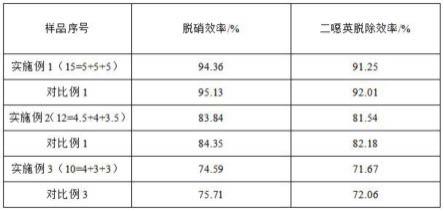
一种利用废scr脱硝催化剂制备脱硝脱二噁英催化剂的方法
技术领域
1.本发明涉及废旧催化剂资源回收技术领域,具体的是一种利用废scr脱硝催化剂制备脱硝脱二噁英催化剂的方法。
背景技术:
2.选择性催化还原(scr)技术被广泛应用于火力发电、钢铁冶炼、印染纺织、水泥化工、采矿制造、皮革鞣制、食品饮料等行业各种特大、大、中、小燃煤、燃油、燃气锅炉,以及熔炉,炉窑,烧结机类等烟气的氮氧化物治理。随着国家关于大气环境治理的“蓝天保卫战”的有效实施,针对工业烟气中氮氧化物的污染治理已经取得明显成效。但是随之而来的是大量退役的废旧scr脱硝催化剂。工业用scr脱硝催化剂一般以钒钨钛系催化剂(v2o
5-wo3/tio2)为主,其寿命通常为3年左右。退役的废scr脱硝催化剂作为固体危险废物需要进行无害化处置,否则随意处置会对环境造成严重危害。无害化处理后的催化剂可以再生继续使用或者作为新脱硝催化剂的制备的原料循环利用。
3.对于废scr脱硝催化剂,一般通过负压吹扫清灰、水洗、专用清洗液清洗等步骤进行无害化处理后再生使用作为新催化剂制备的原料。如中国专利cn202011230286.4公布了一种失活scr脱硝催化剂再生并用于制备脱硝脱二噁英催化剂的方法,对失活scr脱硝催化剂先进行清灰和清洗,然后使用清洗液深度清洁催化剂表面毒物,最后负载活性组分经干燥煅烧后制备得到脱硝脱二噁英催化剂。然而,这种方法制备出来的脱硝脱二噁英催化剂由于活性组分类似于分步浸渍于载体上,后负载上去的活性组分与原催化剂中的活性组分不能产生充分的相互作用,会导致催化剂的协同脱硝脱二噁英效果不理想。由于常规的清洗方法无法完全清除催化剂表面的有毒有害物种,因此通过上述处理工序得到的再生催化剂并不能作为全部的载体来使用,通常需要加入适量新鲜的钛白粉共同作为载体才能达到较好的催化效果。
4.基于目前市场上退役大量废scr脱硝催化剂的现状,以及当前废旧scr脱硝催化剂再生重复利用的大趋势,本发明立足催催化剂再生和制备技术,对回收回来的废钒钨钛系脱硝催化剂依次进行碱处理、酸处理和第三活性组分负载,最终制备得到适用于固废焚烧行业烟气协同脱硝脱二噁英催化剂。
技术实现要素:
5.为解决上述背景技术中提到的不足,本发明的目的在于提供一种利用废scr脱硝催化剂制备脱硝脱二噁英催化剂的方法,本发明使用依次负压清灰、水洗、清洗液清洗、碱液高温高压水热处理的方法充分去除废催化剂中的有毒有害物质,经过处理后的催化剂可以直接用于新催化剂的制备而无需添加新鲜二氧化钛载体;使用酸液高温高压水热处理的方法使原催化剂上的活性组分浸出到溶液中,与后续加入的钒、钨、铈的前驱体发生充分的相互作用,从而提高了催化剂的性能。
6.本发明的目的可以通过以下技术方案实现:
7.一种利用废scr脱硝催化剂制备脱硝脱二噁英催化剂的方法,包括以下几个步骤:
8.s1、废scr催化剂的清灰与清洗,废scr催化剂先采用负压清灰,然后依次采用清水清洗、专用清洗液清洗和清水二次冲洗,烘干后破碎磨粉备用;
9.s2、废scr催化剂的碱水热压处理,将s1得到的废scr催化剂粉浸没于一定浓度的碱性水溶液中,然后转移至密闭高压反应釜中,进行高温高压水热处理一定时间,自然降温后取出过滤、清洗至近中性;
10.s3、废scr催化剂的酸水热压处理,将s2得到的废scr催化剂浸没于一定浓度的酸性水溶液中,然后转移至密闭高压反应釜中,进行高温高压水热处理一段时间,自然降温后取出备用;
11.s4、活性组分前驱体的负载与活化,向s3得到的含有催化剂的固液混合物中加入一定量的偏钒酸铵、偏钨酸铵和铈盐前驱体,充分搅拌溶解后通过减压蒸馏除去过量的水,使混合物保持一定的水含量,再依次经过干燥和高温煅烧,得到协同脱硝脱二噁英催化剂。
12.进一步地,所述s1中的废scr脱硝催化剂为蜂窝式钒钨钛系脱硝催化剂,其主要组成为v2o
5-wo3/tio2,所述s1中的废scr脱硝催化剂清洗用的水用量为废催化剂质量的1~2倍,所述s1中的专用清洗液中主要成分的浓度为5~20%,清洗液的用量为废催化剂质量的1.5~3倍,所述s1中的废催化剂二次冲洗用的清水用量为废催化剂质量的12倍,所述s1中的烘干方式为热风鼓风烘干,烘干温度为90~110℃,烘干时间为1~2h,所述s1中的废催化剂破碎磨粉至200目以下。
13.进一步地,所述s2中的碱性水溶液为氢氧化钠水溶液、氢氧化钾水溶液、氨水中的一种,碱的浓度为5~15%,所述s2中的碱性水溶液用量为废催化剂质量的2~6倍,所述s2中的高温热压水处理的温度为120~200℃,处理时间为4~12h。
14.进一步地,所述s3中的酸性溶液为硫酸、盐酸、硝酸、乙酸、草酸水溶液中地一种,酸的浓度为0.1~1mol/l,所述s3中的酸性水溶液用量为废催化剂质量的2~4倍,所述s3中的高温热压水处理的温度为120~200℃,处理时间为4~12h。
15.进一步地,s4中的铈盐前驱体为六水合硝酸铈(ce(no3)3·
6h2o)、二氧化铈(ceo2)、氢氧化铈(ce(oh)4)、氢氧化亚铈(ce(oh)3)、乙酸铈(ce(c2h3o2)3·
nh2o)等中的一种,所述s4中按照全部活性组分(分别以v2o5、wo3、ceo2计)占催化剂总质量的10~15%加入偏钒酸铵、偏钨酸铵和铈盐前驱体,所述s4中加入偏钒酸铵、偏钨酸铵和铈盐前驱体后全部活性组分中v2o5、wo3、ceo2分别占催化剂总质量的4~5%、3~5%、3~5%,所述s4中减压蒸馏除水后混合物的含水量保持在30~50%,所述s4中干燥温度为90~130℃,干燥时间为5-10h,所述s4中煅烧温度为400~600℃,煅烧时间为5~10h。
16.本发明的有益效果:本发明使用依次负压清灰、水洗、清洗液清洗、碱液高温高压水热处理的方法充分去除废催化剂中的有毒有害物质,经过处理后的催化剂可以直接用于新催化剂的制备而无需添加新鲜二氧化钛载体;使用酸液高温高压水热处理的方法使原催化剂上的活性组分浸出到溶液中,与后续加入的钒、钨、铈的前驱体发生充分的相互作用,从而提高了催化剂的性能。
附图说明
17.下面结合附图对本发明作进一步的说明。
18.图1是协同脱硝脱二噁英催化剂性能测试结果。
具体实施方式
19.下面将结合本发明实施例中的附图,对本发明实施例中的技术方案进行清楚、完整地描述,显然,所描述的实施例仅仅是本发明一部分实施例,而不是全部的实施例。基于本发明中的实施例,本领域普通技术人员在没有作出创造性劳动前提下所获得的所有其它实施例,都属于本发明保护的范围。
20.实施例一
21.一种利用废scr脱硝催化剂制备脱硝脱二噁英催化剂的方法,切割500g经过负压清灰处理的块状蜂窝式废钒钨钛脱硝催化剂,用500g水进行冲洗后,用750g、质量浓度为15%的专用清洗液对催化剂进行深度清洗,清洗完成后继续用500g清水进行清洗,后续用90℃热风鼓风烘干2h,最后将催化剂破碎磨粉至全部过200目筛,将s1得到的催化剂粉末与1l、浓度为15%的氨水溶液充分混合后转移至1l高压反应釜中,在120℃搅拌水热处理12h,水热处理结束后自然冷却降至室温,进行过滤并洗涤至近中性,将s2得到的催化剂滤饼分散至2l、1mol/l的草酸溶液中,然后转移至密闭的高压反应釜中,在200℃搅拌水热处理8h,水热处理结束后自然冷却至室温,取出备用,对s3得到的催化剂进行v2o5、wo3、tio2含量的测定,根据测定的结果,按照总活性组分占比15%,v2o5、wo3、ceo2占比均为5%的比例,向s3的混合溶液中补加适量的偏钒酸铵、偏钨酸铵和六水合硝酸铈,充分搅拌溶解后通过减压蒸馏除去多余水分,使混合物水分保持在50%左右;然后在130℃干燥5h,500℃煅烧7.5h,得到协同脱硝脱二噁英催化剂。
22.实施例二
23.一种利用废scr脱硝催化剂制备脱硝脱二噁英催化剂的方法,切割500g经过负压清灰处理的块状蜂窝式废钒钨钛脱硝催化剂,用750g水进行冲洗后,用1500g、质量浓度为5%的专用清洗液对催化剂进行深度清洗,清洗完成后继续用1000g清水进行清洗,后续用110℃热风鼓风烘干1h,最后将催化剂破碎磨粉至全部过200目筛;将s1得到的催化剂粉末与3l、浓度为5%的氢氧化钠水溶液充分混合后转移至5l高压反应釜中,在200℃搅拌水热处理4h,水热处理结束后自然冷却降至室温,进行过滤并洗涤至近中性,将s2中得到的催化剂滤饼分散至1l、0.1mol/l的硫酸溶液中,然后转移至密闭的高压反应釜中,在120℃搅拌水热处理12h,水热处理结束后自然冷却至室温,取出备用,对s3得到的催化剂进行v2o5、wo3、tio2含量的测定,根据测定的结果,按照总活性组分占比12%,v2o5、wo3、ceo2占比分别为4.5%、4%、3.5%,向s3的混合溶液中补加适量的偏钒酸铵、偏钨酸铵和六水合硝酸铈,充分搅拌溶解后通过减压蒸馏除去多余水分,使混合物水分保持在30%左右;然后在100℃干燥7h,600℃煅烧5h,得到协同脱硝脱二噁英催化剂。
24.实施例三
25.一种利用废scr脱硝催化剂制备脱硝脱二噁英催化剂的方法,切割500g经过负压清灰处理的块状蜂窝式废钒钨钛脱硝催化剂,用1000g水进行冲洗后,用1000g、质量浓度为10%的专用清洗液对催化剂进行深度清洗,清洗完成后继续用750g清水进行清洗,后续用100℃热风鼓风烘干1.5h,最后将催化剂破碎磨粉至全部过200目筛,将s1得到的催化剂粉末与2l、浓度为10%的氢氧化钾水溶液充分混合后转移至5l高压反应釜中,在160℃搅拌水
热处理8h,水热处理结束后自然冷却降至室温,进行过滤并洗涤至近中性,将s2得到的催化剂滤饼分散至1.5l、0.5mol/l的盐酸溶液中,然后转移至密闭的高压反应釜中,在160℃搅拌水热处理4h,水热处理结束后自然冷却至室温,取出备用,对s3得到的催化剂进行v2o5、wo3、tio2含量的测定,根据测定的结果,按照总活性组分占比12.5%,v2o5、wo3、ceo2占比分别为4%、3%、3%,向s3的混合溶液中补加适量的偏钒酸铵、偏钨酸铵和六水合硝酸铈,充分搅拌溶解后通过减压蒸馏除去多余水分,使混合物水分保持在40%左右;然后在90℃干燥10h,400℃煅烧10h,得到协同脱硝脱二噁英催化。
26.分别按照实施例1、实施例2、实施例3的s4计算得到的催化剂配方,将偏钒酸铵、偏钨酸铵和铈前驱体与二氧化钛混合水溶液进行充分搅拌混合,然后通过减压蒸馏除水,再经过相同的干燥和煅烧过程,得到以新鲜钒、钨、钛、铈等化合物为原料制备的协同脱硝脱二噁英催化剂。
27.催化剂测试条件:测试温度为180℃,no通入浓度500ppm,nh3通入浓度500ppm、二噁英通入浓度5ng-teq/nm3,o2为7%(v/v),ar为平衡气,气体体积空速为6000h-1
。通过氮氧化物检测仪检测催化剂进出口no浓度计算脱硝效率,通过气相色谱定量分析催化剂进出口二噁英浓度计算二噁英脱除效率,分析结果如图1所示,从图1可以看出,采用本发明提供的方法以废旧钒钨钛系脱硝催化剂制备得到的协同脱硝脱二噁英催化剂较使用新鲜钒、钨、钛、铈等化合物为原材料制备得到的催化剂具备相近的协同脱硝脱二噁英性能。
28.工作原理:与现有废旧scr脱硝催化剂再生利用技术相比,本发明使用依次负压清灰、水洗、清洗液清洗、碱液高温高压水热处理的方法充分去除废催化剂中的有毒有害物质,经过处理后的催化剂可以直接用于新催化剂的制备而无需添加新鲜二氧化钛载体;使用酸液高温高压水热处理的方法使原催化剂上的活性组分浸出到溶液中,与后续加入的钒、钨、铈的前驱体发生充分的相互作用,从而提高了催化剂的性能。
29.在本说明书的描述中,参考术语“一个实施例”、“示例”、“具体示例”等的描述意指结合该实施例或示例描述的具体特征、结构、材料或者特点包含于本发明的至少一个实施例或示例中。在本说明书中,对上述术语的示意性表述不一定指的是相同的实施例或示例。而且,描述的具体特征、结构、材料或者特点可以在任何的一个或多个实施例或示例中以合适的方式结合。
30.以上显示和描述了本发明的基本原理、主要特征和本发明的优点。本行业的技术人员应该了解,本发明不受上述实施例的限制,上述实施例和说明书中描述的只是说明本发明的原理,在不脱离本发明精神和范围的前提下,本发明还会有各种变化和改进,这些变化和改进都落入要求保护的本发明范围内。
再多了解一些
本文用于企业家、创业者技术爱好者查询,结果仅供参考。