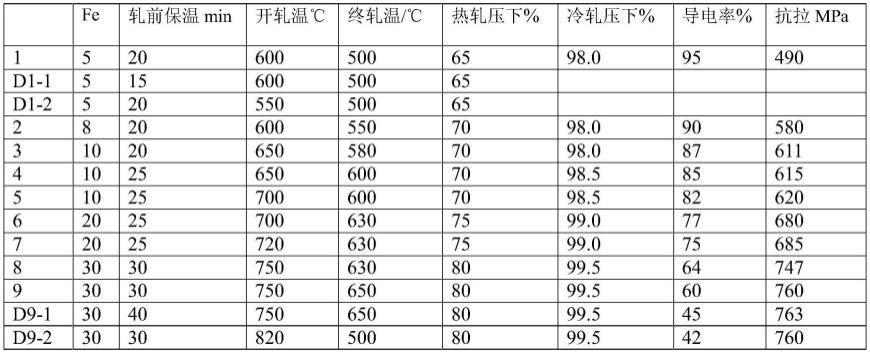
:
1.本发明属于合金制备技术领域,具体涉及一种高导电高强铜铁合金制备方法。
背景技术:
2.cu-fe合金因其高强度、高导电性、优异的磁性和电磁屏蔽性能,在电子、机械和运输领域有着广泛的应用。但是由于难混溶区的存在,cu-fe合金在重力场凝固过程中极易形成严重偏析,产生合金成分、组织和性能不均匀的问题,从而无法充分发挥其应用价值。
3.目前,制备cu-fe合金的主要方法为粉末冶金法、快速凝固法、定向凝固法等。其中粉末冶金法是先通过机械合金化或雾化得到合金粉末,然后经烧结及后续处理,因此有效地阻止了成品中宏观偏析的发生。快速凝固法通过快速冷却,使液态金属降温到远低于其发生平衡凝固时的温度而不形核,金属仍以液态的形式存在并发生相变直至最后凝固。定向凝固法的基本原理为:给凝固界面施加一定速度使之上移,致第二相液滴被界面前沿吞并,最终获得第二相弥散分布的合金组织。例如申请公布号为cn 104232962 a的专利,其制备铜铁合金方法为:将cu粉和fe粉经过球磨混粉后过筛,然后依次经过预压制、高温热压烧结、固溶处理、时效处理,即得到cu-fe合金。申请公布号为cn 108251684 a的专利,采用雾化法制备合金粉末;然后将合金粉末进行烧结处理,得到烧结坯;再将烧结坯进行拔丝处理,得到丝材;最后将丝材经过时效处理后得到铜铁合金。
4.快速凝固法和定向凝固法对产品尺寸有限制,不适合工业生产,而且基体中fe元素固溶度大,严重降低cu-fe合金的导电性能。
5.目前粉末冶金法制备铜铁合金时,混粉阶段绝大多数都采用球磨法或使用合金粉末,这会导致fe溶于cu晶格中,降低导电率。即使经过后续热处理,导电性能也与传统熔铸法类似,最高导电率为60%iacs左右,并且工艺流程复杂、需要静压机等设备,投资成本高。
技术实现要素:
6.本发明的目的是克服上述现有技术存在的不足,提供一种高导电高强铜铁合金制备方法,通过原料组分及工艺调控,在大冷轧压下率下保证高强度获得,同时在材料内部位错密度大情况下,无需时效处理,仍能兼顾保证极高的导电性能。
7.为实现上述目的,本发明采用以下技术方案:
8.一种高导电高强铜铁合金制备方法,包括以下步骤:
9.(1)按高导电高强铜铁合金组分备料,将cu粉和fe粉不经过球磨直接混合均匀,获得混合粉末,其中,所述的高导电高强铜铁合金包括组分及质量百分含量为fe 5-30%,余量为cu70-95%;
10.(2)将混合粉末装入金属容器,真空封装后,进行热轧成型,冷却至室温,获得热轧态合金,其中,所述的热轧开轧温度600-750℃,热轧前进行保温20-30min;
11.(3)将热轧态合金去壳后,进行冷加工变形处理,得到变形态cu-fe合金,即为高导电高强铜铁合金。
12.所述的步骤(1)中,cu粉粒度为1-100μm,优选为5-50μm,fe粉粒度为1-100μm,优选为5-50μm。
13.所述的步骤(1)中,cu粉和fe粉在混粉机中进行混合,混合时间为5-24h,混合过程中,无需加入磨球。
14.所述的步骤(2)中,金属容器为长方体不锈钢金属容器或长筒形不锈钢金属容器,优选为长方体不锈钢金属容器。
15.所述的步骤(2)中,真空封装方式为真空焊接,优选为真空电子束焊接。
16.所述的步骤(2)中,保温温度与热轧开轧温度等温,热轧开轧温度>终轧温度。
17.所述的步骤(2)中,热轧压下率为60%-90%。
18.所述的步骤(2)中,终轧温度500-650℃。
19.所述的步骤(2)中,冷却方式为空冷。
20.所述的步骤(2)中,热轧前保温操作使金属粉末的原子振动振幅加大,形成粘接面。
21.所述的步骤(2)中,通过热轧实现粉末成型,获得热轧态cu-fe合金,但合金内部fe原子向cu基体中的扩散极少。
22.所述的步骤(3)中,去壳方式为铣削或线切割等方式。
23.所述的步骤(3)中,冷加工变形处理方式为冷轧、冷锻或冷拔中的一种;冷加工变形量为90%-99.8%。
24.所述的步骤(3)中,制备的高导电高强铜铁合金导电率为60-95%,抗拉强度为490-760mpa。
25.本发明的有益效果:
26.本发明方法在高导电高强铜铁合金的制备过程中,采用不经过球磨直接混合 控制热轧温度的方法,最大限度地减少fe向cu基体中的扩散,有效地抑制fe原子对导电性能的影响,使合金在保持高强度的同时拥有极高的导电率。本发明工艺流程简单,无需球磨、静压等流程且获得了兼具导电率和抗拉强度综合性能优异的cu-fe合金,这是目前其它任何制备方法无法达到的。
附图说明:
27.图1为本发明实施例5制备的高导电高强铜铁合金扫描电镜图;
28.图2为本发明d1-1例制备的热轧合金宏观照片;
29.图3为本发明d1-2例制备的热轧合金宏观照片。
具体实施方式:
30.下面结合实施例对本发明作进一步的详细说明。
31.实施例1
32.一种本发明的高导电高强铜铁合金,该铜铁合金的fe含量为5wt.%,导电率为95%iacs,抗拉强度为490mpa。
33.本实施例的高导电高强cu-fe合金的制备方法,包括以下步骤:
34.(1)将粒度为15μm的fe粉和cu粉按质量比为5:95在混粉机中混粉10h;
35.(2)将混合粉末装入长方体金属容器中;
36.(3)将金属容器进行真空电子束焊接;
37.(4)将焊接完的工件在600℃保温20min后热轧,终轧温度为500,压下率为65%,空冷至室温;
38.(5)利用铣削将轧制完的工件去壳;
39.(6)将工件进行冷轧,压下率为98.0%,得到高导电高强铜铁合金,其性能数据如表1所示。
40.d1-1
41.同实施例1,区别在于,开轧前保温时间为15min,获得热轧合金出现开裂,热轧合金宏观照片如图2所示,无法实现铜铁合金制备。经理论分析,原因在于混合粉末保温时间过短,受热不均,中间部位温度低,粉末界面无法实现良好结合,导致轧后无法成型。
42.d1-2
43.同实施例1,区别在于,开轧温度降至550℃,获得热轧合金出现开裂,热轧合金宏观照片如图3所示,无法实现铜铁合金制备。经理论分析原因在于混合粉末保温温度过低,孔隙率过大,粉末界面结合力弱,导致轧后无法成型。
44.实施例2
45.一种本发明的高导电高强铜铁合金,该铜铁合金的fe含量为8wt.%,导电率为90%iacs,抗拉强度为580mpa。
46.本实施例的高导电高强cu-fe合金的制备方法,包括以下步骤:
47.(1)将粒度为15μm的fe粉和cu粉按8:92比例在混粉机中混粉5h;
48.(2)将混合粉末装入长方体金属容器中;
49.(3)将金属容器进行真空电子束焊接;
50.(4)将焊接完的工件在600℃保温20min后热轧,终轧温度为550,压下率为70%,空冷至室温;
51.(5)利用线切割将轧制完的工件去壳;
52.(6)将工件进行冷轧,压下率为98%,得到高导电高强铜铁合金,其性能数据如表1所示。
53.实施例3
54.一种本发明的高导电高强铜铁合金,该铜铁合金的fe含量为10wt.%,导电率为87%iacs,抗拉强度为611mpa。
55.本实施例的高导电高强cu-fe合金的制备方法,包括以下步骤:
56.(1)将粒度为15μm的fe粉和cu粉按1:9比例在混粉机中混粉8h;
57.(2)将混合粉末装入长方体金属容器中;
58.(3)将金属容器进行真空电子束焊接;
59.(4)将焊接完的工件在650℃保温20min后热轧,终轧温度为580,压下率为70%,空冷至室温;
60.(5)利用线切割将轧制完的工件去壳;
61.(6)将工件进行冷轧,压下率为98%,得到高导电高强铜铁合金,其性能数据如表1所示。
62.实施例4
63.同实施例1,区别在于,合金成分与制备工艺参数有所不同,得到高导电高强铜铁合金,其方案参数及性能数据如表1所示。
64.实施例5
65.同实施例1,区别在于,合金成分与制备工艺参数有所不同,得到高导电高强铜铁合金,扫描电镜图如图1所示,其方案参数及性能数据如表1所示。
66.实施例6
67.同实施例1,区别在于,合金成分与制备工艺参数有所不同,得到高导电高强铜铁合金,其方案参数及性能数据如表1所示。
68.实施例7
69.同实施例1,区别在于,合金成分与制备工艺参数有所不同,得到高导电高强铜铁合金,其方案参数及性能数据如表1所示。
70.实施例8
71.同实施例1,区别在于,合金成分与制备工艺参数有所不同,得到高导电高强铜铁合金,其方案参数及性能数据如表1所示。
72.实施例9
73.同实施例1,区别在于,合金成分与制备工艺参数有所不同,得到高导电高强铜铁合金,其方案参数及性能数据如表1所示。
74.d9-1
75.同实施例9,区别在于,开轧前保温时间调整为40min,对制备的铜铁合金进行性能测试,具体数据见表1,导电率降至45%。经对合金微观结构检测发现,开轧前过长的保温工艺下,致使fe原子向cu基体中明显扩散,虽然合金强度实现有限提升,但导电率显著降低。
76.d9-2
77.同实施例9,区别在于,开轧温度为820℃,对制备的铜铁合金进行性能测试,具体数据见表1,可见其导电性能明显下降。经对合金微观结构检测发现,由于过高的开轧温度导致fe原子向cu基体中明显扩散,导电率显著降低。
78.表1
79.
再多了解一些
本文用于企业家、创业者技术爱好者查询,结果仅供参考。