。
32.借助于随后根据图2和3描述的钻螺纹孔工具加工在图1中示出的螺纹盲孔-孔1。因此,在图2中,工具具有夹紧柄15,螺纹孔钻本体17联接在夹紧柄上。在图3中,在螺纹孔钻本体17上构造第一钻孔切削部s1和第二钻孔切削部s2,钻孔切削部在工具周向u上彼此相距楔角α。在图3中,钻螺纹孔工具具有两个在工具纵向上伸延的孔钻桥接部14。在这两个孔钻桥接部14的每个上分别构造一个钻孔切削部s1、s2。两个孔钻桥接部14在工具周向u(图3)上通过容屑槽23彼此间隔开。钻孔切削部s1、s2中的每一个分别具有在工具纵向上伸延的纵向切削棱27(仅仅在图12和14中指出)和构造在工具顶端上的端侧的横向切削棱29。端
侧的横向切削棱29在径向外部的刀尖33处过渡到纵向切削棱27中。
33.限定容屑槽23的切削面在纵向切削棱27处过渡到周侧的孔钻桥接部自由面35(图3)中。在周侧的孔钻桥接部自由面35处分别构造侧向伸出的导向边37。此外,在宽的孔钻桥接部14处(确切的说在其孔钻桥接部自由面35处)构造有工具螺纹加工区段39。在图3中,工具螺纹加工区段由总共三个加工齿组成,即,预加工齿40,中间齿41和精加工齿42。备选地或附加地,也可设置其它齿(例如在图1中示出的齿43)。在图3中,齿40至42相继地布置在工具周向u上并且在轴向上例如布置在相同高度上。然而,此外备选地,工具螺纹加工区段39不限制在该特定的实施变型方案上。相反地,也可提供更少或更多的切割齿和/或切割齿也可轴向彼此错位地布置在孔钻桥接部自由面35上。
34.此外,在轴向上观察,螺纹加工区段39在加工齿40、41、42的两侧分别具有周侧的圆柱形地伸延的支撑桥接部44(图3和图4),在加工螺纹时(见图7)支撑桥接部的外直径近似为底孔直径d
vb
,从而在加工螺纹时钻螺纹孔工具的支撑桥接部(44)抵靠在底孔壁上。
35.如还可从图3中得到,第一和第二钻孔切削部s1、s2的外部的切割轮廓在工具旋转时在具有切割轮廓直径(等于底孔直径dk)的钻孔切削部圆形轨迹45上运动。以相同的方式,工具螺纹加工区段39的齿廓在工具旋转时在具有齿廓直径的齿廓圆形轨迹或包络线47(图3和4)上运动。在图3或4中,齿廓直径设计成小于切割轮廓直径(与底孔直径dk相同)。由此,在钻孔切削部圆形轨迹45和齿廓圆形轨迹47之间得到径向的工具自由空间49(图3或4)。在稍后描述的退刀步骤f(图8b)中需要该工具自由空间49。
36.接下来根据图4至图8描述借助于根据本发明的钻螺纹孔工具加工螺纹:因此,在钻孔行程b(图4和5)中,在形成底孔51的情况下,使旋转的钻螺纹孔工具攻入没有底孔的工件5中直至额定孔深tb。在钻孔行程b中,两个钻孔切削部s1、s2与工件5切削接合,而工具螺纹加工区段39保持无负载并且与底孔壁脱开接合。工具轴w与孔轴线a同轴地定向,可自由选择钻螺纹孔工具的进给量vf以及转速n。在图4中在绘出的旋转方向38上例如左旋地进行钻孔过程。
37.在钻孔行程(图5)结束之后,通过以下过程步骤准备攻丝行程g(图8a):即,在钻孔行程b之后,首先进行逆向行程r1(图6),在逆向行程中,使钻螺纹孔工具在与钻孔方向相反的逆向方向上如此程度地从底孔51中引导出来,使得可进行第一偏移行程v1(图7)。在第一偏移行程v1中,将从底孔51中引导出来的钻螺纹孔工具径向地调整径向偏移量δr1。
38.随后,开始攻丝行程(图8a),在攻丝行程中,沿着绕孔轴线a的圆形轨迹53引导径向调整的旋转的钻螺纹孔工具进行圆周转动运动(图7),并且以攻丝进给量和与其同步的攻丝转速将钻螺纹孔工具引入底孔51中。在攻丝行程g中,进行工具旋转以及不仅在相同的同向旋转方向上而且在相同转速下的工具圆周运动,例如这在图7中示出。
39.在攻丝行程g(图8a)中,钻螺纹孔工具的螺纹加工区段39加工内螺纹9直至达到额定螺纹深度tg。随着达到额定螺纹深度tg,使攻丝行程g延伸到自由切削行程f(图8a)中。在自由切削行程f中,钻螺纹孔工具的进给量vf和转速n不再彼此同步。因此,在没有螺距的情况下加工紧接着内螺纹9的环绕的退刀槽13。
40.在加工环绕的退刀槽13之后,进行第二偏移行程v2(图8b),在第二偏移行程中,使钻螺纹孔工具在径向上从退刀槽13中自由移出径向偏移量δr2。这实现了第二逆向行程r2(图8b),在第二逆向行程中,钻螺纹孔工具可无负载地、也就是说在没有螺纹接合的情况下
并且在没有切削接合的情况下从工件螺纹孔1中引导出来。
41.以下描述特别地涉及钻孔过程步骤以及钻螺纹孔工具的钻孔区段:普遍地,在设计钻孔过程步骤时,如此使过程参数(也就是说钻孔工具的转速n以及进给量vf)与钻孔切削部s1、s2在钻孔工具上的位置相协调,使得每个钻孔切削部s1、s2的钻孔切削部负载几乎相同,也就是说,理想地每个钻孔切削部s1、s2的进给量v
fz
(齿进给量)相同。在传统的钻螺纹孔工具(图9和10)中,这通过在钻孔切削部s1、s2之间恒定的步距实现。因此,在图9中,钻孔切削部s1、s2相对于工具轴w对角地相对,从而每个钻孔切削部s1、s2的进给量(齿进给量)几乎相同,这从图10中得到。在图10中,以改进方案示出了传统的钻孔工具的周面。相应地,钻孔切削部s1、s2定位在相同的轴向高度h上。在图10中,钻孔切削部s1、s2分别通过相同的切割宽度s与工件孔的内壁切削接合。在图10中,示出了在钻孔过程中得到的两个钻孔切削部s1、s2的切削行程w1和w2。切削行程w1和w2以升程角β螺旋形地沿着孔内壁伸延,从而在该改进方案(图10)中,得到切削行程w1和w2的直线的伸延。在图10中,切削行程w1和w2不重叠,而是相反地在轴向上无重叠地过渡到彼此中。
42.在图11至图14的实施例中,(与根据图9和图10的现有技术不同地)在两个钻孔切削部s1、s2之间的步距不再相同,而是不同。相应地,在图12中,对于每个钻孔切削部来说,每次钻孔切割的进给量f
fz
不再相同,而是不同。也就是说,在图12中,钻孔切削部s1、s2在钻孔过程中不再均匀地、而是不同地受到负载。根据图12,为第一钻孔切削部s1分配每次钻孔切割最大的进给量v
fz
,也就是说,第一钻孔切削部s1暴露在较大的切割负载下。在图12中,两个钻孔切削部s1、s2在没有轴向高度错移量δh的情况下定位在相同的高度h上。根据图13和14,每个钻孔切削部s1、s2的每个横向切削棱29与工具轴w包夹锐角β1、β2。在图14中(如在具有对称的钻孔切削部分布的传统的钻孔工具中那样)两个钻孔切削部s1、s2的锐角β1、β2设计成相同的。此时,如此选择锐角β1、β2,使得在工具周侧上,也就是说在两个钻孔切削部s1、s2的刀尖33上得到轴向的高度错移量δh,也就是说钻孔切削部s1、s2的不同高度位置h1、h2,如在图14中示出的那样。
43.尽管距离间隔不同,为了保证近似均匀的钻孔切削部s1、s2的负载,在根据图15至18的实施例中,钻孔切削部s1、s2不再定位在相同的轴向高度h1、h2上,而是相反地布置在不同的高度位置h1和h2上。如此选择高度位置h1和h2,使得与图11和12相比,得到两个钻孔切削部s1、s2的更均匀的钻孔切削部负载。根据在钻孔过程中的过程参数(也就是说工具转速,工具进给量)并且根据相应的步距选择高度位置h1和h2。
44.如从图16中得到的那样,钻孔切削部s1、s2(与图9和10相似地)分别通过相同的切割宽度s与孔内壁切削接合。此外,在图14中,切削行程w1和w2彼此不重叠,而是相反地无重叠地过渡到彼此中。
45.根据图17和图18,每个钻孔切削部s1、s2的每个横向切削棱29与工具轴线w包夹锐角β1、β2。在图18中,两个钻孔切削部s1、s2的锐角β1、β2(如在具有对称的钻孔切削部分布的传统的钻孔工具中那样)设计成不是一样的,而是相反地设计成彼此不同。此时,如此选择锐角β1、β2,使得在工具周侧上,也就是说在两个钻孔切削部s1、s2的刀尖33上得到轴向的高度错移量δh,也就是说钻孔切削部s1、s2的不同高度位置h1、h2,如在图16中示出的那样。
46.附图标记清单
47.1 螺纹孔
48.3 孔底部
49.5 工件
50.7 螺纹下沉部
51.8 边/刃带
52.9 内螺纹
53.13 环绕的退刀槽
54.14 孔钻桥接部
55.15 夹紧柄
56.17 工具体
57.14、16 孔钻桥接部
58.s1、s2 钻孔切削部
59.23 容屑槽
60.25 纵向切削棱
61.29 横向切削棱
62.30 端侧的自由面
63.33 刀尖
64.35 孔钻桥接部自由面
65.37 导向边
66.38 在钻孔行程中的旋转方向
67.39 工具螺纹加工区段
68.40、41、42 螺纹加工区段的切割齿
69.43 备选的切割齿
70.44 基础支撑件
71.45 钻孔切削部圆形轨迹
72.47 螺纹加工区段39的包络线
73.49 工具自由空间
74.51 底孔
75.53 圆周圆形轨迹
76.t
b 额定孔深
77.d
k 底径
78.u 工具周向
79.α 楔角
80.a 孔轴线
81.w 工具轴
82.b 钻孔行程
83.g 攻丝行程
84.f 自由切削行程
85.v1、v2 偏移行程
86.δr1、δr
2 径向偏移量
87.δh 高度错移量
88.h1、h2 高度位置
89.β1、β
2 锐角
90.v
f 进给量
91.t
g 额定螺纹深度
再多了解一些
本文用于创业者技术爱好者查询,仅供学习研究,如用于商业用途,请联系技术所有人。