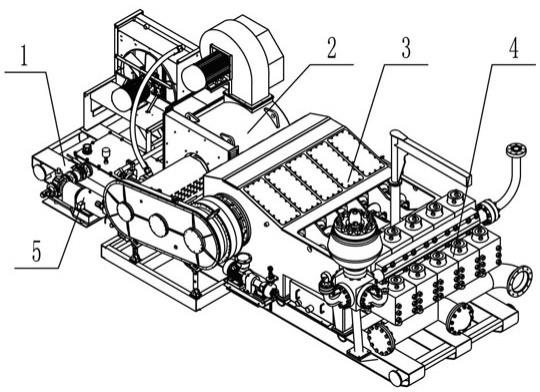
1.本发明具体涉及泥浆泵技术领域,尤其涉及一种多缸大流量高压力泥浆泵。
背景技术:
2.泥浆泵,又称钻机的心脏,在钻井的过程中,一方面,向井底动力钻具提供动力;另一方面,向井底输送和循环钻井液,以达到清除、携带井底岩屑的目的。常用的泥浆泵采用活塞式或柱塞式,由电机带动泵的曲轴回转,曲轴通过十字头再带动活塞或柱塞在泵缸中做往复运动。在吸入和排出阀的交替作用下,实现压送与循环钻井液的目的。
3.现有三缸单作用泥浆泵在高压力、大排量下,具有排出压力峰值波动大、高压排出管线振动较大、管汇易损坏、可靠性低、效率低等缺点,难以满足超深井、高压喷射钻井、大位移水平井、超深井、海洋平台钻井、复杂井的钻井工艺要求。鉴于以上问题,特提出一种多缸大流量高压力泥浆泵装置。
技术实现要素:
4.本发明的目的是为了解决现有技术中存在的缺点,而提出的一种多缸大流量高压力泥浆泵。
5.为了实现上述目的,本发明采用了如下技术方案:一种多缸大流量高压力泥浆泵,包括底座,所述底座上设置有传动系统总成、动力端总成、液力端总成及动力端润滑系统,所述传动系统总成连接动力端总成,所述动力端总成连接液力端总成;所述传动系统总成包括变频电机、十字传动轴、减速器、减速器支座、减速器支座和曲轴连杆机构,其中,十字传动轴包括输入端、输出端、万向十字轴、万向十字轴和叉头法兰;所述动力端总成包括机壳、焊接在机壳上的一个右轴承座、五个左轴承座、五个十字头缸套及前端板;机壳分别形成五个曲轴-连杆-十字头总成腔室、五个十字头-活塞总成腔室;所述液力端总成包括设置在动力端机壳上的多个一体式吸排缸、锻造排出管、排出高压阀组件及活塞总成,活塞总成与十字头总成连接,一体式吸排缸内设置有吸入高压阀组件,一体式吸排缸与排出管之间具有相互连通的流道;所述动力端润滑系统包括溢流阀、散热器、润滑油箱、齿轮油泵电机组、过滤器、温控阀。
6.进一步的,所述传动系统总成中,变频电机与底座进行连接,变频电机的输出端与十字传动轴的输入端驱动连接,输入端通过万向十字轴与叉头法兰连接,叉头法兰通过万向十字轴与十字传动轴的输出端连接;输出端与减速器的输入端驱动连接,减速器的输出端与曲轴连杆总成进行驱动连接,减速器安装在减速器支座和减速器支座上。
7.进一步的,所述传动系统总成中,曲轴连杆总成包括多个轴承内圈安装组件、多个
轴承外圈安装组件、一个圆柱滚子轴承、曲轴、连杆总成、多个圆柱滚子轴承;曲轴采用五曲拐六支撑的结构,曲轴包括五曲拐和六支撑,曲轴在每个曲拐及每个支撑均开有润滑油口;连杆总成的两端为一体式和分体式。
8.进一步的,所述十字头总成包括十字头体、十字头销、上下两块铜套、介杆及润滑油道,十字头销用于连接连杆总成及十字头体,缸套与十字头体使用螺钉连接,介杆与十字头体使用螺栓连接。
9.进一步的,所述连杆总成上为的一端用十字头销连接于十字头体处,连杆总成上为的一端使用内六角圆柱螺钉固定于曲轴的曲拐处;曲轴带动连杆总成做圆周运动,连杆总成的运动带动十字头总成在十字头缸套内进行往复直线运动,十字头总成的运动带动活塞总成在十字头-活塞总成腔室内做往复直线运动。
10.进一步的,所述活塞总成包括连接介杆、十字头-活塞杆卡箍总成、活塞杆、活塞、缸套座、耐磨垫、双头螺柱、缸套压环、缸套卡圈及缸套。
11.进一步的,所述一体式吸排缸包括排出端及吸入端,吸入端连接吸入总管,排出端通过销轴、螺钉与缸套座连接,排出端、缸套座通过双头螺柱与动力端总成中的前端板固定,双头螺柱的一端与排出端螺纹连接,另一端采用螺母进行连接。
12.本发明的有益效果为:1.通过采用变频电机,实现绿色钻井要求,相比柴油机噪声降低20%-30%,能耗降低50%-60%,相比异步电机,能耗降低20%-30%,相比三缸泵排量波动降低2/3,有效提高了钻井效率,通过采用减速器驱动泥浆泵,用齿轮传动代替传统的带传动、链传动,综合能效提高约7%-10%,通过采用的液力端总成,相比同型号三缸泵减重15%,方便现场对液力端维护保养,提高工人维护效率。
13.2.通过曲轴采用五曲拐六支撑的结构,提高曲轴承载强度及刚度,减小曲轴重量,提高动力端的可靠性及经济性。
14.3.通过在曲轴曲拐、十字头销处摒弃滚动摩擦结构,采用滑动摩擦,并通过强制润滑的形式,降低设备重量及外形尺寸。
15.4.在相同流量下,由于泵的缸数增加,可降低泵每分钟冲次,冲次的降低能大大提高易损件的使用时间,从而增加泵的可靠性。
附图说明
16.图1是本发明的示意图。
17.图2是本发明中传动系统总成的结构示意图。
18.图3是本发明中十字传动轴的结构示意图。
19.图4是本发明中动力端总成的结构示意图。
20.图5是本发明中曲轴连杆机构的结构示意图。
21.图6是本发明中曲轴的结构示意图。
22.图7是本发明中十字头总成的结构示意图。
23.图8是本发明中液力端总成的结构示意图。
24.图9是本发明中动力端润滑系统的结构示意图。
25.图中:图中标记:1-底座、2-传动系统总成、21-变频电机、22-十字传动轴、22a-十
字传动轴输入端、22b-十字传动轴输出端、220a-万向十字轴、220b-万向十字轴、221-叉头法兰、23-减速器、24-减速器支架、25-减速器支架、26-曲轴连杆机构、260-轴承内圈安装组件、261-圆柱滚子轴承、262曲轴、262a-曲轴支撑、262b-曲轴曲拐、262c-曲轴支撑润滑油口、262d-曲轴曲拐润滑油口、263-连杆总成、263a-一体式连杆端部、263b-分体式连杆端部、264-圆柱滚子轴承、265-轴承外圈安装组件、3-动力端总成、31-右轴承座、32-曲轴-连杆-十字头总成腔室、33-左轴承座、34-十字头缸套、35-十字头总成、351-十字头体、352-十字头销、353-铜套、354-介杆、355-润滑油道、36-前端板、37-十字头-活塞总成腔室、38-机壳、4-液力端总成、41-活塞总成、410-十字头-活塞杆卡箍总成、411-活塞杆、412-活塞、42-缸套座、420-耐磨垫、421-双头螺柱、422-缸套压环、423-缸套卡圈、424-缸套、43-一体式吸排缸、43a-一体式吸排缸排出端、43b-一体式吸排缸吸入端、430-螺钉、431-定位销、44-吸入总管、45-吸入高压阀组件、46-锻造排出管、47-流道、48-排出高压阀组件、5-动力端润滑系统、51-溢流阀、52-散热器、53-润滑油箱、54-齿轮油泵电机组、55-过滤器、56-温控阀。
具体实施方式
26.下面将结合本发明实施例中的附图,对本发明实施例中的技术方案进行清楚、完整地描述。
27.参照图1-9,一种多缸大流量高压力泥浆泵,包括底座1、传动系统总成2、动力端总成3、液力端总成4及动力端润滑系统5;传动系统总成2、动力端总成3、液力端总成4及动力端润滑系统5均布置与底座1上,传动系统总成2连接动力端总成3,动力端总成3连接液力端总成4,其中,传动系统总成2为动力端总成3提供动力,动力端总成3驱动液力端总成4工作,动力端润滑系统5为动力端总成3提供润滑。
28.传动系统总成2包括变频电机21、十字传动轴22、减速器23、减速器支座24、减速器支座25、曲轴连杆机构26,变频电机21的输出端驱动十字转动轴22输入端22a转动,十字转动轴22的输出端22b带动减速器23的输入端转动,减速器23的输出端驱动曲轴连杆总成26转动,从而实现曲轴连杆机构26的运动,其中,减速器支座24和减速器支座25用来支撑安装减速器23。
29.作为更具体的设计,传动系统总成2中,变频电机21使用螺栓与底座1进行连接;变频电机21的输出端使用螺栓与十字传动轴22的输入端22a进行连接,十字传动轴22的输出端22b使用螺栓与减速器23的输入端进行连接,减速器23通过行星齿轮加平行齿轮的方式对输入端高转速进行降速处理,以达到规定的输出转速,传递到减速器输出端,减速器输出端与曲轴连杆总成26的输入端是用花键连接,进而带动曲轴连杆总成26的运动。
30.作为更具体的设计,传动系统总成2中,十字传动轴22的输入端22a与叉头法兰221通过万向十字轴220a连接,叉头法兰221与十字传动轴22的输出端22b通过万向十字轴220b连接,十字传动轴22可在万向十字轴220a、220b进行一定角度范围内的调整,本设计允许变频电机21的输出端与减速器23输入端不在同一条中心线上,允许有一定的工作角度,通过调整万向十字轴220a、220b进行安装,可避免因变频电机21的输出端与减速器23的输入端不同心带来的安装不便;曲轴连杆总成26包括30个轴承内圈安装组件260、20个轴承外圈安装组件265、1个
圆柱滚子轴承261、曲轴262、连杆总成263、5个圆柱滚子轴承264;30个轴承内圈安装组件260使用螺栓连接限制圆柱滚子轴承261、圆柱滚子轴承264内圈的左右移动;20个轴承外圈安装组件265与轴承座31、轴承座33使用螺栓连接,限制圆柱滚子轴承261、圆柱滚子轴承264外圈的左右移动;作为更具体的设计,曲轴262采用五曲拐六支撑的结构,五曲拐262b用来安装5个连杆总成263,六支撑262a用来安装圆柱滚子轴承261和圆柱滚子轴承264;曲轴262在每个曲拐262b及每个支撑262a均开有润滑油口262c及262d,以达到润滑的目的。
31.连杆总成263的两端263a和263b,连杆总成263的一端263a采用一体式设计,连杆总成263的另一端263b采用分体式设计,连杆总成263的一端263a用十字头销352连接于十字头体351处,连杆总成263的另一端263b使用内六角圆柱螺钉固定于曲轴262的曲拐262b处。
32.动力端总成3包括机壳38、焊接与机壳38上的1个右轴承座31、5个左轴承座33、5个十字头缸套34及用于连接液力端总成4的前端板36,右轴承座31焊接在机壳38上,用于连接减速器23及固定圆柱滚子轴承261,多个左轴承座33焊接在机壳38上,用于固定圆柱滚子轴承264。
33.机壳38采用整体焊接的形式,机壳38分别形成5个曲轴-连杆-十字头总成腔室32、十字头缸套34、十字头总成35、5个十字头-活塞总成腔室37,十字头总成35包括十字头体351、十字头销352、上下两块铜套353、介杆354及润滑油道355。
34.曲轴262带动连杆总成263做圆周运动,连杆总成263的运动带动十字头总成35在十字头缸套34内进行往复直线运动,十字头总成35的运动带动活塞总成41在十字头-活塞总成腔室37内做往复直线运动。
35.十字头销352用于连接连杆总成263及十字头体351,缸套353与十字头体使用螺钉连接,介杆354与十字头体351使用螺栓连接。十字头体351及铜套353均开有润滑油道355,十字头总成35在十字头缸套34内运动时,保证供油充分,以达到润滑的目的。
36.焊接在机壳38上的多个十字头缸套34采用一体式结构设计,此结构可提高十字头缸套的使用寿命;十字头总成35在十字头缸套34内做往复直线运动。
37.曲轴262的曲拐262b处与连杆总成263的263b处、连杆总成263的263a处与十字头销352处、十字头总成35的铜套353处与十字头缸套34内部摒弃滚动摩擦结构,采用滑动摩擦结构。
38.液力端总成4,包括设置在动力端机壳上的多个“l”型布置的一体式吸排缸43、锻造排出管46、一体式吸排缸43内设置有吸入高压阀组件45和排出高压阀组件48及连接动力端总成中十字头总成35的活塞总成41。活塞总成41的往复运动带动一体式吸排缸打开/关闭,进而控制液体的吸入/排出,一体式吸排缸43与锻造排出管46之间具有相互连通的流道47。多个“l”型布置的一体式吸排缸43,具有互换性。
39.作为更具体的设计,活塞总成41包括连接介杆354与活塞杆411的十字头-活塞杆卡箍总成410、活塞杆411及活塞412,活塞杆411采用分段式,便于拆卸及安装,活塞412在缸套424中做直线运动,以带动吸入高压阀组件45和排出高压阀组件48的打开或闭合。
40.作为更具体的设计,基于上述具体实施方式的设计基础上,动力端总成3中设置有
5个十字头-活塞总成腔室37,用于装配、拆卸活塞总成41。
41.作为更具体的设计,一体式吸排缸43包括排出端43a及吸入端43b,吸入端43b连接吸入总管44,排出端43a通过销轴431、螺钉430与缸套座42连接,排出端43a、缸套座42通过双头螺柱421与动力端总成3中的前端板36固定,双头螺柱35的一端与排出端43a螺纹连接,另一端采用螺母进行连接。
42.作为更具体的机构设计,缸套424安装于缸套座42内,缸套424与排出端43a之间设置有耐磨垫420,防止活塞总成41在运动过程中撞击排出端43a,进而提高一体式吸排缸43的使用寿命。
43.基于上述具体结构的的设计基础上,为了保证装配效果,具体的,缸套座42与排出端43a使用定位销431进行定位、使用螺钉430进行安装。缸套座42与一体式吸排缸43装配完成后,使用双头螺柱421与动力端总成3的前墙板36进行固定。多个一体式吸排缸43与前墙板36装配完成后,使用双头螺柱安装锻造排出管46,使用螺栓安装吸入总管44,及安装多个吸入高压阀组件45和多个排出高压阀组件。缸套座42与前墙板36完成装配后,先将耐磨垫420装入缸套座42的内部,然后进行缸套424的安装,接着进行缸套压环422的安装,缸套压环422与缸套座42通过螺纹连接固定,随着缸套压环422旋进,顶着缸套424前进,缸套424顶着耐磨垫420前进,当耐磨垫420运动至排出端43a的端面时,缸套压环422旋进停止,进一步的安装缸套挡圈423,最后安装活塞总成41。
44.基于上述具体结构的的设计基础上,为了保证拆卸效果,具体的,缸套424上设置有缸套挡圈,缸套压环422旋出时,当旋至缸套挡圈423处时,随着缸套压环422的继续旋出,带动缸套422退出,从而取出耐磨垫420。
45.动力端润滑系统5包括51溢流阀、52散热器、53润滑油箱、54齿轮油泵电机组、55过滤器、56温控阀,在齿轮油泵电机组54的作用下,从润滑油箱53中吸入润滑油,润滑油经过管路进入过滤器55过滤,经过过滤后的润滑油进入温控阀56,根据润滑油温度的情况分流到散热器51进行冷却,经冷却后的润滑油润滑管路,在此对润滑油的油压进行检测,通过溢流阀51对油压进行控制,以此达到润滑减速器23及动力端总成3的目的。
再多了解一些
本文用于企业家、创业者技术爱好者查询,结果仅供参考。