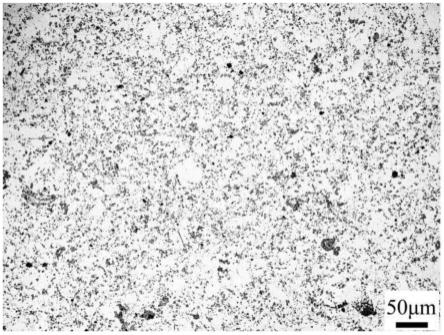
1.本发明属于轻质有色金属及合金的熔炼铸造技术领域,尤其涉及一种含金属硅化物的高刚度镁合金及其制备方法。
背景技术:
2.在能源严重紧缺和装备性能加速革新的大背景下,武器装备、航空航天、高速列车、新能源汽车等国民经济重点领域对轻量化需求迫切。镁合金作为目前最轻的金属结构材料,同时作为中国具有资源、科研和产业链优势的有色金属品种,对于中国装备轻量化具有重大意义。
[0003]“强度-模量不匹配”问题是目前制约镁合金高端应用的重要因素之一,镁合金研发长期偏重于强韧性提升,而我国的高刚度镁合金目前仍处于实验室研发阶段,尚未见工程化应用的报道。目前,镁合金的抗拉强度已接近500mpa,但弹性模量仅45gpa,显著低于铝合金(70gpa)和钛合金(110gpa),因此,镁合金承力结构件在高受力状态下容易发生显著弹性变形,从而影响服役效果。武器装备和航空航天是高刚度镁合金最重要的应用领域,航天器在高速飞行过程中承受强烈的气动加载和加热作用,为了控制飞行精度,航天器对弹性变形有严格限制,此时镁合金弹性模量低的弱点被暴露出来。针对类似应用场景,设计人员不得不放弃镁合金,而选用弹性模量更高的铝合金或钛合金,或者采用增大截面积的办法提升刚度,但这会导致减重效果大打折扣。因此,在实现高强度的基础上,开发高刚度镁合金具有重大现实意义,高刚度镁合金的弹性模量通常不低于50gpa。
[0004]
金属材料的弹性模量取决于材料本身的晶体学特性,其大小是晶体中原子结合力(化学键类型和键能)的反映,对组织变化不敏感,因而塑性变形和热处理无法有效提升刚度,合金化和复合化是提高金属材料弹性模量的最基本和最有效的途径。简而言之,根据胡克定律,δx=δf/e,e为弹性模量,可见,弹性变形量δx随外加载荷δf的增加而线性增加。通常情况下,普通镁合金无法承受太大的载荷,因而弹性变形有限,不足以影响服役效果,而针对能够承受巨大载荷的高强镁合金,例如超高声速或大过载的航天器舵翼面和舱体,必须考虑弹性变形过大的问题,因此,对提升弹性模量需求最迫切的是高强度或者超高强度镁合金。mg-re(rare earth,指稀土元素,gd、y、nd、ce是镁合金中最常用到的稀土元素)系是目前最重要的超高强镁合金体系,以mg-gd-y-zr系为典型代表。有研工程技术研究院有限公司开发的vw75超高强变形镁合金已批量用于我国某型航天器,该材料t5态抗拉强度大于450mpa,而弹性模量仅45gpa,目前只能通过增大截面积的办法提升刚度,但这也会降低减重效果。为了进一步拓展mg-re系超高强镁合金在武器装备和航空航天领域的应用范围,同时进一步提升减重效果,迫切需要开发高刚度高强度镁合金。
[0005]
复合化是现有技术中提升镁合金刚度的最有效方法,即:在镁合金基体中引入高模量增强相,同时,要求增强相与基体之间形成一个能够传递应力的冶金结合界面。按照增强相加入方式不同,镁基复合材料的制备方法分为两种:外加法和原位自生法。外加法是将预先制备好的增强体分散到镁合金熔体中,由于增强体表面易受污染,从而导致与基体之
间的润湿性差,界面结合力弱。所谓原位自生法,是指增强体是通过两种或多种元素或化合物之间在高温熔体中发生化学反应形成的,与外加法相比具有显著优势:(1)增强体在基体中具有热力学上的稳定性,有利于高温服役工况;(2)增强体与基体之间的界面干净,润湿性好,故界面结合强度高;(3)制备工艺相对简单,成本较低。因此,近年来,通过原位自生法制备镁基复合材料受到重视。吉林大学王慧远教授2004年博士论文报道:采用镁熔体内自蔓延高温合成(shs)反应法能成功制备原位tic和tib2颗粒增强镁基复合材料,但shs工艺涉及粉末冶金,技术难度大,成本较高。中南大学胡继龙2012年硕士论文报道了在mg-8%gd-4%y-1%nd-3%zn体系中添加3%si,利用高模量增强体mg2si(弹性模量e=120gpa)、gd5si3(e=168gpa)和ysi2(e=136gpa)将复合材料的弹性模量提升至57gpa,然而,铸锭直径仅35mm,挤压材直径仅8mm,增强相的沉降问题并不突出,处于实验室阶段。上海交通大学萧柱华2015年硕士论文报道了在mg-12%gd-4%y合金中添加1%si,将复合材料的弹性模量提升至51gpa,纳米压痕测得re-si化合物的弹性模量为148.8gpa,铸坯的最大厚度仅45mm,增强相的沉降问题并不严重,尚处于实验室阶段。重庆大学潘复生团队采用传统铸造和热挤压制备了mg-7gd-4y-2zn-0.5mn-0.8si合金(2019年),动态弹性模量达到49.3gpa,纳米压痕试验测得gd5si3的弹性模量87gpa,ysi的弹性模量为100gpa,该工作制备的铸锭直径为82mm,si以mg-5wt.%si中间合金形式加入,搅拌情况和沉降问题未在文章中提及,尚处于实验室阶段。可见,在mg-re系高强度合金中添加si后利用原位自生的re-si增强相提升弹性模量是目前最具应用潜力的方法。然而,现有技术目前处于实验室阶段,其产业化进程尚有许多“卡脖子”技术难点需要克服。
[0006]
re-si属于稀土金属与硅发生原位反应形成的硅化物,客观上说,re-si化合物的密度较高,抑制沉降的成本高,同时,该硅化物的弹性模量偏低(87~168gpa),因此,re-si并非最理想的高刚度镁合金增强相。事实上,金属硅化物是一个庞大的家族,硅化物中的原子结合力很强,其化学键既有金属键的特点又有很强的共价键性质,因此,金属硅化物的性质介于金属与陶瓷之间,许多金属硅化物具有较高的熔点和弹性模量,例如mosi2的弹性模量达到440gpa,wsi2的弹性模量达到468gpa,tisi2的弹性模量达到265gpa,它们也可以成为高刚度镁合金的增强相,但目前尚未见到采用这些金属硅化物提升镁合金刚度的报道。
[0007]
目前,高刚度高强度镁合金最具应用潜力的制备工艺是:在mg-re镁合金熔体中添加si,利用原位自生法在基体中形成re-si金属硅化物,该制备技术目前处于实验室阶段,同时,大量的其他金属硅化物尚未受到关注。
[0008]
对已报道的原位自生法制备技术进行总结,技术关键点为:(1)在同一个坩埚中进行合金化:纯镁熔化后,在750-760℃,利用不锈钢网包裹硅块没入镁液中,或者利用钟罩法将硅粉压入镁液中,搅拌直至硅完全熔化,取出不锈钢网或者钟罩,然后升温至770-780℃,添加gd、y、zn和zr等元素,搅拌1-5分钟;(2)搅拌结束后,为防止增强体粗化和沉降,将熔体迅速浇注到小型不锈钢模具中,快速凝固形成锭坯。
[0009]
上述技术虽然简单易行,但重要缺陷在于:(1)时效处理后,复合材料的强度相比于mg-re-zr合金大幅下降。mg-re-zr的高强度来源于时效处理过程中形成的高体积分数mg-re强化相β
′
相(mg7re),当在mg-re-zr合金中添加si后,re与si结合形成re-si化合物,因此β
′
时效强化相随之减少,因而时效强化效应大幅下降。以有研工程技术研究有限公司开发的vw75(mg-7%gd-5%y-1%nd-0.5%zr,重量百分比)为例,“挤压 t5时效处理”状态
的室温拉伸力学性能为:弹性模量45gpa,抗拉强度420mpa,屈服强度380mpa,延伸率2%;而添加2%si后,相同状态室温拉伸力学性能为:弹性模量49gpa,抗拉强度309mpa,屈服强度241mpa,延伸率5.0%;可见,添加si后,虽然弹性模量大幅提升,但强度明显下降;(2)由于re和si之间的结合力非常强,导致re-si增强相非常容易粗化,加之密度远大于镁熔体,因此很容易发生沉降,re-si增强相的沉降问题是目前制约原位自生高模量镁合金工程化的关键因素。航空航天和军事装备通常需要大尺寸的镁合金零件,而现有制备技术为了加快凝固速度和抑制增强相沉降,熔体量很小,无法满足工业化需求。随着熔体量增加,凝固时间相应增加,re-si相有充足的时间长大和粗化,增强相沉降更加显著。综上所述,相比于原位反应mg 2si
→
mg2si,xre ysi
→
re
x
siy在热力学上更容易发生,而现有制备技术无法有效抑制re与si的化学反应,也无法有效解决re-si相的粗化和沉降问题。因此,现有制备技术即无法保持基体合金原有的高强度,又无法满足工程化需求的大规格;(3)目前常用的re-si弹性模量偏低87~168gpa,同时密度偏大(~5g/cm3),防止沉降的成本高,其他金属硅化物尚未充分利用。
[0010]
基于上述问题,亟待提供一种新的镁合金材料制备方法以克服上述镁合金复合材料以及制备方法中存在的缺陷。
技术实现要素:
[0011]
为了解决上述问题,本发明提出了一种含金属硅化物的高刚度镁合金材料的制备方法,步骤如下:
[0012]
1)配料
[0013]
准备纯mg、纯si以及用于形成金属硅化物和/或改善镁合金基体性能的第三类金属原料;
[0014]
将一部分纯mg和全部纯si配制成si含量1-10wt%(质量百分数)的mg-si二元合金;
[0015]
将剩余纯mg和第三类金属原料配制mg-m多元合金原料;
[0016]
2)温度确定
[0017]
分析或计算确定所述步骤1)配比的mg-si二元合金的液相线温度和共晶温度以及mg-m多元合金的液相线温度;
[0018]
3)分别熔炼
[0019]
3-1)mg-si二元合金:将mg-si二元合金原料中,依次熔化mg原料和si原料,熔化完成后,将熔体控温至第i中间温度进行保温;
[0020]
第i中间温度等于mg-si二元合金的液相线温度或介于mg-si二元合金的液相线温度和共晶温度之间;
[0021]
3-2)mg-m多元合金:将mg-m多元合金原料中,依次熔化余量mg原料和剩余第三类金属原料,熔化完成后,将熔体控温至第ii中间温度保温;
[0022]
第ii中间温度不低于mg-m多元合金的液相线温度,二者温差不超过10℃;
[0023]
4)原位自生反应
[0024]
比较mg-si二元合金的共晶温度与mg-m多元合金的固相线温度,取高者作为参考对掺温度t1,实际对掺温度t不低于参考对掺温度t1,二者温差在10℃以内;
[0025]
将步骤3)中mg-si二元合金和mg-m多元合金熔体分别控温在实际对掺温度后,将两种熔体混合,保温搅拌或者降温至更低的温度进行半固态搅拌。
[0026]
5)凝固
[0027]
搅拌结束,成分分布均匀后立即对熔体进行冷却凝固,脱模后得到含金属硅化物的高刚度镁合金材料。
[0028]
在一些实施例中,所述第i中间温度与mg-si二元合金共晶温度的温差不超过2~10℃;优选的,不超过2~5℃;更优选的,在2℃以下;
[0029]
第ii中间温度与mg-m多元合金液相线温度的温差不超过2~10℃;优选的,不超过2~5℃;更优选的,在2℃以下。
[0030]
在一些实施例中,所述第三类金属包括碱土金属和/或过渡族金属。
[0031]
在一些实施例中,碱土金属包括ca、sr、ba任意一种或几种;
[0032]
过渡族金属包括sc、ti、zr、v、nb、cr、mo、w、mn、fe、co、ni、cu任意一种或几种;
[0033]
在一些实施例中,所述第三类金属中还包括稀土金属或其他金属;
[0034]
其中,稀土元素具体包括单一稀土y、混合稀土mm任意一种或两种;
[0035]
其他金属包括zn、al、li、sn其中一种或几种。
[0036]
在一些实施例中,所述步骤3)原料熔化过程中,在前添加原料完全熔融后分批次加入在后原料。
[0037]
在一些实施例中,所述分别熔炼和原位自生反应过程中,保持搅拌状态;具体的,采用半固态机械搅拌、电磁搅拌或超声处理。
[0038]
在一些实施例中,所述步骤2)温度确定方法依据mg-si二元相图、差热分析法、采用pandat软件或factsage软件进行的热力学计算。
[0039]
在一些实施例中,将得到的所述镁合金材料进行后处理:包括塑性变形和/或热处理。
[0040]
本发明还提供一种所述制备方法得到的含金属硅化物的高刚度镁合金材料。
[0041]
本发明的有益效果在于:
[0042]
1、本发明的设计原则大幅拓展了高刚度镁合金的种类,通过分别熔炼mg-si二元合金和mg-m多元合金的方式,然后在各自接近液相线温度或半固态温度进行搅拌混合,从而最大限度抑制了金属硅化物颗粒的粗化,从而能有效解决金属硅化物增强相的沉降问题,提升增强相的分布均匀性,并且适合大规格构件的制备。
[0043]
2、本发明提供的镁合金体系对于含re的镁合金,采用这种制备方法,能抑制re和si的结合,让re充分发挥固溶强化和析出强化作用,利用mg2si硅化物提升刚度,从而兼顾高强度和高刚度。
附图说明
[0044]
图1为实施例1制备的mg-10%gd-8%y-2%si-1%zn镁合金材料金相图;
[0045]
图2为对比例1制备得到的镁合金材料的金相图。
具体实施方式
[0046]
刚度低是镁合金的一个突出劣势,弹性模量仅约45gpa,铝合金的弹性模量约为
70gpa,钛合金的约为90gpa,钢铁的约为110gpa,由上述比较可知,镁合金受力后更容易发生弹性变形,虽然卸载后能得以恢复,但会造成尺寸稳定性较差,不能满足高受力服役条件下对尺寸稳定性的要求。
[0047]
金属硅化物由于具有共价键,键合强度非常高,对提升弹性模量(刚度)非常有利。
[0048]
基于上述优势和不足,本发明提供一种镁基复合材料以及制备方法。
[0049]
该镁基复合材料由基体相和高弹性模量增强相构成;基体相为高强高塑性的镁合金材料,增强相为金属硅化物;增强相由si和碱土、过渡或稀土金属在镁熔体中通过原位反应生成,属于原位自生型镁基复合材料。本发明高刚度镁基复合材料的制备方法采用原位自生法,根据实际服役条件进行成分设计,然后在不断搅拌的条件下,通过分别熔炼以及低温对掺的技术手段,制备得到兼具高强度和高弹性模量(高刚度)的镁基复合材料。
[0050]
原位自生法生产的增强相颗粒尺寸细小,并且界面干净无污染。
[0051]
将mg-si体系和mg-m体系分别熔炼并在低温下进行对掺混合,从而减小si与m的反应时间和反应温度,起到细化金属硅化物尺寸的作用,有效减轻沉降。其中当m为稀土元素re时,还能抑制re与si的结合,让re充分发挥固溶强化和析出强化作用,让mg2si发挥提升刚度的作用,实现高强度和高刚度的同时兼顾。
[0052]
具体方法步骤为:
[0053]
1)配料
[0054]
准备纯mg、纯si以及第三类金属原料;原料纯度为99.9%以上;
[0055]
将一部分纯mg和全部纯si配制成si含量1-10wt%的mg-si二元合金;
[0056]
将剩余纯mg和第三类金属原料配制成mg-m多元合金;
[0057]
配料过程中,根据实际服役要求,设计合理的镁合金基体成分,再选择合理的增强相种类和含量,两者确定好了之后,确定各种原材料投入量,包括mg、si、碱土金属、过渡金属、稀土金属以及其他金属。
[0058]
金属硅化物是通过化学反应在镁熔体中原位形成,化学反应的公式表示为:
[0059]
si 碱土、过渡、稀土金属
→
金属硅化物
[0060]
2)温度确定
[0061]
分析或计算确定所述步骤1)配比的mg-si二元合金的液相线温度和共晶温度以及mg-m多元合金的液相线温度;
[0062]
3)分别熔炼
[0063]
3-1)mg-si二元合金:将mg-si二元合金原料中,依次熔化mg原料和si原料,熔化完成后,将熔体控温至第i中间温度进行保温;第i中间温度等于mg-si二元合金的液相线温度或介于mg-si二元合金的液相线温度和共晶温度之间;
[0064]
具体过程为:将mg-si二元合金原料中,纯镁熔化后,升温至850~900℃,采用钟罩分批将si颗粒迅速没入熔体中,持续搅拌直至si颗粒完全熔化,上一批完全熔化后再加入下一批,所有si颗粒熔化后,将熔体控温至第i中间温度进行保温;保温和等待过程中持续搅拌;
[0065]
3-2)mg-m多元合金:将mg-m多元合金原料中,依次熔化余量mg原料和第三类金属原料,熔化完成后,将熔体控温至第ii中间温度保温;
[0066]
第ii中间温度不低于mg-m多元合金的液相线温度,二者温差不超过10℃;
[0067]
具体熔炼过程为:将mg-m多元合金原料中,将余量纯镁熔化后,升温至780~860℃添加剩余合金原料,完全熔化后,将熔体控温至第ii中间温度保温,整个过程保持搅拌;
[0068]
4)原位自生反应
[0069]
比较mg-si二元合金的共晶温度与mg-m多元合金的液相线温度,取高者作为参考对掺温度t1,实际对掺温度t不低于参考对掺温度t1,二者温差在10℃以内,即t=t1 (0~10℃);
[0070]
将步骤3)中mg-si二元合金和mg-m多元合金熔体分别控温在实际对掺温度后,将mg-si二元合金和mg-m多元合金混合,保温搅拌或者降温至更低的温度进行半固态搅拌,在保证一定流动性的前提下尽可能地降低熔体温度,能增大熔体粘度,缓解沉降,通过搅拌实现成分均匀和增强相分布均匀;
[0071]
5)凝固
[0072]
搅拌结束,成分分布均匀后立即对熔体进行冷却凝固,脱模后得到含金属硅化物的高刚度镁合金材料。
[0073]
在一些实施例中,第i中间温度与mg-si二元合金共晶温度的温差不超过2~10℃;优选的,不超过2~5℃;更优选的,在2℃以下;
[0074]
第ii中间温度与mg-m多元合金液相线温度的温差不超过2~10℃;优选的,不超过2~5℃;更优选的,在2℃以下。
[0075]
在一些实施例中,第三类金属包括碱土金属和/或过渡族金属。
[0076]
在一些实施例中,碱土金属包括ca、sr、ba任意一种或几种;
[0077]
过渡族金属包括sc、ti、zr、v、nb、cr、mo、w、mn、fe、co、ni、cu任意一种或几种;
[0078]
在一些实施例中,第三类金属中还包括稀土金属或其他金属;
[0079]
其中,稀土元素具体包括单一稀土y、混合稀土mm任意一种或两种;
[0080]
其他金属包括zn、al、li、sn其中一种或几种,其他金属与硅形成低共熔合金。
[0081]
在一些实施例中,步骤3)原料熔化过程中,在前添加原料完全熔融后分批次加入在后原料。
[0082]
在一些实施例中,分别熔炼和原位自生反应过程中,保持搅拌状态;具体的,采用半固态机械搅拌、电磁搅拌或超声处理。
[0083]
在一些实施例中,步骤2)温度确定方法依据mg-si二元相图、差热分析法、采用pandat软件或factsage软件进行的热力学计算。
[0084]
在一些实施例中,将得到的镁合金材料进行后处理:包括塑性变形和/或热处理。具体的包括,对镁合金材料的铸锭进行挤压,制备挤压材和/或进行t5人工时效处理。
[0085]
采用塑性变形生产挤压材、锻件和轧制材等产品,通过消除孔洞类缺陷、细化组织、破碎增强相,还能通过热处理或形变热处理方法,实现力学性能的进一步提升。
[0086]
本发明提供的镁合金及其制备方法能有效细化颗粒增强相,解决金属硅化物的沉降问题,并且适合大规格构件的制备。对于含re的镁合金,本发明能抑制re和si的结合,让re充分发挥固溶强化和析出强化作用,利用mg2si硅化物提升刚度,从而兼顾高强度和高刚度。上述组成成分能抑制re和si的结合,让re充分发挥固溶强化和析出强化作用,利用mg2si硅化物提升刚度,从而兼顾高强度和高刚度。
[0087]
本发明在镁合金基体中引入高弹性模量金属硅化物实现刚度的提升,与si形成金
属硅化物的金属包含稀土元素(含y和混合稀土mm)、碱土金属元素(ca、sr、ba)和过渡族金属元素(sc、ti、zr、v、nb、cr、mo、w、mn、fe、co、ni、cu)。
[0088]
优选的合金成分(质量百分数)为:(1)si含量0.1~25%;(2)第三类金属包括:从能够形成金属硅化物的金属中选择一种以上的金属,单个金属的含量0.1~25%,所选元素能一部分形成金属硅化物,另一部分起到强韧化作用或其他有益作用;以及其他具有强韧化或其他有益作用的合金元素(al、zn、li、sn),单个元素的含量0.1~25%;(3)mg为余量。
[0089]
以下结合具体实施例对本发明作进一步的详细说明:
[0090]
实施例1:
[0091]
根据实际服役情况制备mg-10%gd-8%y-2%si-1%zn(质量百分数)高弹性模量高强度镁合金材料铸锭,通过re-si金属硅化物实现模量提升,铸锭直径φ160mm,长度350mm,总投料约20kg。
[0092]
原材料包括纯mg、纯gd、纯y、纯zn块和纯si颗粒。gd的收得率100%,y的收得率90%,zn的收得率100%,si的收得率100%。
[0093]
纯gd 2kg;纯y1.7kg;纯zn 0.2kg;纯si 0.4kg;纯镁16kg。
[0094]
1)分两炉配料。
[0095]
1-1)第一炉为mg-si二元合金,成分为mg-5%si,si需要0.4kg,纯mg需要8kg,
[0096]
1-2)第二炉为不含si的mg-gd-y-zn合金,使用剩余原材料:纯镁为8kg,纯gd为2kg;纯y为1.7kg;zn为0.2kg,成分为mg-17%gd-13%y-1.6%zn,
[0097]
2)温度确定
[0098]
依据mg-si二元相图,mg-5%si的液相线温度约780℃;取mg-10wt.%si的共晶温度638℃。
[0099]
采用热力学软件pandat计算,得到该体系的液相线温度为560℃,固相线温度为545℃。
[0100]
3)分两炉熔炼。
[0101]
准备两套坩埚,两炉同时熔炼。
[0102]
3-1)第一炉熔炼mg-si二元合金。纯镁熔化后,升温至850~900℃,采用钟罩分批将si颗粒迅速没入熔体中,每批100g,持续搅拌直至si颗粒完全熔化,上一批完全熔化后再加入下一批,所有si颗粒熔化后,将熔体降温至640℃保温,降温和等待过程中持续搅拌;
[0103]
3-2)第二炉熔炼mg-gd-y-zn合金。纯镁熔化后,升温至780~860℃添加gd、y、zn,完全熔化后,将熔体降温至半固态温度550℃;
[0104]
将mg-si二元合金原料中,纯镁熔化后,升温至850~900℃,采用钟罩分批将si颗粒迅速没入熔体中,每批100g,持续搅拌直至si颗粒完全熔化,上一批完全熔化后再加入下一批,所有si颗粒熔化后,将熔体降温至640℃保温,降温和等待过程中持续搅拌;
[0105]
将mg-m多元合金原料中,将余量纯镁熔化后,升温至780~860℃添加剩余合金原料,完全熔化后,将熔体降温至半固态温度550℃。
[0106]
4)两炉熔体混合,进行原位自生反应
[0107]
比较mg-si二元合金的共晶温度与mg-gd-y-zn多元合金的固相线温度,取高者作为参考对掺温度t1=638℃,实际对掺温度为t=t1 5℃=643℃;
[0108]
将步骤3)中mg-si二元合金和mg-gd-y-zn多元合金熔体分别控温在实际对掺温度
643℃后,搅拌状态下,将mg-si二元合金加入mg-gd-y-zn多元合金中,继续搅拌保温5分钟。
[0109]
5)控制凝固
[0110]
搅拌结束后立即对熔体进行冷却凝固,脱模后得到高刚度高强度镁合金材料铸锭,如图1所示为制备的mg-10%gd-8%y-2%si-1%zn镁合金材料金相图,从图中可以看出,尺寸细小,分布均匀。
[0111]
后处理过程:塑性变形和热处理
[0112]
对上述实施例1得到的φ160mm镁合金材料铸锭进行挤压,制备φ25mm挤压材,对挤压材进行t5人工时效处理,热处理制度200℃-26h。
[0113]
对比例1
[0114]
针对mg-10%gd-8%y-2%si-1%zn高模量镁合金φ25mm挤压材,采用传统熔炼方法进行制备,先将纯mg熔化后,将原料si、gd、y、zn依次加入镁熔体,然后在稍高于液相线温度进行搅拌,之后凝固,得到镁合金材料铸锭,制备得到的镁合金材料的金相图示于图2。从图2中能看出,分布不均匀,并且尺寸明显超过实施例1。
[0115]
采用本发明实施例1方法相同的室温拉伸性能和动态弹性模量对比如表1所述:
[0116]
表1性能测试结果
[0117]
再多了解一些
本文用于企业家、创业者技术爱好者查询,结果仅供参考。