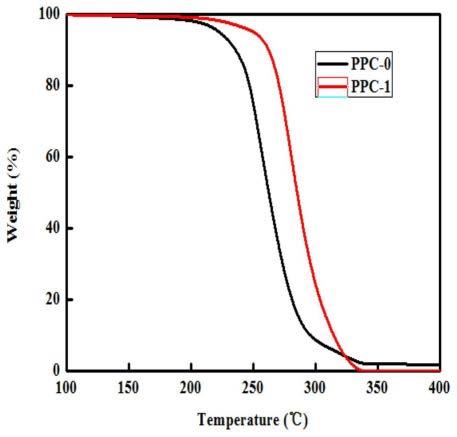
1.本发明涉及催化合成技术领域,尤其涉及一种高分子多元醇负载催化剂、其制备方法及应用。
背景技术:
2.二氧化碳是一种常见的温室气体,我国目前二氧化碳排放占全世界1/4以上,带来了严重的环境污染问题。二氧化碳固定和利用的研究一直受到企业和科研单位的广泛关注,但附加值低严重限制了其应用范围,如何高值化利用二氧化碳一种是产业界难题之一。以二氧化碳为原料合成高分子材料一直以来是提高二氧化碳应用附加值的重要手段之一,自1969年日本inoue教授首次利用二氧化碳与环氧化物共聚得到具有生物降解性的脂肪族聚碳酸酯以来,经过近50年的研究,二氧化碳与环氧化物制备高分子材料已经成为实现二氧化碳高值化应用的有效手段,国内目前多家研究机构及企业从事此方面工作。
3.对于二氧化碳与环氧丙烷共聚物-聚碳酸亚丙酯的制备而言,目前稀土三元催化剂、有机羧酸锌催化剂以其合成简单,单位产品成本低廉的特点率先实现了聚碳酸亚丙酯的工业化应用,金属氰化物催化剂早已实现了在聚醚产业的广泛应用,但由于用于催化聚碳酸亚丙酯聚合过程中,存在碳酸酯含量低的问题,一直未能大规模应用。
4.不管是稀土三元催化体系、有机羧酸锌催化体系还是双金属氰化物催化剂在聚合前期都存在引发时间,而引发时间的长短不一严重影响到聚合反应的效率,同时过长的引发时间也使聚合过程难于控制,产品稳定性难于保证。中国专利cn200810051413.7提出了一种用氧化铝或二氧化硅为载体,负载稀土三元催化剂的方法,可提高催化效率30%~48%;中国专利cn201210569798.2公布了一种以通过浸渍法以及原位活化法将戊二酸锌以纳米尺寸负载到硅烷化改性分子筛的表面,得到高分散性的非均相催化剂,能够将戊二酸锌催化效率提高至81.5g聚合物/g戊二酸锌;中国专利cn201610192925.x公布了一种以水滑石为载体,负载双金属氰化物(dmc)催化剂及用于催化二氧化碳与环氧化物聚合,具有催化活性高,产物选择性好的优点,共聚产物的碳酸酯单元含量高而环状碳酸酯含量低的特点。但现有工艺一般引发时间超过2h,引发时间较长,产品稳定性有待于提高。
技术实现要素:
5.有鉴于此,本发明要解决的技术问题在于提供一种高分子多元醇负载催化剂、其制备方法及应用,本发明提供的高分子多元醇负载催化剂用于聚碳酸亚丙酯的制备中,引发时间短,催化效果较优。
6.本发明提供了一种高分子多元醇负载催化剂的制备方法,包括以下步骤:
7.将催化剂粉料和载体混合后,在120~190℃下负载与活化,经挤出造粒或粉碎后,得到高分子多元醇负载催化剂;
8.所述催化剂粉料按照以下方法制备得到:
9.将催化剂在氩气中研磨,得到活化催化剂粉料;
10.所述催化剂包括稀土三元催化剂、有机羧酸锌催化剂或双金属氰化物催化剂;
11.所述载体包括碳酸酯质量含量为40%~60%的聚碳酸酯多元醇。
12.优选的,所述催化剂粉料和载体的质量比为5~9:1~5。
13.优选的,所述负载与活化的时间为2~20min。
14.优选的,将催化剂在氩气中研磨的时间为0.3~0.8h。
15.优选的,所述聚碳酸酯多元醇的重均分子量为10~50kda。
16.本发明还提供了一种上文所述的制备方法制得的高分子多元醇负载催化剂。
17.本发明还提供了一种聚碳酸亚丙酯的制备方法,包括以下步骤:
18.将上文所述的高分子多元醇负载催化剂、环氧丙烷和二氧化碳在温度为50~80℃、压力为3.8~5.0mpa下进行聚合反应,得到聚碳酸亚丙酯。
19.优选的,所述聚合反应在转速为450~550rpm的条件下进行。
20.优选的,所述聚合反应后,还包括:冷却至40℃以下,卸压至常压,得到聚碳酸亚丙酯。
21.优选的,所述卸压至常压后,还包括:用无水乙醇洗涤后,进行真空干燥。
22.本发明提供了一种高分子多元醇负载催化剂的制备方法,包括以下步骤:将催化剂粉料和载体混合后,在120~190℃下负载与活化,经挤出造粒或粉碎后,得到高分子多元醇负载催化剂。本发明中,所述催化剂粉料按照以下方法制备得到:将催化剂在氩气中研磨,得到活化催化剂粉料;所述催化剂包括稀土三元催化剂、有机羧酸锌催化剂或双金属氰化物催化剂。本发明提供的高分子多元醇负载催化剂用于聚碳酸亚丙酯的制备中,在达到反应温度后,可以迅速引发反应,消除引发时间影响,保证产品稳定性,催化效果较优。同时,由于高分子载体吸水率低,耐潮性好,可以保证催化剂长时间存放后,依然具有较好催化效率。
附图说明
23.图1为本发明实施例2的聚碳酸亚丙酯与对比例2的聚碳酸亚丙酯的热失重分析结果。
具体实施方式
24.下面将结合本发明实施例,对本发明的技术方案进行清楚、完整地描述,显然,所描述的实施例仅仅是本发明一部分实施例,而不是全部的实施例。基于本发明中的实施例,本领域普通技术人员在没有做出创造性劳动前提下所获得的所有其他实施例,都属于本发明保护的范围。
25.本发明提供了一种高分子多元醇负载催化剂的制备方法,包括以下步骤:
26.将催化剂粉料和载体混合后,在120~190℃下负载与活化,经挤出造粒或粉碎后,得到高分子多元醇负载催化剂。
27.本发明中,所述催化剂粉料按照以下方法制备得到:
28.将催化剂在氩气中研磨,得到活化催化剂粉料;
29.所述催化剂包括稀土三元催化剂、有机羧酸锌催化剂或双金属氰化物催化剂。
30.在本发明的某些实施例中,所述稀土三元催化剂为二乙基锌-甘油-三氯乙酸钇三
元稀土催化剂。在某些实施例中,每升二乙基锌-甘油-三氯乙酸钇三元稀土催化剂中含y(ccl3coo)3为0.0015mol、甘油为0.03mol和znet2为0.03mol。本发明对所述二乙基锌-甘油-三氯乙酸钇三元稀土催化剂的来源并无特殊的限制,可以按照中国专利cn103214666a中公开的三元催化剂的制备方法进行制备。
31.在本发明的某些实施例中,所述有机羧酸锌催化剂为戊二酸锌催化剂。本发明对所述戊二酸锌催化剂的来源并无特殊的限制,可以按照中国专利cn105899290a中实施例1的制备方法进行制备。
32.本发明对所述双金属氰化物催化剂的来源并无特殊的限制,可以按照中国专利cn101928390a中公开的金属氰化物催化剂的制备方法进行制备。
33.在本发明的某些实施例中,将催化剂在氩气中研磨的时间为0.3~0.8h。在本发明的某些实施例中,所述研磨在研磨机中进行。
34.在本发明的某些实施例中,将催化剂在氩气中研磨之前,还包括:将催化剂进行冷冻干燥,所述冷冻干燥的温度可以为20℃,时间可以为24h。
35.本发明中,所述载体包括碳酸酯质量含量为40%~60%的聚碳酸酯多元醇。
36.在本发明的某些实施例中,所述聚碳酸酯多元醇的重均分子量为10~50kda。
37.在本发明的某些实施例中,所述聚碳酸酯多元醇为聚碳酸酯二元醇、聚碳酸酯三元醇或聚碳酸亚丙酯二醇,具体的可以为碳酸酯质量含量为50%的聚碳酸酯二元醇、碳酸酯质量含量为40%的聚碳酸酯三元醇或碳酸酯质量含量为60%的聚碳酸亚丙酯二醇。
38.本发明对所述聚碳酸酯多元醇的来源并无特殊的限制,可以按照中国专利cn103881077a中公开的聚碳酸酯多元醇的制备方法进行制备。
39.得到催化剂粉料和载体后,将催化剂粉料和载体混合,在120~190℃下负载与活化。
40.在本发明的某些实施例中,所述混合为混合均匀。
41.在本发明的某些实施例中,所述催化剂粉料和载体的质量比为5~9:1~5。
42.在本发明的某些实施例中,所述负载与活化在密炼机中进行,所述负载与活化的温度为130℃或140℃,时间为2~20min。负载与活化后,经过粉碎,得到高分子多元醇负载催化剂。在本发明的某些实施例中,所述粉碎前,还包括:降温至室温。
43.在本发明的某些实施例中,所述负载与活化在双螺杆挤出机中进行,所述螺杆的温度为150~190℃,真空排气段绝压≤50kpaa。在某些实施例中,真空排气段绝压为10kpaa。负载与活化后,经挤出造粒,得到高分子多元醇负载催化剂。
44.本发明还提供了一种上文所述的制备方法制得的高分子多元醇负载催化剂。
45.本发明还提供了一种聚碳酸亚丙酯的制备方法,包括以下步骤:
46.将高分子多元醇负载催化剂、环氧丙烷和二氧化碳在温度为50~80℃、压力为3.8~5.0mpa下进行聚合反应,得到聚碳酸亚丙酯。
47.在本发明的某些实施例中,所述高分子多元醇负载催化剂和环氧丙烷的用量比为0.1~2g:40ml。在某些实施例中,所述高分子多元醇负载催化剂和环氧丙烷的用量比为2g:40ml、0.5g:40ml、0.1g:40ml。
48.在本发明的某些实施例中,所述聚合反应的温度为75℃或70℃。
49.在本发明的某些实施例中,所述聚合反应的压力为4.2mpa。
50.在本发明的某些实施例中,所述聚合反应在转速为450~550rpm的条件下进行。在某些实施例中,所述聚合反应的转速为500rpm。
51.在本发明的某些实施例中,所述聚合反应的时间为10~14h。在某些实施例中,所述聚合反应的时间为12h。
52.在本发明的某些实施例中,所述聚合反应中,催化剂的引发时间小于0.5h。在某些实施例中,所述聚合反应中,催化剂的引发时间≤10min或≤5min。在某些实施例中,所述聚合反应中,催化剂的引发时间为2min、5min或10min。
53.在本发明的某些实施例中,所述聚合反应在带有红外检测器的高压反应釜中进行。
54.在本发明的某些实施例中,所述聚合反应后,还包括:冷却至40℃以下,卸压至常压,得到聚碳酸亚丙酯。在某些实施例中,冷却至20℃。
55.在本发明的某些实施例中,所述卸压至常压后,还包括:用无水乙醇洗涤后,进行真空干燥。在某些实施例中,所述洗涤的次数为3次。在某些实施例中,所述真空干燥的温度为40℃,真空度为-0.1mpa,时间为10h。
56.本发明对上文采用的原料来源并无特殊的限制,可以为一般市售。
57.为了进一步说明本发明,以下结合实施例对本发明提供的一种高分子多元醇负载催化剂、其制备方法及应用进行详细描述,但不能将其理解为对本发明保护范围的限定。
58.实施例中,二乙基锌-甘油-三氯乙酸钇三元稀土催化剂按照中国专利cn103214666a中公开的三元催化剂的制备方法进行制备;戊二酸锌催化剂按照中国专利cn105899290a中实施例1的制备方法进行制备;双金属氰化物催化剂按照中国专利cn101928390a中公开的金属氰化物催化剂的制备方法进行制备;聚碳酸酯多元醇按照中国专利cn103881077a中公开的聚碳酸酯多元醇的制备方法进行制备。
59.实施例1
60.(1)将二乙基锌-甘油-三氯乙酸钇三元稀土催化剂在20℃下冷冻干燥24h后,在氩气中研磨0.5h,得三元稀土催化剂粉料;
61.(2)以对苯二甲酸为引发剂、双金属氰化物为催化剂,制备重均分子量为20kda、碳酸酯质量含量为50%的聚碳酸酯二元醇(ppcoh-20k-5);
62.(3)在密炼机中,将所述三元稀土催化剂粉料和ppcoh-20k-5以质量比5:5混合后,升温至130℃,密炼5min,降温至室温,粉碎后得到高分子多元醇负载催化剂。
63.为验证所述高分子多元醇负载催化剂的引发效果及聚合效果,以所述高分子多元醇负载催化剂为催化剂,在带有在红外检测器的100ml高压反应釜中进行聚合试验:向其中加入高分子多元醇负载催化剂2g,环氧丙烷40ml并充入二氧化碳,在温度为75℃、转速为500rpm、压力为4.2mpa的条件下进行聚合反应,达到聚合反应温度后,催化剂引发时间为2min(通过在线红外光谱进行测试),聚合反应12h后冷却至20℃,泄压至常压后,打开高压反应釜得到混合产物,用无水乙醇对混合产物洗涤3次后,在40℃、-0.1mpa的条件下干燥10h,得到28.6g聚碳酸亚丙酯。
64.1h-nmr测得聚碳酸亚丙酯链段中酯含量为95.5%,副产物碳酸丙烯酯6.1%;以窄分布聚苯乙烯为标样,二氯甲烷为流动相,经gpc测得本实施例制备得到的聚碳酸亚丙酯的重均分子量为470kda,分子量分布为3.03。
65.实施例2
66.(1)将戊二酸锌催化剂40g,在氩气中研磨0.5h,得戊二酸锌催化剂粉料;
67.(2)以柠檬酸为引发剂,双金属氰化物为催化剂,制备重均分子量为20kda,碳酸酯含量40%的聚碳酸酯二元醇(ppcoh-40k-4);
68.(3)在密炼机中,将所述戊二酸锌催化剂粉料和ppcoh-40k-4以质量比8:2混匀后,加入双螺杆挤出机中,螺杆温度为150~190℃,真空排气段绝压为10kpaa,挤出后空气冷却,造粒得到高分子多元醇负载催化剂。
69.为验证所述高分子多元醇负载催化剂的引发效果及聚合效果,以所述高分子多元醇负载催化剂为催化剂,在带有在红外检测器的100ml高压反应釜中进行聚合试验:向其中加入高分子多元醇负载催化剂0.5g,环氧丙烷40ml并充入二氧化碳,在温度为75℃、转速为500rpm、压力为4.2mpa的条件下进行聚合反应,达到聚合反应温度后,催化剂引发时间为5min(通过在线红外光谱进行测试),聚合反应12h后冷却至20℃,泄压至常压后,打开高压反应釜得到混合产物,用无水乙醇对混合产物洗涤3次后,在40℃、-0.1mpa的条件下干燥10h,得到20.3g聚碳酸亚丙酯。
70.1h-nmr测得聚碳酸亚丙酯链段中酯含量为93.3%,副产物碳酸丙烯酯4.4%;以窄分布聚苯乙烯为标样,二氯甲烷为流动相,经gpc测得本实施例制备得到的聚碳酸亚丙酯的重均分子量为593kda,分子量分布为2.77。
71.实施例3
72.(1)将双金属氰化物催化剂30g在氩气中研磨1h,得双金属氰化物催化剂粉料;
73.(2)制备重均分子量为50kda、碳酸酯质量含量为60%的聚碳酸亚丙酯二醇(ppc-50k-6);
74.(3)在密炼机中,将所述双金属氰化物催化剂粉料和ppc-50k-6以质量比6:4混合后,升温至140℃,密炼10min,降温至室温,粉碎后得到高分子多元醇负载催化剂。
75.为验证所述高分子多元醇负载催化剂的引发效果及聚合效果,以所述高分子多元醇负载催化剂为催化剂,在带有在红外检测器的100ml高压反应釜中进行聚合试验:向其中加入高分子多元醇负载催化剂0.1g,环氧丙烷40ml并充入二氧化碳,在温度为70℃、转速为500rpm、压力为4.2mpa的条件下进行聚合反应,达到聚合反应温度后,催化剂引发时间为10min(通过在线红外光谱进行测试),聚合反应12h后冷却至20℃,泄压至常压后,打开高压反应釜得到混合产物,用无水乙醇对混合产物洗涤3次后,在40℃、-0.1mpa的条件下干燥10h,得到55.8g聚碳酸亚丙酯。
76.1h-nmr测得聚碳酸亚丙酯链段中酯含量为86.5%,副产物碳酸丙烯酯4.8%;以窄分布聚苯乙烯为标样,二氯甲烷为流动相,经gpc测得本实施例制备得到的聚碳酸亚丙酯的重均分子量为390kda,分子量分布为3.30。
77.对比例1
78.(1)将双金属氰化物催化剂30g在氩气中研磨1h,得双金属氰化物催化剂粉料。
79.为验证所述双金属氰化物催化剂粉料的引发效果及聚合效果,以所述双金属氰化物催化剂粉料为催化剂,在带有在红外检测器的100ml高压反应釜中进行聚合试验:向其中加入高分子多元醇负载催化剂0.1g,环氧丙烷40ml并充入二氧化碳,在温度为70℃、转速为500rpm、压力为4.2mpa的条件下进行聚合反应,达到聚合反应温度后,催化剂引发时间为
20min(通过在线红外光谱进行测试),聚合反应12h后冷却至20℃,泄压至常压后,打开高压反应釜得到混合产物,用无水乙醇对混合产物洗涤3次后,在40℃、-0.1mpa的条件下干燥10h,得到45.8g聚碳酸亚丙酯。
80.1h-nmr测得聚碳酸亚丙酯链段中酯含量为70.5%,副产物碳酸丙烯酯3.3%;以窄分布聚苯乙烯为标样,二氯甲烷为流动相,经gpc测得本实施例制备得到的聚碳酸亚丙酯的重均分子量为545kda,分子量分布为5.38。
81.对比例2
82.(1)将戊二酸锌催化剂40g,在氩气中研磨0.5h,得戊二酸锌催化剂粉料。
83.为验证所述戊二酸锌催化剂粉料的引发效果及聚合效果,以所述戊二酸锌催化剂粉料为催化剂,在带有在红外检测器的100ml高压反应釜中进行聚合试验:向其中加入高分子多元醇负载催化剂0.5g,环氧丙烷40ml并充入二氧化碳,在温度为75℃、转速为500rpm、压力为4.2mpa的条件下进行聚合反应,达到聚合反应温度后,催化剂引发时间为120min(通过在线红外光谱进行测试),聚合反应12h后冷却至20℃,泄压至常压后,打开高压反应釜得到混合产物,用无水乙醇对混合产物洗涤3次后,在40℃、-0.1mpa的条件下干燥10h,得到17.6g聚碳酸亚丙酯。
84.1h-nmr测得聚碳酸亚丙酯链段中酯含量为91.5%,副产物碳酸丙烯酯6.3%;以窄分布聚苯乙烯为标样,二氯甲烷为流动相,经gpc测得本实施例制备得到的聚碳酸亚丙酯的重均分子量为625kda,分子量分布为3.42。
85.将实施例2的聚碳酸亚丙酯(ppc-1)与对比例2的聚碳酸亚丙酯(ppc-0)进行热失重分析,结果如图1所示。图1为本发明实施例2的聚碳酸亚丙酯与对比例2的聚碳酸亚丙酯的热失重分析结果。从图1可知,ppc-0的5%热失重温度为225℃,ppc-1的5%热失重温度为250℃。
86.同时,对实施例1、实施例3和对比例1的聚碳酸亚丙酯进行热失重分析,实验结果表明,实施例1的聚碳酸亚丙酯的5%热失重温度为255℃,实施例3的聚碳酸亚丙酯的5%热失重温度为250℃,对比例1的聚碳酸亚丙酯的5%热失重温度为210℃。
87.由此可以说明,本发明制备的聚碳酸亚丙酯的稳定性较优。
88.以上实施例的说明只是用于帮助理解本发明的方法及其核心思想。对这些实施例的多种修改对本领域的专业技术人员来说将是显而易见的,本文中所定义的一般原理可以在不脱离本发明的精神或范围的情况下,在其它实施例中实现。因此,本发明将不会被限制于本文所示的这些实施例,而是要符合与本文所公开的原理和新颖特点相一致的最宽的范围。
再多了解一些
本文用于企业家、创业者技术爱好者查询,结果仅供参考。