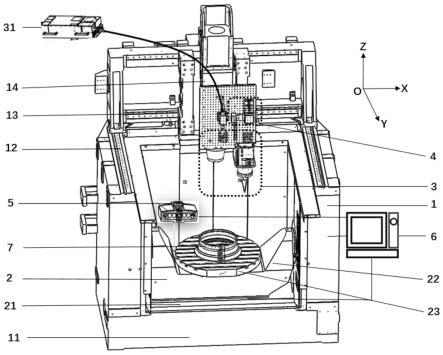
基于五轴数控机床用激光加工发动机火焰筒气膜孔的装置
1.技术领域
2.本发明涉及数控与激光技术领域,尤其是一种基于五轴数控机床应用激光技术加工发动机火焰筒气膜孔的装置。
背景技术:
[0003][0004]
航空发动机是靠燃烧室高温高压气体推动叶片高速旋转而产生巨大动力,燃烧室最主要的高温部件是火焰筒,在高温、高压的燃烧火焰和热燃气的作用下,火焰筒承受着高强度的热负荷、热冲击负荷及机械振动负荷,导致火焰筒会发生裂纹、翘曲和变性等损坏现象,甚至还会出现热障涂层掉块、磨损和烧穿等故障。因此高温部件一直是航空发动机研究的重点。为保障火焰筒在极端高温环境下稳定持续工作,必须对其进行冷却降温。
[0005]
目前,提高火焰筒耐温技术主要综合采用壁面冷却技术、热障涂层技术与耐高温材料技术。对于耐高温材料技术,由早期的不锈钢,发展到各种类型的铁基、镍基、钴基、金属基化合物、金属基复合材料(mmc)以及陶瓷基复合材料(cmc)等;对于热障涂层技术,是在火焰筒合金材科上涂覆涂层并结合气膜冷却的方式;对于壁面冷却技术,是在火焰筒壁面设计上采用气膜孔冷却的方式来提高叶片的耐高温性,即通过在火焰筒壁开若干排气膜孔,冷却空气通过设定的进气形式进入火焰筒并贴着壁面流动,在内壁面和热燃气之间形成连续的温度较低的冷气膜,从而实现隔热和冷却的作用。现有技术多采用热障涂层技术与壁面冷却技术相结合的技术方案对火焰筒进行冷却降温。对于带热障涂层的火焰筒上的气膜孔的加工并非简单,存在的问题是,一是,当下多采用电火花打孔,即先打孔再涂覆热障涂层,由于电火花打孔受限于材料属性,难以加工新型的非导电材料;二是,存在着涂层崩碎、产生剥离的缺陷;三是,存在孔壁的重铸层厚,涂层材料沉积导致孔径缩小及孔型不规则的缺陷。为了加工出质量更高的火焰筒气膜孔,亟需研发一种用于加工航空发动机火焰筒异形气膜孔的装置以满足国家重大需求。
技术实现要素:
[0006]
本发明的目的是针对现有技术的不足而提供的一种基于五轴数控机床应用激光技术加工发动机火焰筒气膜孔的装置,本发明采用将一台设有x、y及z轴直角坐标系的数控机床及一台设有x、y及z轴直角坐标系的数控摇篮置于同一直角坐标系中;并将数控机床的第一数控装置及数控摇篮的第二数控装置与计算机联控构成五轴数控机床。本发明采用激光切割系统及同轴成像系统构成一套与五轴数控机床联动的气膜孔激光加工及孔型检测系统。其中,激光切割系统中的激光器选用了高功率纳秒激光器,借助纳秒激光器的高重复频率和二维振镜的高运动速度,充分的发挥了高功率、高重复频率激光加工的优势,能更加有效提高气膜孔的加工效率及加工质量;本发明克服了材料属性的限制,消除了涂层崩碎、
产生剥离的缺陷,保证了孔型的精度,且满足国家对于关键装备的重大需求。
[0007]
实现本发明目的的具体技术方案是:一种基于五轴数控机床用激光加工发动机火焰筒气膜孔的装置,其特点包括数控机床、数控摇篮、激光切割系统、同轴成像系统、三维扫描仪、计算机及火焰筒;所述数控机床上设有x、y及z轴直角坐标系,数控机床上设有基座,基座上设有沿y轴运行的横梁,横梁上设有沿x轴运行的托板,托板上设有沿z轴运行的刀架;所述数控机床内设第一数控装置;所述基座上还设有扫描仪座;所述数控摇篮上设有x、y及z轴直角坐标系,数控摇篮上设有摇篮座,摇篮座上设有绕z轴转动的转盘,转盘上设有绕x轴或y转轴动的工作台;所述数控摇篮内设第二数控装置;所述数控摇篮的摇篮座设于数控机床的基座上;且数控摇篮与数控机床设于同一直角坐标系中;所述激光切割系统由激光器、第一反射镜、第二反射镜、第三反射镜及二维振镜构成,且激光器、第一反射镜、第二反射镜、第三反射镜及二维振镜依次光路连接;所述同轴成像系统由第四反射镜、白光光源及ccd相机构成,所述同轴成像系统设于激光切割系统中;其中,白光光源穿过激光切割系统的第二反射镜经第三反射镜反射至二维振镜,且白光光源与二维振镜的旋切光束共路;ccd相机经第四反射镜反射与激光切割系统的第二反射镜光路连接;所述三维扫描仪设于基座11的扫描仪座上;所述计算机设于机床的外侧;所述计算机分别与数控机床内的第一数控装置、数控摇篮内的第二数控装置、三维扫描仪、激光切割系统内的激光器及同轴成像系统内的ccd相机数据线连接;所述激光切割系统及同轴成像系统设于数控机床的刀架上。
[0008]
所述激光切割系统由激光器发出的激光束依次经过第一反射镜、第二反射镜及第三反射镜后进入到二维振镜,并由二维振镜改变激光光束的路径形成旋切光束汇聚到火焰筒上。
[0009]
所述同轴成像系统由白光光源发出的白光穿过第二反射镜之后,经第三反射镜反射至二维振镜,且白光与二维振镜的旋切光束共路,直接汇聚到火焰筒的气膜孔上,并经气膜孔反射,依次经过二维振镜、第三反射镜、第二反射镜到达第四反射镜,经第四反射镜反射至ccd相机进行成像。
[0010]
本发明采用将数控机床上沿x、y及z三个运行方向的刀架与数控摇篮上绕z轴转动及绕x轴或y轴两个转动方向的工作台结合成五轴机床,并将数控机床的第一数控装置及数控摇篮的第二数控装置与计算机联控构成五轴数控机床。
[0011]
本发明采用激光切割系统及同轴成像系统构成一套与五轴数控机床联动的气膜孔激光加工及孔型检测系统。本发明克服了材料属性的限制,消除了涂层崩碎、产生剥离的缺陷,保证了孔型的精度,且满足国家对于关键装备的重大需求。
[0012]
本发明与现有技术相比具有以下有益的技术效果和优点:1)、本发明采用数控机床1上沿x、y及z三个运行方向的刀架与数控摇篮上绕z轴转动及绕x轴或y轴转动两个运行方向的工作台结合成五轴机床,充分利用第一数控装置及第
二数控装置与计算机6联网,构成五轴数控机床,借助五轴数控机床数控性能及高精度移动能力,以实现对火焰筒进行精准的空间定位与移动,保证每一个欲加工的气膜孔姿态精准的吻合到二维振镜形成旋切光束的位置,大大减化了加工过程中的控制及调整程序,提高了工作效率。
[0013]
2)、在加工过程中数控机床会快速逐一对每一个欲加工的气膜孔姿态精准定位,通过刀架驱动激光切割系统及同轴成像系统在z轴的移动,获得二维振镜形成的旋切光束与欲加工气膜孔的最佳距离,便于利用二维振镜高速、准确的运动特性实现不同类型气膜孔的填充式、旋切式加工;由于二维振镜在高速运动的同时能够高精度加工,可以减小脉冲累积热效应导致的热障涂层崩裂剥离,大大提高孔型的规则性,减小重铸层和微裂纹,提高气膜孔的加工质量。
[0014]
3)、每个气膜孔加工过程中都是气膜孔的中心轴垂直放置在二维振镜形成的旋切光束下方,该放置方式在激光加工过程中烧蚀物喷发对孔型的影响很小,因此,这种加工方式具有很明显的优势,克服了现有中心轴非垂直放置导致喷出物造成孔型不对称的加工缺陷。
[0015]
4)、借助高重复频率激光器,加之二维振镜的高速运动,能更充分的发挥高功率、高速度及高重复频率激光加工气膜孔的优势。
[0016]
5)、同轴成像系统能够对每一个气膜孔的位置信息和尺寸信息进行成像和测量,测量的信息反馈至计算机与数控机床内设第一数控装置及数控摇篮内设第二数控装置实时交互,若有偏差,便于对气膜孔进行二次加工修正,大大提高了气膜孔的加工效率。
[0017]
6)、将火焰筒与专用夹具安装在数控摇篮的工作台采用三维扫描仪对火焰筒进行3d建模,解决了火焰筒空间精准定位的难题,提高了打孔的精确度和效率。且该方法可拓展于其它复杂工件的3d建模及激光加工。
附图说明
[0018]
图1为本发明的结构示意图;图2为本发明激光切割系统及同轴成像系统的结构示意图;图3本发明激光切割系统及同轴成像系统的光路原理图。
具体实施方式
[0019]
参阅图1,本发明包括数控机床1、数控摇篮2、激光切割系统3、同轴成像系统4、三维扫描仪5、计算机6及火焰筒7;所述数控机床1上设有x、y及z轴直角坐标系,数控机床1上设有基座11,基座11上设有沿y轴运行的横梁12,横梁12上设有沿x轴运行的托板13,托板13上设有沿z轴运行的刀架14;所述数控机床1内设第一数控装置;所述基座11上还设有扫描仪座;所述数控摇篮2上设有x、y及z轴直角坐标系,数控摇篮2上设有摇篮座21,摇篮座21上设有绕z轴转动的转盘22,转盘22上设有绕x轴或y转轴动的工作台23;所述数控摇篮2内设第二数控装置;所述数控摇篮2的摇篮座21设于数控机床1的基座11上;且数控摇篮2与数控机床1
设于同一直角坐标系中。
[0020]
参阅图1、图2、图3,所述激光切割系统3由激光器31、第一反射镜32、第二反射镜33、第三反射镜34及二维振镜35构成,且激光器31、第一反射镜32、第二反射镜33、第三反射镜34及二维振镜35依次光路连接;所述同轴成像系统4由第四反射镜37、白光光源38及ccd相机39构成,所述同轴成像系统4设于激光切割系统3中;其中,白光光源38穿过激光切割系统3的第二反射镜33经第三反射镜34反射至二维振镜35,且白光光源38与二维振镜35的旋切光束共路;ccd相机39经第四反射镜37反射与激光切割系统3的第二反射镜33光路连接;所述三维扫描仪5设于基座11的扫描仪座上;所述计算机6设于机床1的外侧;所述计算机6分别与数控机床1内的第一数控装置、数控摇篮2内的第二数控装置、三维扫描仪5、激光切割系统3内的激光器31及同轴成像系统4内的ccd相机39数据线连接;所述激光切割系统3及同轴成像系统4设于数控机床1的刀架14上。
[0021]
参阅图1、图2、图3,所述激光切割系统3由激光器31发出的激光束依次经过第一反射镜32、第二反射镜33及第三反射镜34后进入到二维振镜35,并由二维振镜35改变激光光束的路径形成旋切光束汇聚到火焰筒7上。
[0022]
参阅图1、图2、图3,所述同轴成像系统4由白光光源38发出的白光穿过第二反射镜33之后,经第三反射镜34反射至二维振镜35,且白光与二维振镜35的旋切光束共路,直接汇聚到火焰筒7的气膜孔上,并经气膜孔反射,依次经过二维振镜35、第三反射镜34、第二反射镜33到达第四反射镜37,经第四反射镜37反射至ccd相机39进行成像。
实施例
[0023]
气膜孔孔形激光加工的工作过程:步骤1、参阅图1,将欲加工的火焰筒7安装在专用夹具上,并通过专用夹具将火焰筒7安装在数控摇篮2的工作台23上;步骤2、参阅图1,将火焰筒7与专用夹具安装在数控摇篮2的工作台23后,通过三维扫描仪5对火焰筒7进行x、y及z轴直角坐标系定位和3d拟合建模,且火焰筒7、数控摇篮2及数控机床1设于同一直角坐标系中,将火焰筒7的直角坐标系数据及3d拟合建模数据通过三维扫描仪5输送至计算机6;由计算机6从ug模型中提取出火焰筒7上数个气膜孔在直角坐标系中的孔位坐标,气膜孔的孔位坐标以(xn、yn、zn)标定,其中n代表孔的序号,获得精准孔位点云群;步骤3、参阅图1,加工时,通过计算机6调取某个气膜孔的孔位坐标,并通过计算机6控制数控摇篮2上摇篮座21的转盘22绕z轴转动,控制转盘22上的工作台23绕x轴或y转轴动,完成该气膜孔孔位的坐标轴线与z轴在空间平行;步骤4、参阅图1,通过计算机6控制数控机床1上基座11的横梁12沿y轴运行,控制横梁12上的托板13沿x轴运行,完成该气膜孔孔位的坐标轴线与激光切割系统3上二维振镜35发射的激光束在z轴上共线;步骤5、参阅图1,由计算机6控制激光器31按设定的激光参数,触发二维振镜35发射激光束对该气膜孔进行激光加工,并通过计算机6控制控制托板13上沿z轴运行的刀架
14,控制激光束对该气膜孔的进刀量,直至完成该气膜孔孔形的激光加工。
[0024]
步骤6、重复上述步骤3、步骤4及步骤5,依次完成下一个气膜孔孔形的激光加工。
[0025]
激光切割系统与同轴成像系统的工作过程:参阅图1、图2、图3,首先激光切割系统3的激光器31发出的激光束依次经过第一反射镜32、第二反射镜33及第三反射镜34后进入到二维振镜35,由二维振镜35改变激光光束的路径形成旋切光束汇聚到火焰筒7上进行气膜孔的激光加工。
[0026]
其次,同轴成像系统4的白光光源38发出的白光穿过第二反射镜33之后,经第三反射镜34反射至二维振镜35,且白光与二维振镜35的旋切光束共路,直接汇聚到火焰筒7的气膜孔上,此时,汇聚的白光照亮正在加工的气膜孔,并白光经气膜孔反射,依次经过二维振镜35、第三反射镜34,并穿透第二反射镜33到达第四反射镜37,经过第四反射镜37反射至ccd相机39进行成像,这样同轴成像系统4就可以实时观察气膜孔表面加工的形貌信息并对气膜孔的形貌成像。
[0027]
进一步的,为了保证加工精度,防止火焰筒7变形,优化加工效果,对于不同型号的火焰筒7须匹配各自的专用夹具,火焰筒的专用夹具须严格契合其火焰筒7的型号。
[0028]
进一步的,为配置二维振镜35的标刻速度和激光的重复频率,本发明在计算机6内设置有激光参数,该激光参数是依据每个气膜孔的结构设定二维振镜35的加工程序,二维振镜35可直接控制激光器31。
[0029]
进一步的,将激光参数统一导入到数控机床1内设第一数控装置及数控摇篮2内设第二数控装置中,通过机床位置触发控制二维振镜35加工程序的运行,并依次逐个完成气膜孔激光加工。
[0030]
进一步的,通过二维振镜35实现不同类型气膜孔的高速填充式和旋切式加工,可有效避免了脉冲累积热效应导致的热障涂层崩裂剥离,大大提高孔型的规则性,减小重铸层和微裂纹。
[0031]
进一步的,将完成激光加工的气膜孔利用同轴成像系统4进行拍照分析,同轴成像系统4的ccd相机39能够对每一个气膜孔的位置信息和尺寸信息进行成像及测量,测量的信息反馈至计算机6与数控机床1内设第一数控装置及数控摇篮2内设第二数控装置实时交互,若有偏差,由计算机6修整激光参数,并导入到数控机床1内设第一数控装置及数控摇篮2内设第二数控装置中,通过数控机床1及数控摇篮2配合激光器31再次对该气膜孔进行加工,直到孔型符合要求。
[0032]
进一步的,将火焰筒7与专用夹具安装在数控摇篮2的工作台23后,通过三维扫描仪5对火焰筒7进行x、y及z轴直角坐标系定位和3d拟合建模,且火焰筒7、数控摇篮2及数控机床1设于同一直角坐标系中,三维扫描仪5的使用能够快速对对火焰筒7进行3d建模,解决了火焰筒7空间精准定位的难题,提高了打孔的精确度和效率。
再多了解一些
本文用于企业家、创业者技术爱好者查询,结果仅供参考。