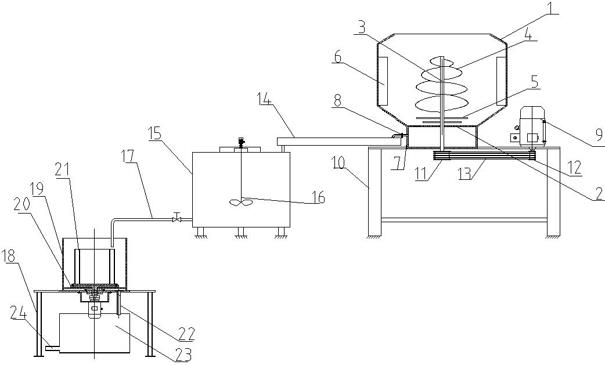
1.本发明涉及陶瓷纤维管的制备技术领域,尤其涉及一种陶瓷纤维管的湿法制备工艺。
背景技术:
2.现有无机纤维陶瓷管的制备流程为打浆-真空成型-烘干。公开号为cn113134893a的中国专利公开了一种高温烟气净化陶瓷纤维滤管的制备方法,将添加剂与陶瓷纤维搅拌混合得到浆料,浆料注入抽滤磨具中进行真空抽滤,预成型后湿脱模得到陶瓷纤维坯体,干燥固化得到陶瓷纤维滤管。该方法中采用真空抽滤方式进行坯体成型,成型后湿态产品含水率高,湿强度低,烘干时间长,导致生产效率低、生产成本高。
技术实现要素:
3.为了解决上述技术问题,本发明提供了一种陶瓷纤维管的湿法制备工艺及制备系统,产品湿强度大,产品湿态含水率低,可以大幅度提高生产效率。
4.为实现此技术目的,本发明工艺采用如下方案:陶瓷纤维管的湿法制备工艺,按如下步骤进行:s1、水力制浆:将陶瓷纤维棉及总水量30%~60%的水,加入到水力制浆桶内,通过水力制浆桶打散陶瓷棉散棉,得到陶瓷纤维棉初级浆液;s2、加胶搅拌:把硅溶胶、剩余水按比例加入到陶瓷纤维棉初级浆液中混合搅拌制浆,得到浆料,并存放在缓冲箱中,缓冲箱保持低速搅拌;s3、离心成型:启动离心成型机,使模具整体低速缓慢旋转,同时通过注浆管将缓冲箱中的浆料连续注入模具型腔中,直至模具型腔充满并完整成型;s4、离心脱水:成型后停止注浆,并提高离心机转速,进行离心脱水,得到陶瓷纤维管坯体;s5、烘干:将陶瓷纤维管坯由模具上脱出分离,脱模后的陶瓷纤维管坯体置于烘干炉内烘干,得到陶瓷纤维管。
5.进一步地,陶瓷纤维棉、硅溶胶和总水量的质量比为1:0.3:300。
6.进一步地,硅溶胶为碱性硅溶胶。
7.进一步地,s2中加入添加剂,添加剂与陶瓷纤维棉的质量比为0.2:1。
8.进一步地,添加剂为淀粉或纤维素。
9.进一步地,s2中缓冲箱的搅拌为20r/min~30r/min。
10.进一步地,s3注浆时模具转速为10r/min~50r/min,s4成型后脱水时模具转速为300r/min~500r/min。
11.进一步地,s3注浆时,浆料流量是0.3m
³
/min~2m
³
/min。
12.进一步地,烘干炉为微波烘干炉,烘干温度为110℃~120℃,烘干时间1h~2h。
13.与现有技术相比,本发明工艺的有益效果在于:本方法将陶瓷纤维棉、硅溶胶和水
搅拌混合制成浆液,浆液注入低速旋转的离心成型机中,直到模具型腔充满浆液并完整成型,成型后停止注浆,提高离心成型机的旋转速度,实现离心脱水,注浆与脱水时模具转速不同,保证产品成型质量好的同时降低了坯体的含水率,缩短了成型时间和烘干时间,提高了生产效率,降低了生产成本。
附图说明
14.图1为本发明实施例提供的陶瓷纤维管的湿法制备系统的结构示意图;图2为本发明实施例提供的水力制浆桶的结构示意图;图3为本发明实施例提供的水力制浆桶的俯视结构示意图;图4为本发明实施例提供的流槽的剖面图;图5为本发明实施例提供的离心成型机的结构示意图;图中标记为:1、桶体;2、筛网;3、旋转轴;4、螺旋叶片;5、转刀;6、扰流板;7、中间箱;8、出浆管;9、驱动电机;10、支架;11、第一皮带轮;12、第二皮带轮;13、传动皮带;14、流槽;15、缓冲箱;16、搅拌桨叶;17、注浆管;18、机架;19、护罩;20、模具安装盘;21、成型模具;22、回水管;23、集水箱;24、排水管;25、挡板。
具体实施方式
15.为充分了解本发明之目的、特征及功效,借由下述具体的实施方式,对本发明做详细说明,但本发明并不仅仅限于此。
16.请参阅图1,本发明提供的一种陶瓷纤维管的湿法制备系统,由水力制浆桶、流槽14、缓冲箱15、注浆管17和离心成型机等组成。
17.如图2和图3所示,水力制浆桶由桶体1、碎棉搅拌机构、筛网2、中间箱7、驱动电机9、第一皮带轮11、第二皮带轮12、传动皮带13和支架10等组成,桶体1的上端为敞口结构,桶体1的底面固定有筛网2,起到过滤浆液的作用。筛网2下方的桶体1与中间箱7连接,中间箱7侧壁连接有出浆管8。中间箱7的下端固定在支架10上。
18.支架10上还装有驱动电机9,驱动电机9的输出轴穿过支架10与第二皮带轮12键链接,第二皮带轮12通过传动皮带13与第一皮带轮11连接,第一皮带轮11与碎棉搅拌机构连接。
19.碎棉搅拌机构由螺旋叶片4、转刀5和旋转轴3组成,旋转轴3一端与第一皮带轮11键链接,旋转轴3的另一端穿过支架10、中间箱7和筛网2延伸至桶体1中上部,位于桶体1内的旋转轴3侧壁由上至下固定有螺旋叶片4,螺旋叶片4下方的旋转轴3侧壁环向均布有若干个转刀5,转刀5位于筛网2的上侧。鉴于浆液中含有陶瓷纤维棉容易发生缠绕,因此选用螺旋叶片4搅拌效果更好,螺旋叶片转动的同时,转刀5将底部浆液中颗粒物进一步打碎,保证浆液浓度均匀。桶体1的内壁环向均布有若干个扰流板6,以便与螺旋叶片4形成逆向水流,扰流板6为长条板结构。
20.如图4所示,流槽14为上端敞口的长方体槽结构,长方体槽的内侧槽壁固定有对称设置的竖直插槽,竖直插槽中插装有挡板25。挡板25为多级挡板,长方体槽上插装有多块挡板,沿着浆液流动方向,挡板25的下端面逐渐降低,起到限流和稳流的作用。长方体槽的一端固定有封堵板,水力制浆桶的出浆管8位于长方体槽的封端板内部;长方体槽的另一端为
开口结构,该端架设在缓冲箱的上方,浆液由端部敞口直接下落至缓冲箱15中。
21.缓冲箱15上端为敞口结构,缓冲箱15的上端面固定有电机支撑架,电机支撑架上固定有搅拌电机,搅拌电机的输出轴朝下设置,输出轴与搅拌桨叶16连接,搅拌桨叶16位于缓冲箱15的中心轴线处,使用搅拌桨叶16对缓冲箱内的浆液进行缓慢搅,保证浆液中固体物料不沉积。缓冲箱15的底部侧壁开设有出浆孔,出浆孔与注浆管17一端连通,注浆管17另一端架设在离心成型机的注浆口或模具夹层中。
22.如图5所示,离心成型机由机架18、护罩19、模具安装盘20和成型模具21等组成,机架18顶面上设置有圆筒状的护罩19,机架18顶面上且位于护罩19内部转动设置有模具安装盘20,模具安装盘20上设置有成型模具21,机架18的底面上设置有电机,电机的输出端与模具安装盘20驱动连接,机架18上且位于护罩19内设置有回水孔,回水孔处向下设置有回水管22,位于回水管22的下方机架18中设置有集水箱23,集水箱23一侧面的底部连接有排水管24。
23.模具安装盘20底面轴线位置竖向设置转轴,机架18上设置轴承座,转轴向下穿过轴承座后与电机的输出端连接,实现电机带动模具安装盘20转动。
24.成型模具21由内模滤筒和外模滤筒组成,内模滤筒的一端设置有内膜法兰,外模滤筒的一端设置有外模法兰,外模滤筒同轴套设在内模滤筒外侧,且外模滤筒与内模滤筒通过外模法兰和内膜法兰固定。
25.模具安装盘20包括圆盘本体,圆盘本体上沿径向方向间隔设置有多个定位长孔,定位长孔内活动设置有定位螺栓,定位螺栓上设置有定位块;圆盘本体上沿径向方向间隔设置有多组螺栓孔。定位块可以为矩形金属块,矩形金属块上开设长孔,定位螺栓依次穿过定位长孔和矩形金属块上的长孔将两者连接。成型模具21在进行安装时,放置到模具安装盘上,定位块抵在外模法兰外周上,通过轻敲定位块来调整成型模具的位置,使得外模法兰上的法兰孔与螺栓孔对准后通过螺栓固定安装。
26.实施例1按1kg陶瓷纤维棉、0.3kg碱性硅溶胶、300kg水比例在水力制浆桶中制浆,然后启动离心机,使离心成型机以10r/min转速旋转,同时通过注浆管向成型模具型腔内连续匀速注浆,直至型腔充满并完整成型,成型后停止注浆,并提高离心成型机转速至300r/min,达到离心脱水的目的,脱水后将模具整体从离心机转盘上取下,经脱模后获得陶瓷纤维管状坯体,再经110℃微波烘干1.5h获得成品。
27.实施例2按1kg陶瓷纤维棉、0.3kg碱性硅溶胶、0.2kg淀粉、300kg水比例制浆,然后启动离心机,使模具以50r/min转速旋转,同时通过注浆管向模具型腔内连续匀速注浆,直至型腔充满并完整成型,成型后停止注浆,并提高离心成型机转速至500r/min,达到离心脱水的目的,脱水后将模具整体从离心机转盘上取下,经脱模后获得陶瓷纤维管状坯体,再经120℃微波烘干1h获得成品。
28.实施例3按1kg陶瓷纤维棉、0.3kg碱性硅溶胶、0.2kg羧甲基纤维素、300kg水比例制浆,然后启动离心机,使模具以30r/min转速旋转,同时通过注浆管向模具型腔内连续匀速注浆,直至型腔充满并完整成型,成型后停止注浆,并提高离心成型机转速至400r/min,达到离心
脱水的目的,脱水后将模具整体从离心机转盘上取下,经脱模后获得陶瓷纤维管状坯体,再经115℃微波烘干1.4h获得成品。
29.对比例使用普通搅拌桶进行制浆,制得的浆料输送至缓冲箱暂存,之后注入真空模具中,利用真空抽滤的方式得到陶瓷纤维管坯体,在电阻丝或化学燃料烘干炉中进行烘干,烘干温度110℃,烘干时间40~45h,得到陶瓷纤维管。
30.将实施例1-3和对比例得到的陶瓷纤维管进行坯体含水率(坯体质量与烘干后成品的质量差占烘干后产品质量的百分比)和烘干后尺寸变形率(坯体直径与成品直径的差值占坯体直径的百分比)进行测试,结果如下表所示: 实施例1实施例2实施例3对比例坯体含水率/a5558360成品尺寸变形率/2.42.812烘干所需时间/h1.511.440~45通过检测结果可知,本发明提供的制备工艺明显降低了坯体的含水率,极大地缩短了烘干时间,提高效率的同时节约能耗;并且成品产品的尺寸变形率很低,保证了成品的质量。
31.陶瓷纤维管的直径 φ200~1000mm,长度1000mm,厚度50mm~200mm,密度120~180kg/m
³ꢀ
,导热系数 0.035 至 0.038 w /(m. k 25℃),最高工作温度 800 ℃ ,长期工作温度500℃。
32.最后,需要注意的是:以上列举的仅是本发明的优选实施例,当然本领域的技术人员可以对本发明进行改动和变型,倘若这些修改和变型属于本发明权利要求及其等同技术的范围之内,均应认为是本发明的保护范围。
再多了解一些
本文用于企业家、创业者技术爱好者查询,结果仅供参考。