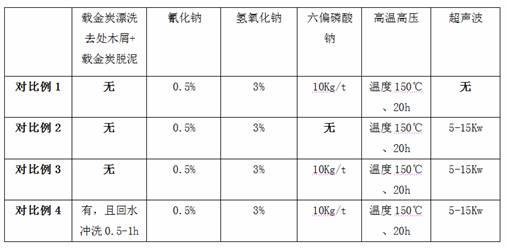
1.本发明涉及一种高银铜钙复杂载金炭高效提取金银铜方法,所属冶金领域。
背景技术:
2.近年来,随着易选、易浸金矿资源日趋减少,含硫、砷、铁、铜、银、金多金属复杂且难处理矿石存在氧化未充分,或夹带红土矿,或为氧硫混合带的矿石,矿石中除了金、银、铜外还含有硫、红土矿等,如何从难处理多金属复杂矿石中高效综合回收金银,成为选冶生产研究领域面临的重要挑战和困难。氰化炭浆工艺仍是处理此类矿石的主要方法之一,其存在金银浸出率高,流程短等特点,常用工艺流程为:矿石—粗碎—磨矿—氰化浸出—磁选—载金炭解吸电解—金泥提纯精炼,获得金、银、铁等产品。
3.该矿石采用氰化炭浆工艺生产过程中,为进一步除硫提升金银浸出率,氰化钠、石灰用量较易选矿石大幅提升,氰化钠用量从2kg/t提升至4kg/t,石灰用量从5kg/t提升至10kg/t,氰化浸出液中含大量铜氰、硫氰、银氰络合等杂质离子。活性炭在槽子内吸附金银的同时,大量的铜、铁、钙、泥质被吸附,严重影响后续载金炭解吸电解生产工艺,存在解吸电解设备难以正常作业、金银解吸率低、解吸时间长、药耗高等一些列问题,制约金银回收率指标,成为此类矿石选冶流程中的一项重大技术瓶颈。如何从高银铜钙复杂载金炭中高效回收金银铜,在既保证技术指标同时又保证经济指标的前提下,是该类矿山企业面临的一个难题,寻求科学合理及效果显著的处理方法是提取此类载金炭中提取金银铜有价成分的关键。
4.目前高银铜钙载金炭多数采用高温高压解吸电解工艺,活性炭装入解吸柱后靠解吸电解液浸出,含金银铜解吸电解液进入电解槽内进行电解,金银铜络合离子在阴极板发生还原沉淀,得到金泥。传统方法中,解吸电解液中的泥质和钙生成硫酸钙微溶物,大量附着解吸柱柱顶、柱底筛网,解吸电解液管道内壁上产生大面积粘稠状硫酸钙附着,解吸电解流量严重偏低,经常面临非正常停机、拆卸筛网、清理管道等问题。药耗高,氰化钠溶液未能有效与炭表面接触,氰化钠、氢氧化钠用量大。解吸电解时间长,由于贫炭指标高,需采取延长解吸电解时间的措施,导致耗时长。金银铜解吸指标低,贫炭含金银品位高,铜几乎得不到解吸电解,金银解吸率指标低于90%。
5.采用先酸洗后解吸方法处理此类载金炭,用硝酸先酸洗后解吸,其工艺流程长,铜得不到回收,且酸洗成本高,用盐酸酸洗后解吸,其工艺流程长,残硫的氯离子对电解槽阳极板腐蚀严重,金银铜回收率指标均较低。
6.综述,对这类复杂载金炭,采用传统高温高压解吸电解、先酸洗后解吸等方法难以获得较好的效果。
技术实现要素:
7.为了解决上述技术问题,本发明提供一种高银铜钙复杂载金炭中高效提取金银铜的方法,针对含au>500g/t、ag>4000g/t、cu>15000g/t、ca>20000g/t、fe>4000g/t的复
杂载金炭(活性炭)。获得合格的金泥和解吸贫炭,同时,解决硫酸钙引起筛网、管道堵塞问题,解吸电解流量稳定,设备正常运行,降低氰化钠、氢氧化钠消耗量,缩短每柱解吸电解时间,提高金银铜解吸率,降低贫炭金银铜品位,达到高效综合提取金、银、铜的目的。
8.具体技术方案为:一种高银铜钙复杂载金炭中高效提取金银铜的方法,包括以下步骤:(1)活性炭吸附。矿石经过氰化炭浆法提取金银铜等,在炭密度12~15g/t、吸附时间24~35h的吸附条件下,高铜、银、钙氰化浸出液中被活性炭有效吸附,载金炭含au>500g/t、ag>4000g/t、cu>15000g/t、ca>20000g/t、fe>4000g/t。
9.(2)载金炭漂洗除木屑。高银铜钙复杂载金炭从氰化槽经过水力输送至储炭槽中,在储炭槽内使用含氰回水进行冲洗,溢流去除炭中的木屑杂质,水压0.4mpa、冲洗时间0.5h。
10.(3)载金炭脱泥、吹风、称重、取样。将完成上述步骤(2)获得的载金炭靠重力自流作用转入清洗及称重罐内,先后进行载金炭清洗、吹风、称重作业,使用含氰回水进行清洗,水压控制0.2-0.3mpa,流量20-30m3/h,脱泥时间0.5-1h,泥质从称重罐底部24目筛网进入沉降池,定期返回氰化槽,脱泥炭进行吹风、称重、取样并检测载金炭化学成分,待转入解吸柱内进行解吸电解提取金银铜元素。
11.此类载金炭表面附着的泥质多,载金炭虽然经过提炭振动筛及木屑漂洗槽中进行了清洗,但表面泥质未得到有效脱除,对解吸电解药耗,解吸率指标有直接影响,该步骤可进一步脱除载金炭中的泥质,提高炭洁净度。
12.(4)除钙及金银提取用解吸电解液配制,氰化钠浓度0.2-0.3%、氢氧化钠浓度2-2.2%、六偏磷酸钠10kg/吨炭,氰化钠、氢氧化钠、六偏磷酸钠三种药剂混合使用,配液量为总炭量的2倍。
13.解吸电解液是影响活性炭中金银铜的脱附效果、金属络合离子在阴极板沉淀效率的重要因素,高浓度氰化钠能够促进载金炭中银及铜解吸,氢氧化钠在解吸过程中起到保护氰根离子分解,同时提供na
,六偏磷酸钠在高温高压解吸过程中与硫酸钙反应生成碳酸钙沉淀,阻止钙、铁等杂质形成粘稠性物(该物质易附着在筛网及管道上、影响流量稳定)。系统试验和生产实践表明,处理此类复杂载金炭的解吸药剂制度为:氰化钠浓度0.2-0.3% 氢氧化钠浓度2.0-2.2% 六偏磷酸钠10kg/吨炭,三种药剂一同配制使用。
14.(5)载金炭装柱,将完成上述步骤(3)获得的脱泥载金炭经过水力输送至解吸柱内,采用“氰化钠 氢氧化钠 六偏磷酸钠 高温高压 超声波方法”进行解吸电解提取金银铜。
15.(6)高银铜钙载金炭解吸电解,将完成上述步骤(4)获得的解吸电解液进至解吸柱、电解槽内,进液结束后启动电加热器、电解槽整流柜、超声波进行金银铜的提取和钙的脱除,得到低金银铜解吸电解贫炭和电解金泥。在此过程中,解吸电解流量控制3-4倍炭床体积,一段温度125℃恒温3h,二段温度直接升温165℃,电解电压4.5v,电流密度50a/m2,超声波发生器功率调节为5-15kw。
16.载金炭解吸电解工艺中,由于金铜银电积电位不同,金属络合离子的阴极放电顺序为:ag(cn)
2->cu(cn)
2->au(cn)
2->fe(cn)
2-,解吸电解液电解过程铜银优先于金电解。温度在125℃时银电解率达到波峰,一段恒温过程中银优先于金和铜得到快速提取,故一段
温度125℃恒温3h,二段温度直接升温165℃。先快速回收银,后续在超声波的强力浸出作用下,快速提取金和铜。
17.此类载金炭规模化解吸电解工艺中,装有载金炭的解吸柱作为浸出系统,解吸柱柱顶设有传统的出液管、安全阀外,包含2套超声波聚能器,将2套超声聚能器从柱顶分别下放至解吸柱内,下放深度为离近柱底位置,两组超声波聚能器平均发布于炭层中;在启动电加热器、整流柜开始正常解吸电解作业的情况下,同时开启2套超声波发生器,此时超声波通过超声波聚能器同时作用于解吸柱内炭床中;超声波聚能器和超声波发生器运行周期为半年,每柱开机时间为8小时,期间测量并记录贵、贫液的金、银、铜目标元素浓度及解吸电解流量,计算出矿层渗透系数和浸出速率的变化。超声波能量促进解吸电解液与炭表面充分接触,加快金属络合离子从炭中脱附,进入解吸电解液中,实现快速提取金银铜,同时防止硫酸钙微溶物在解吸柱筛网表面的附着与堵孔。
18.下放深度为离近柱底位置为离解吸柱柱定1.5m,超声波发生器功率调节范围为5-15kw,功率可调节,调节方式为先低后高,超声波聚能器主体材料为能耐高温及强碱腐蚀的310s不锈钢或钛合金材料,超声波聚能器长度为6-9m。
19.有益效果:该类载金炭在吸附金银的同时,大量的钙、铜、硫等杂质被吸附,载金炭在氰化钠及氢氧化钠溶液中发生浸出反应时,铜、钙等同金银被溶解至解吸贵液中。在解吸柱筛网、管道内极易生成类似面糊状的物质,阻碍解吸液正常流动,影响金银铜贫炭指标和解吸率指标,对该物质检测研究表明,该物质主要为粘稠性大的硫酸钙水合物,由于工艺设备为全封闭设备,难以及时清理,对生产影响极大。
20.活性炭解吸电解工艺中,由于金铜银电积电位不同,金属络合离子的阴极放电顺序为:ag(cn)
2->cu(cn)
2->au(cn)
2->fe(cn)
2-,解吸液电解过程铜银优先于金电解,但高配合物的铜氰络合离子其电积电位低,不利于析出,考虑金银回收,在高氰化钠条件下,解吸开始阶段,铜以cu(cn)
43-和cu(cn)
32-高配合物形式存在,传统方法起始阶段铜电解率偏低。
21.传统工艺为“氰化钠(0.5%) 氢氧化钠(3%) 高温高压解吸电解(温度150℃、时间20)”,本发明工艺为:载金炭漂洗去处木屑 载金炭脱泥(回水冲洗0.5-1h) 氰化钠(0.2-0.3%) 氢氧化钠(2-2.2%) 六偏磷酸钠(10kg/t) 高温高压(125℃3h后直升165℃) 超声波(5-15kw),解决原工艺存在的技术瓶颈。通过试验研究及实际生产应用对比发现,本发明金银铜解吸率指标明显提高、解吸电解设备运行稳定性、解吸药剂单耗明显下降、解吸电解时间明显缩短。
22.在载金炭装柱前,采用回水池上清液进一步清洗脱泥,确保炭洁净度,避免泥质进入解吸电解系统,大量消耗氰化钠,降低金银解吸率,且金泥含泥增加,该回水二次沉降后可重复循环使用,增强了水资源综合利用效率。
23.采用载金炭脱泥 氰化钠 氢氧化钠 六偏磷酸钠 高温高压 高电压 超声波的方法,获得理想的效果。
24.六偏磷酸钠作用:(1)活性炭高温高压解吸过程中,能软化高钙、硫解吸液,促进解吸液的流动及循环;
(2)六偏磷酸钠与硫酸钙水合物反应生成na4[ca(p03)6],阻止钙、铁等杂质形成粘稠性物(该物质易附着在筛网及管道上、影响流量稳定),同时能够降低解吸液粘度,保障管道筛网畅通及解吸流量的稳定;(3)六偏磷酸钠提供部分钠离子,在发生解吸反应时能够快速替代氰金银,促进金银铜离子的快速溶解;(4)铜氰络合溶液电积过程中起到氰根保护剂及促进铜电解反应的作用,电解过程可降低氰根离子在阳极的氧化损失,同时保护剂与铜离子在阴极发生复杂的电化学反应,从而可促进和提高铜的电解回收率,且药剂不影响活性炭金银解吸。
[0025]
目前,国内外尚无针对高银铜钙复杂载金炭,采用六偏磷酸钠作为解吸电解药剂的相关应用研究。超声波作为一种机械波,其震动频率在20khz以上,在传播时具有方向性好、穿透力强、能量集中以及可引起空化作用等优点,被广泛应用于测距测速、采油、碎石、废水处理、防除结垢、湿法冶金等方面。但在全泥氰化氰化炭浆领域中,超声波仅仅应用于设备清洗及氰化浸出过程,而超声波作用载金炭解吸电解过程从而提高金银铜解吸率、解决管道设备堵塞的方法在国内尚属空白。
[0026]
超声波能量促进解吸电解液与炭表面充分接触,加快金属络合离子从炭中脱附,进入解吸电解液中,实现快速提取金银铜,同时防止硫酸钙微溶物在解吸柱筛网表面的附着与堵孔,解吸贫炭中金银铜品位、解吸电解时间、药耗明显下降,金银铜解吸率指标显著提升、筛网及管道堵塞问题彻底解决。
[0027]
该工艺解决了传统工艺解吸电解设备效率低、设备运行稳定性差、金银解吸率低、铜难以回收等技术难题。
[0028]
该工艺对高银、铜、钙复杂载金炭实现了铜、金、银的高效综合提取,资源价值得到最大化利用,且金银铜解吸率指标稳定性较好,工艺适应性较强,其有较好的潜在商业推广价值。
[0029]
该工艺采用回水分阶段、针对性地分别循环利用,即浮选回水用于浮选系统和氰化浸出系统回水用于浸出系统,有效地避免了不同阶段回水交叉而产生的不良后果,使回水得到最大限度地高效提取利用,增强了水资源综合利用效率,降低了环境污染风险。
[0030]
本发明针对针对含au>500g/t、ag>4000g/t、cu>15000g/t、ca>20000g/t、fe>4000g/t的复杂载金炭,获得合格金泥,贫炭金银铜品位和解吸率处于国内外前列,同时,解吸电解时间、药耗大幅下降,达到高效综合提取金、银、铜、硫的目的。本发明解决了以下问题:(1)从高银铜钙复杂载金炭中综合高效提取金、银、铜等有价成分;(2)解决了高钙引起的管道筛网频繁堵塞、解吸流量不稳定、解吸泵和加热器等设备难以正常运行的问题。
[0031]
(3)解决贫炭金银品位高和金银解吸率低的问题;(4)解决传统方法铜难以回收的问题;(5)解决从高银铜钙复杂载金炭中提取金银铜,氰化钠和氢氧化钠药耗高、解吸电解耗时长的问题。
具体实施方式
[0032]
以下结合具体实施例来进一步说明本发明,但实施例并不对本发明做任何形式的限定。在不背离本发明精神和实质的情况下,对本发明方法、步骤或条件所作的简单修改或替换,均属于本发明的范围。
[0033]
实施例一:我国南方某多金属黄金矿山,载金炭日处理量量4t/d生产车间内技术应用。
[0034]
2017年以来因矿石性质变化,地面易选冶氧化矿逐渐减少,逐渐向深部氧硫混合带采矿,矿石中除金银外还赋存有硫铁铜等,选冶流程大量使用石灰,致使活性炭在吸附过程中吸附大量银、铜、钙、铁等元素,含au大于952g/t、ag大于5382.95g、/t、cu大于20000g/t、ca大于25000g/t。2017年-2018年使用传统“氰化钠(0.5%) 氢氧化钠(3%) 高温高压解吸电解(温度150℃、时间20)”工艺处理该载金炭,生产难以稳定运转。2020-2021年采用载金炭漂洗去处木屑 载金炭脱泥(回水冲洗0.5-1h) 氰化钠(0.2-0.3%) 氢氧化钠(2-2.2%) 六偏磷酸钠(10kg/t) 高温高压(125℃3h后直升165℃) 超声波(5-15kw)处理。工艺改进前后对比分析。
[0035]
最终得到以下结论:2018年传统工艺,解吸柱筛网需要1天1拆,解吸流量只有2-3m3/h(正常需要4-6m3/h),氰化钠耗用6.08kg/t,氢氧化钠耗用26.26kg/t,每柱解吸电解时间20.85h,贫炭含au144.63g/t、ag153.93g/t,金银铜解吸率分别为84.3%、96.73%和40%。通过系统小型试验研究及工艺技术优化后,采用新方法,解吸柱筛网拆换频次从1天1拆降至15天1拆,解吸电解液流量从2-3m3/h提升至5-6m3/h,氰化钠耗用从6.08kg/t降至4kg/t,氢氧化钠耗用26.26kg/t降至20kg/t,每柱解吸电解时间从20.85h大幅度降至10h,贫炭含au36.77g/t、ag72.07g/t,金解吸率从原来的84.3%提升至95.17%,银解吸率从原来的96.73%提升至98.36%,铜解吸率从原来的20%提升至80%,金解吸率提升10.87%以上,银解吸率提升1.63%以上,铜解吸率提升60%以上。
[0036]
实施例二:我国南方某多金属黄金矿山,载金炭日处理量量8t/d生产车间内技术应用。
[0037]
活性炭在吸附过程中吸附大量银、铜、钙、铁等元素,含au大于732g/t、ag大于5000g、/t、cu大于15000g/t、ca大于2000g/t。2018年-2019年使用传统“氰化钠(0.5%) 氢氧化钠(3%) 高温高压解吸电解(温度150℃、时间20)”工艺处理该载金炭,生产难以稳定运转。2020-2021年采用载金炭漂洗去处木屑 载金炭脱泥(回水冲洗0.5-1h) 氰化钠(0.2-0.3%) 氢氧化钠(2-2.2%) 六偏磷酸钠(10kg/t) 高温高压(125℃3h后直升165℃) 超声波(5-15kw)处理。工艺改进前后对比分析。
[0038]
最终得到以下结论:2019年传统工艺,解吸柱筛网需要2天1拆,解吸流量只有7-8m3/h(正常需要10-12m3/h),氰化钠耗用5.6kg/t,氢氧化钠耗用25.13kg/t,每柱解吸电解时间18.87h,贫炭含au135.72g/t、ag219.83g/t,金银铜解吸率分别为85.77%、95.67%和30%。通过系统小型试验研究及工艺技术优化后,采用新方法,解吸柱筛网拆换频次从2天1拆降至20天1拆,解吸电解液流量从7-8m3/h提升至10-11m3/h,氰化钠耗用从5.6kg/t降至3kg/t,氢氧化钠耗用25.13kg/t降至20kg/t,每柱解吸电解时间从18.87h大幅度降至10h,贫炭含au32.66g/t、ag58.62g/t,金解吸率从原来的85.77%提升至95.54%,银解吸率从原来的95.67%提升至98.76%,铜解吸率从原来的30%提升至75%,金解吸率提升9.97%以上,银解
吸率提升3.09%以上,铜解吸率提升45%以上。
[0039]
表1 相应的对比实验分析对比例1效果:
①
拆换筛网频率:1天1拆降至5-6天1拆;
②
解吸流量:由原来的1倍炭床体积提升至2倍炭床体积;
③
解吸时间:由原来基础上下降百分之20%。
[0040]
④
解吸率:金解吸率由以前的84-90%,提升至90-93%。
[0041]
对比例2效果:
①
拆换筛网频率:1天1拆降至3-4天1拆;
②
解吸流量:由原来的1倍炭床体积提升至2倍炭床体积;
③
解吸时间:由原来20-21h/柱降至11-13h/柱;
④
解吸率:金解吸率由以前的90%提升至92-95%;银解吸由原来的94-95%提升96-98%;铜解吸率由原来的40%提升至60%以上。
[0042]
对比例3效果:
①
拆换筛网频率:1天1拆降至12-13天1拆;
②
解吸流量:由原来的1倍炭床体积提升至3-4倍炭床体积;
③
解吸时间:由原来20-21h/柱降至10-11h/柱;
④
解吸率:金解吸率由以前的90%提升至95-96%;银解吸由原来的94-95%提升97-98%;铜解吸率由原来的40%提升至60%以上。
[0043]
⑤
贫炭金银品位:由原来的100-200g/t降至60g/t以内;对比例4效果:
①
拆换筛网频率:1天1拆降至13-14天1拆;
②
解吸流量:由原来的1倍炭床体积提升至4-5倍炭床体积;
③
解吸时间:由原来20-21h/柱降至10h/柱;
④
解吸率:金解吸率由以前的90%提升至96%以上;银解吸由原来的94-95%提升98%以上;铜解吸率由原来的40%提升至60%以上;
⑤
贫炭金银品位:由原来的100-200g/t降至50g/t以内;
⑥
氰化钠药耗:降至3kg/吨以内。
[0044]
综上所述,采用该工艺铜大部分得到提取,金银解吸率提高了,矿产资源得到较好的综合利用。更重要的是,总氰化钠和氢氧化钠消耗较大幅度降低,贫炭金银品位也大幅度下降,解吸时间大幅缩短,解吸电解系统得到稳定运行。表明,采用该工艺指标较稳定较好,适应性较强,特别对金、铜的提取指标有较大幅度的提高。
再多了解一些
本文用于创业者技术爱好者查询,仅供学习研究,如用于商业用途,请联系技术所有人。