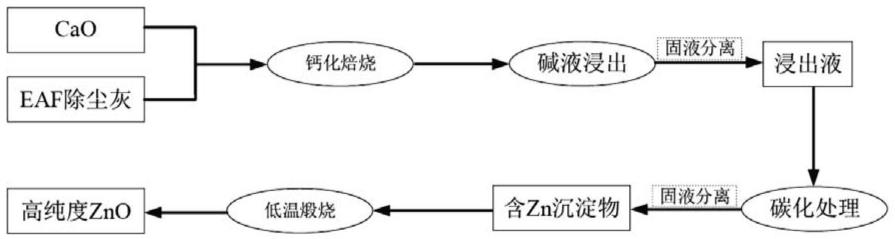
1.本发明属于钢铁冶金领域,特别涉及一种回收电弧炉除尘灰锌资源的方法。
背景技术:
2.电弧炉除尘灰是电弧炉炼钢过程中产生富含zn等有价金属资源的固体废弃物,zn含量一般在10%~30%,已成为回收冶炼zn的主要原料,其回收方法主要有火法和湿法两种工艺。火法工艺包括熔融还原和直接还原两种,当前我国主要以直接还原工艺为主,还原剂主要为碳质还原剂。火法工艺对原料适应性较强,运行较稳定,缺点是投资高,还原剂消耗量大,能源利用效率低,且运行成本高。湿法浸出工艺主要分酸浸法、氨浸法和碱浸法。湿法工艺处理能耗小、对zno浸出率高,但是酸浸过程设备腐蚀严重,会有大量铁离子进入浸出液,氨浸和碱浸对除尘灰中铁酸锌浸出效果差,整体zn浸出率不高,浸出渣需进一步处理。因此,如何实现火法工艺和湿法工艺的优势互补,实现电弧炉除尘灰绿色、高效化资源综合利用是研究的重点及关键。
3.为此,本领域技术人员设计了多种工艺手段来回收电弧炉除尘灰锌资源,以下为举例说明:
4.公开号为cn114480841a的中国专利公开了一种电炉除尘灰及其提铁尾渣全量化、高值利用方法,其通过碳热还原、辅以真空冶炼电炉除尘灰提铁尾渣,制备zn-pb合金。
5.公开号为cn114315255a的中国专利公开了一种利用电炉除尘灰制备高纯合金及尾渣资源利用方法,其将电炉除尘灰与碳粉进行混匀,随即加入粘结剂成型并制成球团,辅以真空冶炼来提取高纯zn-pb合金产品。
6.上述两种工艺都通过球团制备-真空冶炼-真空冷却-磁选分离来回收高纯zn-pb合金,须额外加入碳质还原剂,且该方法对fe的回收利用率高,不适用于含zn量较高的电弧炉除尘灰资源化综合利用。
7.公开号为cn113787085a的中国专利公开了一种提取电炉除尘灰中fe、zn、pb并高值化利用的方法,其利用草酸作为浸出剂,在低温常压下进行络合反应,来达到梯级提取fe、zn资源。但是,低温常压下除尘灰中的铁酸锌浸出率较低,如果采用加压热酸浸出可以溶解铁酸锌,锌浸出率可达95%,但同时也有约60%的铁浸出,导致后续浸出液中锌铁分离工序复杂,增加生产成本,与专利初心不符。
8.公开号为cn108502915a的中国专利公开了一种以高锌除尘灰制备纳米氧化锌的方法,和公开号为cn108408760a的中国专利公开了一种以高锌除尘灰制备高纯氧化锌的方法,都将高锌除尘灰溶于硫酸溶液中,对滤液中加入碳酸钠溶液,产生前驱体碱式碳酸锌,最后对前驱体碱式碳酸锌进行煅烧后得到纳米氧化锌。虽然此工艺对zno浸出率高,但是硫酸是强酸,对设备腐蚀严重,使其可用期限减小,生产成本高,。
9.公开号为cn102776384a的中国专利公开了一种从有色金属废渣中提取锌的方法,其通过火法冶炼、酸浸、沉锌和还原熔炼等步骤,实现zn的回收利用。但该方法锌回收产量较少,品味较低。
技术实现要素:
10.为解决现有技术中存在的问题,本发明的目的在于提供一种回收电弧炉除尘灰锌资源的方法,该方法是一种绿色高效回收电弧炉除尘灰锌资源的工艺,可以有效实现火法工艺和湿法工艺的优势互补,处理电弧炉除尘灰全流程无须额外加入碳质还原剂,且除尘灰中微量c形成的co2可在后续碳化沉淀处理中消化,真正实现eaf除尘灰有价金属资源无碳、低耗、绿色化高效利用。
11.本发明采用的技术方案如下:
12.一种回收电弧炉除尘灰锌资源的方法,包括如下过程:
13.将电弧炉除尘灰与石灰混合均匀,之后进行钙化焙烧,得到焙烧产物;
14.对焙烧产物进行常压碱液浸出,并进行固液分离得到浸出液;
15.向浸出液中通入co2,调节浸出液ph=6.5~8.0,实现zn元素定向沉淀,进行固液分离得到含zn沉淀产物;
16.将含zn沉淀产物经去离子水洗涤后,于130~200℃、空气氛围下进行煅烧,之后随炉冷却至室温,得到纳米zno,实现回收电弧炉除尘灰锌资源。
17.优选的,将电弧炉除尘灰与石灰进行混合时,将电弧炉除尘灰与石灰按照ca/zn摩尔比=1.5~3进行混合。
18.优选的,进行钙化焙烧时,温度为950~1150℃,时间为1~4h。
19.优选的,对焙烧产物进行常压碱液浸出时,液固比=8~30,浸出温度为25~50℃,浸出时间为2~5h,浸出搅拌速度为200~500r/min,碱溶液浓度为0.5~5.0mol/l。
20.优选的,向浸出液中通入co2、实现zn元素定向沉淀时,co2浓度0.05~0.5mol/l,流量为10~80ml/min,沉淀反应温度为25~80℃,沉淀反应时间为1~4h。
21.优选的,将含zn沉淀产物经去离子水洗涤后,于130~200℃、空气氛围下进行煅烧时,煅烧时间为1~3h。
22.优选的,所述电弧炉除尘灰含zn质量分数为10%~30%,含fe质量分数为30%~50%,所述石灰含cao质量分数大于97%。
23.优选的,所述电弧炉除尘灰粒度为10~100μm,所述石灰粒度为10~200μm。
24.优选的,所述碱液为naoh、koh和ba(oh)2其中的一种或几种的混合物。
25.优选的,所述纳米zno的纯度大于99%,尺寸50~200nm。
26.与现有技术相比,本发明的有益效果为:
27.本发明回收电弧炉除尘灰锌资源的方法通过将混合均匀后的电弧炉除尘灰和石灰进行火法焙烧处理,随后对焙烧产物进行常压碱液浸出,然后对浸出液进行zn元素定向沉淀,最后对沉淀产物进行低温煅烧,得到纯度大于99%,尺寸50~200nm的高纯纳米zno。本发明方法将火法工艺和湿法工艺进行优势互补,处理电弧炉除尘灰全流程无须额外加入碳质还原剂,且除尘灰中微量c形成的co2可在后续碳化沉淀处理中消化,真正实现eaf除尘灰有价金属资源无碳、低耗、绿色化高效利用。综上,本发明实现了绿色、高效回收电弧炉除尘灰锌资源。此外,本发明提供的回收电弧炉除尘灰锌资源的方法操作简单,所用各反应原料均是价廉易得的物质,反应条件温和、能耗低。
附图说明
28.图1是本发明回收电弧炉除尘灰锌资源的方法的工艺流程图;
29.图2是本发明实施例1所得高纯氧化锌的扫描电镜图;
30.图3是本发明实施例2所得高纯氧化锌的扫描电镜图;
31.图4是本发明实施例3所得高纯氧化锌的扫描电镜图;
具体实施方式
32.为了使本发明的目的、技术方案及优点更加清楚明白,以下结合实施例,对本发明进行进一步详细说明。应当理解,此处所描述的具体实施例仅用以解释本发明,并不用于限定本发明。
33.参照图1,本发明回收电弧炉除尘灰锌资源的方法,包括如下步骤:
34.(1)钙化焙烧:将电弧炉除尘灰与石灰按照ca/zn摩尔比=1.5~3进行混合,混合均匀后将混合粉末在950~1150℃焙烧1~4h,得到焙烧产物。
35.(2)碱液浸出:对焙烧产物进行常压碱液浸出,并进行固液分离得到浸出液,浸出过程液固比=8~30,浸出温度为25~50℃,浸出时间为2~5h,浸出搅拌速度为200~500r/min,碱溶液浓度为0.5~5.0mol/l。所述碱液采用naoh、koh和ba(oh)2其中的一种或几种的混合物。
36.(3)碳化沉淀:向浸出液中通入co2,调节浸出液ph=6.5~8.0,实现zn元素定向沉淀,并进行固液分离得到含zn沉淀产物,定向沉淀过程中co2浓度为0.05~0.5mol/l,流量为10~80ml/min,定向沉淀反应温度为25~80℃,反应时间为1~4h。
37.(4)低温煅烧:将碳化沉淀产物(即上述含zn沉淀产物)经去离子水洗涤后置于加热炉进行低温煅烧,煅烧温度为130~200℃,煅烧时间为1~3h,煅烧气氛为空气,煅烧后随炉冷却至室温,得到纯度大于99%,尺寸50~200nm的纳米zno。所述加热炉采用感应加热炉、电阻加热炉或微波加热炉。
38.电弧炉除尘灰的成分如下:电弧炉除尘灰含zn质量分数为10%~30%,含fe质量分数为30%~50%。本发明以下实施例采用的电弧炉除尘灰的成分检测如下:电弧炉除尘灰含zn质量分数为30%,含fe质量分数为50%,电弧炉除尘灰粒度为10~100μm。
39.本发明采用的石灰中,含cao质量分数大于97%,杂质太多的话会影响实验效果,本发明以下实施例采用的石灰含cao质量分数为99%,石灰粒度为10~200μm。
40.实施例1
41.本实施例回收电弧炉除尘灰锌资源的方法,包括如下步骤:
42.(1)钙化焙烧:将电弧炉除尘灰与石灰按照ca/zn摩尔比=1.5经混料机进行混合,混合时间为0.5,混合均匀后将混合粉末在950℃焙烧1h,得到焙烧产物。
43.(2)碱液浸出:对焙烧产物在与氢氧化钡和氢氧化钾的混合碱液中进行常压碱液浸出,并进行固液分离得到浸出液,浸出过程液固比=8,浸出温度为25℃,浸出时间为2h,浸出搅拌速度为200r/min,碱溶液浓度为0.5mol/l。
44.(3)碳化沉淀:向浸出液中通入co2,调节浸出液ph=6.5~8.0,实现zn元素定向沉淀,并进行固液分离得到含zn沉淀产物,定向沉淀过程中co2浓度为0.5mol/l,流量为80ml/min,定向沉淀反应温度为25℃,反应时间为1h。
45.(4)低温煅烧:将碳化沉淀产物经去离子水洗涤后置于箱式炉进行低温煅烧,煅烧温度为130℃,煅烧时间为1h,煅烧气氛为空气,煅烧后随炉冷却至室温,得到纯度为99.02%,尺寸50~200nm的纳米zno。
46.由图2可知,本实施例获得的纳米zno形貌为不均匀短棒状。
47.实施例2
48.本实施例回收电弧炉除尘灰锌资源的方法,包括如下步骤:(1)钙化焙烧:将电弧炉除尘灰与石灰按照ca/zn摩尔比=2.2经混料机进行混合,混合时间为1.0h,混合均匀后将混合粉末在1100℃焙烧3h,得到焙烧产物。
49.(2)碱液浸出:对焙烧产物在氢氧化钠碱液中进行常压碱液浸出,并进行固液分离得到浸出液,浸出过程液固比=30,浸出温度为35℃,浸出时间为5h,浸出搅拌速度为400r/min,碱溶液浓度为3.0mol/l。
50.(3)碳化沉淀:向浸出液中通入co2,调节浸出液ph=6.5~8.0,实现zn元素定向沉淀,并进行固液分离得到含zn沉淀产物,定向沉淀过程中co2浓度为0.1mol/l,流量为40ml/min,定向沉淀反应温度为45℃,反应时间为3h。
51.(4)低温煅烧:将碳化沉淀产物经去离子水洗涤后置于箱式炉进行低温煅烧,煅烧温度为155℃,煅烧时间为2.5h,煅烧气氛为空气,煅烧后随炉冷却至室温,得到纯度为99.9%,尺寸50~200nm的纳米zno。
52.由图3可知,本实施例获得的纳米zno产物呈针状结构,排列十分紧密,密度大。
53.实施例3
54.本实施例回收电弧炉除尘灰锌资源的方法,包括如下步骤:(1)钙化焙烧:将电弧炉除尘灰与石灰按照ca/zn摩尔比=3经混料机进行混合,混合时间为2h,混合均匀后将混合粉末在1150℃焙烧4h,得到焙烧产物。
55.(2)碱液浸出:对焙烧产物在氢氧化钾碱液中进行常压碱液浸出,并进行固液分离得到浸出液,浸出过程液固比=16,浸出温度为50℃,浸出时间为3h,浸出搅拌速度为500r/min,碱溶液浓度为5.0mol/l。
56.(3)碳化沉淀:向浸出液中通入co2,调节浸出液ph=6.5~8.0,实现zn元素定向沉淀,并进行固液分离得到含zn沉淀产物,定向沉淀过程中co2浓度为0.05mol/l,流量为10ml/min,定向沉淀反应温度为80℃,反应时间为4h。
57.(4)低温煅烧:将碳化沉淀产物经去离子水洗涤后置于箱式炉进行低温煅烧,煅烧温度为200℃,煅烧时间为3h,煅烧气氛为空气,煅烧后随炉冷却至室温,得到纯度为99.36%,尺寸50~200nm的纳米zno。
58.由图4可知,本实施例获得的纳米zno晶体择优生长,形成较为均匀的棒状结构,且呈蒲公英排列。
59.从上述方案可以看出,本发明通过火法工艺和湿法工艺优势互补,克服了传统火法工艺能源利用率低、成本高,湿法工艺对除尘灰中铁酸锌浸出率低等缺点,实现了电弧炉除尘灰锌资源绿色、低耗高值化回收利用。
60.以上技术方案阐述了本发明的技术思路,不能以此限定本发明的保护范围,凡是未脱离本发明技术方案的内容,依据本发明的技术实质对以上技术方案所作的任何改动及修饰,均属于本发明技术方案的保护范围。
再多了解一些
本文用于创业者技术爱好者查询,仅供学习研究,如用于商业用途,请联系技术所有人。