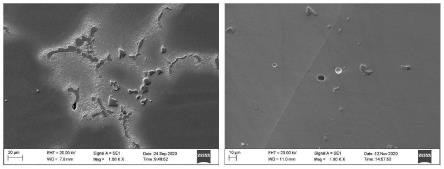
1.本发明涉及一种镍基高温合金热轧板的制造方法,属于特种合金材料制作领域。
背景技术:
2.镍基高温合金具有良好的热强性和良好的耐蚀性。通常在耐蚀用途中,主要用以耐hno3、hno3 h2so4、hno3 hf的混酸以及含h2so4和f
-
、cl
-
的湿法磷酸以及耐海水腐蚀等,在时效状态下也优良的耐氯化物和硫化物应力腐蚀的性能以及耐晶间腐蚀、耐点蚀、耐缝隙腐蚀等性能。可用于耐蚀高强度材料,制造塔、槽、容器、管线以及反应器、换热器、阀件等。
3.影响镍基高温合金耐蚀性的主要因素有合金内夹杂物水平和碳化物析出程度,获得超纯净的钢锭母材,可以给材料性能的提高奠定良好基础。
4.而晶间腐蚀是由于cr
23
c6的析出导致晶界附近出现贫铬区,从而降低了合金的耐晶间腐蚀性能。为了提高耐晶间腐蚀性能,大都采用固溶化处理以及稳定化处理。但是目前稳定化处理在镍基高温合金上应用工艺报道较少,而且固溶加稳定化处理的时间大都在20小时以上,存在效率低、能耗高等缺点。因此研究一种适用于提高镍基高温合金的耐晶间腐蚀性能的热处理工艺具有重要的意义。
技术实现要素:
5.为了克服上述不足,本发明旨在提供一种镍基高温合金热轧板的制造方法,在电渣重熔环节特别在渣面补入强脱氧剂al粒,避免了钢锭熔池中al与预熔渣反应导致产品al含量散失及渣面反应产物al2o3夹杂物向熔池内扩散导致产品纯净度恶化的倾向。为了解决高合金钢在凝固过程中产生的偏析问题,在锻造前将电渣锭进行均质化操作,成分的均匀一致促使产品性能提高。为了提高材料的耐晶间腐蚀性能,热处理时采用三级温度梯度保温处理,尽量避免碳化物的析出。
6.本发明的技术思路:(1) 、合金冶炼合金首先采用真空感应炉熔炼,按照高温合金通用冶炼方法生产。
7.真空锭表面氧化皮如不清理干净,进行重熔后变成夹杂物影响母材性能,因此表面氧化皮的车光是十分必要的。
8.(2) 、电渣重熔采用电渣重熔工艺进一步提高产品的纯净度及合金质量,本发明中的高温合金成分中含有0.2-0.8%的al元素,含量较高的易氧化元素al极易与预熔渣中的feo反应生成al2o3夹杂物而污染钢水,因此在电渣过程中向预熔渣内少量的加入al粒与casi粉,生成的al2o3夹杂物可与cao结合保持在渣内,可有效阻止熔池中al元素的散失及夹杂物扩散。
9.(3) 、电渣锭均质化镍基高温合金中含有较高的合金元素,凝固过程极易发生成分偏析,解决成分偏析最有效途径为均质化操作,本发明采用两段式保温,均质化温度为1120℃、保温20h,然后
升至1220℃保温时间60h。
10.(4) 、钢板热处理首先,将镍基高温合金热轧态试样进行1120℃保温的高温固溶处理,保温时间过长晶粒长大或不均匀,因此保温时间要根据钢板厚度而定,经验时间≤60min,固溶后使析出相回溶并获得均匀的晶粒度,将固溶处理后的镍基高温合金在本发明提供的温度范围内进行分段式加热保温热处理,首先快速度通过cr
23
c6的析出温度范围,尽可能少的析出cr
23
c6以减少晶界贫铬,然后再通过nbc的优先形成以避免cr
23
c6形成所导致的晶界贫铬,以及cr
23
c6的回溶从而综合提高合金的耐晶间腐蚀性能。
11.本发明提供了一种镍基高温合金热轧板的制造方法,其中,镍基高温合金成分(%代表的是质量百分比)如下:c≤0.08、si≤0.35、mn≤0.35、p≤0.015、s≤0.015、cr 17.00~21.00、nb ta 4.75~5.50、co≤1.00、mo:2.8~3.30、al:0.20~0.80、ti:0.65~1.15、ni:50.00~55.00、fe余量。
12.上述制造方法,按照以下步骤进行:(1)真空感应炉冶炼出直径300mm-400mm的原始钢锭坯,并将钢锭表面氧化皮用车床切削干净后使用电渣炉进行电渣重熔操作。电渣重熔开始前底吹氩气对熔体进行保护,流量为80-100nl/min,电极开始熔化后计时,每隔5min向预熔渣面上加入al粒50~55g,ca-si粉20~30g直至电极全部重熔完毕,关闭氩气阀门。
13.(2)电渣锭锻造前均质化:将钢锭低于500℃入炉,以小于80℃/h的升温速度升至1120
±
10℃,保温20
±
2h,然后升至1220-1230℃保温时间60-70h,炉冷至800-900℃后空冷;(3)锻造板坯:用砂轮修磨净表面氧化皮后进加热炉加热,加热炉均热段温度1280
±
10℃,保温时间60-70min后轧制成5-20mm厚度的热轧板;(4)钢板热处理及稳定化:先将钢板进行固溶处理,1120
±
10℃保温时间≤60min,获得均匀晶粒度;固溶后进行稳定化操作,第一个保温温度为200℃,时间为2~3h,然后以≤50℃/h升温速度升至500℃;第二个保温温度为500℃,时间为2~3h,然后以≤80℃/h升温速度升至1000-1020℃;第三个保温温度为1000-1020℃,保温8-12h,然后出炉空冷。
14.经本发明方法生产的镍基高温合金热轧板,具有良好的抗晶间腐蚀性能,腐蚀速率较不补入强脱氧剂al粒和不采用三级温度梯度保温处理的工艺降低20-40%。本发明保证了产品成分满足标准的同时可使产品全氧含量降低至20
×
10
-6
以下,夹杂物级别d类细系0.5级。
15.本发明的有益效果:(1)本发明在电渣重熔时不间断的加入强脱氧剂,使本发明中涉及的镍基高温合金钢锭全氧及纯净度降低至极低水平,原料上减少了因夹杂物引起的腐蚀性能下降问题,产品成分满足标准的同时可使产品全氧含量降低至20
×
10
-6
以下,夹杂物级别d类细系0.5级;(2)电渣锭开坯前进行均质化操作,消除镍基高温合金中易偏析元素的偏析问题,成分更加均匀,大幅度提升了产品的最终使用性能,采用均质化后电渣锭锻造轧制成的热
轧板无明显成分偏析,性能良好,屈服强度和抗拉强度均有所提高。
16.(3)热轧板进行三级温度梯度保温处理,200℃的低温段保温防止高合金温度急剧升高时导致的开裂问题,500℃的中温段保温预热,可以使钢板快速通过cr
23
c6析出的敏感温度区间,1000℃的高温段长时间保温溶解cr
23
c6的同时促进nbc的析出,进一步避免了由cr
23
c6形成所导致的晶界铬贫,钢板获得了良好的耐晶间腐蚀性能,腐蚀速率较正常工艺降低20-40%,并进一步改善其综合性能。
附图说明
17.图1为实施例1均质化处理前(左)和均质化处理后(右)sem图;图2为实施例1的夹杂物图。
18.图3为实施例1稳定化处理前(左)和1000℃稳定化处理后(右)的sem图;图4为实施例2稳定化处理前和(左)1010℃稳定化处理后(右)sem图;图5为实施例3稳定化处理前(左)和1020℃稳定化处理后(右)sem图。
具体实施方式
19.下面通过实施例来进一步说明本发明,但不局限于以下实施例。
20.实施例1:实施的步骤依次如下:1、真空感应炉冶炼出尺寸φ470mm的坯料,成分(%质量百分比)为:c 0.05%、si 0.30%、mn 0.28%、p 0.013%、s 0.001%、cr 17.50%、nb ta 5.20%、co 0.05%、mo 3.00%、al 0.30%、ti 0.70%、ni 51.00%、fe余量。
21.2、车床将真空感应锭表面氧化皮车削干净,后作为电极进行电渣重熔。电渣重熔时开始前底吹氩气对熔体进行保护,流量为90nl/min,送电后,电极开始熔化计时,每隔5min向预熔渣面上加入al粒50g,ca-si粉20g直至电极全部重熔完毕,关闭氩气阀门。
22.3、电渣锭锻造前将钢锭均质化,300℃入炉,60℃/h的升温速度升至1120℃,保温20h,然后升至1220℃保温时间60h,出炉锻造成尺寸200mm(厚)
×
1500mm(宽)
×
l的板坯。均质化处理前后效果如图1所示。从图1可以看出:凝固过程中析出的有害相已全部回溶,增加了材料的可加工性。
23.4、锻造板坯用砂轮修磨净表面氧化皮,坯料磨后表面粗糙度108μm,进加热炉加热,加热炉均热段温度1260℃,保温时间60min后轧制成10mm厚钢板。
24.5、钢板热处理,1110℃保温30min,后空冷。
25.6、钢板稳定化处理,将加热炉炉温升至200℃,将固溶处理态的镍基高温合金装入热处理炉,保温2h;以30℃/h升温速度升至500℃,保温2h;以60℃/h升温速度升至1000℃,保温8h后出炉冷却。
26.将实施例1中的镍基高温合金钢板中全氧含量16
×
10
-6
,夹杂物图片如图2所示。从图2可以看出:可见夹杂物较少,评为d类0.5级,材料的纯净度大大提高。
27.进行晶间腐蚀试验检测,检测结果如下表1所示。从表1可以看出:耐晶间腐蚀性能明显提高。
28.表1 晶间腐蚀性能检测结果
图3为实施例1稳定化处理前(左)和1000℃稳定化处理后(右)的sem图;从图3可以看出:析出相已全部溶解,晶内及晶界都已无析出相。
29.实施例2:1、真空感应炉冶炼出尺寸φ470mm的坯料,成分(%质量百分比)为:c 0.06%、si 0.30%、mn 0.28%、p 0.013%、s 0.001%、cr 17.50%、nb ta 5.20%、co 0.05%、mo 3.00%、al 0.30%、ti 0.70%、ni 51.00%、fe余量。
30.2、车床将真空感应锭表面氧化皮车削干净,后作为电极进行电渣重熔。电渣重熔时开始前底吹氩气对熔体进行保护,流量为90nl/min,送电后,电极开始熔化计时,每隔5min向预熔渣面上加入al粒50g,ca-si粉20g直至电极全部重熔完毕,关闭氩气阀门。
31.3、电渣锭锻造前将钢锭均质化,300℃入炉,60℃/h的升温速度升至1120℃,保温20h,然后升至1220℃保温时间60h,出炉锻造成尺寸200mm(厚)
×
1500mm(宽)
×
l的热轧板坯。
32.4、锻造板坯用砂轮修磨净表面氧化皮,坯料磨后表面粗糙度108μm,进加热炉加热,加热炉均热段温度1270℃,保温时间60min后轧制成10mm厚钢板。
33.5、钢板热处理,1110℃保温30min,后空冷。
34.6、钢板稳定化处理,将加热炉炉温升至200℃,将固溶处理态的镍基高温合金装入热处理炉,保温2h;以30℃/h升温速度升至500℃,保温2h;以60℃/h升温速度升至1010℃,保温12h后出炉冷却。
35.将实施例2中的镍基高温合金钢板中全氧含量17
×
10
-6
。进行晶间腐蚀试验检测,检测结果如下表2所示。从表2可以看出耐晶间腐蚀性能明显提高。
36.表2 晶间腐蚀性能检测结果图4为实施例2稳定化处理前和1010℃稳定化处理后sem图;从图4可以看出:析出相已全部溶解,晶内及晶界都已无析出相。
37.实施例3:1、真空感应炉冶炼出尺寸φ470mm的坯料,成分(质量百分比)为:c 0.07%、si 0.30%、mn 0.28%、p 0.013%、s 0.001%、cr 17.50%、nb ta 5.20%、co 0.05%、mo 3.00%、al 0.30%、ti 0.70%、ni 51.00%、fe余量。
38.2、车床将真空感应锭表面氧化皮车削干净,后作为电极进行电渣重熔。电渣重熔时开始前底吹氩气对熔体进行保护,流量为90nl/min,送电后,电极开始熔化计时,每隔
5min向预熔渣面上加入al粒50g,ca-si粉20g直至电极全部重熔完毕,关闭氩气阀门。
39.3、电渣锭锻造前将钢锭均质化,300℃入炉,60℃/h的升温速度升至1120℃,保温20h,然后升至1220℃保温时间60h,出炉锻造成尺寸200mm(厚)
×
1500mm(宽)
×
l的热轧板坯。
40.4、锻造板坯用砂轮修磨净表面氧化皮,坯料磨后表面粗糙度108μm,进加热炉加热,加热炉均热段温度1290℃,保温时间60min后轧制成10mm厚钢板。
41.5、钢板热处理,1130℃保温30min,后空冷。
42.6、钢板稳定化处理,将加热炉炉温升至200℃,将固溶处理态的镍基高温合金装入热处理炉,保温2h;以30℃/h升温速度升至500℃,保温2h;以60℃/h升温速度升至1020℃,保温12h后出炉冷却。
43.将实施例3中的镍基高温合金钢板中全氧含量15
×
10
-6
。进行晶间腐蚀试验检测,检测结果如下表3所示。从表3可以看出:耐晶间腐蚀性能明显提高。
44.表3 晶间腐蚀性能检测结果图5为实施例3稳定化处理前和1020℃稳定化处理后sem图。从图5可以看出:析出相已全部溶解,晶内及晶界都已无析出相。
再多了解一些
本文用于创业者技术爱好者查询,仅供学习研究,如用于商业用途,请联系技术所有人。