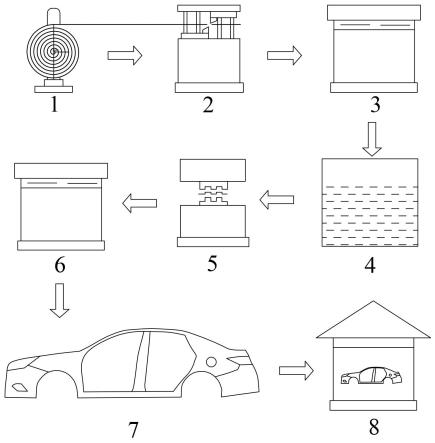
一种超硬铝合金7075耐蚀汽车b柱零件冷冲压成形方法
技术领域
1.本发明属于汽车零部件加工技术领域,具体涉及一种超硬铝合金7075耐蚀汽车b柱零件冷冲压成形方法。
背景技术:
2.全球节能减排的标准不断提高,节能减排压力愈发凸显。汽车制造工业中,汽车轻量化是最容易实现、潜力相对较大的方式,也是汽车未来发展的大势所趋。汽车轻量化的有效途径有结构轻量化、工艺轻量化、材料轻量化三个方面,其中材料轻量化是当前实现轻量化最主要的研究与发展方向,为当前轻量化的核心,结构轻量化与工艺轻量化起辅助作用。铝合金由于比强度大、耐磨性好、耐蚀性强及回收利用率高等优点,在当前各类轻质材料中最为主流,仅次于钢材的用量。
3.超硬铝合金7075属于al-zn-mg-cu系可热处理强化多元时效合金,是商用最强力铝合金之一,具有密度小、比强度高、韧性好及成本较低等一系列优点,广泛用于航天、航空和交通运输领域,相较5000系、6000系铝合金及高强钢有更显著的轻量化效果。然而,超硬铝合金7075峰值时效(t6)状态下强度最高,但是室温成形能力低且对应力腐蚀很敏感,成形后回弹量很大,给超硬铝合金7075-t6板材冲压成形大规模应用带来很大的挑战。双级时效可以显著提高超硬铝合金7075的抗应力腐蚀性能,却使其抗拉强度和屈服强度大幅度下降,在预时效之后进行短时高温回归,然后再次进行时效,这种三级时效称为回归再时效,能使晶界上连续网状分布的析出相转化为断续析出物,既保持了材料强度性能,又显著改善了超硬铝合金7075的抗应力腐蚀性能。中国发明cn102216484a公开了一种铝合金薄板构件的成形方法,中国发明cn102712985a公开了成形复杂形状部件的方法,中国发明cn109433924a公开了一种实现模内快速成形和淬火的模具,均属于成形-淬火复合成形技术。热成形技术虽然能提高铝合金复杂零件的成品率,但超硬铝合金7075对冷却速度敏感,模内淬火冷却速率控制要求较高。超硬铝合金7075-t6中的析出物在温成形温度范围内受到影响,导致材料强度降低,后续工艺难以恢复。同时,刀具和板材之间的润滑条件在高温下变差,成形零件的表面质量较差。
技术实现要素:
4.为了解决上述技术问题,本发明提供一种超硬铝合金7075耐蚀汽车b柱零件冷冲压成形方法,该方法将超硬铝合金7075-t6板材预先进行双级固溶处理,随后在室温冷水中淬火,形成过饱和固溶体w态,然后进行冷冲压成形,最后再通过预时效加烘烤时效,以提高零件的力学性能和耐蚀性能。
5.一种超硬铝合金7075耐蚀汽车b柱零件冷冲压成形方法的目的通过如下技术方案来实现,包括以下步骤:步骤一,采用商业成形软件dynaform对汽车b柱零件进行毛坯尺寸反求,计算出毛坯形状尺寸,并通过模具完成下料;
步骤二,对步骤一所得的坯料进行双级固溶处理。先将固溶加热炉设定为初级固溶温度,待温度恒定后,把坯料插入固溶加热炉内加热,待坯料温度达到初级固溶温度后保温一定时间,然后将固溶加热炉的温度升高到二级固溶温度,保温一定时间,完成固溶处理;步骤三,将步骤二固溶处理后的坯料从固溶加热炉取出,迅速浸入冷水中淬火,待冷却至室温后得到过饱和固溶体即w态坯料;步骤四,将步骤三所得的w态坯料放入冷拉深切边复合模具完成汽车b柱零件拉深成形和切边,制得汽车b柱零件;步骤五,从步骤四中的拉深切边复合模具中取出汽车b柱零件,放入另一时效加热炉进行预时效,取出后室温冷却,得到预时效的汽车b柱零件;步骤六,将步骤五所得的预时效汽车b柱零件完成车身焊装,车身油漆后随车身进入烘烤房烘烤。
6.优选地,步骤二所述的双级固溶处理,初级固溶温度为460℃,保温60min;二级固溶温度为480℃,保温30 min。
7.优选地,步骤三所述的浸入冷水这一过程用时不超过10秒。
8.优选地,步骤四所述的汽车b柱零件拉深成形过程中凸模下行速度为14毫米/秒。
9.优选地,步骤五所述的预时效温度为120℃,保温60 min,在这一条件下过饱和固溶体主要析出相是gp区和半共格亚稳相η
´
,且在晶界η
´
相呈网状连续分布。
10.进一步地,步骤六所述的车身油漆烘烤温度为180℃,时间为30 min。
11.进一步地,步骤六所述的汽车b柱零件焊装后随车身经过180℃烘烤30min后,晶内析出相尺寸有所长大,开始析出短棒状析出相(η
´
相),以获得较高的强度;同时,晶界析出相开始长大,并呈现长条状的不连续分布,溶断了晶界的网状析出相,有效提升了耐蚀性。
12.步骤六所述汽车b柱零件随车身经过180℃烘烤30min后,b柱零件抗拉强度达到559 mpa,相较峰值时效t6条件抗拉强度565mpa仅损失了1.06%;导电率却从31.07%iacs 上升为42.37%iacs,相较双级时效t73条件下40%iacs 略有提高。
13.与现有技术相比,本发明具有如下的有益效果:(1)本发明通过双级固溶处理获得w态铝合金坯料,随后冷冲压成形制得汽车b柱零件,相较热冲压成形和热冲压淬火一体化成形方法,冷成形克服了热冲压模具成本高、生产效率低、表面氧化严重及冷却速率控制难等问题。
14.(2)本发明属于冷成形工艺,相比热成形工艺对成型设备要求低。由于铝合金的固溶温度与其淬火敏感区间仅相差几十摄氏度,所以热成形温度区间相对较窄。铝合金的热传导率大,散热速度快,材料的温度容易变化,因此,热成形过程中,固溶后铝合金板材的转移和成形需要在很短时间内完成,这就对成形设备提出了更高要求。
15.(3)本发明采用双级固溶处理,比单级固溶处理可获得更高程度的过饱和固溶体,为后续时效处理做好组织准备。
16.(4)本发明对冷冲压成形后的零件综合油漆烘烤时效进行双级时效处理,在维持较高的强度前提下,提升了零件耐蚀性能,同时结合油漆烘烤工艺,提高了生产效率。
附图说明
17.图1为本发明的超硬铝合金7075汽车b柱零件冷冲压成形工艺流程图。
18.图2为本发明的超硬铝合金7075汽车b柱零件冷冲压成形工艺方案。
19.附图标记说明1—开卷,2—落料,3—固溶处理,4—冷水淬火,5—冷冲压成形,6—预时效,7—车身焊装,8—油漆烘烤。
具体实施方式
20.下面结合具体实施例对本发明进行详细说明。以下实施例将有助于本领域的技术人员进一步理解本发明,但不以任何形式限制本发明。特别指出的是,在本发明构思的前提下做出若干变形和改进,均属于本发明的保护范围。
21.本发明属于汽车零部件加工技术领域,具体说是峰值时效高强铝合金经过固溶处理后形成过饱和固溶体,采用冷冲压工艺成形,再经过预时效和油漆烘烤时效获得高强度且耐蚀性强的汽车b柱零件的方法。
22.本实施例中,所述汽车b柱零件初始材料为超硬铝合金7075-t6板材,厚度为2mm;所述固溶加热炉和时效加热炉温度设定范围为0-1000℃,温度测量精度《1%,适用于大多数金属材料加热。
23.本实施例提供一种超硬铝合金7075耐蚀汽车b柱零件冷冲压成形方法,所述方法的工艺流程图如图1所示,主要包括开卷1、落料2、固溶处理3、冷水淬火4、冷冲压成形5、预时效6、车身焊装7和油漆烘烤8;冷冲压成形工艺方案如图2所示,室温rt下原始t6态材料析出相主要为gp区和半共格亚稳相η
´
(a点状态),经过固溶处理并水冷淬火后形成w态,析出相几乎全部溶解到基体内(b点状态),最后经历双级失效后晶内析出细小的gp区和半共格亚稳相η
´
,晶界上连续网状分布的析出相转化为断续析出物(c点状态)。
24.本实施方式通过以下步骤实现:步骤一,采用商业成形软件dynaform对汽车b柱零件进行毛坯尺寸反求,计算出毛坯形状尺寸,并通过模具完成下料;步骤二,对步骤一所得的坯料进行双级固溶处理。先将固溶加热炉设定为初级固溶温度460℃,待温度恒定后,把坯料插入固溶加热炉内加热,待坯料温度达到初级固溶温度后保温60分钟,然后将固溶加热炉升高到二级固溶温度480℃,保温30分钟,完成固溶处理;步骤三,将步骤二固溶处理后的坯料从固溶加热炉取出,迅速浸入室温冷水中,这一过程不超过10秒,待冷却至室温后得到过饱和固溶体即w态坯料;步骤四,将步骤三所得的w态坯料放入冷拉深切边复合模具完成汽车b柱零件拉深成形和切边,拉深成形过程中凸模下行速度为14毫米/秒,得到汽车b柱零件;步骤五,从步骤四所述的拉深切边复合模具中取出汽车b柱零件,放入另一时效加热炉进行预时效,预时效温度为120℃,保温60分钟,随后取出室温冷却,得到预时效的汽车b柱零件;步骤六,将步骤五所得的预时效汽车b柱零件焊装成车身,车身油漆后进入烘烤房烘烤,油漆烘烤温度为180℃,时间为30分钟。
25.本发明适用范围广,工艺简单易操作,能成形复杂零件,成本低、生产效率高,且成形零件强度性能和耐蚀性能大幅度提升。
26.以上所述仅为本发明的优选实施例而已,并不用于限制本发明,对于本领域的技术人员来说,本发明可以有各种更改和变化。凡在本发明的精神和原则之内,所作的任何修改、等同替换、改进等,均应包含在本发明的保护范围之内。
再多了解一些
本文用于创业者技术爱好者查询,仅供学习研究,如用于商业用途,请联系技术所有人。