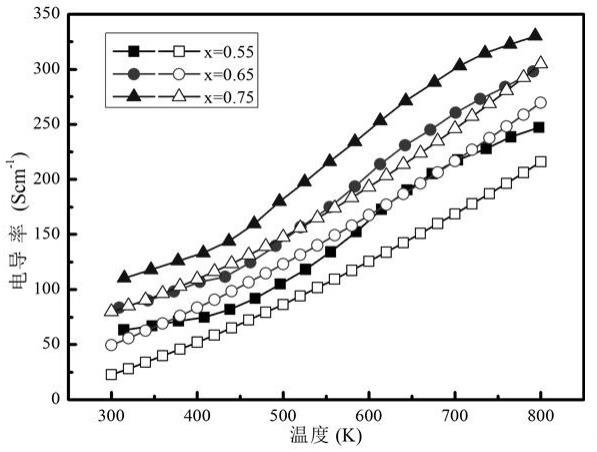
1.本发明属于合金熔炼技术领域,涉及一种精确成分控制的镁硅锡三元合金及感应熔炼方法。
背景技术:
2.镁硅锡三元合金mg2(si, sn)是由mg2si和mg2sn金属间化合物组成的固溶体合金,由于mg2si和mg2sn均无固溶度,因此mg∶si/sn原子比必须为2∶1,才能获得成分均匀的单相固溶体合金。但是由于mg元素易挥发、易氧化,合金制备过程中难以精确控制其含量。
3.镁硅锡三元合金mg2(si, sn)是一种高性能热电材料,获得成分精确的原始铸锭是获得纳米级或单晶的前提。目前,mg2(si, sn)三元合金通常采用固相反应法和常规感应熔炼法制备。其中固相反应法采用mg、si、sn粉末混合,经长时间球磨后烧结成块体;此方法采用金属粉末为原料,价格昂贵,且mg粉极易爆炸,危险性高,所得合金粉和烧结后的块体由于晶粒度小,晶界处极易氧化。其中常规感应熔炼法将mg、si和sn纯金属块加入熔炼坩埚中,通过感应加热熔化金属成为合金;但由于mg(熔点651℃)和si(熔点1410℃)元素的熔点差极大,si熔化时温度已远超mg的沸点(1107℃),mg的挥发非常严重,挥发量难以控制,通常加入过量mg进行补偿,但这种做法无法保证合金成分的精准性;此外,si作为一种半导体材料,感应熔炼过程中往往需要更大的感应电流,进一步导致mg元素的挥发和成分的偏移。
4.综合上述,亟待一种精确控制合金成分的镁硅锡三元合金mg2(si, sn)及制备方法,以提高优质mg2(si, sn) 三元合金的产量,扩大其应用范围。
技术实现要素:
5.为了达到上述目的,本发明提供一种精确成分控制的镁硅锡三元合金及感应熔炼方法,通过将mg源通过电阻加热方式,将si源和sn源通过感应加热方式分别进行加热处理,消除单质成分的熔点差,减少mg在后续过程中的挥发;并采用二次熔炼手段,保证了mg2(si, sn)三元合金成分的精准和均匀性,可对各种si/sn成分配比的mg2si
1-x
sn
x
合金进行熔炼,且不同的合金成分对应不同的加热温度参数;可以通过控制mg的挥发量获得精确成分配比的mg2(si,sn)三元合金;获得大晶粒尺度铸锭,降低晶界处mg的氧化率,解决了现有技术中存在的问题。
6.本发明所采用的技术方案是,一种精确成分控制的镁硅锡三元合金感应熔炼方法,包括以下步骤:步骤1:按照2:1-x:x的原子比,分别精确称量高纯的mg块、si块和sn块,其中0≤x≤1;步骤2:将mg块装于石墨坩埚内,采用电阻加热方式;将si块和sn块同时装于感应熔炼坩埚内,采用感应加热方式;石墨坩埚位于感应熔炼坩埚的正下方,石墨坩埚和感应熔炼坩埚受保护气氛保护;步骤3:在保护气氛下,同时对下方的石墨坩埚和上方的感应熔炼坩埚进行加热,
待感应熔炼坩埚内si和sn成分完全熔化,将感应熔炼坩埚翻转,将si-sn成分液浇至下方含有mg液的石墨坩埚中,保温10min~15min,再降温至150℃~200℃,然后关闭电源,随炉冷却至室温,得到初始铸锭;步骤4:在保护气氛下,将所得初始铸锭置于上方的感应熔炼坩埚中,加热至初始铸锭的合金熔点以上150℃~200℃,保温15min~20min;与此同时,将下方的石墨坩埚加热至600℃~650℃;感应熔炼坩埚保温结束后,将其翻转并将感应熔炼坩埚内的合金液浇铸至下方的石墨坩埚内,冷却至室温后,得到精确成分控制的mg2(si, sn)三元合金。
7.进一步地,步骤1中,x的取值为:0.5≤x≤0.8。
8.进一步地,步骤2中,石墨坩埚和所述感应熔炼坩埚受保护气氛保护;保护气氛为高纯氩气。
9.进一步地,步骤2中,感应熔炼坩埚由三层坩埚套设而成,外层和内层均为刚玉坩埚,中间层为石墨坩埚。
10.进一步地,步骤3中,同时对下方的石墨坩埚和上方的感应熔炼坩埚进行加热,具体为:其中对于下方的石墨坩埚,以15℃/min~30℃/min的加热速率加热至纯mg熔点以上50℃~100℃;对于上方的感应熔炼坩埚,以0.15kw/min~0.3kw/min的加热速率加热至6kw~6.5kw。
11.进一步地,步骤3中,降温速率为3℃/min~5℃/min。
12.进一步地,步骤4中,加热至初始铸锭的合金熔点以上150℃~200℃时的加热速率为0.2kw/min。
13.进一步地,步骤4中,冷却至室温具体为:以3℃/min~5℃/min的降温速率降温至150℃~200℃,然后关闭电源,随炉冷却至室温。
14.本发明的另一发明目的,在于提供一种精确成分控制的镁硅锡三元合金,如上述精确成分控制的镁硅锡三元合金感应熔炼方法制备而得。
15.本发明的有益效果是:本发明提供一种精确成分控制的镁硅锡三元合金及感应熔炼方法,通过将mg源通过电阻加热方式,将si源和sn源通过感应加热方式分别进行加热处理,消除单质成分的熔点差,减少mg在后续过程中的挥发;并采用二次熔炼手段,保证了mg2(si, sn)三元合金成分的精准和均匀性,可对各种si/sn成分配比的mg2si
1-x
sn
x
合金进行熔炼,且不同的合金成分对应不同的加热温度参数;可以通过控制mg的挥发量获得精确成分配比的mg2(si,sn)三元合金;获得大晶粒尺度铸锭,降低晶界处mg的氧化率。
附图说明
16.为了更清楚地说明本发明实施例或现有技术中的技术方案,下面将对实施例或现有技术描述中所需要使用的附图作简单地介绍,显而易见地,下面描述中的附图仅仅是本发明的一些实施例,对于本领域普通技术人员来讲,在不付出创造性劳动的前提下,还可以根据这些附图获得其他的附图。
17.图1是本发明实施例采用的精确成分控制的镁硅锡三元合金感应熔炼装置图。
18.图2是本发明实施例制备的精确成分控制的镁硅锡三元合金的xrd图谱。
19.图3a是本发明实施例制备的精确成分控制的镁硅锡三元合金的sem图和eds图谱。
20.图3b是本发明实施例制备的精确成分控制的镁硅锡三元合金的sem图和eds图谱。
21.图3c是本发明实施例制备的精确成分控制的镁硅锡三元合金的sem图和eds图谱。
22.图4是本发明对比例制备的镁硅锡三元合金的sem图。
23.图5是本发明实施例制备的镁硅锡三元合金的电导率随温度的变化曲线。
具体实施方式
24.下面将结合本发明实施例中的附图,对本发明实施例中的技术方案进行清楚、完整地描述,显然,所描述的实施例仅仅是本发明一部分实施例,而不是全部的实施例。基于本发明中的实施例,本领域普通技术人员在没有做出创造性劳动前提下所获得的所有其他实施例,都属于本发明保护的范围。
25.一种精确成分控制的镁硅锡三元合金感应熔炼方法,包括以下步骤:步骤1:按照2:1-x:x的原子比,分别精确称量高纯的mg块、si块和sn块,其中0≤x≤1,优选0.5≤x≤0.8。
26.针对某一确定成分的合金,如mg2si
0.5
sn
0.5
,其原子比为2:0.5:0.5,可根据其原子比换算相应的质量比,具体为24
×
2:28
×
0.5:119
×
0.5。
27.步骤2:将mg块装于石墨坩埚内,采用电阻加热方式;将si块和sn块同时装于感应熔炼坩埚内,采用感应加热方式;石墨坩埚位于感应熔炼坩埚的正下方,石墨坩埚和感应熔炼坩埚受保护气氛保护,保护气体为高纯氩气。
28.其中,石墨坩埚分半,且其内璧涂有bn脱模剂,方便脱模。由慢的电阻加热方式,容易通过热电偶控制温度,温于镁的熔点较低,因此采用加热速度稍区也更加稳定。
29.如图1所示,感应熔炼坩埚由三层坩埚套设而成,外层和内层均为刚玉坩埚,中间层为石墨坩埚,外层刚玉坩埚用于将感应线圈与石墨坩埚隔绝开来,内层刚玉坩埚用于方便根据熔炼成分进行更换,而无需更换石墨坩埚,节约成本,石墨坩埚用于通过铜线圈感应加热,保证温区的稳定。感应加热方式的加热速度更快,使硅、锡快速融化,同时可通过观察窗判断熔炼成分的融化程度。
30.步骤3:在保护气氛下,同时对下方的石墨坩埚和上方的感应熔炼坩埚进行加热;其中对于下方的石墨坩埚,以15℃/min~30℃/min的加热速率,加热至纯mg熔点以上50℃~100℃(即700℃~750℃);对于上方的感应熔炼坩埚,以0.15kw/min~0.3kw/min的加热速率,加热至6kw~6.5kw(感应熔炼通过功率控制温度,6kw对应约1500℃);待感应熔炼坩埚内si和sn成分完全熔化,将感应熔炼坩埚翻转,将si-sn成分液浇至下方含有mg液的石墨坩埚中,保温10min~15min,使其充分反应,再以3℃/min~5℃/min的降温速率降温至150℃~200℃,然后关闭电源,随炉冷却至室温,得到初始铸锭。
31.缓慢降温的目的是尽量保持晶粒粗大,有效降低晶界数量,进而有效降低mg的氧化率(晶界处mg容易氧化),稳定晶粒内部。
32.下方的石墨坩埚为电阻加热,可设置加热速率和降温速率,通过热电偶实时测定温度;上方的感应熔炼坩埚通过控制电流控制加热功率,采用热电偶测温,通过观察窗可以确定成分的熔化程度,加热速率和降温速率可以手动调节设置。
33.本步骤获得初始铸锭的目的是将三种成分进行合金化处理,消除单质成分的熔点差,减少mg在后续过程中的挥发。
34.步骤4:为确保合金成分的充分均匀性,在保护气氛下,将所得初始铸锭置于上方
的感应熔炼坩埚中,以0.2kw/min的加热速率加热至初始铸锭的合金熔点以上150℃~200℃,从观察窗观察初始铸锭完全融化后,保温15min~20min,使其充分反应;与此同时,将下方的石墨坩埚加热至600℃~650℃;感应熔炼坩埚保温结束后,将其翻转并将坩埚内的合金液浇铸至下方的石墨坩埚内,并以3℃/min~5℃/min的降温速率降温至150℃~200℃,然后关闭电源,随炉冷却至室温,得到精确成分控制的mg2(si, sn)三元合金。
35.不同成分的初始铸锭合金熔点不同,其熔点可根据mg2si-mg2sn赝二元相图中具体成分确定。
36.本方法采用二次熔炼手段,保证了mg2(si, sn)三元合金成分的精准和均匀性。可对各种si/sn成分配比的mg2si
1-x
sn
x
合金进行熔炼,且不同的合金成分对应不同的加热温度参数;可以通过控制mg的挥发量获得精确成分配比的mg2(si,sn)三元合金;获得大晶粒尺度铸锭,降低晶界处mg的氧化率。
37.实施例1一种精确成分控制的镁硅锡三元合金感应熔炼方法,包括以下步骤:(1)按照2:0.45:0.55的原子比,分别精确称量高纯的mg块、si块和sn块。
38.(2)将mg块装于石墨坩埚内,采用电阻加热方式;将si块和sn块同时装于感应熔炼坩埚内,采用感应加热方式;石墨坩埚位于感应熔炼坩埚的正下方,石墨坩埚和感应熔炼坩埚受保护气氛保护,保护气体为高纯氩气。
39.(3)在保护气氛下,同时对下方的石墨坩埚和上方的感应熔炼坩埚进行加热;其中对于下方的石墨坩埚,以20℃/min的加热速率,加热至纯mg熔点;对于上方的感应熔炼坩埚,以0.2kw/min的加热速率,加热至6kw;待感应熔炼坩埚内si和sn成分完全熔化,将感应熔炼坩埚翻转,将si-sn成分液浇至下方含有mg液的石墨坩埚中,保温15min,再以5℃/min的降温速率降温至200℃,然后关闭电源,随炉冷却至室温,得到初始铸锭。
40.(4)在保护气氛下,将所得初始铸锭置于上方的感应熔炼坩埚中,以0.2kw/min的加热速率加热至初始铸锭的合金熔点以上,从观察窗观察初始铸锭完全融化后,保温20min;与此同时,将下方的石墨坩埚加热至600℃;感应熔炼坩埚保温结束后,将其翻转并将坩埚内的合金液浇铸至下方的石墨坩埚内,并以5℃/min的降温速率降温至200℃,然后关闭电源,随炉冷却至室温,得到精确成分控制的mg2(si, sn)三元合金。
41.实施例2一种精确成分控制的镁硅锡三元合金感应熔炼方法,包括以下步骤:(1)按照2:0.35:0.65的原子比,分别精确称量高纯的mg块、si块和sn块;(2)将mg块装于石墨坩埚内,采用电阻加热方式;将si块和sn块同时装于感应熔炼坩埚内,采用感应加热方式;石墨坩埚位于感应熔炼坩埚的正下方,石墨坩埚和感应熔炼坩埚受保护气氛保护,保护气体为高纯氩气。
42.(3)在保护气氛下,同时对下方的石墨坩埚和上方的感应熔炼坩埚进行加热;其中对于下方的石墨坩埚,以15℃/min的加热速率,加热至纯mg熔点以上50℃;对于上方的感应熔炼坩埚,以0.15kw/min的加热速率,加热至6kw;待感应熔炼坩埚内si和sn成分完全熔化,将感应熔炼坩埚翻转,将si-sn成分液浇至下方含有mg液的石墨坩埚中,保温10min,使其充分反应,再以3℃/min的降温速率降温至150℃,然后关闭电源,随炉冷却至室温,得到初始铸锭。
43.(4)为确保合金成分的充分均匀性,在保护气氛下,将所得初始铸锭置于上方的感应熔炼坩埚中,以0.2kw/min的加热速率加热至初始铸锭的合金熔点以上150℃,从观察窗观察初始铸锭完全融化后,保温15min~20min,使其充分反应;与此同时,将下方的石墨坩埚加热至620℃;感应熔炼坩埚保温结束后,将其翻转并将坩埚内的合金液浇铸至下方的石墨坩埚内,并以3℃/min的降温速率降温至150℃,然后关闭电源,随炉冷却至室温,得到精确成分控制的mg2(si, sn)三元合金。
44.实施例3一种精确成分控制的镁硅锡三元合金感应熔炼方法,包括以下步骤:(1)按照2:0.25:0.75的原子比,分别精确称量高纯的mg块、si块和sn块;(2)将mg块装于石墨坩埚内,采用电阻加热方式;将si块和sn块同时装于感应熔炼坩埚内,采用感应加热方式;石墨坩埚位于感应熔炼坩埚的正下方,石墨坩埚和感应熔炼坩埚受保护气氛保护,保护气体为高纯氩气。
45.(3)在保护气氛下,同时对下方的石墨坩埚和上方的感应熔炼坩埚进行加热;其中对于下方的石墨坩埚,以30℃/min的加热速率,加热至纯mg熔点以上100℃;对于上方的感应熔炼坩埚,以0.3kw/min的加热速率,加热至6.5kw;待感应熔炼坩埚内si和sn成分完全熔化,将感应熔炼坩埚翻转,将si-sn成分液浇至下方含有mg液的石墨坩埚中,保温12min,使其充分反应,再以4℃/min的降温速率降温至180℃,然后关闭电源,随炉冷却至室温,得到初始铸锭。
46.(4)为确保合金成分的充分均匀性,在保护气氛下,将所得初始铸锭置于上方的感应熔炼坩埚中,以0.2kw/min的加热速率加热至初始铸锭的合金熔点以上200℃,从观察窗观察初始铸锭完全融化后,保温18min,使其充分反应;与此同时,将下方的石墨坩埚加热至650℃;感应熔炼坩埚保温结束后,将其翻转并将坩埚内的合金液浇铸至下方的石墨坩埚内,并以4℃/min的降温速率降温至180℃,然后关闭电源,随炉冷却至室温,得到精确成分控制的mg2(si, sn)三元合金。
47.实施例4一种精确成分控制的镁硅锡三元合金感应熔炼方法,包括以下步骤:除(1)按照2:0.2:0.8的原子比,分别精确称量高纯的mg块、si块和sn块;其余均与实施例1相同。
48.实施例5一种精确成分控制的镁硅锡三元合金感应熔炼方法,包括以下步骤:除(1)按照2:0.5:0.5的原子比,分别精确称量高纯的mg块、si块和sn块;其余均与实施例1相同。
49.对比例1常规感应熔炼浇铸法:将一定量的mg、si和sn单质原料分别按实施例1~3的比例同时放入感应熔炼坩埚中,以0.2kw/min速率进行感应加热,加热过程中将温度加至si的熔点(1414℃)以上,确保所有原材料全部融化,此温度已远超mg的沸点,因此会有大量的mg挥发损耗,通常采用加入过量的mg(10wt%左右)来进行弥补。待合金成分全部融化后保温10min,然后浇铸至模具,获得铸锭,此方法的缺陷在于无法对mg的成分进行精确控制,获得的铸锭呈富mg或富si/sn
态,需要进行进一步处理去除第二相组织。
50.对比例2钽管封装熔炼法:将一定量的mg、si和sn单质原料按实施例1比例放入钽管中,采用电弧焊将钽管密封,然后进行感应加热熔炼,加热过程中同样须将温度加至si的熔点(1414℃)以上,确保所有原材料全部融化,因在密封钽管中进行而减小了mg的损耗,加热完成后自然降温冷却,将钽管进行切割后取出合金铸锭。此方法的缺陷在于无法进行浇铸,很难保证合金中三种元素的均匀性,成分偏析严重(特别是sn元素和mg/si的密度差异很大),且密封钽管导致凝固过程中铸锭中的气体难以排出,容易产生大量的孔洞,导致铸锭性能的降低,此外钽管成本极高,且不能重复利用。
51.对比例3一种镁硅锡三元合金感应熔炼方法,包括以下步骤:除不采用步骤(4);其余均与实施例1相同。
52.图4为本对比例得到的mg2(si, sn)三元合金的sem图,可以看出明显的成分不均的现象,不同颜色区域代表成分不同的相。
53.对比例4一种镁硅锡三元合金感应熔炼方法,包括以下步骤:除(4)中不以5℃/min的降温速率降温至200℃,直接随炉冷却至室温;其余均与实施例1相同。
54.不对降温速率进行限制,会导致铸锭冷速过快,带来的影响包括;(1)作为单相金属间化合物,不同成分的mg2si
1-x
sn
x
合金均具有较大的脆性,冷速过快会使金属铸锭容易碎裂,无法得到完整的铸锭;(2)冷速过快会导致晶粒度降低,晶界处mg更易氧化。
55.实验例对本发明实施例1~3制备的镁硅锡三元合金进行x射线衍射图谱进行测试,其结果如图2所示,成分为mg2si
0.45
sn
0.55
、mg2si
0.35
sn
0.65
和mg2si
0.25
sn
0.75
三种合金的xrd衍射峰均位于mg2si和mg2sn标准峰之间,表明合金中仅包含mg2si
1-x
sn
x
单相,无si、sn等杂相生成。
56.图3a~图3c分别为实施例1~实施例3对应的镁硅锡三元合金的sem和eds测试结果,根据测试结果可知,mg、si和sn原子比与实验设定的成分接近,没有严重的成分偏析。
57.图5为本发明实施例制备的镁硅锡三元合金的电导率随温度的变化曲线,实心图标为本文所述方法制备的合金,成分分别为x=0.55、0.65和0.75,空心图标曲线为普通感应浇铸方法制备的同成分合金,结果说明,减少合金中si/sn第二相可以极大降低电子传输过程中的散射,提升电导率。根据图5,实施例1~3的不同的si/sn成分配比中,sn含量越高,载流子浓度越大,电导率也越高。
58.本说明书中的各个实施例均采用相关的方式描述,各个实施例之间相同相似的部分互相参见即可,每个实施例重点说明的都是与其他实施例的不同之处。
59.以上所述仅为本发明的较佳实施例而已,并非用于限定本发明的保护范围。凡在本发明的精神和原则之内所作的任何修改、等同替换、改进等,均包含在本发明的保护范围内。
再多了解一些
本文用于企业家、创业者技术爱好者查询,结果仅供参考。