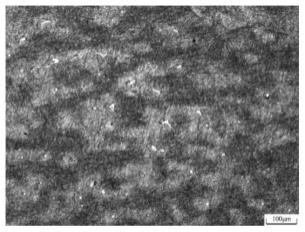
1.本发明涉及一种适用于高强钢轧制的成品机架工作辊的制备方法,属于特色化轧辊材料技术领域。
背景技术:
2.随着各轧线高强钢、薄板坯等特殊板材比例的增加,使得全面实现全线高速钢的应用需求愈发迫切:如何提高产线效率,如何在单位时间之内获得高效产出,以及如何使得轧辊在机周期间获得更多的产量,高性能轧辊无疑是解决当前迫切需求的有效途径之一。当前,粗轧、精轧前段都相应有对应的材质来适应轧线长辊役的需求,因精轧后段机架尤其是成品机架存在表面质量要求高、甩尾的工况特点,使得精轧后段轧辊目前仍以高镍铬为主。但是,该种轧辊在轧制硅钢、高强钢等高附加值产品时存在在机辊役短,板面存在双边浪的问题,因此,研发精轧后段、尤其是成品机架高速钢,来满足精轧后段高表面质量及长辊役的轧制需求显得尤为关键。
3.如何设计全新精轧后段尤其是成品机架工作辊的基体成分,如何设计铸造参数,如何设计与新材料相匹配的热处理工艺等技术参数都是开发高性能精轧轧辊材料急需解决的问题。
技术实现要素:
4.本发明通过对热连轧轧制薄板、硅钢等特殊板材的轧制工况及使用问题进行调研及分析,采用创新方法,最终得出了适应于精轧后段尤其是成品机架的解决方案,提供了一种适用于硅钢等高强钢轧制的高性能成品机架工作辊制备方法,提高工作层的耐磨性及硬度,解决了现有轧辊在轧制硅钢、高强钢等高附加值产品时存在在机辊役短,板面存在双边浪的问题。
5.为解决上述技术问题,本发明所采用的技术方案是:
6.一种适用于高强钢轧制的成品机架工作辊的制备方法,包括如下步骤:
7.步骤a、采用废钢、钒铁、钼铁、硅铁、锰铁为初始炉料进行配料,分为外层及芯部材质;
8.工作辊外层化学组分为:c 0.4-1.0,si 0.2-1.2,mn 0.2-1.5,cr 2.0-8.0,ni 0.2-3.0,mo 3.0-12.0,v 2.0-10.0,0.3≤w≤0.8,0.2≤nb≤1.0,余量为fe,其中,外层c还需满足:c≤(0.06
×
cr% 0.063
×
mo% 0.033
×
w% 0.235
×
v% 0.13
×
nb% 0.25
×
ti%)/3;外层碳化物含量≤2.0%;
9.工作辊芯部材质为石墨钢,化学组分为:c 1.5-2.0,si 0.8-2.0,mn 0.5-1.0,cr≤0.6,ni 0.1-1.0,mo 0.1-0.8,v≤0.1,其余杂质元素总含量不超过0.1%,余量为fe;
10.步骤b、采用灰铁冷型,喷涂1-2mm锆英粉在灰铁冷型内壁;
11.步骤c、在中频炉中进行熔炼,外层钢液熔化完毕后提温至1610-1710℃保温5-10min后出炉,温度降至1550-1560℃开始浇注;芯部钢水熔炼完毕后提温至1600-1700℃保
温5-10min出炉,温度降至1500-1510℃开始浇注芯部;
12.步骤d、毛坯在浇注完毕后50-100h开箱,开箱后放置在高温炉中进行预备热处理;
13.步骤e、对产品进行粗加工,粗加工完毕后进行热处理,热处理完毕后进行精加工直至成品。
14.本发明技术方案的进一步改进在于:所述步骤b中灰铁冷型在浇注前进行预热,预热温度100-200℃,预热时间2-10h。
15.本发明技术方案的进一步改进在于:所述步骤c中外层钢液浇注前进行吹氩处理,吹氩时间2-10min。
16.本发明技术方案的进一步改进在于:所述步骤d中预备热处理温度800-900℃,保温时间10-20h,加热结束采用空冷的方式进行冷却,冷却至辊身550-600℃装炉,保温5-10h后以≤10℃/h的速率进行炉冷。
17.本发明技术方案的进一步改进在于:所述步骤e中热处理方式为高温热处理,采用等硬层热处理技术,包括加热时间在5-10min内工作层径向和轴向温度差控制在5-10℃范围内,加热时间55-65min,工作层加热温度1000-1100℃,冷却采用高压喷雾 喷风的方式进行冷却,冷却风压0.4-0.5mpa、水压0.3-0.35mpa下喷雾10-30min,风压0.3-0.5mpa吹30-60min,辊面温度至430-460℃停风,空冷30-300min至辊身200-500℃装炉,回火2-3次,回火温度500-600℃,保温时间25-50h。
18.本发明技术方案的进一步改进在于:制备的工作辊的辊身硬度范围在hsd80-90,辊颈硬度hsd38-50,辊颈强度≥600mpa。
19.由于采用了上述技术方案,本发明取得的技术进步是:
20.本发明基于高镍铬在精轧后段及成品机架使用过程中板面边部存在边浪及无法提升辊役的问题,从提高材质耐磨性,同时需保证轧辊材质性能均匀性上进行研究,通过使主要的合金均进入基体获得高耐磨性的基体,避免了基体中夹杂着过多硬质相碳化物,导致磨损不均影响板面的情况,因此通过增加合金元素的同时,避免大量的合金元素以碳化物的形式存在,限定了碳化物形成元素c的加入含量,即
21.c≤(0.06
×
cr% 0.063
×
mo% 0.033
×
w% 0.235
×
v% 0.13
×
nb% 0.25
×
ti%)/3,
22.碳化物含量≤2.0%,通过该技术发明,对c含量进行限定,使碳化物的含量进行了限定,使得合金元素主要进入基体达到强化基体,达到提高基体耐磨性的目的。
23.本发明采用改善基体组织,通过限定碳化物含量,合金元素适量的形成碳化物,其余合金元素进入基体,强化基体,提高基体强度,获得马氏体基体组织,相较于常规成品机架使用的高镍铬工作辊,组织类型变为了马氏体,基体强度可达到hv630以上,较高镍铬基体显微硬度(hv≥520)明显提高,同时,形成少量的碳化物作为硬质相,避免过多的碳化物导致碳化物与基体的不均匀磨损。
附图说明
24.图1是本发明显微组织示意图;
25.图2是粗轧高速钢显微组织示意图;
26.图3是精轧前段高速钢显微组织示意图;
27.图4是高镍铬显微组织示意图。
具体实施方式
28.下面结合实施例对本发明做进一步详细说明:
29.实施例1:
30.废钢、钒铁、钼铁、硅铁、锰铁等原材料,分别利用工频感应熔炼炉熔炼外层及芯部钢水,外层成分达到设计组分:c 0.46%,si 0.95%,mn 0.65%,p≤0.05%,s≤0.06%,cr 3.6%,ni 0.39%,mo 8.96%,v 8.93,w 0.56%,nb 0.39和fe余量,芯部成分c1.85,si 1.26,mn 0.85,cr 0.35,ni 0.19,mo 0.13,v 0.06的标准成分后,将外层钢液温度加热到1635℃出钢,0.25mpa吹氩3.5min,温度降至1558℃后浇注,芯部钢水在1620℃出炉,在1510℃浇注;浇注完毕后60h开箱。开箱后粗加,在960℃进行保温30h后空冷,空冷至辊身520℃时装炉以8℃/h的冷却速度进行炉冷。炉冷结束进行粗加工,粗加辊身直径余量5mm,辊身长度余量20mm,利用高温加热炉在1050℃下加热60min,加热结束后在0.5mpa风压、0.3mpa水压下对辊身喷雾25min,在风压0.45mpa的参数下吹风55min,空冷至350℃装炉回火,530℃回火保温35h,两次回火后卸炉,进行后续加工至成品。
31.如图1所示为实施例1的电子显微镜图片,高性能成品机架工作辊碳化物含量少,仅在晶界部位析出二次碳化物,起到了第二相质点强化的作用,同时,对于轧制温度高的硅钢来说,还有利于提高产品的抗热裂性,尤其是结合给工作层的等硬层热处理工艺技术,有利于实现工作层的轴向及径向均匀磨损。
32.实施例2
33.废钢、钒铁、钼铁、硅铁、锰铁等原材料,分别利用工频感应熔炼炉熔炼外层及芯部钢水,外层成分达到设计组分:c 0.89%,si 0.93%,mn 0.63%,p≤0.03%,s≤0.05%,cr 3.5%,ni 0.36%,mo 11.53%,v 8.53,w 0.46%,nb 0.37和fe余量,芯部成分c1.89,si 1.23,mn 0.86,cr 0.31,ni 0.16,mo 0.11,v 0.05的标准成分后,将外层钢液温度加热到1625℃出钢,0.26mpa吹氩3.3min,温度降至1535℃后浇注,芯部钢水在1610℃出炉,在1500℃浇注;浇注完毕后55h开箱。开箱后粗加,在930℃进行保温33h后空冷,空冷至辊身510℃时装炉以9℃/h的冷却速度进行炉冷。炉冷结束进行粗加工,粗加辊身直径余量6mm,辊身长度余量15mm,利用高温加热炉在1080℃下加热55min,加热结束后在0.4mpa风压、0.4mpa水压下对辊身喷雾28min,在风压0.46mpa的参数下吹风56min,空冷至380℃装炉回火,550℃回火保温39h,两次回火后卸炉,进行后续加工至成品。
34.实施例3
35.废钢、钒铁、钼铁、硅铁、锰铁等原材料,分别利用工频感应熔炼炉熔炼外层及芯部钢水,外层成分达到设计组分:c 0.95%,si 0.80,mn 0.63%,p≤0.06%,s≤0.06%,cr 256%,ni 0.89%,mo 10.53%,v 9.65,w 0.53%,nb 0.39和fe余量,芯部成分c1.93,si 1.28,mn 0.89,cr 0.35,ni 0.19,mo 0.15,v 0.06的标准成分后,将外层钢液温度加热到1620℃出钢,0.25mpa吹氩3.9min,温度降至1539后浇注,芯部钢水在1650℃出炉,在1500℃浇注;浇注完毕后53h开箱。开箱后粗加,在920℃进行保温35h后空冷,空冷至辊身530℃时装炉以10℃/h的冷却速度进行炉冷。炉冷结束进行粗加工,粗加辊身直径余量8mm,辊身长度余量19mm,利用高温加热炉在1030℃下加热60min,加热结束后在0.45mpa风压、0.4mpa水
压下对辊身喷雾28min,在风压0.46mpa的参数下吹风59min,空冷至500℃装炉回火,530℃回火保温40h,两次回火后卸炉,进行后续加工至成品。
36.实施例4
37.废钢、钒铁、钼铁、硅铁、锰铁等原材料,分别利用工频感应熔炼炉熔炼外层及芯部钢水,外层成分达到设计组分:c 0.35%,si 0.75,mn 0.70%,p≤0.07%,s≤0.05%,cr 2.39%,ni 0.75%,mo 11.35%,v 8.53,w 0.36%,nb 0.41和fe余量,芯部成分c1.79,si 1.21,mn 0.81,cr 0.23,ni 0.11,mo 0.11,v 0.03的标准成分后,将外层钢液温度加热到1650℃出钢,0.29mpa吹氩4.5min,温度降至1520后浇注,芯部钢水在1635℃出炉,在1512℃浇注;浇注完毕后56h开箱。开箱后粗加,在950℃进行保温33h后空冷,空冷至辊身520℃时装炉以9℃/h的冷却速度进行炉冷。炉冷结束进行粗加工,粗加辊身直径余量6mm,辊身长度余量17mm,利用高温加热炉在1085℃下加热65min,加热结束后在0.49mpa风压、0.41mpa水压下对辊身喷雾26min,在风压0.49mpa的参数下吹风55min,空冷至520℃装炉回火,550℃回火保温39h,两次回火后卸炉,进行后续加工至成品。
38.实施例5
39.废钢、钒铁、钼铁、硅铁、锰铁等原材料,分别利用工频感应熔炼炉熔炼外层及芯部钢水,外层成分达到设计组分:c 0.65%,si 0.79,mn 0.69%,p≤0.06%,s≤0.07%,cr 2.31%,ni 0.76%,mo 11.39%,v 7.56,w 0.36%,nb 0.41和fe余量,芯部成分c1.79,si 1.21,mn 0.81,cr 0.23,ni 0.11,mo 0.11,v 0.03的标准成分后,将外层钢液温度加热到1650℃出钢,0.29mpa吹氩4.5min,温度降至1520℃后浇注,芯部钢水在1635℃出炉,在1512℃浇注;浇注完毕后56h开箱。开箱后粗加,在950℃进行保温33h后空冷,空冷至辊身520℃时装炉以9℃/h的冷却速度进行炉冷。炉冷结束进行粗加工,粗加辊身直径余量6mm,辊身长度余量17mm,利用高温加热炉在1085℃下加热65min,加热结束后在0.49mpa风压、0.41mpa水压下对辊身喷雾26min,在风压0.49mpa的参数下吹风55min,空冷至520℃装炉回火,550℃回火保温39h,两次回火后卸炉,进行后续加工至成品。
40.实施例6
41.实施例6为对照例,粗轧高速钢轧辊,电子显微图片如图2所示。
42.实施7
43.实施例7为对照例,精轧高速钢轧辊,电子显微图片如图3所示。
44.实施8
45.实施例8为对照例,高镍铬工作辊,电子显微图片如图4所示。
46.取实施例1~实施例7产品进行试样拉伸力学性能检测,性能检测执行国家标准gb/t 228.检测结果见表1。
47.表1实施例产品拉伸力学性能检测结果
[0048][0049][0050]
通过对比新材质粗轧工作辊辊身硬度、耐磨性及抗冲击性能,表明新性能成品机架工作辊硬度较粗轧高速钢略有上升,与精轧高速钢硬度水平相当,耐磨性高于粗轧高速钢,与精轧高速钢相当,抗冲击即抗事故性能高于粗轧高速钢及精轧高速钢,可适用成品机架甩尾等异常工况,相较于目前应用于精轧后段的高镍铬材质,高性能工作辊从辊身硬度、耐磨性及抗事故性能都明显高于常规高镍铬工作辊。
[0051]
经实验数据表明,高性能成品机架工作辊可实现工作层均匀磨损,具有优异抗事故性,辊役较目前高镍铬工作辊可大幅延长,大大延长在机周期,达到高镍铬工作辊在机周期的2倍及以上,可适应硅钢、薄板等特殊板材的轧制。
[0052]
通过对比本发明与粗轧高速钢、精轧前段高速钢和高镍铬的显微组织图,能够看出粗轧高速钢轧辊碳化物呈类似网状分布、精轧前段高速钢轧辊碳化物含量较多、高镍铬轧辊碳化物过于密集且粗大,上述轧辊存在:1)在轧制温度较高的硅钢时热裂纹较严重;2)使用过程中会影响了基体的均匀磨损;而本发明基体中碳化物在数量上更少,仅在晶界上析出少量颗粒状碳化物,可实现工作层均匀磨损,具有优异抗事故性,大幅延长在机周期,可适应硅钢、薄板等特殊板材的轧制,同时解决了使用过程中板面边部存在边浪的问题。
再多了解一些
本文用于创业者技术爱好者查询,仅供学习研究,如用于商业用途,请联系技术所有人。