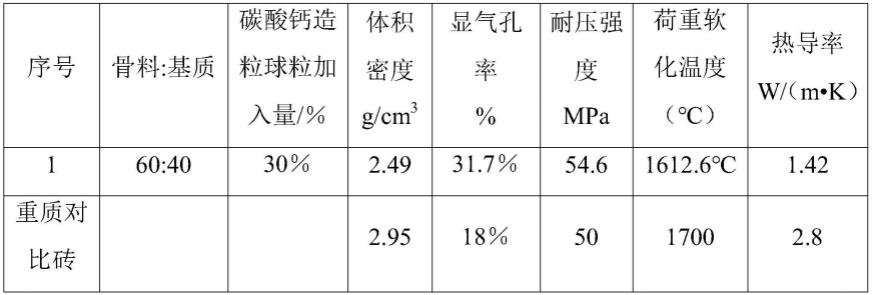
1.本发明属于耐火材料生产技术领域,特别涉及一种尖晶石-刚玉质轻量耐火材料及其制备方法。
背景技术:
2.随着全球节能减排进程的不断推进,水泥回转窑的节能减排势在必行。在水泥窑运行过程中,由于低的能源利用效率,大量热能通过窑壳以传导、辐射和对流的方式散失,据统计数据显示,通过回转窑窑壳的热损失可占水泥生成全过程能量损失的8~15%。研究人员发现,具有隔热性能的耐火材料越靠近回转窑的高温工作面,其隔热节能效果越好。因此,既具有重质耐火材料高强度、耐侵蚀等特点,又具有轻质耐火材料低导热特点的轻量耐火材料应运而生。作为水泥回转窑过渡带常用的耐火材料之一,镁铝尖晶石质耐火材料由于其优异的使用性能,近年来成为代替镁铬制品的最有竞争力的产品之一。同时我国丰富的菱镁矿和铝土矿资源,是发展镁铝系列制品良好的原料基础。关于尖晶石-刚玉质轻量耐火材料的制备目前主要通过引入多孔骨料如微孔刚玉。研究证实,轻量骨料的引入使耐火材料使用性能的降低尤其是抗侵蚀性能下降,降低了耐火材料的使用寿命。
技术实现要素:
3.为了克服上述现有技术的缺点,本发明的目的在于提供一种尖晶石-刚玉质轻量耐火材料及其制备方法,以引入具有核壳结构的碳酸钙造粒球粒利用高温反应时kirkendall扩散制备尖晶石-刚玉轻量耐火材料。
4.为了实现上述目的,本发明采用的技术方案是:
5.一种尖晶石-刚玉质轻量耐火材料的制备方法,包括如下步骤:
6.步骤一,将碳酸钙细粉通过造粒机造粒得到母粒,再将刚玉细粉包裹在母粒表面,干燥后得到以碳酸钙细粉作为球核,以刚玉细粉作为球壳的碳酸钙造粒球粒;
7.步骤二,选取尖晶石细粉和刚玉微粉作为反应原料,将反应原料磨细混匀,作为耐火材料配料中细粉部分;
8.步骤三,按照颗粒级配进行配料,骨料部分为不同质量比的尖晶石颗粒、镁砂颗粒和碳酸钙造粒球粒;
9.步骤四,将骨料部分混合,再加入mgcl2溶液混合,之后加入细粉部分混合,完成混合后进行睏料;
10.步骤五,将睏料后的物料成型、干燥,然后1600℃~1650℃烧结保温,保证碳酸钙造粒球粒发生kirkendall扩散,即得尖晶石-刚玉质轻量耐火材料。
11.在一个实施例中,所述步骤一,碳酸钙造粒球粒的粒径约为1mm
±
0.2mm左右,所述步骤二,将尖晶石细粉和刚玉微粉磨细至180目及以下,等质量混匀。
12.在一个实施例中,所述步骤一,刚玉细粉为电熔刚玉细粉;所述碳酸钙细粉为普通碳酸钙细粉,所述步骤三,所述尖晶石颗粒为电熔镁铝尖晶石颗粒;所述镁砂颗粒为烧结镁
砂颗粒。
13.在一个实施例中,所述步骤一,碳酸钙细粉与刚玉细粉按摩尔比1:10备料,包裹刚玉细粉时以稀释后的铝溶胶作为结合剂于造粒机中进行造粒包裹。
14.在一个实施例中,所述步骤三,尖晶石颗粒、镁砂颗粒和碳酸钙造粒球粒的质量比为5:(m1 m2),镁砂颗粒与碳酸钙颗粒比例变化,m1和m2分别表示镁砂颗粒和碳酸钙造粒球粒的质量;骨料部分与细粉部分的质量比为3:2。
15.在一个实施例中,所述步骤四,骨料部分混合2~5分钟,加入mgcl2溶液后混合3~5分钟,加入细粉部分后混合5~20分钟,混合时间总计20~30分钟,混合后置于密闭容器或塑料袋中睏料2小时至6小时。
16.在一个实施例中,所述步骤五,睏料后的物料采用半干法成型;之后自然晾晒半天至1天,然后在干燥设备中,采用阶段升温和保温方式进行干燥,最后在110℃保温6到24小时,再进行烧结保温。
17.在一个实施例中,所述步骤五,所述烧结保温在空气气氛下进行。
18.采用上述方法制备的尖晶石-刚玉轻量耐火材料,其体积密度为2.69~2.76g/cm3,强度为54.6~136.7mpa。
19.与现有技术相比,本发明的有益效果是:
20.(1)由于采用引入具有核壳结构的碳酸钙造粒球粒通过kirkendall效应实现材料的造孔和反应烧结,为此可以通过调整碳酸钙造粒球粒的加入量、球粒粒径和烧成温度,方便的调节制品的体积密度、气孔率和气孔分布及大小,从而调控耐火材料的保温隔热性能。
21.(2)由于采用引入具有核壳结构的碳酸钙造粒球粒通过kirkendall效应实现材料的造孔和反应烧结,高温下碳酸钙造粒球粒分解并由于kirkendall效应扩散造孔,实现了一步法制备尖晶石-刚玉轻量耐火材料,避免了轻量刚玉骨料的制备,实现了轻量化。
22.(3)以碳酸钙造粒球粒作为骨料,烧成后试样中球粒外壳由于反应生成具有板状结构的六铝酸钙,六铝酸钙的出现不仅提高了球粒内部闭气孔的体积,同时大大改善了耐火材料的抗热震稳定性。
23.(4)由于碳酸钙造粒球粒属于核壳结构,所以烧成后耐火材料中的孔洞均为闭气孔,更好的促进了尖晶石-刚玉质耐火材料的轻量化。
24.(5)可以根据不同使用场合选择使用刚玉细粉、氧化铝微粉或其他氧化铝质材料,产品性能可调控范围大。
具体实施方式
25.下面结合实施例详细说明本发明的实施方式。
26.本发明为一种尖晶石-刚玉轻量耐火材料的制备方法,具体包括下列步骤:
27.步骤一,选取碳酸钙细粉作为球核,刚玉细粉作为球壳,将碳酸钙细粉通过造粒机造粒得到母粒,再将刚玉细粉包裹在母粒表面形成球壳。得到碳酸钙造粒球粒,粒径约为1mm左右,经过干燥后可以作为骨料使用。
28.示例地,本步骤中刚玉细粉为电熔刚玉细粉或其他氧化铝质材料细粉,碳酸钙细粉为普通碳酸钙细粉,碳酸钙细粉与刚玉细粉的摩尔比为1:10。
29.步骤二,选取尖晶石细粉和刚玉微粉作为反应原料,将反应原料磨细混匀,作为耐
火材料配料中细粉部分。
30.示例地,本步骤中将反应原料磨细至180目及以下,尖晶石细粉和刚玉微粉的质量比50:50。
31.步骤三,将耐火材料原料按照一定的颗粒级配进行配料,骨料部分为不同质量比的尖晶石颗粒、镁砂颗粒和碳酸钙造粒球粒。
32.示例地,本发明实施例中,尖晶石颗粒为电熔镁铝尖晶石颗粒,镁砂颗粒为烧结镁砂颗粒。其中,尖晶石颗粒、镁砂颗粒和碳酸钙造粒球粒的质量比为5:(m1 m2),镁砂颗粒与碳酸钙颗粒比例变化,骨料部分与细粉部分的质量比可为60:40,细粉部分需共混至混合均匀。
33.步骤四,将骨料部分混合,再加入mgcl2溶液混合,之后加入细粉部分混合,完成混合后进行睏料。
34.示例地,本步骤中,先加入骨料混合2~5分钟,再加入mgcl2溶液搅拌3~5分钟后加入细粉部分。混合5~20分钟,在混合机中混合时间总计在20~30分钟。混合后置于密闭容器或塑料袋中睏料2小时至6小时。
35.步骤五,睏料后的物料成型。
36.示例地,本步骤中,采用半干法成型,压制成不同尺寸的圆柱型试样,不同尺寸试样采用不同成型压力成型。
37.步骤六,将成型好的试样干燥。
38.示例地,本步骤中,先自然晾晒半天至1天,然后在干燥设备中,采用阶段升温和保温方式进行干燥,最后在110℃保温6到24小时。
39.步骤七,烧结保温。
40.示例地,本步骤中,干燥后成型试样烧成在高温炉内进行,空气气氛下将炉体加热至1600℃~1650℃,到达该温度范围内即进行保温,保证试样内碳酸钙造粒球粒发生kirkendall扩散,成型试样通过反应烧结,获得具有体积密度为2.69~2.76g/cm3,强度为54.6~136.7mpa的尖晶石-刚玉轻量耐火材料。
41.本发明引入具有核壳结构的碳酸钙造粒球粒通过kirkendall效应制备轻量耐火材料,其基本原理是:在耐火材料配料时,在骨料中引入一部分具有核壳结构的碳酸钙造粒球粒,高温下碳酸钙造粒球粒的球核发生分解,分解产生的cao由于kirkendall效应的作用会不断向球壳中扩散并与球壳发生反应生成六铝酸钙。球核由于碳酸钙分解和kirkendall孔洞的聚集出现中孔,成功地于耐火材料内部产生闭气孔,降低了体积密度。球壳部分反应产生的六铝酸钙使试样具有良好的热震稳定性和高温荷载能力。另外,高温下镁砂颗粒于刚玉细粉发生反应生成原为尖晶石使试样具有较高的机械性能。
42.本发明制备的尖晶石-刚玉轻量耐火材料,具有体积密度较低,耐压强度较高的特点,可望在保证保温隔热性能的同时,具有较好的高温稳定性。
43.以下是发明人给出的本发明的最优实施例,本发明不限于这些实施例,经申请人的实验证明,在本发明给出的范围内,均能够制备尖晶石-刚玉轻量耐火材料。
44.实施例1:
45.将180目刚玉细粉、180目尖晶石细粉,按质量比50:50混合均匀。分别以1~3mm的尖晶石颗粒和1-0mm的镁砂颗粒和碳酸钙造粒球粒为粗颗粒和中颗粒。以刚玉细粉和尖晶
石细粉为基质部分配料,粗颗粒:中颗粒(镁砂 碳酸钙造粒球粒):细粉比例为30:30:40。以mgcl2溶液作为结合剂,加入量占配料总重量的5%,配料经充分混合后,置于密闭容器或塑料袋中睏料2小时后在液压机上成型,成型压力150mpa,将压制成型的试样自然晾晒半天至1天,然后在干燥设备中,采用阶段升温和保温方式进行干燥,最后在110℃保温12小时。干燥后成型试样在高温炉中烧成,空气气氛下,加热至1600℃时开始保温,保温4小时,得到尖晶石-刚玉轻量耐火材料。性能见表1。
46.表1:实施例1尖晶石-刚玉轻量耐火材料的性能
[0047][0048]
实施例2:
[0049]
将180目刚玉细粉、180目尖晶石细粉,按质量比50:50混合均匀。分别以1~3mm的尖晶石颗粒和1-0mm的镁砂颗粒和碳酸钙造粒球粒为粗颗粒和中颗粒。以刚玉细粉和尖晶石细粉为基质部分配料,粗颗粒:中颗粒(镁砂 碳酸钙造粒球粒):细粉比例为30:30:40。以mgcl2溶液作为结合剂,加入量占配料总重量的5%,配料经充分混合后,置于密闭容器或塑料袋中睏料2小时后在液压机上成型,成型压力150mpa,将压制成型的试样自然晾晒半天至1天,然后在干燥设备中,采用阶段升温和保温方式进行干燥,最后在110℃保温12小时。干燥后成型试样在高温炉中烧成,空气气氛下,加热至1650℃时开始保温,保温4小时,得到尖晶石-刚玉轻量耐火材料。性能见表2。
[0050]
表2:实施例2尖晶石-刚玉轻量耐火材料的性能
[0051][0052]
实施例3:
[0053]
将180目刚玉细粉、180目尖晶石细粉,按质量比50:50混合均匀。分别以1~3mm的尖晶石颗粒和1-0mm的镁砂颗粒和碳酸钙造粒球粒为粗颗粒和中颗粒。以刚玉细粉和尖晶石细粉为基质部分配料,粗颗粒:中颗粒(镁砂 碳酸钙造粒球粒):细粉比例为30:30:40。以
mgcl2溶液作为结合剂,加入量占配料总重量的5%,配料经充分混合后,置于密闭容器或塑料袋中睏料2小时后在液压机上成型,成型压力150mpa,将压制成型的试样自然晾晒半天至1天,然后在干燥设备中,采用阶段升温和保温方式进行干燥,最后在110℃保温12小时。干燥后成型试样在高温炉中烧成,空气气氛下,加热至1700℃时开始保温,保温4小时,得到尖晶石-刚玉轻量耐火材料。性能见表3。
[0054]
表3:实施例3尖晶石-刚玉轻量耐火材料的性能
[0055][0056]
实施例4:
[0057]
将180目刚玉细粉、180目尖晶石细粉,按质量比50:50混合均匀。分别以1~3mm的尖晶石颗粒和1-0mm的镁砂颗粒和碳酸钙造粒球粒为粗颗粒和中颗粒。以刚玉细粉和尖晶石细粉为基质部分配料,粗颗粒:中颗粒(镁砂 碳酸钙造粒球粒):细粉比例为30:30(10 20):40。以mgcl2溶液作为结合剂,加入量占配料总重量的5%,配料经充分混合后,置于密闭容器或塑料袋中睏料2小时后在液压机上成型,成型压力150mpa,将压制成型的试样自然晾晒半天至1天,然后在干燥设备中,采用阶段升温和保温方式进行干燥,最后在110℃保温12小时。干燥后成型试样在高温炉中烧成,空气气氛下,加热至1650℃时开始保温,保温4小时,得到尖晶石-刚玉轻量耐火材料。性能见表4。
[0058]
表4:实施例4尖晶石-刚玉轻量耐火材料的性能
[0059][0060]
综上,本发明制备的该尖晶石-刚玉轻量耐火材料在保持低热导率的情况下,在材料内部形成闭孔,实现了轻量化,并在保证使用性能的同时,提高了材料的保温隔热能力。通过调整骨料比例,可制备出保温隔热性能好、体积密度可调,耐压强度和荷重软化温度较高的耐火材料。
再多了解一些
本文用于企业家、创业者技术爱好者查询,结果仅供参考。