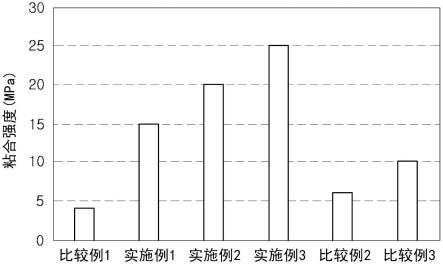
1.本发明涉及一种金属-塑料复合材料及其制造方法。
背景技术:
2.近20年来,过度使用能源的问题成为焦点,为了减少能源的使用,整个工业正在积极地进行材料的轻量化。对于严重消耗能源所造成的环境污染问题和汽车需求的剧增所造成的能源的枯竭的担忧日益增加。因此,正在对材料的轻量化进行积极的研究,并且诸如铝等轻质材料的使用量也逐年增加。特别地,在汽车工业中,汽车材料的轻量化是长期以来备受关注的事项,并且是所有汽车企业的下一代开发目标。世界知名的汽车制造商以及部件和材料相关公司的目标在于通过开发和使用新材料来实现汽车轻量化,从而生产具有高燃油效率的汽车,并且正在开展激烈的技术竞争。
3.另外,在轻质材料中,在非铁系材料中铝最广泛地被用作汽车材料,特别是被用作汽车外板的比例正在增加。但是,铝的问题在于,在加工过程中消耗大量能源,并且在价格方面不利。
4.因此,作为对应于铝的材料,厚度薄的高强度钢板正在兴起。但是,当使用高强度钢板时,随着厚度变薄,存在外板的刚性不足的问题,并且一定厚度以下的高强度钢板具有在加工过程中发生微细褶皱或回弹现象的局限性。作为替代方案,正在研究在钢板之间插入具有粘合性质的轻质高分子层的轻质夹层钢板。
5.但是,对于这种插入塑料层的形式的复合钢板进行如下工艺:为了粘合塑料层与钢板,在涂覆粘合剂后进行层压(参见韩国公开专利第2017-0068716号),或者对钢板的表面进行等离子体处理后进行层压的工艺等。但是,涂覆粘合剂的方法存在产生有害物质或者由于加工或温度变化而导致界面分离的问题,并且对钢板的表面进行等离子体处理的方法具有无法确保塑料层与钢板之间的充分的粘合力的局限性。
技术实现要素:
本发明要解决的技术问题
6.本发明的目的在于提供一种粘合强度和成型性优异的金属-塑料复合材料及其制造方法。解决技术问题的技术手段
7.根据本发明的一个方面,本发明提供一种金属-塑料复合材料,所述金属-塑料复合材料包括:金属层;以及在所述金属层的至少一面上的塑料层,其中,所述金属层和所述塑料层之间具备硅烷偶联剂的薄膜层,所述金属层和所述塑料层通过与所述硅烷偶联剂的共价键粘合。
8.根据本发明的另一个方面,本发明提供一种制造金属-塑料复合材料的方法,该方法包括以下步骤:将硅烷偶联剂涂覆在金属层的一面或两面以形成硅烷偶联剂的薄膜层;将塑料层层叠在所述薄膜层上以制造金属-塑料层叠材料;以及向所述金属-塑料层叠材料
施加热和压力来进行粘合。发明效果
9.本发明通过共价键粘合金属层和塑料层,因此与使用粘合剂的情况相比,可以以显著薄的厚度粘合金属层和塑料层,并且可以在短时间内粘合,不产生使用粘合剂时可能会产生的挥发性有机化合物,可以确保恒定且优异的粘合强度。此外,可以防止在加工过程中产生的微细褶皱或回弹等现象,并且不会发生周围环境引起的劣化,而且与塑料的种类/特性无关地,可以使与钢板的粘合力更牢固。
附图说明
10.图1的(a)是示出本发明的通过共价键粘合塑料层和金属层的形式的示意图,图1的(b)是示出塑料层和金属层之间形成的共价键的一个实例的图,图1的(c)是示出通过硅烷偶联剂形成的共价键的一个实例的图。
11.图2中示出测量根据本发明的实施例制造的复合材料的粘合强度的结果。
12.图3中示出测量根据本发明的实施例制造的复合材料的成型性的结果。
13.图4是示出实施例1、实施例3和比较例3中制造的复合材料的加工时的粘合界面的图像。最佳实施方式
14.以下,参照附图,对本发明的优选的实施方案进行说明。但是,本发明的实施方案可以变形为各种其它实施方案,本发明的范围并不限定于下面说明的实施方案。
15.通常,制造夹层钢板时,通过粘合剂粘合金属和塑料的情况下,通过范德瓦尔斯键或氢键等非共价键粘合,所述夹层钢板的粘合强度弱且不规则。此外,由于使用粘合剂,粘合层的厚度为数十μm,厚度非常厚,并且粘合所需时间也很长。此外,粘合时由于粘合剂本身的成分而产生挥发性有机化合物,或者因周围环境(湿度、热、酸性气氛等)而发生劣化现象,因此存在需要根据金属和塑料选择粘合剂的不便,并且存在还需要伴随彻底的质量控制的问题。
16.此外,有一种通过对金属的表面进行等离子体处理后层压塑料的方法来制造夹层钢板的方法,但如上所述的方法具有无法确保塑料和金属之间的充分的粘合力的局限性。
17.因此,本发明人研究了将金属和塑料粘合时可以获得显著优异的粘合力的结构,其结果确认了通过共价键粘合金属和塑料时(图1的(a)),具有可以改善如上所述的粘合强度、粘合层的厚度、粘合所需的时间等的优点。
18.因此,本发明的目的在于提供一种通过金属和塑料的分子键(或共价键)而具有优异的粘合力和成型性的金属-塑料复合材料及其制造方法。
19.详细地,本发明可以提供一种金属-塑料复合材料,所述金属-塑料复合材料包括:金属层;以及在所述金属层的至少一面上的塑料层,其中,所述金属层和所述塑料层之间具备硅烷偶联剂的薄膜层,所述金属层和所述塑料层通过与所述硅烷偶联剂的共价键粘合。
20.此外,本发明可以提供一种制造金属-塑料复合材料的方法,该方法包括以下步骤:将硅烷偶联剂涂覆在金属层的一面或两面以形成硅烷偶联剂的薄膜层;将塑料层层叠在所述薄膜层上以制造金属-塑料层叠材料;以及向所述金属-塑料层叠材料施加热和压力来进行粘合。
21.更具体地,对本发明的金属-塑料复合材料中使用的金属层和塑料层进行说明。
22.所述金属层的材料只要是用于现有的金属-塑料复合材料的金属,则可以不受限制地使用。优选地,可以使用在金属表面形成有官能团的镀覆钢板。
23.因此,本发明的金属-塑料复合材料中,在所述金属表面形成的官能团与硅烷偶联剂形成共价键,而且硅烷偶联剂与塑料也形成共价键,从而可以形成金属-塑料复合材料(图1的(b))。
24.此外,所述金属层的厚度例如可以为0.2-1.2mm,但并不受限于此。
25.另外,本发明的金属-塑料复合材料中,为了轻量化,使用塑料,所述塑料可以以夹在金属层和金属层之间的形式使用,或者可以以粘合在一个金属层上的状态使用。
26.例如,本发明的金属-塑料复合材料可以具有金属层/塑料层的双层结构、金属层/塑料层/金属层、塑料层/金属层/塑料层等夹层式三层结构,并且可以在塑料层的两面形成金属层,而且还可以具有除此之外的各种层叠结构。
27.所述塑料层的材料可以使用工程塑料,但并不受限于此。工程塑料是指用作工业材料或结构材料的高强度塑料的总称。工程塑料由分子量为数十万至数百万范围的高分子物质形成,在这一方面与由数十至数百左右的低分子物质形成的现有的塑料存在区别。
28.工程塑料的性能和特征根据其化学结构而不同,但本发明中只要可以通过共价键粘合金属和塑料,则可以不受限制地使用任何塑料,因此,例如,所述塑料层可以包含选自聚酰胺、聚缩醛、聚碳酸酯、聚苯醚、聚乙烯、聚丙烯、聚酯和聚氨酯中的一种以上的聚合物。此外,可以使用作为聚酯之一的聚对苯二甲酸丁二醇酯。
29.所述塑料层的厚度例如可以为0.2-1.2mm,但并不受限于此。
30.另外,本发明的塑料层和金属层的厚度比可以为3:1至1:5,优选可以为2:1至1:2,复合材料的总厚度可以为0.4-3.6mm。在如上所述的范围内,可以同时实现金属-塑料复合材料的刚性和轻量化,但并不受限于此,并且可以根据需要调整所述厚度比。
31.此外,本发明可以包括硅烷偶联剂的薄膜层,以使如上所述的塑料层和金属层共价键合。此时,硅烷偶联剂与形成在金属层上的官能团形成共价键,同时所述硅烷偶联剂与塑料层形成共价键。
32.所述官能团只要可以与硅烷偶联剂形成共价键,则不受限制,例如,所述官能团可以是选自胺基、乙烯基、羧基、羰基、烷氧基和羟基中的至少一种官能团。
33.例如,可以通过金属表面的脱脂、氧化等在金属表面形成羟基。基本上,硅烷是与钢板具有粘合力的无机物,通过用硅烷偶联剂处理金属,可以形成金属和硅烷偶联剂的共价键。
34.此外,所述薄膜层的厚度为数nm至数百nm,所述薄膜层的厚度可以为1nm以上至小于1000nm,例如,所述薄膜层可以是将硅烷偶联剂以50-200mg/m2涂覆在金属层的表面而形成的薄膜层。这是因为所述薄膜层形成几乎接近单分子的层,因此可以具有如上所述的厚度,由此使复合材料的界面最小化,在进行加工时可以减少金属和塑料粘合的部分的剥离现象。
35.此外,所述硅烷偶联剂可以分别与金属层和塑料层形成共价键,所述硅烷偶联剂可以使用具有乙氧基、胺基等的硅烷偶联剂、三官能或四官能的硅烷偶联剂(图1的(c))。例如,所述硅烷偶联剂可以使用具有可与羟基反应的甲氧基或乙氧基的3-环氧丙氧基丙基三
甲氧基硅烷(3-glyci doxy propyl trimethoxy silane)、6-[[3-(三乙氧基甲硅烷基)丙基]氨基]-1,3,5-三嗪-2,4-二硫醇单钠(6-[[3-(triethoxysilyl)propyl]amino]-1,3,5-triazine-2,4-dithiol monosodium,tes)、3-丙烯酰氧基丙基三甲氧基硅烷(3-acryloxy propyl trimethoxy silane)、3-氨基丙基三乙氧基硅烷(3-amino propyl triethoxy silane)和四甲氧基硅烷(tetramethoxy silane)等,但并不受限于此。
[0036]
另外,为了更牢固的粘合强度,所述薄膜层可以包含少量的聚氨酯类树脂或苯氧基类树脂。但是,所述树脂难以与金属层和塑料层形成共价键,优选地,与硅烷偶联剂相比,使用少量的所述树脂。例如,以薄膜层的总重量为基准,硅烷偶联剂的含量可以为5-99重量%,聚氨酯类树脂或聚苯氧基类树脂的含量可以为1-5重量%。
[0037]
此外,为了确保金属-塑料复合材料的耐蚀性、耐化学性等,可以进一步包含六氟锆酸(iv)、草酸、单宁酸、有机ti螯合物、消泡剂、润湿(wetting)剂等,但优选地,所述成分的含量也是不阻碍硅烷偶联剂的共价键的程度。例如,以薄膜层的总重量为基准,所述成分的含量可以为1-5重量%。
[0038]
此外,所述共价键是由形成在金属层的表面上的官能团与硅烷偶联剂以及由所述硅烷偶联剂与塑料层形成,所述共价键可以形成为任何键,例如可以是碳-碳键、硅氧烷键、酰胺键、酯键或醚键,但并不受限于此。
[0039]
此时,向所述金属-塑料层叠材料施加热和压力来进行粘合时可以形成如上所述的共价键,可以通过向所述金属-塑料层叠材料施加热和压力来形成硅烷偶联剂与金属层以及所述硅烷偶联剂与塑料层的共价键。
[0040]
所述热和压力可以在热压机(hot press)中进行,但并不受限于此,并且可以根据粘合的聚合物材料的熔点而变化。考虑到通常通过热熔合方法制造的金属-塑料复合材料中使用的塑料的熔点,可以在80-280℃的温度下进行。当低于上述温度时,可能不发生热熔合,当超过上述温度时,熔合的塑料熔化,因此可能发生塑料的性质可能会变形的问题。
[0041]
另外,当用粘合剂粘合金属和塑料时,难以找到可以同时粘合金属和塑料的粘合剂。此外,粘合成如“金属-粘合剂-塑料”的结构,界面的数量增加,因此制造的复合材料存在加工时在粘合面容易发生剥离的问题。但是,这种问题可以通过如本发明的利用共价键的金属-塑料的粘合来解决。
[0042]
此外,通过辊或化学/电化学蚀刻在金属的表面上形成凹凸,并赋予所述凹凸和塑料的粘合效果时,存在难以形成均匀的凹凸的问题。此外,所述塑料需要熔融并流入所述凹凸之间以表现出粘合效果,但流变学(rheology)特性根据塑料的种类而不同,因此在规定最佳的凹凸结构方面存在局限性。但是,本发明通过共价键粘合金属和塑料,而与塑料的种类无关,因此可以克服如上所述的限制。
[0043]
此外,对塑料进行改性而赋予化学官能团后与金属粘合时,通过紫外线(uv)处理、臭氧处理、自由基反应、接枝反应和交联剂处理等,将极性官能团引入塑料层的表面。但是,这种工艺复杂或所需时间长,而且为了具有与钢板的粘合力,需要交联剂等。此外,存在难以通过塑料的改性来均匀地引入极性官能团的问题。但是,本发明中通过共价键粘合金属和塑料,因此无需如上所述将极性官能团引入塑料中。
[0044]
以下,通过具体的实施例,对本发明进行更具体的说明。下述实施例仅仅是有助于理解本发明的示例,本发明的范围并不限定于此。
具体实施方式
[0045]
实施例
[0046]
实施例1
[0047]
金属层使用两张热浸镀锌钢板(切割成宽度为150mm、长度为120mm且厚度为0.3mm的薄板形式,然后用蒸馏水洗涤并干燥而准备),并且使用由尼龙6形成的塑料层(宽度为150mm,长度为50mm,厚度为1mm)。
[0048]
为了在所述金属层的表面形成官能团,通过棒涂将硅烷偶联剂水溶液涂覆在所述金属层上,然后在80-120℃之间进行固化。之后,以金属-塑料-金属的三层结构进行层叠(在经表面处理的钢板上放置塑料层,并再次层叠经表面处理的钢板,以使经表面处理的钢板与塑料接触),并利用热压机在180℃下粘合。
[0049]
此时,将硅烷偶联剂水溶液以50-300mg/m2的量进行涂覆,所述硅烷偶联剂水溶液的每100g的水中包含2.5g的四甲氧基硅烷和4.5g的3-氨基丙基三乙氧基硅烷,由此在所述金属层的表面形成厚度小于1μm的薄膜层。
[0050]
之后,将所述塑料层置于所述金属层之间,以使所述塑料层与两张金属层上形成的所述薄膜层接触,利用热压机进行加压和加热处理,从而制造金属-塑料复合材料。
[0051]
实施例2和实施例3
[0052]
除了硅烷偶联剂的含量使用实施例1的1.5倍的重量(实施例2)和2倍的重量(实施例3)之外,通过与实施例1相同的方法制造金属-塑料复合材料。
[0053]
比较例1
[0054]
除了在实施例1中不使用硅烷偶联剂水溶液之外,通过与实施例1相同的方法制造金属-塑料复合材料。
[0055]
比较例2
[0056]
将电镀钢板切割成宽度为150mm、长度为120mm且厚度为0.3mm的薄板形式,然后用蒸馏水进行洗涤并干燥而准备,将60-250g/l的naoh溶液用作电解液,施加电压设为5-2v,施加时间设为10-30分钟,通过电解蚀刻对电镀钢板进行物理蚀刻。
[0057]
将如上所述蚀刻的金属和包含尼龙6的塑料层以金属-塑料-金属的三层结构进行层叠(在经表面处理的钢板上放置塑料层,并再次层叠经表面处理的钢板,以使经表面处理的钢板与塑料接触),并利用热压机在180℃下粘合。
[0058]
比较例3
[0059]
除了在实施例1中使用市售的氨基甲酸酯类粘合剂作为粘合剂来形成厚度为1μm的薄膜层之外,通过与实施例1相同的方法制造金属-塑料复合材料。
[0060]
实验例
[0061]
测量实施例1至实施例3和比较例1至比较例3中制造的金属-塑料复合材料的粘合强度、成型性和弯曲加工性。
[0062]
[粘合强度的测量]
[0063]
通过常规的搭接剪切实验(lap.shear test,astm d 1002)测量粘合强度。
[0064]
其结果,如图2所示,可以确认与比较例1至比较例3的金属-塑料复合材料相比,实施例1至实施例3的金属-塑料复合材料表现出至少1.5倍的粘合强度。
[0065]
[成型性的测量]
[0066]
为了测量金属-塑料复合材料的成型性,进行埃里克森评价。
[0067]
具体地,改变冲头冲程,并测量实施例1的金属-塑料复合材料和厚度与所述金属-塑料复合材料相同的热浸镀钢板的成型性。
[0068]
其结果,如图3所示,可以确认与仅由热浸镀钢板形成的材料的成型不同,即使增加冲头冲程的力,实施例1的金属-塑料复合材料也不会因所述冲头冲程而破裂,并且获得了进一步提高的成型性。图3中,gi cq表示仅由所述热浸镀钢板形成的材料,cpc表示实施例1的金属-塑料复合材料。
[0069]
[弯曲加工性的测量]
[0070]
使用台钳(vise),将比较例3的金属-塑料复合材料进行180
°
弯曲加工后确认塑料和钢板是否剥离。
[0071]
如图4的(a)所示,可以确认将比较例3中制造的金属-塑料复合材料弯曲时,由于粘合力差,复合材料的界面剥离。
[0072]
另一方面,如图4的(b)所示,可以确认实施例1和实施例3的复合材料在弯曲加工时,由于粘合力优异,复合材料的界面没有剥离。
[0073]
以上,对本发明的实施例进行了详细的说明,但本发明的权利范围并不限定于此,在不脱离权利要求书中记载的本发明的技术思想的范围内可以进行各种修改和变形,这对于本领域技术人员而言是显而易见的。
再多了解一些
本文用于企业家、创业者技术爱好者查询,结果仅供参考。