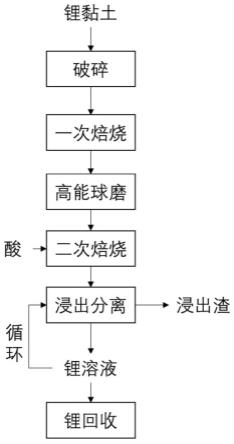
1.本发明属于锂矿石提锂技术领域,具体涉及一种从锂黏土中回收锂的方法。
背景技术:
2.随着锂离子电池的迅速推广,锂作为锂离子电池中的关键元素,愈发受到行业关注,以碳酸锂和氢氧化锂为代表的锂盐产品,市场已经供不应求,价格高居不下。所以,锂资源的进一步开发显得十分迫切。
3.目前,市场上的锂盐产品主要来源于锂辉石提锂、锂云母提锂、盐湖提锂以及退役锂离子电池中的锂回收,而锂黏土由于氧化锂品位较低一度被忽视,近年随着矿物勘探工作的深入开展,国内外均发现许多大型的锂黏土矿,其碳酸锂当量均在百万吨级以上,储量非常可观。相对于十分有限、日渐枯竭、价格高昂的锂辉石、锂云母矿,黏土矿的开采和冶炼十分具有发展前景。
4.针对锂黏土中锂的回收,目前国内相关提锂技术十分有限。专利cn110358931 a公布了一种离子交换法提取碳酸粘土型锂矿中锂的方法,该法通过三价铁盐和焙烧黏土熟料在85℃以离子交换的形式实现锂的浸出,但浸出率偏低,铁盐的消耗较高,工业化难度较大;专利cn111893318a公布了一种含锂黏土提锂的方法,该法将球磨后的锂黏土同碳酸钙、硫酸钠、硫酸钾按一定比例焙烧,粉碎后浸出得到含锂溶液,该法产生大量的钙硅废渣,难以处理,渣中氧化锂含量达到0.2%,仅适用于氧化锂品位较高的黏土矿;专利cn103849761b公布了一种低品位含锂粘土矿提锂的方法,该法提出了一种“改性焙烧-堆浸”的新工艺,但焙烧过程引入了氟化钙,氟离子对设备的腐蚀性较大,产生的氟化氢也对大气存在污染。
技术实现要素:
5.本发明旨在至少解决上述现有技术中存在的技术问题之一。为此,本发明提出一种从锂黏土中回收锂的方法,该方法工艺简单,可行性高,过程能耗低,对低品位的锂黏土具有较高的锂浸出率。
6.根据本发明的一个方面,提出了一种从锂黏土中回收锂的方法,包括以下步骤:
7.s1:将锂黏土原料进行破碎,得到锂黏土粉料,将所述锂黏土粉料进行第一次焙烧,得到一次焙烧料;
8.s2:将所述一次焙烧料与添加剂混合后进行研磨,得到研磨料;所述添加剂为钠盐、钾盐、氢氧化钠或氢氧化钾中的至少一种;
9.s3:将所述研磨料与酸混合后进行第二次焙烧,得到二次焙烧料;
10.s4:所述二次焙烧料加入浸出剂进行浸出,固液分离得到浸出液。
11.在本发明的一些实施方式中,步骤s1中,所述锂黏土原料的锂含量0.1-0.8wt%。
12.在本发明的一些实施方式中,步骤s1中,所述锂黏土粉料的粒径为50-300目。优选的,所述锂黏土粉料的粒径为100-200目。
13.在本发明的一些实施方式中,步骤s1中,所述第一次焙烧的温度为600-1200℃。优选的,所述第一次焙烧的温度为600-900℃。
14.在本发明的一些实施方式中,步骤s1中,所述第一次焙烧的时间为1-8h。优选的,所述第一次焙烧的时间为2-4h。
15.在本发明的一些实施方式中,步骤s2中,所述添加剂为naoh、koh、na2co3、k2co3、ch3coona、ch3cook、nahco3或khco3中的至少一种。与ca、mg相比,na、k的离子半径较小,离子交换动力学较高,同时避免ca、mg的引入增加后续锂溶液回收的难度,降低后续除杂成本。
16.在本发明的一些实施方式中,步骤s2中,所述添加剂与一次焙烧料的质量比为1:(5-30)。优选的,所述添加剂与一次焙烧料的质量比为1:(10-20)。
17.在本发明的一些实施方式中,步骤s2中,所述研磨的转速为100-1200rpm。优选的,所述研磨的转速为500-800rpm。
18.在本发明的一些实施方式中,步骤s2中,所述研磨的时间为1-12h。优选的,所述研磨的时间为2-6h。
19.在本发明的一些实施方式中,步骤s2中,所述研磨采用行星式球磨机、卧式球磨机、破碎机或振动球磨机中的一种。
20.在本发明的一些实施方式中,步骤s3中,所述酸为盐酸、硫酸或硝酸中的至少一种。
21.在本发明的一些实施方式中,步骤s3中,所述酸的质量浓度为2-50%。优选的,所述酸的质量浓度为5-10%。
22.在本发明的一些实施方式中,步骤s3中,所述酸与所述研磨料的质量比为(0.2-2):1。优选的,所述酸与所述研磨料的质量比为(0.5-1):1。含锂黏土矿结构复杂,存在火山岩型、碳酸岩型等多种结构,考虑到工艺兼容性和成本,加少量的酸在低温下进行焙烧,有利于残锂的浸出,也有利于不同含锂黏土矿中锂的提取。
23.在本发明的一些实施方式中,步骤s3中,所述第二次焙烧的温度为150-300℃。优选的,所述第二次焙烧的温度为200-250℃。
24.在本发明的一些实施方式中,步骤s3中,所述第二次焙烧的时间为1-10h。优选的,所述第二次焙烧的时间为2-4h。
25.在本发明的一些实施方式中,步骤s4中,所述浸出液作为所述浸出剂循环使用以富集锂。
26.在本发明的一些实施方式中,步骤s4中,所述浸出剂为水,或者选自的硫酸、盐酸、硝酸或饱和碳酸溶液中的至少一种。进一步的,所述硫酸、盐酸或硝酸的浓度为1-2mol/l。
27.在本发明的一些优选的实施方式中,步骤s4中,所述浸出剂为水。
28.根据本发明的一种优选的实施方式,至少具有以下有益效果:
29.本发明基于一次焙烧、高能研磨和二次酸化焙烧的方式实现锂黏土的锂提取,先通过一次焙烧脱除黏土矿中的结构羟基,致使黏土矿晶格间距增大,有利于锂离子的脱嵌和交换;再通过高能研磨使物料和添加剂之间发生局部高能碰撞,进一步破坏黏土矿的结构,提供反应所需活化能,使得na
/k
同黏土矿中的li
发生离子交换,同时研磨过程减小颗粒尺寸,有利于提高离子交换动力学,研磨后的锂以碳酸盐/碳酸氢盐等形式存在,该过程能实现大部分的晶格锂的脱离;再通过二次酸化焙烧,加入一定量的酸,将脱离的锂转化为
易溶解的锂盐,同时酸在焙烧过程中用于深度提取黏土矿中的锂,酸化焙烧后的物料利用浸出剂浸出,浸出的锂溶液可通过循环浸出实现锂的富集。该工艺适用于低品位锂黏土锂的浸出,浸出率高,浸出液锂浓度高,工艺兼容性强,适用于不同含锂黏土矿中锂的提取,极具应用前景。
附图说明
30.下面结合附图和实施例对本发明做进一步的说明,其中:
31.图1为本发明的工艺流程图。
具体实施方式
32.以下将结合实施例对本发明的构思及产生的技术效果进行清楚、完整地描述,以充分地理解本发明的目的、特征和效果。显然,所描述的实施例只是本发明的一部分实施例,而不是全部实施例,基于本发明的实施例,本领域的技术人员在不付出创造性劳动的前提下所获得的其他实施例,均属于本发明保护的范围。
33.实施例1
34.一种从锂黏土中回收锂的方法,参照图1,具体过程为:
35.s1:将含锂黏土破碎至100目;
36.s2:将得到破碎混料在800℃下进行焙烧,焙烧时间为2h,得到一次焙烧料;
37.s3:取500g一次焙烧料与碳酸氢钠按15:1的质量比在行星式球磨机中进行混合球磨,转速设为800rpm,研磨4h;
38.s4:将研磨后的混料按质量比1:2与10%的硫酸混合,混合均匀后在250℃下焙烧2h,得到二次焙烧料;
39.s5:得到的二次焙烧料按液固比3:1ml/g加入纯水进行浸出,分离得到浸出液与浸出渣,浸出液作为浸出剂循环浸出三次实现锂的富集,富集后的浸出液进行锂回收。
40.对本实施例的锂黏土组成以及浸出渣和浸出液,采用电感耦合等离子体发射光谱仪(icp-oes)和原子吸收分光光度计检测,检测结果如表1所示。其中锂的浸出率=(浸出液体积*锂浓度)/(浸出物料质量*锂含量)*100%,计算得到s5中锂的浸出率为90.5%,浸出液中的锂浓度经过三次循环富集后达到3095ppm。
41.表1实施例1锂黏土原料及浸出液组成
42.元素linakmgcaalsi锂黏土原料%0.380.891.110.130.2817.5216.89一次浸出液/ppm1146471721502151762853520富集锂液/ppm30951415687523765126150786
43.实施例2
44.一种从锂黏土中回收锂的方法,具体过程为:
45.s1:将含锂黏土破碎至100目;
46.s2:将得到破碎混料在800℃下进行焙烧,焙烧时间为2h,得到一次焙烧料;
47.s3:取500g一次焙烧料与碳酸氢钾按15:1的质量比在行星式球磨机中进行混合球磨,转速设为800rpm,研磨4h;
48.s4:将研磨后的混料按质量比1:2与10%的硫酸混合,混合均匀后在250℃下焙烧2h,得到二次焙烧料;
49.s5:得到的二次焙烧料按液固比3:1ml/g加入纯水进行浸出,固液分离得到浸出液与浸出渣,浸出液作为浸出剂循环浸出三次实现锂的富集。
50.对本实施例的锂黏土组成以及浸出渣和浸出液,采用电感耦合等离子体发射光谱仪(icp-oes)和原子吸收分光光度计检测,检测结果如表2所示。其中锂的浸出率=(浸出液体积*锂浓度)/(浸出物料质量*锂含量)*100%,计算得到s5中锂的浸出率为89.2%,浸出液中的锂浓度经过三次循环富集后达到3375ppm。
51.表2实施例2锂黏土原料及浸出液组成
[0052][0053][0054]
实施例3
[0055]
一种从锂黏土中回收锂的方法,具体过程为:
[0056]
s1:将含锂黏土破碎至100目;
[0057]
s2:将得到破碎混料在800℃下进行焙烧,焙烧时间为2h,得到一次焙烧料;
[0058]
s3:取500g一次焙烧料与碳酸氢钠按10:1的质量比在行星式球磨机中进行混合球磨,转速设为800rpm,研磨4h;
[0059]
s4:将研磨后的混料按质量比1:2与10%的硫酸混合,混合均匀后在250℃下焙烧2h,得到二次焙烧料;
[0060]
s5:得到的二次焙烧料按液固比3:1ml/g加入纯水进行浸出,固液分离得到浸出液与浸出渣,浸出液作为浸出剂循环浸出三次实现锂的富集。
[0061]
对本实施例的锂黏土组成以及浸出渣和浸出液,采用电感耦合等离子体发射光谱仪(icp-oes)和原子吸收分光光度计检测,检测结果如表3所示。其中锂的浸出率=(浸出液体积*锂浓度)/(浸出物料质量*锂含量)*100%,计算得到s5中锂的浸出率为95.5%,浸出液中的锂浓度经过三次循环富集后达到3998ppm。
[0062]
表3实施例3锂黏土原料及浸出液组成
[0063]
元素linakmgcaalsi锂黏土原料%0.420.750.750.080.1218.5117.52一次浸出液/ppm133745251700182511850421富集锂液/ppm39981352552301054894562801
[0064]
实施例4
[0065]
一种从锂黏土中回收锂的方法,具体过程为:
[0066]
s1:将含锂黏土破碎至100目;
[0067]
s2:将得到破碎混料在800℃下进行焙烧,焙烧时间为2h,得到一次焙烧料;
[0068]
s3:取500g一次焙烧料与碳酸氢钠按15:1的质量比在行星式球磨机中进行混合球磨,转速设为800rpm,研磨10h;
[0069]
s4:将研磨后的混料按质量比1:2与10%的硫酸混合,混合均匀后在250℃下焙烧2h,得到二次焙烧料;
[0070]
s5:得到的二次焙烧料按液固比3:1ml/g加入纯水进行浸出,固液分离得到浸出液与浸出渣,浸出液作为浸出剂循环浸出三次实现锂的富集。
[0071]
对本实施例的锂黏土组成以及浸出渣和浸出液,采用电感耦合等离子体发射光谱仪(icp-oes)和原子吸收分光光度计检测,检测结果如表4所示。其中锂的浸出率=(浸出液体积*锂浓度)/(浸出物料质量*锂含量)*100%,计算得到s5中锂的浸出率为97.5%,浸出液中的锂浓度经过三次循环富集后达到4025ppm。
[0072]
表4实施例4锂黏土原料及浸出液组成
[0073]
元素linakmgcaalsi锂黏土原料%0.420.750.750.080.1218.5117.52一次浸出液/ppm136545171528651892103389富集锂液/ppm40251362448901335126554798
[0074]
对比例1
[0075]
一种从锂黏土中回收锂的方法,与实施例1的区别在于,二次焙烧未加入酸,具体过程为:
[0076]
s1:将含锂黏土破碎至100目;
[0077]
s2:将得到破碎混料在800℃下进行焙烧,焙烧时间为2h,得到一次焙烧料;
[0078]
s3:取500g一次焙烧料与碳酸氢钠按质量比15:1的比例在行星式球磨机中进行混合球磨,转速设为800rpm,研磨4h。
[0079]
s4:将研磨后的混料在250℃下焙烧2h,得到二次焙烧料;
[0080]
s5:得到的二次焙烧混料按液固比3:1ml/g加入纯水进行浸出,固液分离得到浸出液与浸出渣,浸出液作为浸出剂循环浸出三次实现锂的富集。
[0081]
对本对比例的锂黏土组成以及浸出渣和浸出液,采用电感耦合等离子体发射光谱仪(icp-oes)和原子吸收分光光度计检测,检测结果如表1所示。其中锂的浸出率=(浸出液体积*锂浓度)/(浸出物料质量*锂含量)*100%,计算得到s5中锂的浸出率为72.3%,浸出液中的锂浓度经过三次循环富集后达到2573ppm。
[0082]
表5对比例1锂黏土原料及浸出液组成
[0083]
元素linakmgcaalsi锂黏土原料%0.360.920.950.180.3219.2517.56一次浸出液/ppm868509131021681862412456富集锂液/ppm25731526384324523696538953
[0084]
对比例1未经过酸化焙烧,从表5可以看出,锂的浸出率较低,这是由于对比例1仅经过高能球磨,球磨过程本身属于固相反应,反应动力学有限,仅靠球磨过程不能使锂浸出彻底。实施例加少量的酸在低温下进行酸化焙烧,能够深度提取黏土矿中的锂,提高锂浸出率。
[0085]
上面结合附图对本发明实施例作了详细说明,但是本发明不限于上述实施例,在
所属技术领域普通技术人员所具备的知识范围内,还可以在不脱离本发明宗旨的前提下作出各种变化。此外,在不冲突的情况下,本发明的实施例及实施例中的特征可以相互组合。
再多了解一些
本文用于企业家、创业者技术爱好者查询,结果仅供参考。