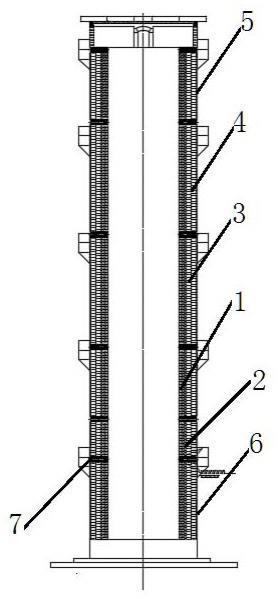
1.本实用新型涉及全自动石灰窑,特别涉及一种全自动低碳节能环保高寿命石灰窑,属于窑炉技术领域。
背景技术:
2.钢铁工业、电石工业、氧化铝工业、耐火材料等行业都需要消耗大量的石灰,所以需要大量的石灰窑为这些行业供料,随着科学技术的发展,传统的土烧石灰窑已经被逐渐淘汰,在国家严厉的环境和节能降耗指令下,全自动运行石灰窑已经成为行业的主流,目前的全自动石灰窑能够实现自动配料、上料、控温、出料,较传统的土烧窑有了明显的技术进步,能耗、效率方面均有明显的改善,在自动控制技术下,通过精确运行各环节的工艺来降低能耗是一种技术手段,这一技术手段随着测量、传感器技术的发展在全自动石灰窑的节能降耗中发挥了很大的作用,很多石灰窑设计、建造企业较为关注这也方面,石灰窑是一个整体系统的工程,其窑体的设计建造方案本身就对能耗、寿命影响很大,例如传统的窑炉耐材结构采用一层345mm长(在炉体径向上的尺寸)、高约75mm的高铝标砖 轻质保温砖 隔热纤维 钢质炉,高铝标砖、轻质保温砖均为长方形,石灰窑最内层仅为一层高铝砖,而窑炉出现问题,在使用中发现,这种砌筑的炉体大部分情况都是从砖与砖之间的砌筑灰缝跑火,而紧挨着高铝砖的保温砖本身不耐高温,窑内火通过灰缝跑到保温层的话很快就会把保温层烧坏,引起连锁反应窑炉耐材大面积损坏,造成能耗高,严重情况下造成炉体坍塌,窑炉使用寿命大幅度降低。
技术实现要素:
3.本实用新型的目的在于克服目前现有的石灰窑中存在的上述问题,提供一种全自动低碳节能环保高寿命石灰窑。
4.为实现本实用新型的目的,采用了下述的技术方案:一种全自动低碳节能环保高寿命石灰窑,包括配料系统、出料系统,炉体,所述的炉体自内向外依次为第一高铝砖层构、第二高铝砖层构、第一保温砖层构、第二保温砖层构、耐火纤维层、钢炉壳,其中第一高铝砖层构、第二高铝砖层构、第一保温砖层构、第二保温砖层构均为采用耐火砖砌筑而成的砌筑体,所述的耐火砖为楔形砖,每块耐火砖的高度为100-130mm,同一层构中上下相邻的层的砖缝错开,相连的两层构的砖缝错开,在高度上每隔4-6米具有一层楔形高铝结构砖砌筑层,该层中的每块形高铝结构砖自内向外从第一高铝砖层构覆盖至第二保温砖层构。
5.进一步的;第一高铝砖层构壁厚为290-320mm,第二高铝砖层构的壁厚为90-110mm,壁厚指在炉体径向上的尺寸。
6.进一步的;所述的耐火纤维层为5
㎝
厚的硅酸铝耐火纤维。
7.进一步的;各砖构层中相邻的耐火砖之间的灰缝为2mm。
8.进一步的;每块耐火砖的高度为120mm,第一高铝砖层构壁厚为295-310mm、第二高铝砖层构的壁厚为95-105mm。
9.本实用新型的积极有益技术效果在于:本石灰窑采用两层高铝砖层构,这两层高铝砖层构之间水平左右错缝,竖向上下错缝布置,避免出现内外通缝现象,即使最里面一层高铝砖出现问题跑火,还有一层高铝砖进行保护,不会把火传导到保温层,这种设计极大的提高了窑炉耐材的使用寿命,节约了能耗,较传统的石灰窑实现了低碳节能,耐火砖为楔形,灰缝尺寸均匀,火不会对某个灰缝侵蚀严重,砖的高度也设计为120mm大尺寸,大大的减少了灰缝数量,大幅避免了灰缝耐火泥砌筑质量所引起的砌筑质量问题,同时也大幅提高了耐材的施工效率,窑炉耐材每隔4-6米左右,设置一层楔形的高铝结构砖,把窑炉竖向分成多段,这种设计对窑炉耐材的整体结构强度进行了加强,保证了窑内即使每段有少部分耐材损坏,耐材砌体在整体强度上也影响不大,本窑炉上配置现有的配料系统、出料系统、测量系统、控制系统,可形成全自动节能环保高寿命石灰窑。
附图说明
10.图1是窑体的竖直截面图。
11.图2是图1下部的放大图。
12.图3是图2中a-a向的截面图。
13.图4是图2中b-b向的截面图。
具体实施方式
14.为了更充分的解释本实用新型的实施,提供本实用新型的实施实例。这些实施实例仅仅是对本实用新型的阐述,不限制本实用新型的范围。
15.结合附图对本实用新型进一步详细的解释,附图中各标记为:1:第一高铝砖层构;2:第二高铝砖层构;3:第一保温砖层构;4:第二保温砖层构;5:耐火纤维层;6:钢炉壳;7:高铝结构砖砌筑层;701:高铝结构砖;702:热电偶工艺孔。
16.如附图所示,一种全自动低碳节能环保高寿命石灰窑,包括炉体,所述的炉体自内向外依次为第一高铝砖层构1、第二高铝砖层构2、第一保温砖层构3、第二保温砖层构4、耐火纤维层5、钢炉壳4,其中第一高铝砖层构、第二高铝砖层构、第一保温砖层构、第二保温砖层构均为采用耐火砖砌筑而成的砌筑体,所述的耐火砖为楔形砖,为便于制作,楔形转在炉体壁厚方向上的两个端面仍然采用平面,在炉体周向上的两个端面内端面窄、外端面宽,楔形的数据可有炉体的直径、砖在壁厚上的尺寸、灰缝尺寸、砖在炉体周向上的尺寸得到,每块耐火砖的高度为100-130mm,更为详细的,每块耐火砖的高度为120mm。
17.第一高铝砖层构壁厚为290-320mm,第二高铝砖层构的壁厚为90-110mm,更为详细的,第一高铝砖层构壁厚为295-310mm、第二高铝砖层构的壁厚为95-105mm,本实施例中,第一高铝砖层构壁厚为302mm,第二高铝砖层构的壁厚为102同一层构中上下相邻的砖缝错开,相连的两层构的砖缝错开,在高度上每隔4-6米具有一层楔形高铝结构砖砌筑层,楔形高铝结构砖砌筑层指高铝结构砖砌筑层中的高铝结构砖也是楔形,层该层中的每块形高铝结构砖自内向外从第一高铝砖层构覆盖至第二保温砖层构。所述的耐火纤维层为5
㎝
厚的硅酸铝耐火纤维。各砖构层中相邻的耐火砖之间的灰缝为2mm。本实用新型的高铝砖了采用lz-55或lz-65型高铝砖,楔形定制制作。
18.本石灰窑上具有配置有配料系统、出料系统,为jhzs型石灰竖窑,jhzs型石灰竖窑
上的配料系统、出料系统为现有技术,在目前的全自动石灰窑中具有现有的应用,本石灰窑科学设计炉子高径比,例如250m3石灰窑内径4米,外径6米,有效高度22米,窑内耐火保温层创造性的采用两层高铝砖 两层轻质保温砖 硅酸铝耐火纤维 钢质炉壳的结构,和传统的砌筑方式相比具有节能、省煤、使用寿命长等优点,窑炉耐材由两层高铝质耐火砖和两层轻质保温耐火砖以及一层硅酸盐耐火纤维构成,总厚度为1米,其中两层保温砖总厚度有60cm,最大限度的避免了窑炉热量经窑体热传导的损失,是窑炉低能耗生产的保证,传统的石灰窑最内层仅为一层高铝砖,而窑炉出现问题,大部分情况都是从砖与砖之间的砌筑灰缝跑火,而紧挨着高铝砖的保温砖本身不耐高温,窑内火通过灰缝跑到保温层的话很快就会把保温层烧坏,引起连锁反应窑炉耐材大面积损坏,造成能耗高、窑炉使用寿命大幅度降低等众多弊端。本石灰窑采用两层高铝砖,这两层高铝砖之间水平左右错缝,竖向上下错缝布置,避免出现内外通缝现象,即使最里面一层高铝砖出现问题跑火,后面还有一层高铝砖进行保护,不会把火传导到保温层,这种设计极大的提高了窑炉耐材的使用寿命,节约了能耗;耐材砌体与钢炉壳间设置5
㎝
厚的硅酸铝耐火纤维,在给窑炉保温的同时,在炉壳与耐火砖砌体之间形成软接触缓冲,防止窑钢壳摆动对砌体的结构产生影响;窑炉耐材每5米左右,设置一层通长大型高铝预制结构砖砌筑层,一共5层结构砖把窑炉竖向分成6段,这种设计对窑炉耐材的整体结构强度进行了加强,保证了窑体即使每段有少部分耐材损坏,窑炉砌体在整体强度上也影响不大。
19.本窑炉的工艺与传统的jhzs型石灰竖窑相同,本石灰窑在中:物料在窑内的煅烧分为三个阶段,预热带、煅烧带和冷却带。主供风装置安置在窑下部特定位置向上鼓风,窑上部烟气管道由变频控制的引风机作用形成负压向上引风,使窑内料面上方形成微负压区,这个微负压保证了炉内气流顺畅,非常有利于煅烧带石灰石进行分解,同时从窑体下部鼓入的常温下的助燃风进入窑内后从下向上首先接触到窑内下部烧成的成品灰,在降低出灰温度的同时,把成品灰上的余热向上带走,随后暖风进入到煅烧带参与煅烧补氧,而后经煅烧带后的高温气流继续上升到预热带和后进入窑炉还未燃烧的常温原料充分接触,其热量被原料充分吸收,积累石灰分解所需的热量,这样的热交换过程极大限度的减少了热量从上部和下部的散失,使排出的成品灰温度在60℃以下,窑顶部排出的烟气温度在150℃以下,使得煤所释放的热量最大限度的被石头吸收,也就是节约了热量、节约了煤的使用量。本石灰窑在窑体上进料了创造性的改进,其余部分可沿用现有技术,现有技术部分在本实用新型中没有再赘述。
20.在详细说明本实用新型的实施方式之后,熟悉该项技术的人士可清楚地了解,在不脱离上述申请专利范围与精神下可进行各种变化与修改,凡依据本实用新型的技术实质对以上实施例所作的任何简单修改、等同变化与修饰,均属于本实用新型技术方案的范围,且本实用新型亦不受限于说明书中所举实例的实施方式。
再多了解一些
本文用于企业家、创业者技术爱好者查询,结果仅供参考。