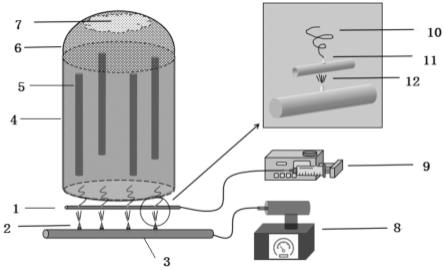
1.本发明属于溶液喷射纺丝技术领域,尤其涉及一种泰勒锥的形成及复合陶瓷纤维制备装置与方法。
背景技术:
2.溶液喷射纺丝是一种经济有效的纤维材料制备工艺,可以生产多种高效、低成本的纤维材料,包括陶瓷材料、金属材料和聚合物材料。其借助高速热气流将喷丝孔处流出的聚合物溶液或熔体直接喷射,在高速气体的剪切作用下形成泰勒锥射流。在射流运动过程中,溶剂进一步分裂挥发,最后,在收集器上形成、凝固并收集。
3.而泰勒锥最早是由泰勒(taylor)在静电纺丝的过程中提出,他推导计算得出液滴拉伸变形所形成的半锥角度为49.30
°
,所以被称为泰勒锥(taylor cone)。泰勒锥是静电纺丝射流的源头,泰勒锥的个数直接决定了射流的数目,并且泰勒锥排布的均匀性也直接决定了所制备纤维直径和纤维膜厚度的均匀性。
4.传统静电纺丝技术是利用毛细管针头挤出溶液或者熔体进行纺丝,效率较低,难以产业化。溶液喷射纺丝与静电纺丝相比是一种更为简单的方法,其成本更低,且以高速气流为驱动力纺丝效率更高。此外,作为纤维的样品可以被任何类型的收集器收集,如塑料或金属网或无纺布。并且与静电纺丝不同,溶液喷射纺丝既可以生产二维非晶薄膜,也可以产生三维立体纤维棉。
5.专利“一种中空陶瓷微纳米纤维及其制备方法和隔热保温材料”(申请号:cn202110149945.x)公开了一种采用溶液喷射纺丝制备中空陶瓷微纳米纤维的方法。该制备方法将高分子材料溶解于溶剂中,然后将陶瓷前驱体与高分子溶液混合均匀的纺丝前驱体溶液采用溶液喷射纺丝技术进行纺丝,制得复合纤维。再通过锻烧制得中空陶瓷微纳米纤维;专利“一种复合纤维过滤材料及其制备方法”(申请号:cn201810520375.9)涉及一种复合纤维过滤材料及其制备方法,其通过溶液喷射纺丝制备得到两种直径不同的复合纤维,对于烟尘具有良好的吸附和过滤作用;专利“一种交联型聚酞亚胺基微/纳米纤维膜及其制备方法”(申请号:cn201710358431.9)涉及一种交联型聚酞亚胺基微/纳米纤维膜及其制备方法,其先在非质子极性溶剂中采用“一步法”合成聚酞亚胺溶液,后通过溶液喷射纺丝技术得到聚酞亚胺微/纳米纤维膜,再将其浸入到含有吠喃基芳香型聚酞胺和交联剂的溶液中,经热压使纤维膜中的微/纳米纤维在交叉处产生化学交联制得交联型聚酞亚胺基微/纳米纤维膜;专利“一种制备两步法合成聚酞亚胺基微/纳米纤维的方法”(申请号:cn201510337445.3)涉及一种制备两步法合成聚酞亚胺基微/纳米纤维的方法。其鲜明的特征在于两步法合成聚酞亚胺,然后制备得到聚酞亚胺基微/纳米纤维。首先是采用原位聚合的方法合成制备聚酞亚胺前驱体,聚酞胺酸聚合物溶液,然后采用溶液喷射纺丝技术制备聚酞胺酸微/纳米纤维毡。最后将制备的聚酞胺酸微/纳米纤维毡采用热亚胺化的方法制备出聚酞亚胺微/纳米纤维毡。最后通过碳化实验,制备得到聚酞亚胺基微/纳米碳化纤维。专利“一种聚丙烯睛基纳米碳纤维的制备方法”(申请号:cn201210491215.9)涉及一种纳米碳
纤维的制备方法,特别涉及一种聚丙烯睛基纳米碳纤维的制备方法。其将聚丙烯睛溶解在溶剂中形成丝溶液,再将纺丝溶液供应到含有喷丝孔的喷丝模头,使其从喷丝孔挤出形成纺丝溶液细流。同时利用至少一股温度为20-80℃、速度高于溶液细流挤出速度500-3000倍的高速喷射气流以0-30
°
的喷射角喷吹溶液细流,使溶液细流细化并促进溶剂挥发形成聚丙烯睛纳米纤维;再将聚丙烯睛纳米纤维置于160-300℃的空气氛围中进行预氧化处理、900-1800℃的氮气氛围中进行碳化处理即可得到纳米碳纤维;专利“一种碳化硅先驱体复合纤维的制备方法”(申请号:cn201210491184.7)涉及一种碳化硅先驱体复合纤维的制备方法。将一种碳化硅先驱体聚合物溶解在至少一种有机溶剂中,制成质量分数为10-70%的均一油相溶液;再将一种水溶性成纤聚合物溶解在水中,加入表面活性剂,形成质量分数为1-50%的均一水相溶液;将所述的先驱体溶液和水溶性聚合物溶液以体积比1:10~1:1搅拌混合,得到稳定的水包油型(0/w)纺丝乳液后利用溶液喷射纺丝方法纺制先驱体纤维,可得到直径为50nm-50μm的先驱体复合纤维;再将先驱体纤维经过不熔化和高温锻烧处理后可得到碳化硅纤维。
6.上述的研究利用溶液喷射纺丝工艺实现了不同种材料的制备,但过程复杂,生产效率较低,不易实现规模产业化制备。本发明采用多孔注射的方式生产复合陶瓷纤维,生产效率高,工艺流程简单,操作简便,并且可通过改变相关参数有效地控制成丝直径、成丝厚度,可形成的均匀柔性较好的复合陶瓷纤维,易实现规模产业化制备。
技术实现要素:
7.为了解决背景技术的问题,本发明提供了一种泰勒锥的形成及复合陶瓷纤维的制备装置和方法。本发明采用多孔注射的方式生产复合陶瓷纤维,生产效率高,工艺流程简单,操作简便,并且可通过改变相关参数有效地控制成丝直径、成丝厚度,可形成的均匀柔性较好的复合陶瓷纤维,易实现规模产业化制备。
8.本发明采用的技术方案如下:
9.一、一种泰勒锥的形成及复合陶瓷纤维制备装置
10.包括液滴供给管、气流喷射管和纤维收集装置;液滴供给管水平放置,朝向纤维收集装置的一侧开有一排微孔;液滴供给管下方设置有平行布置的气流喷射管,气流喷射管朝向纤维收集装置的一侧设置有多个气流喷射喷嘴,多个气流喷射喷嘴在竖直方向上分别与液滴供给管上的各个微孔位置相对应;气流喷射喷嘴呈锥形状,顶部设置有朝向液滴供给管的喷气口,底部进气口与气流喷射管内部相通;液滴供给管上方设置有纤维收集装置,纤维收集装置包括加热管道、红外加热灯、网状收集罩,加热管道内侧面布置有多个红外加热灯,顶部设置有网状收集罩,底部与外界相通。
11.液滴供给管一端封闭,另一端与微量注射器相连,通过微量注射器向液滴供给管注入溶胶;气流喷射管一端封闭,另一端通过气体压缩机提供高速气流。
12.所述液滴供给管上的微孔直径为0.3~0.8mm;微孔直径不可过大,因为微孔的直径大小会直接决定形成纤维的直径大小。插入液滴供给管的微量注射器针头直径为0.8~1.2mm;注射针头的直径大小主要影响液滴的形成速度,较大的针头应采用较低的注射速度。
13.气流喷射喷嘴的喷气口直径为0.6~1.0mm;液滴供给管的微孔与气流喷射喷嘴喷
气口之间的间距为10~15cm。气流喷射喷嘴的喷气口朝液滴喷射高速气流,在气流的喷射作用下在液滴微孔处形成泰勒锥;该喷嘴位置与微孔相互对应并可形成高速气流对液滴进行喷射,在气流的喷射作用下可在液滴微孔处形成泰勒锥;通过热气流的作用拉长液滴形成的泰勒锥并促进其溶剂挥发,最后在纤维收集装置上进行收集。
14.所述加热管道长度为70~110cm;加热管道底部内径大于气流喷射喷嘴以及微孔中液滴的喷射范围;加热管道底部与气流喷射喷嘴保持10~25cm的间距。
15.所述网状收集罩采用铁制或铝制材料,网格孔隙大小为0.6~1.0cm;网状收集罩内表面铺设有厚度为0.5~1.5mm的棉花作为基底,利用软着陆的方法对纤维进行收集,以增强纤维的柔性。
16.二、采用上述装置制备复合陶瓷纤维的方法
17.包括以下步骤:
18.步骤1)将粘度为60~100pa/s的溶胶以0.001~0.008ml/s的缓慢速度通过微量注射器注入到液滴供给管内;
19.步骤2)在注射压力作用下,液滴从微孔渗出,流出的液滴在背对的气流喷射喷嘴的高速气流作用下经牵伸形成泰勒锥,在加热管道内热气流的作用下拉长液滴形成纤维状细流,由下至上喷射进入加热管道内;
20.步骤3)进入加热管道内的纤维状细流在向上的热气流作用下,向上挥发,之后在网状收集罩上凝固集聚形成陶瓷纤维;
21.步骤4)收集网状收集罩上集聚的陶瓷纤维,使用马弗炉进行烧结以去除有机组分获得复合陶瓷纤维。
22.所述步骤1)中,溶胶的制备方法如下:将0.5~1.0g的peo溶于10~15g的去离子水溶液后再加入8~15g的teos溶液,搅拌均匀后加入0.3~0.8g的al(no3)3·
9h2o颗粒或0.3~0.8g的氯化钙颗粒继续搅拌,搅拌时加入0.1~0.5ml的微量磷酸促进水解;
23.所述步骤1)中,溶胶粘度不可过大,否则将导致溶胶无法从微孔处顺利流出。
24.所述步骤1)中,注射压力仅需要保持微孔处形成液滴即可,不宜过大;注入速度不可过快,否则将导致微孔处形成较大液滴,进而影响后续气流喷射形成的陶瓷纤维直径大小,不利于纤维的制备。
25.所述步骤2)中,气流喷射喷嘴的气流喷射速度为80~150pa/s,喷射速度应保持在可以使液滴微孔处形成稳定的泰勒锥即可,不易过快,否则会导致形成的陶瓷纤维因集聚过快或溶剂没有挥发彻底而发生团聚从而降低纤维性能。
26.所述步骤2)中,喷射气流的喷射方向垂直于液滴供给管,且使网状收集罩位于喷射气流的正上方,这样更有利于形成泰勒锥和收集纤维。
27.所述步骤2)中,喷射过程中,气流需连续稳定,这样更有利于形成直径均匀,形态良好的纤维。
28.所述步骤3)中,加热管道内的温度为400~700℃。
29.所述步骤4)中,将陶瓷纤维放入马弗炉,以2~5℃/min的速率升温至450℃~800℃,在450℃~800℃的温度下保温1~2h后随炉降温,以去除纤维中所含有机组分。
30.所述步骤4)中,利用马弗炉进行高温烧结时需要将炉门拧紧,防止反应过程中空气进入发生氧化。
31.本发明的有益效果:
32.(1)通过具有一排微孔的液滴供给管进行供给,可实现多孔注射,极大地提高了成丝效率。
33.(2)采用多孔注射以及气流喷射的方式进行纺丝,生产效率高,工艺流程简单,操作简便,并且可通过改变相关参数有效地控制成丝直径、成丝厚度,可形成均匀柔性较好的复合陶瓷纤维,易实现规模产业化制备。
附图说明
34.图1所示为本发明的制备装置;
35.图2所示为本发明的制备流程;
36.图3所示为实施例1制备所得复合陶瓷纤维实物图;(a)复合陶瓷纤维平面展开图;(b)复合陶瓷纤维正面折叠图;(c)复合陶瓷纤维侧面折叠图;
37.图4所示为实施例1制备所得复合陶瓷纤维sem图。
38.图中:1液滴供给管,2气流喷射喷嘴,3气流喷射管,4加热管道,5红外加热灯,6网状收集罩,7陶瓷纤维,8气体压缩机,9微量注射器,10纤维细流,11泰勒锥,12高速气流。
具体实施方式
39.下面结合具体实施例,进一步阐述本发明。这些实施案例仅用于说明本发明而不用于限制本发明的范围。
40.本发明的实施例如下:
41.实施例1:
42.(1)如图1所示,制备装置采用微孔直径为0.4mm的液滴供给管及装有直径为0.8mm的较细针头微量注射器,配备喷气口直径约为0.6mm,气流喷射速度约为100pa/s的气流喷射喷嘴。在收集纤维时,采用400℃的加热板配有80cm的加热管道及0.6cm的网络孔隙收集板进行收集。并在收集板上铺垫一层厚度约为0.5mm的棉花作为基底,
43.(2)利用此装置制备复合陶瓷纤维的方法包括以下步骤:首先制备粘度为70pa/s的溶胶:将0.5g的peo溶于10g的去离子水溶液后再加入8g的teos溶液,搅拌均匀后加入0.3g的al(no3)3·
9h2o颗粒继续搅拌,搅拌时可加入0.1ml的微量磷酸促进水解,而后以0.2mg/s的流速流入液滴管;将喷出的复合陶瓷纤维放入马弗炉中以2℃/min的升温速率,在800℃的温度下保温1.5h后随炉降温,以去除纤维中所含有机组分。
44.所得复合陶瓷纤维实物图如图3所示。由图3可看出采用本发明的制备装置及方法制备所得的复合陶瓷纤维具有较好柔性,结构致密,纤维缠绕交联紧密。其显微结构如图4所示。由图4可看出复合陶瓷纤维微观分布均匀,交缠紧密,纤维长度较长,是良好的陶瓷纤维材料。
45.实施例2:
46.(1)制备装置采用微孔直径为0.6mm的液滴供给管及装有直径为0.8mm的较细针头微量注射器,配备喷气口直径约为0.8mm,气流喷射速度约为120pa/s的气流喷射喷嘴。在收集纤维时,采用600℃的加热板配有80cm的加热管道及0.6cm的网络孔隙收集板进行收集。并在收集板上铺垫一层厚度约为0.5mm的棉花作为基底,
47.(2)利用此装置制备复合陶瓷纤维的方法包括以下步骤:首先制备粘度为80pa/s的溶胶:将0.8g的peo溶于10g的去离子水溶液后再加入10g的teos溶液,搅拌均匀后加入0.5g的al(no3)3·
9h2o颗粒继续搅拌,搅拌时可加入0.5ml的微量磷酸促进水解,而后以0.2mg/s的流速流入液滴管;将喷出的复合陶瓷纤维放入马弗炉中以5℃/min的升温速率,在800℃的温度下保温1.5h后随炉降温,以去除纤维中所含有机组分。
48.实施例3:
49.(1)制备装置采用微孔直径为0.6mm的液滴供给管及装有直径为0.8mm的较细针头微量注射器,配备喷气口直径约为0.8mm,气流喷射速度约为140pa/s的气流喷射喷嘴。在收集纤维时,采用500℃的加热板配有80cm的加热管道及0.6cm的网络孔隙收集板进行收集。并在收集板上铺垫一层厚度约为0.5mm的棉花作为基底,
50.(2)利用此装置制备复合陶瓷纤维的方法包括以下步骤:首先制备粘度为0.08pa/s的溶胶:将0.6g的peo溶于10g的去离子水溶液后再加入10g的teos溶液,搅拌均匀后加入0.5g的al(no3)3·
9h2o颗粒继续搅拌,搅拌时可加入0.5ml的微量磷酸促进水解,而后以0.2mg/s的流速流入液滴管;将喷出的复合陶瓷纤维放入马弗炉中以5℃/min的升温速率,在600℃的温度下保温1.5h后随炉降温,以去除纤维中所含有机组分。
再多了解一些
本文用于创业者技术爱好者查询,仅供学习研究,如用于商业用途,请联系技术所有人。