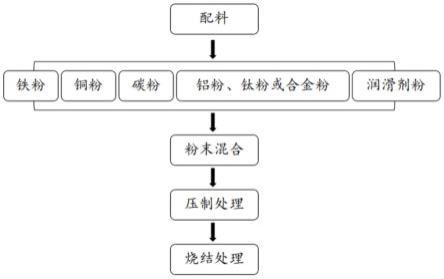
一种含al和ti的fe-cu-c基合金材料及其制备方法
技术领域
1.本发明涉及粉末冶金材料技术领域,尤其涉及一种含al和ti的fe-cu-c基合金材料及其制备方法。
背景技术:
2.高温结构件广泛应用于航空航天领域,随着特殊应用场景的不断发展,对高温结构件的高温强度、高温抗氧化性能等关键性能的要求也不断提高。如何通过易于加工且具有优良高温强度和高温抗氧化性能的合金材料替代传统铁基金属材料制备高温结构件,是领域内研究的重点。
3.为改善传统铁基材料的抗氧化性能,许多研究者通过在合金表面添加抗氧化涂层来提高合金的抗氧化性能。然而,由于涂层的厚度有限,且涂层、基体层以及在氧化过程中出现的氧化层三者的热膨胀系数不同,在氧化环境中的涂层之间以及涂层与基体层之间均存在内应力,消耗涂层的同时氧化层会发生剥落,造成材料的二次氧化。
4.在铁基材料中,通常还会加入如cr、ni、al、si等合金元素来提高合金的抗氧化性能,各元素对铁基合金高温抗氧化的影响程度大小顺序为al>si>cr>ni。在实际开发和应用中,上述元素的应用存在以下不足:1)在高温氧化过程中,ni需要与其他元素的相互作用才能对铁基高温合金的抗氧化性有一定的影响。2)在铁基合金中加入cr元素,合金在氧化后会形成具有一定保护性的氧化膜,但在富fe的氧化层中存在大量的裂纹,氧化层不致密。随着氧化时间的延长,氧化外层剥落,从而使得内层发生二次氧化;并且,在fe基合金中加入cr元素成本高,因此不利于材料的生产。3)将al元素加入铁基合金中,在氧化过程中,合金会形成al2o3的氧化膜,且随着al含量的增加,合金的抗氧化性能提高,但是al2o3氧化膜附着力差,al含量越高,氧化时形成的al2o3越多且越容易发生剥落,而且al的加入会显著降低合金的力学性能,使得合金的使用受到限制。
5.因此,如何克服现有技术的不足,提高铁基合金材料的高温抗氧化性能,成为亟待解决的技术问题。
技术实现要素:
6.有鉴于此,为了解决传统铁基粉末冶金材料在氧化过程中氧化膜容易开裂,从而导致合金抗氧化性差的问题,本发明提供了一种具有良好的抗氧化性能的含al和ti的fe-cu-c基合金材料及其制备方法,通过组分配比和工艺控制提高合金的自抗氧化性能。
7.一方面,本发明提供一种含al和ti的fe-cu-c基合金材料,包括:碳0.5-1.0wt.%,铜5.0-20.0wt.%,铝和钛共3.0-14.0wt.%,硬脂酸类润滑剂0.5-1.0wt.%,余量为铁,其中,铝至少为1.0wt.%,钛至少为2.0wt.%。
8.进一步地,本发明的含al和ti的fe-cu-c基合金材料,在1000℃下氧化20h后氧化增重不大于80.4mg/cm2。
9.另一方面,本发明提供一种含al和ti的fe-cu-c基合金材料的制备方法,包括:
10.一、配料
11.按以下配比:碳0.5-1.0wt.%,铜5.0-20.0wt.%,铝和钛共3.0-14.0wt.%,硬脂酸类润滑剂0.5-1.0wt.%,余量为铁,进行配料,其中,铝至少为1.0wt.%,钛至少为2.0wt.%,得到原料粉体和润滑剂;
12.二、粉末混合
13.在室温下通过罐磨机对原料粉体进行机械混合,其中,混合时添加0.5-1.0wt.%的硬脂酸类润滑剂,混合转速为500-600rpm,混合时间为60-180min,得到混合粉体;
14.三、压制处理
15.在室温下通过粉末液压机对混合粉体进行压制,压制形式为干压成形,压制压力为400-700mpa,保压时间为30-60s,得到压制生坯;
16.四、烧结处理
17.在非氧化性保护气氛中对压制生坯进行烧结,烧结温度为1050-1250℃,烧结时间为60-180min,升温速率为5℃/min,得到含al和ti的fe-cu-c基合金材料。
18.进一步地,本发明含al和ti的fe-cu-c基合金材料制备方法的步骤一中,铁、铜和碳为单质粉末,其中,铁单质粉末粒度为30-150μm,铜单质粉末粒度为10-50μm,碳单质粉末粒度为2-10μm。
19.进一步地,本发明含al和ti的fe-cu-c基合金材料制备方法的步骤一中,铝为单质粉末、铝钛合金粉末或铁铝合金粉末中的一种,其中,铝单质粉末粒度为1-5μm,铝钛合金粉末粒度为10-50μm,铁铝合金粉末粒度为50-75μm。
20.进一步地,本发明含al和ti的fe-cu-c基合金材料制备方法的步骤一中,钛为单质粉末、铝钛合金粉末或铁钛合金粉末中的一种,其中,钛单质粉末粒度为1-5μm,铝钛合金粉末粒度为10-50μm,铁钛合金粉末粒度为50-75μm。
21.进一步地,本发明含al和ti的fe-cu-c基合金材料制备方法的步骤一中,铝钛合金中al与ti的摩尔比为1:3,铁铝合金中fe与al的摩尔比为3:1,铁钛合金中fe与ti的摩尔比为2:1。
22.进一步地,本发明含al和ti的fe-cu-c基合金材料制备方法的步骤一中,硬脂酸类润滑剂为硬脂酸或硬脂酸锌中的一种。
23.进一步地,本发明含al和ti的fe-cu-c基合金材料制备方法的步骤四中,非氧化性保护气氛为纯氢气氛或氮-氢混合气氛。
24.进一步地,本发明含al和ti的fe-cu-c基合金材料制备方法的氮-氢混合气氛中,氮气与氢气的体积比为10:90。
25.本发明含al和ti的fe-cu-c基合金材料及其制备方法,具有以下有益效果:
26.1.通过添加铝和钛元素,改善合金在氧化过程中样品表面出现优先优化的现象,使得合金材料在氧化过程中形成相对致密的氧化表面,从而提高合金的抗氧化性。
27.2.通过添加铝和钛元素,改善铁基合金材料氧化过程中氧化层与基体层之间热膨胀系数差异较大的问题,提高氧化层与基体层之间的附着力,避免氧化层的开裂,从而提高合金的抗氧化性。
28.3.本发明的制备方法操作简单、能耗小、成本低、生产效率高,适于工业推广应用。
附图说明
29.为了更清楚地说明本发明实施例的技术方案,下面将对实施例中所需要使用的附图作简单地介绍,显而易见地,下面描述中的附图仅仅是本发明的一些实施例,对于本领域普通技术人员来讲,在不付出创造性劳动的前提下,还可以根据这些附图获得其它的附图。
30.图1为本发明示例性实施例1-5的含al和ti的fe-cu-c基合金材料的制备方法的流程图;
31.图2是根据本发明示例性实施例1-5以及对比例制备材料试样在1000℃下氧化20h后单位面积增重曲线图;
32.图3为根据本发明示例性实施例2制备材料试样的氧化截面sem图及eds谱图;
33.图4为根据本发明示例性实施例3制备材料试样的氧化表面sem图;
34.图5为根据本发明示例性实施例4制备材料试样的氧化截面sem图及eds谱图;
35.图6为根据本发明示例性实施例5制备材料试样的氧化截面sem图;
36.图7为根据本发明对比例制备材料试样的氧化表面sem图;
37.图8为根据本发明对比例制备材料试样的氧化截面sem图。
具体实施方式
38.下面结合附图对本发明实施例进行详细描述。
39.需说明的是,在不冲突的情况下,以下实施例及实施例中的特征可以相互组合;并且,基于本公开中的实施例,本领域普通技术人员在没有作出创造性劳动前提下所获得的所有其他实施例,都属于本公开保护的范围。
40.图1为本发明含al和ti的fe-cu-c基合金材料的制备方法的流程图;本发明实施例1至实施例5为图1所示方法的优选实施例。
41.实施例1
42.一、配料
43.按以下配比:碳0.8wt.%,铜5.0wt.%,铝1.0wt.%,钛2.0wt.%,硬脂酸0.7wt.%,余量为铁,进行配料,其中,铁、铜和碳为单质粉末,铁单质粉末粒度为30-150μm,铜单质粉末粒度为10-50μm,碳单质粉末粒度为2-10μm;铝为单质粉末,铝单质粉末粒度为1-5μm;钛为单质粉末,钛单质粉末粒度为1-5μm,得到原料粉体和硬脂酸润滑剂;
44.二、粉末混合
45.在室温下通过罐磨机对原料粉体进行机械混合,其中,混合时添加0.7wt.%的硬脂酸作为润滑剂,混合转速为500rpm,混合时间为60min,得到混合粉体;
46.三、压制处理
47.在室温下通过粉末液压机对混合粉体进行压制,压制形式为干压成形,压制压力为500mpa,保压时间为30s,得到压制生坯,生坯密度为6.60g/cm3;
48.四、烧结处理
49.在纯氢气保护气氛中对压制生坯进行烧结,烧结温度为1050℃,烧结时间为180min,升温速率为5℃/min,得到含al和ti的fe-cu-c基合金材料。
50.实施例2
51.一、配料
52.按以下配比:碳0.8wt.%,铜10.0wt.%,铝为2.0wt.%,钛为2.0wt.%,硬脂酸0.5wt.%,余量为铁,进行配料,其中,铁、铜和碳为单质粉末,铁单质粉末粒度为30-150μm,铜单质粉末粒度为10-50μm,碳单质粉末粒度为2-10μm;铝为单质粉末,铝单质粉末粒度为1-5μm;钛为单质粉末,钛单质粉末粒度为1-5μm,得到原料粉体和硬脂酸润滑剂;
53.二、粉末混合
54.在室温下通过罐磨机对原料粉体进行机械混合,其中,混合时添加0.5wt.%的硬脂酸作为润滑剂,混合转速为550rpm,混合时间为120min,得到混合粉体;
55.三、压制处理
56.在室温下通过粉末液压机对混合粉体进行压制,压制形式为干压成形,压制压力为550mpa,保压时间为45s,得到压制生坯,生坯密度为6.61g/cm3;
57.四、烧结处理
58.在氮气与氢气的体积比为10:90的氮-氢混合气氛中对压制生坯进行烧结,烧结温度为1140℃,烧结时间为90min,升温速率为5℃/min,得到含al和ti的fe-cu-c基合金材料。
59.实施例3
60.一、配料
61.按以下配比:碳0.5wt.%,铜15.0wt.%,铝为4.0wt.%,钛为10.0wt.%,硬脂酸钠0.8wt.%,余量为铁,进行配料,其中,铁、铜和碳为单质粉末,铁单质粉末粒度为30-150μm,铜单质粉末粒度为10-50μm,碳单质粉末粒度为2-10μm;铝为单质粉末,铝单质粉末粒度为1-5μm;钛以铁钛合金粉末的形式配比,铁钛合金粉末粒度为50-75μm,铁钛合金中fe与ti的摩尔比为2:1,得到原料粉体和硬脂酸钠润滑剂;
62.二、粉末混合
63.在室温下通过罐磨机对原料粉体进行机械混合,其中,混合时添加0.8wt.%的硬脂酸钠作为润滑剂,混合转速为600rpm,混合时间为120min,得到混合粉体;
64.三、压制处理
65.在室温下通过粉末液压机对混合粉体进行压制,压制形式为干压成形,压制压力为700mpa,保压时间为40s,得到压制生坯,生坯密度为7.43g/cm3;
66.四、烧结处理
67.在纯氢气保护气氛中对压制生坯进行烧结,烧结温度为1100℃,烧结时间为60min,升温速率为5℃/min,得到含al和ti的fe-cu-c基合金材料。
68.实施例4
69.一、配料
70.按以下配比:碳0.8wt.%,铜20.0wt.%,铝为8.0wt.%,钛为2.0wt.%,硬脂酸0.9wt.%,余量为铁,进行配料,其中,铁、铜和碳为单质粉末,铁单质粉末粒度为30-150μm,铜单质粉末粒度为10-50μm,碳单质粉末粒度为2-10μm。铝以铁铝合金粉末的形式配比,铁铝合金粉末粒度为50-75μm,铁铝合金中fe与al的摩尔比为3:1;钛为单质粉末,钛单质粉末粒度为1-5μm,得到原料粉体和润滑剂;
71.二、粉末混合
72.在室温下通过罐磨机对原料粉体进行机械混合,其中,混合时添加0.9wt.%的硬脂酸作为润滑剂,混合时添加0.9wt.%的硬脂酸类润滑剂,混合转速为600rpm,混合时间为
120min,得到混合粉体;
73.三、压制处理
74.在室温下通过粉末液压机对混合粉体进行压制,压制形式为干压成形,压制压力为600mpa,保压时间为50s,得到压制生坯,生坯密度为7.31g/cm3;
75.四、烧结处理
76.在纯氢气保护气氛中对压制生坯进行烧结,烧结温度为1100℃,烧结时间为120min,升温速率为5℃/min,得到含al和ti的fe-cu-c基合金材料。
77.实施例5
78.一、配料
79.按以下配比:碳1.0wt.%,铜15wt.%,铝为1.0wt.%,钛为5.0wt.%,硬脂酸锌1.0wt.%,余量为铁,进行配料,其中,铁、铜和碳为单质粉末,铁单质粉末粒度为30-150μm,铜单质粉末粒度为10-50μm,碳单质粉末粒度为2-10μm;铝和钛均以铝钛合金粉末的形式配比,铝钛合金粉末粒度为10-50μm,铝钛合金中al与ti的摩尔比为1:3,得到原料粉体和硬脂酸锌润滑剂;
80.二、粉末混合
81.在室温下通过罐磨机对原料粉体进行机械混合,其中,混合时添加1.0wt.%的硬脂酸锌作为润滑剂,混合转速为550rpm,混合时间为180min,得到混合粉体;
82.三、压制处理
83.在室温下通过粉末液压机对混合粉体进行压制,压制形式为干压成形,压制压力为400mpa,保压时间为60s,得到压制生坯,生坯密度为7.11g/cm3;
84.四、烧结处理
85.在氮气与氢气的体积比为10:90的氮-氢混合气氛中对压制生坯进行烧结,烧结温度为1250℃,烧结时间为60min,升温速率为5℃/min,得到含al和ti的fe-cu-c基合金材料。
86.实施例6(对比例)
87.一、配料
88.按以下配比:碳0.8wt.%,铜10wt.%,硬脂酸0.7wt.%,余量为铁,进行配料,其中,铁、铜和碳为单质粉末,铁单质粉末粒度为30-150μm,铜单质粉末粒度为10-50μm,碳单质粉末粒度为2-10μm,得到原料粉体和硬脂酸润滑剂;
89.二、粉末混合
90.在室温下通过罐磨机对原料粉体进行机械混合,其中,混合时添加0.7wt.%的硬脂酸作为润滑剂,混合转速为550rpm,混合时间为120min,得到混合粉体;
91.三、压制处理
92.在室温下通过粉末液压机对混合粉体进行压制,压制形式为干压成形,压制压力为500mpa,保压时间为45s,得到压制生坯,生坯密度为6.65g/cm3;
93.四、烧结处理
94.在纯氢气保护气氛中对压制生坯进行烧结,烧结温度为1100℃,烧结时间为120min,升温速率为5℃/min,得到fe基材料。
95.实施例7
96.采用阿基米德排水法对实施例1-5制备的压制生坯以及实施例6制备的压制生坯
进行密度测试,测试结果参见表1,其中,在测试过程中所用天平为电子天平,精度为0.0001。试样编号分别为fcc1、fcc2、fcc3、fcc4、fcc5以及fcc0。
97.表1
98.实施例试样编号加入铝或钛的形式压制压力mpa生坯密度g/cm3实施例1fcc1单质金属粉5006.60实施例2fcc2单质金属粉5506.61实施例3fcc3钛铝合金粉7007.43实施例4fcc4铁铝合金粉6007.31实施例5fcc5铝钛合金粉4007.11实施例6fcc0-5006.65
99.对实施例1-5制备的含al和ti的fe-cu-c基合金材料以及实施例6制备的fe基材料分别进行打磨抛光后,采用线切割将上述材料切割成规格为4mm
×
4mm
×
8mm的氧化试样,然后再将氧化试样采用200#、400#、600#、800#、1200#sic砂纸依次打磨后进行抛光,最后将抛光后的样品进行超声清洗并干燥处理备用,试样编号分别为fcc1、fcc2、fcc3、fcc4、fcc5以及fcc0。
100.根据中华人民共和国航空工业标准hb 5258-2000《钢及高温合金的抗氧化性测定方法》对根据实施例1-6制备的试样进行抗氧化性测试,其中,氧化实验采用的是循环氧化,具体步骤为:对试样进行尺寸测量和称重,并记录,再将样品放入小坩埚中进行称重备用;将马弗炉升温至目标温度,然后将放有样品的小坩埚放入炉中,待马弗炉温度恢复至目标温度后开始计时,在前10h内均每1.0h取样一次,待坩埚冷却至室温后进行称重并记录,在10.0-20.0h时间内每10h取样一次。将得到的样品氧化增重进行计算,得到各合金样品的单位面积增重。合金氧化20.0h后的单位面积增重数据如表2和图2所示。
101.表2
102.实施例试样编号加入铝或钛的形式润滑剂单位面积增重/mg/cm2实施例1fcc1单质金属粉硬脂酸73.4实施例2fcc2单质金属粉硬脂酸78.9实施例3fcc3钛铝合金粉硬脂酸锌57.7实施例4fcc4铁铝合金粉硬脂酸65.0实施例5fcc5铝钛合金粉硬脂酸锌80.4实施例6fcc0-硬脂酸100.4
103.如表2和图2所示,各实施例制备的试样在1000℃下氧化20h后的氧化增重不同。在氧化过程中,添加al和ti元素后合金的单位面积增重均低于未添加合金,说明其抗氧化性由于在铁基合金中添加了合金元素al和ti。结合氧化表面和氧化截面可知,单位面积增重结果与氧化表面和氧化截面图相匹配。
104.采用日立su8020冷场发射扫描电子显微镜对实施例2-6制备的经过1000℃下循环氧化20h后的试样(试样编号分别为fcc2、fcc3、fcc4、fcc5、fcc0)的氧化截面进行表征,实施例2制备试样的氧化截面sem图和eds能谱图参见图3;实施例3制备试样的氧化表面sem图参见图4;实施例4制备试样的氧化截面sem图和eds能谱图参见图5;实施例5制备试样的氧化表面sem图参见图6;实施例6制备试样的氧化表面和截面sem图分别参见图7和图8。
105.如图3所示,实施例2制备的材料的氧化层与基体层结合良好,未发现明显的开裂。从能谱结果可以看出,氧元素含量从外到内逐渐减少。
106.如图4所示,实施例3制备的材料的氧化表面在氧化过程中形成相对致密的氧化层,同时,没有明显的凸起和优先氧化区域产生。
107.如图5所示,实施例4制备的材料的氧化层与基体层结合良好,未发现明显的开裂。从能谱结果可以看出,各元素的质量百分比为fe:cu:al:ti=42.6:20.3:7.8:1.6,基本满足合金原料的配比。
108.如图6所示,实施例5制备的材料氧化后出现明显的氧化层,且氧化层与基体层之间结合良好,并未发现明显的开裂,基体层相对致密。
109.如图7、图8所示,实施例6制备的材料氧化后合金表面出现较多孤岛状区域,说明合金在氧化过程中存在优先氧化;同时,氧化后的氧化截面中,氧化外层出现裂纹,氧化外层与基体层之间结合处也存在裂纹和剥落坑。与实施例2-5制备材料的试样相比,实施例6制备的未添加al和ti的材料试样,氧化更明显,其抗氧化性明显低于添加合金元素后的合金。
110.需要说明的是,根据本发明实施例制备的具有良好的抗氧化性能的含al和ti的fe-cu-c基合金材料方法,显著改善铁基合金氧化过程中氧化层与基体层之间热膨胀系数差异较大的问题,改善形成的氧化膜易剥落的问题,提高氧化层与基体层的附着力,从而提高合金的抗氧化性。
111.以上所述,仅为本发明的具体实施方式,但本发明的保护范围并不局限于此,任何熟悉本技术领域的技术人员在本发明揭露的技术范围内,可轻易想到的变化或替换,都应涵盖在本发明的保护范围之内。因此,本发明的保护范围应以权利要求的保护范围为准。
再多了解一些
本文用于创业者技术爱好者查询,仅供学习研究,如用于商业用途,请联系技术所有人。