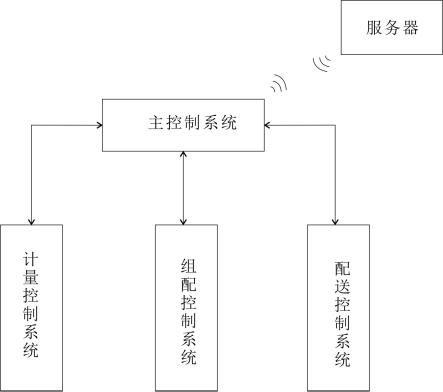
1.本发明涉及食品加工领域,具体讲是一种固态物料防错防呆配料系统及其配料方法。
背景技术:
2.复合调味料(如火锅底料)是由多种物料经过炒制而成,在炒制前,需要对不同种类的物料进行计量和组配,再将组配好的物料配送至炒锅;而传统的复合调味料生产中,计量、组配和配送是相互独立,没有相互关联和制约,容易出现物料的长时间呆滞停留或者计量跟不上后续的组配或配送,难以管控,降低效率;同时在计量时,多为人工称重,却没有实时对人工称重进行监控,容易出现多料或少料的计量错误问题;而这些由于控制的严格出现的计量错误或物料呆滞,在整个生产线加工中就容易被放大,从而导致物料的浪费或加工效率的低下,并且加工的质量不稳定。
技术实现要素:
3.因此,为了解决上述不足,本发明在此提供方便自动化控制的固态物料防错防呆配料系统,以及基于该系统的配料方法;本发明通过固态物料(如湿料、固体粉料、液态小料等)在计量、组配和配送过程中,各步骤的检查与匹配来判断物料的准确性,以达到防错防呆的目的。
4.具体的,一种固态物料防错防呆配料系统,包括主控制系统、服务器、计量控制系统、组配控制系统和配送控制系统,所述主控制系统实现任务的处理和传输;所述服务器通过无线网络与所述主控制系统连接,实现远程监控和控制;所述计量控制系统与所述主控制系统连接,实现固态物料的计量任务处理;所述组配控制系统与所述主控制系统连接,对计量好的物料进行组配任务处理;所述配送控制系统与所述主控制系统连接,对组配好的物料进行配送任务处理。
5.在该固态物料防错防呆配料系统中,所述计量控制系统包括计量控制器,计量输入模块,配料秤,计量显示模块和计量报警模块;所述计量控制器通过无线网络与所述主控制系统连接;所述计量输入模块具有识别单元并与所述计量控制器连接;所述配料秤与所述计量控制器连接,并配置有与计量控制器连接的车锁模块;所述计量显示模块与所述计量控制器连接;所述计量报警模块与所述计量控制器连接。
6.在该固态物料防错防呆配料系统中,所述组配控制系统包括组配控制器,托盘组,组配输入模块,组配显示模块,组配报警模块和品控确认模块;所述组配控制器通过无线网络与所述主控制系统连接;所述托盘组位于暂存区,由数个托盘组成,每个所述托盘均配置有与组配控制器
连接的扫描枪;所述组配输入模块位于组配区与所述组配控制器连接,实现对现场信息的输入;所述组配显示模块与所述组配控制器连接,对现场信息的显示;所述组配报警模块与所述组配控制器连接。
7.所述品控确认模块与所述组配控制器连接,用于现场品控人员确认组配物料。
8.在该固态物料防错防呆配料系统中,所述配送控制系统包括配送控制器,物料量确认模块,炒前扫描模块和配送显示模块;所述配送控制器通过无线网络与所述主控制系统连接;所述物料量确认模块与所述配送控制器连接,用于工作人员对暂存区物料量信息确认;所述炒前扫描模块与所述配送控制器连接,用于工作人员在炒制前对物料信息的确认;所述配送显示模块与所述配送控制器连接。
9.该固态物料防错防呆配料系统通过对计量工序、组配工序和配送工序各个环节进行控制和监控,提高各个工序之间的准确性和流畅度,提高整个配料工序的配料效率,同时还可以达到防错防呆的目的;并且能够计量各个环节的操作计量和数据,便于后台的统一监管和问题追溯。
10.本发明所述配料方法是基于所述固态物料防错防呆配料系统,包括如下步骤,步骤一、计量工序,根据物料子配方的要求计量物料;步骤二、组配工序,将计量好的物料组合到指定的托盘;步骤三、配送工序,通过托盘将组配好的物料运送至指定炒锅旁。
11.在该配料方法中,所述计量工序的具体步骤如下:配料员随机拿取物料桶,并放在物料车上;将物料车推到配料秤,通过车锁模块将配料秤与物料车锁在一起,并扫描绑定工单;配料员扫工牌,绑定工作任务;配料员根据计量显示模块显示的任务指标,称取多种物料;物料称取重量合格后,配料员通过计量输入模块进行确认,确认后将实测重量和配料员信息通过计量控制器输送至主控系统,并存入服务器,确认成功后车锁模块解锁,物料车可移动;若物料称取重量不合格,配料员在进行确认时,计量报警模块发出报警,提升加量或减量,同时车锁模块不会解锁,物料车不可移动;将完成计量后的物料小车推送至指定区域。
12.其中计量料小车与车锁模块配合,能够提高计量的精确度,只有物料计量精确后车锁模块才能够解锁,物料小车才能够移动。
13.在该配料方法中,所述组配工序的具体步骤如下:组配人员根据组配显示模块的任务指令,找到对应的位于物料车的物料桶;组配员将物料车推送至指定托盘前,用扫描枪扫描物料桶,亮起绿灯的,说明物料匹配成功,组配人员将物料桶转移到托盘上;红灯亮起的,说明物料匹配错误,组配人员需要重新确认任务并找到正确的托盘;若匹配错误而强行放置的,组配显示模块上的物料将
始终处于红色报警状态,并通过组配报警模块报警,品控人员应及时到现场处理;当一个托盘的物料组配完毕,其对应位置上的绿灯亮起,组配人员将其拖出;转移至现场品控区,由现场品控人员对物料种类、数量、重量进行审核;审核通过,品控在随身携带的品控确认模块上点击品控确认, 组配显示模块上对应显示;若审核不通过,则要求立即返回对应计量区域返工;现场审核通过的,组配人员将物料转移至物料暂存区,物料暂存区和炒锅位置一一对应,物料进仓的,由组配显示模块显示该仓有料,炒料人员在配送控制系统的配送显示模块上可见。
14.在该配料方法中,所述配送工序的具体步骤如下:炒制人员在最后一组物料下锅后,可以在物料量确认模块上查该炒锅对应暂存区是否有料;若有料,可以发起要料通知;若无料,可以提前在物料量确认模块上备料,以协调配料室插单准备;通过主控制器计算,接到优先要料通知的,配送人员到指定区域找到物料托盘,将其运送到指定炒锅旁;托盘离开后该指定区域处于空置状态,可以装下组物料;在炒锅旁,炒制人员需通过炒制扫描模块对配送过来的物料进行扫码确认,杜绝物料错拿;物料送达且经过确认后,配送人员需将空桶和托盘一并运回,送至对应的桶、托盘存放区域,完成一次生产闭环工序;配送人员有权限检查物料桶的洁净程度,有权决定该物料桶的清洗时间和频次。
15.所述计量工序、组配工序和配送工序均受控于所述主控制系统和服务器,工作人员可以通过主控制控制各个计量工序、组配工序和配送工序,同时也可通过服务器发送指令和监控各个工序。
16.通过上述的配料方法,能够从计量开始实现严格的监控和精度的控制,再将精确计量后的物料在指定区域组配,组配时,也通过严格的管控,能够防止物料误拿,并且在配送时进行指定配送,在炒制时也需要进行确认,提高物料配料时的精确性,同时炒制时,可以监控暂存区的物料情况,炒制物料时可以进行催促备料,以提高配送和炒制效率。
附图说明
17.图1是本发明所述固态物料防错防呆配料系统的系统模块示意图;图2是本发明所述计量控制系统的系统模块示意图;图3是本发明所述组配控制系统的系统模块示意图;图4是本发明所述配送控制系统的系统模块示意图;图5是本发明所述计量工序的流程示意图;图6是本发明所述组配工序的流程示意图;图7是本发明所述配送工序的流程示意图;图8是本发明所述配料方法中配料工序流程逻辑示意图;图9是本发明所述配料方法中组配工序流程逻辑示意图;图10是本发明所述配料方法中组配的品检逻辑示意图;
图11是本发明所述配料方法中配送工序程逻辑示意图。
具体实施方式
18.下面将结合附图1-图11对本发明进行详细说明,对本发明实施例中的技术方案进行清楚、完整地描述,显然,所描述的实施例仅仅是本发明一部分实施例,而不是全部的实施例。基于本发明中的实施例,本领域普通技术人员在没有做出创造性劳动前提下所获得的所有其他实施例,都属于本发明保护的范围。
19.实施例一:如图1所示,一种固态物料防错防呆配料系统,包括主控制系统(例如基于plc芯片的控制器),服务器(如电脑),计量控制系统,组配控制系统和配送控制系统;所述主控制系统实现任务的处理和传输;所述服务器通过无线网络与所述主控制系统连接,实现远程监控和控制;所述计量控制系统与所述主控制系统连接,实现固态物料的计量任务处理;所述组配控制系统与所述主控制系统连接,对计量好的物料进行组配任务处理;所述配送控制系统与所述主控制系统连接,对组配好的物料进行配送任务处理。
20.所述计量控制系统,组配控制系统和配送控制系统均受控于所述主控制系统和服务器,工作人员可以通过主控制控制各个计量工序、组配工序和配送工序,同时也可通过服务器发送指令和监控各个工序。
21.如图2所示,在该实施例中,所述计量控制系统包括计量控制器,计量输入模块,配料秤,计量显示模块以及计量报警模块;所述计量控制器通过无线网络与所述主控制系统连接;所述计量输入模块具有识别单元并与所述计量控制器连接;所述配料秤与所述计量控制器连接,并配置有与计量控制器连接的车锁模块;所述计量显示模块与所述计量控制器连接;所述计量报警模块与所述计量控制器连接。
22.配料员随机拿取物料桶,并放在物料车上;所述计量控制系统在实施时,配料员随机拿取物料桶,并放在物料车上;再将物料车推到配料秤,通过车锁模块将配料秤与物料车锁在一起,并扫描绑定工单;配料员再扫工牌,绑定工作任务;配料员根据计量显示模块显示的任务指标,称取多种物料(例如豆瓣酱20kg、大蒜10kg、生姜15kg);配料员先舀取豆瓣酱放入物料桶内,重量不足或超出时,显示屏亮红灯,无任何操作界面;当重量进入计量范围(19.8-20.5kg) 时,显示屏亮绿灯,屏幕上出现“确认”键;在物料称取重量合格后,配料员通过计量输入模块进行确认,确认后将实测重量和配料员信息通过计量控制器输送至主控系统,并存入服务器,确认成功后车锁模块解锁,物料车可移动;若物料称取重量不合格,配料员在进行确认时,计量报警模块发出报警,提升加量或减量,同时车锁模块不会解锁,物料车不可移动;将完成计量后的物料小车推送至指定区域。
23.如图3所示,在该实施例中,所述组配控制系统包括组配控制器,托盘组,组配输入模块,组配显示模块、组配报警模块和品控确认模块;所述组配控制器通过无线网络与所述主控制系统连接;
所述托盘组位于暂存区,由数个托盘组成(数个所述托盘的编号采用阿拉伯数字进行标记,例如托盘1、托盘2等),每个所述托盘均配置有与组配控制器连接的扫描枪(每个扫描枪的编号采用阿拉伯数字进行标记,例如扫描枪1、扫描枪2等);所述组配输入模块位于组配区与所述组配控制器连接,实现对现场信息的输入;所述组配显示模块与所述组配控制器连接,对现场信息的显示;所述组配报警模块与所述组配控制器连接。
24.所述品控确认模块与所述组配控制器连接,用于现场品控人员确认组配物料。
25.该组配控制系统在实施时,组配人员根据组配显示模块的任务指令,找到对应的位于物料车的物料桶;组配员将物料车推送至指定托盘前,用扫描枪扫描物料桶,亮起绿灯的,说明物料匹配成功,组配人员将物料桶转移到托盘上;红灯亮起的,说明物料匹配错误,组配人员需要重新确认任务并找到正确的托盘;若匹配错误而强行放置的,组配显示模块上的物料将始终处于红色报警状态,并通过组配报警模块报警,品控人员应及时到现场处理;当一个托盘的物料组配完毕,其对应位置上的绿灯亮起,组配人员将其拖出;转移至现场品控区,由现场品控人员对物料种类、数量、重量进行审核;审核通过,品控在随身携带的品控确认模块上点击品控确认, 组配显示模块上对应显示;若审核不通过,则要求立即返回对应计量区域返工;现场审核通过的,组配人员将物料转移至物料暂存区,物料暂存区和炒锅位置一一对应,物料进仓的,由组配显示模块显示该仓有料,炒料人员在配送控制系统的配送显示模块上可见。
26.如图4所示,在该实施例中,所述配送控制系统包括配送控制器,物料量确认模块,炒前扫描模块和配送显示模块;所述配送控制器通过无线网络与所述主控制系统连接;所述物料量确认模块与所述配送控制器连接,用于工作人员对暂存区物料量信息确认;所述炒前扫描模块与所述配送控制器连接,用于工作人员在炒制前对物料信息的确认;所述配送显示模块与所述配送控制器连接。
27.在该实施例中,所述计量控制器,组配控制器和配送控制器均为plc芯片的控制器。
28.所述配送控制系统在实施时,炒制人员在最后一组物料下锅后,可以在物料量确认模块上查该炒锅对应暂存区是否有料;若有料,可以发起要料通知;若无料,可以提前在物料量确认模块上备料,以协调配料室插单准备;通过主控制器计算,接到优先要料通知的,配送人员到指定区域找到物料托盘,将其运送到指定炒锅旁;托盘离开后该指定区域处于空置状态,可以装下组物料;在炒锅旁,炒制人员需通过炒制扫描模块对配送过来的物料进行扫码确认,杜绝物料错拿;物料送达且经过确认后,配送人员需将空桶和托盘一并运回,送至对应的桶、托盘存放区域,完成一次生产闭环工序;配送人员有权限检查物料桶的洁净程度,有权决定该物料桶的清洗时间和频次。
29.所述固态物料防错防呆配料系统通过对计量、组配和配送进行管控,每个步骤都严格按照标一定准执行,能够降低错误率,提高每个步骤的运行效率,降低物料呆滞的问
题,提高工作效率和降低物料的浪费。
30.实施例二:一种配料方法,该配料方法是基于实施例一所述固态物料防错防呆配料系统,包括如下步骤:s1、计量工序,根据物料子配方的要求计量物料;s2、组配工序,将计量好的物料组合到指定的托盘;s3、配送工序,通过托盘将组配好的物料运送至指定炒锅旁。
31.如图5所示,在该实施例中,所述步骤s1计量工序的具体步骤如下:s11、配料员随机拿取物料桶,并放在物料车上;s12、将物料车推到配料秤,通过车锁模块将配料秤与物料车锁在一起,并扫描绑定工单;s13、配料员扫工牌,绑定工作任务;s14、配料员根据计量显示模块显示的任务指标,称取多种物料;s15、物料称取重量合格后,配料员通过计量输入模块进行确认,确认后将实测重量和配料员信息通过计量控制器输送至主控系统,并存入服务器,确认成功后车锁模块解锁,物料车可移动;若物料称取重量不合格,配料员在进行确认时,计量报警模块发出报警,提升加量或减量,同时车锁模块不会解锁,物料车不可移动;s16、将完成计量后的物料小车推送至指定区域。
32.具体的,假设步骤s14中所述任务指标是称取豆瓣酱20kg、大蒜10kg和生姜15kg这三种物料时,计量工序的具体操作是,配料员随机拿取物料桶,并放在物料车上;再将物料车推到配料秤,通过配料秤的车锁模块将配料秤与物料车自动锁死锁在一起,并扫描绑定工单;配料员再扫工牌,绑定工作任务;配料员根据计量显示模块(即计量区现场位于智能配料秤上的屏幕)显示的任务指示,进行称取豆瓣酱;现场的配料员先舀取豆瓣酱放置于物料桶内,重量不足或超出时,显示屏亮红灯,无任何操作界面;当重量进入计量范围(19.8-20.5kg) 时,显示屏亮绿灯,屏幕上出现“确认”键,完成第一个物料的计量,实测重量上传至服务器,按该该方法称量大蒜和生姜,三个物料称量完毕,并确认成功后智能称锁死装置(即车锁模块)打开,配料员量物料小车推出,移动至配料室外。
33.如图8所示,计量工序的逻辑是;员工在识别单元刷卡进行称重,该识别单元可采用射频识别(rfid)技术,再推入小车开到配料秤,开设称重时具有两个识别条件(识别条件1是否识别rfid;识别条件2、小车进入后启动车锁模块(即气动阀)进行小车锁定);两个识别条件同时满足后,根据当前物料信息进行称重,否则重新配对识别;而在称重时也具有两个称重条件(称重条件1、物料重量是否达到配方标准,称重条件2、人工判断物料正确性),两个称重条件同时满足后则,称重完成,否则计量报警模块报警,并根据错误提示进行更改;在称重完成后,车锁模块解锁,工作人员拉出小车,与此同时,查看现场的计量显示模块(即称重区现场的大屏)显示是否还有任务,若没有任务则完成,若有任务则进行下轮任务称重。
34.如图6所示,在该实施例中,所述步骤s2组配工序的具体步骤如下:s21、组配人员根据组配显示模块(现场的大屏幕)的任务指令,找到对应的位于物料车的物料桶;
s22、组配员将物料车推送至指定托盘前,用扫描枪扫描物料桶,亮起绿灯的,说明物料匹配成功,组配人员将物料桶转移到托盘上;红灯亮起的,说明物料匹配错误,组配人员需要重新确认任务并找到正确的托盘;若匹配错误而强行放置的,组配显示模块上的物料将始终处于红色报警状态,并通过组配报警模块报警,品控人员应及时到现场处理;s23、当一个托盘的物料组配完毕,其对应位置上的绿灯亮起,组配人员将其拖出;s24、转移至现场品控区,由现场品控人员对物料种类、数量、重量进行审核;审核通过,品控在随身携带的品控确认模块(例如pad)上点击品控确认, 组配显示模块上对应显示;若审核不通过,则要求立即返回对应计量区域返工;s25、现场审核通过的,组配人员将物料转移至物料暂存区,物料暂存区和炒锅位置一一对应,物料进仓的,由组配显示模块显示该仓有料,炒料人员在配送控制系统的配送显示模块上可见。
35.如图9所示,组配工序的逻辑是:工作人员观察组配显示模块(机组配区现场的大屏)显示进行当前任务(配料区每完成一次称重任务后,组配区大屏都会像是该称重物料信息,组配人员根据指定信息进行组配任务。),若没有任务则实时观察,若有任务,则根据任务装运至指定位置,在放置到指定区域前,通过扫描枪扫描容器桶的标签,若扫描成功品控确认模块通过,则可以放入指定位置,反正则组配报警模块,工作人员根据错误提示进行更改;在放入指定位置后,工作人员查看现场的组配显示模块(机组配区现场的大屏)显示是否还有任务,若没有任务则完成,若有任务则进行下轮组配任务。
36.如图10所示,在上述步骤s24中由现场品控人员对物料种类、数量、重量进行审核的具体逻辑是,现场品控人员手持设备进行rfid扫描,若扫描不成功,则继续核对扫描,若扫描成功则通过扫描结果生成物料信息页面,再由人工做对比,并进行判断;若判断成功,则品检通过,工作人员再进行是否有任务的核对,若是没有任务,则完成审核,若不是没有任务,则继续审核;若判断不成功,则品检未通过,未通过品检时,出现是否当时处理逻辑,若是当是处理,则直接修改参数,填写备注,品检通过;若不是当时处理,则进入放置空闲区,工作人员发出重新下发(即在系统中点击重新下发)的任务(该过程更多是针对容易过保质期物品的常用流程),再释放容器桶,任务重新下发至计量工序,在计量完成后,运送至品检区,品控人员再通过手持设备进行rfid扫描,唤醒挂起任务,进行物料复检,并品检通过。
37.如图7所示,在该实施例中,所述步骤s3配送工序的具体步骤如下:s31、炒制人员在最后一组物料下锅后,可以在物料量确认模块(可以是现场的操作屏)上查该炒锅对应暂存区是否有料;s32、若有料,可以发起要料通知;若无料,可以提前在物料量确认模块上备料,以协调配料室插单准备;s33、通过主控制器计算,接到优先要料通知的,配送人员到指定区域找到物料托盘,将其运送到指定炒锅旁;托盘离开后该指定区域处于空置状态,可以装下组物料;s34、在炒锅旁,炒制人员需通过炒制扫描模块对配送过来的物料进行扫码确认,杜绝物料错拿;s35、物料送达且经过确认后,配送人员需将空桶和托盘一并运回,送至对应的桶、
托盘存放区域,完成一次生产闭环工序;s36、配送人员有权限检查物料桶的洁净程度,有权决定该物料桶的清洗时间和频次。
38.如图11所示,配送工序的逻辑是:工作人员通过炒前扫描模块(可采用手持式设备进行rfid扫描)进行判断,该判断具有两个判断条件(判断条件1、人工扫描任意物料桶上芯片,后台进行任务释放。判断条件2、释放:从组配区或品检区释放,重新绑定到存放区并改变炒锅物料信息。)若两个判断条件同时满足则释放物料信息,反正进行重新判断;若释放物料信息成功,则推入存放区,若不成功则检查为什么没有释放物料信息;在推入存放区后,工作人员查看现场的配送显示模块(即配送区现场的大屏)显示是否还有任务,若没有任务则完成,若有任务则进行下轮任务。
39.该实施例能够从计量开始实现严格的监控和精度的控制,再将精确计量后的物料在指定区域组配,组配时,也通过严格的管控,能够防止物料误拿,并且在配送时进行指定配送,在炒制时也需要进行确认,提高物料配料时的精确性,同时炒制时,可以监控暂存区的物料情况,炒制物料时可以进行催促备料,以提高配送和炒制效率;同时各个工序的操作人员的操作计量和各个数据都能够存储于服务器,以便于管理人员的统一监管和问题追溯。
40.对所公开的实施例的上述说明,使本领域专业技术人员能够实现或使用本发明。对这些实施例的多种修改对本领域的专业技术人员来说将是显而易见的,本文中所定义的一般原理可以在不脱离本发明的精神或范围的情况下,在其它实施例中实现。因此,本发明将不会被限制于本文所示的这些实施例,而是要符合与本文所公开的原理和新颖特点相一致的最宽的范围。
再多了解一些
本文用于企业家、创业者技术爱好者查询,结果仅供参考。