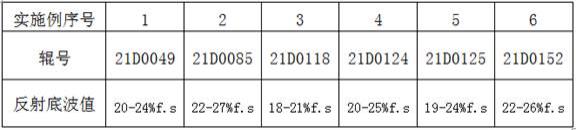
1.本发明属于冶金技术领域,具体涉及一种预防球墨铸铁轧辊芯部疏松的方法。
背景技术:
2.球墨铸铁轧辊铸造生产中经常遇到缩松方面的质量问题,特别是辊身内部的细微疏松,超声波探伤检验表现为底波衰减,即无损探伤检验底波反射波小于10%,超过国家要求标准,这种疏松缺陷将影响轧辊的刚性和强度等使用性能,也会造成生产线上机使用的轧辊断辊,导致一些轧辊铸造企业的废品率高达30%,因此在行业内亟需研究出一种防止离心复合轧辊芯部疏松解决方法。
3.近年来,国内外各大型轧辊企业虽然针对离心轧辊辊身芯部疏松造成的底波衰减问题采用更改浇注方式、调整铁水凝固顺序、增加冒口铁水量等措施,但未能从根本上有效解决,仍然无法避免底波衰减问题产生。
4.由于上述这些措施都是通过增加宏观的铁水流动性,延迟铁水凝固方式以利于补缩,消除疏松,但对于辊身较长的轧辊,特别是离心复合轧辊,由于多层离心层材质与芯部相结合,离心层与芯部相互进行热作用,具有复杂的温度场和凝固特性,造成铁水凝固顺序复杂多变,所以单纯用提高铁水流动性、延迟凝固方式进行补缩的常规宏观手段无法有效解决这种疏松问题。因此,需要深入研究球墨铸铁铸造产生缩松缺陷的本质机理,避开错综复杂的宏观条件影响,从铁水微观组织形态方面,利用铁水凝固后析出的石墨球体积的膨胀来进行补缩,进而消除这种细微型的疏松。本发明主要从增大石墨化膨胀,减少缩孔缩松方面提出技术方案,实现利用石墨体积膨胀起到自补缩作用,进而从本质上解决疏松引起的底部衰减问题。
技术实现要素:
5.本发明要解决的技术问题是提供一种预防球墨铸铁轧辊芯部疏松的方法,与行业内现有工艺相比,本发明方法能够预防球墨铸铁轧辊芯部疏松,使轧辊耐磨性和使用寿命有显著提高,杜绝了使用断辊现象。
6.为解决上述技术问题,本发明所采取的技术方案是:一种预防球墨铸铁轧辊芯部疏松的方法,所述生产方法包括熔炼、铁水变质处理、浇注、保温、热处理工序;所述热处理工序,采用高温正火 两段去应力退火热处理工艺,正火温度970~990℃,正火时间15~17小时;第一段退火温度为515~535℃,保温时间11~13h;第二段退火温度为550~570℃,保温时间11~13h。
7.本发明所述轧辊芯部碳当量4.1%≤c% 1/3si%≤4.4%,增大石墨化膨胀,减少缩孔缩松,提高球铁的流动性,有利于补缩。轧辊规格:φ800~1050mm*1880~2500mm。
8.本发明所述熔炼工序,控制铁液中的含硫量≤0.03%,按铁水重量的0.1~0.2%加入23#稀土硅铁合金,净化铁液,尽可能降低含硅量和残镁量;铁液的出炉温度为1460~1480℃。
9.本发明所述铁水变质处理工序,铁水出铁前包底加入铁水量0.5~1.0%的75fesi,1.7~1.9%的稀土镁合金,0.1~0.3%的硅锆合金。利用稀土镁合金、硅锆合金复合球化剂生产的球墨铸铁轧辊不仅石墨球数多,而且石墨球的尺寸大小不一,凝固初期形成的石墨球数也略有减少,中、小尺寸的石墨球数明显增多,说明凝固过程中石墨析出量自始至终比较一致,因此,在凝固后期有较大的膨胀且以中、小石墨球为主,尺寸分布偏向于较细小的石墨球,即缩孔、缩松倾向较小。
10.本发明所述铁水变质处理工序,分别采用两个中频感应炉熔炼工作层及芯部铁水;铁水化清后液面加入碎玻璃5~10kg/t铁水,保护铁水防止氧化,出铁水前10min在炉内调整成分合格。
11.本发明所述浇注工序,包内铁水温度达到1350~1370℃时进行浇注,浇注时间≤3min,辊身与冒口浇注时间相等。合理选择浇注温度,以免产生球化衰退和使铁液的形核能力降低,缩孔、缩松倾向增大。浇注温度高,有利于补缩,但太高会增加液态收缩量,对消除缩孔、缩松不利。
12.本发明所述保温工序,浇注完毕2~4小时内冷却至800~900℃,然后开始扣保温罩,保温罩进行全封闭保温,保温7~9h后拆除保温罩,铸型放于干燥背风处;型内保温≥48h后开箱。采用缓冷技术防止缩孔、缩松缺陷的产生,还有利于增加石墨球的数量和提高球化率;扣保温罩的时间过短会延长凝固时间而使组织变差。
13.本发明所述熔炼工序,采用碳酸钠脱硫剂进行脱硫,用量为5-10kg/t铁水。
14.本发明所述球墨铸铁轧辊芯部化学成分组成及质量百分含量为:c:3.4~3.6%、si:2.2~2.4%、mn:0.4~0.8%、p≤0.05%、s≤0.03%,余量为铁及不可避免的杂质。
15.本发明所述球墨铸铁轧辊无损探伤检验底波反射值大于10%,其硬度能够达到40~45hsd,屈服强度≥420mpa,抗拉强度≥450mpa。
16.本发明熔炼工序加入的23#稀土硅铁合金化学成分为:re:22.0~24.0%、ce/re≥46%、si≤44.0%、mn≤2.5%、ca≤5.0%、ti≤2.0%,余量为fe。本发明铁水变质处理工序加入的稀土镁合金化学成分为:re:22.0~24.0%、mg:6~8%,si:40~45%、余量为fe。
17.本发明设计思路:采取特殊工艺措施,使单位时间的铁水收缩和膨胀、收缩与补缩按比例进行,利用膨胀与动态收缩叠加,由石墨析出产生的体积膨胀起到自补缩作用,达到球墨铸铁轧辊的补缩目的,防止球墨铸铁轧辊产生缩孔缩松。
18.a、流程设计:熔炼
‑‑
变质处理
‑‑‑
浇注
‑‑‑
保温
‑‑‑
拆箱
‑‑
热处理,最后轧辊进行精加工、检验、入库。
19.b、成分设计:本发明所述球墨铸铁化学成分组成及质量百分含量为:c:3.4~3.6%、si:2.2~2.4%、mn:0.4~0.8%、p≤0.05%、s≤0.03%、ni:0.30~0.40%、cr≤0.20%、mg≥0.04%,余量为铁及不可避免的杂质。
20.c、熔炼:按步骤a中所述轧辊要求的材质成分分别在中频感应炉进行熔炼。
21.冶炼过程采用碳酸钠脱硫剂进行脱硫,防止与球化元素镁化合生产硫化镁。原铁水含硫愈高,消耗的球化元素愈多,不但产生大量的硫化镁将以夹渣物的形态存在于铁水中造成夹渣缺陷,使轧辊辊颈和芯部强度降低;而且影响球化效果和石墨形态与数量。
22.d、变质处理:
工作层铁水化清后液面加入碎玻璃保护铁水防止氧化,出铁前15min在炉内加入铁水量0.5%的钒铁、粒度10~20mm,出铁前10min加入0.2%的锰铁颗粒、粒度5~10mm。
23.芯部铁水出铁前包底加入铁水量0.5%~1.0%的75sife,1.7%~1.9%的稀土镁合金,0.1%~0.3%的硅锆合金。
24.f、浇注:出炉温度1460~1480℃,浇注温度1350~1370℃;浇注时随浇注铁水流均匀加入0.2%的粒度1~3mm硅锆合金随流孕育剂。随流孕育剂每8秒加入一袋,每袋0.5kg。浇注完成后,立即向冒口加入2kg/t的发热剂。
25.g、保温:浇注完成后2~4小时内冷却至800~900℃扣保温罩保温,保温7~9小时后拆除保温罩,型内保温48h后开箱,铸型放于干燥背风处。毛坯辊清砂后按照图纸进行粗加工,完成后进行热处理。
26.h、热处理:本发明采用高温正火 两段去应力退火热处理工艺,以充分消除残余奥氏体组织和组织应力,有利于提高轧辊的耐磨性能和抗热裂性;利用高温正火细化晶粒度。
27.本发明填补冶金轧辊铸造领域的空白,通过一种预防离心复合轧辊芯部球墨铸铁疏松的方法,包括成分设计,工艺创新,研发出一种球墨铸铁轧辊,满足轧辊的刚性和强度等使用性能。
28.本发明通过轧辊芯部球墨铸铁碳当量的设计及浇注温度的设计、铁液成分的控制、熔炼工艺、球化孕育处理、缓冷与热处理等技术手段实现球墨铸铁轧辊芯部疏松的综合预防,保证轧辊的刚性和强度等使用性能。
29.采用上述技术方案所产生的有益效果在于:1、本发明通过合理的成分设计、出炉与浇注温度设计、球化孕育工艺、保温与热处理等手段,实现球墨铸铁轧辊芯部疏松的综合预防,保证轧辊的刚性和强度等使用性能,其硬度能够达到40~45hsd,屈服强度≥420mpa,抗拉强度≥450mpa。2、本发明在显著提高轧辊的耐磨性、热稳定性基础上,使球墨铸铁铁水单位时间的收缩和膨胀、收缩与补缩按比例进行,利用膨胀与动态收缩叠加,由石墨析出产生的体积膨胀起到自补缩作用,达到球墨铸铁轧辊的补缩目的,防止球墨铸铁轧辊产生缩孔缩松。3、新工艺生产球墨铸铁轧辊使用安全、可靠,相比于原工艺生产球墨铸铁轧辊,消除了探伤底波衰减现象,杜绝轧制使用断辊异常现象,推广应用具有显著的经济和社会效益。
具体实施方式
30.下面结合具体实施例对本发明做进一步详细说明。
31.实施例1本实施例为规格φ800mm*1880mm离心复合轧辊,其芯部球墨铸铁材质的化学成分组成及质量百分含量见表2。
32.本实施例预防球墨铸铁轧辊芯部疏松的生产工艺包括熔炼、铁水变质处理、浇注、保温、热处理工序,具体工艺步骤如下所述:(1)熔炼工序:按轧辊要求的材质成分分别在中频感应炉进行熔炼。采用碳酸钠脱硫剂进行脱硫,用量为6.3kg/t铁水,控制铁液含硫量0.026%,加入23#稀土硅铁合金(按铁水重量的0.14%)以净化铁液,降低含硅量和残镁量。熔炼工艺的出炉温度为1474℃,镇静3
分钟,以利于非金属夹杂物的上浮、聚集。
33.(2)铁水变质处理工序:分别采用10t、20t中频感应炉熔炼工作层及芯部铁水,工作层铁水化清后液面加入碎玻璃7.3kg/t保护铁水防止氧化,出铁前15min在炉内加入铁水量0.5%的钒铁、粒度10~20mm,出铁前10min加入0.2%的锰铁颗粒、粒度5~10mm。
34.芯部铁水出铁前包底加入铁水量0.75%的75sife,1.8%的稀土镁合金,0.2%的硅锆合金。
35.(3)浇注工序:浇注温度1364℃;浇注时随浇注铁水流均匀加入0.2%的粒度1~3mm硅锆合金随流孕育剂。随流孕育剂每8秒加入一袋,每袋0.5kg。浇注完成后,立即向冒口加入2kg/t的发热剂。浇注时间2.7min,浇注辊身时间与冒口浇注时间相等。
36.(4)保温工序:浇注完毕4小时内冷却至860℃,然后开始扣保温罩,保温8h后拆除保温罩,型内保温48h后开箱,铸型放于干燥背风处。
37.(5)热处理工序:采用高温正火 两段去应力退火热处理工艺,正火温度980℃,正火16小时,轧辊组织转变均匀,高温热处理产生体积膨胀消除芯部疏松。第一段退火温度为515℃,保温时间13h;第二段退火温度为564℃,保温时间12h,热处理完成后,轧辊进行精加工,检验入库。
38.本实施例轧辊芯部经超声波探伤检验的底波衰减情况见表1。
39.实施例2本实施例为规格φ820mm*2100mm离心复合轧辊,其芯部球墨铸铁材质的化学成分组成及质量百分含量见表2。
40.本实施例预防球墨铸铁轧辊芯部疏松的生产工艺包括熔炼、铁水变质处理、浇注、保温、热处理工序,具体工艺步骤如下所述:(1)熔炼工序:按轧辊要求的材质成分分别在中频感应炉进行熔炼。采用碳酸钠脱硫剂进行脱硫,用量为5.0kg/t铁水,控制铁液含硫量0.030%,加入23#稀土硅铁合金(按铁水重量的0.18%)以净化铁液,降低含硅量和残镁量。熔炼工艺的出炉温度为1479℃,镇静3分钟,以利于非金属夹杂物的上浮、聚集。
41.(2)铁水变质处理工序:分别采用10t、20t中频感应炉熔炼工作层及芯部铁水,工作层铁水化清后液面加入碎玻璃9.2kg/t保护铁水防止氧化,出铁前15min在炉内加入铁水量0.5%的钒铁、粒度10~20mm,出铁前10min加入0.2%的锰铁颗粒、粒度5~10mm。
42.芯部铁水出铁前包底加入铁水量0.75%的75sife,1.8%的稀土镁合金,0.2%的硅锆合金。
43.(3)浇注工序:浇注温度1368℃;浇注时随浇注铁水流均匀加入0.2%的粒度1~3mm硅锆合金随流孕育剂。随流孕育剂每8秒加入一袋,每袋0.5kg。浇注完成后,立即向冒口加入2kg/t的发热剂。浇注时间≤2.9min,浇注辊身时间与冒口浇注时间相等。
44.(4)保温工序:浇注完毕4小时内冷却至830℃,然后开始扣保温罩,保温8h后拆除保温罩,型内保温48h后开箱,铸型放于干燥背风处。
45.(5)热处理工序:采用高温正火 两段去应力退火热处理工艺,正火温度970℃,正火时间17小时,轧辊组织转变均匀,高温热处理产生体积膨胀消除芯部疏松。第一段退火温度为518℃,保温时间12h;第二段退火温度为567℃,保温时间12h,热处理完成后,轧辊进行精加工,检验入库。
46.本实施例轧辊芯部经超声波探伤检验的底波衰减情况见表1。
47.实施例3本实施例为规格φ1050mm*2500mm离心复合轧辊,其芯部球墨铸铁材质的化学成分组成及质量百分含量见表2。
48.本实施例预防球墨铸铁轧辊芯部疏松的生产工艺包括熔炼、铁水变质处理、浇注、保温、热处理工序,具体工艺步骤如下所述:(1)熔炼工序:按轧辊要求的材质成分分别在中频感应炉进行熔炼。采用碳酸钠脱硫剂进行脱硫,用量为9.1kg/t铁水,控制铁液含硫量0.017%,加入23#稀土硅铁合金(按铁水重量的0.13%)以净化铁液,降低含硅量和残镁量。熔炼工艺的出炉温度为1476℃,镇静3分钟,以利于非金属夹杂物的上浮、聚集。
49.(2)铁水变质处理工序:分别采用10t、20t中频感应炉熔炼工作层及芯部铁水,工作层铁水化清后液面加入碎玻璃10.0kg/t保护铁水防止氧化,出铁前15min在炉内加入铁水量0.5%的钒铁、粒度10~20mm,出铁前10min加入0.2%的锰铁颗粒、粒度5~10mm。
50.芯部铁水出铁前包底加入铁水量0.75%的75sife,1.8%的稀土镁合金,0.2%的硅锆合金。
51.(3)浇注工序:浇注温度1363℃;浇注时随浇注铁水流均匀加入0.2%的粒度1~3mm硅锆合金随流孕育剂。随流孕育剂每8秒加入一袋,每袋0.5kg。浇注完成后,立即向冒口加入2kg/t的发热剂。浇注时间2.4min,浇注辊身时间与冒口浇注时间相等。
52.(4)保温工序:浇注完毕3小时内冷却至900℃,然后开始扣保温罩,保温9h后拆除保温罩,型内保温48h后开箱,铸型放于干燥背风处。
53.(5)热处理工序:采用高温正火 两段去应力退火热处理工艺,正火温度由990℃,正火时间15小时,轧辊组织转变均匀,高温热处理产生体积膨胀消除芯部疏松。第一段退火温度为521℃,保温时间12h;第二段退火温度为570℃,保温时间11h,热处理完成后,轧辊进行精加工,检验入库。
54.本实施例轧辊芯部经超声波探伤检验的底波衰减情况见表1。
55.实施例4本实施例为规格φ910mm*2050mm离心复合轧辊,其芯部球墨铸铁材质的化学成分组成及质量百分含量见表2。
56.本实施例预防球墨铸铁轧辊芯部疏松的生产工艺包括熔炼、铁水变质处理、浇注、保温、热处理工序,具体工艺步骤如下所述:(1)熔炼工序:按轧辊要求的材质成分分别在中频感应炉进行熔炼。采用碳酸钠脱硫剂进行脱硫,用量为10.0kg/t铁水,控制铁液含硫量0.014%,加入23#稀土硅铁合金(按铁水重量的0.12%)以净化铁液,降低含硅量和残镁量。熔炼工艺的出炉温度为1476℃,镇静3分钟,以利于非金属夹杂物的上浮、聚集。
57.(2)铁水变质处理工序:分别采用10t、20t中频感应炉熔炼工作层及芯部铁水,工作层铁水化清后液面加入碎玻璃8.6kg/t保护铁水防止氧化,出铁前15min在炉内加入铁水量0.5%的钒铁、粒度10~20mm,出铁前10min加入0.2%的锰铁颗粒、粒度5~10mm。
58.芯部铁水出铁前包底加入铁水量0.50%的75sife,1.7%的稀土镁合金,0.3%的硅锆合金。
59.(3)浇注工序:浇注温度1350℃;浇注时随浇注铁水流均匀加入0.2%的粒度1~3mm硅锆合金随流孕育剂。随流孕育剂每8秒加入一袋,每袋0.5kg。浇注完成后,立即向冒口加入2kg/t的发热剂。浇注时间2.5min,浇注辊身时间与冒口浇注时间相等。
60.(4)保温工序:浇注完毕4小时内冷却至820℃,然后开始扣保温罩,保温7h后拆除保温罩,型内保温52h后开箱,铸型放于干燥背风处。
61.(5)热处理工序:采用高温正火 两段去应力退火热处理工艺,正火温度985℃,正火时间16小时,轧辊组织转变均匀,高温热处理产生体积膨胀消除芯部疏松。第一段退火温度为535℃,保温时间11h;第二段退火温度为560℃,保温时间12h,热处理完成后,轧辊进行精加工,检验入库。
62.本实施例轧辊芯部经超声波探伤检验的底波衰减情况见表1。
63.实施例5本实施例为规格φ850mm*2350mm离心复合轧辊,其芯部球墨铸铁材质的化学成分组成及质量百分含量见表2。
64.本实施例预防球墨铸铁轧辊芯部疏松的生产工艺包括熔炼、铁水变质处理、浇注、保温、热处理工序,具体工艺步骤如下所述:(1)熔炼工序:按轧辊要求的材质成分分别在中频感应炉进行熔炼。采用碳酸钠脱硫剂进行脱硫,用量为8.2kg/t铁水,控制铁液含硫量0.020%,加入23#稀土硅铁合金(按铁水重量的0.13%)以净化铁液,降低含硅量和残镁量。熔炼工艺的出炉温度为1472℃,镇静3分钟,以利于非金属夹杂物的上浮、聚集。
65.(2)铁水变质处理工序:分别采用10t、20t中频感应炉熔炼工作层及芯部铁水,工作层铁水化清后液面加入碎玻璃5.0kg/t保护铁水防止氧化,出铁前15min在炉内加入铁水量0.5%的钒铁、粒度10~20mm,出铁前10min加入0.2%的锰铁颗粒、粒度5~10mm。
66.芯部铁水出铁前包底加入铁水量1.0%的75sife,1.9%的稀土镁合金,0.1%的硅锆合金。
67.(3)浇注工序:浇注温度1360℃;浇注时随浇注铁水流均匀加入0.2%的粒度1~3mm硅锆合金随流孕育剂。随流孕育剂每8秒加入一袋,每袋0.5kg。浇注完成后,立即向冒口加入2kg/t的发热剂。浇注时间3min,浇注辊身时间与冒口浇注时间相等。
68.(4)保温工序:浇注完毕2小时内冷却至850℃,然后开始扣保温罩,保温9h后拆除保温罩,型内保温50h后开箱,铸型放于干燥背风处。
69.(5)热处理工序:采用高温正火 两段去应力退火热处理工艺,正火温度由950℃提高到980℃,正火时间由8小时延长到16小时,轧辊组织转变均匀,高温热处理产生体积膨胀消除芯部疏松。第一段退火温度为525℃,保温时间12h;第二段退火温度为563℃,保温时间12h,热处理完成后,轧辊进行精加工,检验入库。
70.本实施例轧辊芯部经超声波探伤检验的底波衰减情况见表1。
71.实施例6本实施例为规格φ860mm*2400mm离心复合轧辊,其芯部球墨铸铁材质的化学成分组成及质量百分含量见表2。
72.本实施例预防球墨铸铁轧辊芯部疏松的生产工艺包括熔炼、铁水变质处理、浇注、保温、热处理工序,具体工艺步骤如下所述:
(1)熔炼工序:按轧辊要求的材质成分分别在中频感应炉进行熔炼。采用碳酸钠脱硫剂进行脱硫,用量为7.2kg/t铁水,控制铁液含硫量0.023%,加入23#稀土硅铁合金(按铁水重量的0.15%)以净化铁液,降低含硅量和残镁量。熔炼工艺的出炉温度为1478℃,镇静3分钟,以利于非金属夹杂物的上浮、聚集。
73.(2)铁水变质处理工序:分别采用10t、20t中频感应炉熔炼工作层及芯部铁水,工作层铁水化清后液面加入碎玻璃6.7kg/t保护铁水防止氧化,出铁前15min在炉内加入铁水量0.5%的钒铁、粒度10~20mm,出铁前10min加入0.2%的锰铁颗粒、粒度5~10mm。
74.芯部铁水出铁前包底加入铁水量0.80%的75sife,1.75%的稀土镁合金,0.25%的硅锆合金。(3)浇注工序:浇注温度1370℃;浇注时随浇注铁水流均匀加入0.2%的粒度1~3mm硅锆合金随流孕育剂。随流孕育剂每8秒加入一袋,每袋0.5kg。浇注完成后,立即向冒口加入2kg/t的发热剂。浇注时间2.5min,浇注辊身时间与冒口浇注时间相等。
75.(4)保温工序:浇注完毕4小时内冷却至800℃,然后开始扣保温罩,保温8h后拆除保温罩,型内保温48h后开箱,铸型放于干燥背风处。
76.(5)热处理工序:采用高温正火 两段去应力退火热处理工艺,正火温度由950℃提高到980℃,正火时间由8小时延长到16小时,轧辊组织转变均匀,高温热处理产生体积膨胀消除芯部疏松。第一段退火温度为518℃,保温时间12h;第二段退火温度为550℃,保温时间13h,热处理完成后,轧辊进行精加工,检验入库。
77.本实施例轧辊芯部经超声波探伤检验的底波情况见表1。
78.表1 实施例1~6高铬铸铁轧辊芯部超声波探伤底波值从表1中可知,通过技术方案的实施,6个实施例底波均大于10%,表明本发明生产工艺能够有效消除轧辊芯部细微疏松。
79.表2 实施例1~6高铬铸铁轧辊芯部碳当量、化学成分及质量百分含量(%)表2中余量为fe和不可避免的杂质表3实施例1~6高铬铸铁轧辊性能检测结果
以上实施例仅用以说明而非限制本发明的技术方案,尽管参照上述实施例对本发明进行了详细说明,本领域的普通技术人员应当理解:依然可以对本发明进行修改或者等同替换,而不脱离本发明的精神和范围的任何修改或局部替换,其均应涵盖在本发明的权利要求范围当中。
再多了解一些
本文用于企业家、创业者技术爱好者查询,结果仅供参考。