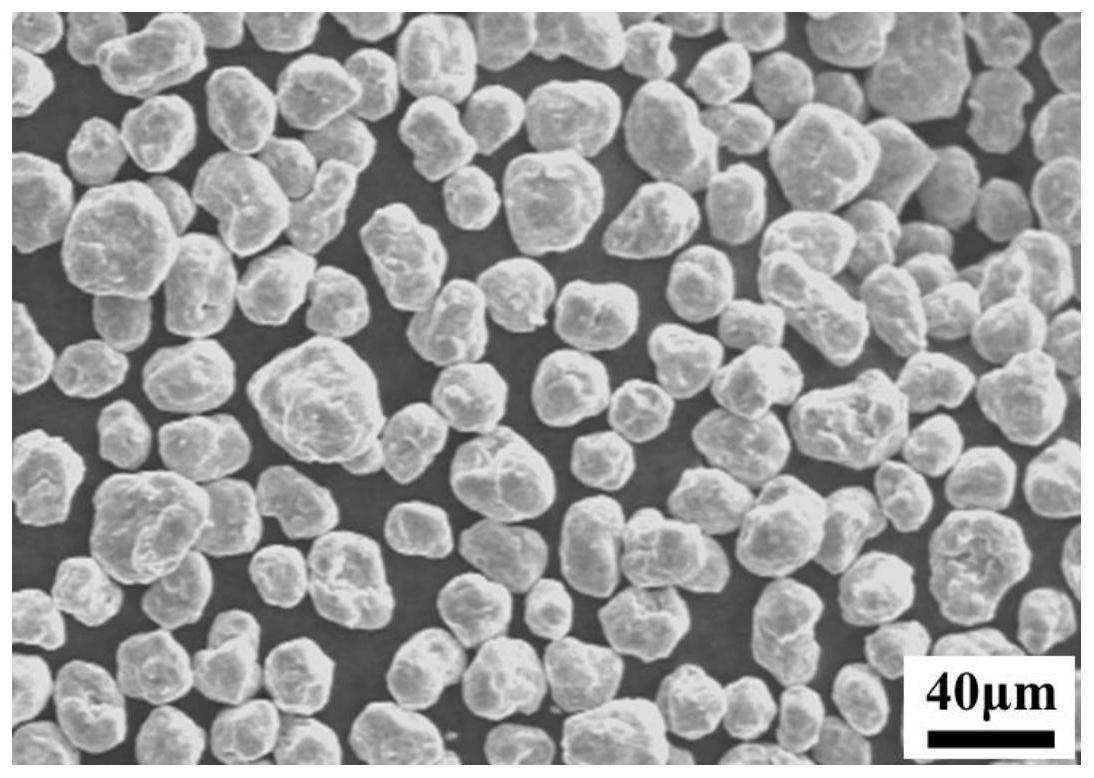
1.本发明涉及金属材料及其制备技术,特别是一种基于钛废料的低成本近球形钛基粉末为原料的高性能钛合金制件及其制备方法。
背景技术:
2.钛及钛合金由于具有密度低、比强度高、耐热性强、耐蚀性好、无毒无磁和良好生物相容性等性能,广泛应用于航空航天、生物医用、汽车等领域。但是钛具有高活性、高熔点、低热导率等特征,采用现有技术的铸造机加工方法存在制备复杂结构困难、成品率低、资源浪费大、生产成本高等问题,严重限制了材料应用水平。
3.以粉末为原料发展日趋成熟的增材制造技术在产品结构功能优化设计、性能调控方面展现出独特优势,可满足高端装备对材料多样化、轻量化和快速研制的需求,已在钛和钛合金领域得到较为广泛深入的研究。然而适用于制备高性能增材制造制件的钛粉要求具有纯净度高、氧含量低、球形度好、粒度小且分布均匀等特征。同时,不同的增材制造技术对钛粉粒度也有严苛的要求,其中激光选区熔化(slm)技术用钛粉粒度应为15~53μm,电子束选区熔化(ebm)用钛粉粒度粒度应为40~110μm,等离子束增材(pdm)用钛粉粒度在50~100μm。但是目前无论是气雾化还是旋转雾化等钛粉制备技术都无法避免产生相当量的超粗(》120μm)和超细粉末(《15μm),它们分别占据粉末总量的40%和10%以上。同时制粉过程中也会出现球形度、氧含量等指标不合格的产品,这种低品钛粉占据粉末总量的5~10%以上。这些粉末缺乏利用价值,成为制粉过程的副产品,目前普遍采用处理方式是廉价出售用于烟花、炮竹等民用产品或者重新回炉熔炼为锭,造成钛资源极大浪费,同时影响后续产品的稳定性。常用制粉技术制得的满足使用要求的粉末收得率,价格昂贵,因此,将钛废料“变废为宝”,开发适合增材制造工艺的低成本钛基粉末是本领域亟待解决的问题。
技术实现要素:
4.本发明所要解决的技术问题是针对现有技术的上述缺陷,提供一种基于钛废料的低成本近球形钛基粉末为原料的高性能钛合金制件及其制备方法。
5.为了实现上述目的,本发明提供了一种钛合金制件的制备方法,其中,包括如下步骤:
6.s100、按所需钛合金制件的零件形状绘制待加工件三维模型并导出;
7.s200、对所述待加工件三维模型进行分层切片处理得到待加工件二维数据,并将得到的所述待加工件二维数据信息输入金属打印装置中;
8.s300、以废残钛结合高温球磨制备的不规则氢化脱氢钛粉为原料,以纯钛板为基板,通过所述金属打印装置通过选择性激光熔化技术制备得到规定形状的钛制件;以及
9.s400、待所述基板温度冷却至室温后取出,并将所述钛制件与所述基板分离,得到钛合金制件成品。
10.上述的钛合金制件的制备方法,其中,还包括:
11.s500、将所述钛合金制件成品在酒精中超声清洗,超声清洗的时间为20min;然后在真空干燥箱中干燥处理,干燥处理的时间为30min,干燥处理的温度为60℃;
12.s600、通过拉伸实验测试步骤s500处理后的所述钛合金制件的抗拉强度和延伸率。
13.上述的钛合金制件的制备方法,其中,步骤s100中采用solidworks软件绘制并导出所述待加工件三维模型。
14.上述的钛合金制件的制备方法,其中,步骤s200进一步包括:
15.s201、将所述待加工件三维模型导入快速成型辅助软件materialise magics中,进行分层切片处理,得到所述待加工件二维数据信息;以及
16.s202、将所述待加工件二维数据信息进行扫描路径生成,并将所得数据输入所述金属打印装置中,设置所述金属打印装置的工艺参数为:激光功率为150~200w,扫描速度为600~900mm/s,扫描间距为0.1~0.14mm,铺粉层厚为20~30μm。
17.上述的钛合金制件的制备方法,其中,步骤s300中的近球形钛基粉末原料采用如下步骤制成:
18.s301、对钛废料进行清洗烘干,清除表面的油污杂质,随后于旋转炉中进行氢化还原除杂,然后对吸氢物料进行清洗-破碎-脱氢处理,最后对脱氢后物料进行二次破碎与筛分,得到规定粒度的不规则氢化脱氢钛粉;
19.s302、将所述不规则氢化脱氢钛粉和氧化锆球按设定球料比放入高温球磨罐中并置于旋转炉炉管,通入设定量的氩气,排尽旋转炉炉管和高温球磨罐中的空气,使所述不规则氢化脱氢钛粉和氧化锆球处于惰性气体保护环境中;
20.s303、待所述旋转炉炉管和高温球磨罐内部空气完全排出,打开所述旋转炉的加热系统,以设定升温速率加热至设定温度,打开所述旋转炉的旋转系统,在恒定温度下以设定转速进行球磨,并以设定速率持续稳定通入氩气;
21.s304、高温球磨结束后,关闭所述旋转炉的加热系统和旋转系统,使粉末随炉冷却且持续稳定通入氩气,当冷却至室温后,停止通气,取出所述高温球磨罐并分离钛粉粉末与氧化锆球;
22.s305、对高温球磨后收集的钛粉粉末进行分级筛分,相邻筛网的筛孔尺寸相差≤15μm,只取相邻筛网之间的钛粉粉末;以及
23.s306、使用真空干燥箱,对筛分后的钛粉粉末进行干燥处理,干燥时间为2-3h,干燥后的钛粉粉末真空封装保存,以用于制备钛合金制件。
24.上述的钛合金制件的制备方法,其中,步骤s301中,使用除油剂及10%hcl和10%hf的混合溶液对钛废料进行清洗;氢化还原除杂使用钙、镁氢化物为还原剂,还原温度为600-800℃,保温时间为30min;所述吸氢物料先后用蒸馏水和10%hcl溶液清洗;所述脱氢处理的温度为600-700℃,时间为5-30h,所述二次破碎与筛分后得到的钛粉粉末粒径为20-44μm。
25.上述的钛合金制件的制备方法,其中,步骤s302中,所述不规则氢化脱氢钛粉的质量为50-1000g,所述氧化锆球与所述氢化脱氢钛粉的质量比为0.5~2:1;所述氧化锆球直径分别为6mm和3mm,两种直径的所述氧化锆球的比例为1:1;所述氩气的流量为1-1.5l/min,通气时间为30-60min。
26.上述的钛合金制件的制备方法,其中,步骤s303中,所述旋转炉的升温速率为5-10℃/min,升温至300-600℃;所述旋转炉的转速为30-60rpm,旋转时间为5-10h;所述氩气流量为1-1.5l/min。
27.上述的钛合金制件的制备方法,其中,步骤s300还包括:
28.s307、真空封装前取钛粉粉末分别通过扫描电子显微镜、霍尔流速计及惰气脉冲红外热导法检测高温球磨后钛粉粉末的形貌、流动性和氧含量,并计算钛粉粉末的氧增量。
29.为了更好地实现上述目的,本发明还提供了一种采用上述钛合金制件的制备方法制得的钛合金制件。
30.本发明的技术效果在于:
31.本发明以废残钛为原料制备不规则氢化脱氢钛粉,在此基础上,结合高温球磨技术制备满足3d打印用粉末要求的低成本高性能钛粉,最终通过增材制造技术制备高性能零部件。该方法节能环保、成本低、杂质含量可控且适于制备高性能复杂结构钛制件;此外,该方法也可应用于其它金属粉末的整形处理及高性能制件的制备。
32.以下结合附图和具体实施例对本发明进行详细描述,但不作为对本发明的限定。
附图说明
33.图1为本发明一实施例制备的涡轮制件图;
34.图2为本发明一实施例的钛粉制备原理图;
35.图3为本发明一实施例的高温球磨罐示意图;
36.图4为本发明实施例1制备的钛粉整形前的扫描电镜照片;
37.图5为本发明实施例1制备的钛粉整形后的扫描电镜照片。
38.其中,附图标记
[0039]1ꢀꢀ
旋转炉炉管
[0040]2ꢀꢀ
高温球磨罐
[0041]3ꢀꢀ
罐盖
[0042]4ꢀꢀ
通气孔
[0043]5ꢀꢀ
罐体
[0044]6ꢀꢀ
卡槽
[0045]7ꢀꢀ
待加工物料
具体实施方式
[0046]
下面结合附图对本发明的结构原理和工作原理作具体的描述:
[0047]
参见图1,图1为本发明一实施例制备的涡轮制件图。本发明利用钛废料通过增材制造方式制备低成本高性能制件,首先通过氢化脱氢法利用氢在钛中的可逆特性将钛废料制备成不规则钛粉;然后通过高温球磨将不规则钛粉整形处理得到近球形粉末;最终以近球形粉末为原料,利用选择性激光熔化等增材制造技术制备低成本高性能的钛制件。本发明的钛合金制件采用如下方法制备,该制备方法包括如下步骤:
[0048]
步骤s100、按所需钛合金制件的零件形状绘制待加工件三维模型并导出,优选采用solidworks软件绘制并导出所述待加工件三维模型;
[0049]
步骤s200、对所述待加工件三维模型进行分层切片处理得到待加工件二维数据,并将得到的所述待加工件二维数据信息输入金属打印装置中;
[0050]
步骤s300、以废残钛结合高温球磨技术制备的不规则氢化脱氢钛粉为原料,以纯钛板为基板,通过所述金属打印装置通过选择性激光熔化技术制备得到规定形状的钛制件;以及
[0051]
步骤s400、待所述基板温度冷却至室温后取出,并将所述钛制件与所述基板分离,得到钛合金制件成品。
[0052]
本实施例还可包括:
[0053]
步骤s500、将所述钛合金制件成品在酒精中超声清洗,超声清洗的时间为20min;然后在真空干燥箱中干燥处理,干燥处理的时间为30min,干燥处理的温度为60℃;
[0054]
步骤s600、通过拉伸实验测试步骤s500处理后的所述钛合金制件的抗拉强度和延伸率。
[0055]
其中,步骤s200进一步包括:
[0056]
步骤s201、将所述待加工件三维模型导入快速成型辅助软件materialise magics中,进行分层切片处理,得到所述待加工件二维数据信息;以及
[0057]
步骤s202、将所述待加工件二维数据信息进行扫描路径生成,并将所得数据输入所述金属打印装置中,设置所述金属打印装置的工艺参数为:激光功率为150~200w,扫描速度为600~900mm/s,扫描间距为0.1~0.14mm,铺粉层厚为20~30μm。
[0058]
参见图2及图3,图2为本发明一实施例的钛粉制备原理图,图3为本发明一实施例的高温球磨罐2示意图。本实施例中,步骤s300中的近球形钛基粉末原料采用如下设备和工艺制成:将旋转炉与惰性气源连通,高温球磨罐2的罐盖3上设置有通气孔4,高温球磨罐2的罐体5上设置有与旋转炉炉管1内壁连接的卡槽6,待加工物料7放入罐体5内后,将罐盖3通过固定螺丝与罐体5固定连接,将罐体5通过卡槽6和顶丝与旋转炉炉管1连接,旋转炉设置有加热系统和旋转系统,旋转炉带动高温球磨罐2旋转,使得位于罐体5内的待加工物料7和罐体5内壁发生相对运动,使待加工物料7与罐体5之间相互摩擦碰撞,以改善待加工物料7的表面形貌和粒度分布。近球形钛基粉末制备具体包括如下步骤制成:
[0059]
步骤s301、对钛废料进行清洗烘干,清除表面的油污杂质,随后于旋转炉中进行氢化还原除杂,然后对吸氢物料进行清洗-破碎-脱氢处理,最后对脱氢后物料进行二次破碎与筛分,得到规定粒度的不规则氢化脱氢钛粉;
[0060]
步骤s302、将所述不规则氢化脱氢钛粉和氧化锆球按设定球料比放入高温球磨罐2中并置于旋转炉炉管1,通入设定量的氩气,排尽旋转炉炉管1和高温球磨罐2中的空气,使所述不规则氢化脱氢钛粉和氧化锆球处于惰性气体保护环境中;
[0061]
步骤s303、待所述旋转炉炉管1和高温球磨罐2内部空气完全排出,打开所述旋转炉的加热系统,以设定升温速率加热至设定温度,打开所述旋转炉的旋转系统,在恒定温度下以设定转速进行球磨,并以设定速率持续稳定通入氩气;
[0062]
步骤s304、高温球磨结束后,关闭所述旋转炉的加热系统和旋转系统,使粉末随炉冷却且持续稳定通入氩气,当冷却至室温后,停止通气,取出所述高温球磨罐2并分离钛粉粉末与氧化锆球;
[0063]
步骤s305、对高温球磨后收集的钛粉粉末进行分级筛分,相邻筛网的筛孔尺寸相
差≤15μm,只取相邻筛网之间的钛粉粉末;以及
[0064]
步骤s306、使用真空干燥箱,对筛分后的钛粉粉末进行干燥处理,干燥时间为2-3h,干燥后的钛粉粉末真空封装保存,以用于制备钛合金制件。
[0065]
该制备过程还可包括:步骤s307、真空封装前取钛粉粉末分别通过扫描电子显微镜、霍尔流速计及惰气脉冲红外热导法检测高温球磨后钛粉粉末的形貌、流动性和氧含量,并计算钛粉粉末的氧增量。
[0066]
本实施例的步骤s301中,优选使用除油剂及10%hcl和10%hf的混合溶液对钛废料进行清洗;氢化还原除杂优选使用钙、镁氢化物为还原剂,还原温度优选为600-800℃,保温时间优选为30min;所述吸氢物料先后用蒸馏水和10%hcl溶液清洗;所述脱氢处理的温度优选为600-700℃,时间优选为5-30h,所述二次破碎与筛分后得到的钛粉粉末粒径优选为20-44μm。步骤s302中,所述不规则氢化脱氢钛粉的质量优选为50-1000g,所述氧化锆球与所述氢化脱氢钛粉的质量比优选为0.5~2:1;所述氧化锆球直径分别优选为6mm和3mm,两种直径的所述氧化锆球的比例优选为1:1;所述氩气的流量优选为1-1.5l/min,通气时间优选为30-60min。步骤s303中,所述旋转炉的升温速率优选为5-10℃/min,升温至300-600℃;所述旋转炉的转速优选为30-60rpm,旋转时间优选为5-10h;所述氩气流量优选为1-1.5l/min。
[0067]
下面以具体实施例进一步说明本发明的钛合金制件及其制备过程:
[0068]
实施例1
[0069]
用除油剂清洗废残钛,以去除表面油污,然后用10%hcl和10%hf的混合溶液进行酸洗处理,酸洗后进行烘干;将烘干后的废残钛与氢化钙、氢化镁混合放入旋转炉并抽真空,随后升温至600℃并保温30min,通入高纯氩气至0.3mpa并保持10h;将吸氢处理后的物料先后用蒸馏水和10%hcl清洗并烘干;随后将上述物料在惰性气体保护下进行机械破碎;破碎处理后的物料于真空炉中在700℃条件下脱氢处理8h;最后通过二次破碎及筛分得到粒径在20-44μm的不规则氢化脱氢钛粉(参见图4),以作为高温球磨制备选区激光熔化(slm)用钛粉原料。
[0070]
分别称取500g上述不规则形貌氢化脱氢钛粉,500g直径6mm和500g直径3mm的氧化锆球,然后将其均匀混合放入高温球磨罐2中,并将高温球磨罐2用螺丝固定于旋转炉炉管1中。自旋转炉炉管1左端向右端持续稳定通入ar,流量为1.5l/min,待30min后旋转炉炉管1和高温球磨罐2内部的空气全部排出,打开旋转炉的加热系统,以5℃/min升温速率加热至500℃;再打开旋转炉的旋转系统使旋转炉炉管1以60rpm的速度旋转,进行5h高温球磨处理,整个过程以1.5l/min的流量持续稳定通入ar;球磨结束后关闭旋转炉的加热系统和旋转系统,使钛粉粉末随炉冷却,整个过程以1.5l/min的流量持续稳定通入ar;冷却至室温后,停止通气并取出高温球磨罐2,将钛粉与氧化锆球从高温球磨罐2中取出并分离,经筛分得到粒度25-40μm的近球形钛粉,干燥后进行真空封装;重复上述球磨步骤5次,并将5次得到的粉末混合均匀,干燥并真空封装保存。封装前取少量粉末,通过扫描电子显微镜观察高温球磨处理后的氢化脱氢钛粉的形貌(参见图5),并测试其流动性和氧含量,以得到处理后钛粉粉末的氧增量,结果如表1所示。
[0071]
以上述获得的低成本近球形钛基粉末为原料,通过以下步骤制备高性能钛合金制件:
[0072]
步骤s100、利用solidworks软件按所需零件形状绘制三维模型并导出;
[0073]
步骤s200、将cad模型导入快速成型辅助软件materialise magics中,进行分层切片处理,得到二维数据信息,并将得到的二维数据信息输入金属打印设备中,具体工艺参数为:激光功率175w,扫描速度900mm/s,扫描间距0.14mm,铺粉层厚30μm;
[0074]
步骤s300、以上述高温球磨处理得到的近球形钛粉为原料、纯钛板为基板,通过选择性激光熔化制备得到规定形状的钛制件;
[0075]
步骤s400、打印完成,待基板温度冷却至室温后取出基板,并通过线切割制件从基板切下;
[0076]
步骤s500、将步骤s400中得到的制件在酒精中超声清洗20min,然后在真空干燥箱中干燥处理30min,干燥处理温度为60℃;以及
[0077]
步骤s600、通过拉伸实验测试经步骤s500处理得到的制件的抗拉强度和延伸率,并测试制件的致密度,结果如表1所示。
[0078]
实施例2
[0079]
用除油剂清洗废残钛,以去除表面油污,然后用10%hcl和10%hf的混合溶液进行酸洗处理,酸洗后进行烘干;将烘干后的废残钛与氢化钙、氢化镁混合放入旋转炉并抽真空,随后升温至800℃并保温30min,通入高纯氩气至0.1mpa并保持10h;将吸氢处理后的物料先后用蒸馏水和10%hcl清洗并烘干;随后将上述物料在惰性气体保护下进行机械破碎;破碎处理后的物料于真空炉中在600℃条件下脱氢处理15h;最后通过二次破碎及筛分得到粒径在20-44μm的不规则氢化脱氢钛粉,以作为高温球磨制备选区激光熔化的原料。
[0080]
分别称取800g上述不规则形貌氢化脱氢钛粉,800g直径6mm和800g直径3mm的氧化锆球,然后将其均匀混合放入高温球磨罐2中,并将高温球磨罐2用螺丝固定于旋转炉炉管1中。自旋转炉炉管1左端向右端持续稳定通入ar,流量为1.25l/min,待30min后旋转炉炉管1和高温球磨罐2内部的空气全部排出,打开旋转炉的加热系统,以5℃/min升温速率加热至300℃;再打开旋转炉的旋转系统使旋转炉炉管1以60rpm的速度旋转,进行10h高温球磨处理,整个过程以1.25l/min的流量持续稳定通入ar;球磨结束后关闭旋转炉的加热系统和旋转系统,使钛粉粉末随炉冷却,整个过程以1.25l/min的流量持续稳定通入ar;冷却至室温后,停止通气并取出高温球磨罐2,将钛粉与氧化锆球从高温球磨罐2中取出并分离,经筛分得到粒度28-43μm的近球形钛粉,干燥后进行真空封装。重复3次上述高温球磨过程,并将3次得到的粉末混合均匀,干燥并真空封存。封装前取少量粉末,通过扫描电子显微镜观察高温球磨处理后的氢化脱氢钛粉的形貌,并测试其流动性和氧含量,以得到处理后粉末的氧增量,结果如表1所示。可多次重复上述操作至所制备粉末量满足打印需求。
[0081]
以上述获得的低成本近球形钛基粉末为原料,通过以下步骤制备高性能钛合金制件:
[0082]
步骤s100、利用solidworks软件按所需零件形状绘制三维模型并导出;
[0083]
步骤s200、将cad模型导入快速成型辅助软件materialise magics中,进行分层切片处理,得到二维数据信息,并将得到的二维数据信息输入金属打印设备中,工艺参数为:激光功率200w,扫描速度600mm/s,扫描间距0.14mm,铺粉层厚30μm;
[0084]
步骤s300、以上述高温球磨处理得到的近球形钛粉为原料、纯钛板为基板,通过选择性激光熔化技术制备得到规定形状的钛制件;
[0085]
步骤s400、打印完成,待基板温度冷却至室温后取出基板,并通过线切割制件从基板切下;
[0086]
步骤s500、将步骤s400中得到的制件在酒精中超声清洗20min,然后在真空干燥箱中干燥处理30min,干燥处理温度为60℃;以及
[0087]
步骤s600、通过拉伸实验测试经步骤s500处理得到的制件的抗拉强度和延伸率,并测试制件的致密度,结果如表1所示。
[0088]
实施例3
[0089]
用除油剂清洗废残钛,以去除表面油污,然后用10%hcl和10%hf的混合溶液进行酸洗处理,酸洗后进行烘干;将烘干后的废残钛与氢化钙、氢化镁混合放入旋转炉并抽真空,随后升温至700℃并保温30min,通入高纯氩气至0.5mpa并保持5h;将吸氢处理后的物料先后用蒸馏水和10%hcl清洗并烘干;随后将上述物料在惰性气体保护下进行机械破碎;破碎处理后的物料于真空炉中在650℃条件下脱氢处理5h;最后通过二次破碎及筛分得到粒径在20-44μm的不规则氢化脱氢钛粉,以作为高温球磨制备选区激光熔化用钛粉。
[0090]
分别称取1000g上述不规则形貌氢化脱氢钛粉、1000g直径6mm和1000g直径3mm的氧化锆球,然后将其均匀混合放入高温球磨罐2中,并将高温球磨罐2用螺丝固定于旋转炉炉管1中。自旋转炉炉管1左端向右端持续稳定通入ar,流量为1l/min,待30min后旋转炉炉管1和高温球磨罐2内部的空气全部排出,打开旋转炉的加热系统,以5℃/min升温速率加热至600℃;再打开旋转炉的旋转系统使旋转炉炉管1以30rpm的速度旋转,进行5h高温球磨处理,整个过程以1l/min的流量持续稳定通入ar;球磨结束后关闭旋转炉的加热系统和旋转系统,使粉末随炉冷却,整个过程以1l/min的流量持续稳定通入ar;冷却至室温后,停止通气并取出高温球磨罐2,将钛粉与氧化锆球从高温球磨罐2中取出并分离,经筛分得到粒度23-38μm的近球形钛粉,干燥后进行真空封装。重复3次上述高温球磨过程,并将3次得到的粉末混合均匀,干燥并真空封存。封装前取少量粉末,通过扫描电子显微镜观察高温球磨处理后的氢化脱氢钛粉的形貌,并测试其流动性和氧含量,以得到处理后粉末的氧增量,结果如表1所示。可多次重复上述操作至所制备粉末量满足打印需求。
[0091]
以上述获得的低成本近球形钛基粉末为原料,通过以下步骤制备高性能钛合金制件:
[0092]
步骤s100、利用solidworks软件按所需零件形状绘制三维模型并导出;
[0093]
步骤s200、将cad模型导入快速成型辅助软件materialise magics中,进行分层切片处理,得到二维数据信息,并将得到的二维数据信息输入金属打印设备中,工艺参数为:激光功率为150w,扫描速度为650mm/s,扫描间距为0.1mm,铺粉层厚为20μm;
[0094]
步骤s300、以上述高温球磨处理得到的近球形钛粉为原料、纯钛板为基板,通过选择性激光熔化制备得到规定形状的钛制件;
[0095]
步骤s400、打印完成,待基板温度冷却至室温后取出基板,并通过线切割将制件从基板切下;
[0096]
步骤s500、将步骤s400中得到的制件在酒精中超声清洗20min,然后在真空干燥箱中干燥处理30min,干燥处理温度为60℃;以及
[0097]
步骤s600、通过拉伸实验测试经步骤s500处理得到的制件的抗拉强度和延伸率,并测试制件的致密度,结果如表1所示。
[0098]
表1
[0099]
组别实施例1实施例2实施例3不规则氢化脱氢钛粉氧含量/ppm120012501100高温球磨后钛粉氧含量/ppm145014501400氧增量/ppm250200300流动性/(s/50g)343235制件致密度/%99.8499.6599.52制件拉伸强度/mpa985.4978.5962.8制件拉伸塑性/%17.313.914.7
[0100]
从表1可以看出,实施例1-3中高温球磨整形处理后的钛粉增氧量极低,在200-300ppm范围内,且粉末流动性为32-35s/50g,可满足选区激光熔化技术用原料粉末的要求。高温球磨工艺具有成本低、工艺和设备简单、氧含量可控、粉末收得率高等优点,有利于增材制造钛产品的大规模应用;此外,该方法可应用于其它金属粉末的整形处理,生产电子束熔化等其他增材制造技术、热等静压、注射成形等粉末近净成形技术用金属粉末。实施例1-3中制备得到的制件具有高致密度且兼具高强度和高塑性,致密度均高于99.5%。实施例1-3中制件强度和延伸率分别在962.8mpa-985.4mpa和13.9%-17.3%范围内,均高于美国astm-b381标准锻造ti-6al-4v合金(895mpa,10%)水平。
[0101]
综上,本发明主要具备如下优点:
[0102]
1)节能环保,以废残钛为原料生产氢化脱氢钛粉,可从根本上解决以钛矿原料,经过冶炼或是电化学法制备纯钛工艺存在的局限性,即消耗大量能源,同时产生大量废物和废气严重污染环境的问题;
[0103]
2)成本低,采用废残钛为原料,可大幅度降低原料成本,提高钛材料循环利用率;通过高温球磨技术对钛粉进行整形处理,工艺流程及设备简单,钛粉收得率高接近100%,大幅降低了生产成本;
[0104]
3)杂质含量可控,废残钛制备氢化脱氢钛粉过程是在氢气氛围下进行热还原,相比于现有技术的氩气氛围,除杂效果更好;同时在球磨升温前把高温球磨罐和旋转炉炉管中的空气全部排除,并在整个球磨过程中持续保持氢气稳定的通入,有效防止高温环境中钛粉受到污染,使整形后钛粉的氧含量得到严格的控制;
[0105]
4)处理后粉末流动性较好,采用高温球磨整形工艺,高温使钛粉的本征强度降低,更有利于其发生塑性变形和小颗粒之间的焊合和团聚,得到较机械球磨更好的整形效果;该过程中粉末颗粒与氧化锆球、粉末颗粒和高温球磨罐之间相互摩擦、碰撞,使粉末尖锐的棱角得到有效磨削而消失,小颗粒粉末团聚,从而得到流动性好的近球形钛粉;
[0106]
5)适于制造高性能复杂结构钛制件,采用选择性激光熔化技术制备钛制件,该工艺具有快速冷凝特征,可达到103-108k/s,有利于形成晶粒细小组织结构,进而可提高制件的力学性能;基于数字模型,运用离散-堆积原理,在计算机软件等数控系统控制下,逐点、逐线、逐层堆积并熔化粉末,可准确控制零件的宏观结构和内部微观拓扑结构,实现复杂结构零件的精确制造。
[0107]
当然,本发明还可有其它多种实施例,在不背离本发明精神及其实质的情况下,熟悉本领域的技术人员当可根据本发明作出各种相应的改变和变形,但这些相应的改变和变
形都应属于本发明所附的权利要求的保护范围。
再多了解一些
本文用于企业家、创业者技术爱好者查询,结果仅供参考。