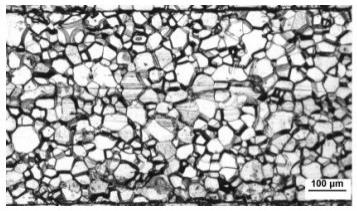
1.本发明涉及钢铁冶金领域和金属材料领域,尤其涉及一种低合金高强度无取向硅钢及其生产方法。
背景技术:
2.硅钢是一种功能材料,一直以来被认为最重要的性能是磁性能。但随着电机行业的蓬勃发展,对硅钢的力学提出了更高的要求,也有了更深的认识。目前,硅钢的高力学性能主要有两方面作用。一方面,为电机的高转速设计提供安全保障,因为高转速意味着转子铁芯将受到高的离心力,需要使用强度较高的硅钢片;另一方面,高强度硅钢片可提升铁芯的加工性能,比如提高铁芯铆接强度,或防止铁芯大冲片发生翘曲等。
3.无取向硅钢各个方向的力学性能不同,轧制方向的力学强度最低,本发明中都以轧制方向力学作为衡量。本发明力学的代表性指标为规定塑性延伸强度rp0.2和上屈服强度reh。规定塑性延伸强度rp0.2是指力学拉伸试验中规定塑性延伸率为0.2%时的应力。上屈服强度reh是指力学拉伸试验中试样发生屈服而力首次下降前的最大应力。
4.普通硅钢要求磁性能优异,所以强化方式仅为si、al、mn的固溶强化,而且主要依靠si元素。常规最高牌号无取向硅钢的si含量可高达3.3%,轧制方向的规定塑性延伸强度rp0.2典型值为420mpa。而对于常规的中低牌号无取向硅钢,若想轧制方向的规定塑性延伸强度rp0.2达到275mpa以上,si的质量百分比需达到2.0%以上,或mn的质量百分比需达到1.0%以上,合金成本特别高。
5.另外,常规无取向硅钢的上屈服强度reh与规定塑性延伸强度rp0.2很接近,二者差异在10mpa以内,没有体现出reh的力学优势。而金属材料在应变发生屈服过程中,所受应力需先达到上屈服强度reh,才能进一步发生屈服现象。从电机运行的安全角度考虑,具备高的上屈服强度reh对于硅钢材料来说更有价值。从这个角度看,上屈服强度reh比规定塑性延伸强度rp0.2更能代表硅钢材料力学性能的优劣。
6.对于si含量1.25-1.55%、mn含量≤0.45%,且不经过常化工序的常规中低牌号无取向硅钢,力学性能较差,轧制方向的规定塑性延伸强度rp0.2仅为215~240mpa,上屈服强度reh仅为220~250mpa;铁损p1.5/50为3.4~4.5w/kg。
7.中国专利申请号201810585897.7的文献,公开一种高强度无取向硅钢、及其制造方法和应用,主要使用si、mn、p的固溶强化,存在合金成本高的不足,且p含量高存在冷轧易断带、磁性能易恶化的风险。
8.中国专利申请号202010522716 .3的文献,公开一种低铁损低时效高强度50w800无取向硅钢及其制造方法,主要使用固溶p进行强化,同样存在p含量高的相关风险。且发明中的产品力学性能偏低。
9.中国专利申请号201910272331 .3的文献,公开一种冷轧无取向电工钢35wd1900及其生产方法,提高强度主要依靠si、p的固溶强化,合金成本较高。且在高si含量钢中继续添加高含量p,冷轧断带的风险更大。
10.综上,常规的中低牌号无取向硅钢,若其轧制方向的规定塑性延伸强度rp0.2达到275mpa以上,需以高合金含量、高成本为代价,且具有reh与rp0.2差异小的不足。
11.本发明针对现有技术存在的不足,提供一种轧制方向规定塑性延伸强度rp0.2≥275mpa 、上屈服强度reh≥300mpa的低合金高强度无取向硅钢及其生产方法。在较低的合金含量下,主要使用细晶强化、析出强化来提升产品的力学性能。产品同时具备优异的规定塑性延伸强度rp0.2和上屈服强度reh,且产品reh明显高于rp0.2。产品可广泛用于风力发电机、柴油发电机等中大型电机。
技术实现要素:
12.本发明的目的就是针对上述问题,提供一种低合金高强度无取向硅钢及其生产方法。
13.本发明的目的是这样实现的:一种低合金高强度无取向硅钢及其生产方法,包括以下步骤:转炉冶炼
→
rh精炼
→
连铸
→
加热炉加热
→
热轧
→
酸洗
→
冷轧
→
退火
→
涂层;所述rh精炼工序析出强化元素含量要求:nb为0.0010~0.0030%,ti为0.0005~0.0015%,v为0.0010~0.0025%,0.0045%<ti nb v<0.0065%;c为0.0012-0.0035%,n为0.0012-0.0035%,si为1.25-1.55%,al≤0.35%,mn≤0.45%,p≤0.02%,s≤0.0035%;所述热轧工序要求加热温度1250~1330℃,加热时间5~7h,热轧终轧温度为800~850℃,卷取温度为540~580℃,热轧材的厚度≤2.0mm;所述退火工序:冷轧卷进行退火,退火温度t℃与退火速度cm/min需满足关系式:0.0467
·c2 ‑ꢀ
9.593
·
c 1269 ≤ t ≤ 0.0467
·c2 ‑ꢀ
9.593
·
c 1329。
14.进一步的讲,所述硅钢轧制方向的力学为:规定塑性延伸强度275mpa≤ rp0.2≤320mpa、上屈服强度300mpa≤reh≤350mpa;磁性能为:铁损p1.5/50≤6.0w/kg,磁极化强度1.68t≤j5000≤1.72t。
15.进一步的讲,冷轧目标厚度为0.496~0.504mm。
16.进一步的讲,退火工序使用炉膛长度200~215米的连续退火炉,退火速度为100~150m/min。
17.进一步的讲,其化学成分为:si:1.25-1.55%,al≤0.35%,mn≤0.45%,p≤0.02%,s≤0.0035%,及总重量含量不超过0.5%的sn、sb、b、ce、la 中任一种或多种。
18.本发明的有益效果是:(1)针对常规中低牌号无取向硅钢,主合金含量为si:1.25-1.55%,al:≤0.35%,mn:≤0.45%时,轧制方向规定塑性延伸强度rp0.2较低的现状,通过使用nb、ti、v碳氮化物的析出强化,和细晶强化,使成品轧制方向规定塑性延伸强度rp0.2提升至275mpa以上。
19.(2)针对常规中低牌号无取向硅钢上屈服强度reh与规定塑性延伸强度rp0.2差异在10mpa以内的现状,通过使用nb、ti、v碳氮化物的析出强化,和细晶强化,抑制屈服前期位错滑移系的大规模开动,从而有效提升硅钢的上屈服强度reh。通过此方法,对于本发明主合金含量为si:1.25-1.55%,al:≤0.35%,mn:≤0.45%的硅钢,轧制方向的上屈服强度reh可达到300mpa及以上。
20.(3)针对常规中低牌号无取向硅钢,当轧制方向规定塑性延伸强度rp0.2达到275mpa以上时,si的质量百分比需达到2.0%以上,或mn的质量百分比需达到1.0%以上,合金成本特别高的现状。本发明的低合金高强度无取向硅钢,通过析出强化和细晶强化方法提
升强度,具有产品合金成本低的有益效果。
附图说明
21.下面结合附图对本发明作进一步的描述。
22.图1是850℃ 退火温度下成品板组织图。
23.图2是790℃ 退火温度下成品板组织图。
24.图3是940℃ 退火温度下成品板组织图。
具体实施方式
25.本发明提供一种低合金高强度无取向硅钢及其生产方法。
26.生产方法中,硅钢的主合金元素含量保持低水平,主要通过细晶强化和析出强化来实现提升力学性能的目的。通过限定析出强化元素nb、ti、v的含量,并配以特定的热轧工艺参数,确保析出相细小弥散析出,实现析出强化目的。通过制定退火温度和退火速度的匹配关系式,合理匹配退火温度和退火速度,使产品具备合适的晶粒尺寸,实现细晶强化目的。析出强化与细晶强化相结合,一方面整体提升产品的力学水平;另一方面加强抑制屈服前期位错滑移系的大规模开动,使硅钢材料具备更高的上屈服强度reh。析出强化和细晶强化通常会劣化产品磁性能。本发明强化方法的设计,通过对成分、工艺的严格限制,保障不严重劣化磁性能,从而实现力学性能和磁性能的兼顾。综合以上方法,可制备一种低合金高强度无取向硅钢,产品力学可达到:轧制方向规定塑性延伸强度rp0.2≥275mpa 、上屈服强度reh≥300mpa;产品磁性能可达到:铁损p1.5/50≤6.0w/kg,磁极化强度j5000≥1.68t 。产品si、mn含量以质量百分比计,分别不超过1.55%、0.45%,具备较低的合金成本。产品可广泛用作风力发电机、柴油发电机等中大型电机的铁芯材料。
27.本发明的技术方案具体为:si、al、mn是本发明硅钢的主合金元素,可增大材料电阻率,降低铁损。同时,引发材料基体晶格畸变,一定程度上提高材料强度。这三个元素为本发明营造一个基本的元素环境,是实现材料力学性能和磁性能的基础保障。综合考虑磁性能、力学性能、产品成本而制定其含量要求。要求si:1.25-1.55%,mn≤0.45%, al≤0.35%。
28.ti、nb、v为主要的析出强化元素,在热轧过程中与钢中的c、n元素相结合而细小弥散析出,起到析出强化的作用。析出的碳氮化物一方面钉扎晶界、位错,抑制形变过程晶界、位错的运动,从而整体提高力学强度。另一方面,在形变过程位错滑移系开动之初,可强烈抑制位错滑移系的大规模开动,所以可显著提升材料的上屈服强度reh。ti、nb、v的含量设计考究,含量的下限是考虑起到足够的析出强化效果而设计得出,含量的上限设计是为防止析出相严重恶化磁性能。要求ti:0.0005-0.0015%,nb:0.0010-0.0030%,v:0.0010-0.0025%, ti、nb、v的总量:0.0045-0.0065%。
29.c、n元素在普通无取向硅钢中一般被视为杂质元素,在本发明中为析出强化必不可少的元素。含量的下限设计,是为了在碳氮化物析出后,基体中能够保留一部分固溶c、n,防止产品成为无间隙原子钢。固溶的c、n是以间隙原子的状态存在于基体中,可增强晶格畸变,产生的应力场可与位错应力场、析出相应力场相互作用,增加材料强度。c、n含量过低,则都以碳氮化物的形式存在于钢中,使钢成为无间隙原子钢,不利于力学性能的提升。因
此,根据ti、nb、v的含量要求,设定了c、n含量的下限。同时,c、n含量不可过高。否则在模拟电机运行的低温时效过程中,会析出大量的含铁碳氮化物,严重劣化产品磁性能。综合考虑以上,要求c:0.0012-0.0035%,n:0.0012-0.0035%。
30.p元素具有明显的固溶强化效果,但对不常化处理的中低牌号硅钢来说,p含量高会严重劣化磁性能,且使冷轧过程存在脆断风险。考虑到实际生产控制水平,要求p≤0.02%。
31.s元素在本发明中与常规无取向硅钢中一样,被认为是杂质元素。本发明不使用mns的析出强化,s含量高会增大mns的析出量、恶化产品磁性能。故要求s≤0.0035%。
32.本发明生产流程为:转炉冶炼
→
rh精炼
→
连铸
→
加热炉加热
→
热轧
→
酸洗
→
冷轧
→
退火
→
涂层。
33.rh精炼过程需达到本发明的成分要求,特别是对析出强化元素nb、ti、v、c、n需进行严格把控,为热轧过程析出相形成创造前提条件。
34.精炼得到本发明要求的钢水成分后,通过连铸制备成铸坯。
35.铸坯在加热炉加热5小时及以上,加热温度不低于1250℃。以确保nb、ti、v、c、n元素全部且均匀地溶解在铸坯中。如果未全部溶解,则热轧过程析出效果不好,即不利于析出相的细小弥散析出。如果未均匀溶解在铸坯中,则可能导致最终成品性能的不均匀。
36.热轧终轧温度和热轧材厚度的设定范围,目的在于创造足够的热轧储能。热轧储能可以被析出过程所利用,与析出相的析出吉布斯自由能相叠加,一起做为析出动能,促进析出相细小弥散析出。终轧温度高,热轧储能小;终轧温度低,热轧困难。热轧材厚度越薄,热轧储能越大。结合生产实际,经多次摸索,确定本发明的热轧终轧温度范围为800~850℃,热轧材厚度≤2.0mm。
37.热轧卷取温度的设计原理为,卷取温度尽可能与析出相的最大形核率温度相对应。因特定温度下析出相的体积分数不变,形核率越大,那么析出相的个数最多,析出相也就最细小。析出相越细小,对产品力学的提升效果越大。理论上,成分、生产工艺确定时,析出相的最大形核率温度是确定的。但实际生产过程中,成分、工艺有一定的允许偏差,所以析出相的最大形核率温度也有一定的变化。根据多次摸索,本发明要求卷取温度介于540~580℃。
38.冷轧目标厚度主要影响产品磁性能。本发明热轧卷酸洗后,冷轧至目标厚度0.496~0.504mm。
39.冷轧卷进行退火,退火设备为炉膛长度约208米的连续退火炉,退火速度可选取100~150m/min。退火温度t(℃)与退火速度c(m/min)需满足关系式:0.0467
·c2 ‑ꢀ
9.593
·
c 1269 ≤ t ≤ 0.0467
·c2 ‑ꢀ
9.593
·
c 1329。退火的主要作用是使冷轧组织发生再结晶,通过不同的退火工艺来调整成品晶粒尺寸、织构,从而使成品性能满足用户需求。晶界可以抑制形变过程中位错的运动,也可以抑制屈服前期位错滑移系的大规模开动。所以增大基体中的晶界总面积,可以整体提升屈服强度,并且使材料具备较高的上屈服强度reh。本发明细晶强化是主要强化方式之一,不同的退火工艺可得到不同的晶粒尺寸,对应产品也就具备不同的性能。上述关系式是多次摸索得到的规律。 关系式的上限温度是为满足本发明力学要求而设计,采用上限温度可以达到本发明的基本力学要求;下限温度是兼顾产品磁性能所需的最低温度,温度若继续降低以偏近下限温度,则力学会进一步提升。
40.为了充分了解本发明的目的、特征及功效,通过下述具体实施方式,对本发明作详细说明。本发明的工艺方法除下述内容外,其余均采用本领域的常规方法或装置。下述名词术语除非另有说明,否则均具有本领域技术人员通常理解的含义。
41.本文使用的术语“第一”“第二”等不表示任何顺序或重要性,而是用于区别一个要素与另一要素,术语“该”“所述”“一个”和“一种”不表示数量的限制,而是表示存在至少一个所提及的对象。另外,本文公开的所有范围包括端点,可独立地组合。
42.具体的,本发明提供了一种轧制方向规定塑性延伸强度rp0.2≥275mpa,上屈服强度reh≥300mpa的低合金高强度无取向硅钢及其生产方法。
43.具体包括以下步骤:(1)转炉出钢后,使用rh精炼得到本发明要求的钢水成分。nb:0.0010~0.0030%,ti:0.0005~0.0015%,v:0.0010~0.0025%,且0.0045%<ti nb v<0.0065%; c:0.0012-0.0035%,n:0.0012-0.0035%;si:1.25-1.55%,al≤0.35%,mn≤0.45%,p≤0.02%,s≤0.0035%。另外,为了改善硅钢成品性能的需求,还可考虑再添加总含量不超过0.5%的sn、sb、b、ce、la中一种或多种。
44.(2)对所得钢水进行连续浇铸,形成一定尺寸规格的连铸坯。铸坯厚度一般介于210~240mm,铸坯尺寸对本发明性能的影响很小,不做刻意要求。
45.(3)对铸坯进行加热,要求加热温度≥1250℃,加热时间≥5h,然后热轧至≤2.0mm。粗轧温度对本发明不构成本质影响,不做过多说明,本发明使用900~1000℃。热轧终轧温度介于800~850℃,卷取温度介于540~580℃。
46.(4)热轧卷进行酸洗。酸洗无过多要求,以酸洗后表面无氧化铁皮残留为宜。
47.(5)使用廿辊轧机或连轧机将酸洗后的热轧卷轧至目标厚度0.496~0.504mm。
48.(6)对冷轧卷进行退火、涂层。本发明退火设备为炉膛有效加热长度约208米的连续退火炉,退火温度t(℃)与退火速度c(m/min)需满足以下关系式的规定。
49.0.0467
·c2 ‑ꢀ
9.593
·
c 1269 ≤ t ≤ 0.0467
·c2 ‑ꢀ
9.593
·
c 1329
ꢀꢀꢀꢀ
(关系式一)(7)依据gb/t 228进行轧向试样的力学检测。依据gb/t 3655进行磁性检测。
50.需要特别说明的是,关系式一仅适用于按照本发明方法进行热处理的情况,因为不同炉膛长度的热处理设备的热处理能力差别很大。
51.实施例
52.下面通过实施例的方式进一步说明本发明,但并不因此将本发明限制在所述的实施例范围之中。下列实施例中未注明具体条件的实验方法,按照常规方法和条件。
53.本发明冷轧卷退火过程使用炉膛有效加热长度约208m的连续炉。后续不再特别说明。
54.实施例1rh精炼得到主合金目标成分为1.41%si-0.23%al-0.35%mn的钢水,ti、nb、v含量见下表。钢水浇铸成截面尺寸230
×
1100mm的铸坯。铸坯加热温度1260℃,加热5.5h。铸坯粗轧至厚度31mm,在热连轧机组经七道次轧到目标厚度1.96mm,精轧终轧温度为840~850℃,卷
取温度为550~560℃。热轧卷酸洗后,在连轧机组轧制到0.498mm。冷轧卷进行退火,退火速度110m/min,退火温度830℃。对成品进行磁性和力学检测,磁性检测使用爱泼斯坦方圈,力学检测使用与轧制方向平行的纵向试样,成品性能见下表。
55.对比例4、5,(ti nb v)总含量未达到发明要求下限,屈服强度低。对比例6,(ti nb v)总含量超出发明要求上限,磁性能恶化较明显,磁极化强度j5000明显偏低。
56.发明例1、2、3析出强化元素nb、ti、v满足本发明要求,表现出优良的力学性能和磁性能。
57.实施例2rh精炼得到主合金目标成分为1.52%si-0.21%al-0.35%mn,(nb、ti、v)总量为0.0055~0.0061%的钢水,钢水浇铸成截面尺寸210
×
1080mm的铸坯。铸坯加热温度1280℃,加热6小时10分。铸坯粗轧至厚度36mm,在热连轧机组经七道次轧到目标厚度1.89mm,精轧终轧温度、卷取温度见下表。热轧卷酸洗后,在廿辊轧机轧制到0.50mm。冷轧卷进行退火,退火速度133m/min,退火温度840℃。对成品进行磁性和力学检测,磁性检测使用爱泼斯坦方圈,力学检测使用与轧制方向平行的纵向试样,成品性能见下表。
58.对比例4、5、6,热轧终轧温度、卷取温度未达到发明要求范围,对析出相的细小弥散析出造成影响,屈服强度低。
59.发明例1、2、3,热轧终轧温度、卷取温度满足本发明设计范围,为析出相的细小弥散析出创造有利条件,成品力学性能都较高。
60.实施例3rh精炼得到主合金目标成分为1.28%si-0.26%al-0.41%mn,(nb、ti、v)总量为0.0057~0.0064%的钢水,钢水浇铸成截面尺寸210
×
1150mm的铸坯。铸坯加热温度1310℃,加热5h。铸坯粗轧至厚度38mm,在热连轧机组经七道次轧到目标厚度2.0mm,精轧终轧温度为820~830℃,卷取温度为560~570℃。热轧卷酸洗后,在连轧机轧制到0.497mm。冷轧卷进行
退火,退火速度、退火温度见下表。对成品进行磁性和力学检测,磁性检测使用爱泼斯坦方圈,力学检测使用与轧制方向平行的纵向试样,成品性能见下表。对于不满足本发明要求的,以下划线标示。
61.上表发明例1和发明例4,满足本发明退火温度和退火速度的匹配关系式,力学性能、磁性能都达到了本发明的目标。
62.对比例2、3、5、6,退火温度和退火速度没有满足本发明要求的匹配关系。退火温度低于下限的,铁损未达到本发明目标;退火温度高于上限的,力学性能未达到本发明目标。
63.上表发明例4、对比例5、对比例6,退火速度为134m/min,退火温度分别850、790、940℃,对应的成品板金相组织如下图所示。790℃退火温度低,导致成品未完全再结晶,是铁损差的主要原因。940℃退火温度高,晶粒尺寸过大,是力学低的主要原因。
64.以上所述仅为本发明的具体实施例,但本发明所保护范围的结构特征并不限于此,任何本领域的技术人员在本发明的领域内,所作的变化或修饰皆涵盖在本发明的专利范围内。
再多了解一些
本文用于创业者技术爱好者查询,仅供学习研究,如用于商业用途,请联系技术所有人。