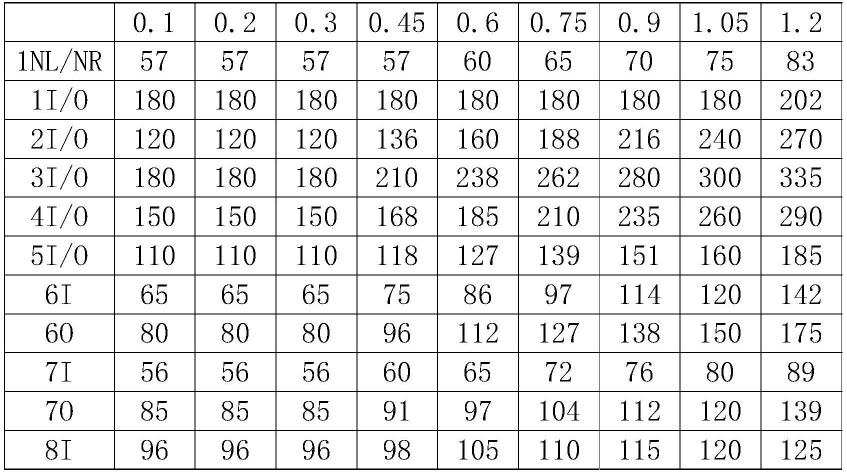
1.本发明属于耐候钢q450nqr1生产技术领域,尤其涉及一种高氮高强耐候钢板坯及其生产方法。
背景技术:
2.随着铁路的高速化与重载化,新一代铁路用耐候钢正朝着高强耐蚀方向发展。在耐候钢的研制与工程应用方面,国外已日趋成熟,建立了完善的耐候钢数据库,形成了体系化、标准化的研发模式。同国外相比,国内耐候钢研究起步比较晚,但发展较快。随着我国高速铁路技术的快速发展,铁路建设规模急剧提升,对耐候钢的需求逐渐增大,铁路部门提出货车提速且减重的目标。因此急需开发新型低成本、长寿命、高品质、高强度和耐蚀性好的铁路用钢。
3.我国对耐候钢的研发重点在于耐候钢的高强化。宝钢、攀钢和包钢等企业相
4.继在2002和2004年研制出了q450nqr1、yq450nqr1和yq450nbre等高强度耐候钢,均使屈服强度提升到450mpa级,铁道货车的运载能力也增加到约80吨。2010年,宝钢研发出了耐腐蚀性能比q450nqr1提高50%的s450ew高耐蚀性耐候钢板。
技术实现要素:
5.针对现有技术存在的问题,本发明提供了一种高氮高强耐候钢板坯及其生产方法。
6.本发明是这样实现的,一种高氮高强耐候钢板坯,其特征在于,耐候钢q450nqr1板坯,该板坯化学成分及百分含量:c:0.09-0.13、si:0.39~0.42、mn:1.30~1.50、p:《0.015、s:《0.010、cr:3.8-4.2、cu:0.42-0.46、v:0.10-0.14、ti:0.010~0.020、als:0.025-0.035、n:0.012-0.018,其他为fe和残留元素。
7.本发明还公开上述高氮高强耐候钢板坯的生产方法,其特征在于:包括如下步骤:
8.(1)原料:入炉铁水要求:si:0.40-0.95%、p:0-0.090%、s:0-0.030%;
9.(2)转炉冶炼:转炉吹炼过程底吹采用全程吹氮模式,实现转炉出钢时钢水中氮含量在80-90ppm;转炉出钢采取挡渣出钢,控制下渣量0-50mm,防止回磷;转炉在出钢过程中向钢包内加入合成渣料进行渣洗,同时进行钢包顶渣的改质,进一步脱硫去夹杂;转炉中需要控制cu、cr的含量,出钢目标要求c:≥0.12%、p:≤0.008%,出钢温度为1650-1680℃;
10.(3)lf精炼:钢水进站后吹氮,并根据钢水情况补充部分渣料,选择306v电压、20ka电流快速化渣,化好渣后,进行测温、取样;分期分批加入精炼渣料和还原剂,采用al粉、电石、碳化硅扩散脱氧,白渣精炼时间≥20分钟,白渣形成后取钢水样做全分析,调整成分目标值:c:0.05-0.08%、si:0.39~0.42%、mn:1.30~1.50%、p:《0.015%、s:《0.010%、cr:3.8-4.2%、cu:0.42-0.46%、v:0.10-0.14%、ti:0.010~0.020%、als:0.025-0.035%;以3m/s的速度喂入出钢喂入钒氮合金混合包芯线,钢包取样做氮含量保证钢水中氮含量在n:0.012-0.018%;
11.(4)连铸采用奥钢联铸机,该奥钢联铸机共计14个扇形段,其中,1-6段为弧形段,7-8段为矫直段,9-14段为水平段;采用奥钢联铸机生产250mm
××
2100mm断面铸坯,使用铝碳套管进行全程保护浇注,;连铸过程中钢水过热度控制在10-25℃范围内,拉速全程控制在0.90-1.00m/min,结晶器液面波动控制在
±
3mm以内;结晶器加入保护渣,保护渣碱度为1.00-1.25、熔点为1000-1150℃、1300℃时粘度为0.20-0.35pa
·
s,设定奥钢联铸机结晶器锥度为1.05%/m,宽面水量稳定在4100-4500l/min、窄面水量稳定在410-450l/min;钢液浇注时,结晶器振动方式采用非正弦振动,非正弦振动曲线的波形偏斜率10%,负滑脱时间tn=0.137-0.145s。
12.优选的,保护渣按重量百分比包含以下成分:cao:33-39%、sio2:25-31%、al2o3:2-4%、fe2o3:≤6%、mgo≤6%、na2o:7.7-10.7%、f-:8.0-11.0%、c:6-8%。
13.优选的,根据q450nqr1钢特点及拉速范围,奥钢联铸机二冷区采用弱冷,设计二冷曲线表比水量为0.5l/kg,提高1区、2区、3区水量,有利于增加铸坯坯壳厚度防止铸坯产生鼓肚;降低4区、5区水量保证铸坯角部温度大于900℃防止铸坯在矫直过程中产生角部裂纹。
14.优选的,奥钢联铸机二冷采用电磁搅拌:电流为380a、频率为3.0hz;采用动态轻压下的方式轻压下区间确定为:45%-95%、压下量为4.7mm,轻压下的分配系数为:压下区间系数0、0.3、0.7和1;对应的压下量系数为0、0.2、0.8和1。
15.本发明具有的优点和技术效果:
16.由于本发明采用上述技术方案,通过本发明中的方法,能够生产大截面q450nqr1板坯,该钢种化学成分控制严格,整批供货均匀,波动较小;采用结晶器非正弦振动和专用保护渣,铸坯表面振痕较浅;二冷动态配水技术保证铸坯在二冷区内的均匀冷却,减少了铸坯表面裂纹,鼓肚缺陷的发生;动态轻压下技术使铸坯凝固组织均匀致密,起到改善中心偏析和减少中心疏松的作用。
附图说明
17.图1是本发明实施例1提供的铸坯低倍形貌图;
18.图2是本发明实施例2提供的铸坯低倍形貌图;
19.图3是本发明实施例3提供的铸坯低倍形貌图。
具体实施方式
20.为了使本发明的目的、技术方案及优点更加清楚明白,以下结合实施例,对本发明进行进一步详细说明。应当理解,此处所描述的具体实施例仅仅用以解释本发明,并不用于限定本发明。
21.一种高氮高强耐候钢板坯,耐候钢q450nqr1板坯,该板坯化学成分及百分含量:c:0.09-0.13、si:0.39~0.42、mn:1.30~1.50、p:《0.015、s:《0.010、cr:3.8-4.2、cu:0.42-0.46、v:0.10-0.14、ti:0.010~0.020、als:0.025-0.035、n:0.012-0.018,其他为fe和残留元素。
22.以上高氮高强耐候钢板坯成分设计理论分析如下:
23.钒氮微合金化有其独特的优势:1)容易通过再结晶细化奥氏体晶粒、2)vn或富氮
的v(c,n)在奥氏体中析出,增加相变过程中和相变后铁素体的形核位置、3)加速冷却,增大相变时的形核驱动力等方法,钒氮微合金化钢同样可获得与铌微合金化钢相同的铁素体晶粒细化水平。钒氮微合金化钢具有较高的屈服强度和抗拉强度,同时具有较好的塑性和韧性。屈服强度和抗拉强度随着钒、氮含量的增加而增大,对于钒含量为0.10%的钢,每增加10ppm的氮,屈服强度和抗拉强度约提高12mpa和7mpa。经过研究分析钢中钒氮微合金化能够有效的提高钢的综合性能,同时也要注意钒氮含量的匹配,氮含量过高时,部分氮游离在铸坯中容易产生气泡等缺陷,当0.10%v-0.01%n配比时,钢的性能最为优秀。因此在对q450nqr1钢进行钒氮微合金化时,其v、n含量按照0.10%v-0.01%n比例进行设计,能够充分发挥钒细化晶粒、沉淀析出的作用。)
24.钒氮微合金化耐候钢增氮主要有两种方式:
25.(1)采取的是直接充氮的方式。也就是在钢还处于液相的时候,在钢包的上面部分或者是底部的位置这两个地方,将氮气直接通入到钢包中的钢液当中去。这种充氮的方式虽然操作简单,但是存在着一定的弊端,主要是由于氮气较为稳定,且难溶。因此在进行直接充氮的时候,实际溶解到钢液当中的氮量是很微量的,同时也具有较大的波动性,不能保证充氮量的准确性与稳定性。
26.(2)将氮以固态的方式加入,即首先将氮进行合金化,也就是一般所说的氮合金,常用的有氮化锰铁等,然后再将这种氮合金在冶炼时加入。然而,由于氮化锰铁中低的含氮量(仅为2%~5%)和高的mn含量(达65%~75%),这就会限制了应用范围。另外由于在冶炼时,为了实现钒与氮两种元素的交互协同作用,因此还需要向其中加入一定量的钒铁元素。这就给耐候钢的冶炼与合金量的增加带来了一定的技术障碍。本专利决定采用钒氮合金混合包芯线(芯粉氮含量在8~12%范围内,钒收得率为94~99%,氮收得85~90%)进行钢中氮含量最终控制。
27.本发明还公开一种上述高氮高强耐候钢板坯的生产方法,包括如下步骤:
28.(1)原料:入炉铁水要求:si:0.40-0.95%、p:0-0.090%、s:0-0.030%;
29.(2)转炉冶炼:转炉吹炼过程底吹采用全程吹氮模式,实现转炉出钢时钢水中氮含量在80-90ppm;转炉出钢采取挡渣出钢,控制下渣量0-50mm,防止回磷;转炉在出钢过程中向钢包内加入合成渣料进行渣洗,同时进行钢包顶渣的改质,进一步脱硫去夹杂;转炉中需要控制cu、cr的含量,出钢目标要求c:≥0.12%、p:≤0.008%,转炉温度为1650-1680℃;
30.(3)lf精炼:钢水进站后吹氮,并根据钢水情况补充部分渣料,选择选择306v电压、20ka电流快速化渣,化好渣后,进行测温、取样;分期分批加入精炼渣料和还原剂,采用al粉、电石、碳化硅扩散脱氧,白渣精炼时间≥20分钟,白渣形成后取钢水样做全分析,调整成分目标值:c:0.05-0.08%、si:0.39~0.42%、mn:1.30~1.50%、p:《0.015%、s:《0.010%、cr:3.8-4.2%、cu:0.42-0.46%、v:0.10-0.14%、ti:0.010~0.020%、als:0.025-0.035%;以3m/s的速度喂入出钢喂入钒氮合金混合包芯线,钢包取样做氮含量保证钢水中氮含量在n:0.012-0.018%;
31.(4)连铸采用奥钢联铸机,该奥钢联铸机共计14个扇形段,其中,1-6段为弧形段,7-8段为矫直段,9-14段为水平段;采用奥钢联铸机生产250mm
××
2100mm断面铸坯,使用铝碳套管行全程保护浇注,;连铸过程中钢水过热度控制在10-25℃范围内,拉速全程控制在0.90-1.00m/min,结晶器液面波动控制在
±
3mm以内;结晶器加入保护渣,保护渣碱度为
1.00-1.25、熔点为1000-1150℃、1300℃时粘度为0.20-0.35pa
·
s,设定结晶器锥度为1.05%/m,宽面水量稳定在4100-4500l/min、窄面水量稳定在410-450l/min;钢液浇注时,结晶器振动方式采用非正弦振动,非正弦振动曲线的波形偏斜率10%,负滑脱时间tn=0.137-0.145s。
32.进一步优选的,保护渣按重量百分比包含以下成分:cao:33-39%、sio2:25-31%、al2o3:2-4%、fe2o3:≤6%、mgo≤6%、na2o:7.7-10.7%、f-:8.0-11.0%、c:6-8%。
33.进一步优选的,根据q450nqr1钢特点及拉速范围,奥钢联铸机二冷区采用弱冷,设计二冷曲线表(参见表1)比水量为0.5l/kg,提高1区、2区、3区水量,有利于增加铸坯坯壳厚度防止铸坯产生鼓肚;降低4区、5区水量保证铸坯角部温度大于900℃防止铸坯在矫直过程中产生角部裂纹,上述1-5分区是根据奥钢联铸机分区方法进行分区,属于已知技术,再次不进行赘述。
34.表1:二冷比水量分布表
[0035] 0.10.20.30.450.60.750.91.051.21nl/nr5757575760657075831i/o1801801801801801801801802022i/o1201201201361601882162402703i/o1801801802102382622803003354i/o1501501501681852102352602905i/o1101101101181271391511601856i6565657586971141201426o808080961121271381501757i5656566065727680897o85858591971041121201398i969696981051101151201258o1631631631631631631631631759i60606060606060606010i606060606060606060总130913091309141915451696183719652210l/kg3.231.611.080.780.630.560.500.500.50
[0036]
进一步优选的,奥钢联铸机二冷采用电磁搅拌:电流为380a、频率为3.0hz;采用动态轻压下的方式;轻压下区间确定为:轻压下区间设定为45%-95%及压下量为4.7mm有利于降低该钢种铸坯中心偏析和缩孔的程度;轻压下的分配系数参见表2:
[0037]
表2为轻压下的分配系数表
[0038]
压下区间系数压下量系数000.30.20.70.811
[0039]
下面结合具体实施进行说明:
[0040]
实施例1
[0041]
(1)采用精料原则,入炉铁水:si:0.78%、p:0.090%、s:0.026%。
[0042]
(2)转炉冶炼:转炉吹炼过程底吹采用全程吹氮模式;转炉冶炼前期、中期造渣脱p;转炉冶炼中后期是钢水增氮的最佳时期,这时控制好氧枪枪位,防止喷溅;转炉出钢采取挡渣出钢,严格控制下渣量,下渣厚度38mm;出钢过程中向钢包内加入合成渣料进行渣洗,同时进行钢包顶渣的改质,进一步脱硫去夹杂;转炉出钢时c:0.08%、p:0.007%、n:0.0075%、出钢温度为1665℃;
[0043]
(3)lf精炼:钢水进站后吹氮,并根据钢水情况补充部分渣料,选择适当的电压、电流快速化渣,化好渣后,进行测温、取样;分期分批加入精炼渣料和还原剂、采用al粉、电石、碳化硅扩散脱氧,白渣精炼时间23分钟,白渣形成后取钢水样做全分析,调整成分目标值:c:0.11%、si:0.40%、mn:1.35%、p:0.012%、s:0.010%、cr:4.0%、cu:0.45%、v:0.12%、ti:0.015%、als:0.03%;根据钢水中氮含量,喂入钒氮合金混合包芯线100m,喂入后软吹氮时间10min,测定钢水中n:0.015%。连铸到站温度1550℃.
[0044]
(4)连铸生产250mm
×
2100mm断面铸坯,全程保护浇注,使用铝碳套管;连铸过程中钢水过热度为14℃,拉速稳定为0.95m/min,结晶器液面波动
±
3mm;结晶器加入保护渣,保护渣按重量百分比包含以下成分:cao:34%、sio2:26%、al2o3:3%、mgo:5.4%、na2o:8.2%、f-:8.5%、c:7%;结晶器锥度为1.05%/m,宽面水量4260l/min、窄面水量稳定在433l/min;结晶器振动方式采用非正弦振动,非正弦振动曲线的波形偏斜率10%,负滑脱时间tn=0.145s,二冷比水量分布如表1所示。
[0045]
表1:二冷比水量分布表
[0046][0047]
[0048]
采用二冷电磁搅拌技术:电流为380a、频率为3.0hz;采用动态轻压下技术,轻压下区间为:45%-95%、压下量为4.7mm,轻压下的分配系数如表2所示。
[0049]
表2为轻压下的分配系数
[0050]
压下区间系数压下量系数000.30.20.70.811
[0051]
铸坯检验:铸坯外形尺寸良好,铸坯表面无肉眼可见的缺陷;浇铸取低倍试样经过加工后对其截面进行酸浸,其铸坯检验情况如表3所示。
[0052]
中心偏析中心疏松中间裂纹角裂纹三角区裂纹蜂窝状气泡al2o3夹杂b0.50.500000
[0053]
铸坯低倍形貌如图1所示。
[0054]
实施例2
[0055]
(1)采用精料原则,入炉铁水:si:0.84%、p:0.085%、s:0.030%。
[0056]
(2)转炉冶炼:转炉吹炼过程底吹采用全程吹氮模式;转炉冶炼前期、中期造渣脱p;转炉冶炼中后期是钢水增氮的最佳时期,这时控制好氧枪枪位,防止喷溅;转炉出钢采取挡渣出钢,严格控制下渣量,下渣厚度42mm;出钢过程中向钢包内加入合成渣料进行渣洗,同时进行钢包顶渣的改质,进一步脱硫去夹杂;转炉出钢时c:0.07%、p:0.008%、n:0.0065%、出钢温度=1658℃;
[0057]
(3)lf精炼:钢水进站后吹氮,并根据钢水情况补充部分渣料,选择适当的电压、电流快速化渣,化好渣后,进行测温、取样;分期分批加入精炼渣料和还原剂、采用al粉、电石、碳化硅扩散脱氧,白渣精炼时间26分钟,白渣形成后取钢水样做全分析,调整成分目标值:c:0.10%、si:0.38%、mn:1.32%、p:0.013%、s:0.009%、cr:3.9%、cu:0.42%、v:0.12%、ti:0.014%、als:0.028%;根据钢水中氮含量,喂入钒氮合金混合包芯线120m,喂入后软吹氮时间10min,测定钢水中n:0.016%。连铸到站温度1548℃.
[0058]
(4)连铸生产250mm
×
2100mm断面铸坯,全程保护浇注,使用铝碳套管;连铸过程中钢水过热度为12℃,拉速稳定为1.00m/min,结晶器液面波动
±
3mm;结晶器加入保护渣,保护渣按重量百分比包含以下成分:cao:34%、sio2:26%、al2o3:3%、mgo:5.4%、na2o:8.2%、f-:8.5%、c:7%。结晶器锥度1.05%/m,宽面水量4250l/min、窄面水量稳定在430l/min;结晶器振动方式采用非正弦振动,非正弦振动曲线的波形偏斜率10%,负滑脱时间tn=0.145s,二冷比水量分布如表1所示。
[0059]
表1:二冷比水量分布表
[0060] 0.10.20.30.450.60.750.91.051.21nl/nr5757575760657075831i/o1801801801801801801801802022i/o1201201201361601882162402703i/o180180180210238262280300335
4i/o1501501501681852102352602905i/o1101101101181271391511601856i6565657586971141201426o808080961121271381501757i5656566065727680897o85858591971041121201398i969696981051101151201258o1631631631631631631631631759i60606060606060606010i606060606060606060总130913091309141915451696183719652210l/kg3.231.611.080.780.630.560.50.50.5
[0061]
采用二冷电磁搅拌技术:电流为380a、频率为3.0hz;采用动态轻压下技术,轻压下区间为:45%-95%、压下量为4.7mm,轻压下的分配系数如表2所示。
[0062]
表2为轻压下的分配系数表
[0063][0064][0065]
铸坯检验:铸坯外形尺寸良好,铸坯表面无肉眼可见的缺陷;浇铸取低倍试样经过加工后对其截面进行酸浸,其铸坯检验情况如表3所示。
[0066]
中心偏析中心疏松中间裂纹角裂纹三角区裂纹蜂窝状气泡al2o3夹杂b0.50.500000
[0067]
铸坯低倍形貌如图2所示。
[0068]
实施例3
[0069]
(1)采用精料原则,入炉铁水:si:0.76%、p:0.092%、s:0.023%。
[0070]
(2)转炉冶炼:转炉吹炼过程底吹采用全程吹氮模式;转炉冶炼前期、中期造渣脱p;转炉冶炼中后期是钢水增氮的最佳时期,这时控制好氧枪枪位,防止喷溅;转炉出钢采取挡渣出钢,严格控制下渣量,下渣厚度38mm;出钢过程中向钢包内加入合成渣料进行渣洗,同时进行钢包顶渣的改质,进一步脱硫去夹杂;转炉出钢时c:0.06%、p:0.009%、n:0.0065%、温度=1650℃;
[0071]
(3)lf精炼:钢水进站后吹氮,并根据钢水情况补充部分渣料,选择适当的电压、电流快速化渣,化好渣后,进行测温、取样;分期分批加入精炼渣料和还原剂、采用al粉、电石、碳化硅扩散脱氧,白渣精炼时间27分钟,白渣形成后取钢水样做全分析,调整成分目标值:c:0.12%、si:0.42%、mn:1.38%、p:0.013%、s:0.012%、cr:4.3%、cu:0.41%、v:0.10%、ti:0.013%、als:0.027%;根据钢水中氮含量,喂入钒氮合金混合包芯线150m,喂入后软吹
氮时间10min,测定钢水中n:0.017%。连铸到站温度1553℃.
[0072]
(4)连铸生产250mm
×
2100mm断面铸坯,全程保护浇注,使用铝碳套管;连铸过程中钢水过热度为18℃,拉速稳定为1.00m/min,结晶器液面波动
±
3mm;结晶器加入保护渣,保护渣按重量百分比包含以下成分:cao:34%、sio2:26%、al2o3:3%、mgo:5.4%、na2o:8.2%、f-:8.5%、c:7%。结晶器锥度1.05%/m,宽面水量4230l/min、窄面水量稳定在435l/min;结晶器振动方式采用非正弦振动,非正弦振动曲线的波形偏斜率10%,负滑脱时间tn=0.145s,二冷比水量分布如表1所示。
[0073][0074][0075]
采用二冷电磁搅拌技术:电流为380a、频率为3.0hz;采用动态轻压下技术,轻压下区间为:45%-95%、压下量为4.7mm,轻压下的分配系数如表2所示;
[0076]
表2为轻压下的分配系数表
[0077]
压下区间系数压下量系数000.30.20.70.811
[0078]
铸坯检验:铸坯外形尺寸良好,铸坯表面无肉眼可见的缺陷;浇铸取低倍试样经过加工后对其截面进行酸浸,其铸坯检验情况如表3所示。
[0079]
中心偏析中心疏松中间裂纹角裂纹三角区裂纹蜂窝状气泡al2o3夹杂b0.50.500000
[0080]
铸坯低倍形貌如图3所示。
[0081]
以上所述仅为本发明的较佳实施例而已,并不用以限制本发明,凡在本发明的精神和原则之内所作的任何修改、等同替换和改进等,均应包含在本发明的保护范围之内。
再多了解一些
本文用于企业家、创业者技术爱好者查询,结果仅供参考。