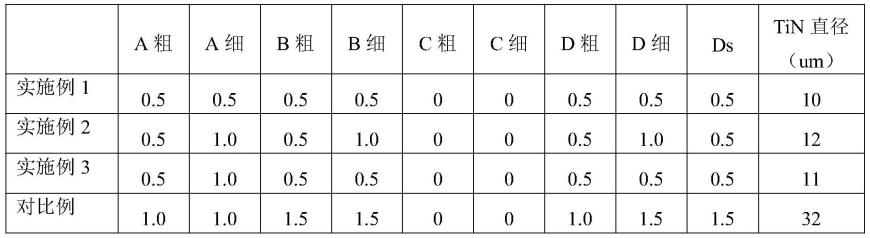
1.本发明涉及钢铁冶炼领域,特别涉及一种热轧弹簧钢的冶炼方法及其制备的热轧弹簧 钢。
背景技术:
2.热轧弹簧钢主要应用于汽车的膜片弹簧离合器,膜片弹簧离合器的结构特别,使用环 境恶劣,热轧弹簧钢因在强压、高温中不断地承受交变载荷而出现疲劳损坏。因此热轧弹 簧钢的冶金质量显得非常关键。目前,我国高等级热轧弹簧钢全部从国外进口,国内在此 领域尚属空白。
3.钢中的氧和非金属氧化物会降低钢材的疲劳寿命和冲击韧性,是疲劳失效裂纹的主要 产生原因。对于安全性要求很高的汽车关键零部件,氧含量和非金属氧化物夹杂需要严格 控制。ti可以固定钢水中的n元素,可以形成tin。但是如果钛含量过多,会形成大颗粒 的tic、tin以及ticn,恶化钢的韧性和抗疲劳性能,因此需要对钛含量进行控制。对于 高等级热轧弹簧钢,为了获得稳定长久的疲劳寿命,还需减少a类硫化物夹杂物。国内现 有冶炼方法生产的热轧高等级弹簧钢质量波动大,夹杂物区间a类1.5-2.5级,b类1.5-2.5 级,氧含量区间为14-31ppm,并含有大颗粒tin,难以达到国外同类产品水平。
4.发明专利申请公布号cn106222362a公开一种弹簧钢的精炼方法,控制lf精炼渣碱 度在1.8-2.5,精炼渣组分包括:cao 50~60wt%,sio222~28wt%,al2o33~6wt%,mgo10~15wt%,mno feo 0.5~1wt%,caf22~4.5wt%,精炼采用si脱氧,达到减少钢中 非金属夹杂物目的。发明专利授权号cn102162068b公开一种弹簧钢及其制造和热处理方 法,生产工艺为电炉-lf-vd-连铸-轧制-热处理,lf精炼渣碱度2.5-3.0,精炼采用si脱氧, 获得优质弹簧钢。发明专利公开号cn201810936796公开一种弹簧钢的lf精炼方法,通 过对精炼渣的精确控制,充分利用精炼渣的吸附作用,达到改善夹杂物的效果。精炼渣系 组分为:cao 55~60wt%,sio211~15wt%,al2o318~19wt%,mgo 11~15wt%,caf
2 2~3wt%,其它;精炼采用al脱氧。
5.高碱度精炼渣有利于钢水脱氧脱硫,但是渣黏度高,吸附夹杂效果差,容易导致钢中b类夹杂物超标,影响弹簧钢的疲劳性能。精炼渣加入caf2,可以有效降低渣黏度,但是 对环境有严重危害。
6.发明专利授权号cn104056871b公开了一种用于控制夹杂物的弹簧钢线材生产工艺, 采用si/mn脱氧冶炼工艺,精炼渣组分cao 25~50wt%,sio235~55wt%,al2o33~10wt%, mgo 5~20wt%,feo mno≤5wt%,碱度控制在0.7-2.0,夹杂物的目标控制范围为sio2: 40-70%,al2o3:10-25%,cao:20-50%;cao与sio2含量的比值为0.2~1.0,获得低熔 点cao
·
sio2·
al2o3系夹杂物,夹杂物的尺寸大部分控制在5μm以下。发明专利申请公布号 cn103510020a公开了一种弹簧钢盘条及其夹杂物控制方法,采用低碱度精炼渣硅锰脱氧, 实现钢中钛含量不大于0.0015%,夹杂物宽度尺寸不大于10um。
7.采用低碱度精炼渣硅锰脱氧工艺可以降低大颗粒tin及b类夹杂物数量,但钢中氧
含 量过高(≥20ppm),钢中硅酸盐类夹杂物容易超标,同时低碱度渣对钢包耐材侵蚀严重。
技术实现要素:
8.本发明的目的在于解决热轧弹簧钢中氧含量、钛含量过高以及夹杂物不易控制的问题。 本发明提供了一种热轧弹簧钢的冶炼方法,有利于降低热轧弹簧钢中氧含量、钛含量并利 于控制热轧弹簧钢中的夹杂物。
9.为解决上述技术问题,本发明公开了一种热轧弹簧钢的冶炼方法,包括以下步骤:转 炉冶炼,出钢时对钢水进行弱脱氧;lf精炼,lf精炼包括第一阶段和第二阶段,第一阶 段包括向钢水中喂入铝线的第一喂铝线步骤,第一阶段的精炼渣目标碱度为4~7,第二阶 段包括向钢水中喂入铝线的第二喂铝线步骤,第二阶段的精炼渣目标碱度为2~3;真空处 理;连铸。
10.lf精炼中需要对精炼渣进行调整,其中包括对于精炼渣碱度的调整以及成分的调整, 通常选定某具体碱度值以及某具体成分比例为目标,通过加入造渣剂等方式对精炼渣进行 控制,使精炼渣的碱度和成分达到目标。上述选定的某具体碱度值则为精炼渣目标碱度, 上述选定的某具体成分比例则为精炼渣目标成分。
11.本发明通过转炉出钢弱脱氧,避免还原转炉渣中ti的氧化物,从而避免ti进入钢水。 在lf精炼过程分批喂入铝线,尽量地避免铝与精炼渣的反应,避免还原精炼渣中ti的氧 化物导致ti进入钢水;并且在lf精炼过程分批喂入铝线,可以确保铝充分进入钢水弥散 脱氧,形成弥散的小颗粒脱氧产物。精炼渣目标碱度从第一阶段的4~7调整到第二阶段的 2~3,第一阶段高碱度有利于脱硫脱氧,第二阶段低碱度可以减少氧化铝夹杂,并且,降 低碱度可以抑制钢水增ti,减少大颗粒的tin夹杂。
12.可选地,在连铸步骤中,钢包注流区采用镁质覆盖剂,中间包浇注区采用钙质覆盖剂。
13.中间包采用两种覆盖剂,钢包注流区采用镁质覆盖剂,避免钢水卷渣形成大颗粒的钙 铝酸盐夹杂,中间包浇注区采用钙质覆盖剂,钙质覆盖剂的上层采用碳化稻壳全部覆盖, 在保温的同时有效吸附去除钢水中夹杂物,因此中间包覆盖剂的选用可以进一步控制热轧 弹簧钢中的夹杂。
14.可选地,在转炉冶炼步骤中,出钢时采用不含铝的脱氧剂对钢水进行弱脱氧。
15.可选地,不含铝的脱氧剂为电石类脱氧剂。
16.可选地,第一喂铝线步骤和第二喂铝线步骤的喂铝线量均为0.3~0.4kg/t钢。
17.可选地,精炼渣为cao-al2o
3-sio
2-mgo-nao系,第一阶段的精炼渣目标成分为cao: 48~56wt%,al2o3:28~34wt%,sio2:8~12wt%,mgo:4~6wt%,nao:1~3wt%,0wt% <mno feo≤0.5wt%,所述第二阶段的精炼渣目标成分为:cao:46~54wt%,al2o3: 21~27wt%,sio2:18~24wt%,mgo:4~6wt%,nao:1~3wt%,0wt%<mno feo≤0.5wt%。
18.可选地,采用碳化稻壳覆盖于钙质覆盖剂的上方。
19.本发明还公开了一种热轧弹簧钢,由上述冶炼方法制备。
20.本发明提供的热轧弹簧钢的冶炼方法,有利于降低热轧弹簧钢中氧含量、钛含量并利 于控制热轧弹簧钢中的夹杂物。
21.可选地,热轧弹簧钢的氧含量≤0.0015wt%,钛含量≤0.0015wt%,tin夹杂的直
径≤27um, a、b、c、d类夹杂均≤1.0级,ds类夹杂≤0.5级。
22.本发明提供的工艺可操作性强,易于控制;高碱度低黏度无氟精炼渣降低了钢包耐材 的侵蚀,又避免了氟对环境的破坏。
具体实施方式
23.以下由特定的具体实施例说明本发明的实施方式,本领域技术人员可由本说明书所揭 示的内容轻易地了解本发明的其他优点及功效。虽然本发明的描述将结合较佳实施例一起 介绍,但这并不代表此发明的特征仅限于该实施方式。恰恰相反,结合实施方式作发明介 绍的目的是为了覆盖基于本发明的权利要求而有可能延伸出的其它选择或改造。为了提供 对本发明的深度了解,以下描述中将包含许多具体的细节。本发明也可以不使用这些细节 实施。此外,为了避免混乱或模糊本发明的重点,有些具体细节将在描述中被省略。需要 说明的是,在不冲突的情况下,本发明中的实施例及实施例中的特征可以相互组合。
24.在本实施例的描述中,需要说明的是,术语“上”、“底”等指示的方位或位置关系为 基于该发明产品使用时惯常摆放的方位或位置关系,仅是为了便于描述本发明和简化描述, 而不是指示或暗示所指的装置或元件必须具有特定的方位、以特定的方位构造和操作,因 此不能理解为对本发明的限制。
[0025][0026]
术语“第一”、“第二”等仅用于区分描述,而不能理解为指示或暗示相对重要性。
[0027]
为使本发明的目的、技术方案和优点更加清楚,下面对本发明的实施方式作进一步地 详细描述。
[0028]
本发明公开了一种热轧弹簧钢的冶炼方法,包括以下步骤:转炉冶炼,出钢时对钢水 进行弱脱氧;lf精炼,lf精炼包括第一阶段和第二阶段,第一阶段包括向钢水中喂入铝 线的第一喂铝线步骤,第一阶段的精炼渣目标碱度为4~7,第二阶段包括向钢水中喂入铝 线的第二喂铝线步骤,第二阶段的精炼渣目标碱度为2~3;真空处理;连铸。
[0029]
本发明通过转炉出钢弱脱氧,避免还原转炉渣中ti的氧化物导致ti进入钢水,有利 于降低钢中钛含量,减小钢中tin夹杂的直径。在lf精炼过程分批喂入铝线,尽量地避 免铝与精炼渣的反应,避免还原精炼渣中ti的氧化物导致ti进入钢水,同样有利于降低 钢中钛含量,减小钢中tin夹杂的直径;并且在lf精炼过程分批喂入铝线,可以确保铝 充分进入钢水弥散脱氧,形成弥散的小颗粒脱氧产物,利于降低钢中氧含量、控制夹杂。
[0030]
精炼渣目标碱度从第一阶段的4~7调整到第二阶段的2~3,第一阶段高碱度有利于脱 硫脱氧,降低钢中氧含量、控制夹杂,第二阶段低碱度可以减少氧化铝夹杂,并且,降低 碱度可以抑制钢水增ti,减少大颗粒的tin夹杂。
[0031]
当第一阶段的精炼渣目标碱度小于4时,不利于钢水脱氧;当第一阶段的精炼渣目标 碱度大于7时,渣的黏度过高,不利于渣对钢中夹杂物的吸附去除。因此,第一阶段的精 炼渣目标碱度应控制为4~7。
[0032]
当第二阶段的精炼渣目标碱度小于2时,脱氧效果差,钢中容易增氧;当第二阶段的 精炼渣目标碱度大于3时,钢中氧化铝夹杂增加,不易控制。因此,第二阶段的精炼渣目 标碱度应控制为2~3。
[0033]
可选地,在连铸步骤中,钢包注流区采用镁质覆盖剂,中间包浇注区采用钙质覆盖剂。
[0034]
钢包注流区采用镁质覆盖剂,避免钢水卷渣形成大颗粒的钙铝酸盐夹杂,从而降低ds 类夹杂的级别。中间包浇注区采用钙质覆盖剂可以有效吸附去除钢水中夹杂物。
[0035]
可选地,在转炉冶炼步骤中,出钢时采用不含铝的脱氧剂对钢水进行弱脱氧。
[0036]
可选地,不含铝的脱氧剂为电石类脱氧剂,电石类脱氧剂的加入量为0.6~0.9kg/t钢。
[0037]
可选地,第一喂铝线步骤和第二喂铝线步骤的喂铝线量均为0.3~0.4kg/t钢。
[0038]
当喂铝线量小于0.3kg/t钢,脱氧效果差,钢中氧含量高;当喂铝线量大于0.4kg/t钢, 容易在钢水中形成过量的氧化铝夹杂,夹杂物聚集,造成b类夹杂超标。
[0039]
可选地,精炼渣为cao-al2o
3-sio
2-mgo-nao系,第一阶段的精炼渣目标成分为cao: 48~56wt%,al2o3:28~34wt%,sio2:8~12wt%,mgo:4~6wt%,nao:1~3wt%,0wt% <mno feo≤0.5wt%,所述第二阶段的精炼渣目标成分为:cao:46~54wt%,al2o3: 21~27wt%,sio2:18~24wt%,mgo:4~6wt%,nao:1~3wt%,0wt%<mno feo≤0.5wt%。
[0040]
精炼渣为cao-al2o
3-sio
2-mgo-nao系,其中cao-al2o
3-sio2三元渣系为常用的精炼 渣系,加入mgo有利于减少钢包的耐材侵蚀,nao有利于提高热轧弹簧钢塑性。mno和 feo为钢水中微量的氧与锰、铁氧化得到的反应产物进入渣中形成。第一阶段的精炼渣目 标成分选择cao:48~56wt%,al2o3:28~34wt%,sio2:8~12wt%,mgo:4~6wt%,nao: 1~3wt%,0wt%<mno feo≤0.5wt%的范围,高碱度渣系脱氧效果好,同时渣系黏度低, 熔点低,吸附夹杂物性能好。第二阶段的精炼渣目标成分选择cao:46~54wt%,al2o3: 21~27wt%,sio2:18~24wt%,mgo:4~6wt%,nao:1~3wt%,0wt%<mno feo≤0.5wt% 的范围,适当降低精炼渣碱度,可以更好控制钢中b类夹杂物。
[0041]
可选地,采用碳化稻壳覆盖于钙质覆盖剂的上方,达到为钢水保温的效果。
[0042]
具体地,本发明公开的热轧弹簧钢的冶炼方法为:
[0043]
(1)转炉冶炼:以铁水与废钢为原材料进行转炉冶炼,铁水占原材料的80~90wt%。 转炉生产前一炉禁止留渣和溅渣。转炉停吹磷含量≤0.005wt%,停吹温度1645~1665℃。出 钢采用前后滑板挡渣。出钢前期钢包加入高纯硅铁、电解锰进行合金化,加入低氮碳粉进 行配碳,加入电石类不含铝的脱氧剂进行脱氧,并加入石灰及部分lf预熔渣,出钢结束 后补加lf预熔渣。合金加入顺序为先加入高纯硅铁,再加入低氮碳粉,再加入电解锰。
[0044]
(2)lf精炼:将钢包移入lf精炼工位,采用喂丝机喂入铝线,加入量0.3~0.4kg/t 钢。添加石灰、nao等造渣剂通电化渣,调整精炼渣成分,nao加入量0.1~0.15kg/t钢。 精炼渣cao-al2o
3-sio
2-mgo-nao系,碱度4~7,目标成分的重量百分比为cao:48~56wt%, al2o3:28~34wt%,sio2:8~12wt%,mgo:4~6wt%,nao:1~3wt%,0wt%<mno feo ≤0.5wt%。精炼渣熔化后取钢水样品分析钢水成分,并喂入铝线,第二次al线加入量 0.3~0.4kg/t钢。根据分析得到的钢水成分补合金成分。精炼末期调整渣系,碱度2~3,目 标成分为cao:46~54wt%,al2o3:21~27wt%,sio2:18~24wt%,mgo:4~6wt%,nao:1~3wt%,0wt%<mno feo≤0.5wt%。
[0045]
(3)真空处理:将lf精炼后的钢包进行真空处理,可采用真空精炼法(vd)或钢 液
真空循环脱气法(rh)。rh法绝对真空度≤67pa,纯脱气时间7min以上,软吹镇静 15-25min;vd法绝对真空度≤300pa,高真空时间15-20min,软吹镇静15-25min。
[0046]
(4)连铸:镇静后的钢水吊到浇铸平台,浇铸全程对长水口采用氩气保护浇铸,中 间包采用两种覆盖剂,钢包注流区采用镁质覆盖剂,中间包浇注区采用钙质覆盖剂,钙质 覆盖剂的上层采用碳化稻壳全部覆盖。
[0047]
其中,精炼渣中加入nao可以改善热轧弹簧钢夹杂物的塑性,而当nao加入量小于 0.1kg/t钢时,改善塑性效果不明显,当nao加入量大于0.15kg/t钢时,产生大量烟气,造 成环境问题,因此nao加入量为0.1~0.15kg/t钢。
[0048]
本发明还公开了一种热轧弹簧钢,由上述冶炼方法制备。
[0049]
可选地,弹簧钢的氧含量≤0.0015wt%,钛含量≤0.0015wt%,tin夹杂的直径≤27um, a、b、c、d类夹杂均≤1.0级,ds类夹杂≤0.5级。
[0050]
可选地,热轧弹簧钢的成分为:c:0.76wt%~0.84wt%,si:0.10wt%~0.35wt%,mn: 0.30wt%~0.6wt%,cr:0.09wt%~0.30wt%,0<p≤0.020wt%,0<s≤0.005wt%,0< n≤0.0070wt%,0<o≤0.0015wt%,0<ti≤0.0015wt%,余量为fe和不可避免的杂质。
[0051]
弹簧钢的性能要求以强度和弹性为主,高碳目的是提高强度极限和屈服极限。适量加 入si、mn目的是提高淬透性,提高钢的回火稳定性,使弹簧钢在相同回火温度下具有较 高的硬度和强度,但si、mn含量过高会增加钢的过热和脱碳。加入一定量的cr,一方面 可以防止过热和脱碳,同时提高淬透性。但是si、cr含量过高,热处理过程中珠光体转变 受到抑制,弹簧钢的强度和弹性差;p、s为钢中有害元素,降低含量有利于提高疲劳寿命; 降低n、o、ti含量可以减少氧化物和氮化钛夹杂物,提高疲劳性能。
[0052]
实施例1
[0053]
(1)转炉冶炼:采用公称容量300t转炉冶炼,以铁水与废钢为原材料,铁水加入275t, 优质废钢45t。转炉生产前一炉禁止留渣和溅渣。第一次造渣石灰加入量4t,轻烧白云石 1t。造渣顶吹流量55000nm3/h,供氧1500nm3后顶吹流量降到45000nm3/h。进行高拉碳 操作,转炉停吹终点碳含量0.2wt%,磷含量0.005wt%,停吹温度1648℃。出钢采用前后 滑板挡渣。出钢1/3顺次加入高纯硅铁、电解锰进行合金化,并加入低氮碳粉进行配碳、 电石进行脱氧,通过粗调钢水中元素成分的含量,满足钢水中各元素成分的下限值。出钢 加入石灰600kg,合金化后立即加入lf预熔渣800kg,出钢结束后再补加lf预熔渣800kg。
[0054]
(2)lf精炼:将钢包移入lf精炼工位,采用喂丝机喂入铝线,铝线的加入量为0.3kg/t 钢。添加石灰1t,碳化硅球0.2t,nao加入量0.1kg/t钢。精炼渣碱度4,成分按重量百分 比为48%cao,31%al2o3,12%sio2,5.5%mgo,3%nao,0.5%mno feo。精炼渣完全 熔化后取样分析钢水成分,并向钢水中喂入铝线,第二次铝线加入量为0.3kg/t钢。根据分 析得到的钢水成分补合金成分。精炼末期加入600kg碳化硅球调整渣系,碱度2,精炼渣 成分按重量百分比为46%cao,24%al2o3,23%sio2,4.3%mgo,2.5%nao,0.2%mno feo。
[0055]
(3)rh处理:将lf精炼后的钢包运到rh工位进行真空处理,绝对真空度65pa, 纯脱气时间7min,软吹镇静20min。
[0056]
(4)连铸:镇静后的钢水吊到浇铸平台,浇铸全程对长水口采用氩气保护浇铸。采 用两种中间包覆盖剂,钢包注流区采用镁质覆盖剂,浇注区采用钙质覆盖剂,钙质覆盖剂 的上层采用碳化稻壳全部覆盖。
的上层采用碳化稻壳全部覆盖。
[0069]
(5)轧制:铸坯经轧制得到热轧弹簧钢。
[0070]
对比例
[0071]
(1)转炉冶炼:采用公称容量300t转炉冶炼,以铁水与废钢为原材料,铁水加入275t, 优质废钢44t。转炉加入石灰、白云石造渣脱磷,停吹终点碳含量0.035wt%,磷含量0.005wt%, 停吹温度1655℃。出钢采用前后滑板挡渣。出钢1/3顺次加入高纯硅铁、电解锰进行合金 化,并加入低氮碳粉进行配碳、铝锭0.5kg/t钢进行脱氧,通过粗调钢水中元素成分的含量, 满足钢水中各元素成分的下限值。出钢加入石灰800kg,合金化后立即加入lf预熔渣1t, 出钢结束后再补加lf预熔渣1t。
[0072]
(2)lf精炼:将钢包移入lf精炼工位通电化渣,精炼渣熔化后取样分析钢水成分, 添加石灰及台铝,通电熔化,根据分析得到的钢水成分补合金成分。石灰加入1t,碳化硅 球400kg,铝加入量0.3kg/t钢。精炼渣碱度为3,成分按重量百分比为51%cao,17%sio2, 26%al2o3,5.5%mgo,0.5%feo mno。
[0073]
(3)rh处理:将lf处理后的钢包运到rh工位进行真空处理,绝对真空度60pa, 纯脱气时间8min,软吹镇静21min。
[0074]
(4)连铸:镇静后的钢水吊到板坯浇铸平台,浇铸全程采用氩气保护浇铸,中间包 采用双层覆盖剂,底层为非晶态预融型钙质覆盖剂,上层采用碳化稻壳全部覆盖。
[0075]
(5)轧制:铸坯经轧制得到热轧弹簧钢。
[0076]
对实施例和对比例得到的热轧弹簧钢进行成分检测,具体测试方法依据:jisg 1253-2002铁和钢-光电发射光谱分析方法,具体结果见表1:
[0077]
表1.热轧弹簧钢成分(wt%)
[0078] csimncrpsnoti实施例10.820.170.410.110.0130.0010.0040.00090.0013实施例20.810.160.400.100.0140.0010.0040.00100.0015实施例30.790.190.410.120.0140.0010.0040.00100.0015对比例0.820.180.410.120.0150.0010.0040.00160.0029
[0079]
对实施例和对比例得到的热轧弹簧钢进行a、b、c、d、ds类夹杂的评级以及tin 夹杂的直径测量,检测标准依据:gb/t 10561-2005/iso4967:1998(e):检验面位于宽度 1/4处的平行于钢材纵轴全厚度截面,抛光面面积200mm2,采用金相显微镜在放大100倍 的视场观察夹杂物的形态和分布,对照标准图谱评价a、b、c、d和ds夹杂物等级。采 用同一试样及观察方法,测量tin夹杂物直径。具体结果见表2:
[0080]
表2.热轧弹簧钢夹杂物
[0081]
[0082]
由表1和表2可知,实施例1~3得到的热轧弹簧钢氧含量≤0.0015wt%,钛含量 ≤0.0015wt%,tin夹杂的直径≤27um,a、b、c、d类夹杂均≤1.0级,ds类夹杂≤0.5级。 而对比例中,转炉冶炼过程中使用铝锭对钢水进行脱氧,在lf精炼过程中一次性加入铝, 并且对精炼渣只做了一次调整,即将其调整为碱度为3的常规精炼渣,因而对比例得到的 热轧弹簧钢氧含量高达0.0016wt%,钛含量高达0.0029wt%,tin夹杂的直径达32um,b 类夹杂1.5级,d细类夹杂1.5级,ds类夹杂1.5级。
[0083]
综上所述,本发明提供的热轧弹簧钢的冶炼方法,通过转炉出钢弱脱氧、在lf精炼 过程分批喂入铝线、精炼渣目标碱度从第一阶段的4~7调整到第二阶段的2~3,可以有效 降低热轧弹簧钢中氧含量、钛含量并有效控制热轧弹簧钢中的夹杂物。
[0084]
虽然通过参照本发明的某些优选实施方式,已经对本发明进行了描述,但本领域的普 通技术人员应该明白,以上内容是结合具体的实施方式对本发明所作的进一步详细说明, 不能认定本发明的具体实施只局限于这些说明。本领域技术人员可以在形式上和细节上对 其作各种改变,包括做出若干简单推演或替换,而不偏离本发明的精神和范围。
再多了解一些
本文用于创业者技术爱好者查询,仅供学习研究,如用于商业用途,请联系技术所有人。